铝合金汽车发动机罩外板冲压成形规律研究
2018-12-02 17:18:57· 来源:锻造与冲压 作者:余万铨,胡志力
伴随着日益严峻的环境资源压力以及严苛的节能减排法律法规,轻量化已成为汽车产业发展不容忽视的主题。轻质材料的使用是实现汽车轻量化的重要途经,而铝合金材料以其比强度高、良好的耐腐蚀性及焊接性等优点,在汽车生产中的应用越来越广
伴随着日益严峻的环境资源压力以及严苛的节能减排法律法规,轻量化已成为汽车产业发展不容忽视的主题。轻质材料的使用是实现汽车轻量化的重要途经,而铝合金材料以其比强度高、良好的耐腐蚀性及焊接性等优点,在汽车生产中的应用越来越广泛。但铝合金弹性模量小、室温条件下成形性较差,因此在冲压成形过程中极易出现起皱、开裂、回弹等缺陷,特别是对于结构复杂、相对厚度小、表面质量要求高的大型外覆盖件(如顶盖外板、发动机罩外板等),铝合金材料在成形性上的劣势就更为突出。如何克服铝合金板材在成形性能上的不足,促进铝合金材料在汽车轻量化中的应用,已成为业内关注的热点问题。
通常来说,影响汽车零部件成形性能的主要因素包括零件结构、材料性能、成形工艺以及模具设计等。在车身外覆盖件冲压成形过程中,对冲压工艺参数及模具结构的优化是提高制件成形质量的主要方式。