冲压CAE技术在汽车开发中的应用
2018-12-03 23:30:50· 来源:文/艾树良 锻造与冲压
拉延凸模、凹模、压边圈及板料采用壳单元进行几何离散,自适应划分网格,并假定凸模、凹模、压边圈三部分为刚体,然后进入工序(Process)进行设计。拉延过程共分三步,分别是重力(Gravity)、闭合(Closing)和拉延(Drawing)。图5所示为侧围外板拉延起始状态下的有限元模型,凹模在上,凸模在下,三个压边圈在中间,行程为220mm。根据初步计算的仿真结果,反复优化压料面、工艺补充面及仿真参数,确定落料轮廓(图6),同时确定外压边力、门框内压料力和拉延筋强度,为现场模具调试提供参考依据。
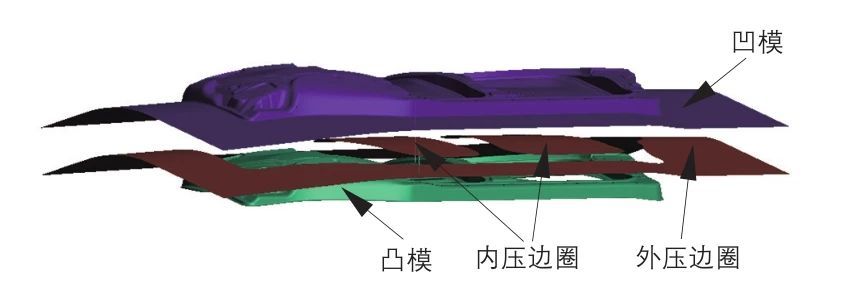
图5 侧围外板拉延件有限元模型
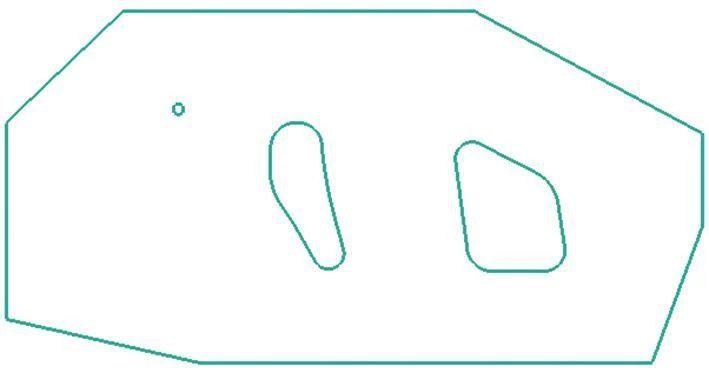
图6 侧围外板落料轮廓
⑵模拟结果分析。
参数设置完成后进行模拟分析计算,对CAE分析结果进行研究,不断修改工艺方案,进行优化处理。调整内容主要包括:压边力、拉延筋、板料轮廓线、型面角度及圆角等。对可能出现的缺陷进行评估,同时提出解决预案。
1)塑性变形。
汽车外覆盖件都具有比较平缓的曲面,通常采用一次拉延成形。为保证零件成形后有足够的刚性和表面质量,必须对塑性变形程度进行控制。塑性变形程度越大,其刚性越好,一般要求毛坯的最小塑性变形伸长率大于3%。图7所示为该侧围外板的拉延成形性分布图,从图中可以看出,B柱上方与顶盖搭接的上边梁部位A区域局部成形不充分。A区域的成形不充分是由于内、外两侧的材料流入不均匀造成的。因为B柱产品结构的限制,内侧材料流动性差。通过调整内外侧拉延筋、压边力和优化门框的工艺孔可以解决。门槛B区域表面变形不充分,原因与A区域相同,采用相同的解决措施。侧围轮罩上方C区域形状相对平坦,位于产品的中部,也容易出现变形不充分情况,产生表面局部凹陷,通过工艺补偿可以解决。
