汽车轻量化技术手段探讨
2018-07-18 14:59:42· 来源:CST汽车轻量化
本文汽车轻量化是在保证汽车强度和安全性能的前提下,尽可能地降低汽车的质量,从而提高汽车的动力利用率,减少燃料消耗,降低排气污染。汽车轻量化还能提高汽车的驾乘动力学性能(如加速、制动、过弯稳定性、碰撞惯性等),而这类性能的改善一直是车辆设计者、制造商和用户追求的目标。
摘要:
本文汽车轻量化是在保证汽车强度和安全性能的前提下,尽可能地降低汽车的质量,从而提高汽车的动力利用率,减少燃料消耗,降低排气污染。汽车轻量化还能提高汽车的驾乘动力学性能(如加速、制动、过弯稳定性、碰撞惯性等),而这类性能的改善一直是车辆设计者、制造商和用户追求的目标。
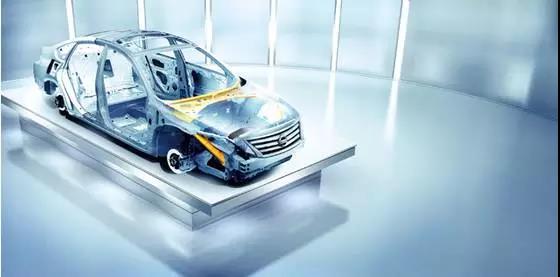
汽车轻量化是目前国内外汽车厂商普遍研究的一个热点,也是未来汽车发展的必然方向。研究表明,约75%的油耗与整车质量有关,降低汽车质量就可有效降低油耗以及排放。
大量研究表明,汽车质量每下降10%,油耗下降8%,排放下降4%。对商用车的研究表明,汽车质量每减1000kg,油耗可降低6%~7%。油耗的下降,意味着CO2、氮氧化物(NOx)等有害气体排放量的下降。因此,车身变轻对于整车的燃油经济性、车辆控制稳定性、碰撞安全性都大有裨益。当前,由于环保和节能的需要,汽车轻量化已经成为世界汽车发展的潮流。
构成汽车的2万多个零件中,约有86%是金属材料,且钢铁占了约80%,这表明通过材料的轻量化来减轻汽车自重有巨大潜力。目前,铝合金、镁合金、高强度钢、工程塑料和复合材料等轻质材料的开发和应用在汽车轻量化中发挥了重大作用。为了提升市场竞争力,国内外汽车厂商均在进行汽车轻量化技术的研究,并力求应用到汽车制造中,以保持自己在市场竞争中的有利地位。
但是,汽车轻量化并非只是简单地降低汽车重量,它必须在保证汽车安全性、整车NVH性能、可制造性以及经济性等各种前提下实现轻量化。同时,汽车轻量化涉及汽车上的每个部件,各个部件之间又相互影响、相互制约,每个部件在材料选择、制造工艺、结构设计等方面也都有不同的设计要求。因此,汽车轻量化是一个多领域技术综合作用的系统工程。
汽车轻量化方法
目前,国内外实现汽车轻量化的主要技术手段包括使用新材料、采用新工艺和轻量化结构设计等三大方面。
1使用新材料
随着材料科学的发展,新型高强度、低密度轻质材料(如高强度钢、铝合金、镁合金、高分子材料和复合材料等)在汽车制造中正逐步替代传统钢铁。目前正广泛研究并逐步应用于汽车制造的有:超高强度钢、铝合金、镁合金以及复合材料等。
国内轻量化新材料研究方面,同济大学将7075铝合金应用于汽车保险杠系统中,通过有限元软件LS-DYNA对不同厚度保险杠模型的低速碰撞进行仿真分析。在碰撞性能相同的条件下,相比原钢质材料,采用铝合金可使保险杠质量下降20.5%。
上海交通大学通过建立某款轿车发动机罩板的有限元模型,选择铝合金材料替换原有钢材料,以罩板综合性能为约束,结合优化设计方法,考虑板材的成形性因素。基于原始钢结构空间布局进行全新设计,在满足结构性能要求和可制造性的前提下使罩板的质量减轻47.1%。
