新能源汽车高节拍总装工厂规划与实践
概述
01 节拍等级的划分
新能源汽车的销售量每年都在增长,预测2022年新能源汽车的销量将达到总销量的30%,这是为了更好地利用优势资源并实现产业规模的效益,有必要建立一个年产量高达百万级的生产制造中心,并确保高节拍总装工厂的一条总装线具有超过70JPH的高节拍生产能力。生产节拍等级的划分见下表:
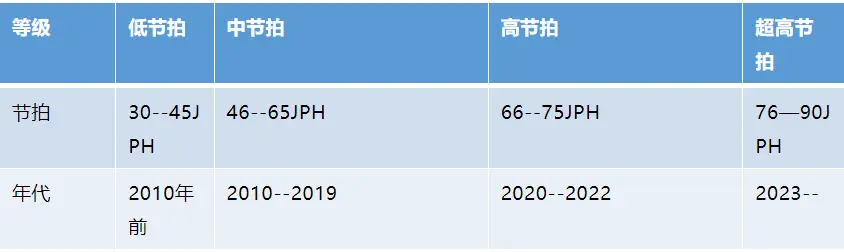
02 高节拍总装工厂的特点,以75JPH为例分析
1)生产线运行速度快,需要采用高速升降机,节拍需要达到48秒;
2)线边工艺设备工作频率高,要求设备可靠,故障率极低;
3)生产线工位多,操作人员多,工艺设计需满足人员效率提升需求;
4)零件物流、整车流密集,需要有高效的物流工艺设计;
5)操作工劳动强度大,需要有好的人机工程设计。如车门线同步带、底盘线同步带;
6)为高效利用产线,需要提升模块化装配比例,或建立总成分装线,如热泵分装、背门分装、前端模块分装、智能面板分装等。
03 高节拍工厂的优势
1)产量大,生产效率高
2)管理成本更低
3)规模效应导致零部件配套成本更低
4)可实现多平台柔性化大批量生产
5)信息化、自动化设备的利用率更高
6)投资产出率更高
高节拍总装线规划
01 方案统筹
在高节拍总装工厂规划中,必须对自动化输送设备,线边工艺设备,物流设备,信息设备,监控系统和智能防错进行整体规划,明确轻重缓急,将有限资金用在该用之处。
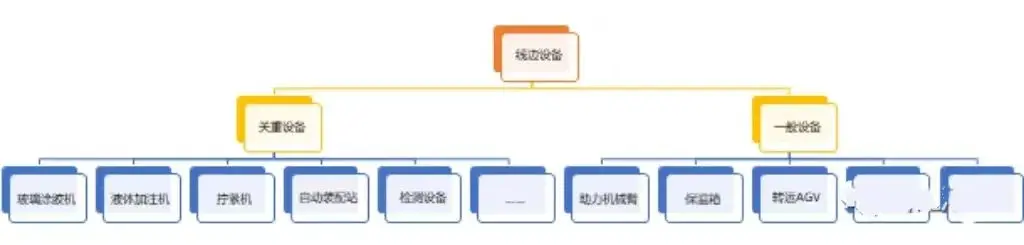
除硬件设备外,规划时还需要统筹考虑:
02 高节拍总装线规划时需要
考虑的12个基本要素:
(1)人机工程
(2)车型自动识别
(3) 运行数据自动检测
(4)过程控制数据自动获取
(5)生产信息实时传递