国内外已经有众多学者对铝合金板材在冲压成形过程中出现的开裂、回弹、起皱等缺陷及其影响因素进行了研究,分析了材料性能、模具结构及工艺参数等对冲压成形性能的影响,极大推动了铝合金材料在汽车轻量化中的应用。
本文通过AutoForm软件平台对铝合金汽车发动机罩外板的冲压成形过程仿真分析,研究了模具型面结构优化及相关冲压工艺参数对铝合金板材成形性的影响,同时采用型面补偿的方法有效减小了发动机罩外板的回弹。最终通过冲压试验实现了冲压件的试制,试验结果与仿真优化结果保持了一致性。
模具型面设计与优化
利用三维建模软件CATIA对铝合金汽车机罩外板进行型面优化,其后基于AutoForm软件平台对板料的成形过程进行数值模拟,讨论型面结构优化对板材成形性的影响,主要集中在可成形性与回弹两方面进行研究。
初始型面设计
根据外板的尺寸大小,取坯料尺寸为1850mm×1245mm×1mm,型面结构如图1所示。
利用AutoForm软件平台进行成形分析。材料选用6016-T4铝合金,本构模型采用Ludwik公式:σ=Kεn,其中σ为真应力,ε为对数塑性应变,n和K为材料常数。模拟单元为弹塑性壳单元,设置压边力为850kN,摩擦系数设为0.15,模具间隙设为t(即板料厚度),冲压速度为1mm/s。分析结果如图2 所示,从中可见产品开裂严重,在翼子板与玻璃交接处的圆角、机罩前端都出现了破裂,故该结果不满足成形要求,需对型面进行进一步改进。