目前发达国家汽车的单车塑料平均使用量超过150kg,占汽车总重量的12%~20%,而我国单车塑料使用量约占汽车自重的7%~10%。工程塑料在汽车工业上的应用虽然越来越广泛,但是由于我国汽车零部件标准体系不健全、国内企业科研投入不足、自主创新能力不足等因素的影响,很大程度上制约了我国工程塑料的发展。
奇瑞汽车股份有限公司汽车工程研究院研究了金属材料镁合金在转向盘骨架、仪表板横梁、变速器壳体、座椅骨架等零部件上的应用。同时,上海通用柳州公司和东风公司正计划推出全复合材料家庭用小轿车。但以上国内材料轻量化技术主要侧重于理论及技术可行性的研究,并未充分考虑生产实际中的一些技术条件及生产成本等限制要求,基本未能投入实际生产。
20世纪90年代,美国钢铁协会AISI成功研制出高强度钢车身,使车身整备质量比普通钢结构车身减轻了25%,由此开创了使用高强度钢等新型材料用于汽车轻量化设计的理念。2006年马自达汽车公司的新MAZDA Demio大量采用了高强度钢板,并提高了强度的级别,使新车型车身比原型车轻了22kg。
近年来,奥迪不断生产全铝车身,使其TT车型比前代车型重量降低多达90kg,新款A6减重多达80kg,奥迪R8 GT高性能跑车重量1525kg;2011年7月,德国宝马汽车在法兰克福发布了两款碳纤维电动汽车,宝马i系列电动车采用轻型的铝材质底盘及加强型的碳纤维车身结构,比传统电动汽车减轻了250~350kg。
德国概念汽车研究中心对汽车结构的发展方向进行了预测,表明多材料结构车身将逐步代替单一的钢结构车身,目的是根据不同需求在适当的位置选用合理的材料,并表示这是实现汽车轻量化的一个非常重要的途径。国外的汽车厂商及研究机构已将新材料广泛用于生产实践,并已取得了明显的轻量化效果。
目前,国内汽车所使用的材料大部分为普通钢材(低碳钢与中碳钢),采用新材料可以实现较大的轻量化效果。但是,替换新材料往往都面临成本高、加工性能差和表面处理难等问题,而且对整车的强度、刚度、疲劳强度、被动安全性能及NVH性能等影响都较大,故新材料的使用需综合考虑生产成本、加工性能及安全性能等各方面的因素。
2采用新工艺
传统的加工工艺已不能满足新材料的使用要求,采用新工艺一方面可以直接带来轻量化效果,另一方面使部分新材料的引入成为可能,进而推动了轻量化新工艺的发展。轻量化新工艺主要包括成形新工艺和连接新工艺两大块。
前者从传统的钢板冷冲压成形、铸造等发展到热冲压成形(HPF)、液压成形(HF)、拼焊板成形(TWBF)、连续变截面辊轧(TRB)、铝合金真空辅助压铸(VAPC)、镁合金压铸(MDC)、铝合金挤压成型(AE)、增量成形(ISF)、弯管成形等。
后者从传统的焊接方式(电阻点焊、MIG/MAG、激光焊)发展到激光-MIG复合焊、双焦点激光复合焊(BHLW)、超声波焊接(USW)、自铆焊(SPR)、搅拌摩擦焊(FSW)、汽车结构胶粘接(ASAT)、电磁焊接(MDW)等。
(1) 成形新工艺
