轿车白车身冲压件VAVE降本方案的策略研究
2018-09-13 10:20:20· 来源:高硕遥 锻造与冲压
研究表明,工艺设计阶段决定了产品制造成本的70% ~ 80%,而设计本身的成本仅占产品总成本的10%。在材料价格不断上涨和汽车市场竞争日趋激烈的今天,如何在设计阶段多维度的完成轿车白车身冲压件V A V E 降本方案有着至关重要的意义。VA
研究表明,工艺设计阶段决定了产品制造成本的70% ~ 80%,而设计本身的成本仅占产品总成本的10%。在材料价格不断上涨和汽车市场竞争日趋激烈的今天,如何在设计阶段多维度的完成轿车白车身冲压件V A V E 降本方案有着至关重要的意义。
VA(Value analysis)是对完成品实施降低成本,扩大利润的活动。VE(Value engineering)是通过产品工艺开发期间优化产品和工艺、完成目标成本的活动。随着环保和能源意识的增强,市场竞争的加剧,各大汽车厂的成本意识也越来越强,降成本活动自设计之初到量产后,无时无刻不在进行。研究表明,工艺设计阶段决定了产品制造成本的70% ~ 80%,而设计本身的成本仅占产品总成本的10%。在材料价格不断上涨和汽车市场竞争日趋激烈的今天,如何在设计阶段多维度的完成轿车白车身冲压件VAVE 降本方案有着至关重要的意义。本文从优化零件设计、创新冲压工艺和材料管理角度详细介绍轿车白车身冲压件VAVE 降本方案。
优化零件设计
创新冲压工艺的成功应用要以合适的零件设计为前提,同步工程期间,零件设计要兼顾满足功能和优化成本的要求,通过优化零件材料和零件形状更好地实现降成本的目的。
零件材料设计
整车轻量化是目前汽车工业的发展方向,特别是车身骨架件的汽车轻量化设计,是整车轻量化的关键。采用高强钢,特别是超高强度钢板,是目前车身轻量化最经济、有效的方法。欧日等先进汽车制造企业高强钢零件的应用比例超过了60%,高强钢的普及应用不仅是汽车轻量化的重要手段,也是降成本的需求。
零件形状设计
通过对产品边界进行合理的“合并、拆分”或“做方、做圆”使产品尽可能规整,减少局部凸出,如果局部凸出,后续再做工艺补充部分时,需要保证边界过渡平滑缓和或进料均匀,从而增加较多的过渡部分。因此需要对产品零件“非圆、非方”部位进行合并,既减少了零件的数量,也减少了对应的模具、检具以及工装夹具的投资费用。
