基于尺寸和表面质量的顶盖模具型面补偿方法
2019-06-10 12:09:28· 来源:锻造与冲压 作者:赵中元,王林
针对奥迪车型天窗顶盖冲压模具,提出在设计阶段通过对各工序模具进行型面补偿来保证零件的质量;结合产品质量要求,确定型面补偿内容为零件型面尺寸的回弹补偿和局部表面的凹陷补偿;结合型面补偿的流程,采用有限元分析软件,对全工序的
针对奥迪车型天窗顶盖冲压模具,提出在设计阶段通过对各工序模具进行型面补偿来保证零件的质量;结合产品质量要求,确定型面补偿内容为零件型面尺寸的回弹补偿和局部表面的凹陷补偿;结合型面补偿的流程,采用有限元分析软件,对全工序的型面回弹进行数值模拟分析,确定模具型面的补偿方案和补偿量,最终应用于实际生产,得到较为理想的结果。
顶盖作为车身关键外覆盖件之一,其冲压件的质量直接影响着后续的焊接工艺和车身的最终质量;奥迪车型由于其自身质量标准以及顶盖与侧围采用激光焊接工艺,因而对顶盖冲压单件的尺寸精度和表面质量有着相对更高的要求。然而由于钢板材料本身的特性以及顶盖产品结构的特点,零件在冲压成形后会产生回弹且无法避免;进而导致零件尺寸发生偏差以及表面产生一些无法避免的质量缺陷。在模具调试阶段对这些问题进行优化时,往往需要对型面进行频繁的烧焊甚至将模具降面,影响模具的制造进度,成本也大幅提高。如果在设计阶段,根据产品质量要求和以往车型的实际生产经验,结合数值模拟分析,对模具各工序型面进行合理的补偿,那么不仅可以有效保证零件的质量,还可以大幅提高效率,降低模具制造成本。
产品特征及冲压工艺概述
天窗顶盖产品如图1 所示,产品外表面为一张A级曲面;按照顶盖在车身上的位置、产品结构主要可以分为以下几个区域:前风窗区域A、与侧围激光焊接区域B、天窗区域C 和尾部(近背门处)流水槽区域D,从各区域轮廓线法向的截面特征可以看出,产品四周相对于整车Z 向均为负角,流水槽区域形状较为复杂,而且深度也相对较大。
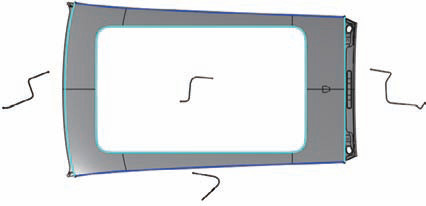
图1 典型顶盖产品
根据产品结构特征,结合冲压工艺设计的基本理论,其冲压工艺设计如图2 所示,共需要六道工序:前风窗区域通过拉延、修边、整形、斜楔整形及冲孔五道工序成形;侧围焊接区域通过拉延、修边、翻边及斜楔翻边四道工序成形;天窗区域采用拉延、修边、翻整三道工序成形,其中翻整工序采用夹料整形;流水槽区域的成形工艺直接影响着零件最终质量,成形难度相对较大,需要拉延、预修边、一次整形、斜楔整形、修边冲孔、上翻加切边六道工序成形,并且一次整形和斜楔整形的区域两侧采用压料整形,以保证成形质量最优及调试便捷。
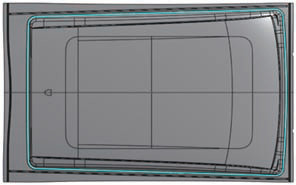
(a) OP20 拉延
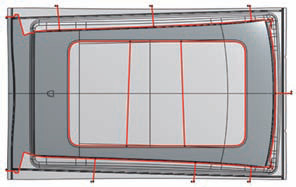
(b) OP30 修边
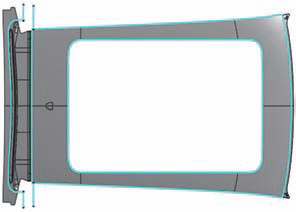