国内方面,阿赛洛、蒂森克虏伯、本特勒等公司建立了超高强度钢热冲压生产线、宝钢、鞍钢等钢铁生产企业建立了拼焊板成形生产线基地,为国内各大汽车生产厂家配货。
其它成形新工艺在国内汽车生产中的应用未见相关报导,而主要是对其进行理论研究,如机械科学研究总院、中国一汽、上海交通大学等在铝合金材料的超塑成型、挤压成形、半固态挤压铸造、铝合金表面处理工艺及连接技术等方面做了大量研究并取得众多专利成果,为开发铝合金车身提供了重要的技术支撑及理论依据。
国外方面,美国通用、福特、克莱斯勒三大汽车公司的门内板、侧围、门框等零件均采用了拼焊板成形技术;沃尔沃(VOLVO)、保时捷、戴姆勒-克莱斯勒、大众等公司在车身安全件上大多采用了超高强度钢的热冲压成形技术。
德国大众公司开发出了镁合金汽车覆盖件的热冲压技术,成功地生产出镁合金汽车门内板。美国通用开发了真空辅助压铸和高真空压铸技术,用于生产高整体性的车体和底盘零件,采用低压金属型铸造工艺生产了结构用薄壁空心铸件等。
(2) 连接新工艺
国内方面,车身连接工艺还主要为电弧焊、电阻点焊、激光焊、MIG/MAG等传统焊接方式。而国外方面,传统的焊接方式正逐渐被取代,如2002年奥迪A8 D3的铆接点为2400个,而电阻焊铝焊点全部取消;大众辉腾的车门焊缝中激光-MIG复合焊焊缝长度占总长(4980mm)的72%,而MIG焊缝与激光焊焊缝长度之和仅占总长的28%。美国通用汽车在其大部分车型上正广泛应用结构胶技术作为其实现轻量化的重要手段之一,在保持车身质量不变的情况下将车身刚度提高25%左右。
综上所述,国内轻量化新工艺在汽车制造中所占的比重、相关研究的投入及实践探索方面均远远落后于国外汽车厂商。在国内汽车生产制造中,很少涉及轻量化新工艺,车身零部件的制造也基本是靠冷成形加工获得。国内汽车厂家若想生产高质量汽车,必须加大力度进行研究,争取在工艺技术上有所突破或创新。
3轻量化结构设计
汽车轻量化结构设计主要是在满足设计性能要求的前提下,尽可能使汽车零部件的材料在空间合理分布,避免不必要的材料利用,以获得最轻的结构设计。
国内相关研究方面,中北大学针对某越野车悬架的摆臂结构,应用轻型的铝合金材料替代原来的钢板材料并对其结构进行拓扑优化,使该越野车的悬架摆臂减重12.1%。
华南理工大学和浙江吉利汽车研究院有限公司共同研究了在满足车身模态、刚度和碰撞安全等多项性能要求前提下的轻量化车身结构多目标优化方法,优化结果提高了整车的碰撞安全性,使白车身扭转刚度得到了很好的控制,同时实现了白车身零件的轻量化效果。
大连理工大学提出了一种在概念设计阶段,确定截面几何特性的算法和基于尺寸向量控制截面形状的方法以优化薄壁杆件的截面形状,并采用基于粒子群的优化算法对杆件截面厚度和形状进行优化,以达到车身的轻量化目的。
吉林大学通过对不同类型薄壁梁的几何及力学特性的基础理论分析,考虑车身结构几何特性、力学特性及工艺因素,对轿车碰撞参数化结构的建模方式进行研究,分别建立轿车车身部件的有限元模型及其相应的参数化简化模型,为轿车参数化结构建模及优化奠定基础。
