同步工程在新车型模具开发中的应用
2019-04-08 15:28:53· 来源:《锻造与冲压》
汽车上有60%~70%的零件是用冲压工艺生产出来的,汽车冲压模具的开发是新车型生产准备的重要部分,随着我国汽车市场自主品牌车型开发的激烈竞争,模具开发能否按期完成,成为关系着新车型能否顺利按计划实现SOP的关键。同步工程技术集成
汽车上有60%~70%的零件是用冲压工艺生产出来的,汽车冲压模具的开发是新车型生产准备的重要部分,随着我国汽车市场自主品牌车型开发的激烈竞争,模具开发能否按期完成,成为关系着新车型能否顺利按计划实现SOP的关键。同步工程技术集成了汽车公司和模具公司各自的优势,在车身开发阶段就考虑到产品模具制造各个环节可能遇到的问题,同步进行车身设计和模具制造的可行性分析,提高产品的设计质量,降低产品成本,有效缩短模具制造周期。
同步工程是指在汽车设计阶段进行工程化可行性分析,在设计阶段把后期制造过程中可能出现的问题暴露出来,通过产品设变、工艺优化等技术手段解决制造隐患,避免后期制造的风险。在国外,同步工程又可称为基于可制造性的设计——DFM。当前,全球汽车制造商面临着巨大的成本压力,传统的汽车开发制造流程由于周期长、成本高,而无法适应新的全球竞争的要求。冲压SE在汽车开发中的应用对于缩短模具开发周期、提高材料利用率、降低工艺难度、减少开发成本、提高产品质量及改善冲压工艺性等方面发挥重要作用,为汽车制造商对汽车开发制造流程进行了优化。特别是随着计算机技术的发展,许多原来需要通过制造验证的产品设计以及工艺,都可以通过CAE技术在设计阶段进行验证,CAE技术的不断成熟和完善使同步工程能够得到广泛的应用。现在汽车行业做的比较多的、成熟的同步工程是四大工艺的同步工程。同步工程已经成为各主机厂车身开发的重要流程。
在车身冲压模具工艺开发中的应用
冲压同步工程将冲压工艺与计算机辅助工程相结合,对冲压零件进行工程可行性分析,产品开发的各个子过程之间互相配合,尽可能同步进行。汽车开发经过对标车分析阶段和模型设计阶段后是产品工程化阶段,也是整个产品设计思想体现的关键,该阶段产生的数据决定整个产品开发速度及产品质量。冲压SE人员协同模具制造商从产品质量、冲压工艺性、模具结构、操作性、成本等因素考虑,制定合理的工艺方案,编制产品工艺规划,计算产品材料利用率,借助计算机辅助工程对产品数模进行冲压工艺性分析,提出ECR(Engineer Change Request)工程更改申请书,提供数模整改建议和参考数模。其主要工作内容是确定工程数模实现的可能性:判断暗伤开裂可能产生的位置及改善方案;起皱可能产生的位置及改善方案;成形不足可能产生的的位置及改善方案;冲击线、滑移线可能产生的位置及改善方案;回弹可能产生的位置及改善方案;材料变薄率;刚性分析;强度分析;扣合性分析等。图1所示为传统车身工程和模具开发流程与应用同步工程的车身工程和模具开发流程的对比。
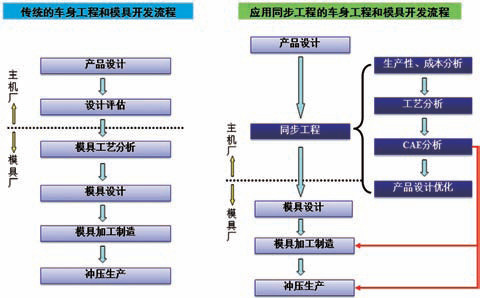
图1 车身工程和模具开发流程
在车身冲压工艺分析中的应用
以某MPV车型尾门外板冲压工艺性分析为例,介绍同步工程在车身冲压工艺分析上的应用。第一步,确定材料及成形参数:材质为H220B+Z,料厚为0.65mm;按BQB403-2009标准,查出材料抗拉强度、屈服强度、N值、r值;确定摩擦系数等。第二步,将产品数据按成形力中心与压力机中心重合原则放入,设置冲压方向和拉延压料面,按产品成形深度确定行程,生成补充面,如图2所示。第三步,成形过程模拟:按照冲压的实际成形过程进行模拟成形,如图3所示。第四步,分别进行成形性检查、变薄率检查、起皱检查、滑移线检查等。