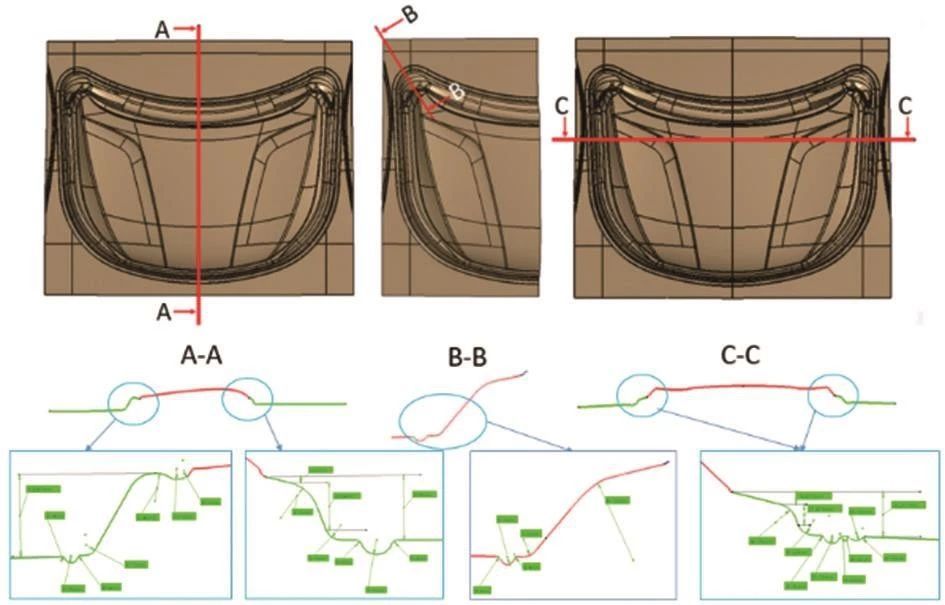
图1 初始型面结构
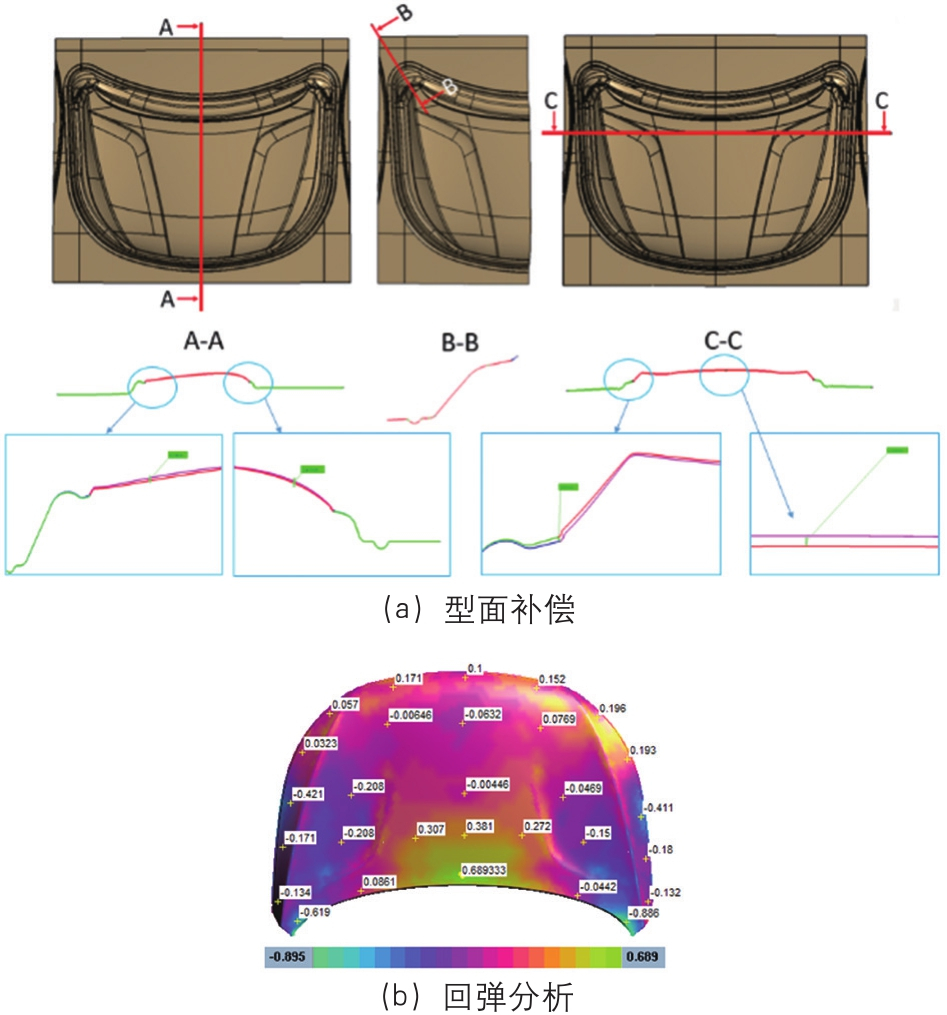
图2 初始型面成形性分析
第一次型面优化
坯料尺寸不变,在初始型面的基础上,在型面两侧增加拉延筋,并将拉延筋半径从8mm增加至10mm,其他较初始型面无改变,型面结构如图3所示。
图4为成形仿真分析结果,虽然开裂问题有所改善,但是挡风玻璃与翼子板交界侧的圆角处仍出现明显破裂问题,需对型面进行进一步改进。
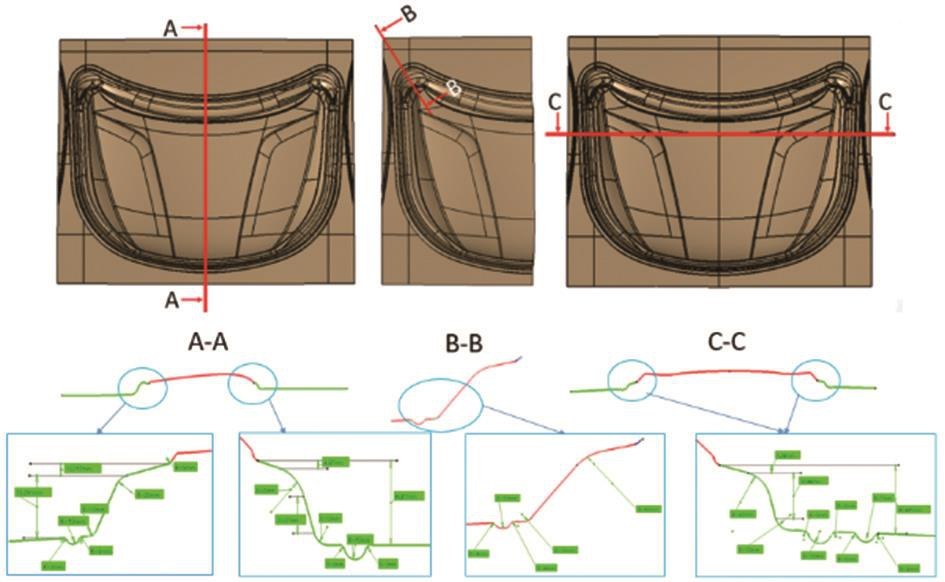
图3 第一次型面优化结构
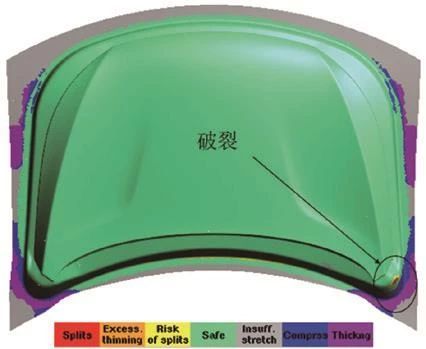
图4 第一次型面优化成形性分析
第二次型面优化
设定坯料尺寸为1929mm×1320mm×1mm,型面结构在第一次优化的基础上在玻璃侧增加余肉造型,增大圆角改善材料流动,并将分模线向外偏移15mm,对圆弧进行适当的优化,其型面结构如图5所示。
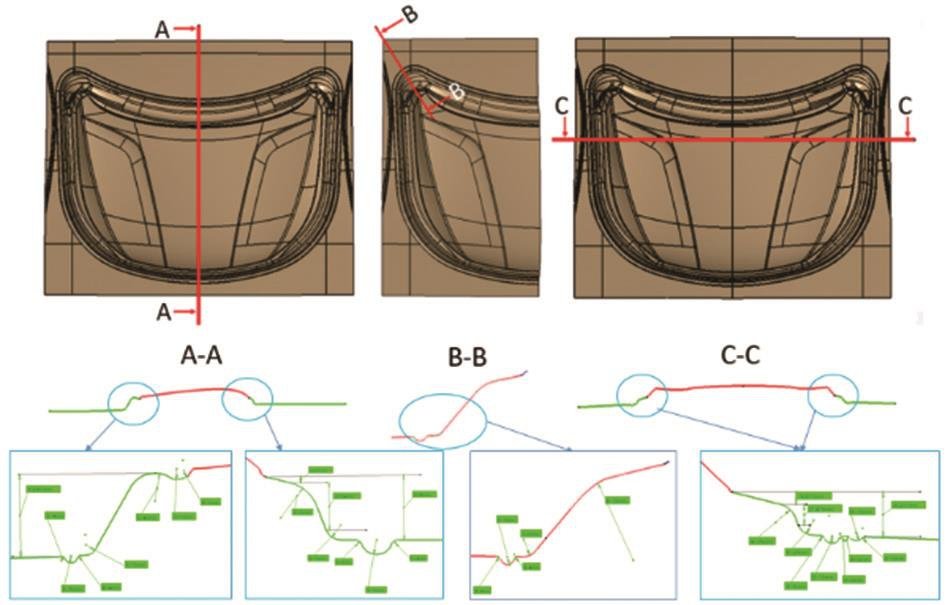
图5 第二次型面优化结构