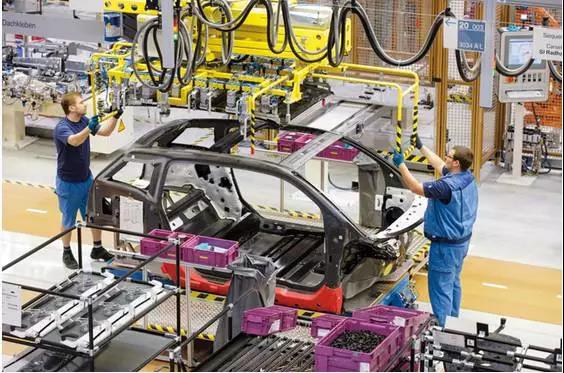
国外方面,英国考文垂大学在满足汽车碰撞安全性的前提下进行某电动汽车的白车身结构拓扑优化,获得了较优的白车身拓扑结构,既满足碰撞安全性能的要求,又实现了白车身的轻量化效果。
美国哥伦比亚大学利用等效静载荷方法开创了一种新的结构设计拓扑优化方法。
澳大利亚皇家墨尔本理工大学基于有限元平台提出了一种新的汽车结构快速设计方法,这种方法在不失精度的情况下可以大大提高分析的效率和计算迭代的步数,并通过某汽车座椅致动器总成的结构优化设计进行了验证。
韩国汉阳大学和美国乔治华盛顿大学利用等效静载荷方法来求解非线性动态响应优化问题,对车顶进行尺寸优化,在满足车辆侧翻安全的同时使车顶达到了轻量化的效果。
在轻量化结构设计方面,国内外均有大量研究。但国内在该部分所做的研究范围(仅关心质量大的零部件)及深度与国外相关厂商或研究机构还有较大差距。随着各种新车型的不断推出,结构优化设计是汽车厂商一直面临的一个问题,该部分的理论及应用价值值得深入研究,以充分挖掘汽车零部件的轻量化潜力,达到轻量化的目的。
综上所述,汽车轻量化是一个涉及技术领域广,影响因素多的系统工程,同时也是目前国内外汽车厂商研究的一个重要课题。综合考虑轻量化研发及技术水平现状等问题,国内各汽车厂商急需建立和完善适合自身发展的轻量化技术平台,这对树立国产汽车产品高端品牌形象,提升其市场竞争力,推动我国汽车制造技术水平的发展等都具有重要作用。
本文汽车轻量化是在保证汽车强度和安全性能的前提下,尽可能地降低汽车的质量,从而提高汽车的动力利用率,减少燃料消耗,降低排气污染。汽车轻量化还能提高汽车的驾乘动力学性能(如加速、制动、过弯稳定性、碰撞惯性等),而这类性能的改善一直是车辆设计者、制造商和用户追求的目标。
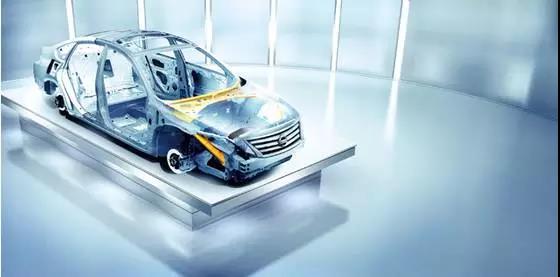
汽车轻量化是目前国内外汽车厂商普遍研究的一个热点,也是未来汽车发展的必然方向。研究表明,约75%的油耗与整车质量有关,降低汽车质量就可有效降低油耗以及排放。
大量研究表明,汽车质量每下降10%,油耗下降8%,排放下降4%。对商用车的研究表明,汽车质量每减1000kg,油耗可降低6%~7%。油耗的下降,意味着CO2、氮氧化物(NOx)等有害气体排放量的下降。因此,车身变轻对于整车的燃油经济性、车辆控制稳定性、碰撞安全性都大有裨益。当前,由于环保和节能的需要,汽车轻量化已经成为世界汽车发展的潮流。
构成汽车的2万多个零件中,约有86%是金属材料,且钢铁占了约80%,这表明通过材料的轻量化来减轻汽车自重有巨大潜力。目前,铝合金、镁合金、高强度钢、工程塑料和复合材料等轻质材料的开发和应用在汽车轻量化中发挥了重大作用。为了提升市场竞争力,国内外汽车厂商均在进行汽车轻量化技术的研究,并力求应用到汽车制造中,以保持自己在市场竞争中的有利地位。
但是,汽车轻量化并非只是简单地降低汽车重量,它必须在保证汽车安全性、整车NVH性能、可制造性以及经济性等各种前提下实现轻量化。同时,汽车轻量化涉及汽车上的每个部件,各个部件之间又相互影响、相互制约,每个部件在材料选择、制造工艺、结构设计等方面也都有不同的设计要求。因此,汽车轻量化是一个多领域技术综合作用的系统工程。