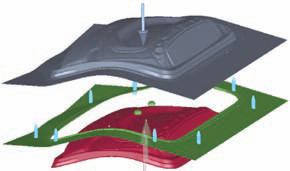
图2 生成补充面
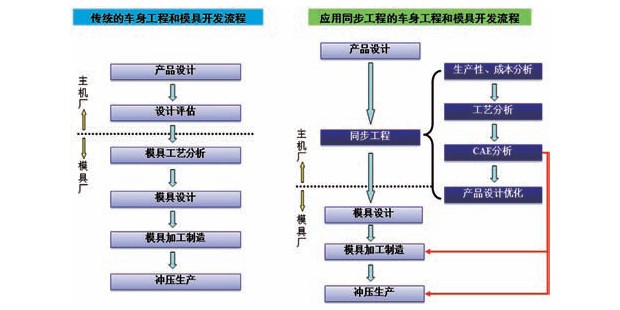
图3 成形过程模拟
⑴成形性检查:CAE分析时零件有两处侧壁有黄色,如图4所示,从软件分析过程看,存在开裂风险的部位在凹模圆角部位向上一段型面上,判断为不开裂;如果现场调试有开裂现象,可适当放大凹模刃口R角,由目前设计的R20最大可放大到R30,可以消除黄色开裂风险。
⑵变薄率检查:除前后侧两处变薄极限略高于20%,其余都控制在4%~20%的范围内,如图5所示,此两处可适当调整拉延筋加以解决。
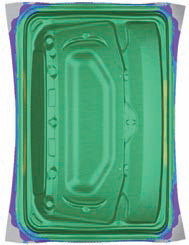
图4 成形性检查
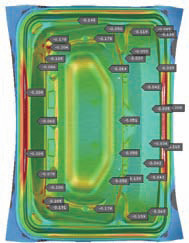
图5 变薄率检查
⑶起皱检查正常,无缺陷,如图6所示。
⑷滑移线检查:两段棱线R值在25~30mm之间,最大滑出R角边界7.8mm,因R值较大,精算滑移线刚好在R角根部,不影响产品外观质量,如图7所示。
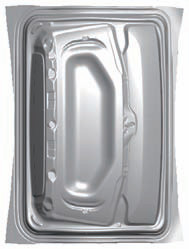
图6 起皱检查
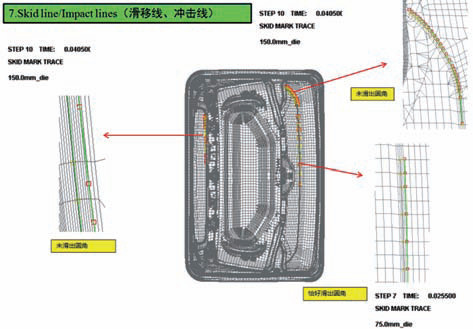
图7 滑移线检查
通过以上模拟分析,可以确定冲压件成形的参数条件,如成形力、压料力、板料尺寸、材料利用率、拉延筋形式和尺寸、顶杆行程、进料量等,对后续模具结构设计和模具调试都有较强的指导作用。
在车身冲压模具结构设计中的应用
⑴确定拉延筋的形状、尺寸,分析板料成形过程各方向的进料量。
根据Dynaform精算结果,确定拉延筋尺寸,对拉延模具结构设计有明显指导作用,可直接设计出整体铸造筋的结构,避免因修改反复设计镶嵌式结构的筋线,减少加工量,提高模具使用寿命,如图8所示。模拟分析板料成形过程各方向的进料量,如图9所示,对后续模具调试提供指导。
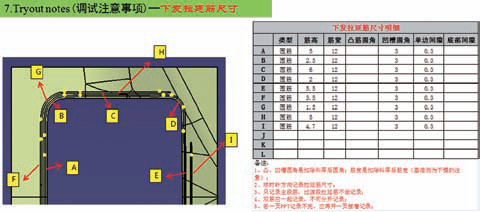
图8 拉延模具拉延筋尺寸设计明细
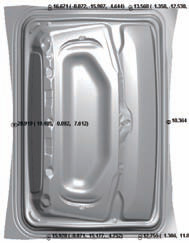
图9 拉延结束后料边与真实筋边缘最小距离信息(Dynaform精算)
⑵对冲压件各工序的回弹量进行模拟分析。
根据Dynaform精算结果,冲压件各工序的回弹量有确切的分析数值。如某车型尾门外板拉延模设计时,可以参照回弹分析结果,将中下部一段型面做出1.2mm回弹量,使产品的尺寸合格率得到提升。尤其在OP40和OP50翻边和侧翻边工序中,由于产品翻边高度较大,翻边后回弹明显,也可以参照分析结果,给出翻边补偿量,可减少后期调整量。该零件OP10工序回弹量如图10所示,OP20工序回弹量如图11所示,OP40工序回弹量如图12所示,OP50工序回弹量如图13所示。
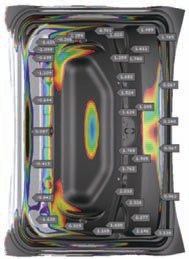
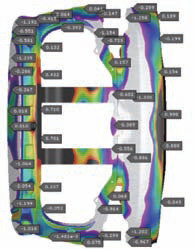
图10 OP10(支撑结果) 图11 OP20(支撑结果)