(6)低能耗/低噪音
(7)设备状态自动监控
(8)工位自动化需求
(9)自动化装配站
(10)分装总成上线自动转接
(11)大总成自动上线
(12)零件物流优先
03 高节拍总装线规划--信息化
总装线的高节拍规划离不开信息化,除公司级的信息系统外,还需要做好总装工厂级及各条生产线的信息系统规划工作,通过信息系统吧各个自动化设备有机地联系在一起,以保证生产执行层与设备控制层自动完成被赋予的工作,如准确地传递信息、数据的实时获取、智能防错、运行状态的实时监控、趋势分析、动态补偿等。
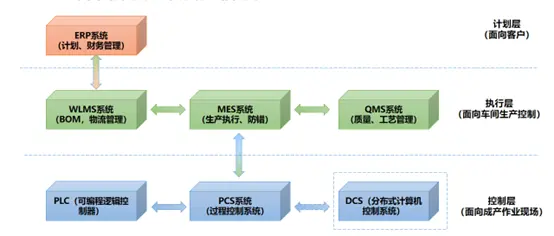
04 以智能制造的思维开展规划工作
高节拍总装线规划,需要以智能制造的思维合理规划汽车总装的工艺流、信息流、物流的规划,实现三流统一、协调、先进,低成本生产、高质量快速交付。
●工艺流:包含工艺流程、生产线、工艺装备、自动化设施、检测设备等科学规划
●信息流:接收、分发、传递和获取、存储、分析、反馈、纠错等与总装制造相关的计划、设备、产品、工艺、检测信息、队列顺序
●物流:包含零件物流、仓储物流、物流设备、物流方式
05 高节拍总装线的厂房规划
总装厂房一般采用类似桁架结构的可承载厂房,普遍为24*24或24*28柱距的网架或桁架结构,主要优势:
①安调工程量相对较少、周期短;
②便于后续线体改造及扩产
③便于工艺线体布局和线边工艺设备的安装;
④便于零件物流存放及转运
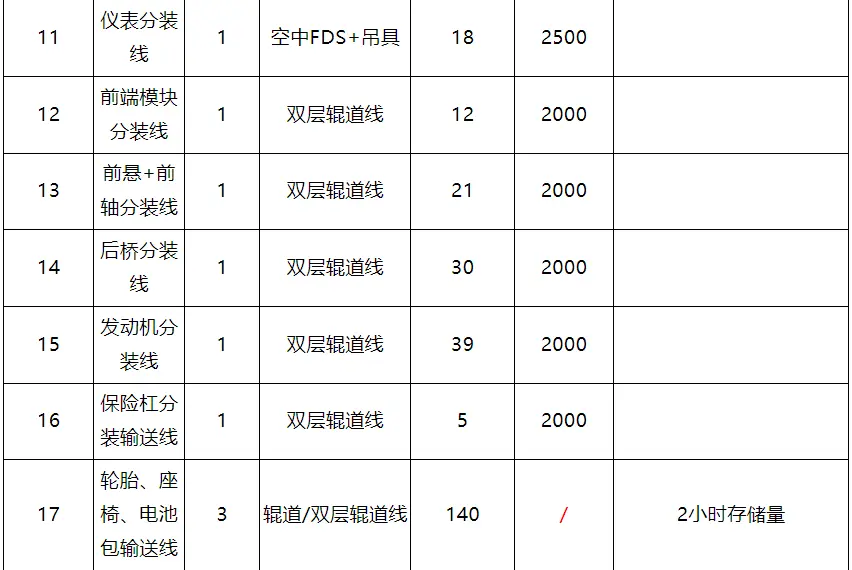
图1 非承载厂房
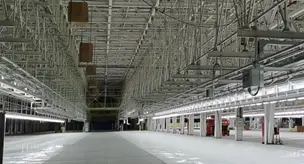
图2 承载式厂房
06 高节拍总装线的工位设计
工位数设计及其影响因素很多,至少应考虑以下几点的平衡:
1)车型平台及主力车型的数量:混动平台、纯电平台、混流生产
2)加工深度及装配零件数:模块化率、厂内形成模块、厂内形成模块、分装区分装线等
3)汽车工时:装配自动化率、自动化工作站、装配工具效率、物流自动化程度
4)人员效率:工位人数、人员素养、人机工程等
5)在线质量门检查、返工及新车型预留工位。
75JPH节拍,根据公司的实际及车型发展,主线的装配工位数大约在210--230个之间,OK线工位数30个左右,总工位数240--260是比较合适的。
07 高节拍总装工厂的工艺平面布置规划
总装主线的布置形式主要有S型、T型、L型等,在装配工艺确定了情况下,以物流优先为原则:
1)底盘及底盘分装区,是大零件或总成的集中区,应靠近大零件的物流区;
2)内饰件以SPS集配为主,要有足够的SPS区及SPS小车自动上下线;
3)对于排序上线的零件,考虑物流路径最短;
4)外购的模块化总成,采用自动对接空中输送至工位,要减少交叉;
5)自动化装配站尽可能布置在生产线的端头;
6)新能源汽车,动力电池是重要变量,可以设计单独的电池包合装线
考虑上述因素,较多采用类似于S型布置方案
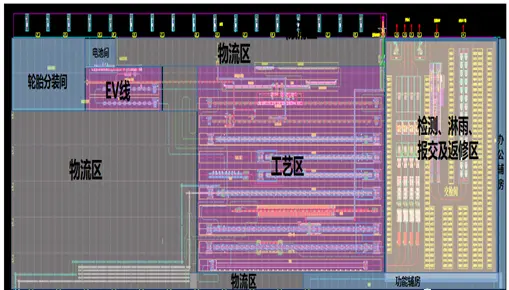
图3 平面布置示意图
08 高节拍总装线的自动化工作站规划
新上总装线自动化程度均有较大幅度提升,部分大型总成件能够实现自动化装配和测试,在做计划时能够依据产品特点和预算情况选择执行项目并构建自动化装配或者测试智能站
Ø风挡玻璃采用了智能工作站
Ø玻璃底涂智能站
Ø天幕自动涂胶装配站
Ø车轮自动化装配智能站
Ø前座椅自动搬运站
Ø动力电池自动拧紧站
Ø底盘合装螺栓自动装配拧紧站
Ø底盘自动检查站
Ø自动投放蓄电池站
Ø车门密封条自动粘贴站;
Ø间隙面差自动检测智能站
Ø仪表板总成与车身合装自动化