汽车轻量化方法
目前,国内外实现汽车轻量化的主要技术手段包括使用新材料、采用新工艺和轻量化结构设计等三大方面。
1使用新材料
随着材料科学的发展,新型高强度、低密度轻质材料(如高强度钢、铝合金、镁合金、高分子材料和复合材料等)在汽车制造中正逐步替代传统钢铁。目前正广泛研究并逐步应用于汽车制造的有:超高强度钢、铝合金、镁合金以及复合材料等。
国内轻量化新材料研究方面,同济大学将7075铝合金应用于汽车保险杠系统中,通过有限元软件LS-DYNA对不同厚度保险杠模型的低速碰撞进行仿真分析。在碰撞性能相同的条件下,相比原钢质材料,采用铝合金可使保险杠质量下降20.5%。
上海交通大学通过建立某款轿车发动机罩板的有限元模型,选择铝合金材料替换原有钢材料,以罩板综合性能为约束,结合优化设计方法,考虑板材的成形性因素。基于原始钢结构空间布局进行全新设计,在满足结构性能要求和可制造性的前提下使罩板的质量减轻47.1%。
目前发达国家汽车的单车塑料平均使用量超过150kg,占汽车总重量的12%~20%,而我国单车塑料使用量约占汽车自重的7%~10%。工程塑料在汽车工业上的应用虽然越来越广泛,但是由于我国汽车零部件标准体系不健全、国内企业科研投入不足、自主创新能力不足等因素的影响,很大程度上制约了我国工程塑料的发展。
奇瑞汽车股份有限公司汽车工程研究院研究了金属材料镁合金在转向盘骨架、仪表板横梁、变速器壳体、座椅骨架等零部件上的应用。同时,上海通用柳州公司和东风公司正计划推出全复合材料家庭用小轿车。但以上国内材料轻量化技术主要侧重于理论及技术可行性的研究,并未充分考虑生产实际中的一些技术条件及生产成本等限制要求,基本未能投入实际生产。
20世纪90年代,美国钢铁协会AISI成功研制出高强度钢车身,使车身整备质量比普通钢结构车身减轻了25%,由此开创了使用高强度钢等新型材料用于汽车轻量化设计的理念。2006年马自达汽车公司的新MAZDA Demio大量采用了高强度钢板,并提高了强度的级别,使新车型车身比原型车轻了22kg。
近年来,奥迪不断生产全铝车身,使其TT车型比前代车型重量降低多达90kg,新款A6减重多达80kg,奥迪R8 GT高性能跑车重量1525kg;2011年7月,德国宝马汽车在法兰克福发布了两款碳纤维电动汽车,宝马i系列电动车采用轻型的铝材质底盘及加强型的碳纤维车身结构,比传统电动汽车减轻了250~350kg。
德国概念汽车研究中心对汽车结构的发展方向进行了预测,表明多材料结构车身将逐步代替单一的钢结构车身,目的是根据不同需求在适当的位置选用合理的材料,并表示这是实现汽车轻量化的一个非常重要的途径。国外的汽车厂商及研究机构已将新材料广泛用于生产实践,并已取得了明显的轻量化效果。
