变速箱换挡导块如何加工?
2018-08-09 09:56:39· 来源:机工机床世界
换挡导块是汽车变速箱中的一个重要零件,其典型零件尺寸如图1所示。长期以来,该类产品工艺中的首先两序加工内孔、定位面常采用立式钻床扩孔,再用车床平定位端面及孔口倒角,然后再拉内孔。
浙江万里扬股份有限公司
蓝健 张裕强 孙宇伦
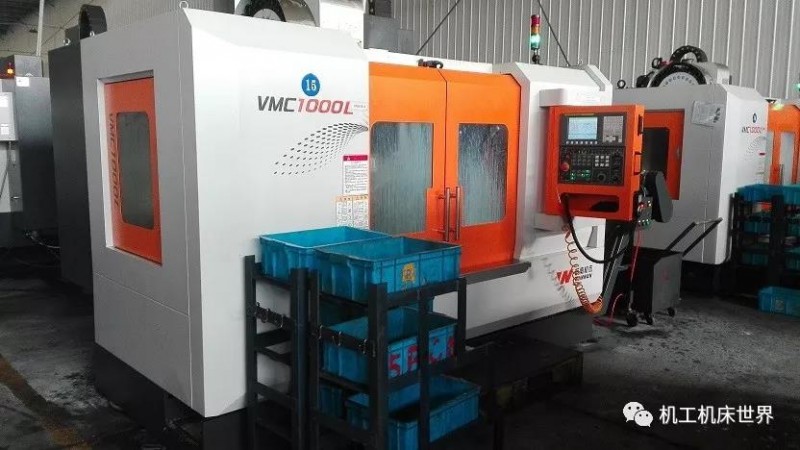
一、加工中出现的问题
换挡导块是汽车变速箱中的一个重要零件,其典型零件尺寸如图1所示。长期以来,该类产品工艺中的首先两序加工内孔、定位面常采用立式钻床扩孔,再用车床平定位端面及孔口倒角,然后再拉内孔。
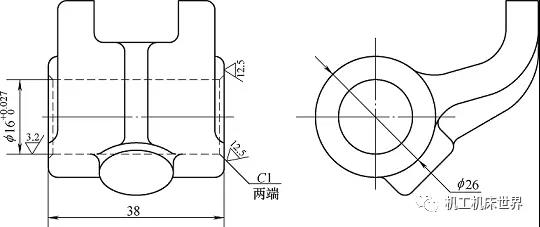
某供应商的机加工典型工艺中,首先进行的工序为:扩孔→车定位面及倒角→拉孔,共使用加工设备3台,需操作人员3人。其中扩孔、车定位面及倒角工序由于工时较拉孔长,经常出现产能不足、加班赶货的现象。扩孔工序采用的是立式钻床配普通麻花钻,以外圆毛坯面定位夹紧,加工时存在孔偏大、偏位的现象,当后道工序再以外圆毛坯面定位夹紧车定位面及倒角时,夹紧点容易发生偏差,导致车出的定位面与底孔垂直度差,进而出现拉孔工序无法将孔完全拉出的现象。
二、工艺改进方案
针对前述工艺缺陷,采用数控车床进行工艺改进,投入液压工装与刀具后,改扩孔为车底孔,同时将车定位面和两端面倒角一并完成,相比原先工艺零件一次装夹完成两道工序,一方面提高了拉前底孔的稳定性,另一方面极大地提高了拉前底孔与定位面的垂直度,完全消除了因此造成的拉孔无法加工出的问题。工艺改进后的工序为:车底孔→平端面及倒角→拉孔。
1、数控车床液压夹具的设计
根据产品结构,一端靠紧,以φ26mm毛坯外圆定位夹紧,设计出数控车床夹具,如图2所示。通过液压系统工作带动联接拉杆前后运动,进而带动活动拉杆运动,实现压爪和V形压块对导块工件的夹紧和松开。夹具主体中充满机油,保证各活动件充分润滑。顶块对工件的毛坯端面进行限位,堵头防止切屑进入主体。设计排屑孔的作用是透空使工件可以实现内倒角。
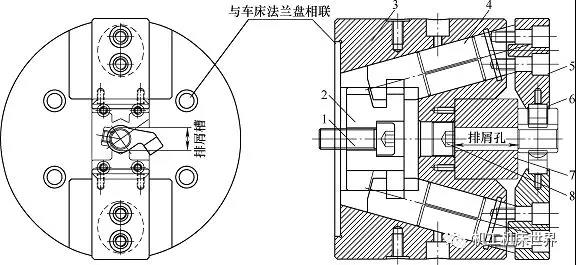
1.联接螺栓 2.联接拉杆 3.主体 4.活动拉杆 5.压爪 6.V形压块 7.顶块 8.堵头
2、刀具的选用
