一秒解锁大平方线束焊接:超声波扭转焊接技术,探索无限潜能!
众所周知,电池充电时间长是限制电动汽车市场增长的关键因素之一。
为了缩短电动汽车电池的充电时间,电动汽车制造商需要提高充电系统中电路承载高压大电流的能力,这就依赖于大载流能力的电缆来实现。因此大横截面积的线束被广泛应用,用以流通更高的电流,同时还具有良好的散热能力,是提高电动汽车电池充电效率的有效方法。
未来电动车用高压线束载流能力将是现有普通电动汽车电缆的四到五倍。以线束尺寸来说,如果选择铜作为导体材料,所用线束的横截面积就将从50mm²提高到200mm²,甚至更高。
作为一家专注超声波技术与解决方案的瑞士公司泰索迡克。专注工业超声波解决方案五十多年,其推出的扭转焊接的核心技术,让大平方焊接线径达200mm²,变得简单又轻松。
了解用于电动汽车电缆端接的 PowerWheel®
超声波焊接技术是一项成熟的焊接工艺在过去的几十年中一直被用于有色金属焊接上。从 20 世纪 80 年代初以来,超声波金属焊接技术一直在汽车工业占据主导地位,汽车线束制造商是此项技术的主要用户。由于超声波焊接工艺无可匹敌的焊接质量及生产效率,迅速取代了绝大部分汽车品牌制造商原有的的机械压接和电阻焊接工艺。伴随着电动汽车 (EV) 的不断普及,超声波焊接在汽车线束中的应用在过去十年出现了更迅猛的增长。Telsonic创新性的扭矩焊接技术在很大程度上促进了这种迅猛增长,因为它具有优良能力来应对各种挑战,例如焊接尺寸、较小区域焊接、几何形状、接触焊接区域、焊接方向和外围组件的振动效应。
线性焊接技术在大面积线束焊接中的挑战
在焊接大型电缆时,需要克服若干技术障碍:
1、理论上焊接宽度越大,线束和端子的焊接效果越好。但,无论是端子的尺寸还是焊头的尺寸大小都会存在限制的。此外,焊接宽度越大,在焊缝的过渡区域就会出现越多的断线或线表面的压痕。且端子焊接区域的面积、几何形状需要进一步增加或改变。
2、线束截面积越大,超声波系统的电箱功率和焊接力就越大。例如 150 mm² 的线束,理论焊接功率超过 10 kW,焊接压力接近 8000 N。对于如此大的焊接压力及功率, 如果焊接压力不是从焊接面积上方直接施加的话, 焊接系统是无法实现稳定焊接的。在如此高的焊接力下焊头会存在显著的弯曲, 会导致超声波系统的能量无法高效的传递到线束和端子之间,从而达到稳定的焊接质量。
3、传统焊接机只有一个取放料口,因此会对不同设计的连接器和焊接方向造成限制。由于特殊震动模态及焊头设计,Telsonic 的 PowerWheel® 可以允许端子的设计上有更大的自由度,可以解决传统的线性系统无法解决的端子避位及线束取放方向的问题。
4、除开上述技术挑战以外,焊缝的过渡区域的断线率及线损伤也是一个很难克服的技术难点。焊接过程中焊头在会在节点处产生收缩和膨胀的, 收缩和膨胀的位移量及为振幅,焊接过程中线束会和焊头一起运动,从而在线束和端子交接面之间产生擦动/ 摩擦的方式。传统的焊接振幅峰值是在焊头的外端, 即在和焊头接触的焊缝过渡区域。为避免或减少断线率和对线束的损伤, 通常焊头会在焊缝过渡区域设计R 角。所以焊头和焊缝过渡区域是以R 角的形式接触的, 焊接过程中线性系统会在R 角处挤压和推动线束, 从而导致更大的断线及线束挤压损伤的可能。但是PowerWheel® 矩焊接技术的震动模态是钟摆式的,得益于此特殊震动模态焊头的R 角度和焊缝过渡区域的线束是以钟摆式弧形的振幅和挤压和推动线束,所以对线束的损伤会更小, 断线率更低,焊接品质更好。
