基于Q-DAS分析的高精度曲轴磨床质量控制
2018-07-02 12:54:09· 来源:AI制造
在曲轴轴颈外圆的磨削加工中,我公司采用的是德国勇克的CBN高速磨床。该磨床具有如下特点:采用跟随摆动式(切点跟踪)磨削连杆颈技术;通过两个砂轮架进给轴与工件回转轴及在线检测进行数控联动的全闭环控制;实现了曲轴两个不同相位的连杆颈的同时磨削;实现了曲轴一次装夹完成对连杆颈、主轴颈的精密加工。
在曲轴轴颈外圆的磨削加工中,我公司采用的是德国勇克的CBN高速磨床。该磨床具有如下特点:采用跟随摆动式(切点跟踪)磨削连杆颈技术;通过两个砂轮架进给轴与工件回转轴及在线检测进行数控联动的全闭环控制;实现了曲轴两个不同相位的连杆颈的同时磨削;实现了曲轴一次装夹完成对连杆颈、主轴颈的精密加工。
在实际生产中,我们采用如下措施对勇克CBN高速磨床磨削曲轴进行质量监控:通过Q-DAS统计50件/次的线旁检具;50件/次的三坐标检测;下线MARPOSS测量仪100%全尺寸测量,数据生成Q-DAS描点图进行跟踪。
曲轴磨削加工质量变异分析
1.测量值稳定,机床修正值与实际相反
下图为一个班次的生产数据,转折点为员工干预调整。问题是:测量值稳定,但是机床修正值与实际相反,越补越差。排除机械类中心支架或者测头的问题,判断可能为电气方面出现故障,导致设备获得假信号。最大的可能就是测头及连接单元进水,导致机床信号失真的可能性比较大。为此,可检查测头是否进水,用替换法更换测头与接线盒之间的传感器线和接头,判断是否失效。
检查发现,故障失效原因是磨削液水汽导致接头产生电容效应,水汽作为容性媒介导致电压信号记忆,从而导致尺寸异常。改进措施:将测头连接模块单元移出加工仓 ,减少水汽接触。
