变速箱齿轮腹板冲孔工艺与模具设计
2019-04-19 13:44:36· 来源:锻造与冲压 作者:李玲蔚
齿轮是汽车变速箱的重要零部件,随着汽车轻量化的不断发展,对零部件的轻量化、精密化要求越来越高。一些高端乘用车变速箱上的齿轮结构复杂化,且在腹板上增加一定数量的孔来实现减重。本文主要介绍该类齿轮的锻造工艺及模具设计,以及利
齿轮是汽车变速箱的重要零部件,随着汽车轻量化的不断发展,对零部件的轻量化、精密化要求越来越高。一些高端乘用车变速箱上的齿轮结构复杂化,且在腹板上增加一定数量的孔来实现减重。本文主要介绍该类齿轮的锻造工艺及模具设计,以及利用Forge软件对工艺方案进行模拟分析。运用模拟工艺及模具进行实际生产验证,锻件形状及尺寸完全满足产品要求。
锻造工艺分析
产品特点
我公司以往锻压机上生产的变速箱齿轮大多余量大,腹板处厚度大于10mm,成形难度低。该腹板冲孔类齿轮(图1)为精密模锻件,尺寸精度要求高(公差±0.5mm),机加工余量小,腹板厚度仅6~7mm,腹板上有6~8个“腰”形长孔,孔径最小仅5mm,且均为非加工部位。图2所示为产品三维模型。
锻造难点
目前我公司主要采用闭式锻造工艺来开发这类薄腹板带减重孔的齿轮,其结构特点决定了工艺性及模具设计的复杂性。
锻造过程中由于腹板薄,金属流动过程中冷却速度快,导致金属流动困难,型腔不易充满,尤其是轮缘内侧圆角部分。锻件截面变化大,锻打易发生变形,出现充不满、折叠等问题。
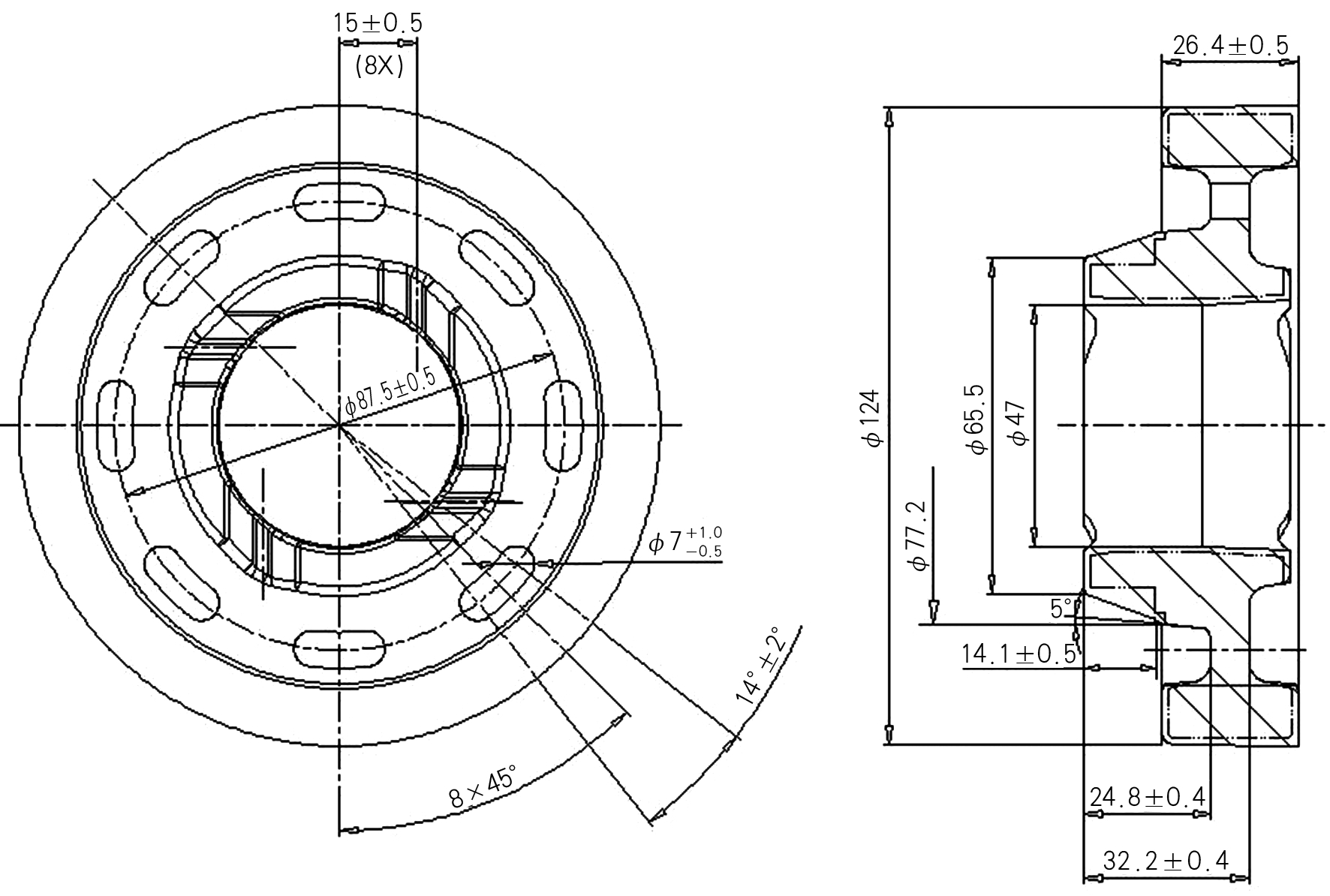
