探秘汽车柔性制造系统 体验前沿智能制造技术
2018-04-27 21:01:53· 来源:金属加工
随着汽车工业的发展,国内汽车企业实力逐步增强,以及国外公司的大规模进入和生产装备的改善,汽车零部件加工正在向柔性制造方向发展。柔性制造系统(FMS,Flexible Manufacturing System)带来了加工的高度灵活性,使得在保持高生产率的同时还能生产更多种类的零件。
随着汽车工业的发展,国内汽车企业实力逐步增强,以及国外公司的大规模进入和生产装备的改善,汽车零部件加工正在向柔性制造方向发展。柔性制造系统(FMS,Flexible Manufacturing System)带来了加工的高度灵活性,使得在保持高生产率的同时还能生产更多种类的零件。
FMS简介
柔性制造系统是由统一的信息控制系统、物料储运系统和一组数字控制加工设备组成,能适应加工对象变换的自动化机械制造系统。FMS是一组数控机床和其他自动化的工艺设备,由计算机信息控制系统和物料自动储运系统有机结合的整体,简单地说,由加工、物流、信息流三个子系统组成。
从FMS的构成看,其兼有加工制造和部分生产管理两种功能。从柔性考虑,一方面是系统适应外部环境变化的能力,可用系统满足新产品要求的程度来衡量;另一方面是系统适应内部变化的能力,在有干扰(如机器出现故障)情况下,系统的生产率与无干扰情况下的生产率期望值之比可以用来衡量柔性。
柔性是FMS的最大特点,主要表现在以下几个方面:
1)按需及时安排生产,缩短交货周期。
2)工序高度集中,可提高设备利用率。
3)减少直接劳动力,在少人看管条件下可实现昼夜24h连续“无人化生产”。
4)提高产品质量的一致性。
5)单台故障,任务可转移其他机床。
柔性组合夹具的产生及应用
柔性组合夹具的产生及发展应用,包括三个方面:柔性元件的设计,柔性组合夹具在现代加工中心上的技术应用,以及在柔性制造技术环境下的柔性组合夹具的管理。
1 柔性元件的设计
以柔性制造单元为代表的加工中心,其对工件多道工序的集合高效加工,形成了夹具一次装夹完成多个工序的加工。机床与夹具和工件形成了与传统加工方式截然相反的关系,即在一个夹具的底板上,尽可能安装最大容量的加工零件,并且这套夹具处于加工位置时,另一些具有相同特点的夹具正在机外装卸工件,甚至一些安装在托板上的夹具,正在传输系统中周转。夹具保证了被加工零件能够精确载入机床的坐标系之中,处在机床加工位置上(即夹具上)的工件全部加工完成后,机内夹具与机外夹具整体交换,夹具与机床实现反复快速的定位连接。由于实现了机外安装夹具和机外装卸工件,机床切削加工时间与夹具安装及工件装夹时间重合,这就大大减少了停机时间。基于此,柔性组合夹具在元件系列的设计上发展出与其相适应和匹配的元件系列。
