广汽丰田第三工厂的智能制造
2018-09-05 09:24:21· 来源:汽车工艺与材料
广汽丰田C-HR是继第八代凯美瑞之后的第二辆基于丰田TNGA量产车。TNGA是丰田继流水线和TPS生产方式后,又一次汽车生产机制的全面革新。它从零开始,对全部零件重新研发、对核心部件全部采用最新技术、对整体产业链全面升级。
广汽丰田C-HR是继第八代凯美瑞之后的第二辆基于丰田TNGA量产车。TNGA是丰田继流水线和TPS生产方式后,又一次汽车生产机制的全面革新。它从零开始,对全部零件重新研发、对核心部件全部采用最新技术、对整体产业链全面升级。
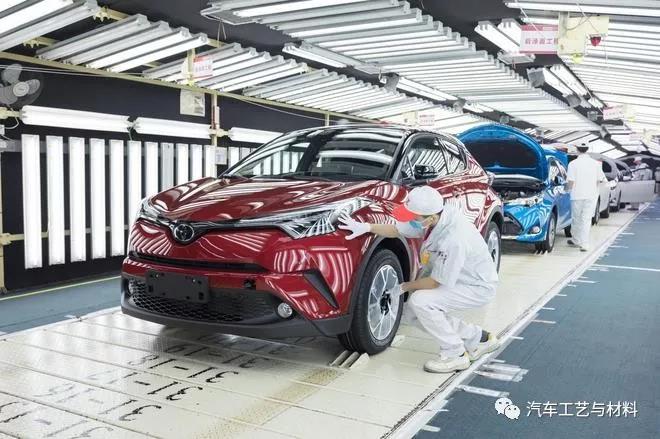
设计理念和冲压工艺
为了实现富有特色的钻石形状,C-HR采用了高难度的冲压工艺,前、后翼子板曲率达到R5(半径5mm),从而将丰田车型的设计变为现实。曲线是二维空间,车身曲面是三维空间,要实现这种复杂造型,并保证精良的面品质,对冲压模具提出严苛的要求。
前车灯的内部零件是2-3个,而C-HR是26个,为一般车辆的约10倍。通过数量较多的零件,实现了复杂的凹凸、精致的设计和配色。在车灯中层,采用了“让点状结构看起来像是在发光”的设计(在丙烯酸树脂板上打钉加工)。
C-HR采用隐藏式后门把手设计,实现了后车门窗到后挡风玻璃的无缝设计。把手形状基于人体工学,在把手内侧增加了鼓起部分和段差(平面高低差),实现很好的操作感。
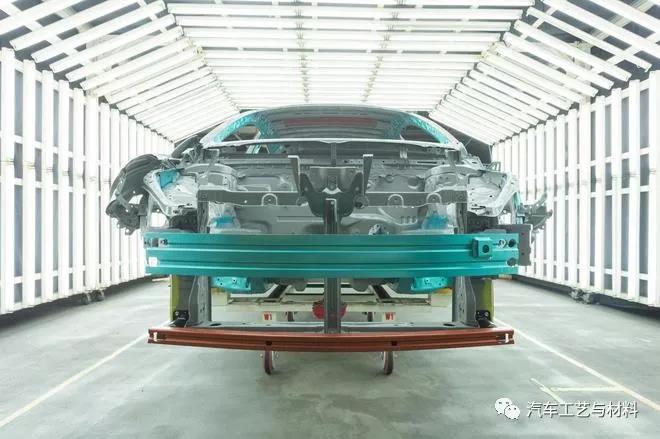
C-HR因设计品质提升,需要冲压的覆盖件更加复杂,对面品质要求更高。广汽丰田内制件规模在业内大幅领先,有利主机厂直接管控零件品质。冲压车间内制大量高强度钢结构件部品,最高强度达到1180MPa。
5100个焊点 “缝制”高刚性车身
C-HR配备了TNGA高刚性车身,以获得优异的高速行驶稳定性。车架主要部位采用1500MPa的超高强度热冲压钢材,590MPa以上超高强度钢材占比高达43%,整车焊点达到5100个,并且内制焊点超过75%,最大程度确保车身焊接的高品质。
