冲压CAE技术在汽车开发中的应用
2018-12-03 23:30:50· 来源:文/艾树良 锻造与冲压
运用有限元软件对汽车车身零件进行成形性分析,得到的冲压仿真分析结果可以为车身零件的造型改进、冲压工艺设计及模具调试提供参考依据,从而达到缩短开发周期,降低开发成本的目的。本文介绍了薄板冲压成形的冲压CAE技术所涉及的核心内
运用有限元软件对汽车车身零件进行成形性分析,得到的冲压仿真分析结果可以为车身零件的造型改进、冲压工艺设计及模具调试提供参考依据,从而达到缩短开发周期,降低开发成本的目的。本文介绍了薄板冲压成形的冲压CAE技术所涉及的核心内容以及CAE技术在模具制造中所发挥的作用,并以AUTOFORM软件为例从不同的角度阐述了冲压CAE技术在冲压工艺研究中的应用情况。
目前,全球汽车制造企业之间的竞争越来越激烈,人们对汽车质量和性能的要求也越来越高。为迎接挑战,汽车界提出了3R战略,即缩短产品的市场化周期,降低产品开发费用和减轻汽车重量。
冲压工艺与模具设计是薄板冲压成形技术的关键,涉及力学中的三大非线性问题:几何非线性(冲压过程中板料产生大位移、大转动、大变形)、物理非线性(又称材料非线性,指材料在冲压中产生的弹塑性变形)、边界非线性(指模具与工件产生的接触摩擦引起的非线性关系)。传统的冲压工艺与模具设计只能以许多简化和假设为基础进行初步计算,然后进行大量反复试模、修模来保证零件品质。
薄板冲压成形的计算仿真实际上是利用数字模拟技术分析板料成形的全过程,每次仿真就相当于一次试模过程,因此成熟的仿真技术可以减少试模次数、缩短新产品开发周期、降低开发成本、提高产品品质和市场竞争力。
冲压成形过程的计算机仿真原理
在薄板冲压成形过程中,模具的刚性通常远远大于板料的刚性,因此模具的变形相对板料的变形来说很小,可以忽略不计。将薄板冲压成形过程抽象成一个力学过程,它包含四种特性不同的运动物体,图1所示为冲压成形的典型力学模型示意图。在这四种物体中,板料为弹塑性变形体,其余三种均可作为刚体看待,但三种刚体的运动特性各不相同。上模作为对板料加载的主动体,其运动状态主要由压力机控制,按一定的频率作上下往复冲压运动,压板在压边力作用下压住板料,下模通常是固定不动的。
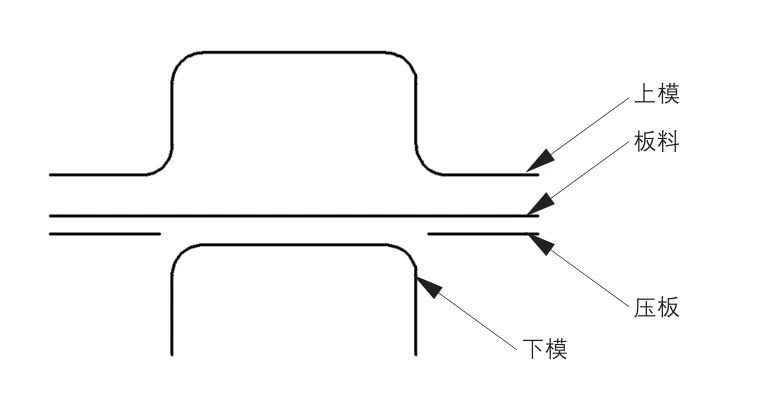
图1 冲压成形的典型力学模型示意图
为得到板料的弹塑性变形过程,必须求解作用在板料上的各种外力。从受力分析可知,作用于板料上的外力主要有三个来源(图2)。其中F1为压板对板料的作用力,F2为上模对板料的作用力,F3为下模对板料的作用力,上述作用力中又包括法向接触力和切向摩擦力。此外板料还受到重力作用,压板的刚体运动与板料的弹塑性变形是相互耦合的,因此必须同时求解。
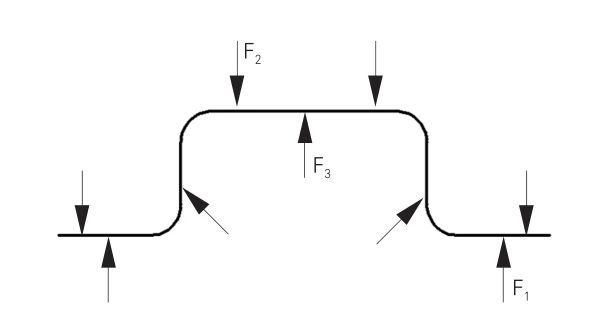
图2 作用在板料上的外力示意图
计算机仿真技术在冲压工艺与模具设计中所能解决的问题
拉裂的预测与消除