这些元件的最大特点是:与机床工作台的连接非常紧密和快捷,可以直接连接在机床的工作台或托板上,甚至托板系统中的“托板”直接按柔性组合夹具元件结构要素进行设计,使其直接成为机床的附件。一些新型多功能的定位组合件、夹紧合件以及定位夹紧组合件相继出现,虽然并未从根本上改变传统组合夹具的元件特点,但是取代了多件叠加的繁琐,一些带有坐标原点的孔类定位元件,使柔性组合夹具在多个工件的定位上能够精确载入机床的坐标系。柔性组合夹具元件的发展,为柔性组合夹具在柔性制造技术环境下的应用奠定了基础。
绅名科技-底盘系统关键零部件柔性装配线
工作中常常谈及装配线柔性问题,个人简单理解为柔性装配线也可称可编程序,快换产品装配线,是在非间歇传送装配的基础上,采用可编程序和转换程序,快速更换工装夹具来实现快速转换装配多项产品的装配线。
1、组成
柔性装配线通常由装配站、物料输送装置和控制系统等组成。
(1)装配站
柔性装配线中的装配站可以是可编程的装配机器人,不可编程的自动装配装置和人工装配工位。
(2)物料输送装置
柔性装配线输入的是组成产品或部件的各种零件,输出的是产品或部件。根据装配工艺流程,物料输送装置将不同的零件和已装配成的半成品送到相应的装配站。输送装置由传送器和换向机构、定位机构、传感机构、控制位系统等的有机组合组成。
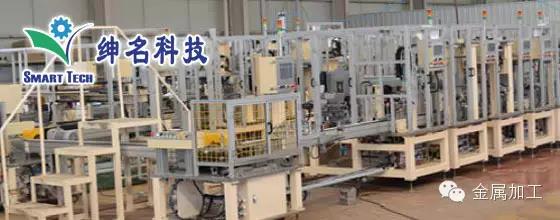
图1
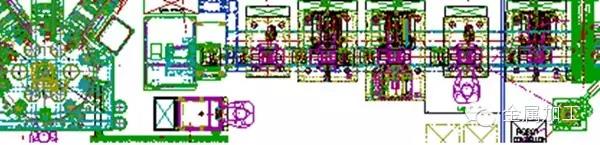
图2
2、机械运动和控制系统
图1是柔性装配线照片,图2是柔性装配线布局示意图。投料工作站中有料库和取料机器人。料库有各种盒子、漏斗、穿料棒等组成,待装配的零件存放在这些存料机构中,取料机器人有各种不同的夹爪,它可以自动地将零件从盒子中取出,并摆放在一个工装中,被装配机构自动检测装配。或者盛有零件的工装托盘由传送带自动地送往装配机器人或装配站完成装配。常用的主要部件有各种送料振动盘、震动导轨、气动元件、液压元件、伺服电机、油脂泵和阀、导轨和丝杠、电动力矩扳手等机械原件和力矩传感器、位移传感器、力传感器、光电传感器、接近传感器、视觉传感器、泄漏测试仪、人机界面(触摸屏)、无线射频识别、工控机、变频器、PLC及电源等的电气元件。
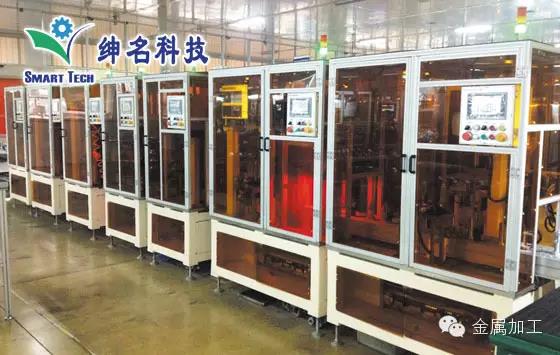
3、柔性的主要实现方式
(1)通过对同类不同产品部件的外形和材质综合分析,设计预制出单台工艺设备可在几分钟内快速跟换调试的工装和夹具来实现柔性装配。设计方面可应用为了快速调试使用通常设置定位销、硬限位、导向槽、快校工装付具。
(2)通过控制模块预留扩展空间和预先编程存储再系统中,可通过增加控制模块或转换开关或触摸屏选项按钮快速转换程序来实现柔性装配。
2柔性组合夹具的应用性
在柔性制造技术中,夹具是影响其柔性发挥的关键因素。在计算机集成制造系统(CIMS)试验以及许多单位的柔性制造系统的多年实践中,大家发现,在机床与加工零件对接的夹具环节上实现无人化或期望理想状态的柔性化,是相当困难的。无人化还须有相当程度的技术支持,或可在某一领域实现,但要扩展到能涵盖更多的领域,是极其困难的。理想状态柔性化实现的最便捷途径,就是改造传统的组合夹具,将组合夹具结构变化上具有的万能性优势,改造成柔性化的特点。