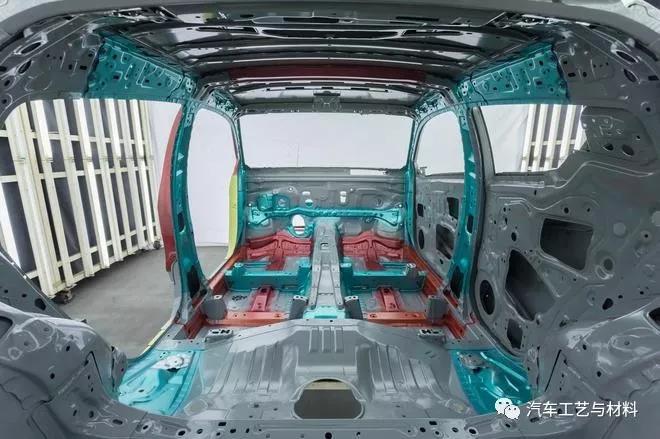
C-HR侧围加强件使用1500MPa热成型钢,结构上由原来的“工”字形,变成了封闭的环形结构,实现坚固的车身刚性。结合后门采用1620MPa双防撞杆,可应对SUV60km/h侧面碰撞。
原厂双色喷涂
C-HR采用“性感+速度+撞色”的色彩设计理念,设定5个基本颜色,可选黑/白车顶双色车身,共11种车身色彩选择。
双色车身需要进行两次喷涂,喷涂的难度在于第二层颜色喷涂。一次喷涂完成后,需要对车身进行遮蔽并露出车顶,然后对车顶进行第二层颜色喷涂,之后拆除遮蔽膜。为了保证二次喷涂的质量,车身遮蔽效果极为重要。遮蔽膜为德国进口材质,每一张造价达500元,耐高温、耐烘烤,在高温作业之后不会融化,不会贴在车身上。遮蔽膜贴完后要求所有边缘部位及转角位置密不透风、精益求精,因为稍有贴合不好就会导致油漆渗漏。分色胶带粘贴必须做到每一步都按规格粘贴,不能偏移,双色交界处涂面品质需严格控制。
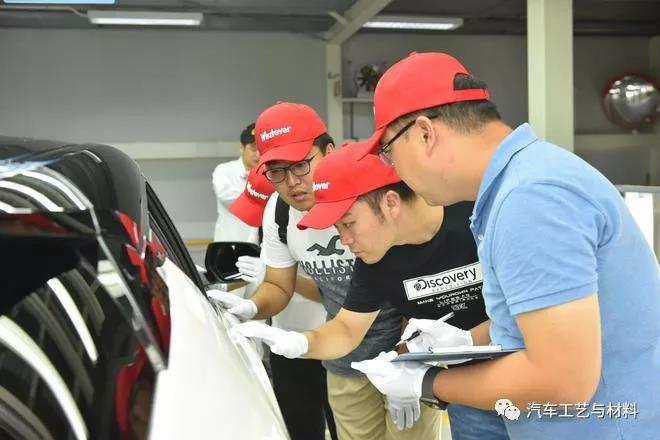
双色车从喷漆前准备到完成双色车身喷涂,比单色车型喷涂多出50多个步骤、增加165分钟生产流程。车身遮蔽作业必须在60分钟内完成,而工匠们经历超过300台操练,同时对工艺效率提升的改善,成功挑战车身遮蔽作业在50分钟内完成。
每个零件凝聚匠心品质
2017年,广汽丰田供应商零部件不良率仅为0.38PPM,即100万个部品中只有0.38件不良。2018年供应商供货不良率的目标是0.3PPM。
带镀锌层1180MPa超高强钢:在大量采用超高强度钢的基础上,镀锌钢材使用比例达到82%,包括首次采用带镀层的1180MPa超高强钢和1500MPa热冲压钢材,在提升车身强度的同时,也提升了车身抗腐蚀性能。
高强度紧固件(螺栓、螺母、螺钉及锻造部品):采用紫色摩擦系数稳定剂,与优化前(红色摩擦系数稳定剂)相比具有更高的耐腐蚀性、更稳定的摩擦系数,增强安全性,提高车辆稳定性。
萨克斯减震器:在减震器中设置回弹弹簧,正常行驶期间悬架行程小时只使用悬架弹簧;转弯时,回弹弹簧抑制内侧悬架伸展,从而在不影响舒适性的情况下,减小侧倾。