Ø动力电池自动合装工作站
Ø前副车架自动拧紧站
Ø后托架螺栓自动拧紧站
Ø底盘自动合装工作站
Ø车门自动合装站
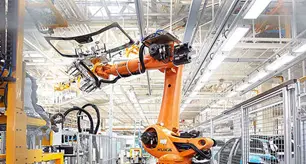
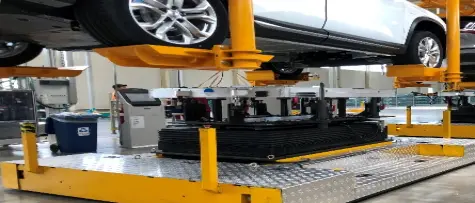
图4 风窗玻璃装配工作站
09 高节拍总装线的数字化
监控系统规划
建立RFID整车跟踪系统,同步规划工艺设备及质量监控系统,实现数据的实时采集、实时分析、实时监控、快速决策、实时调整。
1)整车定位跟踪系统
2)安灯系统
3)质量监控管理系统
4)物流调度系统
5)能源管理系统
6)重点设备、重点工位视频监控系统
7)设备管理系统
需按要求做好每条线路的信息点计划,网线计划,服务器计划,信息设备与软件计划,计划预算中应设置执行项目并进行预算,可以将各生产线子系统干预总装中央监控系统,统一规划协调。
图5 总装中央监控示意图
10 高节拍总装线的质量门系统规划
通过质量门信息系统对生产中装车及检测的质量问题进行记录与跟踪,并自动触发各线质量门灯光指示,实现了对质量门的管理;关联RFID、研发、生产、质量、电检服务器等。能够实时生成车辆数据信息;在线生成需返修、返工车辆的项目,所有项目返修结束并确认合格后放行出总装车间;能分类统计各类缺陷数据。
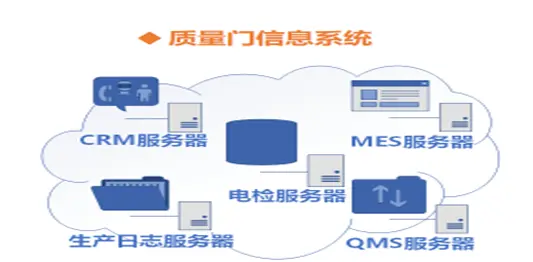
图6 质量门系统示意图
11 高节拍总装线的线体设备规划
近年来,总装线体输送方式并未得到根本改变,尽管新兴AGV线体超柔性特质被更多地应用于分装线中,而主线尚未以全AGV的形式进行输送。
(1)线体输送方式选型--内饰线和最终线
对新能车而言,合装前与合装后内、外饰件的组装工作量比较大,高节拍总装线、内饰线、最终线等均设计为环线。