柔性组合夹具元件的发展,为柔性组合夹具在柔性制造技术中的应用,奠定了基础。柔性组合夹具在汽车的柔性制造中,已经发挥出显着的作用。柔性化组合夹具与元件系列及机床的关系更加紧密,元件系统有了压缩,柔性组合夹具技术在机床上的应用开始简单化,夹具的结构亦从复杂向简单演变。
在汽车柔性制造技术环境下,柔性组合夹具被大量应用,尤其在发动机、变速器及离合器等关键零件的制造中。如在离合器和变速器之类壳体、壳盖的夹具结构中,广泛采用桥梁式夹具结构,使得两面加工得以方便实现。由于这类零件多为铝合金材料,支持被加工零件的局部刚度,在更加直观的现场中,可以轻易实现。各种理想的典型柔性组合夹具结构,就是其技术应用的直接成果。加强这一方面的技术研究与发展,是提高柔性组合夹具柔性化的重要环节。
雄克公司-VERO-S
雄克公司VERO-S零点快换夹持系统能够有效辅助发动机加工线实现柔性生产,颠覆传统的装夹原理。以前每一次重新装夹工件,都可能导致精度的损失。但VERO-S的重复定位精度小于5微米,几乎可做到无任何精度损失,且可使工件坯料一次装夹(或于托板上)完成五面加工,以及多工位互换加工,其卓越的性能、简单的结构、工况的不敏感性,将使之扩展到整个机械制造行业,并带来整个制造工艺系统革新的应用。
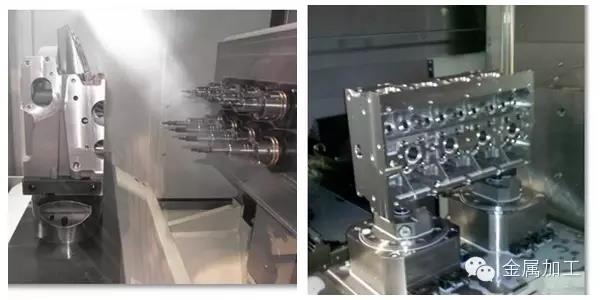
传统的发动机缸体和缸盖夹具为例,其特点主要为:
● 框架结构,刚性好,重量大
● 不易安装,定位精度较高,复杂程度高
● 专机专用,不能重复使用
● 自动化上下料困难
● 夹持点多,夹紧监控复杂
雄克VERO-S系统应用于发动机缸盖的快换装夹时,夹持模块的柔性设计:工件表面无传统夹持方式所带来的额外压力,如弹簧力、液压或气动压板等(依赖于有效的工作空间及拉紧力需求)。
夹持力的均匀分布在缸盖表面:取决于夹紧销的数量、螺栓大小(夹紧销、工件),夹紧销位置及保留的关系。
雄克VERO-S快换系统工艺结构
VERO-S零点快换夹持系统特点:
1.标准化接口。由两部分组成:快换模块与托盘。托盘是连接工件与快换模块接口的载体,通过夹紧定位销与快换模块连接,可兼容各类夹紧工装。
2.强大的夹紧力。单个快换模块的夹紧力高达40kN,增压型可达75kN。
3.可靠的重复定位精度。多个工序之间的重复定位精度确保在0.005mm范围之内。
4.高柔性。可实现不同产品间的快速切换,即使在大批量制造过程中(如发动机缸盖加工),实现柔性的共线生产。
下面是几个柔性组合夹具的具体应用实例。
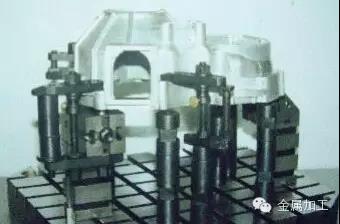
图1,汽车离合器壳体零件在立式加工中心上所采用的柔性组合夹具。此夹具只是定位与夹紧元件的组装,结构简单,敞开性好,完成夹具组装只需30min,在柔性化生产中,其快速性由此可见。
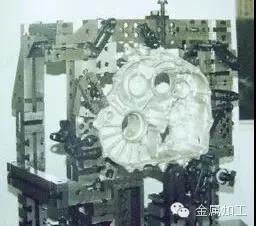