铝合金前防撞梁:国内首次采用7系高强度铝合金。铝合金材料的溃缩吸能性能要优于钢材,采用铝合金防撞梁可以更好减少顾客在低速碰撞受到的伤害。此外,铝合金的耐腐蚀性能更好。
自工序完结
在制造环节,广汽丰田生产质量管理的核心是“自工序完结”。在许多企业还依靠结果管理、依赖检查来保证品质时,广汽丰田的品质管理体系早已转向源头与过程管理,“自工序完结”活动贯穿于从商品企划到销售的整个产业链全过程。品质是在工序中制造出来的,不是检查出来的。
自工序完结的精髓在于“良品条件”加上“作业遵守率”,良品条件是制造出合格品必须具备的条件,告诉员工只要这么做,生产出来的就是合格品;作业遵守率就是百分之百执行作业指导书。
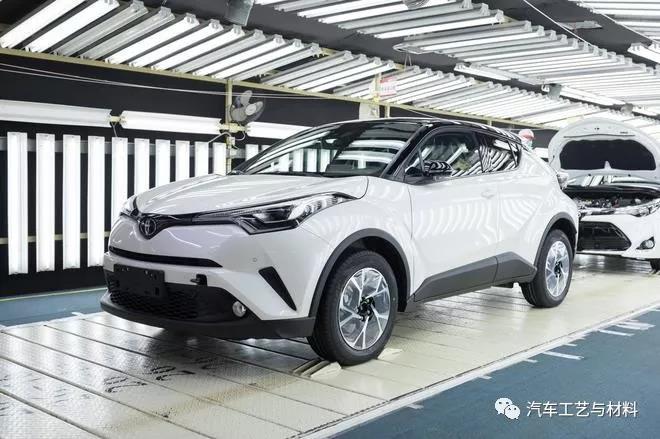
为彻底实现自工序完结,广汽丰田的员工需要在循环反复的工作中不断钻研完善良品条件,并通过师徒传承和长期的磨练提高工作技能,确保能够彻底遵守良品条件。从而实现每个人都能判断工序的好坏,成为自己岗位的工匠,每个人都在自己的工序内保证品质,进而造就全员工匠。
目前广汽丰田生产线的一次合格率,即车辆下总装线就打合格证直接出厂的比率达到98.8%。广汽丰田对品质管理的精髓也灌注到供应商身上。2017年,广汽丰田零部件供应商的供货不良率仅为0.38PPM,即100万个部品中只有0.38件不良,在丰田体系里达到一流品质水准,远远领先业界平均水平。
“丰田全球工厂No.1”工厂
广汽丰田第三工厂是丰田全球第一座按照TNGA新蓝图建成的工厂,是目前丰田TNGA制造体系的代表,有“丰田全球工厂No.1”之誉。
第三工厂目前的年产能是10万辆,可扩至20万辆。
这是一座“无柱子工厂”。45米跨度的车间,没有一根支撑屋顶的立柱。站在车间这一边,一眼望见车间那一边,视线无所阻挡。
智能化是第三工厂的重点建设内容之一。它全面装备了无线传输信息技术,实现了“无纸化作业”。在3条生产线的入口和出口,都装备了车身涂面摄像检测仪器,检测数据无线传输到后台电脑中,经过对比,即可知道车身表面有无划伤和污物等质量问题。类似的诸多措施对质量保障帮助很大。1000余项下线车检测信息被无线传输到后台电脑中进行对比和存储,确保下线车一次合格率达到了惊人的98%。
