基于deform仿真对深孔钻加工的优化改造
2018-03-28 14:16:30· 来源:《工具技术》 作者:赖智宇
孔加工是一种重要的加工方式,据统计,当前孔加工约占机加工总时间的36%。孔加工是一个隐蔽的过程,其切削工艺也很复杂,集金属挤压、金属切削以及金属磨光三种工艺于一体,在切削中会形成高推力、高扭矩、高温度。孔加工是最复杂和最有可能出问题的金属切削工艺之一,而深孔钻削是则是孔加工中最难的一种类型。
孔加工是一种重要的加工方式,据统计,当前孔加工约占机加工总时间的36%。孔加工是一个隐蔽的过程,其切削工艺也很复杂,集金属挤压、金属切削以及金属磨光三种工艺于一体,在切削中会形成高推力、高扭矩、高温度。孔加工是最复杂和最有可能出问题的金属切削工艺之一,而深孔钻削是则是孔加工中最难的一种类型。
1 工艺分析
柳州某汽车发动机制造部生产铸铁类缸体产量达80万台/年,孔加工占所有加工内容的近80%。该工厂深孔钻均采用高转速、高进给的高速切削工艺,单件成本较普通钻头高2-3倍。
调查发现该企业机加工车间缸体线二期M3/4 OP110工位加工B系类某机型产品时,515#孔过程多次出现T22077刀具崩刃事件,引起工件质量不合格,515#孔直径超上差。
查询PFMEA可知直径超上差潜在失效模式分别为:①影响下一工序:螺纹螺牙浅,油堵拧紧扭力不合格,最终试漏不合格,导致零件报废;②影响发动机装配线:油压开关装配扭力不合格,装配试漏不合格;③发动机漏油:影响发动机使用性能。
对515#分析可知,孔深与孔径之比为16,是典型的深孔加工。深孔钻作为机械加工中的难题,主要表现为:刀具悬伸长,加工容易产生震动,目前机械加工中多数钻头都是用硬质合金,该材料硬且脆,机床轻微的震动都会引起刀具断刀;深孔钻削属于半封闭加工,在钻孔孔过程中排屑困难,在加工中极易出现切屑阻塞造成刀具损坏;深孔加工散热困难。