图1 所示的轿车某车型侧围加强板,原始设计方案由3 块TRIP600 材质1.6mm 厚板料与1 块TRIP600材质1.4mm 厚板料拼焊而成。制件前期工艺评审中,从材料利用率、拼焊加工费用、废品率、余废料利用和冲压投资成本等几方面考虑,将产品拼焊焊缝取消,料厚统一为1.6mm,并提出产品门洞废料利用方案,应用于轿车同车型侧围内板。该侧围加强板经过前期综合评审、分析降成本29.36×2=58.72 元/ 车,模具投资预算降低173.63 万元。
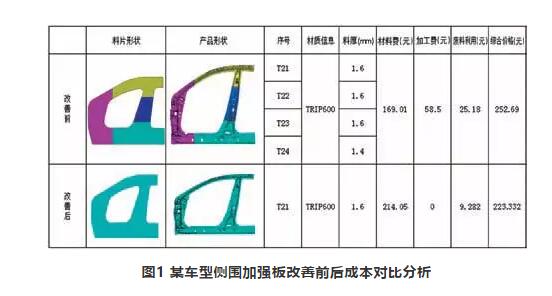
创新冲压工艺
浅拉延
拉延是常用的冲压工序,优点是提高材料的塑性并能生产稳定。但传统的深拉延工序需要较大的工艺补充面,工艺补充面不是产品面,是工艺延伸面,这部分在后序工序中被切除,造成较大的材料损失。因此,为了显著提高材料利用率,必须考虑将凸模轮廓线设计在零件之内,用零件的部分形状做压料面,这种拉延形式称作浅拉延。
图2 是采用浅拉延工艺的中地板,优化后的凸模轮廓线设计在零件产品上,用零件的法兰边做压料面,减小了拉延深度,非常明显地缩小了工艺补充面,材料利用率由64.5% 提升至83.9%,极大地提高了材料利用率。
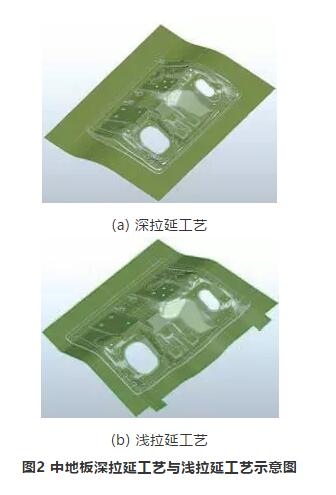
对件合模拉延
白车身上存在着大量的左右对称件,通过对件合模共用中间部分的工艺补充面,从而减少单件的工艺补充面,提高材料利用率。但如果受到生产现场的工艺设备条件限制,导致部分工序无法进行,则使用一模双腔的合模方式,同样可以减少一套模具的费用。图3 所示的左/ 右侧C 柱加强板,优先考虑采用左右件对件合模拉延,提高材料利用率的同时可以提高生产效率。
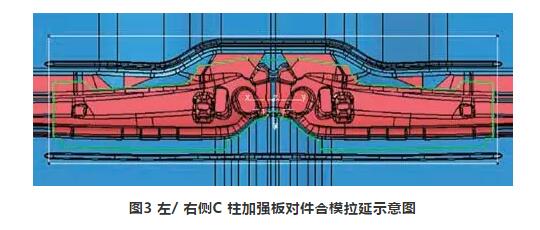
成形代拉延
成形工艺与拉延工艺相比,成形工艺没有工艺补充面,成形前的落料片可以进行排样优化,因而能极大地提高材料利用率。图4 是左/ 右连接板,如果采用拉延工艺,则材料利用率仅为51.1%;而采用成形工艺,零件材料利用率提升至64.58%,且模具套数由原来的5 套减少为4 套。可见,成形工艺不仅能大幅提升零件的材料利用率,而且能有效减少模具套数,节约开发车身成本。
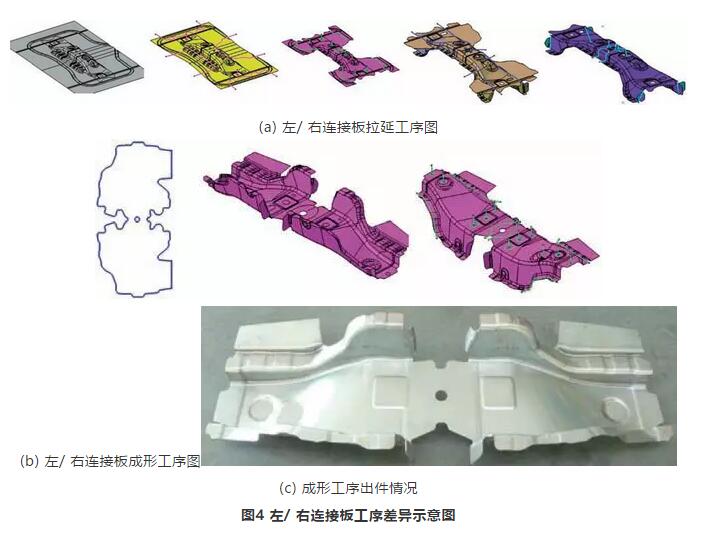
套裁冲压