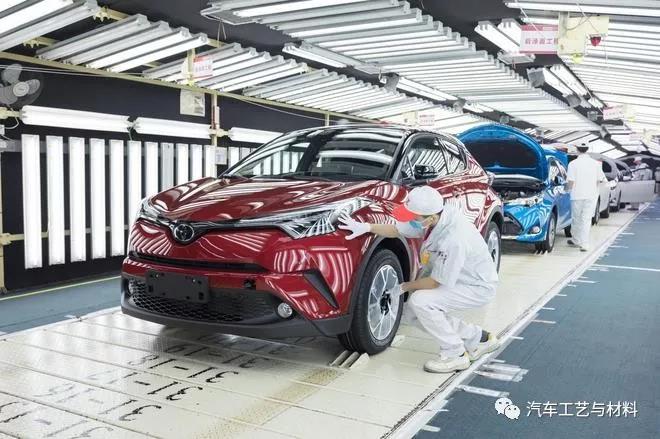
设计理念和冲压工艺
为了实现富有特色的钻石形状,C-HR采用了高难度的冲压工艺,前、后翼子板曲率达到R5(半径5mm),从而将丰田车型的设计变为现实。曲线是二维空间,车身曲面是三维空间,要实现这种复杂造型,并保证精良的面品质,对冲压模具提出严苛的要求。
前车灯的内部零件是2-3个,而C-HR是26个,为一般车辆的约10倍。通过数量较多的零件,实现了复杂的凹凸、精致的设计和配色。在车灯中层,采用了“让点状结构看起来像是在发光”的设计(在丙烯酸树脂板上打钉加工)。
C-HR采用隐藏式后门把手设计,实现了后车门窗到后挡风玻璃的无缝设计。把手形状基于人体工学,在把手内侧增加了鼓起部分和段差(平面高低差),实现很好的操作感。
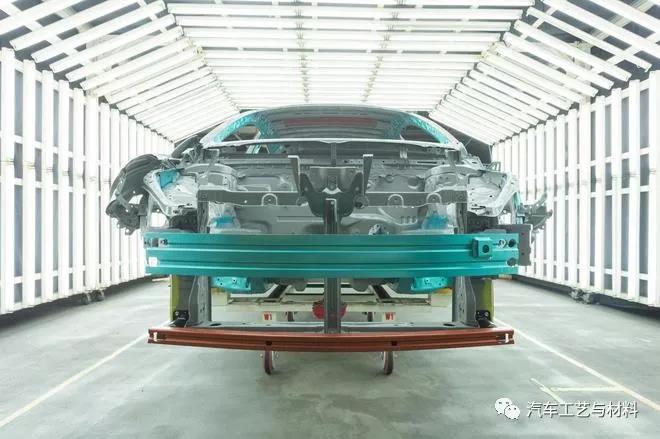
C-HR因设计品质提升,需要冲压的覆盖件更加复杂,对面品质要求更高。广汽丰田内制件规模在业内大幅领先,有利主机厂直接管控零件品质。冲压车间内制大量高强度钢结构件部品,最高强度达到1180MPa。
5100个焊点 “缝制”高刚性车身
C-HR配备了TNGA高刚性车身,以获得优异的高速行驶稳定性。车架主要部位采用1500MPa的超高强度热冲压钢材,590MPa以上超高强度钢材占比高达43%,整车焊点达到5100个,并且内制焊点超过75%,最大程度确保车身焊接的高品质。
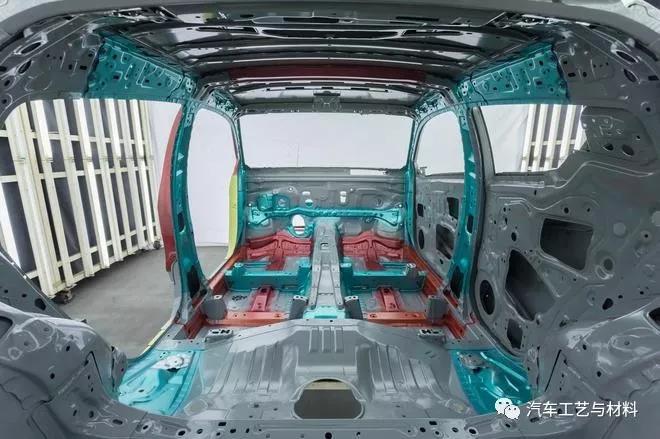
C-HR侧围加强件使用1500MPa热成型钢,结构上由原来的“工”字形,变成了封闭的环形结构,实现坚固的车身刚性。结合后门采用1620MPa双防撞杆,可应对SUV60km/h侧面碰撞。
原厂双色喷涂
C-HR采用“性感+速度+撞色”的色彩设计理念,设定5个基本颜色,可选黑/白车顶双色车身,共11种车身色彩选择。
