汽车总装工艺内部物流模式的突破
2018-12-25 20:17:43· 来源:汽车供应链物流规划与改善
本文对中国汽车制造业总装车间的内部物流进行了深入分析,目前汽车制造业普遍推行精益生产方式,该方式的主要特点是:多品种小批次随机混流生产。随着品种的增加,批次的减小,汽车零件按车型种类供给的不断增多与线边零件存放面积不足的
本文对中国汽车制造业总装车间的内部物流进行了深入分析,目前汽车制造业普遍推行精益生产方式,该方式的主要特点是:多品种小批次随机混流生产。随着品种的增加,批次的减小,汽车零件按车型种类供给的不断增多与线边零件存放面积不足的矛盾日益凸显。以往采用的解决方案是通过增大线边零件存放面积来缓和该种矛盾,但目前可增加的空间已趋于饱和而且此种方案还会带来库存增加,作业取料损失加剧,内部物流复杂混乱等一系列负面影响。因此我们借助现代IE技术,对此种问题进行革新性的改善,同时也为IE技术在汽车制造业的发展运用方向进行探索,本次将以某公司总装底盘线综合物流改善为例,对于上述观点进行说明。
一、某公司IE推进现状
早在80年代末,此公司就引进了日产柴“一个流”的生产方式,经过7个月的推进,在当时此公司生产能力最薄弱的环节上获得了成功:当年转向节生产线产量增长了29.8%,人员减少28%,废品率下降68%,在制品减少79.9%,设备故障停工率下降了84%。而合资方日产汽车公司在推进工业工程方面也形成了一套完整的推进方法。可以说在合资公司成立之前在IE推进方面就已经打下了较好的基础。
合资后此公司非常重视IE部门的建设,在成立之初就在某工厂建立了IE/GK科(GK是日语中现场管理的缩写)。目前IE/GK科有工程师11人,改善员11人,改善中心装配场一处,负责工厂的中期方针规划、工厂及各科室关键绩效指标的设定、日产生产方式的推进、制造成本的管理、劳动生产力的提升和现场改善活动的推进等重要工作。从职能上看,包括了IE的三个技术群:分析型技术群、规划与设计型技术群和管理与控制型技术群,而且还成立了一个专职进行低成本自动化技术应用的改善中心。
此公司还非常重视IE学科的建设,近几年一直保持与清华大学工业工程系的良好合作关系,每年接收清华实习生进行工厂实习。公司还关注IE学科新兴技术的发展,定期派员参加国内外的学习进修,并于2007年购置专业仿真软件EXTEND,投入力量进行应用研究,并取得显著的效果。
二、此工厂总装底盘线物流综合改善案例
1.工厂背景介绍
此工厂是此公司主要的成品车生产厂,产量达到此公司全部产量的80%左右,截至2008年10月,累计生产820,688台。工厂采用模拟订单化生产,完全混流模式,工厂产能设计为年产36万台。
2.总装车间背景介绍与案例总体介绍
总装车间是此工厂占地最大、人员最多、产能最大的车间。2004年5月建成,占地58500平方米,共有两条装配线,最大设计产能45万台/年。目前生产车型为8种,无规则混流上线。总装车间总人数为932人。
此案例是通过对底盘线线边物流现状与需求矛盾的分析,依次展开供料模式、运输模式和布局优化等方面,揭示总装工艺内部物流的变化趋势,探寻IE 新兴技术与现场改善的结合点。
