轴承座锻造工艺与模具设计
2018-09-13 10:08:29· 来源:轴承座锻造工艺与模具设计
本方介绍了一种薄形锻件的锻造工艺及模具设计,解决锻件产品合格率和材料利用率低等各种技术问题,降低生产制造成本。利用金属塑性成形仿真软件D E F O R M -3D,对工艺进行仿真分析,仿真结果有效的验证了工艺方案。用基于模拟验证的工
本方介绍了一种薄形锻件的锻造工艺及模具设计,解决锻件产品合格率和材料利用率低等各种技术问题,降低生产制造成本。利用金属塑性成形仿真软件D E F O R M -3D,对工艺进行仿真分析,仿真结果有效的验证了工艺方案。用基于模拟验证的工艺和设计的模具进行生产试制,轴承座锻件产品的尺寸及性能完全达到了设计要求。
伴随着我国城市化的快速发展,许多城市开始建立城市轻轨线路,以缓解出现的交通拥堵现象。国内某公司与加拿大庞巴迪正在合作研究开发速度更快、效率更高的轻轨机车。轴承座(图1)属于其中有代表性的锻件,投影面积大而锻件大部分厚度非常薄。轴承座在锻造生产过程中会存在各种技术问题,如头尾两端成形困难及切边变形等。通过常规的锻造工艺和模具设计很难实现低成本和高合格率的技术要求。本文介绍了一种锻造成形工艺和模具设计,成功解决了薄形锻件难成形的锻造工艺难题。
轴承座的锻造工艺性分析
我公司承制的某型号轴承座(图1),锻件重11.6kg,材质为16MnDR。轴承座为精密模锻件,尺寸精度要求较高、机械加工余量少,仅在锻件背弧和内孔安装轴承部位有2.5mm 机加余量,其他部位均为非加工面。
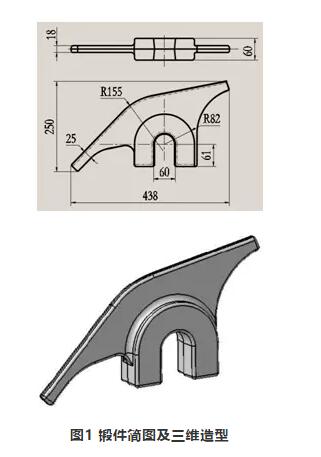
⑴产品特点。
锻件投影面大、腹板薄、截面变化大。锻件的包容体尺寸为437.2mm×248.9mm×60mm,投影面积达到751.20cm2。整个锻件外形结构酷似“腕龙”,从头到脊椎再到尾部长达510mm,厚度仅为18mm。“腕龙”的脚和肚子部位厚度从18mm 急剧变化到60mm。头部和尾巴两端截面面积从450mm2 变化到化到542mm2,中间最大截面面积11206mm2。
⑵锻造难点。
在锻造成形过程中,由于腹部薄,投影面过大,金属流动过程中冷却速度过快,导致金属流动困难,型腔不易充满,尤其是头尾两端距离远容易出现缺肉现象。
轴承座主轴方向上截面形状变化剧烈,容易出现充不满,折叠以及利用率低等问题。需合理选择坯料规格和设计模具结构,合理分配坯料,降低锻件成形力,提高锻件合格率和材料利用率。