VA(Value analysis)是对完成品实施降低成本,扩大利润的活动。VE(Value engineering)是通过产品工艺开发期间优化产品和工艺、完成目标成本的活动。随着环保和能源意识的增强,市场竞争的加剧,各大汽车厂的成本意识也越来越强,降成本活动自设计之初到量产后,无时无刻不在进行。研究表明,工艺设计阶段决定了产品制造成本的70% ~ 80%,而设计本身的成本仅占产品总成本的10%。在材料价格不断上涨和汽车市场竞争日趋激烈的今天,如何在设计阶段多维度的完成轿车白车身冲压件VAVE 降本方案有着至关重要的意义。本文从优化零件设计、创新冲压工艺和材料管理角度详细介绍轿车白车身冲压件VAVE 降本方案。
优化零件设计
创新冲压工艺的成功应用要以合适的零件设计为前提,同步工程期间,零件设计要兼顾满足功能和优化成本的要求,通过优化零件材料和零件形状更好地实现降成本的目的。
零件材料设计
整车轻量化是目前汽车工业的发展方向,特别是车身骨架件的汽车轻量化设计,是整车轻量化的关键。采用高强钢,特别是超高强度钢板,是目前车身轻量化最经济、有效的方法。欧日等先进汽车制造企业高强钢零件的应用比例超过了60%,高强钢的普及应用不仅是汽车轻量化的重要手段,也是降成本的需求。
零件形状设计
通过对产品边界进行合理的“合并、拆分”或“做方、做圆”使产品尽可能规整,减少局部凸出,如果局部凸出,后续再做工艺补充部分时,需要保证边界过渡平滑缓和或进料均匀,从而增加较多的过渡部分。因此需要对产品零件“非圆、非方”部位进行合并,既减少了零件的数量,也减少了对应的模具、检具以及工装夹具的投资费用。
图1 所示的轿车某车型侧围加强板,原始设计方案由3 块TRIP600 材质1.6mm 厚板料与1 块TRIP600材质1.4mm 厚板料拼焊而成。制件前期工艺评审中,从材料利用率、拼焊加工费用、废品率、余废料利用和冲压投资成本等几方面考虑,将产品拼焊焊缝取消,料厚统一为1.6mm,并提出产品门洞废料利用方案,应用于轿车同车型侧围内板。该侧围加强板经过前期综合评审、分析降成本29.36×2=58.72 元/ 车,模具投资预算降低173.63 万元。
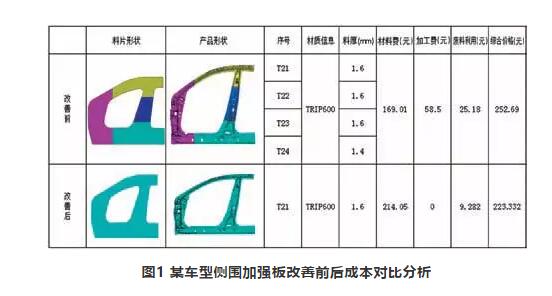
创新冲压工艺
浅拉延