在此案例中,可以看到线边供货模式从“One Pitch”(单品供给)模式到“Strike Zone”(单品同步供给)模式最终发展到“Block & KIT”(KIT同步供给)模式。线边供货模式不断向更高的柔性化程度和更简便的作业方式发展。
“One Pitch”(单品供给)------在线边设定固定料位,专职物流人员通过牵引车将零件批量供给到线边。
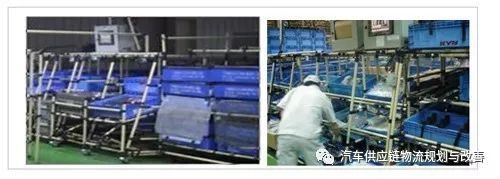
单品供给相对于最原始的料箱直送有一定的提升,解决了零件先进先出和空料箱切换的问题,供给范围广,空间利用率高。但存在取料距离远,取料动作幅度大等问题,对于作业人员的体力和零件识别要求较高。
“Strike Zone”(单品同步供给)------对部分体大件,颜色件,以件为单位,在集配区将零件按照车辆生产顺序进行排列,在适当的时间供给到线边。
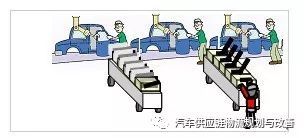
单品同步供给解决部分大零件和零件模块的料位面积问题,改善了取料动作,削减了零件辨识作业。但取料步行依然存在,集配区开始出现,增加了集配人员。在这个阶段没有取得生产效率的有效提升,但为后续的改善指出了方向。
“Block & KIT”(KIT同步供给)------对整车生产用的零件,以一段生产线需求的所有零件为单位,在集中的集配区将零件按照车辆生产计划排列放置在KIT BOX(台套料箱)中,在适当的时间供给到线边。
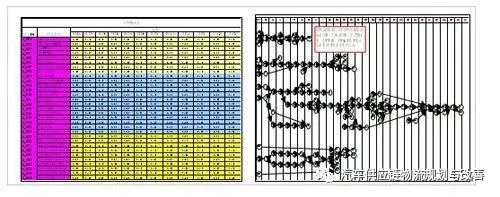
KIT同步供给削减了取料步行和辨识作业、减轻了取料作业负荷,为模块化作业编成提供了条件。同时将线上取料作业损失集中并转移到了集配区,为实施第三方物流或物流自动化创造了条件。KIT同步供给是线边供货模式的最高形态。
3.现状与损失把握
底盘线目前生产车型为4种,生产所需各种物料达到446种,主要的大件有仪表台、发动机舱、后背门饰板和保险杠等,车型间零件差异非常大。
整个底盘线只有约60米长,10个工位,446种零件供货模式大部分采用“One Pitch”模式,少量大零件采用了“Strike Zone”模式,线边面积已基本用完。但后续将再增加一种X车型,预计又会增加零件约100种。这种情况下延续原有的供货模式则有较大的难度,而且不利于生产效率的进一步提升。
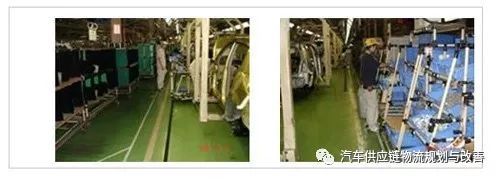
由于地板链的安全性要求,所以斜坡料架距离工位约1.5米,往返一次需4-6步,且每个工位都有装配作业,所以大量的取料作业分散在各个工位,形成各工位损失分散,不易改善的局面。
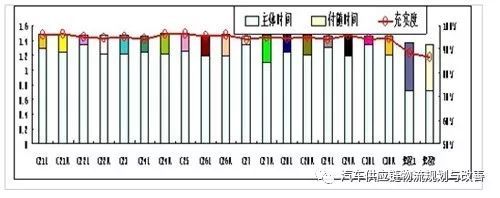
4.改善思路
要解决线边料位不足的问题,就要从供料方式着手考虑。对于任何一种供料方式来说,在正确的时间将正确的零件送到正确的工位是终极的目标。
传统的“One Pitch”是完全建立在物流作业和装配作业分离的角度进行设计,将物流系统和作业系统割裂开来,只考虑了物流作业本身的顺畅和批量运输效率,但对整个系统的生产效率来说是不利的。