⑶锻造工艺流程。
下料→中频感应加热→自由锻出坯→模锻(弯曲- 模锻)→热切边→油压机热校正→抛丸→热处理(正火)→抛丸→终检(机械性能、硬度、金相、探伤等)。
模具设计
设备吨位的确定
摩擦压力机的锻造成形力计算可按下式计算:
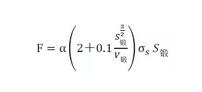
式中:α—与模锻方式有关的系数,开式模锻该值为4;F—螺旋压力机公称压力(N);S 锻—包括毛边在内的锻件在分模面上的投影面积(mm2);V 锻—锻件体积(mm3);σs—锻件在终锻温度下的屈服极限(MPa),通常可用同温度下的强度极限σb 代替。
上式适用于打击一次成形所需的设备吨位,若采用2 ~ 3 次打击成形,则应按计算值减少1/2。
σs 按终锻温度900 ℃ 取值55MPa;S 锻=76820mm2;V 锻≈ 1480500mm3;把参数代入公式,经计算,F ≈ 41206kN。锻件在摩擦压力机上需进行弯曲一锤和模锻两锤成形,因此锻造成形力F 实际=F/2=20603kN<25000kN,可选用2500t 摩擦压力机。
模具设计
⑴滚挤模设计。
锻件的截面经过简化,将自由锻的坯料的外形优化成类似纺锤体形状,中间坯料直径为φ 120mm,两头直径最小为φ 32mm,总长480mm。设计了如图2 所示的滚挤模,保证坯料的一致性和出坯速度。
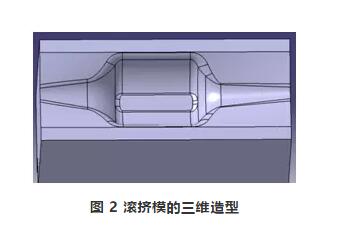
⑵弯曲模设计。
锻件呈“腕龙”形状,头尾脊线角度为145°。弯曲模的形状和角度尺寸根据热锻件的脊线变化进行设计,弯曲模在锻模的侧边。将自由锻制好的坯料压扁后放入弯曲模,弯曲后的坯料可直接放入终锻模膛。
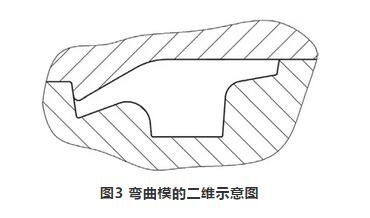
图3 弯曲模的二维示意图
⑶终锻模设计。
轴承座产品的开发,终锻锻模设计需要解决主要的锻造难点为锻件的头尾两端充满。
1) 锻件终锻模的型腔尺寸按锻件图加放收缩率即可。
2) 锻件的腹板投影面大且厚度薄,反映在模具上就是模膛宽而且浅,按常规的设计,料容易从型腔跑到仓部,造成材料利用率低下。按图4 所示设计阻力墙结构,使得坯料在模锻初始阶段变形流动受到四周阻力墙侧壁的限制,提高坯料向外流动的阻力,迫使金属往两端流动充满模膛。
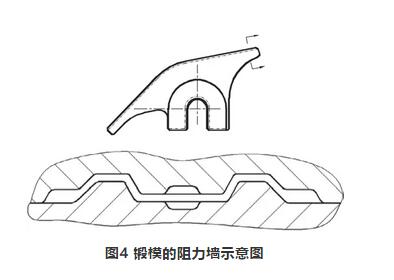
