浅谈数据分析在薄板自动冲压线产能提升中的应用
2019-04-04 23:51:43· 来源:李明昕,吕良等 锻造与冲压
目前,各整车厂基本都建有自己的全自动化冲压生产线,并且进一步实现生产的信息化、数字化管理,掌控设备、模具实时动态,确保自动冲压生产线生产节拍发挥产能优势,同时提高冲压件质量。我厂冲压自动线建成投产后,产能优势一直未发挥出
目前,各整车厂基本都建有自己的全自动化冲压生产线,并且进一步实现生产的信息化、数字化管理,掌控设备、模具实时动态,确保自动冲压生产线生产节拍发挥产能优势,同时提高冲压件质量。我厂冲压自动线建成投产后,产能优势一直未发挥出来,随着近两年整车销量的上升,造成了自动线生产负荷大的局面。为提升自动冲压线的产能,本文结合我厂自动化冲压生产线,阐述了生产数据的分析对于产能提升的帮助。
自动冲压生产线构成
我厂规划建成5600 吨的全自动冲压生产线,主要由拆垛系统、清洗机、涂油机、对中装置、机械压力机以及单臂机械手输送系统构成,如图1 所示。主要负责平台车型的大型驾驶室覆盖件的生产任务,规划产能为10 万辆,规划生产节拍为8 ~ 12spm。

图1 自动化冲压生产线组成示意图
自动化冲压生产线刚建成投产,初始生产任务少,GSPH 值只有180 左右。随着整车销量的提升,自动线的生产负荷达到140% 之多。为保证生产,生产线只能通过工作日拖点和休息日加班补足产能短板,因此提升自动化冲压生产线的产能迫在眉睫。
生产信息的统计和分析
生产信息统计表设计
为分析影响产能的主要因素,需要对自动化冲压生产线的生产情况进行全面的掌握。同时,为了尽快应用,我们根据需要编制了生产信息统计表,如图2所示。