“Strike Zone”是从人机工程的角度出发进行设计,初衷是削减大零件的辨识作业和降低取料作业负荷。改善的效果分散在多个工位,难以形成规模效果,并且由于集配区的出现更降低了整个系统的生产效率,是典型的以效率换取空间、品质、安全的形式,但提供了一种将损失从作业工位剥离并集中化的思想,为后续改善指出了方向。
“Block & KIT”是综合了物流设计、人机工程和作业平衡多方面考虑的理想模式。损失的集中化和转移同时为后续的低成本自动化搬运系统提供了改善空间。
所以此案例采用“Block & KIT”作为目标姿态,从线上损失集中化开始,逐步实现损失的集中和削减,最终达成改善效果。
5.KIT集配系统
基于“为每一台车仅提供这一台车所需的零件”思想,导入了同步配套供货系统,简称KIT系统。
· KIT系统通过在生产线设立集配区,将每一台份的物料放置在一台物料小车中,按照生产顺序投放上线,跟随生产线前进,起到流动料位的作用,而且取消了作业人员选取物料和拆包装的作业。
KIT的构思是比较简单的,困难的部分在于小车如何跟随生产线前进,如何实现小车与工位的相对静止,如何保证小车、零件和产品车的匹配以及如何避免小车对作业的干涉。
在小车的前进动力和定位部分,发挥低成本自动化思想中“充分发挥现有制造设备动力余量”的要求,通过巧妙的小机关设计,利用一个简单的联动支杆,将小车与主线联结,借助主线的动力前进并保持相对固定的位置。既可以降低整个项目投资和技术难度,又提高了可靠性和可维护性。
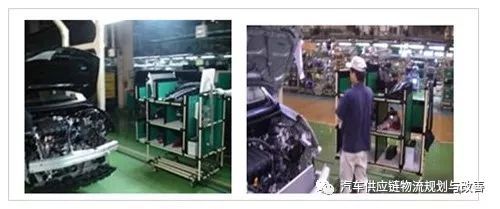
在保证小车、零件和产品车的匹配部分,选择通过集配区的集配指示系统实现。在物料集配区接入生产系统终端,接受生产管理系统的后续生产计划;在每种零件的料箱上方设置指示灯和计数器;中央处理器将生产计划分解为所需零件指示,则对应的零件料箱上指示灯亮起,集配人员取料后按下计数器,则指示灯熄灭;待一台车所需全部零件取料完成后给出集配结束指示,同时系统进行下一台份的集配指示。
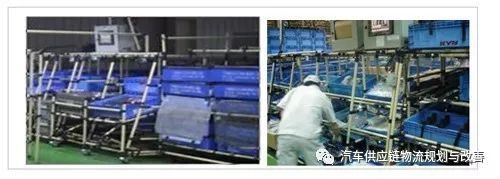
通过集配指示系统,不仅最终削减了零件辨识作业,更将原有体系中信息流的终点由装配人员向集配人员转移。将信息流的传递方式由纸版的作业指示单,提升为集成化的数据系统,保持了物流和信息流的匹配,提升了整个生产流的体系水平。
避免小车对作业的干涉部分需要在料车的设计中体现,设计时充分考虑了人机工效学以进一步消减取料损失。小车的尺寸充分考虑了作业工位和周边设备的要求,高度考虑了作业者的作业便利区域,并在零件位置的设计中考虑了诸如零件的相关就近原则、空间利用原则等一系列人机工程原则。
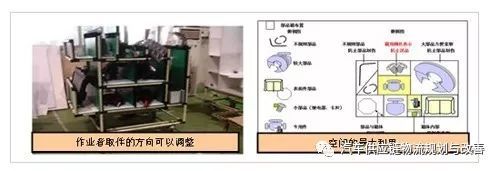
6.线平衡软件
KIT系统导入后线上作业人员的取料动作已经集中至集配区,这就需要增加集配的人员。为保证整个项目的收益性,需要对整个生产线的作业平衡进行调整。
传统的作业线平衡采用手动调整的方法,调整的依据有:
生产节拍和总体作业工时;
零件装配顺序和各零件装配工时;