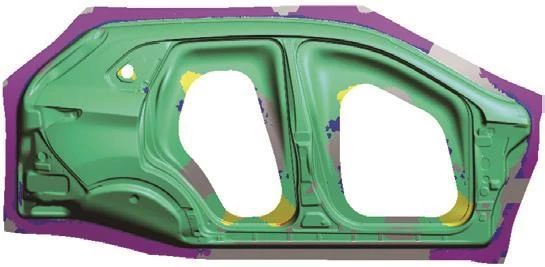
图7 侧围外板拉延成形性分布图
2)起皱分析。
图8(a)是该侧围起皱分布图,侧围在成形过程中,在距拉延到底前40mm时,轮罩下角产生皱纹,但零件最后成形时,皱纹消失,对零件质量影响不大。图8(a)所示的D区域后三角窗位置由于产品造型原因,成形有起皱的风险。在产品设计时,已考虑在D区域增加如图8(b)所示的吸皱筋,这在一定程度上可以避免或减轻因材料线长变化而出现材料堆积的皱纹缺陷。
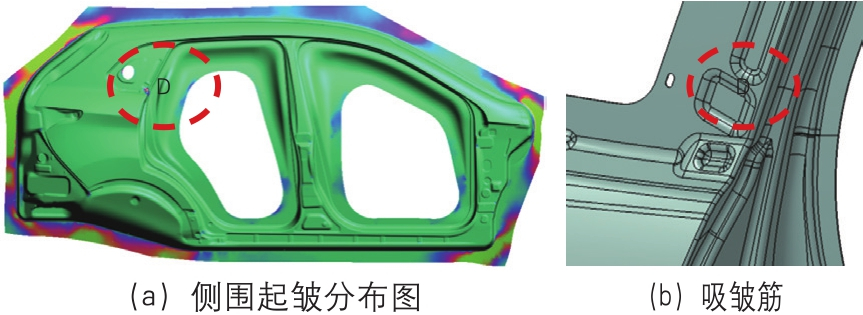
图8 侧围外板拉延起皱分析
3)破裂分析。
图9所示为该侧围减薄分布图,减薄最严重的几个区域分布在尾灯口的E区域和后门洞的F区域,局部最大减薄率达到27%。一般要求DC06材料的最大减薄率不超过20%。由于成形深度较深,侧壁拔模角度和根部圆角较小,材料流动性差,材料过度减薄,成形有开裂的风险。考虑该区域后序有整形工序保证产品特征,拉延工序可以放大侧壁的拔模角度和根部圆角使材料容易流入,解决开裂问题。门框下角的G区域和H区域局部最大减薄率达到25.3%,根部圆角和转角都比较小,容易使材料应力集中,解决预案是调整内侧压边面上的拉延筋、优化门框工艺孔大小。
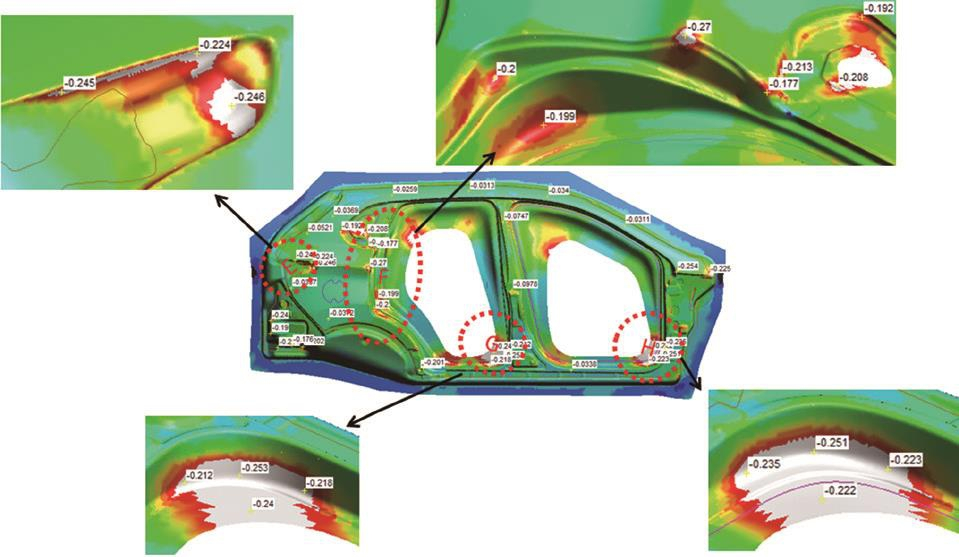
图9 侧围外板拉延材料变薄分析
4)滑移线分析。
汽车外覆盖件产品造型时需要设计一些外观有美感要求的特征棱线,图10(a)所示为产品棱线。这些产品的圆角通常都较小,在零件冲压成形时,凸模棱线的高点与板料接触较早,与凸模高处圆角接触的板料会产生滑动而出现滑移痕迹,从图10(b)中可观察到。为避免在零件外表面出现滑移线,需要保持棱线两侧的进料速度均匀,并控制两侧的材料流入量。
5)冲击线分析。
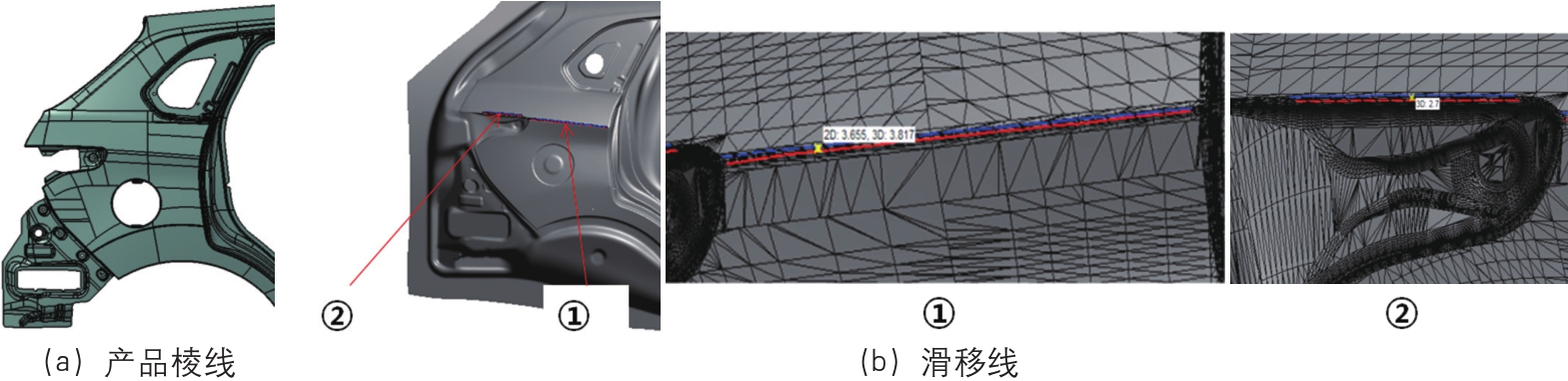
图10 侧围外板滑移线分析

图11 侧围外板冲击线分析