双色车身需要进行两次喷涂,喷涂的难度在于第二层颜色喷涂。一次喷涂完成后,需要对车身进行遮蔽并露出车顶,然后对车顶进行第二层颜色喷涂,之后拆除遮蔽膜。为了保证二次喷涂的质量,车身遮蔽效果极为重要。遮蔽膜为德国进口材质,每一张造价达500元,耐高温、耐烘烤,在高温作业之后不会融化,不会贴在车身上。遮蔽膜贴完后要求所有边缘部位及转角位置密不透风、精益求精,因为稍有贴合不好就会导致油漆渗漏。分色胶带粘贴必须做到每一步都按规格粘贴,不能偏移,双色交界处涂面品质需严格控制。
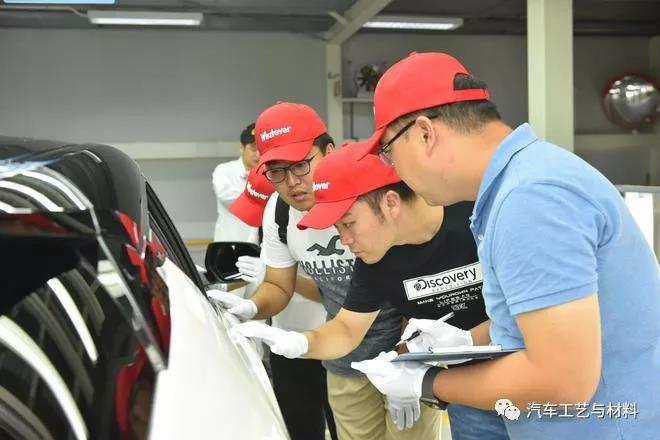
双色车从喷漆前准备到完成双色车身喷涂,比单色车型喷涂多出50多个步骤、增加165分钟生产流程。车身遮蔽作业必须在60分钟内完成,而工匠们经历超过300台操练,同时对工艺效率提升的改善,成功挑战车身遮蔽作业在50分钟内完成。
每个零件凝聚匠心品质
2017年,广汽丰田供应商零部件不良率仅为0.38PPM,即100万个部品中只有0.38件不良。2018年供应商供货不良率的目标是0.3PPM。
带镀锌层1180MPa超高强钢:在大量采用超高强度钢的基础上,镀锌钢材使用比例达到82%,包括首次采用带镀层的1180MPa超高强钢和1500MPa热冲压钢材,在提升车身强度的同时,也提升了车身抗腐蚀性能。
高强度紧固件(螺栓、螺母、螺钉及锻造部品):采用紫色摩擦系数稳定剂,与优化前(红色摩擦系数稳定剂)相比具有更高的耐腐蚀性、更稳定的摩擦系数,增强安全性,提高车辆稳定性。
萨克斯减震器:在减震器中设置回弹弹簧,正常行驶期间悬架行程小时只使用悬架弹簧;转弯时,回弹弹簧抑制内侧悬架伸展,从而在不影响舒适性的情况下,减小侧倾。
铝合金前防撞梁:国内首次采用7系高强度铝合金。铝合金材料的溃缩吸能性能要优于钢材,采用铝合金防撞梁可以更好减少顾客在低速碰撞受到的伤害。此外,铝合金的耐腐蚀性能更好。
自工序完结
在制造环节,广汽丰田生产质量管理的核心是“自工序完结”。在许多企业还依靠结果管理、依赖检查来保证品质时,广汽丰田的品质管理体系早已转向源头与过程管理,“自工序完结”活动贯穿于从商品企划到销售的整个产业链全过程。品质是在工序中制造出来的,不是检查出来的。