图2 生产信息统计表示意图
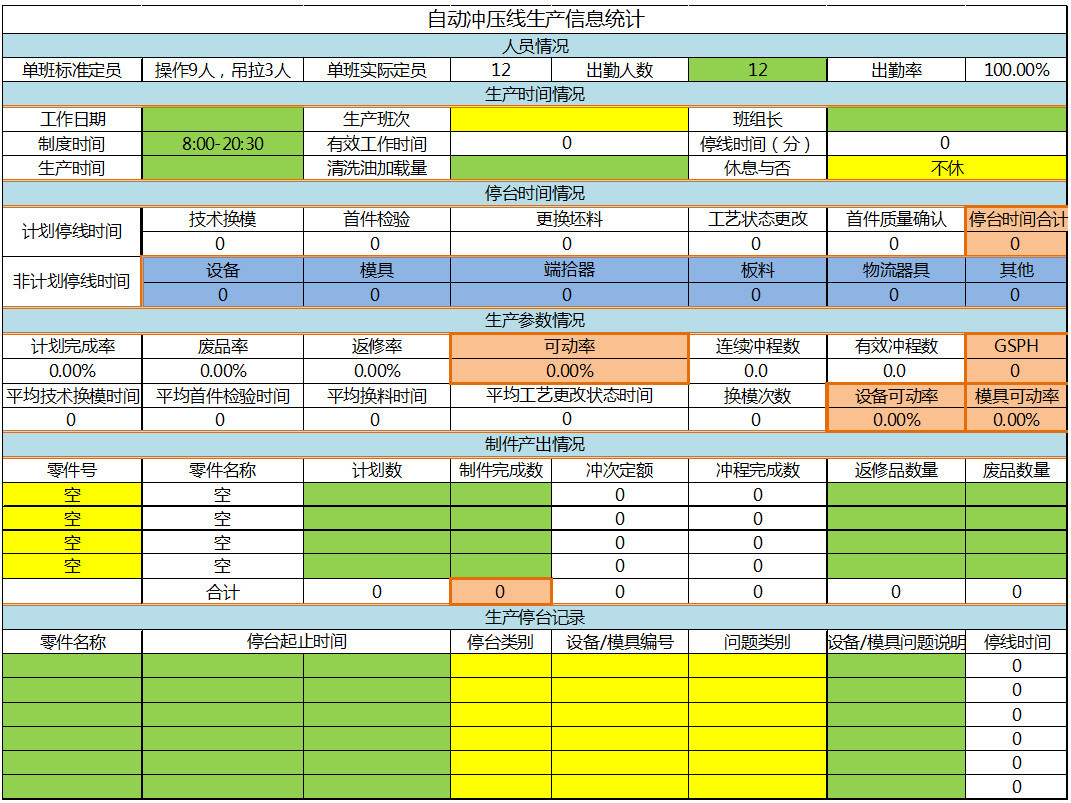
生产线工人需要在生产信息统计表中录入生产时间、班组、生产制件种类、数量、停台问题以及停台时间等项目。通过生产信息统计表就可以观察每班生产可动率、生产效率(GSPH 值)等数据。另外,通过在Excel 表中使用一些函数和VB 程序对整个月的统计信息实现汇总,从而可以分析影响生产效率的因素。
生产信息统计分析
通过每天生产班次填写生产信息统计表,最终将需要关注的信息进行汇总。汇总主要分为两部分,一是各统计项的汇总,如模具、设备停台、GSPH 值等;二是每套模具的停台问题汇总,如表1、表2 所列出汇总表的部分内容。
表1 生产信息统计项汇总表(部分)
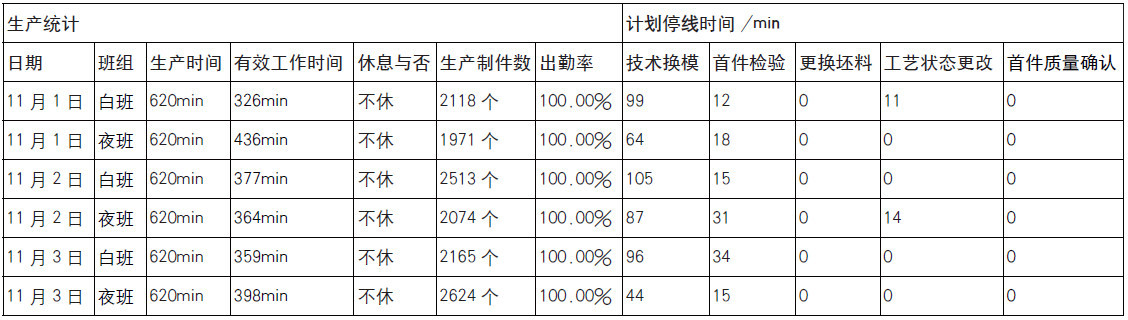
表2 模具停台问题汇总表(部分)
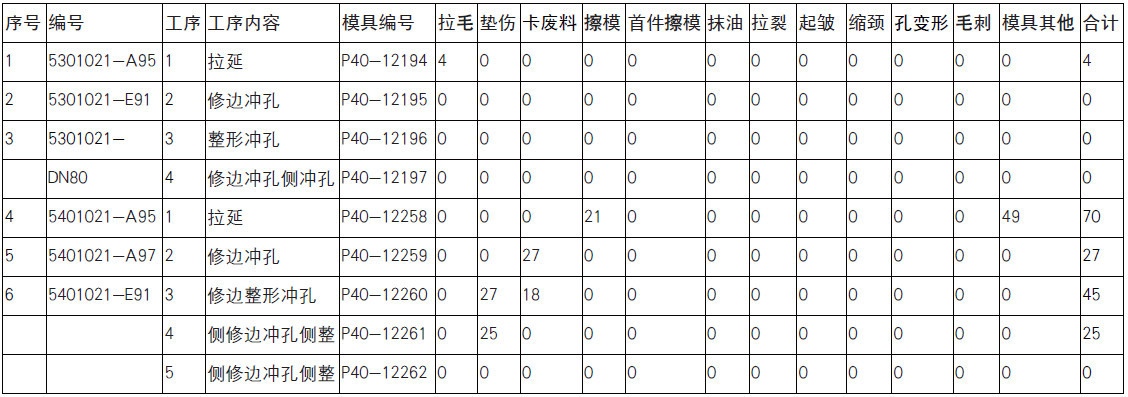
通过数据汇总之后就可以分析影响停台的主要因素,以及分析各项数据的波动规律和趋势,如图3 列出部分数据的统计分析。
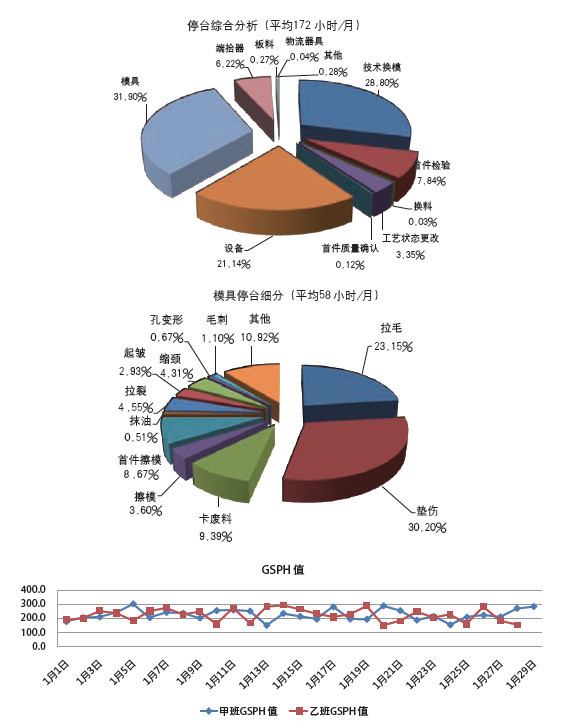
图3 生产统计信息汇总分析图
通过生产数据的统计分析,可以明显的看出影响生产效率的因素主要有模具、设备和技术换模,如图4 所示,这三项的停台时间已经占据总停台时间的82.6%。因此,要提高自动化冲压生产线的产能,首先就需要减少模具、换模和设备的停台时间。后面我们主要围绕这三个方面研究解决措施,以提高自动化冲压生产线的产能。