图11 所示为该侧围在上边梁与顶盖搭接区域的冲击线分布图。板料在拉延过程中,凹模口圆角首先接触板料,随着板料向凹模中流入,凹模口圆角在板料上留下痕迹,材料流入越多痕迹越长,这种痕迹就是冲击线。冲击线距离产品外露面可视边界最近处为8.9mm,不会对外表面质量产生影响。对于外覆盖件,冲击线不允许留在外观面上,在产生冲击线的工艺补充侧壁的下半段增加台阶造型,这种台阶造型的凹模圆角初始接触板料的位置比原始的凹模圆角接触板料位置靠外一点,能够储存一定量的材料。并且在板料成形的前半段产生稍大的拔模角度,材料流入量相对较少;在板料成形的后半段,上模台阶的凸圆角接触板料,此圆角处材料开始流动,最后到拉延成形结束。这样来说可以减缓材料成形上半段的材料流动,减缓了冲击线,同时避免了门洞内开裂的问题。
结束语
冲压CAE分析在汽车开发中的应用缩短了整车钣金件的开发周期,节约了大量的开发成本,大大提高了产品的市场竞争力。在国内外汽车企业中,冲压CAE工程是车身零件冲压成形分析中必不可少的环节,利用冲压CAE有限元模拟分析可以提前预测成形中的缺陷和潜在问题,针对出现的问题采取合理的工艺方案,可以消除大部分质量隐患,提高零件工艺设计质量。
—— 来源:《锻造与冲压》 2018年第22期
举报 0
收藏 0
分享 130
-
乘用车金属冲压
2025-05-29 -
冲压技术在电机叠片制造的应用
2024-09-06 -
车身零部件包边质量控制要点
2024-09-05 -
轻量化技术——热汽胀形工艺技术解析
2024-09-04
最新资讯
-
携手共赴“智”造未来!埃马克推动大
2025-08-27 18:12
-
京东工业发布汽车等九大行业场景采购
2025-08-26 18:11
-
制造现场推动节能革新,电装稳步迈向
2025-08-25 14:04
-
携手共赴“智”造未来!埃马克推动大
2025-08-22 19:41
-
伦福德机脚-汽车平稳行驶的守护者
2025-08-19 16:38