KBH10 - 出色应对硬车削挑战
2018-03-23 20:00:16· 来源:肯纳金属刀具
高硬度工件的加工未必意味着加工过程更加困难,硬车削加工已经拥有数十年的应用历史了,操作中可以精简加工流程,在很多情况下外圆磨削流程可以被省略。这种工艺具有速度快,精度高的特点;这得益于包括肯纳金属公司在内的刀具供应商提供
高硬度工件的加工未必意味着加工过程更加困难,硬车削加工已经拥有数十年的应用历史了,操作中可以精简加工流程,在很多情况下外圆磨削流程可以被省略。这种工艺具有速度快,精度高的特点;这得益于包括肯纳金属公司在内的刀具供应商提供的种类丰富、功能齐全、具有成本优势的刀具产品,这些工具足以应对淬硬钢、超耐热合金,以及冷硬铁等材料的应用需求。在航天航空、汽车、能源以及其他行业不断开发其他更高硬度的金属材料时,刀具制造商也必须不断开发高性能的刀具产品,以应对这些材料的加工需求。
随着 KBH10 - 一款最新系列的多晶立方氮化硼材质(PcBN) 刀片的推出,从而满足了现今市场的对难加工材料的加工应用需求及挑战。全球切削技术部的资深工程师 Helmut Gremer 说道,:“肯纳金属公司推出的这款最新刀片产品是对现有PcBN 材质 KBH20 和 KB5630 产品的补充,这款产品有更高的耐磨性,可以成功用于硬度高达65HRc 材料的加工应用,特别是对表面精度要求更高的加工应用。”
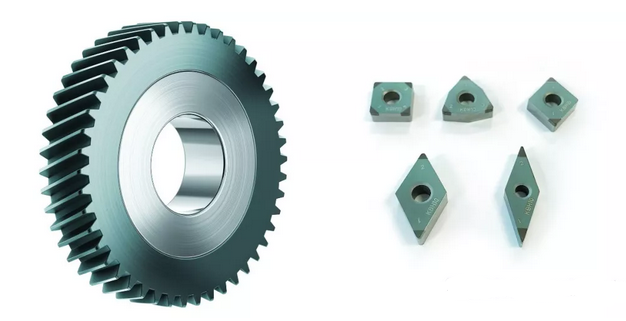
在一个实例中,一家著名的汽车制造商在对直径为 140 mm (5.5 in.) 的5115 合金钢轴承毂(之前经过热处理,硬度高达 62 HRC)进行内端面加工时,可以将刀具寿命延长 2 倍以上- 从每个切削刃加工 150 个工件增加到 350 个工件。还有一家传动轴生产商也取得了相似的结果,在使用立式转塔车床对58HRC UC1(与 S53 相似)钢材料进行车削加工时,刀具寿命从每个切削刃加工 250 个工件增加至450 个工件,并在加工过程中一直保持稳定的 6 Rz 表面精度。
在每个实例中,切削速度为 180 米/分钟(590sfm),平均切削深度为 0.15 毫米(0.006 英寸),平均进给率为每转 0.22 - 0.32 毫米(0.0087- 0.013 ipr)。与现有刀具相比,客户每年还节省了刀具成本达数千美元,这得益于在换刀操作中可显著减少设备停机时间。
KBH 采用全新的基体材料。其采用的PcBN 复合材料可提高切削速度 20%,同时还可确保相同的刀具寿命,有些情况下,刀具使用寿命还会显著延长。肯纳金属的工程师可以轻易实现Ra 0.2 和 Rz 1 的表面粗糙度,同时还可稳定地实现之前所提到的廓形和尺寸公差。因为 KBH10 可以提供几种不同的槽型和刃口处理类型,因此这款产品很快成为多个行业制造商满足其车削加工应用需求的理想产品。
KBH10 特别适合超精加工应用,但也可用于轻微断续或变深切削应用。因为降低了切削力,因此也减少了热量的形成,同样也减少了月牙哇和后刀面磨损,从而延长了刀具的使用寿命。同时还减少了加工表面白层的出现,而加工表面白层在许多硬材料加工中都会出现的。
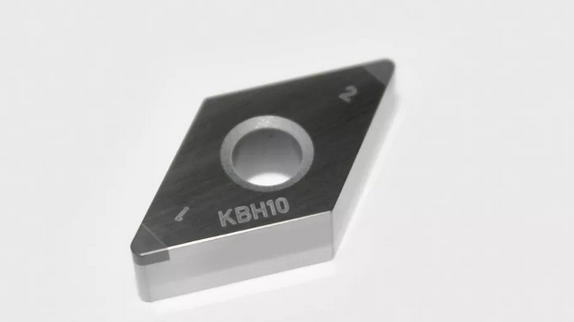
KBH10 是一款非涂层 PcBN 车削刀片,具有出色的耐磨性和极低切削力的特点。所以,很多客户都在享受刀具寿命延长一倍的同时还提高了工件加工质量所带来的优势。
工件加工质量的提高是通过采用独特刃口处理的 KBH10 刀片完成的。在传统刀具制造工艺中,通常会对几乎所有的PcBN 刀具进行瀑布型或圆角刃口处理,但肯纳金属公司开发了一种特殊形状的刃口处理方式,
从而比其它同类刀具产品更为锋利,还具有更好的轻快切削性能,同时还非常坚固,可以应对硬车削加工的挑战。一款经典的硬车削产品。提供多种形状、尺寸和槽型的刀片产品。