图2,汽车离合器上壳体零件在卧式加工中心上所采用的柔性组合夹具。可看出,夹具虽然是围绕零件的框架式结构,但考虑加工状态的切削力,框柱组成双体并作加固,各定位点和辅助支撑点分布得当,充分显示出柔性组合夹具在其结构演变上的柔性化。
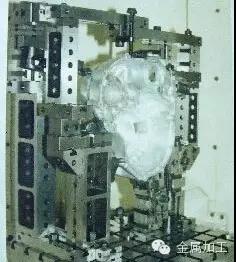
图3,汽车离合器上壳体零件在卧式加工中心上所采用的柔性组合夹具。由于零件的形状特点与定位要求,柔性组合夹具在其技术应用上,几乎可以胜任任何结构的设计,并能经受大切削力条件下的加工要求。
3 加强柔性组合夹具的技术管理性
柔性组合夹具管理,包括元件系列及人的组合装配,以及在这两个因素下衍生出来的比如元件配置规模和在生产准备中所处的管理位置、元件管理和技术管理等,这将决定柔性组合夹具发挥作用的程度,同时也涉及到柔性组合夹具的投入(包含日后的管理投入)与发挥作用的性价比。也可以说,其技术发挥与管理水平的程度决定其柔性化的程度。
柔性组合夹具元件、技术运用、技术管理是柔性组合夹具的三个方面。如果说元件是基础,技术运用是关键,那么技术管理就是前两者的保障,而且在前两者的作用中,本身就贯穿着管理的因素。如元件的型别、配套量,元件间的类别比例,现场流通量与库存量的比例,元件的更换频率和幅度,元件使用的各种必要制度等。在技术管理中,管理的重要性则显现的更为突出。
传统组合夹具的管理模式已经落伍,建立一个庞大“组装站”的管理方法,将会占用大量的资源和资金,在进行生产准备中,实现夹具的快速反应又存在着时间差,故必须予以改变。在现代生产模式下,采用更适合、更科学的管理模式,已经是一个迫在眉睫的问题。
FMS简介
柔性制造系统是由统一的信息控制系统、物料储运系统和一组数字控制加工设备组成,能适应加工对象变换的自动化机械制造系统。FMS是一组数控机床和其他自动化的工艺设备,由计算机信息控制系统和物料自动储运系统有机结合的整体,简单地说,由加工、物流、信息流三个子系统组成。
从FMS的构成看,其兼有加工制造和部分生产管理两种功能。从柔性考虑,一方面是系统适应外部环境变化的能力,可用系统满足新产品要求的程度来衡量;另一方面是系统适应内部变化的能力,在有干扰(如机器出现故障)情况下,系统的生产率与无干扰情况下的生产率期望值之比可以用来衡量柔性。
柔性是FMS的最大特点,主要表现在以下几个方面:
1)按需及时安排生产,缩短交货周期。
2)工序高度集中,可提高设备利用率。
3)减少直接劳动力,在少人看管条件下可实现昼夜24h连续“无人化生产”。
4)提高产品质量的一致性。
5)单台故障,任务可转移其他机床。
柔性组合夹具的产生及应用
柔性组合夹具的产生及发展应用,包括三个方面:柔性元件的设计,柔性组合夹具在现代加工中心上的技术应用,以及在柔性制造技术环境下的柔性组合夹具的管理。
1 柔性元件的设计