515#孔加工为两刀加工,在同一工位先由T22075预钻,预钻孔深16mm,直径8.13mm。预钻后由T22077在预钻孔的基础上继续加工,孔深133mm,直径8.1mm,完成515#孔加工。
(1)预钻孔工艺
目前深孔钻加工通用工艺为预孔+深孔钻。对铸造毛坯面钻孔加工时,为保证钻尖定心良好,需要先铣出一个小平台,再进行预孔钻,预钻孔示意图见图1。预孔钻的主要目的是保证深孔钻较好的定心,保证钻孔的位置度。当深孔钻进入引导孔时,钻头的侧面会受到一定支撑,因此在深孔钻钻削过程中,径向方向受到约束,不易抖动,提高了钻削的稳定性。
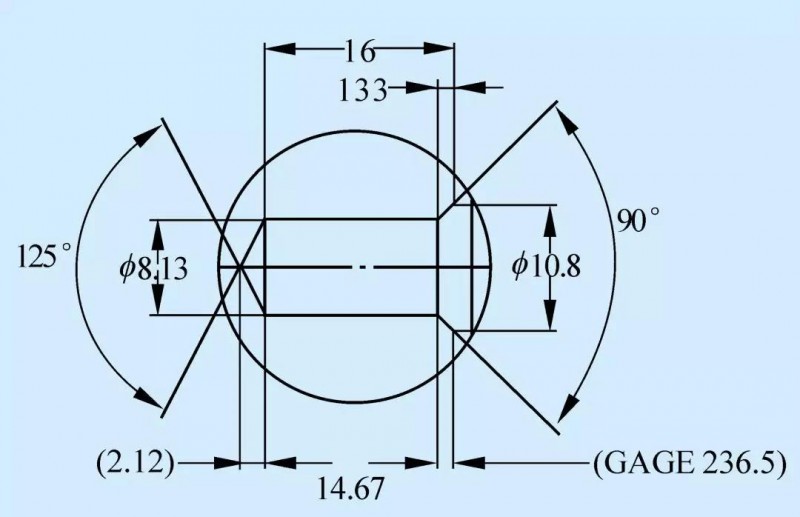
图1 预钻孔示意图
如图4所示,T22075预钻孔仅为深孔钻作支撑作用,深孔钻不参与引导孔的加工,因此,预钻刀具比深孔钻头直径大0.03mm(工艺孔直径8.1mm,预钻孔直径8.13mm);为保证深孔钻横刃先接触工件,而不是两侧的钻尖先接触,将预钻钻尖角度设计比深孔钻大5°(预钻钻尖125°,深孔钻钻尖120°)。
(2)深钻工艺
当预钻孔加工完成后,隔一把刀具进行深孔加工,深孔加工示意图见2。该类工艺设计可有效规避当预孔钻异常断刀时,直接深孔加工带来的后续刀具损伤。当前该发动机工厂在用T22077为TiALN涂层的硬质合金钻头,查询刀具推荐样本可知,该刀具加工铸铁件推荐值为0.12-0.15mm/z。现有参数为F=450mm/min,S=3000r/min,实际每齿进给0.075mm,满足样本推荐值。TiAlN涂层化学稳定性好,具有高热硬性、极佳抗氧化性、耐磨耗等特点,可满足铸铁件高速加工。