调整的方法是手动绘制作业堆积图(又称“山积表”),通过手动调整达成理想的作业平衡。
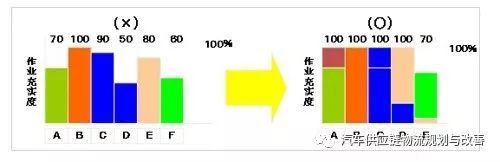
但对于汽车这种复杂工业产品来说,巨大的零件种类和复杂的安装逻辑使手动调整线平衡成为十分困难的作业,而且对于柔性化生产体系,多种车型的零件差异和装配差异特别是此公司采用的4车型混流生产,一个工位可能面临4种完全不同的车种数十种不同配置的情况,对于作业线平衡分析人员来说无疑是天文数字级的工作量。
针对这种情况,导入了专业线平衡软件进行辅助作业是非常必要的。经过多方对比,采用的是ALINE系列软件。该软件具有多产品复合线平衡模式,且可以设定作业模块,符合模块化作业编成的需要。
线平衡软件的制约因素是基本数据的准确性,这就需要企业有较高的作业标准化水平和完善的基本作业工时数据库。在软件导入前,需要进行大量的作业测量工作和作业标准固化作业。
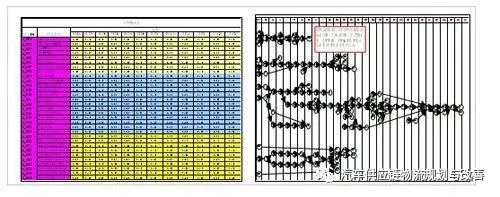
将基本作业工时数据库和安装逻辑输入软件,并设定生产所需的节拍和车型比例,则可以自动生产作业编成,大大减轻了IE工程师的作业负荷,使得IE工程师可以将主要精力投入制造系统的整体设计中。
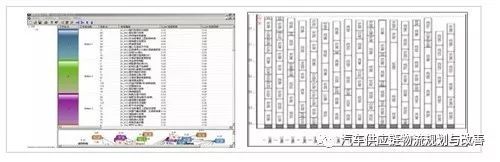
7.AGV自动搬运系统
导入KIT系统后,线上作业和集配作业都得到削减,但由于生产现场的局限性,集配区与生产区有一段较长的距离,又增加了物流的搬运损失,所以又提出了削减物流损失的要求。
· · 如果采用人工或牵引车搬运,可以以第三方物流的形式实现物流成本的削减,但对于整个系统的生产效率是没有帮助的。在这里考虑的是彻底的物流损失削减,用低成本自动化搬运系统进行物流作业。
在充分理解AGV工作原理的基础上,采用了散件进口,自行组装的模式,极大地降低了AGV的成本,保证了项目整体收益性。
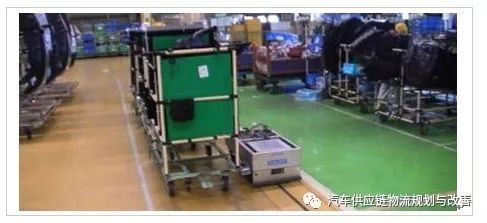
仅有运输工具是无法完全实现物流自动化的,还需要在装卸端进行自动化设计。所以在低成本AGV小车技术实现突破后,巧妙构思设计了简易自动脱钩系统。利用机械连杆和主线地板链的动力,实现了无动力自动化顺序装卸。这样AGV可以在完全自动的情况下,依次卸下所托运的全部KIT料车,实现了AGV能力的最大利用化,而且脱钩系统完全是机械结构,可靠性高且维护简单。
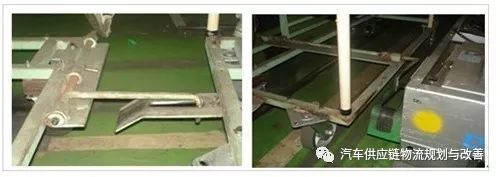
然在AGV小车的成本上实现了突破,但也要对AGV的运输效率进行研究,所以在AGV小车导入前,我们使用仿真技术结合现场物流状况对AGV的运输效率进行分析,得到计算AGV的最经济投入量的运算模型,可快速对应不同生产节拍下的AGV需求核算。
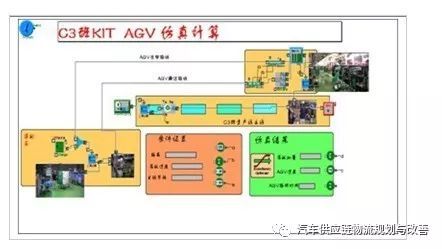
8.物流模式变更引发的布局优化
AGV自动搬运系统的投入极大削减了物流搬运损失,为进一步提升集配效率,优化了集配区布局。为保证车间内多个AGV系统的运行又进行了物流路线的优化。