根据本工序需完成的工作,即平端面、车底孔、内倒角和外倒角,选用的刀具为内孔车刀(见图3)。
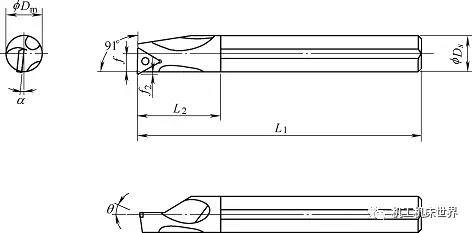
导块的材料为ZG310-570,选用泰珂洛的内孔TAC车刀,具体型号为:刀杆A12M-STFPR1102-D140,配套的刀片型号TPMT110208PM T6130。
3、切削参数的计算与选用
参考金属切削手册,留拉孔余量0.6mm,故内孔车至φ(15.5±0.1)mm。
根据厂家提供的刀具样本上给出的参考参数:vc=60~150m/min,切深ap=1~3mm,进给量f=0.07~0.3mm/r,结合设备的自身状态,选定vc=70m/min,计算转速n=1 000vc/(πd)=1 000×70/(3.14×15.5)≈1 400(r/min),f取0.2mm/r,内孔毛坯底孔约为φ14.5mm,ap取0.5mm。
三、夹具、刀具的安装和生产调试
1、夹具、刀具的安装
将制作完成的夹具安装至车床上,安装时注意不要磕碰,安装完成后对夹具的端面跳动、径向跳动进行检测,检测跳动不大于0.05mm的视为合格,可投入使用。刀杆安装在相应的刀位上,根据工件的长度预留合适的加工空间。对刀杆的安装高度进行复检,确定刀尖和主轴中心在同一高度上,用百分表对刀杆上母线和侧母线进行复检,若跳动较大,利用垫片进行调整,将跳动控制在0.03mm以内。
2、编写加工程序
绘制走刀轨迹如图4所示,其中实线表示切削轨迹。
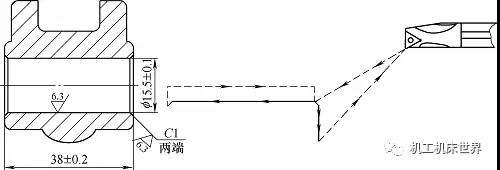
根据走刀轨迹编写加工程序如下:
G99;
M03 S01;
M08;
T03;
G0 X15.8 Z3;
G1 Z-39 F0.2;
U1 Z-39;
U-1.6;
X14.5;
G0 Z-1.7;
G1 X15 F0.2;
Z0 X18;
X29 F0.1;
G0 Z120;
M09;
M05;
M30;
完成对程序的检查后进行试加工,根据实际工况再对加工程序进行优化。
四、经济效益对比分析
由于机物料消耗难以统计,本次改进涉及的几道工序机物料消耗不多,故经济效益主要从人工、电耗和设备几方面计算单件成本的降低(见附表)。
工艺改进前后成本对比
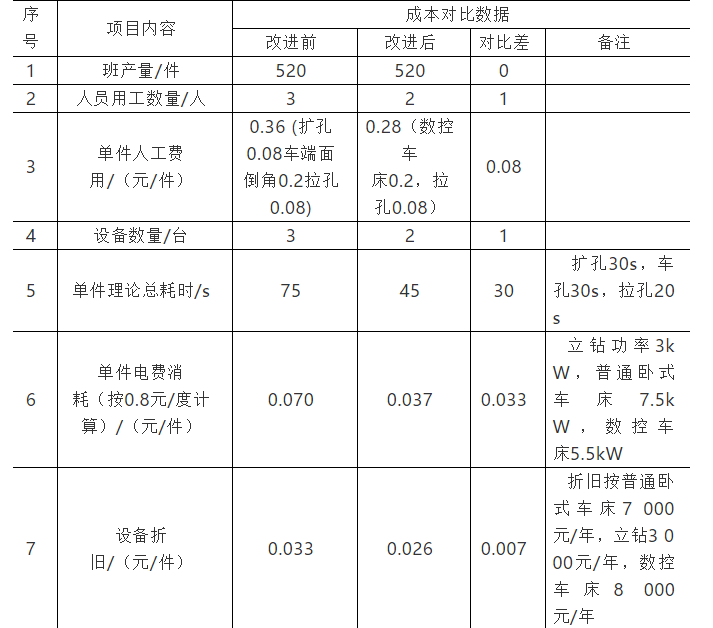

蓝健 张裕强 孙宇伦