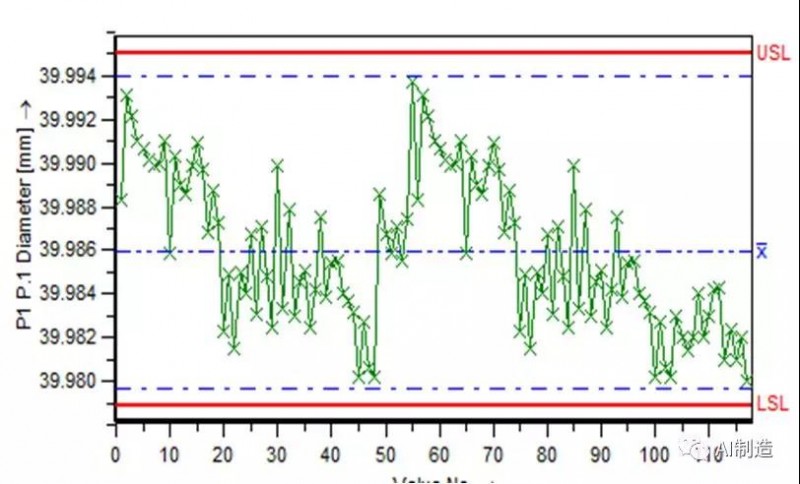
一个班次的生产数据
2.测量值不准
通过线旁检具测量工件尺寸和机床测量尺寸结果进行对比发现,机床测量值有误,进一步分析有确定原因可能来自以下两个方面:
(1)主轴颈中值48.985mm,连杆颈中值39.985mm,直径相差9mm。作用到半径4.5mm基本为测头的行程极限(测头最大行程为5mm),可能测头测量超程了,导致反馈不准。
(2)该测头在正负极限处的线性度差,也会导致反馈值不准确。出现这种连续工件直径偏大一段时间后又恢复正常,问题多数情况为测头波纹管断裂(见下图)或者波纹管测量完一个行程后弹性恢复有卡滞。停机检查测头,用手压或拉测头顶部检查是否有卡滞现象,检查波纹管是否正常,可发现问题产生原因。
经检查发现,问题的原因是测头连接波纹管断裂。于是更换波纹管、量化调整标准,调整V型块间隙2mm(限位),即下图中蓝色箭头标记处。
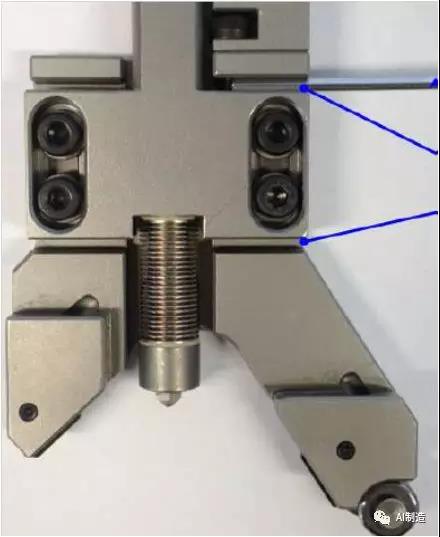
测头波纹管发生断裂
3.连杆颈波动,连杆颈尺寸存在突变,主轴颈尺寸正常
该问题原因一般为随动架随动轨迹存在机械干涉,如常见的与喷嘴或工件的侧臂存在干涉时的质量表现(见下图)。
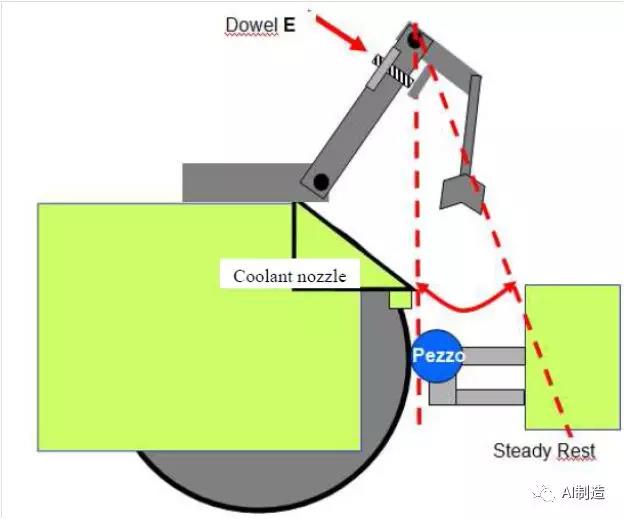
主轴颈尺寸正常
分析确定,问题的根本原因就是测头随动架运动过程中有干涉。随即对连杆颈测头随动架进行最高限位的调整(见下图),问题得到解决。
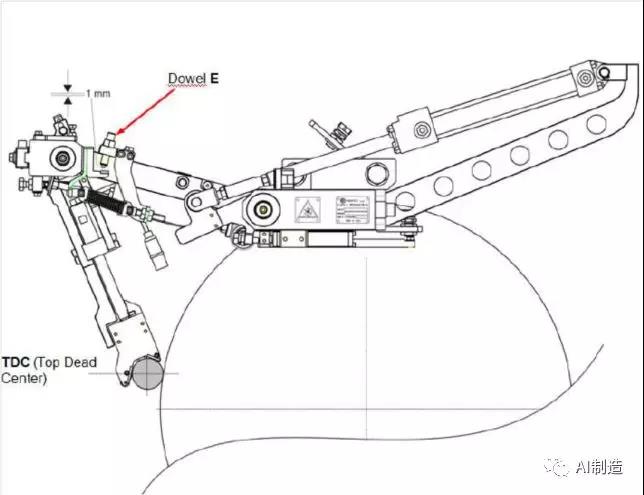