拉裂是薄板冲压成形中常见的失效形式之一,利用CAE软件成形性分析及钣金成形极限图的分析,对板料成形过程中的料厚变化、材料变薄率的变化状态观察,可以较为准确地评估板料在成形过程中开裂的部位及裂纹区域的应变状态。开裂问题通常可以通过调整产品状态及成形材料解决,如适当放大成形圆角,使用延伸性更好的材料等。对于有特殊要求的零件,则需要增加相应工艺手段。当产品开裂区域在制件内部,难以通过板料流动来进行补偿的情况下,根据裂纹位置,采用过拉延手段,放大其成形R角方法,再利用整形工序实现产品的形状控制。当形状裂纹在制件边缘时,可以通过改变毛坯形状、增加切角工艺、调整拉延筋形状等方法解决开裂问题。
起皱的预测与消除
起皱是薄板冲压成形中另一种失效形式,计算机仿真技术能很好的预测给定条件下零件可能产生的起皱。冲压成形是板料在复杂的外力条件下通过流动变形生成制件的成形方式,而成形板料的厚度尺寸相对形状尺寸来说很小,极易在厚度方向上出现失稳并产生皱纹,影响零件表面质量。
利用CAE有限元技术,对相关工艺参数,如拉延筋、压边力、板料形状在极限状态下的模拟分析,得出导致产品失稳起皱的关键因素,从而找到有针对性的解决办法。在产品的边界区域,可通过适当的工艺补充形状,改善产品形状的突变状态,调整拉延筋形状等方法避免起皱现象产生;在产品的内部形状区域,由于特征形状较多,可通过CAE仿真分析软件,评估产品形状在成形时的料厚及应力、应变的变化状态,使其在开始成形时出现的皱纹,在成形结束时通过产品形状的拉延消除产生的皱纹,从而改善产品的质量。
回弹的计算
冲压成形件在卸载后的回弹是不可避免的物理现象。因为回弹现象的存在,模具型腔表面的形状与工件表面设计的形状应当不同,以补偿回弹引起的工件尺寸变化。当仿真计算进行冲压到极限位置时,模具对工件的加载过程结束,计算机会得出工件加载过程的变形轮廓。加载过程结束后,计算机便开始对卸载过程进行模拟。卸载过程中,模具对工件的作用力逐渐减小,工件随之回弹。计算机对工件回弹中的变形进行计算,模具完全脱离工件后得到了最后形状。通过比较卸载前后工件的形状,可得出工件在卸载中产生的回弹量。
压边力的确定
在计算机仿真分析过程中,压边力太小,工件就会起皱;压边力太大,工件就有开裂风险。当模具方案基本确定后,可根据以往经验粗定压边力大小,再用计算机对成形过程进行仿真。若发现起皱,则加大压边力;若发现开裂,则减小压边力,最后确定一个合适的压边力。
毛坯尺寸的计算
采用计算机仿真技术,能够比较准确地掌握一个零件在冲压过程中的材料流动情况。根据零件的形状和工艺补充需要,在仿真得到的冲压件的最后形状上找出一条边界线,以区分应当保留的部分和可以去掉的部分,再将这条分界线反射到原始毛坯上,就可得到合理的毛坯形状和尺寸。
软件在汽车开发中的应用
以下是利用AUTOFORM软件对某车型侧围外板进行CAE分析的实例。
侧围外板的结构特点、质量要求及精度要求
图3所示为某车型侧围外板零件形状,侧围是由形状复杂的空间自由曲面组成,零件的内部还带有门框和窗口形状。侧围外板是汽车外覆盖件中总体尺寸最大的零件,表面质量要求很高,侧围的表面有三类区域:外观表面、开门后可见表面以及不可见表面,其中外观表面质量要求最高,不允许有开裂、皱纹、凹凸不平、冲击线、滑移线、压痕等缺陷,而且产品特征棱线应清晰。它与侧围有匹配关系的零件最多,包括发动机盖、翼子板、前风窗、前后门总成、前后地板、前后轮罩、后盖、尾灯、密封条等。对侧围要求有很高的尺寸精度,包括轮廓尺寸、孔位尺寸等,以保证焊装和总装的准确性、一致性,侧围还要求有很高的形状精度。