内饰线与最终线的线体之间,兼顾实用性和成本,通常会选择普通滑板的线条,在资金允许的情况下,电动升降滑板的形式可以较好的提高人机工程的效果。
(2)线体输送方式选型--底盘线
(3)OK线
OK线主要担负着检查及一些在线调整工作,通常选择钢制宽板链,最近又出现了选择塑料板链的情况,但是成本较高。
(4)总成分装线
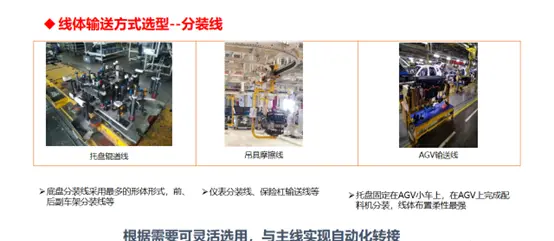
12 高节拍总装线的线边设备选型
充分考虑企业发展需要,建立加注设备、检测设备、合装设备、自动化工作站等工艺设备的模块化标准及设备技术协议标准化文本,使得工艺设备模块化,标准化了设备选型标准,并应对设备进行数字化仿真分析,减少适配风险,缩短了设计安装调试周期。
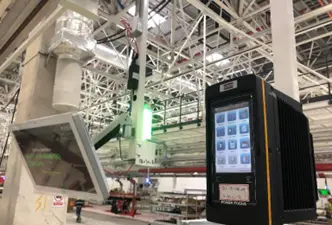
图7 自动化装配智能工作站示意图
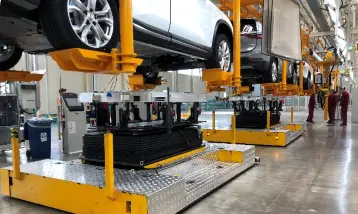
图8 电池包合装模块示意图
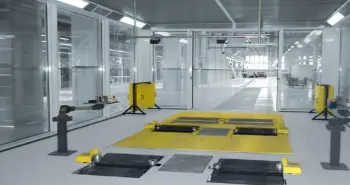
图9 检测线模块示意图
13 高节拍总装线的部件
模块化装配要求
某款外资车型在总装过程中使用模块化总成进行供应,在降低总装线工位数的同时降低了一级总成零部件数量,提升总装效率
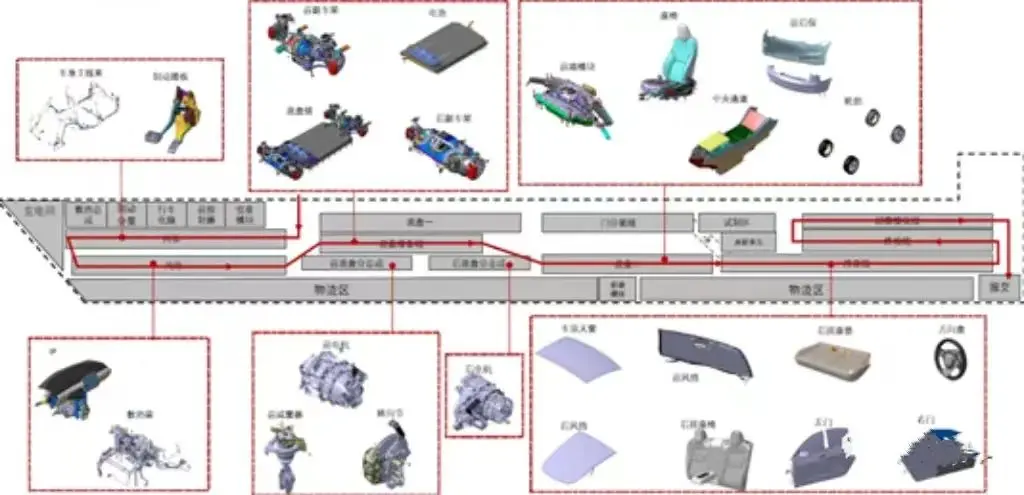
图10 模块化总成示意图
14 高节拍总装线的拧紧工具
电动化要求
在高节拍装配线上,对拧紧工具的要求更为严格,通常全线都会配备高精度的电动工具(拧紧轴+定扭电枪),从而实现了拧紧工具的电动化,以及智能终端,设于关键/重要工位上,用于车辆精确定位与联网管理以及车辆选装信息,质量缺陷,扭矩,拧紧角度等关键工艺信息的运行指导与追踪管理,