Telsonic 的扭矩焊接技术克服了线性焊接技术中的诸多限制,创造了在过去十年之前被认为无法实现或达不到质量标准的突破性应用场景。扭矩焊接技术越来越多地被汽车制造商指定用于电动汽车的减重、电池封装、电缆到端子连接、母线、电池制造和电力电子系统。电动汽车电池的更高功率和更快充电需要更大的电池电缆,有时需要非常规的连接器。Telsonic 的PowerWheel® 扭矩焊接技术,为汽车行业的高质量及高可靠性装配要求提供了可靠的技术解决方案。
图:破损或截断的股线
线性和扭矩焊接的工作原理
如图展示了线性焊接的基本工作原理,对于了解传统线性焊接与 Telsonic 的创新PowerWheel® 焊接技术之间的差异至关重要。
● 术语“振幅”描述了焊头运动的程度——膨胀和收缩。
● 振幅与焊缝交接面的摩擦效果相关。这种运动与压力结合,完成焊接工艺。
线性和扭矩焊接之间的主要区别(表1)
线束和端子焊接PowerWheel® 技术
PowerWheel® 焊接技术使用创新理念振动焊头,其采用扭转方式激发。可实现高达 7.2 kW 与 14.4 kW 焊接功率,不同的应用可以选择不同的功率系统。借助扭矩焊技术可焊接更大尺寸的焊缝、母线、3D 端子、更多几何形状、大避位空间以及需要低振影响的应用。这大大扩展了超声波的应用范围。可以实现以前传统线性焊接无法实现的超声波焊接应用。
PowerWheel® 焊接技术的优势
相比线性系统,焊接宽度可收窄30%, 允许更大的焊后线高。这样一来,可明显节省定位组件所需的材料与空间。另一优势在于能焊接更厚的端子并达到非常的好的结合力。焊接过程中焊头以钟摆式的往复运动模态来产生焊接。因此,振幅始终位于焊接区域中心,能量传导聚焦于焊接区。由于直接对焊接交接面施力且焊缝的过渡区域的振幅相对较小,所以焊接机可以实现更大面积线束的焊接,且又能减少对绞线的损坏(即使有)。由于焊头的扭转运动,焊接区域周围几乎没有由于超声波而产生的负载。因此,扭转工艺特别适用于焊接区域外的振动可能造成损坏的敏感应用。振动沿电缆轴传播的速度缓慢,使得 PowerWheel® 更适合较短的电缆两头超声波焊接的应用。通常情况下,在短线束首尾两头的端子焊接过程中,因第二次焊接振动可能会削弱第一次焊接。2011 年,利用 PowerWheel® 焊接技术对直径 50 mm² 长度180mm 线束进行了研究测试。结果表明,在线束两端的焊接强度方面没有发现差异。此外,机械强度比采用传统线性工艺达到的强度高出约 30 %。
Telsonic 的 PowerWheel® 标准焊头专门针对铜线和铝线优化,满足 OEM 和线缆制造商的要求,并符合 USCAR 38 标准(超声波焊接电缆端子的性能规范)。与传统超声波焊接一样,PowerWheel® 系统还可以用于焊接有色金属。