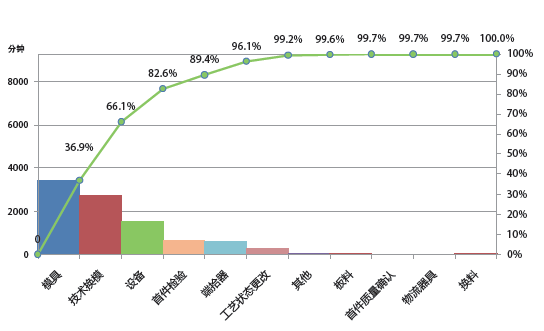
图4 冲压自动线停台时间帕雷多图
产能提升措施
围绕产能提升,我们采取了多项措施,并取得了明显的效果,生产线效率得到了较大的提升。
减少模具停台
影响模具停台时间的主要是因制件垫伤和拉毛而导致生产线停线,如图5 所示。为解决拉毛和垫伤问题,我们通过前面的模具停台问题汇总表确定了拉毛和垫伤停台时间较长的模具和制件。
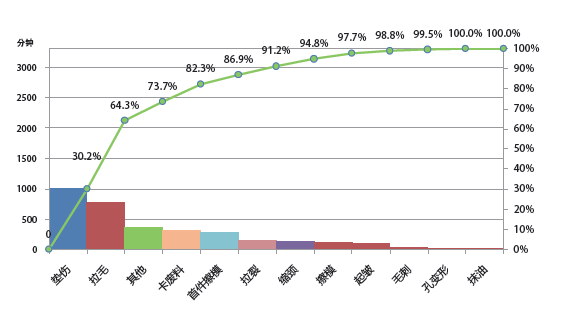
图5 冲压自动线模具停台时间帕雷多图
针对表3 所示10 套拉毛停台时间比较长的模具,我们通过采用模具型腔表面电镀铬(在型腔表面增加一层TiN,提高模具表面硬度),减少制件的拉毛。通过对模具实施电镀,上述10 套模具的拉毛停台时间逐渐降低,在12 月份已经降为0,效果非常理想,所有模具的拉毛停台时间也降至132 分钟,有效地解决了模具拉毛停台。
针对垫伤停台时间比较长的制件,我们主要通过对模具加强维护保养、清除废料屑等措施来改善。虽然后期垫伤停台时间有所降低,但是效果并不理想,后面将进一步研究解决措施。
缩短换模时间
由于我厂的自动化冲压生产线制件品种多达52种,模具190 套,后期随着新车型的导入,制件品种将达到59 种,模具221 套。为满足生产,每班次需要生产4 ~ 5 种制件,因此换模时间的长短对生产时间的影响不断增加,通过图4 可以看出已经成为影响生产效率的第二大因素。
为了减少换模时间,我们采取了以下措施:
⑴对托杆非免换模具进行改造,改造完成后对仍然存在干涉的托杆,在托杆上加工数字标识,如图6所示,更换模具之前将相应托杆拔除,从而在一定意义上实现两侧工作台托杆完全免换。
