宝马全球推进工业4.0,华晨宝马In China for Global
2018-08-09 11:15:13· 来源:汽车商业评论
宝马正在全球内开展工业4.0的推进,并鼓励各地工厂从不同纬度完成本地化的项目探索和尝试。
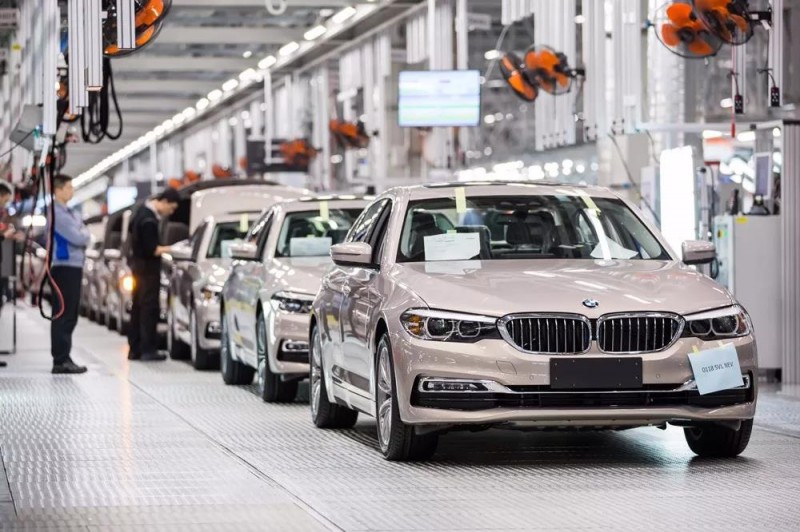
宝马正在全球内开展工业4.0的推进,并鼓励各地工厂从不同纬度完成本地化的项目探索和尝试。
《汽车商业评论》记者 孟为
冲压车间里,激光扫描仪正在以210,000点/秒的速度对车身零件表面的尺寸进行扫描检测,得到点云数据,通过与3D数模的对比,可以得出车身尺寸状态。
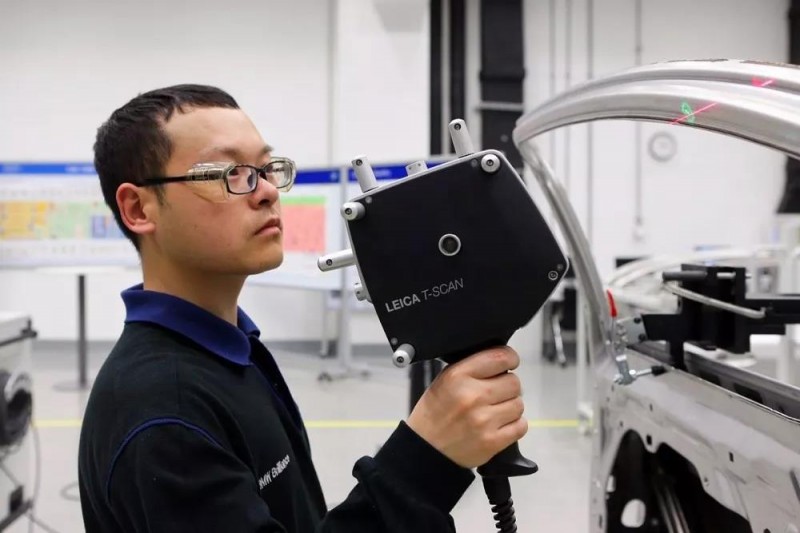
(工人使用激光扫描仪对车身进行检测)
焊装车间内,工人和智能机器人在生产线上协同工作,完成对超过1000多个缝隙、断差的检测,以保证车身质量。
涂装车间里,由4个机器人与视觉系统结合的ADD自动检测系统,对喷涂结束后的白车身表面进行检测。
它利用LED光源、特殊反光板和8个摄像头实现对0.15mm的缺陷识别,将车身表面的缺陷识别率从原来的人工识别率65%上升到98%。
这不是一场对于未来工厂的描绘,而是华晨宝马一个个正在被成熟应用的工业4.0项目。
宝马正在全球内开展工业4.0的推进,并鼓励各地工厂从不同纬度完成本地化的项目探索和尝试。
像文章开头描述的案例在华晨宝马铁西和新大东工厂还有很多。
例如,华晨宝马新大东工厂今年部署了名为DILO的物流管理系统。这个类似于滴滴的系统正在将整个工厂的物流AGV车和叉车等形成智能化呼叫和管理。
2017年,这套系统最先被应用在1个区域,覆盖12台叉车进行测试,它改变了传统模式下叉车司机到工作站找工作单的低效模式,转而采用更高效、最近距离的排单来提升工作效率。
目前,这套系统已经成功覆盖了6个区域和38台设备。下一步,它还将根据工厂的需求进行智能交通最优路线的升级。
在夹具的安装环节,华晨宝马通过AR技术和拍照,实现虚拟和现实的结合,将拍照的夹具设备形成三位图像和数模进行对比,迅速发现装备安装中的缺陷和是否符合设计要求。
按照传统模式,这个过程需要规划技术专家一个个按照数模进行对比,大型设备时可能会有遗漏,甚至需要几轮不同专家来完成。现在采用虚拟现实技术,大大节省了新车型量产夹具调试时间,以及保证夹具的最完美状态。