对连杆颈测头随动架进行最高限位的调整
4.主轴颈加工不稳定,尺寸波动大
该问题通常为测量主轴颈时测头随动架随动轨迹存在机械干涉导致(随动路径与加工连杆颈不一样,行程相对短,调整的限位机构也不同),如常见的与喷嘴或工件的侧臂存在干涉时的质量表现。分析确定,测头随动架运动过程中有干涉,对测头随动架进行限位的调整随即得到解决(见下图)。
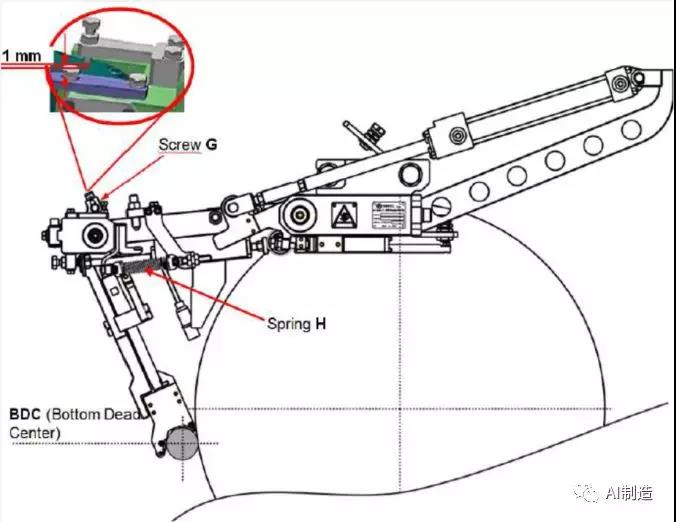
对测头随动架进行限位的调整随
5.所有轴颈尺寸波动大
通过Q-DAS 50件过程能力数据分析,有两台机床的A5/A4直径表现出正弦波动(14um左右),如下图所示,对比另外两台机床发现有两个变化点:两台机床切屑液温度波动比另外两台温度波动大4.5℃;尺寸存在正弦波动,以经验分析受主轴头架跳动影响较大,经过千分表测量发现与头架主轴产生周期性正弦波动一致。
根本原因:头架主轴球笼轴承内轴表面磨损严重;磨削液水温波动大,根据温度补偿公式算出会造成约2um的波动。解决办法:更换顶尖球笼轴承,改进设备冷却系统,减少磨削液温度波动。
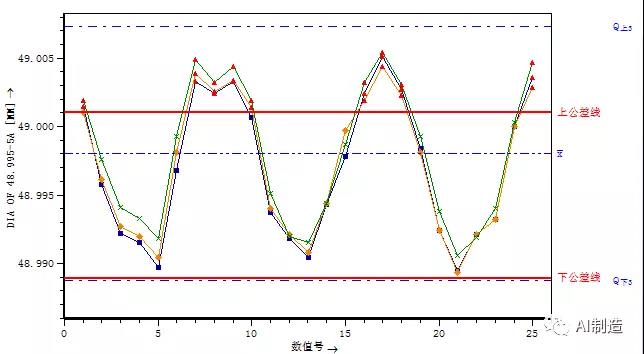
A5/A4轴颈尺寸波动
6.芯轴跳动超差
通过Q-DAS 50件过程能力数据的分析,发现芯轴跳动超差为四台磨床中的一台。通过对机床主夹机构带MASTER测量发现芯轴端跳动大,多次调整未果。进一步分析芯轴端卡爪是否有问题,通过对比其他台磨床发现芯轴夹紧端一卡爪磨损量偏大。确定问题原因:芯轴端卡爪磨损过大,导致加工时候产生径跳。
改进措施:对磨损区域进行轮廓测量,及区域模拟圆弧半径,卡爪半径相差5mm以上,导致定位不准。针对此问题,制定PM更换周期,计划2年更换。