(c) OP40 翻整
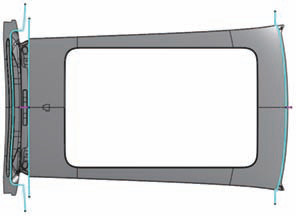
(d) OP50 侧整
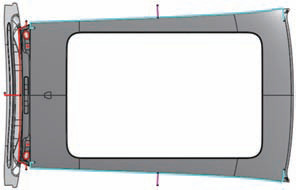
(e) OP60 侧整修边
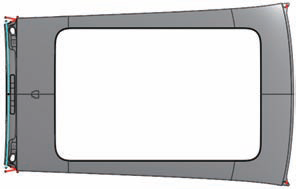
(f) OP70 翻整修边
图2 冲压工艺
型面补偿内容
尺寸
顶盖产品本身曲率较小且单一,产品刚度相对较差,结合多个车型的生产经验,刚度不仅影响着冲压件尺寸和表面质量的稳定性,也对焊接工艺的稳定性有着较大的影响。为保证成形后的产品刚性,要求中心区域自由型面尺寸控制在0.5 ~ 1.0mm 之间,即保证顶盖稍外凸;为保证匹配间隙和目视效果,车身前后两端和天窗的轮廓公差要求为±0.3mm;车身两侧与侧围搭接区域轮廓要做到0 ~ 0.5mm,并且长度在300mm 内尺寸偏差的波动量不超过0.2mm,以保证激光焊接的焊缝质量;在主型面尺寸稳定合格的前提下,只要对轮廓进行了合理的公差偏移和加工偏差预留,对翻边工序预留合理的回弹角,那么轮廓尺寸便比较容易保证,因此尺寸保障的关键在于对主型面进行回弹补偿以保证零件主型面尺寸合格。
表面质量
图3 为完成天窗和流水槽区域成形后,结合应力状态,对可能产生表面缺陷区域的模拟预测,通过模拟结果可以看出,产生表面缺陷的区域主要有产品四角、天窗四角和流水槽上方的表面;由于产品造型和冲压工艺的特点,成形结束零件内部应力释放后,局部会存在残余应力,且应力分布不均匀,从而使零件产生表面缺陷,工艺上很难消除,实际生产经验也确实如此。对于表面区域,要求黑车无扣分项;对流水槽结构面的区域,由于是内可视区,同样要求无起皱、冲击线等缺陷;产品四个角部以及结构面部分表面质量通过合理的冲压工艺以及后续调试比较容易保证;难点是天窗四角和流水槽上方的表面凹陷,尤其是天窗角部在安装完天窗之后,表面质量经常会发生恶化,从而对单件的要求更高;因此需要通过对局部型面进行凹陷补偿,以保障零件的表面质量。
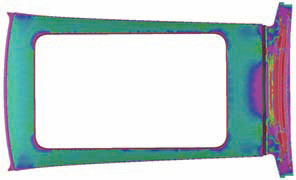
图3 表面缺陷预测
型面补偿方法
补偿流程概述
通过前述分析,为保障零件质量,需要对顶盖的模具型面进行针对尺寸回弹和局部表面凹陷的补偿;型面补偿进行的前提是冲压工艺模拟的各项评价指标,如减薄率、起皱开裂、滑移线、冲击线等能够满足质量要求并且工艺足够稳定,即工艺“最优化”;整个工作流程如图4 所示,首先结合零件的测量方式,对全工序进行精确回弹模拟,根据各工序的回弹模拟结果,分析回弹产生的原因和工序,如果回弹后的零件尺寸无法满足产品公差要求,则根据回弹产生的工序确定回弹补偿方案,结合产品公差要求和回弹量确定补偿量;补偿之后,对结果进行二次模拟验证,保证回弹之后的尺寸在公差允许的范围之内,然后进行各工序的模面替换,最后对局部区域进行表面凹陷补偿,完成整个补偿工作。