PowerWheel® 焊接优势一览
● 创新性的钟摆式振动模态;
更少的断线率, 焊缝的过渡区域更小的线损伤;
焊接面振幅无衰减,更好的焊接面外观品质,减少因过焊导致的发黑及色差现象;
特殊振动模态,附带损伤小,振动更柔和;
● 超强焊接能力中间施力, 效率高
确保线束品质及外观前提下, 可实现更大的接强度, 实现更好的CPK
最大14.4Kw 及8000N 焊接力,可实现最大 160 mm2 的铜线/ 最大200 mm2 的铝线
可实现更大焊线高度, 从而实现更小焊接宽度,约30 %
● 超大避位空间三面可操作及上下料;
可焊接特殊避位空间产品
方便维护
● 高效率
水冷系统, 短焊接时间
高OEE
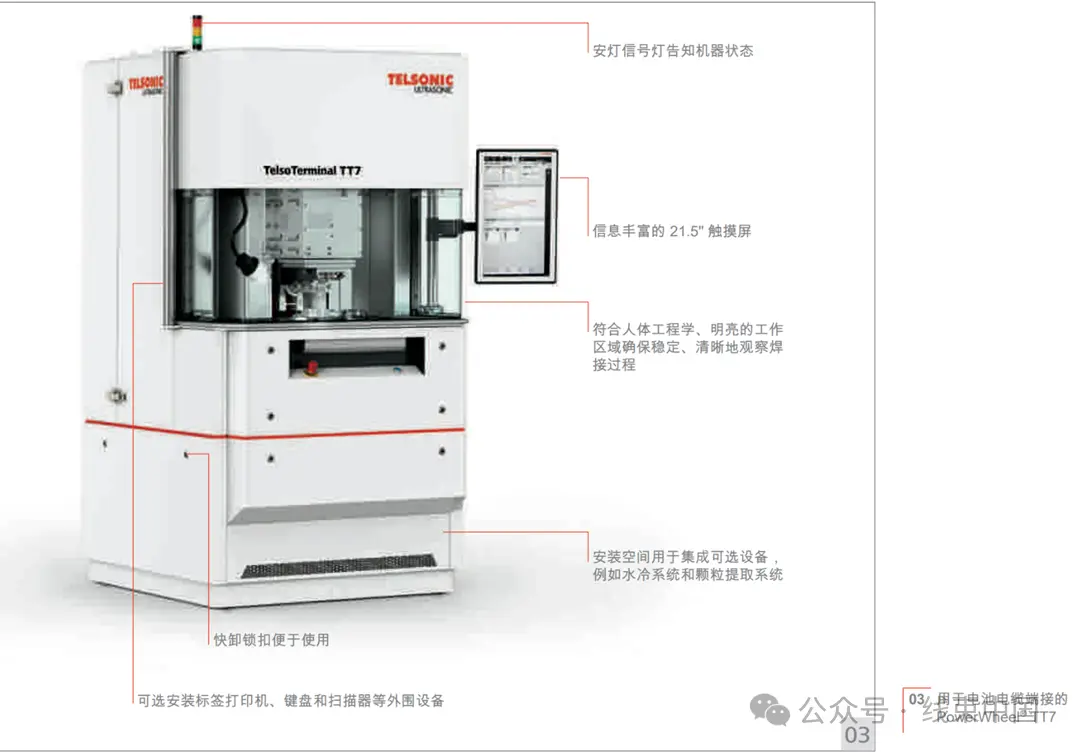
必要设备
与传统超声波焊接一样,超声波扭转焊接机具有电箱、换能器和焊头。然而,与传统系统相比,焊头不会纵向摆动而是扭转摆动,这就是减少部件应力的方式。同时,高达 14.4 kW 的超声波输出功率可以通过焊头传递。因此,电箱在扭转过程中形成的电振动会传递到 PZT 振动变压器中,通过压电效应转换为机械振动。通过在 SONIQTWIST® 振动头中以特定顺序装配声学组件, 可以将线性产生的振动转换为扭转运动。
全新 PowerWheel® Telso®Terminal TT7 超声波金属焊接系统用途广泛,适用于多种应用,包括电缆装配和电池生产。其应用包括采用多样化设计焊接的高压线、电池端子、3D 端子、母线和电池接头。
图:PowerWheel® TT7 焊接区域
凭借紧凑现代的设计,这款模块化系统带来一系列优势,包括使用数字化技术实现精准流程控制、标准接口可供数字联网和轻松集成至自动化系统。这款新型系统也标配整合新一代 Telsonic 成熟的 PowerWheel® 焊接技术,针对横截面高达 200 mm2 金属线缆焊接,可确保优良可靠性和精准的流程控制。
PowerWheel® 焊接技术 – 实际应用案例
1、焊缝宽度小,不损伤细小的电缆股线
在图所示的应用中,高质量的 35 mm2 ProEVTM 电缆焊接到Rosenberger 连接器上,它为这种尺寸的线缆提供了有限的空间。由于高度的灵活性,ProEVTM 电缆是这种应用的理想之选。然而,10 mm 而非11 mm 的可用焊缝宽度和柔性细线带来了一些挑战。这需要一种能够在较小空间上提供焊缝的解决方案,在这样的空间内可以实现所需的焊缝压实,而不会损伤焊缝过渡区的细线。
图:ProEVTM 电缆由隶属于 ECI 公司的 Promark Electronics 生产,焊接到 Rosenberger 公头镀银连接器上
解决方案:
利用扭转 PowerWheel® 焊接技术系统,在柔性 ProEVTM 35 mm2 电缆和10 mm 宽的连接器之间实现优质焊接。工具的设计和配置必须确保补偿因延续使用的连接器半径而导致的有限夹紧力。这种工具设计和配置解决方案可提供足够的焊接能量,从而实现优质焊接。
2、大避位空间要求的应用