2017年10月,由华晨宝马新大东工厂自主设计的底盘PVC检测系统上线,它通过高清摄像头在生产线工作的同时拍照,在40秒内完成图像灰度对比,人工智能识别技术,对PVC厚度、堵孔边缘的厚度和角度等喷涂标准进行自动检测。
而这套系统也将逐渐被宝马集团推广到全球工厂。
汽车商业评论认为,工业4.0的探索和实践,对于华晨宝马来说不仅让它们从原来在产品层面的In China for China形象成功升级到了In China for Global,也为它在宝马全球体系内实现传统燃油车和新能源车的混线生产提供了支持,开创了一种全新的新能源车生产模式。
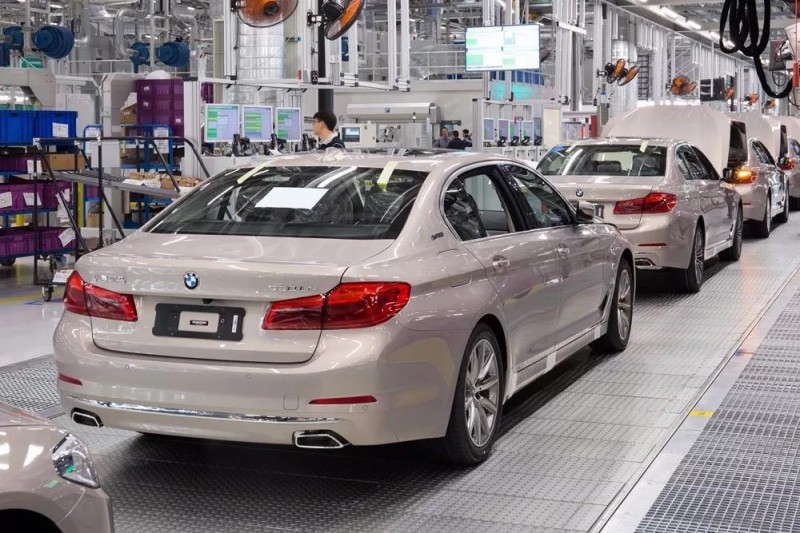
(全新BMW 5系插电式混合动力在华晨宝马新大东工厂下线)
2017年10月24日,华晨宝马动力电池中心在沈阳揭幕,生产全新BMW 5系插电式混合动力车型使用的动力电池;2018年5月28日,华晨宝马动力电池中心二期项目顺利奠基,将生产BMW全新第五代动力电池,用于宝马集团BMW主品牌的首款纯电动车型——全新BMW iX3概念车的量产车型。
同时,作为“工业4.0”技术应用的先锋和典范,华晨宝马的两座整车工厂只需在车身车间及总装车间对设备稍作改造,均可实现新能源车型与传统动力车型的共线灵活生产。
例如,在新大东工厂中,通过对车身车间后车身和翼子板、燃油箱总装、总装车间的高压电池合装三个工位的调整,就实现了全新BMW 5系插电式混合动力车型和传统动力车型的共线生产。
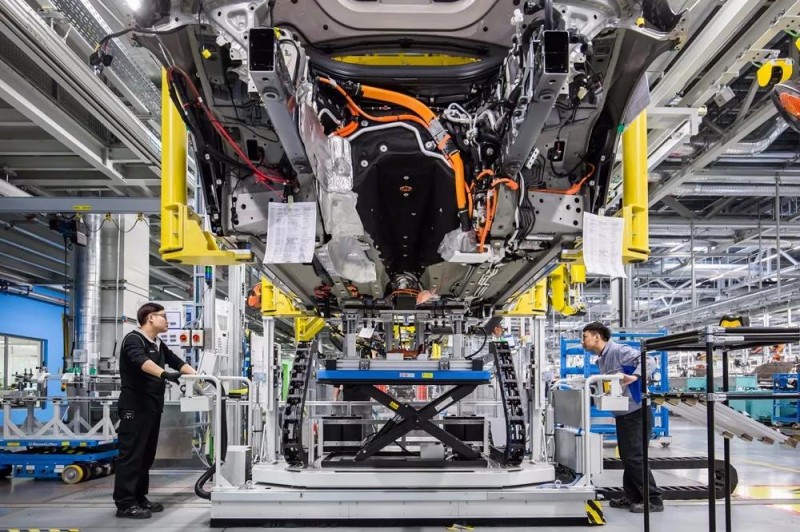
(柔性生产线上混合动力车型高压电池安装)
华晨宝马相信,工业4.0的这些项目不仅帮助华晨宝马实现了数据采集分析、智慧物流、自动化创新和协作系统等能力的提升,也为有助于宝马在全球实现生产零缺陷的目标。
- 下一篇:某车型顶盖天窗废料再利用的实施
- 上一篇:变速箱换挡导块如何加工?
编辑推荐
最新资讯
-
辐射亚太,链接全球——采埃孚再制造
2025-07-30 11:46
-
思看科技发布子品牌SCANOLOGY,全球
2025-07-30 11:06
-
风雨不动安如山——比亚迪叉车构筑“
2025-07-30 08:48
-
NEAS CHINA 新能源汽车技术与生态链
2025-07-29 09:52
-
三维扫描革新碾磨机辊套检测,效率与
2025-07-25 10:46