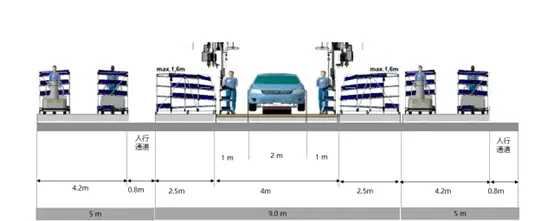
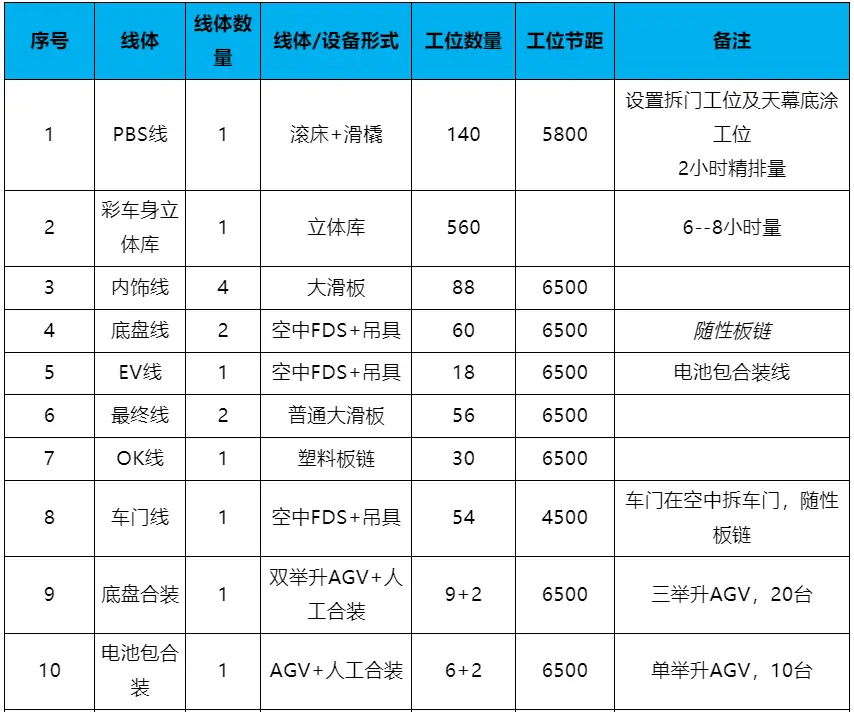
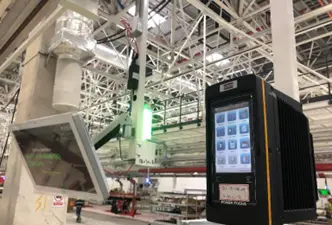
75JPH总装线介绍
01 生产线形式及工位
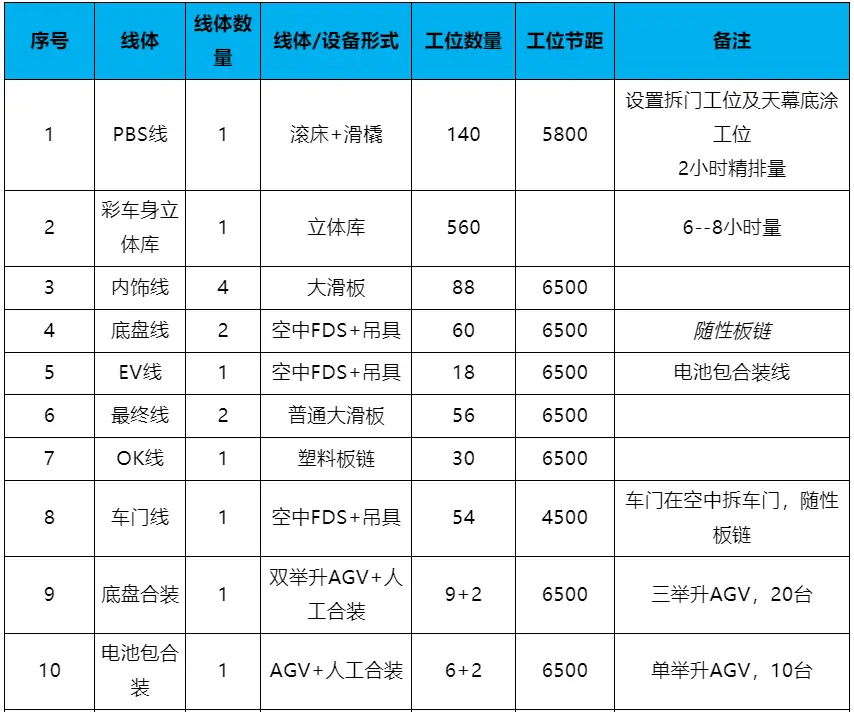
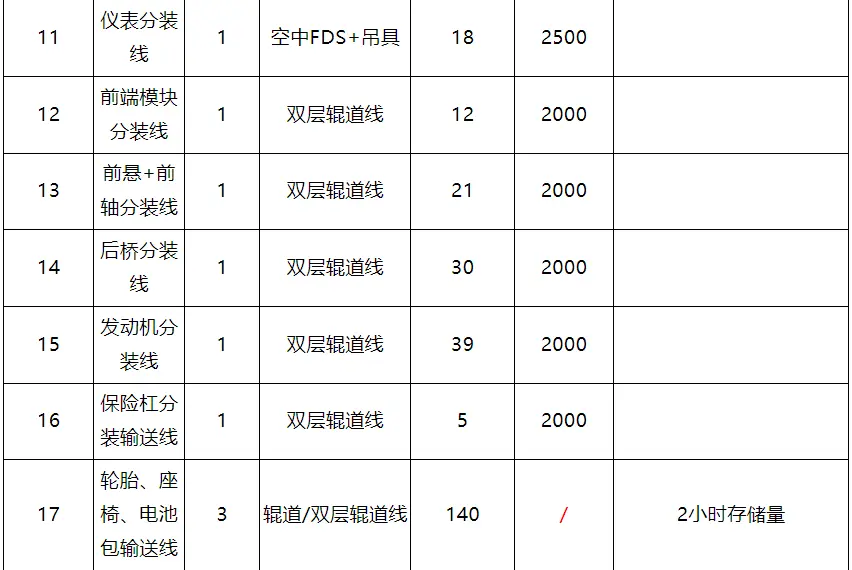
02 油漆车身立体库
鉴于高节拍生产的实际需求,有必要在涂装和总装之间构建一个油漆车身立体库,该库将用于涂装车身的缓存,而车身的存储量将在4--8小时的生产量范围内。有必要对75JPH节拍立库出入口进行效率核算,准确排产彩色车身出立库入PPS线以满足两小时内配送排序需求。
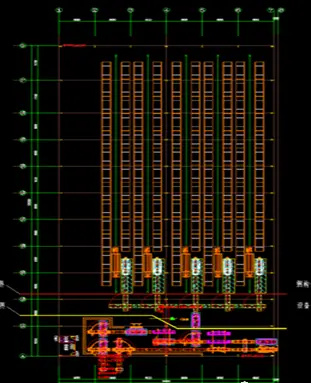
图12 油漆车身立体库示意图
03 工艺布置方案示意
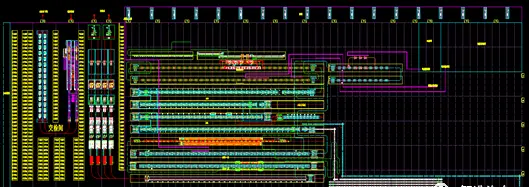
图13 平面布置示意图
04 自动化装配智能站示意
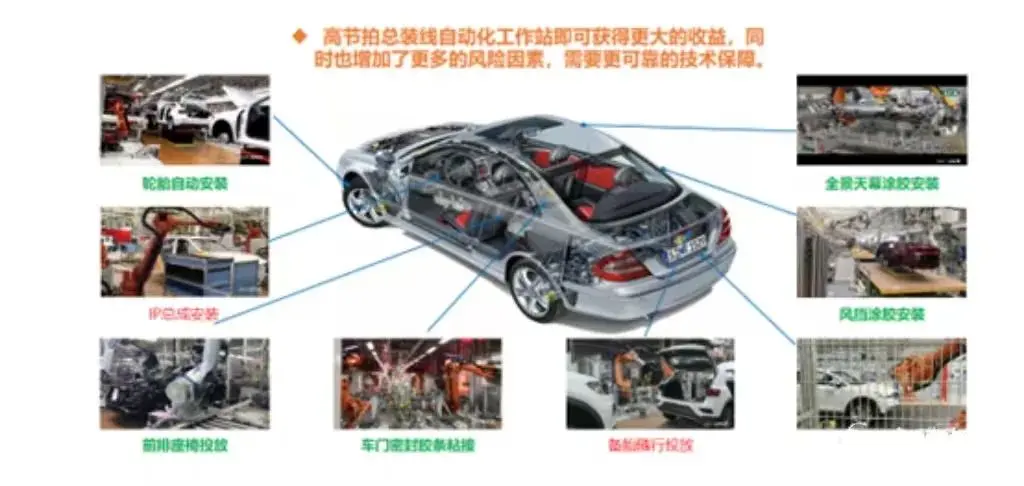
05 滑板宽度及SPS料车设计方案示意
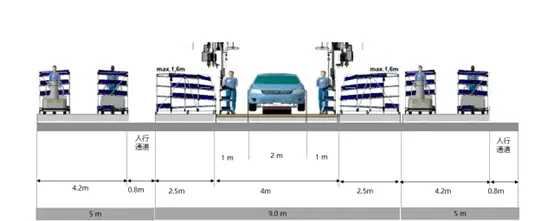
06 随行板链/升降滑板方案示意
●为解决车门线和底盘线高节拍情况下,操作工人机工程学问题,保证装配品质,设计了与主线同步的随行板链。
●为了解决内饰线和最终线的人机工程学问题,选用了可电动升降高度的大滑板。
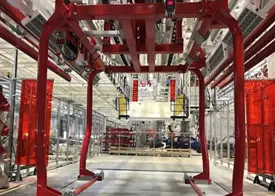
图14 随行装配塑料板链示意图

图·15 电动升降大滑板示意图