第二次型面优化结构成形仿真结果如图6所示,图中可见增加的余肉有效地解决了零件破裂问题,优化后的圆弧尺寸及圆角半径使得零件成形充分,减薄率、应变分布均匀,保证了零件的刚度。成形后板料的减薄率最大为0.04%,最小为-21.50%;回弹最大值为5.98mm,最小值为-4.97mm,出现在零件中部靠近挡风玻璃的局部负向回弹区域,回弹量仍然较大。
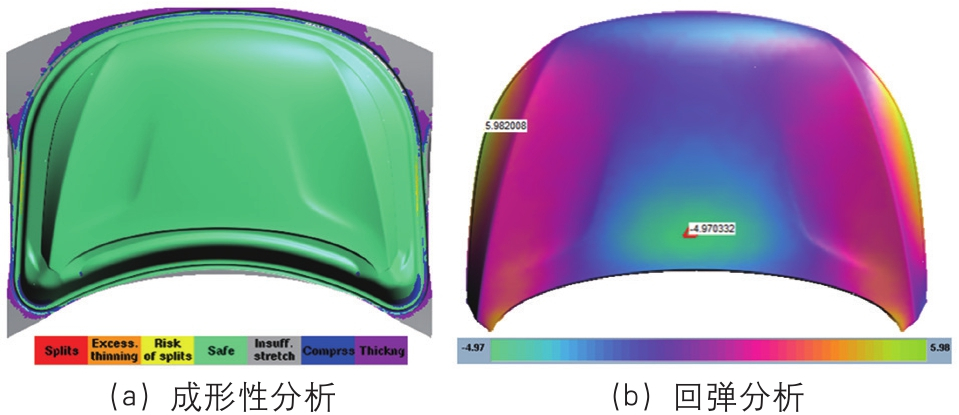
图6 第二次型面优化分析
工艺参数的影响
工艺参数对零件成形质量有显著影响,通常考虑的工艺因素有压边力、模具间隙、冲压速度等。在室温条件下,材料性能随应变速率的变化不明显,因此冲压速度对成形性的影响几乎可以忽略。本文重点关注压边力和模具间隙对成形质量的影响。
压边力的影响
压边力在板材的冲压成形中起到非常重要的作用,通常过小的压边力难以控制材料的流动从而使起皱趋势增大,而过大的压边力则会使材料流动变得困难,破裂趋势增大。同时压边力会影响板料塑性变形中的应力状态,对其成形质量产生影响。采用不同压边力对零件冲压过程进行分析,结果表明随着压边力的增大,外板起皱趋势减小,零件的整体回弹有所减小,但变化不明显,局部区域的负向回弹则出现增大。零件的减薄率与最大回弹量随压边力的变化规律如图7所示。由分析结果可见,外板的起皱趋势随着压边力的增大而减小,减薄率随着压边力的增大而增大,最大回弹都随着压边力的增大而增大。