模拟分析
利用金属塑性成形仿真软件DEFORM-3D,对工艺和模具进行仿真分析。将φ 115mm×180mm 的坯料加热到1200℃,经过第一工位锻造成所需的毛坯经弯曲后,放入终锻模具型腔中,通过上下模的挤压成形。模拟初始条件设置如下:材料为AISI-1025,模具材料为AISI-H-13;坯料温度为1160℃;设备选择2500t 摩擦压力机。对象属性:坯料为塑性体,模具为刚性体;摩擦系数为0.3;热传递系数:坯料与空气换热系数取为0.02N·(mm·s·℃ )-1,模具与坯料之间的热传递系数取为11N·(mm·s·℃ )-1,模具与空气换热忽略不计。
图5 为轴承座成形的速度场模拟结果,锻件两端的速度场显示坯料在受到阻力墙侧壁的限制后,向两端的流动速度增大。锻件的充满情况良好,模具结构设计满足设计要求。
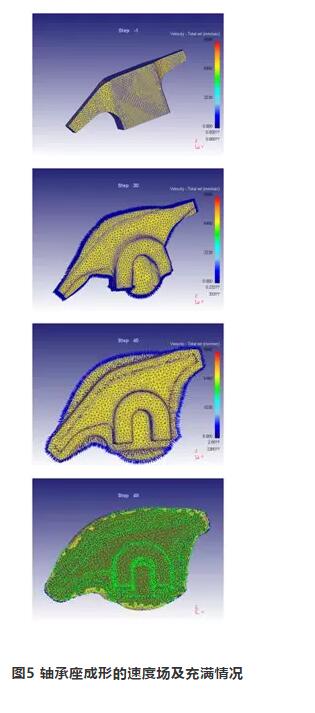
工艺试制
根据模拟结果,采用1t 自由锤锻和2500t 摩擦压力机联合锻造生产工艺。棒料经过自由锻滚挤后压扁,在弯曲模型腔内经过一锤弯曲,终锻模型腔两锤锻打成功。切边后进行油压机热校正。
锻造轴承座时采用φ 115mm×180mm 圆棒料,下料重量14.6kg,材料利用率达到79.5%,产品合格率达到99% 以上。模具投入使用后,该锻件已经进入批量生产验证,尺寸满足图纸要求,锻件精度高,质量稳定。图6 为切边工序结束后的产品实物和锻件正火后的显微组织(细块状的铁素体+ 珠光体)照片。表1 为锻件的机械性能。
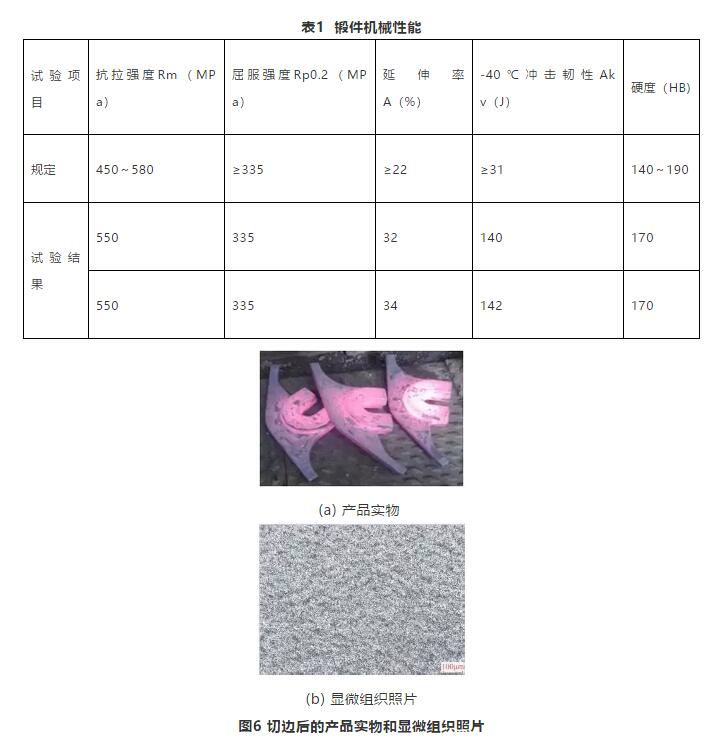
锻件开发初期出现了一些质量问题,主要缺陷是锻件未充满,主要发生在锻件两端和叉口部位(图7)。前期按照常规设计方案设计桥仓部,造成了材料利用率低和合格率较低的情况。通过设计优化,设计了阻力墙结构的模具,极大的提高了产品合格率和材料利用率。
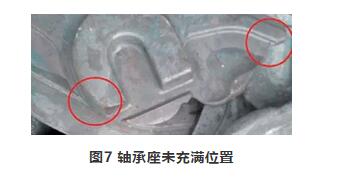
结论
⑴采用自由锻滚挤和模锻相结合的工艺可一火成形精度要求高的轴承座锻件;
⑵采用数值模拟方法可以有效辅助锻造工艺的设计,提高设计效率,提高产品开发成功率;
⑶采用阻力坎的桥部设计,锻件成形效果好,未出现充不满、穿筋等缺陷,尺寸达到要求,质量稳定。
——本文选自《锻造与冲压》2018年第17期