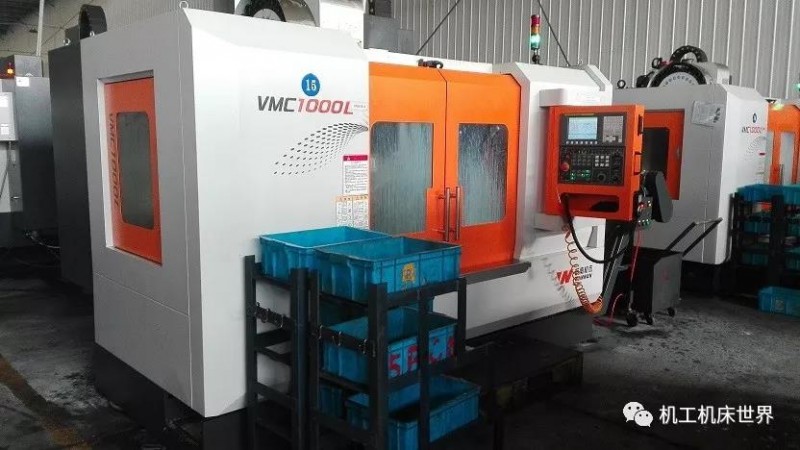
一、加工中出现的问题
换挡导块是汽车变速箱中的一个重要零件,其典型零件尺寸如图1所示。长期以来,该类产品工艺中的首先两序加工内孔、定位面常采用立式钻床扩孔,再用车床平定位端面及孔口倒角,然后再拉内孔。
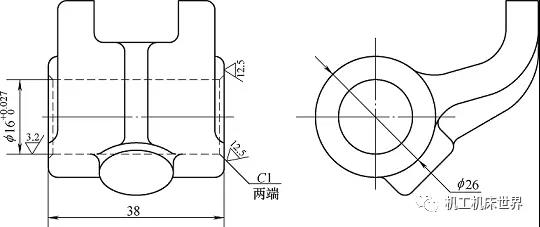
某供应商的机加工典型工艺中,首先进行的工序为:扩孔→车定位面及倒角→拉孔,共使用加工设备3台,需操作人员3人。其中扩孔、车定位面及倒角工序由于工时较拉孔长,经常出现产能不足、加班赶货的现象。扩孔工序采用的是立式钻床配普通麻花钻,以外圆毛坯面定位夹紧,加工时存在孔偏大、偏位的现象,当后道工序再以外圆毛坯面定位夹紧车定位面及倒角时,夹紧点容易发生偏差,导致车出的定位面与底孔垂直度差,进而出现拉孔工序无法将孔完全拉出的现象。
二、工艺改进方案
针对前述工艺缺陷,采用数控车床进行工艺改进,投入液压工装与刀具后,改扩孔为车底孔,同时将车定位面和两端面倒角一并完成,相比原先工艺零件一次装夹完成两道工序,一方面提高了拉前底孔的稳定性,另一方面极大地提高了拉前底孔与定位面的垂直度,完全消除了因此造成的拉孔无法加工出的问题。工艺改进后的工序为:车底孔→平端面及倒角→拉孔。
1、数控车床液压夹具的设计
根据产品结构,一端靠紧,以φ26mm毛坯外圆定位夹紧,设计出数控车床夹具,如图2所示。通过液压系统工作带动联接拉杆前后运动,进而带动活动拉杆运动,实现压爪和V形压块对导块工件的夹紧和松开。夹具主体中充满机油,保证各活动件充分润滑。顶块对工件的毛坯端面进行限位,堵头防止切屑进入主体。设计排屑孔的作用是透空使工件可以实现内倒角。
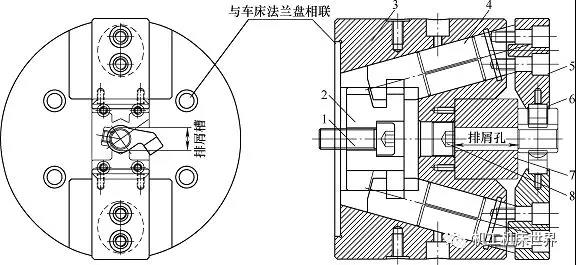
1.联接螺栓 2.联接拉杆 3.主体 4.活动拉杆 5.压爪 6.V形压块 7.顶块 8.堵头
2、刀具的选用
根据本工序需完成的工作,即平端面、车底孔、内倒角和外倒角,选用的刀具为内孔车刀(见图3)。
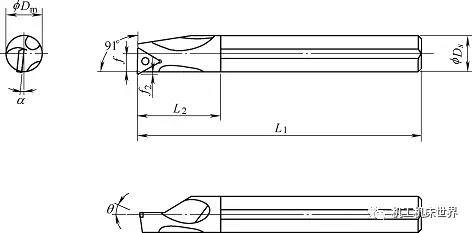
导块的材料为ZG310-570,选用泰珂洛的内孔TAC车刀,具体型号为:刀杆A12M-STFPR1102-D140,配套的刀片型号TPMT110208PM T6130。
3、切削参数的计算与选用