模具间隙的影响
模具间隙是冲压成形中的重要参数,直接影响模具与板料之间的接触情况,进而影响板料在变形过程中的应力-应变状态,对零件的成形质量影响显著。模具间隙分别设为t,1.05t和1.1t(t为板料厚度),并对零件减薄率和回弹进行了分析(图8)。由分析结果可见,外板的起皱趋势随着模具间隙的增大而增大,减薄率随着模具间隙的增大而减小,最大正回弹随着模具间隙的增大而增大。
回弹控制
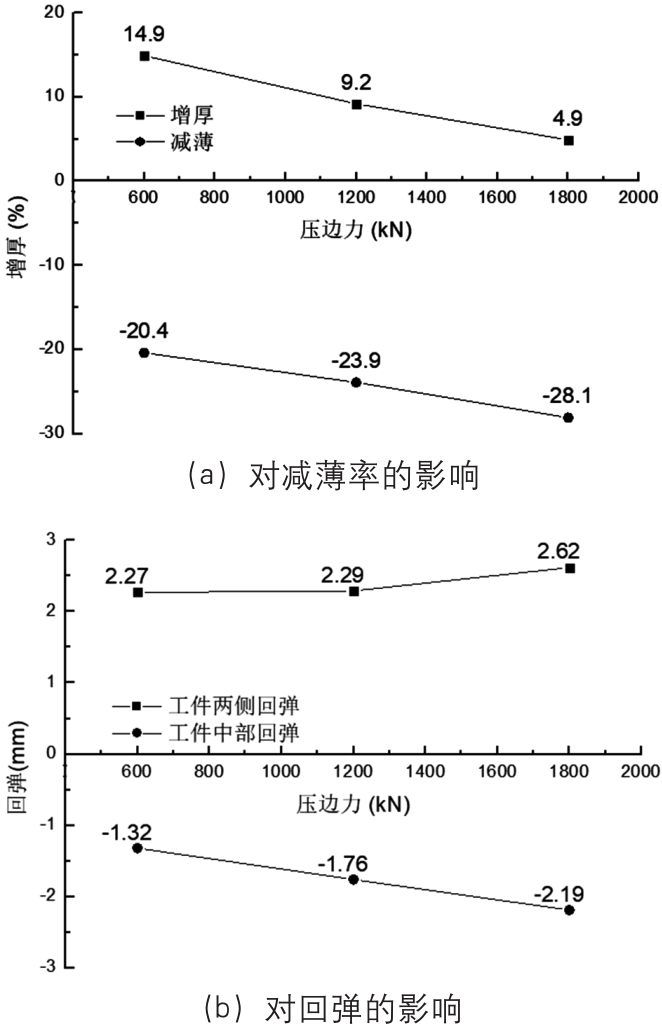
图7 压边力对板料减薄率和回弹的影响
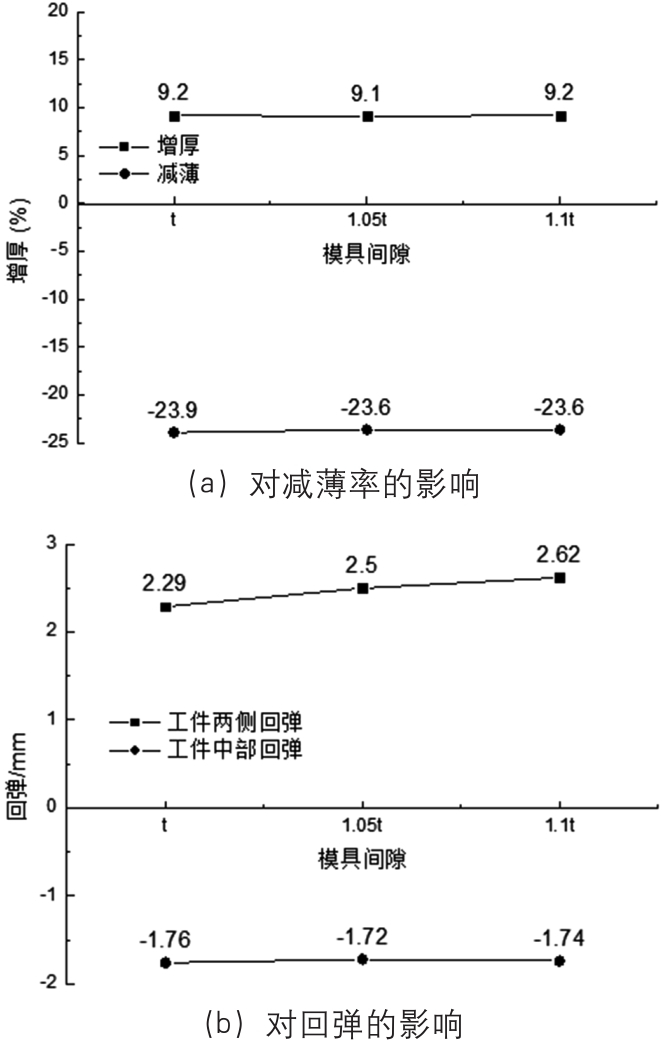
图8 模具间隙对板料减薄率和回弹的影响
如前所述,通过初步的型面优化,零件的可成形性问题得到了解决,但零件的回弹量仍然较大,精度无法保证。在冲压生产过程中,工艺参数的调整对回弹的改善效果有限,型面补偿是解决回弹问题的主要方法,因此在第二次型面优化的基础上,以回弹量为依据,进一步对型面进行补偿优化。同时根据工艺参数对回弹和成形性的影响对其进行调整,达到减小回弹的目的。图9中经型面补偿后零件的回弹可以控制在±1mm以内。