伴随着我国城市化的快速发展,许多城市开始建立城市轻轨线路,以缓解出现的交通拥堵现象。国内某公司与加拿大庞巴迪正在合作研究开发速度更快、效率更高的轻轨机车。轴承座(图1)属于其中有代表性的锻件,投影面积大而锻件大部分厚度非常薄。轴承座在锻造生产过程中会存在各种技术问题,如头尾两端成形困难及切边变形等。通过常规的锻造工艺和模具设计很难实现低成本和高合格率的技术要求。本文介绍了一种锻造成形工艺和模具设计,成功解决了薄形锻件难成形的锻造工艺难题。
轴承座的锻造工艺性分析
我公司承制的某型号轴承座(图1),锻件重11.6kg,材质为16MnDR。轴承座为精密模锻件,尺寸精度要求较高、机械加工余量少,仅在锻件背弧和内孔安装轴承部位有2.5mm 机加余量,其他部位均为非加工面。
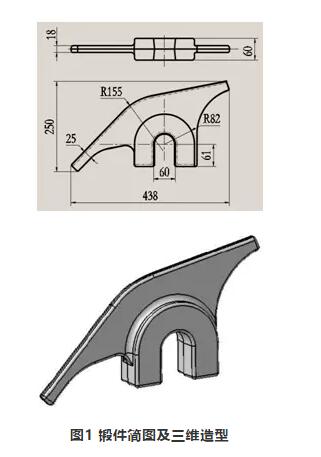
⑴产品特点。
锻件投影面大、腹板薄、截面变化大。锻件的包容体尺寸为437.2mm×248.9mm×60mm,投影面积达到751.20cm2。整个锻件外形结构酷似“腕龙”,从头到脊椎再到尾部长达510mm,厚度仅为18mm。“腕龙”的脚和肚子部位厚度从18mm 急剧变化到60mm。头部和尾巴两端截面面积从450mm2 变化到化到542mm2,中间最大截面面积11206mm2。
⑵锻造难点。
在锻造成形过程中,由于腹部薄,投影面过大,金属流动过程中冷却速度过快,导致金属流动困难,型腔不易充满,尤其是头尾两端距离远容易出现缺肉现象。
轴承座主轴方向上截面形状变化剧烈,容易出现充不满,折叠以及利用率低等问题。需合理选择坯料规格和设计模具结构,合理分配坯料,降低锻件成形力,提高锻件合格率和材料利用率。
⑶锻造工艺流程。
下料→中频感应加热→自由锻出坯→模锻(弯曲- 模锻)→热切边→油压机热校正→抛丸→热处理(正火)→抛丸→终检(机械性能、硬度、金相、探伤等)。
模具设计
设备吨位的确定
摩擦压力机的锻造成形力计算可按下式计算:
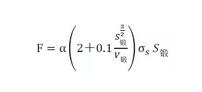
式中:α—与模锻方式有关的系数,开式模锻该值为4;F—螺旋压力机公称压力(N);S 锻—包括毛边在内的锻件在分模面上的投影面积(mm2);V 锻—锻件体积(mm3);σs—锻件在终锻温度下的屈服极限(MPa),通常可用同温度下的强度极限σb 代替。
上式适用于打击一次成形所需的设备吨位,若采用2 ~ 3 次打击成形,则应按计算值减少1/2。