参考金属切削手册,留拉孔余量0.6mm,故内孔车至φ(15.5±0.1)mm。
根据厂家提供的刀具样本上给出的参考参数:vc=60~150m/min,切深ap=1~3mm,进给量f=0.07~0.3mm/r,结合设备的自身状态,选定vc=70m/min,计算转速n=1 000vc/(πd)=1 000×70/(3.14×15.5)≈1 400(r/min),f取0.2mm/r,内孔毛坯底孔约为φ14.5mm,ap取0.5mm。
三、夹具、刀具的安装和生产调试
1、夹具、刀具的安装
将制作完成的夹具安装至车床上,安装时注意不要磕碰,安装完成后对夹具的端面跳动、径向跳动进行检测,检测跳动不大于0.05mm的视为合格,可投入使用。刀杆安装在相应的刀位上,根据工件的长度预留合适的加工空间。对刀杆的安装高度进行复检,确定刀尖和主轴中心在同一高度上,用百分表对刀杆上母线和侧母线进行复检,若跳动较大,利用垫片进行调整,将跳动控制在0.03mm以内。
2、编写加工程序
绘制走刀轨迹如图4所示,其中实线表示切削轨迹。
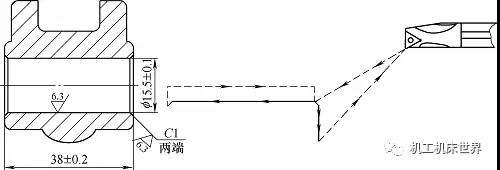
根据走刀轨迹编写加工程序如下:
G99;
M03 S01;
M08;
T03;
G0 X15.8 Z3;
G1 Z-39 F0.2;
U1 Z-39;
U-1.6;
X14.5;
G0 Z-1.7;
G1 X15 F0.2;
Z0 X18;
X29 F0.1;
G0 Z120;
M09;
M05;
M30;
完成对程序的检查后进行试加工,根据实际工况再对加工程序进行优化。
四、经济效益对比分析
由于机物料消耗难以统计,本次改进涉及的几道工序机物料消耗不多,故经济效益主要从人工、电耗和设备几方面计算单件成本的降低(见附表)。
工艺改进前后成本对比
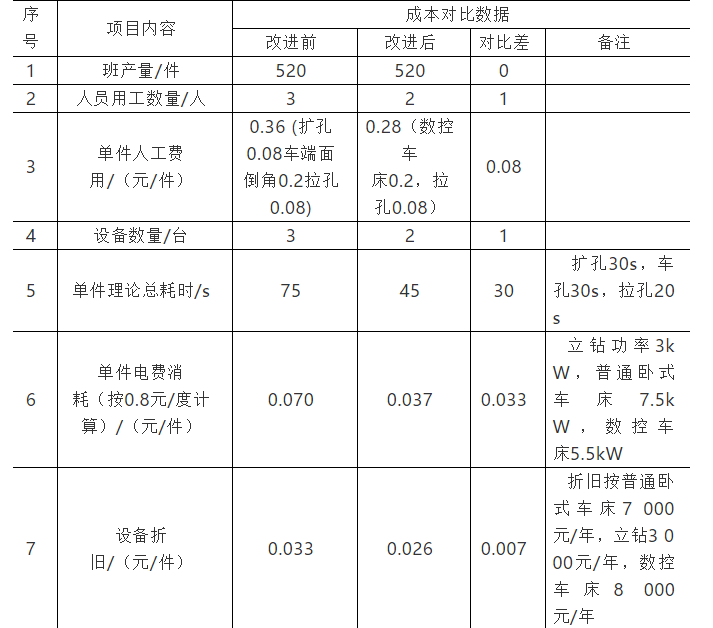

编辑推荐
最新资讯
-
辐射亚太,链接全球——采埃孚再制造
2025-07-30 11:46
-
思看科技发布子品牌SCANOLOGY,全球
2025-07-30 11:06
-
风雨不动安如山——比亚迪叉车构筑“
2025-07-30 08:48
-
NEAS CHINA 新能源汽车技术与生态链
2025-07-29 09:52
-
三维扫描革新碾磨机辊套检测,效率与
2025-07-25 10:46