90° SQ4 端子由 C15100 铜合金制成,焊接区域无电镀。此应用需要焊接 35 mm² 和 50 mm² 的电缆。用于 50 mm² 的端子片宽度从 13 mm 改为18mm,以适应 15 mm 的焊接宽度。当使用 15 mm 焊头时,这也可以在端子每一头实现 1.5 mm 的夹持宽度。但是,约 17 mm 的连接器高度对传统纵向超声波焊接工艺的焊头间隙提出了挑战。在物理上无法设计出能够留空17 mm 高度且仍高效提供所需 20 kHz 频率的线性焊头。
图:90° SQ4 端子焊接到 50 mm2 电缆
解决方案:
利用扭转 PowerWheel® 系统留空连接器高度,并通过 SQ4 端子为 35 mm2 及 50 mm2 电缆实现优质焊接。通过焊头定向可以实现与 90° 端子保持间隙,并提供充足的焊接能量来实现优质焊接,而且得益于温和的振动,并不会影响过渡区域内的细线或连接器本身。
3、更多具有挑战性的应用示例
以下是 Telsonic PowerWheel®系统可以解决的有关在绞合线上超声波焊接端子的一些额外应用和挑战:
① 含管状电缆接线片的高压电缆套件 –焊接被证明可以与 PowerWheel®配合。
② 屏蔽电缆 – 当连接器的表面积受到限制时,可以在较小的焊接区域内焊接可达200 mm² 的大型电缆。
③ 短电缆两端焊接 – 通过线性焊接焊接短电缆的两端可能使第二次焊接振动破坏第一次焊接。扭转焊接的振动效应小得多,因此,它可以焊接短至4 英寸的电缆。
④ 3D 端子 – PowerWheel® 提供更便于接近焊接区域的优势。
⑤ 配备 Al 电缆的大功率锁盒端子– Royal Power Solutions 端子 SQ4,在这种情况下约 17 mm 高。PowerWheel® 是接近焊接区域的方法。
⑥ 端子两股编织线 – 编织线具有非常细的股线,如果不用更温和的扭转振动,可能会有更多的断线。
创新和迅猛增长的电动汽车市场需要全新、正在开发的解决方案来应对未来的挑战。扭矩焊接已成为业界重要的接合工艺。除了用于电池电缆端接各种连接器的解决方案外,这项技术还提供用于电动汽车重量控制、电池封装、母线、电池制造和电力电子系统的焊接解决方案。应用能力的扩展已经超出了之前的想象。随着产品设计师和工艺工程师不断熟悉扭转焊接工艺及其能力,这项技术将助推电动汽车行业达到更高的高度。
*以上文字内容及配图均由泰索迡克提供
- 下一篇:“绿养无忧”——比亚迪叉车助力饲料行业“降本增效”!
- 上一篇:汽车侧围回弹补偿分析
-
汽车车身焊接技术任务
2025-05-29 -
镁合金汽车焊接技术攻坚
2025-05-29 -
熟背铝合金焊接口诀,秒杀一切焊接难题
2024-07-25 -
激光焊接技术
2024-07-10
编辑推荐
最新资讯
-
京东工业发布汽车等九大行业场景采购
2025-08-26 18:11
-
制造现场推动节能革新,电装稳步迈向
2025-08-25 14:04
-
携手共赴“智”造未来!埃马克推动大
2025-08-22 19:41
-
伦福德机脚-汽车平稳行驶的守护者
2025-08-19 16:38
-
比亚迪叉车:新能源时代的绿色智能引
2025-08-19 14:37