07 AGV底盘合装方案示意
利用三举升AGV合装台车实现了前后动力总成和托架总成半自动化组装,可柔性化制造多平台型号。
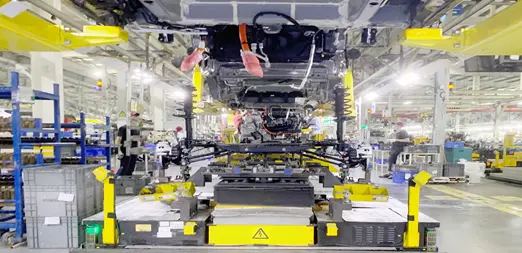
图16 电池包合装示意图
08 双动力总成装配方案示意
底盘合装采用柔性化生产技术方案,可实现电动力总成、双电机总成、混动总成的合装。
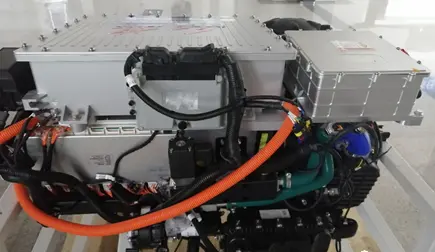
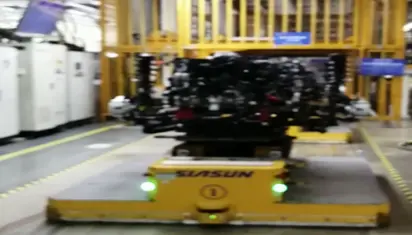
图17 双动力总成合装示意图
09 动力电池包装配方案示意
随着电动汽车电池容量的逐渐增大,车身底盘的有效空间几乎被完全占据,因此需要重新分配底盘吊具的空间。为此,我们建立了一条专为动力电池设计的合装线,即EV线,并将EV线吊具替换为托车轮;避免了大容量动力电池对吊具的干扰。
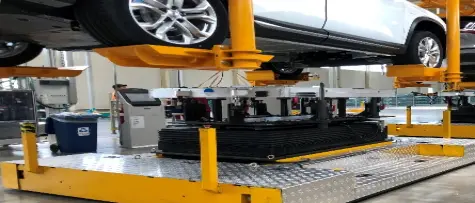
图18 宽电池包合装示意图
10 一体化电池包装配方案示意
一体化电池包作为车身结构的一部分,取代了车身底板,为满足75JPH高节拍的总装生产要求。一体化电池包技术要求总装工艺做到:
保证一体化电池包和车体水密封达标;很好地控制车身精度和合装精度;进车身内组装内饰件安全保障和操作便利性工艺设计。
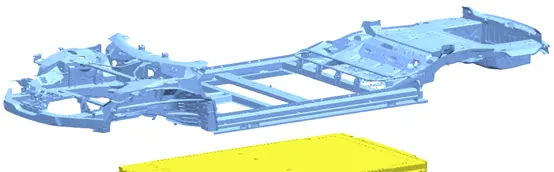
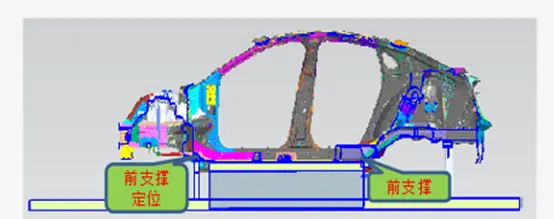
图19 一体化电池包合装示意图
11 动力电池螺栓自动拧紧方案示意
每辆汽车的动力电池都装有多达15个固定螺栓,这些螺栓不仅拧紧力矩巨大,而且其技术标准也是非常高的。研究了采用人工预紧与机器人复紧的装配过程。由三个机器人完成螺栓的复紧及数据采集。