图1 产品简图
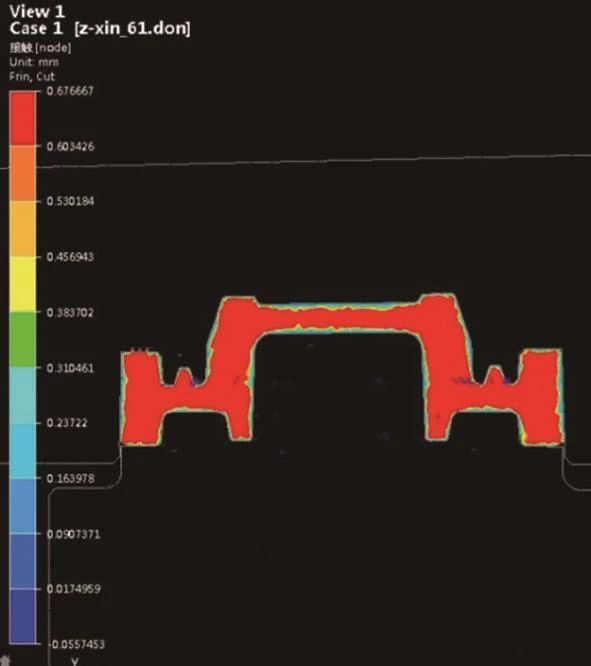
图2 产品三维模型
产品形状复杂,带双侧油槽及装配凸台,腹板孔与锻件凸台均有位置度及尺寸要求,且这些部位尺寸精度要求较为严格(公差±0.4mm),毛坯尺寸控制难度大。锻造冲孔工序同时冲多个腹板减重孔时,锻件受力复杂,尺寸变化大。
图3 锻造工艺流程
锻造工艺流程
为满足锻件尺寸要求,针对其结构特点进行详细的分析,制定了如下工艺方案:下料→中频感应加热→镦粗→预锻→终锻→冲孔、校正→抛丸→热处理(正火)→终检,锻造工艺流程见图3。
模具结构研究
腹板冲孔齿轮类锻件主要在锻压机上开发,其模具总体结构设计需符合设备参数要求。根据锻件成形的工艺流程,将模具设计分为锻模和冲校模具两部分。
锻模设计
锻模包括镦粗模、预锻模以及终锻模具。其中镦粗、预锻为预成形工步,主要起分配坯料的作用;终锻为终成形工步,成形冲孔前的产品功能尺寸。锻模结构设计的合理性对生产有着至关重要的影响。
⑴分块式模具结构,降低模具成本,提高模具寿命。
以往的齿轮终成形部分模具多采用整体结构,模块尺寸大,深型腔部位难充满、锻造时易出现应力集中开裂,凸芯子部位磨损快,模具成本高。现采用分块式模具(图4)结构,在难充满部位分块,上下模各自分成模套和模芯两部分,能有效的解决模具磨损、开裂及锻件充不满等问题,利于提高模具寿命。
模套与模芯之间采取间隙配合,但在实际生产过程中模具受热膨胀等因素影响,模芯易下沉发生侧偏现象,造成锻件厚度值超差。该系列产品厚度公差要求±0.5mm以内,为提高产品一致性,模套与模芯之间配合间隙设计必须合理,在0.10~0.20mm范围。