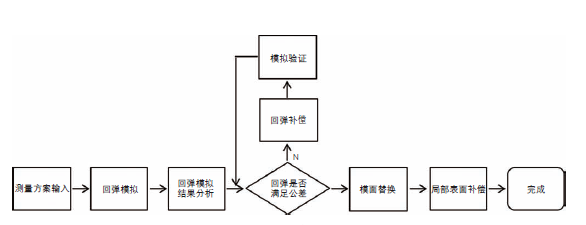
图4 型面补偿流程
弹模拟分析
采用Autoform 分别对各工序的回弹进行模拟,回弹模拟的参数设置按照Autoform 软件标准。实际生产过程中,单件的测量过程是在测量支架上完成的,支架形式如图5 所示;由于产品本身刚性较差,产品自身重力也会对成品件的回弹结果产生一定的影响,因此回弹输出结果是综合考虑重力和夹持状态的回弹,但过度的夹持也会导致型面发生扭曲,真实的回弹被强行消除,从而使回弹补偿无法实现;因此考虑采用一种优化的夹持方案,即仅考虑支撑和图5 处标示的夹持,以保证回弹结果能够真实的体现出实际状态。
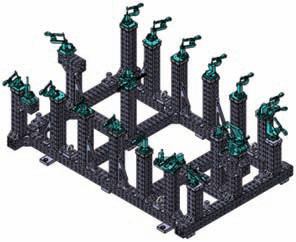
图5 测量支架
图6 为各工序成形完成后的回弹状态,OP20 拉延成形后,拉延件中部稍有塌陷,周边法兰发生翘曲。OP30 切边后应力释放,零件中部塌陷显著增加;OP40 四周及天窗翻边完成后,产品初步定形,回弹后前角翘曲,中部塌陷;OP50 前后侧整形之后,翘曲显著增大;OP60 相对前序,趋势一致,但区域和回弹量有所变化;OP70 由于仅对局部进行翻边成形,对整体型面的回弹影响不大,回弹结果与OP60 基本一致。
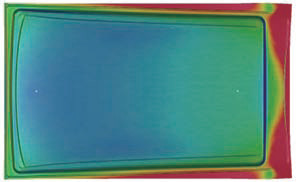
(a) OP20 拉延
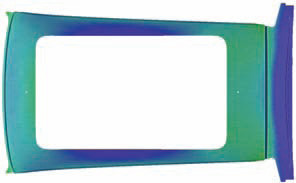
(b) OP30 修边
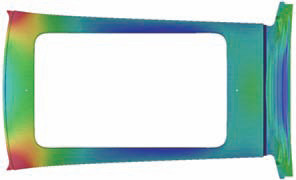
(c) OP40 翻整
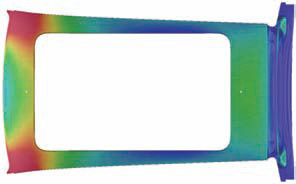
(d) OP50 侧整
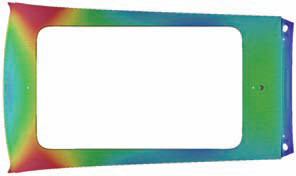
(e) OP60 侧整修边
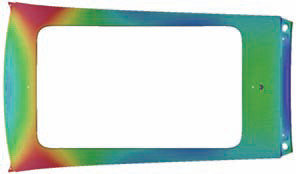
(f) OP70 翻整修边
图6 各工序回弹状态
型面补偿
综合上述分析,结合表面质量优化,型面补偿方案设计如图7 所示,在OP20 到OP60 对主型面进行尺寸回弹补偿,在OP50 对流水槽局部型面进行尺寸回弹补偿;在OP40 对天窗角部表面缺陷进行补偿;在OP40 和OP50 对流水槽区域的表面缺陷进行补偿;侧翻边回弹角度按照1.5°~ 3°预留,OP70 不采取补偿。根据计算得到的回弹结果和表面调试相关经验,补偿区域见图8a 和8b,尺寸方面,两个前角下压4mm,中间型面隆起1.2mm;流水槽局部补偿0 ~ 1.5mm;表面方面,天窗四角补偿0.05 ~ 0.15mm,流水槽上方补偿0 ~ 0.2mm。补偿后的回弹模拟结果见图8c,模拟结果基本达到了预期。
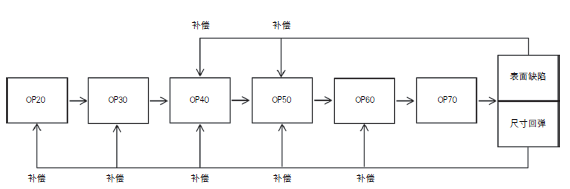
图7 型面补偿方案
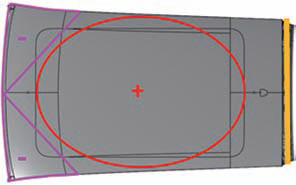