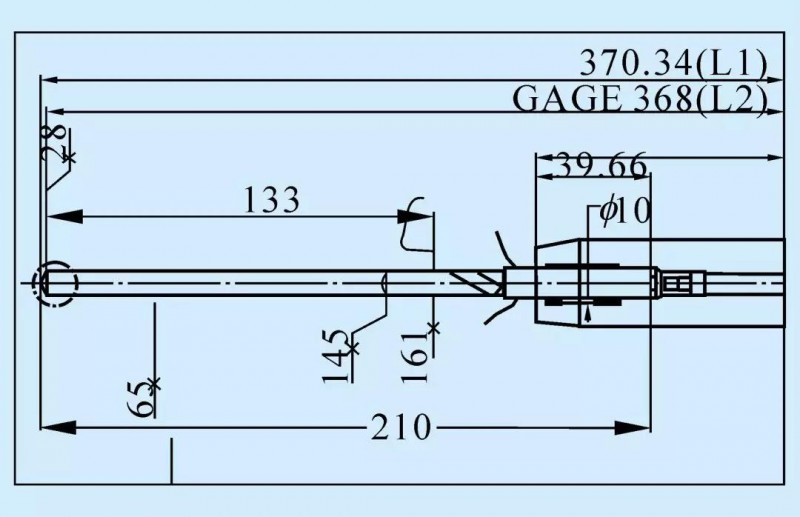
图2 深孔钻示意图
2 切削仿真
515#孔加工工艺特征为交汇孔加工,且非垂直相交,即加工时零件背面为斜面,破壁后钻尖完全出孔前,钻尖存在单边受力,加工示意图见图3。
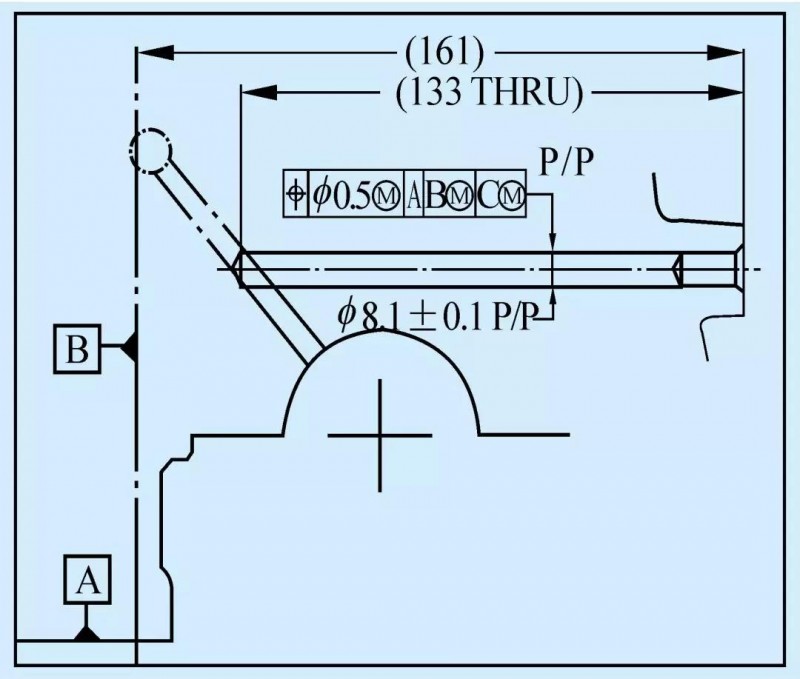
图3 515#孔加工示意图
为更确切地掌握加工过程中刀具的受力状态,对加工过程运用Deform软件进行模拟仿真,建立斜面零件模型,将材质设置为与生产现场铸铁属性接近的牌号,依据实际转速、进给(F=450 mm/min,S=3000r/min)进行切削仿真,切削仿真受力分析见图4。由图可知,在高速条件下,钻尖破壁瞬间,刃口受力突变,该突变极易导致钻尖崩刃,崩刃后后续工件加工时刀尖豁口处受力异常导致加工震动引起孔径变大。仿真结果表明,消除破壁瞬间的受力突变将会消除崩刃刀具异常震动导致的孔径超差。
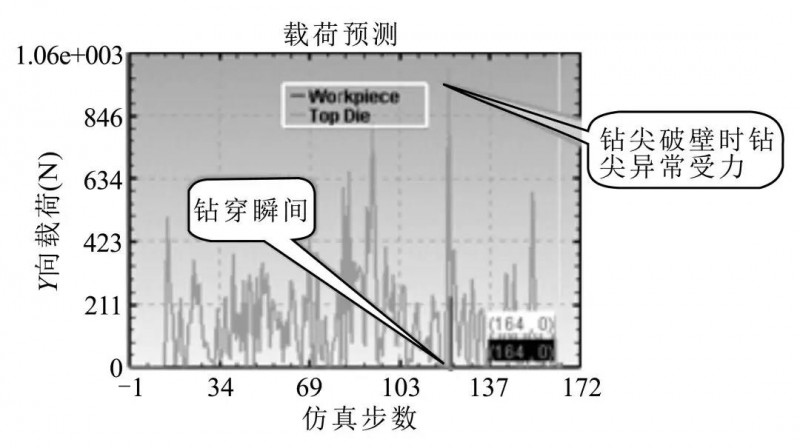
图4 deform切削仿真受力分析
调取排屑性能更好的钻尖120°麻花钻,发现优化钻头前、后角均未能有效消除破壁瞬间受力突变问题。圆头钻在穿破斜面是能有效消除单边受力及应力突变问题,为验证其有效性,在三维数模中将钻头钻尖形式优化为圆形,保持麻花钻及原有刀具前后角,同等工况下切削,输出受力情况见图5。
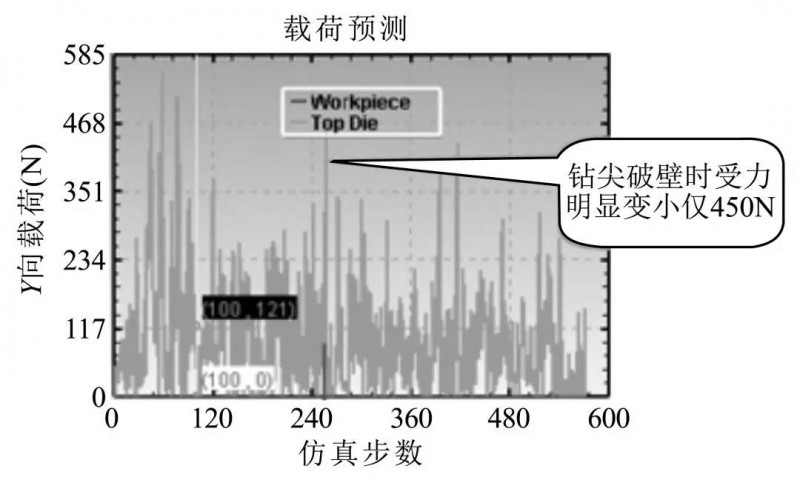
图5圆形钻头切削仿真受力分析
3 优化效果
结合理论分析,2016年2月申请TCR对该刀具进行改造验证,将原有120°钻尖优化为圆形钻尖,如图6所示。验证期间刀具均未发生崩刃现象,将耐用度后期刀具放显微镜下观察,刃口磨损较小,连续跟踪6个月,统计未发现批量515#孔直径超差问题。如图10所示,通过优化钻尖形式有效抑制了崩刃问题的发生,达到了降低制造成本减轻质量风险的预期目的。