⑵双导向结构,有效控制锻件错差。
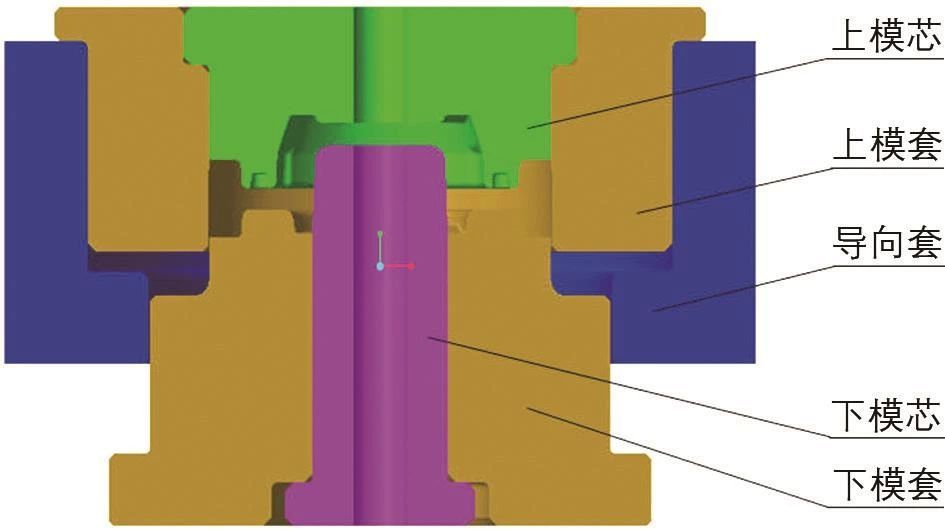
图4 分块模具结构
腹板冲孔齿轮系列产品机械加工余量少,错差必须严格控制才能保证余量均匀、机加工不留黑皮。分块式模具只靠上下模之间导向,生产中错差难以保证。经分析研究,增加导向套实现模具结构双导向。模具工作时导向套与下模先实现导向,当滑块距离下死点10~15mm时,开始进入上下模之间导向。这种结构能够有效减小因设备导轨间隙过大带来的上下模运动偏差,同时也能够减少因模具导向位置处的磨损带来的偏差,实际生产中有效地将锻件错差控制在≤0.4mm。
⑶增加定位凸台,解决冲孔工序定位问题。
产品腹板孔位与双侧凸台均有相对尺寸及位置要求(尺寸公差±0.5mm、角度公差±1°),要保证冲孔后产品满足要求,在冲孔工序必须进行精准定位。靠锻件自身形状无法实现,只能增加辅助定位即终锻工步在减重孔位置设计“凸起连皮”(图5),冲孔工序连皮落入凹模实现精准定位,冲孔时将连皮冲掉,完全不影响产品外观。
复合模设计
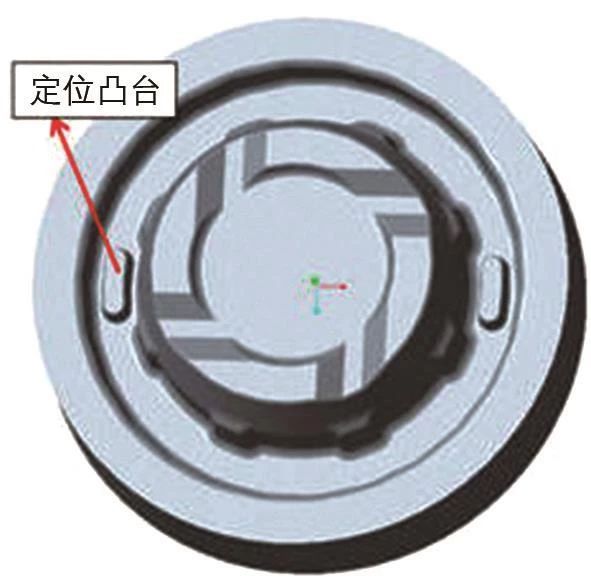
图5 定位凸台
该类齿轮大多腹板薄、孔多、锻造及冲孔后锻件极易变形,为保证产品要求冲孔、校正工步必不可少。由于设备问题,冲孔、校正工步在一台压床完成。考虑到人员成本、生产节拍等因素,联合模结构不适用,需设计冲孔与校正一体的复合模。复合模能实现先冲孔后校正,可有效解决冲孔引起的齿轮腹板变形等问题,生产效率也高。