拉延是常用的冲压工序,优点是提高材料的塑性并能生产稳定。但传统的深拉延工序需要较大的工艺补充面,工艺补充面不是产品面,是工艺延伸面,这部分在后序工序中被切除,造成较大的材料损失。因此,为了显著提高材料利用率,必须考虑将凸模轮廓线设计在零件之内,用零件的部分形状做压料面,这种拉延形式称作浅拉延。
图2 是采用浅拉延工艺的中地板,优化后的凸模轮廓线设计在零件产品上,用零件的法兰边做压料面,减小了拉延深度,非常明显地缩小了工艺补充面,材料利用率由64.5% 提升至83.9%,极大地提高了材料利用率。
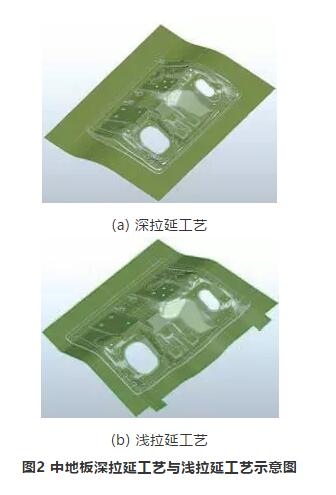
对件合模拉延
白车身上存在着大量的左右对称件,通过对件合模共用中间部分的工艺补充面,从而减少单件的工艺补充面,提高材料利用率。但如果受到生产现场的工艺设备条件限制,导致部分工序无法进行,则使用一模双腔的合模方式,同样可以减少一套模具的费用。图3 所示的左/ 右侧C 柱加强板,优先考虑采用左右件对件合模拉延,提高材料利用率的同时可以提高生产效率。
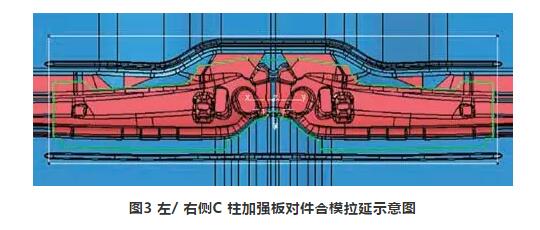
成形代拉延
成形工艺与拉延工艺相比,成形工艺没有工艺补充面,成形前的落料片可以进行排样优化,因而能极大地提高材料利用率。图4 是左/ 右连接板,如果采用拉延工艺,则材料利用率仅为51.1%;而采用成形工艺,零件材料利用率提升至64.58%,且模具套数由原来的5 套减少为4 套。可见,成形工艺不仅能大幅提升零件的材料利用率,而且能有效减少模具套数,节约开发车身成本。
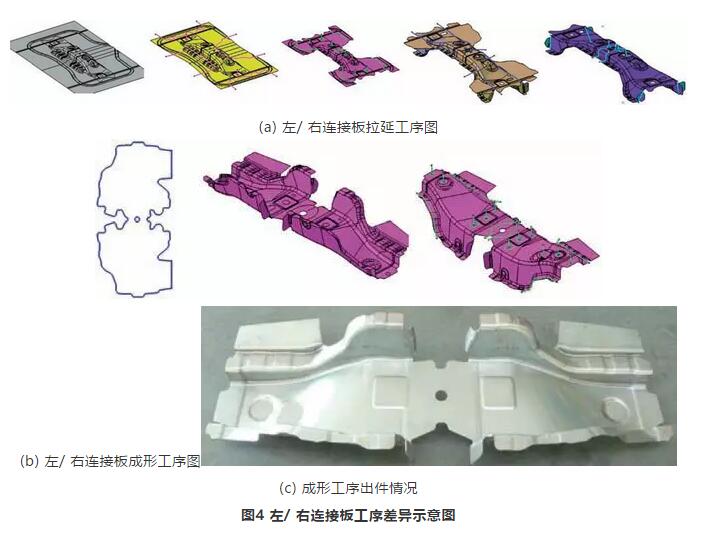
套裁冲压
举报 0
收藏 0
分享 146
-
乘用车金属冲压
2025-05-29 -
冲压技术在电机叠片制造的应用
2024-09-06 -
车身零部件包边质量控制要点
2024-09-05 -
轻量化技术——热汽胀形工艺技术解析
2024-09-04
最新资讯
-
旭化成旗下宾霸品牌重磅亮相2025上海
2025-09-01 16:52
-
中国车企服务出海先行者:新央企新长
2025-08-29 16:13
-
携手共赴“智”造未来!埃马克推动大
2025-08-27 18:12
-
京东工业发布汽车等九大行业场景采购
2025-08-26 18:11
-
制造现场推动节能革新,电装稳步迈向
2025-08-25 14:04