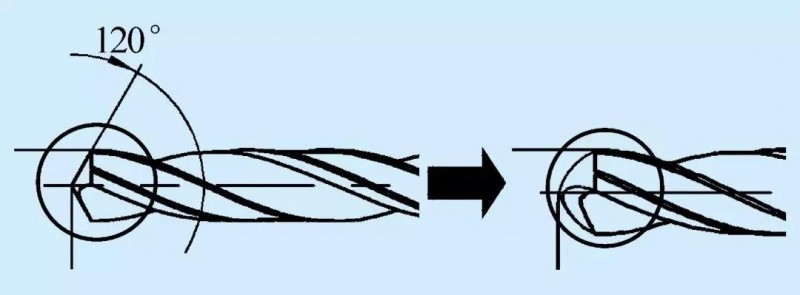
(a) 改造前钻尖形式 (b) 改造后钻尖形式
图6改造前后钻头钻尖结构对比
小结
通过理论分析和模拟仿真明确了工艺优化改进方向,以刀具失效形式为切入点,实现了在不改变机床夹具和工件结构的情况下有效降低刀具崩刃问题的发生,减少工件报废。该工艺优化方案在柳州某汽车发动机生产现场实施后,运行状况良好,取得了可观的经济效益。
1 工艺分析
柳州某汽车发动机制造部生产铸铁类缸体产量达80万台/年,孔加工占所有加工内容的近80%。该工厂深孔钻均采用高转速、高进给的高速切削工艺,单件成本较普通钻头高2-3倍。
调查发现该企业机加工车间缸体线二期M3/4 OP110工位加工B系类某机型产品时,515#孔过程多次出现T22077刀具崩刃事件,引起工件质量不合格,515#孔直径超上差。
查询PFMEA可知直径超上差潜在失效模式分别为:①影响下一工序:螺纹螺牙浅,油堵拧紧扭力不合格,最终试漏不合格,导致零件报废;②影响发动机装配线:油压开关装配扭力不合格,装配试漏不合格;③发动机漏油:影响发动机使用性能。
对515#分析可知,孔深与孔径之比为16,是典型的深孔加工。深孔钻作为机械加工中的难题,主要表现为:刀具悬伸长,加工容易产生震动,目前机械加工中多数钻头都是用硬质合金,该材料硬且脆,机床轻微的震动都会引起刀具断刀;深孔钻削属于半封闭加工,在钻孔孔过程中排屑困难,在加工中极易出现切屑阻塞造成刀具损坏;深孔加工散热困难。