7.某轴颈圆度超差
轴颈圆度偏大为生产中的常见问题,一般检查完机床中心支架抬起度推出度(见下图),确认主夹部分无问题后进行圆度补偿。
造成此问题的原因很多,可通过Q-DAS跟踪各轴颈圆度情况,及时人工干预调整。改进措施:进行圆度补偿,单独编写三坐标圆度测量程序,可节省2/3(约10min)的测量时间。
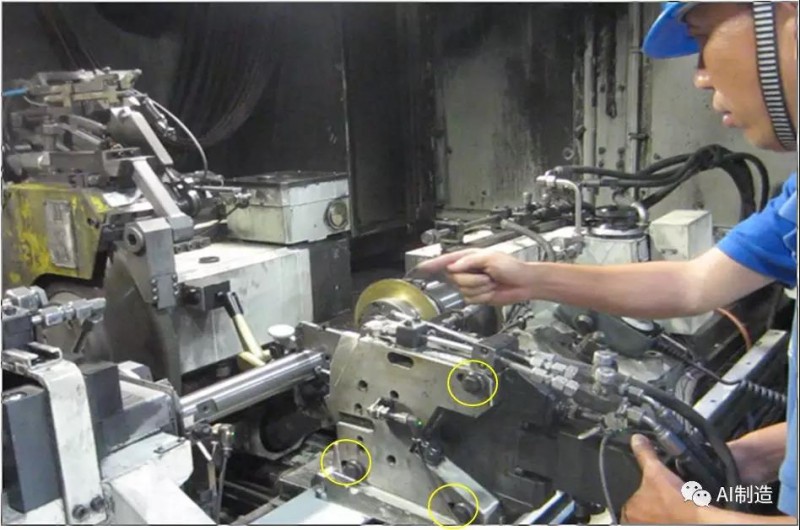
中心支架抬起度推出度检查
结语
曲轴磨削为曲轴生产过程中的重要加工工艺,磨床的稳定性决定了最终下线产品的质量合格率。磨床的高精度和机械结构复杂性,温度、测头机械位置、电气信号、压力和中心支架的抬起度推出度等中的某一个因素(大部分时候为多个因素共同发生)的改变往往会引起大的质量波动,需要花大量时间去查找原因解决问题,成为曲轴生产线的加工瓶颈。本文囊括了曲轴磨床大部分质量超差情况,希望对大家曲轴磨床加工质量改进有所帮助。
在实际生产中,我们采用如下措施对勇克CBN高速磨床磨削曲轴进行质量监控:通过Q-DAS统计50件/次的线旁检具;50件/次的三坐标检测;下线MARPOSS测量仪100%全尺寸测量,数据生成Q-DAS描点图进行跟踪。
曲轴磨削加工质量变异分析
1.测量值稳定,机床修正值与实际相反
下图为一个班次的生产数据,转折点为员工干预调整。问题是:测量值稳定,但是机床修正值与实际相反,越补越差。排除机械类中心支架或者测头的问题,判断可能为电气方面出现故障,导致设备获得假信号。最大的可能就是测头及连接单元进水,导致机床信号失真的可能性比较大。为此,可检查测头是否进水,用替换法更换测头与接线盒之间的传感器线和接头,判断是否失效。