图20 自动拧紧示意图
12 零部件模块化供货方案示意
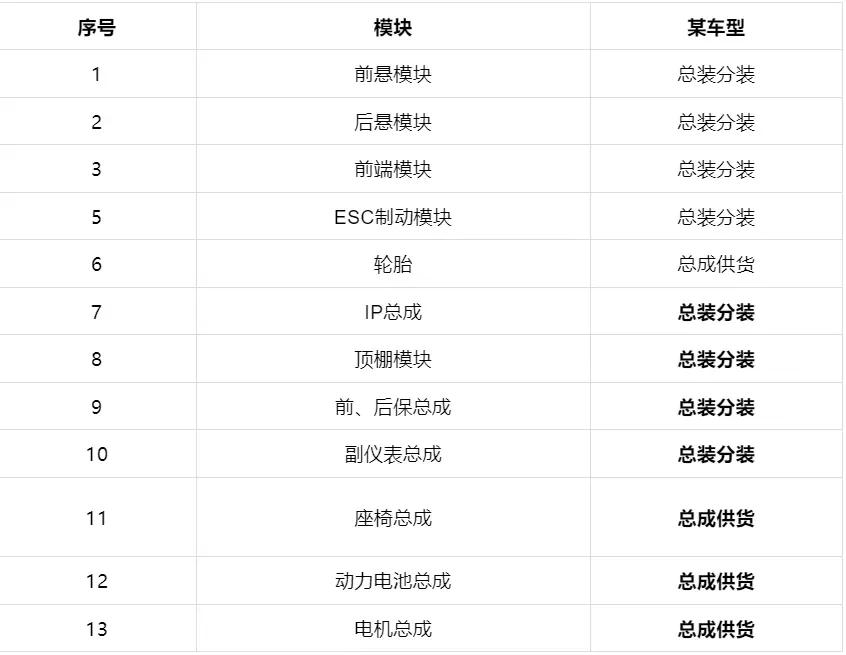
13 整车性能检测方案示意
●75JPH产线,需要设计四条综合检测线,包含整车性能检测及ADAS系统的标定及检测;
●需要设计二条45JPH的淋雨检测线;
图21 检测线布置示意图
●需要设计一条多功能厂内检测跑道
总装下线的整车需要在该厂内跑道上完成包含加速路、ABS路、扭曲路、鹅卵石路、砖路、角钢路、减速带路、搓衣板路、绳索路、驼背冲击路、水坑路、“8”字路等23种不同道路的测试,全部检测合格的车辆才能交付给用户。设计好的厂内检测跑道要功能完善,留有足够的测试区域。测试路进出口要能够容纳80辆以上/时的通行能力并避免车辆通行,一般情况下这些赛道都要设计成商品化停车场附近。
结束语
科技发展不可限量,在智能化新时代下如何规划和建设一条高水平总装线,这是摆在我们面前的新任务,有许多技术问题亟待解决,所要考虑的要素也比较复杂,大家对于构建新能源汽车高节拍总装线有着不同的认识与做法。
-
推动汽车行业转型的引领者——面向未来的总装NE
2024-12-03 -
总装工艺成本优化实践案例
2024-08-05 -
如何提高螺栓连接的强度?
2024-07-30 -
案例分析:螺栓“跑丢了”!
2024-07-29
编辑推荐
最新资讯
-
中国车企服务出海先行者:新央企新长
2025-08-29 16:13
-
携手共赴“智”造未来!埃马克推动大
2025-08-27 18:12
-
京东工业发布汽车等九大行业场景采购
2025-08-26 18:11
-
制造现场推动节能革新,电装稳步迈向
2025-08-25 14:04
-
携手共赴“智”造未来!埃马克推动大
2025-08-22 19:41