⑴采用氮气弹簧退件,简化模具结构,解决拆装难问题。
一般复合模结构复杂,各个部件关联尺寸多,拆装调整难。采用氮气弹簧进行退件,能有效解决冲后粘模问题。考虑该系列产品腹板孔形状位置的严密性,所有腹板孔小冲头设计成冲头座压入式,简化了复合模结构,便于生产中冲头磨损、弯曲变形后拆装更换。利于提高生产效率,并减少模具浪费。
⑵仿形校正模设计,解决冲校后锻件变形超差问题。
锻件腹板冲孔过程中受力非常复杂,尺寸变化大,校正模设计难度大。校正模间隙设计不合理,会出现锻件粘模、尺寸超差、定位包变形等问题,影响锻件质量。经过多方评审论证、工艺模拟分析,校正模采用仿形设计,锻件与模具定位部分设计0.15mm间隙,锻件质量极大程度改善。
模拟分析
利用Forge成形软件对工艺及模具进行模拟分析(图6、图7),模拟初始条件设置如下:材料采用TL4227A,坯料初始温度1200℃,模具材料H13,模具与坯料之间采用水+石墨的润滑,设备选择2000t机械压力机。按照工艺流程模拟,最终实现成形,锻件充满良好,模具结构满足设计要求。
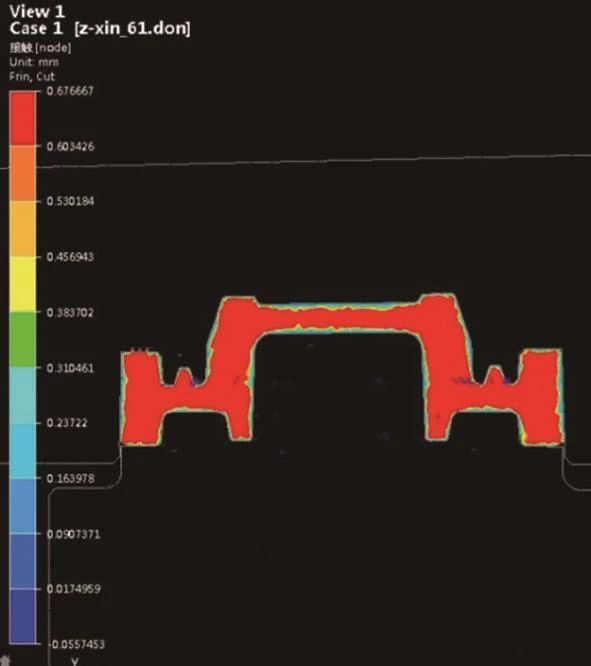
图6 充满示意
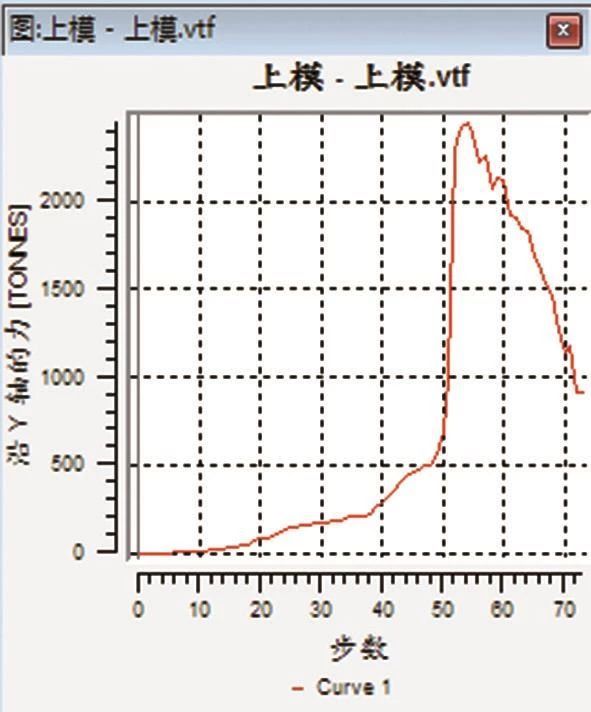
图7 成形力
工艺验证