检查发现,故障失效原因是磨削液水汽导致接头产生电容效应,水汽作为容性媒介导致电压信号记忆,从而导致尺寸异常。改进措施:将测头连接模块单元移出加工仓 ,减少水汽接触。
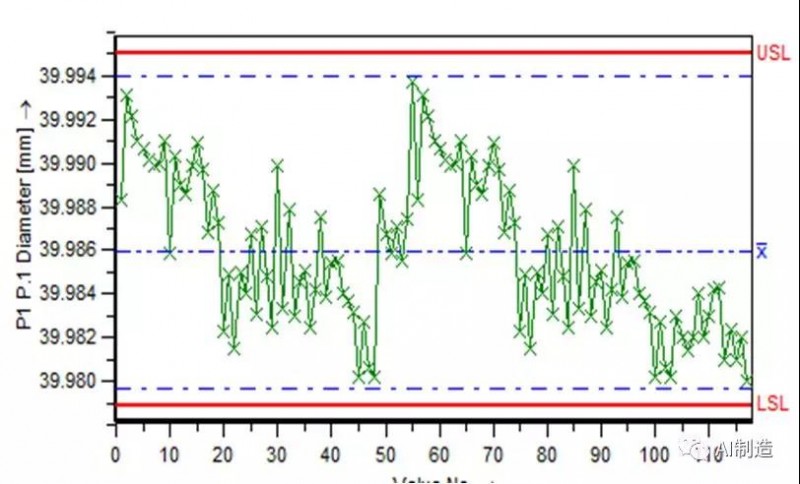
一个班次的生产数据
2.测量值不准
通过线旁检具测量工件尺寸和机床测量尺寸结果进行对比发现,机床测量值有误,进一步分析有确定原因可能来自以下两个方面:
(1)主轴颈中值48.985mm,连杆颈中值39.985mm,直径相差9mm。作用到半径4.5mm基本为测头的行程极限(测头最大行程为5mm),可能测头测量超程了,导致反馈不准。
(2)该测头在正负极限处的线性度差,也会导致反馈值不准确。出现这种连续工件直径偏大一段时间后又恢复正常,问题多数情况为测头波纹管断裂(见下图)或者波纹管测量完一个行程后弹性恢复有卡滞。停机检查测头,用手压或拉测头顶部检查是否有卡滞现象,检查波纹管是否正常,可发现问题产生原因。
经检查发现,问题的原因是测头连接波纹管断裂。于是更换波纹管、量化调整标准,调整V型块间隙2mm(限位),即下图中蓝色箭头标记处。
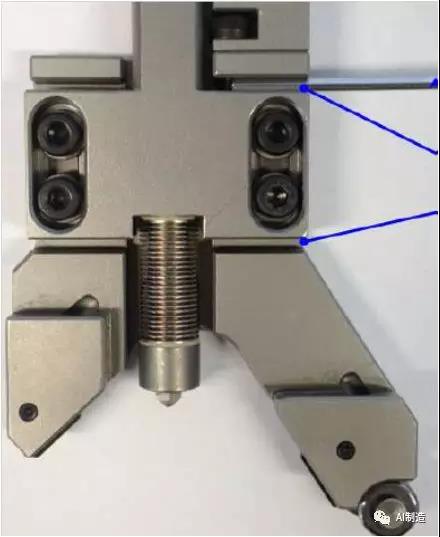
测头波纹管发生断裂
3.连杆颈波动,连杆颈尺寸存在突变,主轴颈尺寸正常
该问题原因一般为随动架随动轨迹存在机械干涉,如常见的与喷嘴或工件的侧臂存在干涉时的质量表现(见下图)。
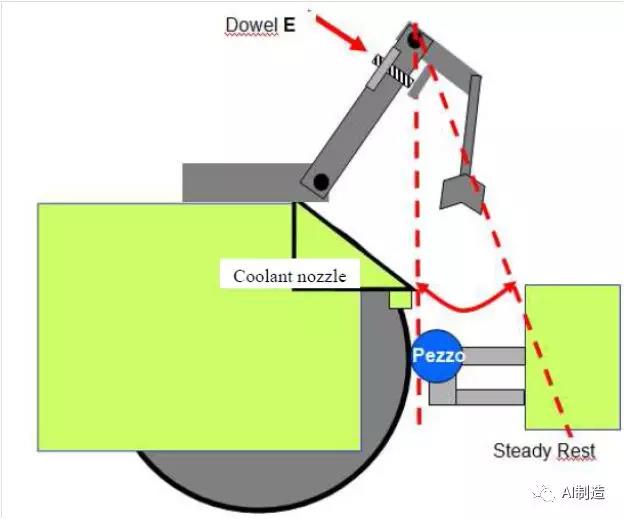
主轴颈尺寸正常