σs 按终锻温度900 ℃ 取值55MPa;S 锻=76820mm2;V 锻≈ 1480500mm3;把参数代入公式,经计算,F ≈ 41206kN。锻件在摩擦压力机上需进行弯曲一锤和模锻两锤成形,因此锻造成形力F 实际=F/2=20603kN<25000kN,可选用2500t 摩擦压力机。
模具设计
⑴滚挤模设计。
锻件的截面经过简化,将自由锻的坯料的外形优化成类似纺锤体形状,中间坯料直径为φ 120mm,两头直径最小为φ 32mm,总长480mm。设计了如图2 所示的滚挤模,保证坯料的一致性和出坯速度。
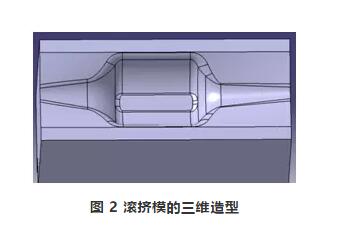
⑵弯曲模设计。
锻件呈“腕龙”形状,头尾脊线角度为145°。弯曲模的形状和角度尺寸根据热锻件的脊线变化进行设计,弯曲模在锻模的侧边。将自由锻制好的坯料压扁后放入弯曲模,弯曲后的坯料可直接放入终锻模膛。
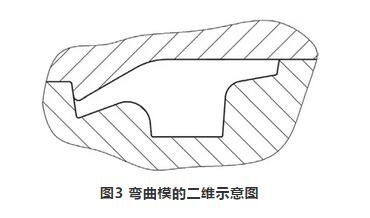
图3 弯曲模的二维示意图
⑶终锻模设计。
轴承座产品的开发,终锻锻模设计需要解决主要的锻造难点为锻件的头尾两端充满。
1) 锻件终锻模的型腔尺寸按锻件图加放收缩率即可。
2) 锻件的腹板投影面大且厚度薄,反映在模具上就是模膛宽而且浅,按常规的设计,料容易从型腔跑到仓部,造成材料利用率低下。按图4 所示设计阻力墙结构,使得坯料在模锻初始阶段变形流动受到四周阻力墙侧壁的限制,提高坯料向外流动的阻力,迫使金属往两端流动充满模膛。
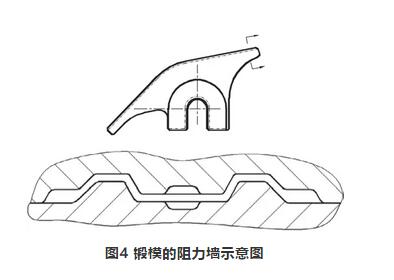
模拟分析
利用金属塑性成形仿真软件DEFORM-3D,对工艺和模具进行仿真分析。将φ 115mm×180mm 的坯料加热到1200℃,经过第一工位锻造成所需的毛坯经弯曲后,放入终锻模具型腔中,通过上下模的挤压成形。模拟初始条件设置如下:材料为AISI-1025,模具材料为AISI-H-13;坯料温度为1160℃;设备选择2500t 摩擦压力机。对象属性:坯料为塑性体,模具为刚性体;摩擦系数为0.3;热传递系数:坯料与空气换热系数取为0.02N·(mm·s·℃ )-1,模具与坯料之间的热传递系数取为11N·(mm·s·℃ )-1,模具与空气换热忽略不计。
图5 为轴承座成形的速度场模拟结果,锻件两端的速度场显示坯料在受到阻力墙侧壁的限制后,向两端的流动速度增大。锻件的充满情况良好,模具结构设计满足设计要求。