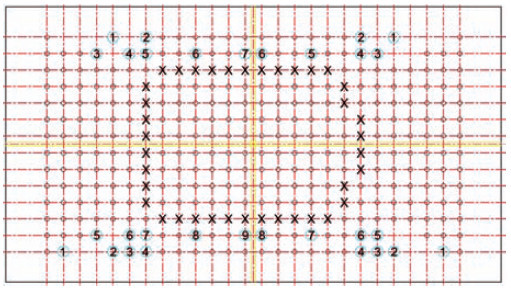
图6 干涉托杆布置示意图
⑵理顺换模流程,对每个环节进行分析,研究缩短换模时间的可能性。通过建立换模时序图,发现在压力机滑块从装模高度调整到闭合高度这部分时间导致换模时间较长,如图7 所示。我们还建立了每串模具相互之间进行换模的时间梯图,如图8 所示。

图7 自动换模时序图
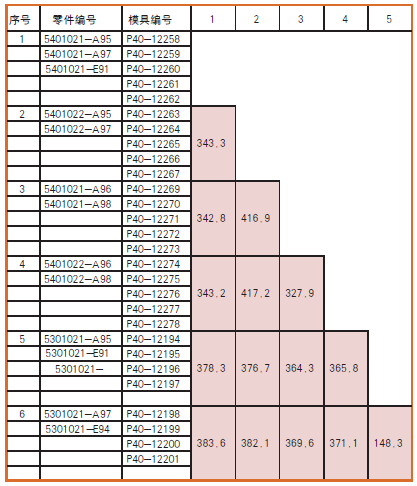
图8 滑块调整时间阶梯示意图
为了降低滑块调整时间,由于模具采用柔性存放,我们将装模高度调整至闭合高度加20mm 的大小,从而降低滑块调整时间,通过阶梯图计算滑块平均调整时间可以由325 秒降至135 秒,节省换模时间3 分钟,最大调整时间降至8 分钟。目前,此项工作正在对每串模具进行验证实施。
通过上述已经采取的措施,换模时间已经由平均24 分钟降至平均19 分钟,取得了一定的效果。
提高单件生产节拍
设备停台问题具有随机性,不可控制性,为了弥补设备停台带来的产能损失,我们对每种制件的整线生产节拍进行了提升。首先,确定了可以提升生产节拍的31 种制件明细,如图9 所示。通过分步实施和解决提升过程中出现的问题,31 种制件的平均生产节拍由6.3spm 提升至7.4spm。
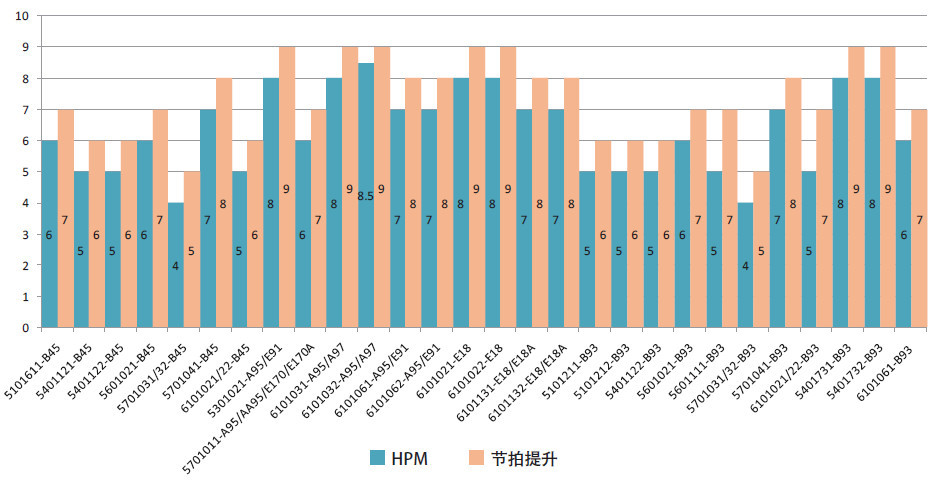
图9 制件生产节拍提升对比图
产能提升效果