(a) 尺寸补偿区域
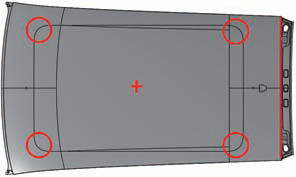
(b) 表面补偿区域
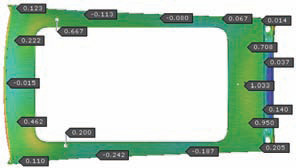
(c) 补偿后回弹结果
图8 补偿区域和最终结果
实际零件质量
采用补偿后的模具型面制造模具,模具加工装配完毕,完成各工序着色研配和翻边间隙确认后,零件的尺寸状态和天窗口的表面质量状态如图9 所示,型面尺寸基本控制在公差内,中间区域的最大量在1mm 左右;达到了预期效果,焊接后白车身质量没有问题,未进行二次整改;天窗前角基本无缺陷,后角为C1 类缺陷(单件油石打磨局部不连续,后续黑车光影稍有不顺,用户不会抱怨),流水槽上方也是C1 类缺陷;由此可以看出,通过前期对型面进行补偿,很好地保证了零件的质量,相较于以往车型的多轮整改,大大提高了效率。
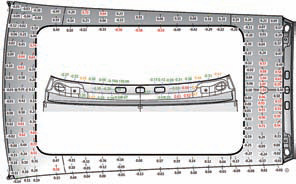
(a) 型面尺寸
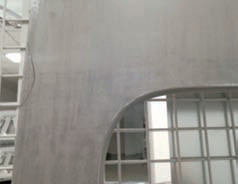
(b) 天窗前角
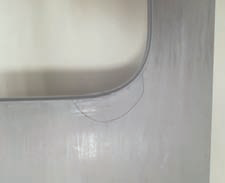
(c) 天窗后角
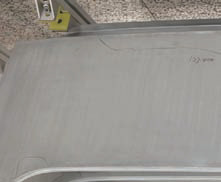
(d) 流水槽上方
图9 实际零件的尺寸和表面状态
结束语
对于冲压模具制造,在满足零件质量要求的前提下,如何降低模具成本和缩短制造周期,是业内人士不断探讨的话题;在前期设计阶段,结合以往生产经验,对零件的质量缺陷进行分析预测,并采取有效措施,无疑会带来非常明显的效果;本文基于某车型顶盖,对设计阶段采用型面补偿来保证零件质量的整体思路和方法进行了论述;首先通过对零件质量要求的分析论述,得出主型面的尺寸精度和局部的表面质量是保证零件质量达标的关键;据此确定型面补偿是针对尺寸回弹和局部表面凹陷两方面内容的补偿;按照补偿流程,通过数值模拟分析结合实际生产经验,确定了各序型面的补偿方案和补偿量。采用补偿后的型面制造冲压模具,最终获得了理想的结果。希望这种针对型面尺寸和表面质量的补偿思路能够给制造高品质冲压外覆盖件模具提供一定参考。
举报 0
收藏 0
分享 132
-
乘用车金属冲压
2025-05-29 -
冲压技术在电机叠片制造的应用
2024-09-06 -
车身零部件包边质量控制要点
2024-09-05 -
轻量化技术——热汽胀形工艺技术解析
2024-09-04
最新资讯
-
携手共赴“智”造未来!埃马克推动大
2025-08-27 18:12
-
京东工业发布汽车等九大行业场景采购
2025-08-26 18:11
-
制造现场推动节能革新,电装稳步迈向
2025-08-25 14:04
-
携手共赴“智”造未来!埃马克推动大
2025-08-22 19:41
-
伦福德机脚-汽车平稳行驶的守护者
2025-08-19 16:38