515#孔加工为两刀加工,在同一工位先由T22075预钻,预钻孔深16mm,直径8.13mm。预钻后由T22077在预钻孔的基础上继续加工,孔深133mm,直径8.1mm,完成515#孔加工。
(1)预钻孔工艺
目前深孔钻加工通用工艺为预孔+深孔钻。对铸造毛坯面钻孔加工时,为保证钻尖定心良好,需要先铣出一个小平台,再进行预孔钻,预钻孔示意图见图1。预孔钻的主要目的是保证深孔钻较好的定心,保证钻孔的位置度。当深孔钻进入引导孔时,钻头的侧面会受到一定支撑,因此在深孔钻钻削过程中,径向方向受到约束,不易抖动,提高了钻削的稳定性。
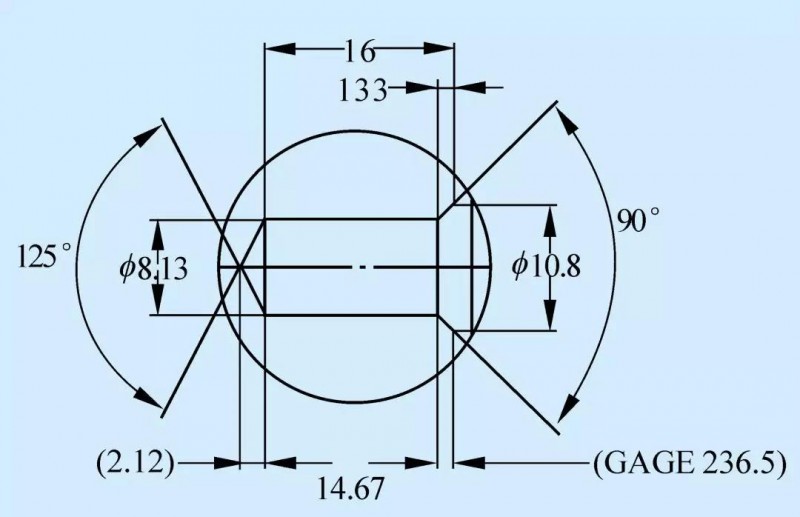
图1 预钻孔示意图
如图4所示,T22075预钻孔仅为深孔钻作支撑作用,深孔钻不参与引导孔的加工,因此,预钻刀具比深孔钻头直径大0.03mm(工艺孔直径8.1mm,预钻孔直径8.13mm);为保证深孔钻横刃先接触工件,而不是两侧的钻尖先接触,将预钻钻尖角度设计比深孔钻大5°(预钻钻尖125°,深孔钻钻尖120°)。
(2)深钻工艺
当预钻孔加工完成后,隔一把刀具进行深孔加工,深孔加工示意图见2。该类工艺设计可有效规避当预孔钻异常断刀时,直接深孔加工带来的后续刀具损伤。当前该发动机工厂在用T22077为TiALN涂层的硬质合金钻头,查询刀具推荐样本可知,该刀具加工铸铁件推荐值为0.12-0.15mm/z。现有参数为F=450mm/min,S=3000r/min,实际每齿进给0.075mm,满足样本推荐值。TiAlN涂层化学稳定性好,具有高热硬性、极佳抗氧化性、耐磨耗等特点,可满足铸铁件高速加工。
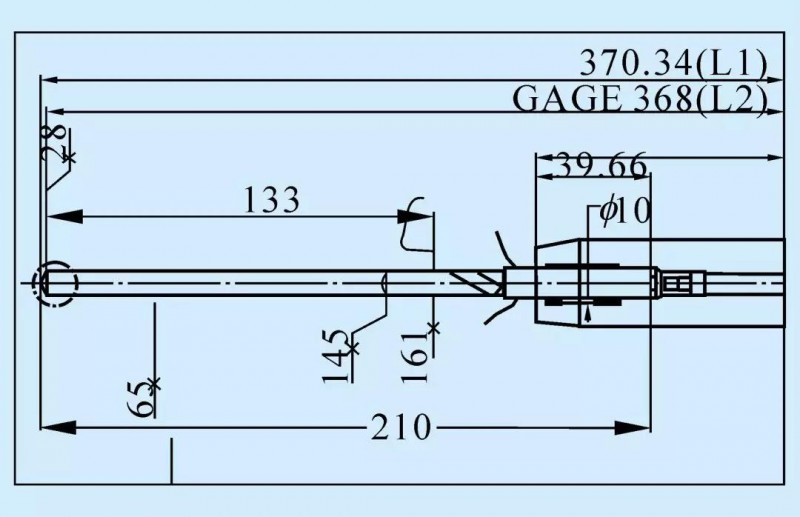
图2 深孔钻示意图
2 切削仿真