通过自动化冲压生产线数据的收集和分析,我们找到了主要问题点,制定相应的措施,一些措施取得了很好的效果,一些措施还需进一步细化实施,一些问题仍需研究解决方法。通过前面几项主要措施以及其他措施的实施,最终自动化冲压生产线的GSPH 值由180 上升至240,如图10 所示。后期,我们将继续围绕自动化冲压生产线的产能提升开展工作,进一步提高自动冲压线的生产效率,满足产能需求。
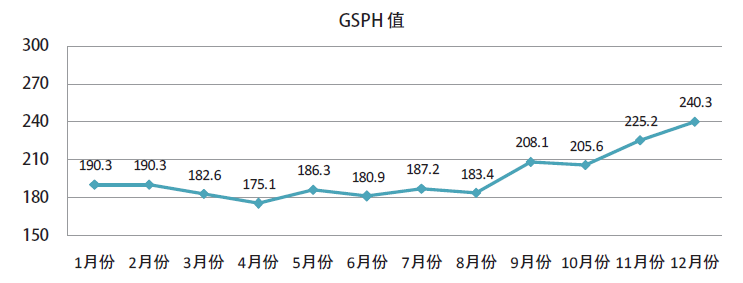
图10 自动化冲压线GSPH 值统计图
结束语
目前,整车制造生产由自动化向智能化生产转变,整车工厂也由制造向智造发展,整车的生产、质量、设备数据的采集、分析也将变得越来越重要。前面,通过使用Excel 表格实现了自动冲压生产线生产数据的统计和分析,为我们提高生产线的产能提供了帮助,同时为我们后期实现数据的联网统计和自动分析奠定了一定的基础。在智能制造上,我们还有很长的路要走,未来智能制造技术一定能为产品设计开发和产品质量提供强有利的支撑。
——本文节选自《锻造与冲压》2019年第6期
举报 0
收藏 0
分享 132
-
乘用车金属冲压
2025-05-29 -
冲压技术在电机叠片制造的应用
2024-09-06 -
车身零部件包边质量控制要点
2024-09-05 -
轻量化技术——热汽胀形工艺技术解析
2024-09-04
最新资讯
-
携手共赴“智”造未来!埃马克推动大
2025-08-27 18:12
-
京东工业发布汽车等九大行业场景采购
2025-08-26 18:11
-
制造现场推动节能革新,电装稳步迈向
2025-08-25 14:04
-
携手共赴“智”造未来!埃马克推动大
2025-08-22 19:41
-
伦福德机脚-汽车平稳行驶的守护者
2025-08-19 16:38