随着 KBH10 - 一款最新系列的多晶立方氮化硼材质(PcBN) 刀片的推出,从而满足了现今市场的对难加工材料的加工应用需求及挑战。全球切削技术部的资深工程师 Helmut Gremer 说道,:“肯纳金属公司推出的这款最新刀片产品是对现有PcBN 材质 KBH20 和 KB5630 产品的补充,这款产品有更高的耐磨性,可以成功用于硬度高达65HRc 材料的加工应用,特别是对表面精度要求更高的加工应用。”
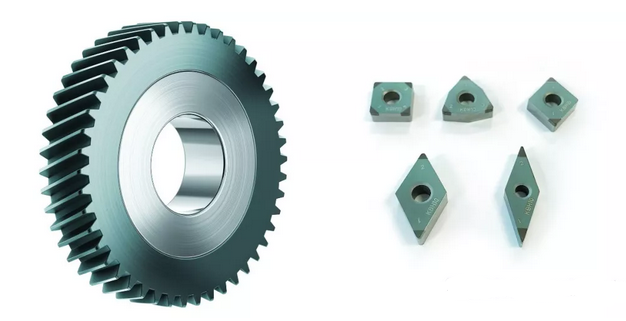
在一个实例中,一家著名的汽车制造商在对直径为 140 mm (5.5 in.) 的5115 合金钢轴承毂(之前经过热处理,硬度高达 62 HRC)进行内端面加工时,可以将刀具寿命延长 2 倍以上- 从每个切削刃加工 150 个工件增加到 350 个工件。还有一家传动轴生产商也取得了相似的结果,在使用立式转塔车床对58HRC UC1(与 S53 相似)钢材料进行车削加工时,刀具寿命从每个切削刃加工 250 个工件增加至450 个工件,并在加工过程中一直保持稳定的 6 Rz 表面精度。
在每个实例中,切削速度为 180 米/分钟(590sfm),平均切削深度为 0.15 毫米(0.006 英寸),平均进给率为每转 0.22 - 0.32 毫米(0.0087- 0.013 ipr)。与现有刀具相比,客户每年还节省了刀具成本达数千美元,这得益于在换刀操作中可显著减少设备停机时间。
KBH 采用全新的基体材料。其采用的PcBN 复合材料可提高切削速度 20%,同时还可确保相同的刀具寿命,有些情况下,刀具使用寿命还会显著延长。肯纳金属的工程师可以轻易实现Ra 0.2 和 Rz 1 的表面粗糙度,同时还可稳定地实现之前所提到的廓形和尺寸公差。因为 KBH10 可以提供几种不同的槽型和刃口处理类型,因此这款产品很快成为多个行业制造商满足其车削加工应用需求的理想产品。
KBH10 特别适合超精加工应用,但也可用于轻微断续或变深切削应用。因为降低了切削力,因此也减少了热量的形成,同样也减少了月牙哇和后刀面磨损,从而延长了刀具的使用寿命。同时还减少了加工表面白层的出现,而加工表面白层在许多硬材料加工中都会出现的。
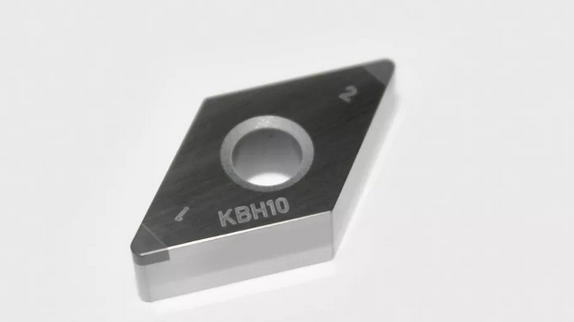
KBH10 是一款非涂层 PcBN 车削刀片,具有出色的耐磨性和极低切削力的特点。所以,很多客户都在享受刀具寿命延长一倍的同时还提高了工件加工质量所带来的优势。
工件加工质量的提高是通过采用独特刃口处理的 KBH10 刀片完成的。在传统刀具制造工艺中,通常会对几乎所有的PcBN 刀具进行瀑布型或圆角刃口处理,但肯纳金属公司开发了一种特殊形状的刃口处理方式,
从而比其它同类刀具产品更为锋利,还具有更好的轻快切削性能,同时还非常坚固,可以应对硬车削加工的挑战。一款经典的硬车削产品。提供多种形状、尺寸和槽型的刀片产品。
举报 0
收藏 0
分享 132
-
精度±微米,节拍7秒——埃马克VST 50的球头车
2025-07-09 -
专家访谈:埃马克 OCTG 加工的技术密钥与生产之
2025-06-25 -
Know-How系列 | 石油钻机核心技术揭秘:埃马克
2025-06-19 -
聚焦机床 | 埃马克USC 850数控万能车床:突破大
2025-06-11
编辑推荐
最新资讯
-
辐射亚太,链接全球——采埃孚再制造
2025-07-30 11:46
-
思看科技发布子品牌SCANOLOGY,全球
2025-07-30 11:06
-
风雨不动安如山——比亚迪叉车构筑“
2025-07-30 08:48
-
NEAS CHINA 新能源汽车技术与生态链
2025-07-29 09:52
-
三维扫描革新碾磨机辊套检测,效率与
2025-07-25 10:46