根据模拟结果,采用1600t锻压机和200t压床进行生产验证,锻件尺寸精度满足图纸要求,且质量比较稳定。只是后期冲孔模寿命偏低,引起锻件腹板冲孔毛刺超差(图8);后续模具已进行优化设计,待批量生产验证。整个锻造过程控制手段不全面,传送带不满足要求,锻件磕碰伤严重(图9)。
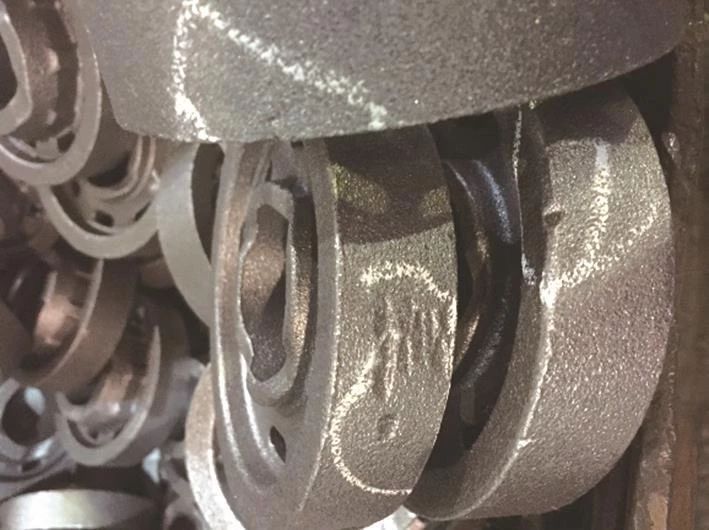
图8 冲孔毛刺
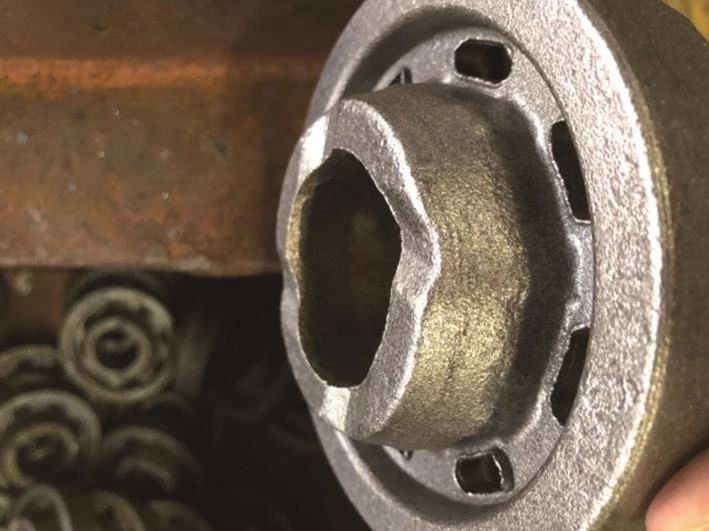
图9 磕碰伤
结论
⑴运用分块结构锻模及冲校复合模进行生产工艺验证,整个锻造工艺过程稳定,锻造产品外形、尺寸及表面质量完全满足客户要求。
⑵目前国内关于乘用车变速箱齿坯腹板冲孔工艺有很大研究空间,掌握该技术可以提高企业的核心市场竞争力,对今后类似产品的研发工作具有重要的影响。
- 下一篇:汽车零部件业的拆分趋势
- 上一篇:舍弗勒与上海国际汽车城签署合作协议
举报 0
收藏 0
分享 119
-
乘用车金属冲压
2025-05-29 -
冲压技术在电机叠片制造的应用
2024-09-06 -
车身零部件包边质量控制要点
2024-09-05 -
轻量化技术——热汽胀形工艺技术解析
2024-09-04
最新资讯
-
辐射亚太,链接全球——采埃孚再制造
2025-07-30 11:46
-
思看科技发布子品牌SCANOLOGY,全球
2025-07-30 11:06
-
风雨不动安如山——比亚迪叉车构筑“
2025-07-30 08:48
-
NEAS CHINA 新能源汽车技术与生态链
2025-07-29 09:52
-
三维扫描革新碾磨机辊套检测,效率与
2025-07-25 10:46