目前,国内汽车所使用的材料大部分为普通钢材(低碳钢与中碳钢),采用新材料可以实现较大的轻量化效果。但是,替换新材料往往都面临成本高、加工性能差和表面处理难等问题,而且对整车的强度、刚度、疲劳强度、被动安全性能及NVH性能等影响都较大,故新材料的使用需综合考虑生产成本、加工性能及安全性能等各方面的因素。
2采用新工艺
传统的加工工艺已不能满足新材料的使用要求,采用新工艺一方面可以直接带来轻量化效果,另一方面使部分新材料的引入成为可能,进而推动了轻量化新工艺的发展。轻量化新工艺主要包括成形新工艺和连接新工艺两大块。
前者从传统的钢板冷冲压成形、铸造等发展到热冲压成形(HPF)、液压成形(HF)、拼焊板成形(TWBF)、连续变截面辊轧(TRB)、铝合金真空辅助压铸(VAPC)、镁合金压铸(MDC)、铝合金挤压成型(AE)、增量成形(ISF)、弯管成形等。
后者从传统的焊接方式(电阻点焊、MIG/MAG、激光焊)发展到激光-MIG复合焊、双焦点激光复合焊(BHLW)、超声波焊接(USW)、自铆焊(SPR)、搅拌摩擦焊(FSW)、汽车结构胶粘接(ASAT)、电磁焊接(MDW)等。
(1) 成形新工艺
国内方面,阿赛洛、蒂森克虏伯、本特勒等公司建立了超高强度钢热冲压生产线、宝钢、鞍钢等钢铁生产企业建立了拼焊板成形生产线基地,为国内各大汽车生产厂家配货。
其它成形新工艺在国内汽车生产中的应用未见相关报导,而主要是对其进行理论研究,如机械科学研究总院、中国一汽、上海交通大学等在铝合金材料的超塑成型、挤压成形、半固态挤压铸造、铝合金表面处理工艺及连接技术等方面做了大量研究并取得众多专利成果,为开发铝合金车身提供了重要的技术支撑及理论依据。
国外方面,美国通用、福特、克莱斯勒三大汽车公司的门内板、侧围、门框等零件均采用了拼焊板成形技术;沃尔沃(VOLVO)、保时捷、戴姆勒-克莱斯勒、大众等公司在车身安全件上大多采用了超高强度钢的热冲压成形技术。
德国大众公司开发出了镁合金汽车覆盖件的热冲压技术,成功地生产出镁合金汽车门内板。美国通用开发了真空辅助压铸和高真空压铸技术,用于生产高整体性的车体和底盘零件,采用低压金属型铸造工艺生产了结构用薄壁空心铸件等。
(2) 连接新工艺
国内方面,车身连接工艺还主要为电弧焊、电阻点焊、激光焊、MIG/MAG等传统焊接方式。而国外方面,传统的焊接方式正逐渐被取代,如2002年奥迪A8 D3的铆接点为2400个,而电阻焊铝焊点全部取消;大众辉腾的车门焊缝中激光-MIG复合焊焊缝长度占总长(4980mm)的72%,而MIG焊缝与激光焊焊缝长度之和仅占总长的28%。美国通用汽车在其大部分车型上正广泛应用结构胶技术作为其实现轻量化的重要手段之一,在保持车身质量不变的情况下将车身刚度提高25%左右。
综上所述,国内轻量化新工艺在汽车制造中所占的比重、相关研究的投入及实践探索方面均远远落后于国外汽车厂商。在国内汽车生产制造中,很少涉及轻量化新工艺,车身零部件的制造也基本是靠冷成形加工获得。国内汽车厂家若想生产高质量汽车,必须加大力度进行研究,争取在工艺技术上有所突破或创新。
3轻量化结构设计
汽车轻量化结构设计主要是在满足设计性能要求的前提下,尽可能使汽车零部件的材料在空间合理分布,避免不必要的材料利用,以获得最轻的结构设计。