自工序完结的精髓在于“良品条件”加上“作业遵守率”,良品条件是制造出合格品必须具备的条件,告诉员工只要这么做,生产出来的就是合格品;作业遵守率就是百分之百执行作业指导书。
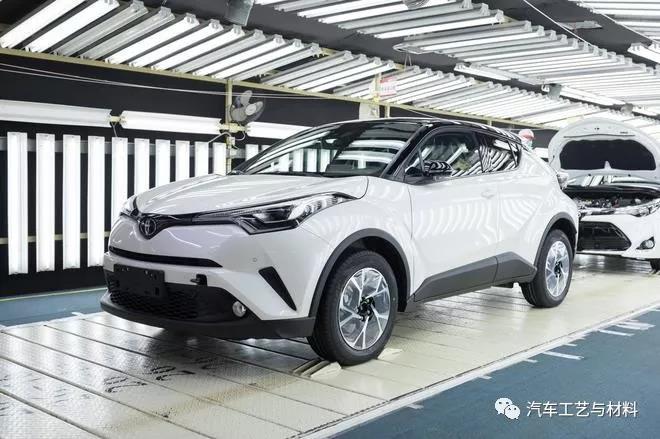
为彻底实现自工序完结,广汽丰田的员工需要在循环反复的工作中不断钻研完善良品条件,并通过师徒传承和长期的磨练提高工作技能,确保能够彻底遵守良品条件。从而实现每个人都能判断工序的好坏,成为自己岗位的工匠,每个人都在自己的工序内保证品质,进而造就全员工匠。
目前广汽丰田生产线的一次合格率,即车辆下总装线就打合格证直接出厂的比率达到98.8%。广汽丰田对品质管理的精髓也灌注到供应商身上。2017年,广汽丰田零部件供应商的供货不良率仅为0.38PPM,即100万个部品中只有0.38件不良,在丰田体系里达到一流品质水准,远远领先业界平均水平。
“丰田全球工厂No.1”工厂
广汽丰田第三工厂是丰田全球第一座按照TNGA新蓝图建成的工厂,是目前丰田TNGA制造体系的代表,有“丰田全球工厂No.1”之誉。
第三工厂目前的年产能是10万辆,可扩至20万辆。
这是一座“无柱子工厂”。45米跨度的车间,没有一根支撑屋顶的立柱。站在车间这一边,一眼望见车间那一边,视线无所阻挡。
智能化是第三工厂的重点建设内容之一。它全面装备了无线传输信息技术,实现了“无纸化作业”。在3条生产线的入口和出口,都装备了车身涂面摄像检测仪器,检测数据无线传输到后台电脑中,经过对比,即可知道车身表面有无划伤和污物等质量问题。类似的诸多措施对质量保障帮助很大。1000余项下线车检测信息被无线传输到后台电脑中进行对比和存储,确保下线车一次合格率达到了惊人的98%。
编辑推荐
最新资讯
-
比亚迪叉车:用科技创新驱动绿色物流
2025-07-10 10:40
-
全球首个!比亚迪率先实现媲美L4级智
2025-07-10 09:31
-
精度±微米,节拍7秒——埃马克VST 5
2025-07-09 18:17
-
跨越速运凭什么“圈粉”万千客户?“
2025-07-01 14:42
-
数智破局启新篇・生态共生再启程 —
2025-06-27 20:13