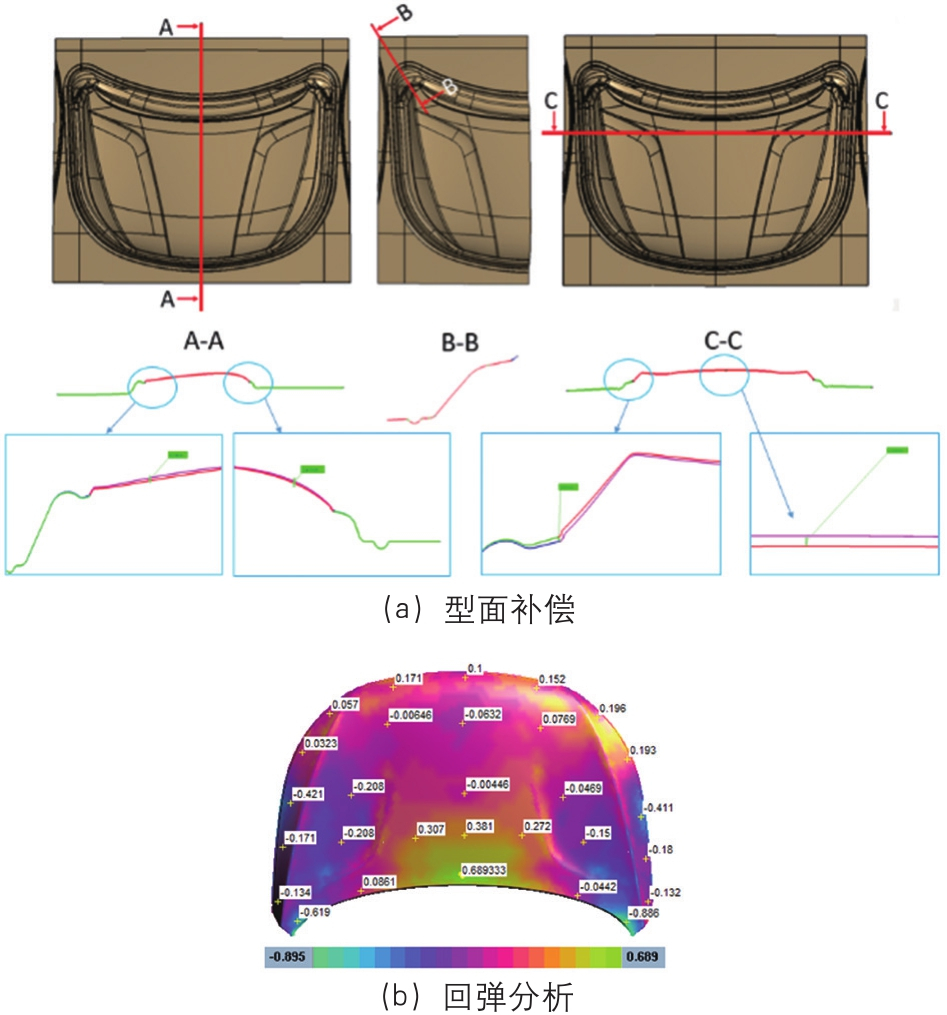
图9 型面补偿及回弹分析
试验验证
基于以上分析和优化,进行模具试制和调试,并对铝合金汽车机罩外板进行冲压试验。试验设备采用800t液压机(图10),所得制件如图11b所示。由仿真结果可见,零件大部分区域的减薄率分布在2%~5%范围内,板料的减薄均匀,保证了零件的刚度,同时最大减薄率为20.59%,避免了过度减薄(图11a),制件易发生破裂的区域(挡风玻璃与翼子板交界侧的圆角处)未出现破裂。另外通过对零件进行精度测试,测得零件的总体回弹量能够控制在±1mm以内(图11b),与仿真结果较为接近,说明实际冲压结果与仿真优化结果取得了较好的一致性。
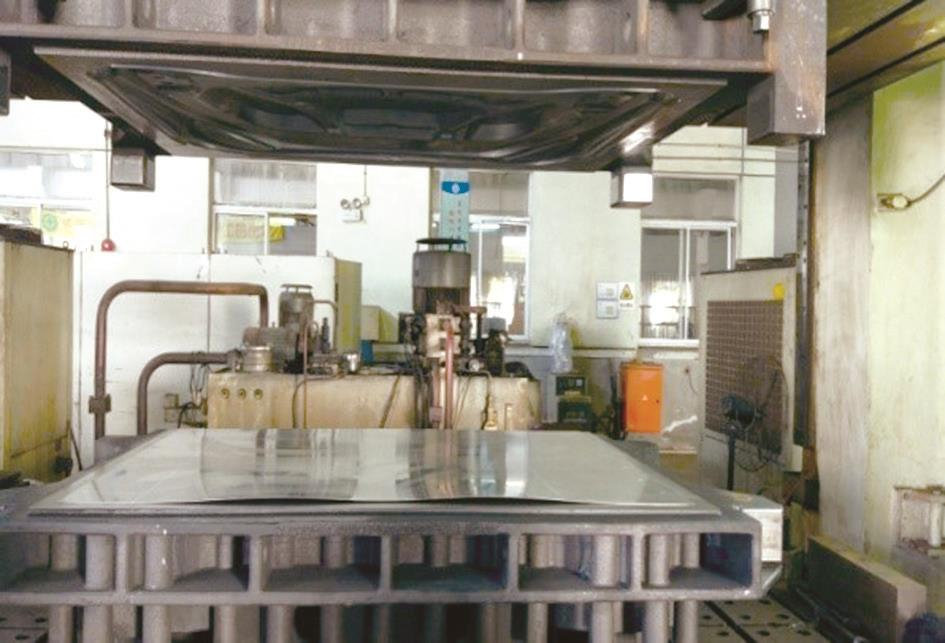
图10 冲压试验设备
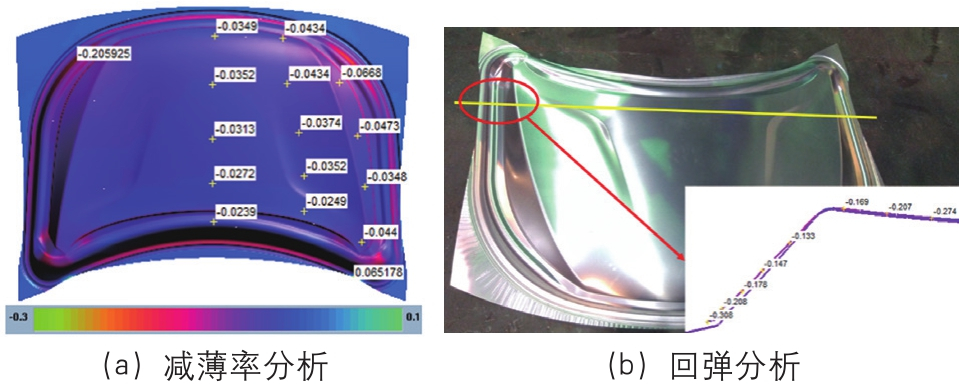
图11 零件减薄率与回弹分析
结束语
通过对铝合金汽车发动机罩外板冲压成形过程仿真分析,优化了模具型面结构,改善了板料流动,进而减少了由局部结构引起的成形缺陷,提高了外板的成形质量。此外还研究了工艺参数对板料减薄及回弹的影响。