以柔性制造单元为代表的加工中心,其对工件多道工序的集合高效加工,形成了夹具一次装夹完成多个工序的加工。机床与夹具和工件形成了与传统加工方式截然相反的关系,即在一个夹具的底板上,尽可能安装最大容量的加工零件,并且这套夹具处于加工位置时,另一些具有相同特点的夹具正在机外装卸工件,甚至一些安装在托板上的夹具,正在传输系统中周转。夹具保证了被加工零件能够精确载入机床的坐标系之中,处在机床加工位置上(即夹具上)的工件全部加工完成后,机内夹具与机外夹具整体交换,夹具与机床实现反复快速的定位连接。由于实现了机外安装夹具和机外装卸工件,机床切削加工时间与夹具安装及工件装夹时间重合,这就大大减少了停机时间。基于此,柔性组合夹具在元件系列的设计上发展出与其相适应和匹配的元件系列。
这些元件的最大特点是:与机床工作台的连接非常紧密和快捷,可以直接连接在机床的工作台或托板上,甚至托板系统中的“托板”直接按柔性组合夹具元件结构要素进行设计,使其直接成为机床的附件。一些新型多功能的定位组合件、夹紧合件以及定位夹紧组合件相继出现,虽然并未从根本上改变传统组合夹具的元件特点,但是取代了多件叠加的繁琐,一些带有坐标原点的孔类定位元件,使柔性组合夹具在多个工件的定位上能够精确载入机床的坐标系。柔性组合夹具元件的发展,为柔性组合夹具在柔性制造技术环境下的应用奠定了基础。
绅名科技-底盘系统关键零部件柔性装配线
工作中常常谈及装配线柔性问题,个人简单理解为柔性装配线也可称可编程序,快换产品装配线,是在非间歇传送装配的基础上,采用可编程序和转换程序,快速更换工装夹具来实现快速转换装配多项产品的装配线。
1、组成
柔性装配线通常由装配站、物料输送装置和控制系统等组成。
(1)装配站
柔性装配线中的装配站可以是可编程的装配机器人,不可编程的自动装配装置和人工装配工位。
(2)物料输送装置
柔性装配线输入的是组成产品或部件的各种零件,输出的是产品或部件。根据装配工艺流程,物料输送装置将不同的零件和已装配成的半成品送到相应的装配站。输送装置由传送器和换向机构、定位机构、传感机构、控制位系统等的有机组合组成。
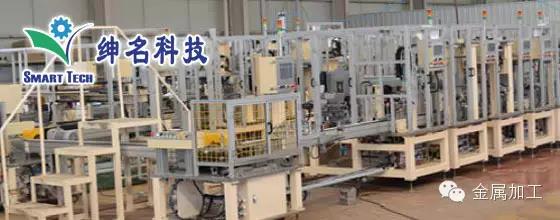
图1
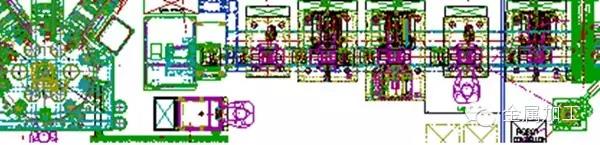
图2
2、机械运动和控制系统
图1是柔性装配线照片,图2是柔性装配线布局示意图。投料工作站中有料库和取料机器人。料库有各种盒子、漏斗、穿料棒等组成,待装配的零件存放在这些存料机构中,取料机器人有各种不同的夹爪,它可以自动地将零件从盒子中取出,并摆放在一个工装中,被装配机构自动检测装配。或者盛有零件的工装托盘由传送带自动地送往装配机器人或装配站完成装配。常用的主要部件有各种送料振动盘、震动导轨、气动元件、液压元件、伺服电机、油脂泵和阀、导轨和丝杠、电动力矩扳手等机械原件和力矩传感器、位移传感器、力传感器、光电传感器、接近传感器、视觉传感器、泄漏测试仪、人机界面(触摸屏)、无线射频识别、工控机、变频器、PLC及电源等的电气元件。
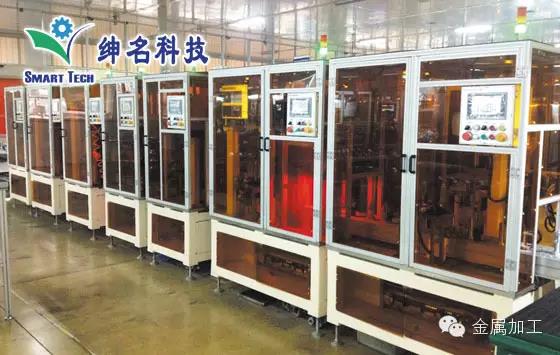