分析确定,问题的根本原因就是测头随动架运动过程中有干涉。随即对连杆颈测头随动架进行最高限位的调整(见下图),问题得到解决。
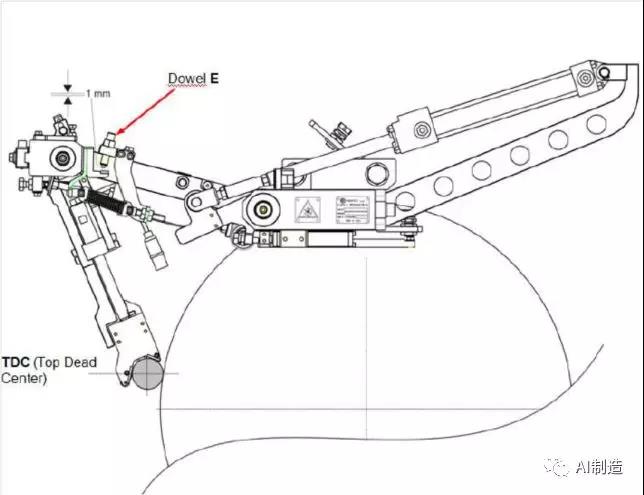
对连杆颈测头随动架进行最高限位的调整
4.主轴颈加工不稳定,尺寸波动大
该问题通常为测量主轴颈时测头随动架随动轨迹存在机械干涉导致(随动路径与加工连杆颈不一样,行程相对短,调整的限位机构也不同),如常见的与喷嘴或工件的侧臂存在干涉时的质量表现。分析确定,测头随动架运动过程中有干涉,对测头随动架进行限位的调整随即得到解决(见下图)。
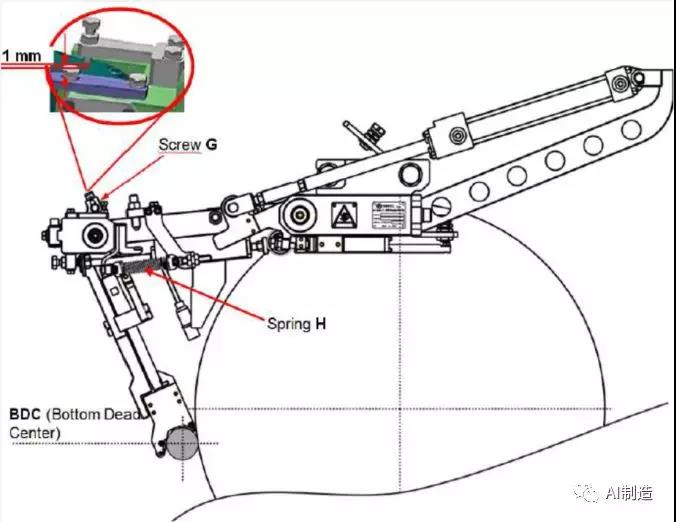
对测头随动架进行限位的调整随
5.所有轴颈尺寸波动大
通过Q-DAS 50件过程能力数据分析,有两台机床的A5/A4直径表现出正弦波动(14um左右),如下图所示,对比另外两台机床发现有两个变化点:两台机床切屑液温度波动比另外两台温度波动大4.5℃;尺寸存在正弦波动,以经验分析受主轴头架跳动影响较大,经过千分表测量发现与头架主轴产生周期性正弦波动一致。
根本原因:头架主轴球笼轴承内轴表面磨损严重;磨削液水温波动大,根据温度补偿公式算出会造成约2um的波动。解决办法:更换顶尖球笼轴承,改进设备冷却系统,减少磨削液温度波动。
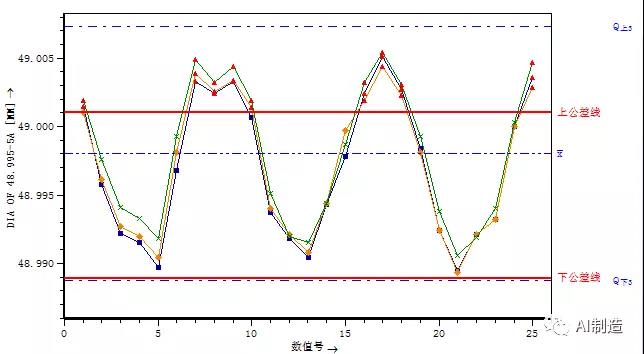
A5/A4轴颈尺寸波动
6.芯轴跳动超差
通过Q-DAS 50件过程能力数据的分析,发现芯轴跳动超差为四台磨床中的一台。通过对机床主夹机构带MASTER测量发现芯轴端跳动大,多次调整未果。进一步分析芯轴端卡爪是否有问题,通过对比其他台磨床发现芯轴夹紧端一卡爪磨损量偏大。确定问题原因:芯轴端卡爪磨损过大,导致加工时候产生径跳。