国内相关研究方面,中北大学针对某越野车悬架的摆臂结构,应用轻型的铝合金材料替代原来的钢板材料并对其结构进行拓扑优化,使该越野车的悬架摆臂减重12.1%。
华南理工大学和浙江吉利汽车研究院有限公司共同研究了在满足车身模态、刚度和碰撞安全等多项性能要求前提下的轻量化车身结构多目标优化方法,优化结果提高了整车的碰撞安全性,使白车身扭转刚度得到了很好的控制,同时实现了白车身零件的轻量化效果。
大连理工大学提出了一种在概念设计阶段,确定截面几何特性的算法和基于尺寸向量控制截面形状的方法以优化薄壁杆件的截面形状,并采用基于粒子群的优化算法对杆件截面厚度和形状进行优化,以达到车身的轻量化目的。
吉林大学通过对不同类型薄壁梁的几何及力学特性的基础理论分析,考虑车身结构几何特性、力学特性及工艺因素,对轿车碰撞参数化结构的建模方式进行研究,分别建立轿车车身部件的有限元模型及其相应的参数化简化模型,为轿车参数化结构建模及优化奠定基础。
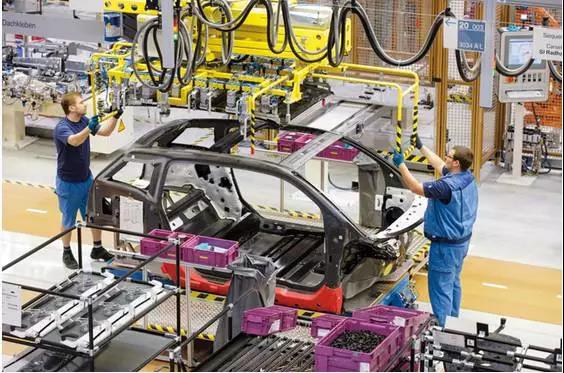
国外方面,英国考文垂大学在满足汽车碰撞安全性的前提下进行某电动汽车的白车身结构拓扑优化,获得了较优的白车身拓扑结构,既满足碰撞安全性能的要求,又实现了白车身的轻量化效果。
美国哥伦比亚大学利用等效静载荷方法开创了一种新的结构设计拓扑优化方法。
澳大利亚皇家墨尔本理工大学基于有限元平台提出了一种新的汽车结构快速设计方法,这种方法在不失精度的情况下可以大大提高分析的效率和计算迭代的步数,并通过某汽车座椅致动器总成的结构优化设计进行了验证。
韩国汉阳大学和美国乔治华盛顿大学利用等效静载荷方法来求解非线性动态响应优化问题,对车顶进行尺寸优化,在满足车辆侧翻安全的同时使车顶达到了轻量化的效果。
在轻量化结构设计方面,国内外均有大量研究。但国内在该部分所做的研究范围(仅关心质量大的零部件)及深度与国外相关厂商或研究机构还有较大差距。随着各种新车型的不断推出,结构优化设计是汽车厂商一直面临的一个问题,该部分的理论及应用价值值得深入研究,以充分挖掘汽车零部件的轻量化潜力,达到轻量化的目的。
综上所述,汽车轻量化是一个涉及技术领域广,影响因素多的系统工程,同时也是目前国内外汽车厂商研究的一个重要课题。综合考虑轻量化研发及技术水平现状等问题,国内各汽车厂商急需建立和完善适合自身发展的轻量化技术平台,这对树立国产汽车产品高端品牌形象,提升其市场竞争力,推动我国汽车制造技术水平的发展等都具有重要作用。
- 下一篇:零件去毛刺工艺概览
- 上一篇:艾默生并购安沃驰,家族再添新成员
编辑推荐
最新资讯
-
BBA集体转向!放弃全面电动化
2025-06-26 17:32
-
比换柜省钱,比自研省心,西门子Xcel
2025-06-25 15:07
-
采埃孚售后再制造中心乔迁临港 领航
2025-06-25 14:44
-
比亚迪叉车:「碳」索未来,献「锂」
2025-06-25 11:04
-
专家访谈:埃马克 OCTG 加工的技术密
2025-06-25 10:51