3、柔性的主要实现方式
(1)通过对同类不同产品部件的外形和材质综合分析,设计预制出单台工艺设备可在几分钟内快速跟换调试的工装和夹具来实现柔性装配。设计方面可应用为了快速调试使用通常设置定位销、硬限位、导向槽、快校工装付具。
(2)通过控制模块预留扩展空间和预先编程存储再系统中,可通过增加控制模块或转换开关或触摸屏选项按钮快速转换程序来实现柔性装配。
2柔性组合夹具的应用性
在柔性制造技术中,夹具是影响其柔性发挥的关键因素。在计算机集成制造系统(CIMS)试验以及许多单位的柔性制造系统的多年实践中,大家发现,在机床与加工零件对接的夹具环节上实现无人化或期望理想状态的柔性化,是相当困难的。无人化还须有相当程度的技术支持,或可在某一领域实现,但要扩展到能涵盖更多的领域,是极其困难的。理想状态柔性化实现的最便捷途径,就是改造传统的组合夹具,将组合夹具结构变化上具有的万能性优势,改造成柔性化的特点。
柔性组合夹具元件的发展,为柔性组合夹具在柔性制造技术中的应用,奠定了基础。柔性组合夹具在汽车的柔性制造中,已经发挥出显着的作用。柔性化组合夹具与元件系列及机床的关系更加紧密,元件系统有了压缩,柔性组合夹具技术在机床上的应用开始简单化,夹具的结构亦从复杂向简单演变。
在汽车柔性制造技术环境下,柔性组合夹具被大量应用,尤其在发动机、变速器及离合器等关键零件的制造中。如在离合器和变速器之类壳体、壳盖的夹具结构中,广泛采用桥梁式夹具结构,使得两面加工得以方便实现。由于这类零件多为铝合金材料,支持被加工零件的局部刚度,在更加直观的现场中,可以轻易实现。各种理想的典型柔性组合夹具结构,就是其技术应用的直接成果。加强这一方面的技术研究与发展,是提高柔性组合夹具柔性化的重要环节。
雄克公司-VERO-S
雄克公司VERO-S零点快换夹持系统能够有效辅助发动机加工线实现柔性生产,颠覆传统的装夹原理。以前每一次重新装夹工件,都可能导致精度的损失。但VERO-S的重复定位精度小于5微米,几乎可做到无任何精度损失,且可使工件坯料一次装夹(或于托板上)完成五面加工,以及多工位互换加工,其卓越的性能、简单的结构、工况的不敏感性,将使之扩展到整个机械制造行业,并带来整个制造工艺系统革新的应用。
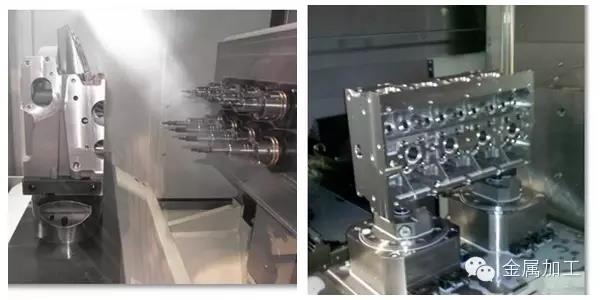
传统的发动机缸体和缸盖夹具为例,其特点主要为:
● 框架结构,刚性好,重量大
● 不易安装,定位精度较高,复杂程度高
● 专机专用,不能重复使用
● 自动化上下料困难
● 夹持点多,夹紧监控复杂
雄克VERO-S系统应用于发动机缸盖的快换装夹时,夹持模块的柔性设计:工件表面无传统夹持方式所带来的额外压力,如弹簧力、液压或气动压板等(依赖于有效的工作空间及拉紧力需求)。
夹持力的均匀分布在缸盖表面:取决于夹紧销的数量、螺栓大小(夹紧销、工件),夹紧销位置及保留的关系。
雄克VERO-S快换系统工艺结构
VERO-S零点快换夹持系统特点:
1.标准化接口。由两部分组成:快换模块与托盘。托盘是连接工件与快换模块接口的载体,通过夹紧定位销与快换模块连接,可兼容各类夹紧工装。
2.强大的夹紧力。单个快换模块的夹紧力高达40kN,增压型可达75kN。
3.可靠的重复定位精度。多个工序之间的重复定位精度确保在0.005mm范围之内。
4.高柔性。可实现不同产品间的快速切换,即使在大批量制造过程中(如发动机缸盖加工),实现柔性的共线生产。
下面是几个柔性组合夹具的具体应用实例。
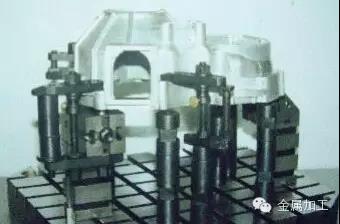
图1,汽车离合器壳体零件在立式加工中心上所采用的柔性组合夹具。此夹具只是定位与夹紧元件的组装,结构简单,敞开性好,完成夹具组装只需30min,在柔性化生产中,其快速性由此可见。
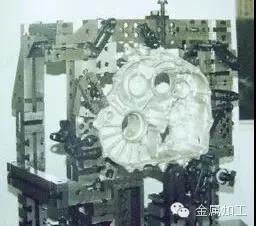
图2,汽车离合器上壳体零件在卧式加工中心上所采用的柔性组合夹具。可看出,夹具虽然是围绕零件的框架式结构,但考虑加工状态的切削力,框柱组成双体并作加固,各定位点和辅助支撑点分布得当,充分显示出柔性组合夹具在其结构演变上的柔性化。
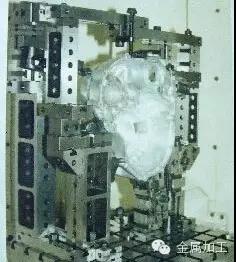
图3,汽车离合器上壳体零件在卧式加工中心上所采用的柔性组合夹具。由于零件的形状特点与定位要求,柔性组合夹具在其技术应用上,几乎可以胜任任何结构的设计,并能经受大切削力条件下的加工要求。
3 加强柔性组合夹具的技术管理性
柔性组合夹具管理,包括元件系列及人的组合装配,以及在这两个因素下衍生出来的比如元件配置规模和在生产准备中所处的管理位置、元件管理和技术管理等,这将决定柔性组合夹具发挥作用的程度,同时也涉及到柔性组合夹具的投入(包含日后的管理投入)与发挥作用的性价比。也可以说,其技术发挥与管理水平的程度决定其柔性化的程度。
柔性组合夹具元件、技术运用、技术管理是柔性组合夹具的三个方面。如果说元件是基础,技术运用是关键,那么技术管理就是前两者的保障,而且在前两者的作用中,本身就贯穿着管理的因素。如元件的型别、配套量,元件间的类别比例,现场流通量与库存量的比例,元件的更换频率和幅度,元件使用的各种必要制度等。在技术管理中,管理的重要性则显现的更为突出。
传统组合夹具的管理模式已经落伍,建立一个庞大“组装站”的管理方法,将会占用大量的资源和资金,在进行生产准备中,实现夹具的快速反应又存在着时间差,故必须予以改变。在现代生产模式下,采用更适合、更科学的管理模式,已经是一个迫在眉睫的问题。
编辑推荐
最新资讯
-
比亚迪叉车:用科技创新驱动绿色物流
2025-07-10 10:40
-
全球首个!比亚迪率先实现媲美L4级智
2025-07-10 09:31
-
精度±微米,节拍7秒——埃马克VST 5
2025-07-09 18:17
-
跨越速运凭什么“圈粉”万千客户?“
2025-07-01 14:42
-
数智破局启新篇・生态共生再启程 —
2025-06-27 20:13