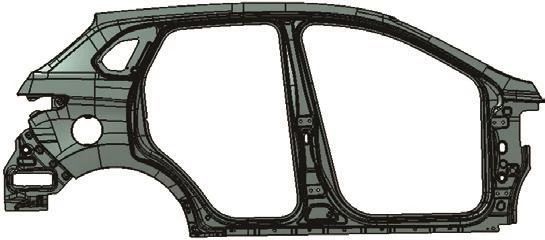
图3 侧围外板零件形状
侧围外板冲压成形的有限元模拟分析
侧围外板属于外覆盖件,要经过拉延、修边冲孔、翻边、整形等工序完成,拉延工序是最重要的,也是难度最大的。工艺设计不当,常常会产生拉裂、起皱等缺陷,给模具调试造成较大的难度,采用AUTOFORM软件的有限元模拟分析计算、深入分析侧围外板成形特征和变形过程的金属流动、合理控制材料流动和应力分布,以避免成形区域局部开裂和起皱的发生,同时为零件的模具调试以及冲压成形质量控制提供技术依据。
⑴建立侧围外板拉延件有限元模型。
1)初始拉延工艺设计。
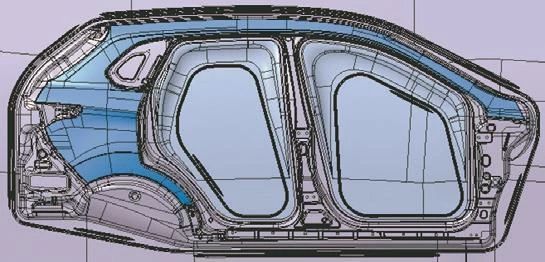
图4 侧围外板拉延型面几何模型
初始型面设计主要依靠工艺设计人员的经验完成,图4所示为用CATIA软件设计完成的侧围外板型面几何模型,它包括产品面、工艺补充面、压料面和拉延筋。产品面是由零件的几何形状所决定的;工艺补充面、压料面和拉延筋是为使产品面达到成形要求而需要增加的部分。设计合理的工艺补充面、压料面和拉延筋是获得高质量产品的关键,工艺设计中通常考虑以下几个方面。
①压料面。确定冲压方向要考虑拉延成形过程中的坯料接触与进料情况,保证接触面尽量大,各处拉延深度尽量均匀,拉延深度的大小决定了产品的成形性。成形性越好,则产品件刚性越好,而且回弹越小,有利于后序整形后获得精度较高的零件,压料面的位置是由适当的冲压方向和拉延深度决定的。
②工艺补充面。做工艺补充面前要考虑产品面的翻边部分,将需要翻边的产品面展开到工艺补充面上。如后序有整形,可适当放大产品部分的圆角和加大立壁拔模角度,工艺补充面是指从产品面边缘延伸出来到压料面的过渡面,工艺补充面的设计要尽可能圆滑,有利于材料流动。
③拉延筋。拉延筋是用来控制和改善材料流动状况的。初步设计拉延筋圆角半径为6mm,高度为5mm,为保证冲压成形性,并方便调整材料的流动速度和流入量,采用双道拉延筋。
2)计算机仿真设置。
首先将在CATIA软件中设计的型面几何模型通过IGS数据转换接口导入AUTOFORM软件中进行网格划分及各项参数设置。AUTOFORM软件用隐式增量有限元法迭代求解进入工序生成器,采用单动拉延工艺,材料为DC06,料厚0.7mm,定义好板料形状(Blank)、工具 (Tool)、拉延筋 (Drawbead)、摩擦系数 (Lube)、工序 (Process)。
举报 0
收藏 0
分享 130
-
乘用车金属冲压
2025-05-29 -
冲压技术在电机叠片制造的应用
2024-09-06 -
车身零部件包边质量控制要点
2024-09-05 -
轻量化技术——热汽胀形工艺技术解析
2024-09-04
最新资讯
-
携手共赴“智”造未来!埃马克推动大
2025-08-27 18:12
-
京东工业发布汽车等九大行业场景采购
2025-08-26 18:11
-
制造现场推动节能革新,电装稳步迈向
2025-08-25 14:04
-
携手共赴“智”造未来!埃马克推动大
2025-08-22 19:41
-
伦福德机脚-汽车平稳行驶的守护者
2025-08-19 16:38