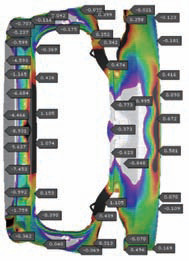
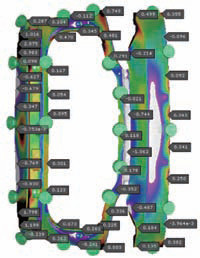
图12 OP40(支撑结果) 图13 OP50(支撑结果)
在车身冲压模具制造中的应用
模具制造商在接到汽车零件的模具制造订单后即参与主机厂家的工程开发。模具厂内部又有不同的分工:汽车零件工艺设计、模具结构设计、模具制造工艺制订、模型制造、模具零件加工制造、标准件采购、模具组装等。模具厂通过“项目计划表”和“模具制造进度表”等实现行之有效的制造工艺同步工程,将不同工艺过程协同管理,通过同步工程管理将模具制造过程各环节紧密联系在一起,提高模具制造进度。模具厂组装钳工在整个模具制造过程中发挥设计参与、进度跟踪、工艺指导和质量把关的关键作用,确保模具按时完成。主机厂安排相关人员在模具制造厂模具制造的不同阶段参与检查监督,有效防止模具制造过程中出现问题。
在车身冲压模具验证投产中的应用
模具的验证投产是实现产品设计思想到实际出零件的重要节点,汽车零件能不能保质保量按时提供,关系着产品开发能否按期投放市场。主机厂人员需及时发现模具在模具厂试模时发现的问题,及时在模具厂进行处理。在模具发运到主机厂前,主机厂应用3D-Simulation虚拟仿真技术,将设备、工装、模具按照1:1建立数模,并反馈到虚拟环境中,通过离线模具设计检查、机械手运动轨迹编辑、干涉曲线优化、端拾器设计、零件受力分析等,提前做好模具验收的各项准备工作,同步做好模具存放及维修场地、验证材料、端拾器、自动化机械手运动轨迹模拟、产品零件料架等准备工作。模具调试验收过程中,除了常规的模具静态检查、动态检查、冲压件尺寸精度和表面质量评估外,还有试模材料的测试确认。试模后采用超声波测厚仪检测冲压件各部位的实际厚度减薄率,通过了解各部位可能发生开裂的程度,进一步评估冲压件生产时的合格率,确保生产稳定。
随着计算机技术的发展,主机厂许多原来需要通过制造验证的产品设计以及工艺,都可以通过CAE技术在设计阶段进行验证,近几年CAE技术的不断成熟和完善,使同步工程能够得到广泛的应用。同时企业通过长期的经验积累,建立企业“数字化样车”知识库,把冲压同步工程与车身设计的其他领域的CAE技术结合,为整车开发提供更全面的支持。通过“虚拟制造”等技术把后序模具开发、制造以及模具验证投产等过程更紧密地与车身开发联系起来,达到企业在新车型开发过程中降低风险、缩短开发、制造周期、控制成本的目的,为企业赢得市场提供有力支持。
—— 来源:《锻造与冲压》2019年第6期
举报 0
收藏 0
分享 152
-
京东工业发布汽车等九大行业场景采购解决方案手
2025-08-26 -
京东集团与东风汽车达成战略合作 打造汽车行业
2025-08-15 -
助力汽车零部件产线智能化升级,西门子Xcelerat
2025-06-27 -
BBA集体转向!放弃全面电动化
2025-06-26
编辑推荐
最新资讯
-
旭化成为芬兰氢能项目提供集装箱式碱
2025-09-02 17:45
-
旭化成旗下宾霸品牌重磅亮相2025上海
2025-09-01 16:52
-
中国车企服务出海先行者:新央企新长
2025-08-29 16:13
-
携手共赴“智”造未来!埃马克推动大
2025-08-27 18:12
-
京东工业发布汽车等九大行业场景采购
2025-08-26 18:11