改进措施:对磨损区域进行轮廓测量,及区域模拟圆弧半径,卡爪半径相差5mm以上,导致定位不准。针对此问题,制定PM更换周期,计划2年更换。
7.某轴颈圆度超差
轴颈圆度偏大为生产中的常见问题,一般检查完机床中心支架抬起度推出度(见下图),确认主夹部分无问题后进行圆度补偿。
造成此问题的原因很多,可通过Q-DAS跟踪各轴颈圆度情况,及时人工干预调整。改进措施:进行圆度补偿,单独编写三坐标圆度测量程序,可节省2/3(约10min)的测量时间。
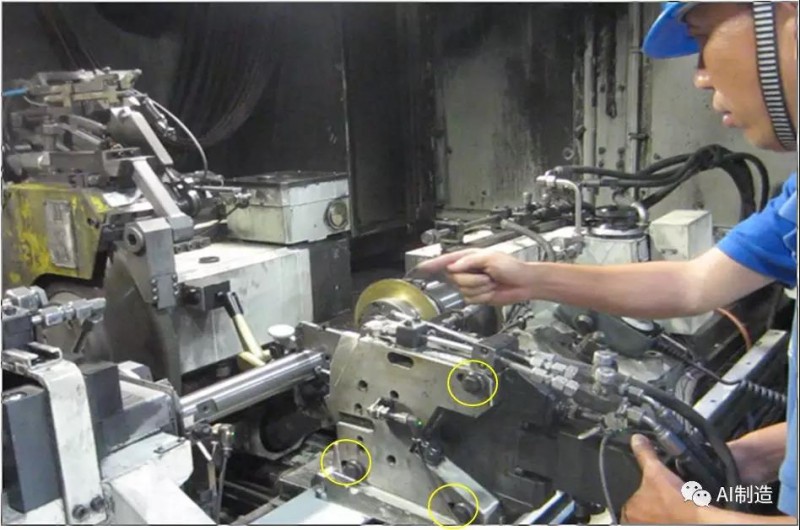
中心支架抬起度推出度检查
结语
曲轴磨削为曲轴生产过程中的重要加工工艺,磨床的稳定性决定了最终下线产品的质量合格率。磨床的高精度和机械结构复杂性,温度、测头机械位置、电气信号、压力和中心支架的抬起度推出度等中的某一个因素(大部分时候为多个因素共同发生)的改变往往会引起大的质量波动,需要花大量时间去查找原因解决问题,成为曲轴生产线的加工瓶颈。本文囊括了曲轴磨床大部分质量超差情况,希望对大家曲轴磨床加工质量改进有所帮助。
编辑推荐
最新资讯
-
数智破局启新篇・生态共生再启程 —
2025-06-27 20:13
-
助力汽车零部件产线智能化升级,西门
2025-06-27 13:59
-
BBA集体转向!放弃全面电动化
2025-06-26 17:32
-
比换柜省钱,比自研省心,西门子Xcel
2025-06-25 15:07
-
采埃孚售后再制造中心乔迁临港 领航
2025-06-25 14:44