集配区布局优化的过程中针对零件种类多的特点采用了SLP的方法,根据物流强度重排了物料布置。
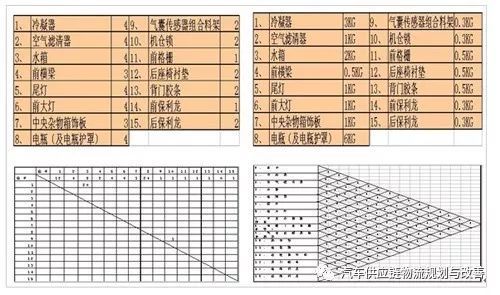
集配区布局优化的过程中除采用SLP的方法外,还根据设施规划思想进行了布局设计,并做出两种方案,二字型与U字型布局模式集配区布局优化的过程中,我们运用了仿真技术对两个方案进行模拟,得到结果二字型的效率更高。
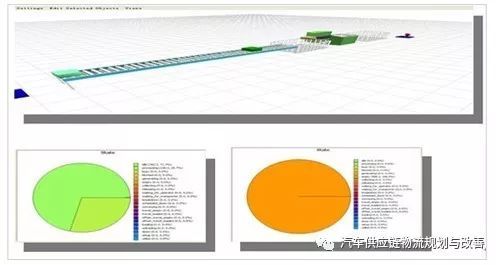
最终我们根据线边的局限性和设备因素综合考虑,将集配区布局成U型的二字型。
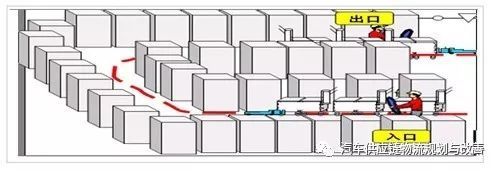
三、总结与思考
1.思路总结—改善着眼点的推移
在整个改善过程中,从线边取料出发,到车间整体的布局优化,从作业指示单到信息指示系统,改善的着眼点不断向生产流程前端移动,构成了两条相对的平行线,揭示了物流类改善的切入点和改善方向。
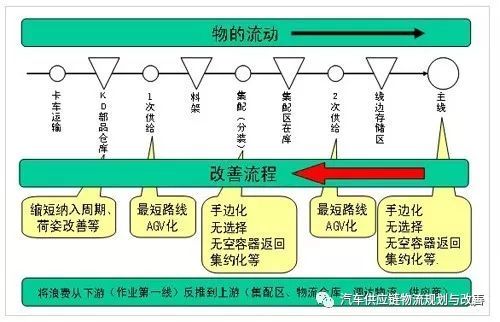
改善的方法是将损失集中化,再通过合适的低成本自动化取代人工作业。
2.探索创新—IE新兴技术与现场改善结合的切入点
在整个改善中,大量运用了IE新兴技术:在重组线平衡的过程中使用了专业线平衡软件;在AGV导入前使用仿真软件进行AGV的运输效率模拟;在集配区的优化过程中使用SLP方法评定零件的物流等级;对集配区变更后的作业情况进行模拟以验证改善的效果;可以说贯穿整个过程。这证明最新的IE技术在现场都可以找到直接的切入点。
对于IE功底比较扎实,即现场作业工时测定准确完整、作业标准化程度高的成熟企业,完全可以导入成熟的专业线平衡软件和辅助作业分析软件来减少IE工程师的工作负担,IE工程师可以专注于工厂制造体系的整体改善,在系统设计的过程中可以广泛使用仿真技术验证设计效果,降低改善风险。
汽车总装工艺内部物流模式借助供货模式的思维突破和低成本自动化搬运系统实用化而发生了革命性的突破,不仅突破了传统的物流观念和物流技术,更是在物流系统设计思想的突破。这种突破是应汽车工业的多品种柔性化生产模式的要求诞生的,但这种思想、这种方法必将扩展至其他工业领域,对中国工业未来发展做出积极的贡献!
- 下一篇:浅析汽车等速传动轴外星轮锻件精锻工艺
- 上一篇:激光焊接是如何影响汽车行业的?
举报 0
收藏 0
分享 145
-
推动汽车行业转型的引领者——面向未来的总装NE
2024-12-03 -
总装工艺成本优化实践案例
2024-08-05 -
如何提高螺栓连接的强度?
2024-07-30 -
案例分析:螺栓“跑丢了”!
2024-07-29
编辑推荐
最新资讯
-
跨越速运凭什么“圈粉”万千客户?“
2025-07-01 14:42
-
数智破局启新篇・生态共生再启程 —
2025-06-27 20:13
-
助力汽车零部件产线智能化升级,西门
2025-06-27 13:59
-
BBA集体转向!放弃全面电动化
2025-06-26 17:32
-
比换柜省钱,比自研省心,西门子Xcel
2025-06-25 15:07