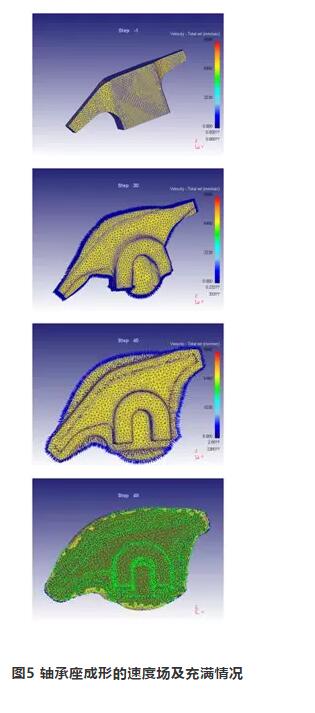
工艺试制
根据模拟结果,采用1t 自由锤锻和2500t 摩擦压力机联合锻造生产工艺。棒料经过自由锻滚挤后压扁,在弯曲模型腔内经过一锤弯曲,终锻模型腔两锤锻打成功。切边后进行油压机热校正。
锻造轴承座时采用φ 115mm×180mm 圆棒料,下料重量14.6kg,材料利用率达到79.5%,产品合格率达到99% 以上。模具投入使用后,该锻件已经进入批量生产验证,尺寸满足图纸要求,锻件精度高,质量稳定。图6 为切边工序结束后的产品实物和锻件正火后的显微组织(细块状的铁素体+ 珠光体)照片。表1 为锻件的机械性能。
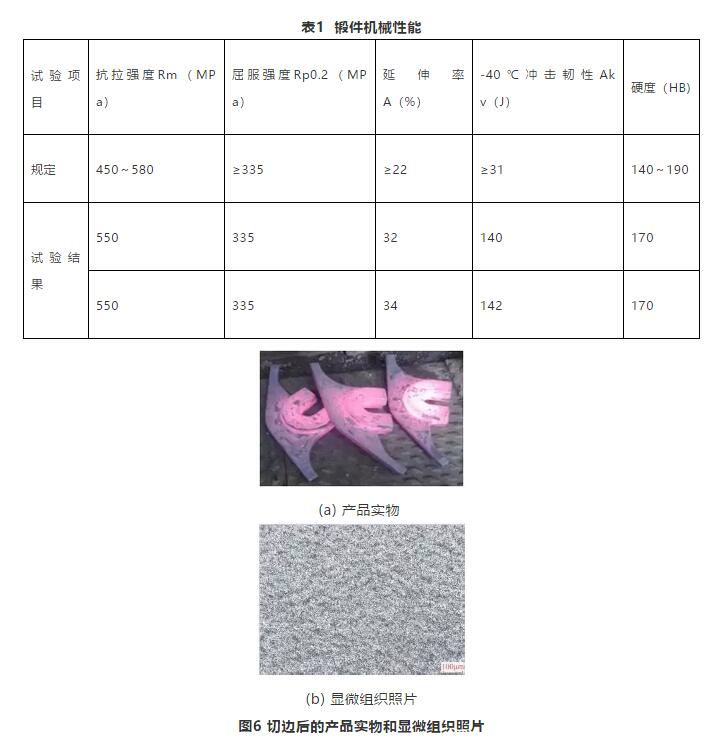
锻件开发初期出现了一些质量问题,主要缺陷是锻件未充满,主要发生在锻件两端和叉口部位(图7)。前期按照常规设计方案设计桥仓部,造成了材料利用率低和合格率较低的情况。通过设计优化,设计了阻力墙结构的模具,极大的提高了产品合格率和材料利用率。
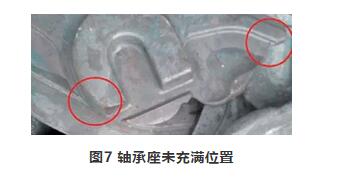
结论
⑴采用自由锻滚挤和模锻相结合的工艺可一火成形精度要求高的轴承座锻件;
⑵采用数值模拟方法可以有效辅助锻造工艺的设计,提高设计效率,提高产品开发成功率;
⑶采用阻力坎的桥部设计,锻件成形效果好,未出现充不满、穿筋等缺陷,尺寸达到要求,质量稳定。
——本文选自《锻造与冲压》2018年第17期
- 下一篇:轿车白车身冲压件VAVE降本方案的策略研究
- 上一篇:“中国心”博格华纳一路相伴
举报 0
收藏 0
分享 119
-
乘用车金属冲压
2025-05-29 -
冲压技术在电机叠片制造的应用
2024-09-06 -
车身零部件包边质量控制要点
2024-09-05 -
轻量化技术——热汽胀形工艺技术解析
2024-09-04
最新资讯
-
旭化成旗下宾霸品牌重磅亮相2025上海
2025-09-01 16:52
-
中国车企服务出海先行者:新央企新长
2025-08-29 16:13
-
携手共赴“智”造未来!埃马克推动大
2025-08-27 18:12
-
京东工业发布汽车等九大行业场景采购
2025-08-26 18:11
-
制造现场推动节能革新,电装稳步迈向
2025-08-25 14:04