在600~1800kN范围内,选用600kN压边力和适当的模具间隙有利于缓解板料减薄,提高了零件的精度和强度。我们最终采用了面补偿配合工艺参数调整,使得零件的最大正回弹减小至0.69mm,最大负回弹减小至0.89mm。对铝合金板料成形质量的影响规律研究与模具型面优化,可以作为实际生产的理论基础和重要参考。模具的制造和调试及对发动机罩外板的冲压成形进行试验验证,试验结果与仿真优化结果保持了一致性。
举报 0
收藏 0
分享 117
-
专家访谈:埃马克 OCTG 加工的技术密钥与生产之
2025-06-25 -
Know-How系列 | 石油钻机核心技术揭秘:埃马克
2025-06-19 -
聚焦机床 | 埃马克USC 850数控万能车床:突破大
2025-06-11 -
DMC中国国际模具装备展今日开幕,600+展商齐聚
2025-06-05
编辑推荐
最新资讯
-
跨越速运凭什么“圈粉”万千客户?“
2025-07-01 14:42
-
数智破局启新篇・生态共生再启程 —
2025-06-27 20:13
-
助力汽车零部件产线智能化升级,西门
2025-06-27 13:59
-
BBA集体转向!放弃全面电动化
2025-06-26 17:32
-
比换柜省钱,比自研省心,西门子Xcel
2025-06-25 15:07