515#孔加工工艺特征为交汇孔加工,且非垂直相交,即加工时零件背面为斜面,破壁后钻尖完全出孔前,钻尖存在单边受力,加工示意图见图3。
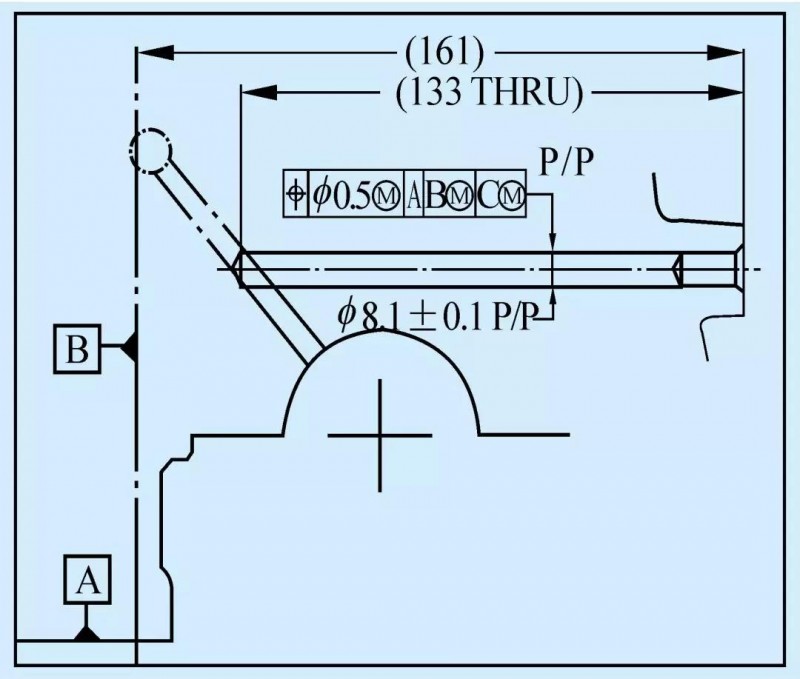
图3 515#孔加工示意图
为更确切地掌握加工过程中刀具的受力状态,对加工过程运用Deform软件进行模拟仿真,建立斜面零件模型,将材质设置为与生产现场铸铁属性接近的牌号,依据实际转速、进给(F=450 mm/min,S=3000r/min)进行切削仿真,切削仿真受力分析见图4。由图可知,在高速条件下,钻尖破壁瞬间,刃口受力突变,该突变极易导致钻尖崩刃,崩刃后后续工件加工时刀尖豁口处受力异常导致加工震动引起孔径变大。仿真结果表明,消除破壁瞬间的受力突变将会消除崩刃刀具异常震动导致的孔径超差。
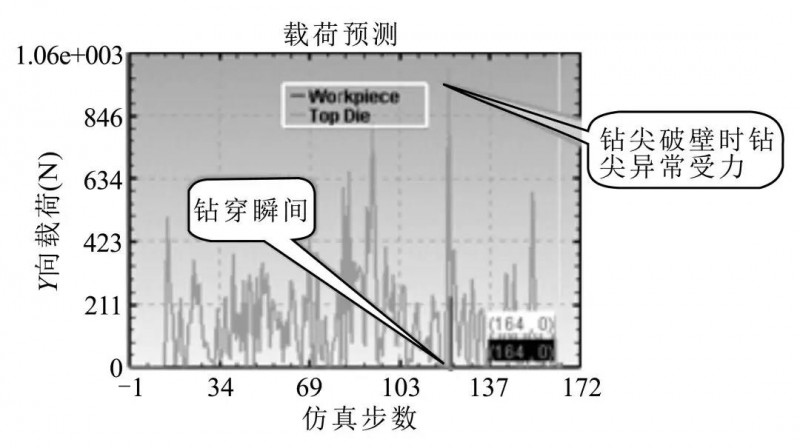
图4 deform切削仿真受力分析
调取排屑性能更好的钻尖120°麻花钻,发现优化钻头前、后角均未能有效消除破壁瞬间受力突变问题。圆头钻在穿破斜面是能有效消除单边受力及应力突变问题,为验证其有效性,在三维数模中将钻头钻尖形式优化为圆形,保持麻花钻及原有刀具前后角,同等工况下切削,输出受力情况见图5。
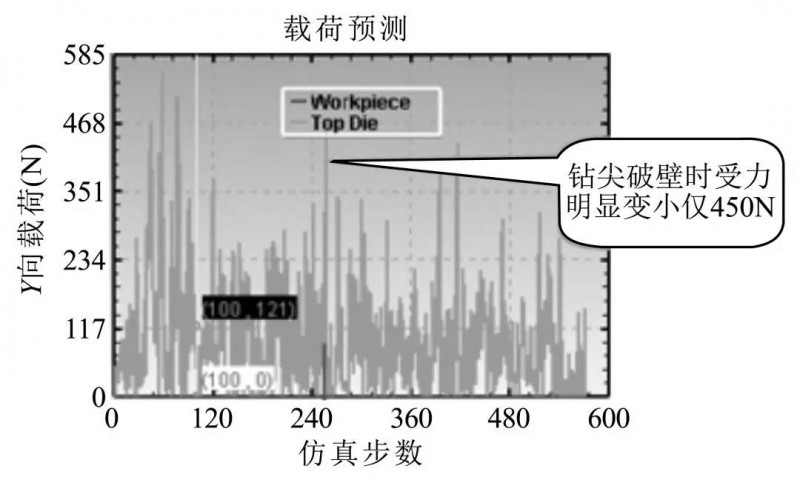
图5圆形钻头切削仿真受力分析
3 优化效果
结合理论分析,2016年2月申请TCR对该刀具进行改造验证,将原有120°钻尖优化为圆形钻尖,如图6所示。验证期间刀具均未发生崩刃现象,将耐用度后期刀具放显微镜下观察,刃口磨损较小,连续跟踪6个月,统计未发现批量515#孔直径超差问题。如图10所示,通过优化钻尖形式有效抑制了崩刃问题的发生,达到了降低制造成本减轻质量风险的预期目的。
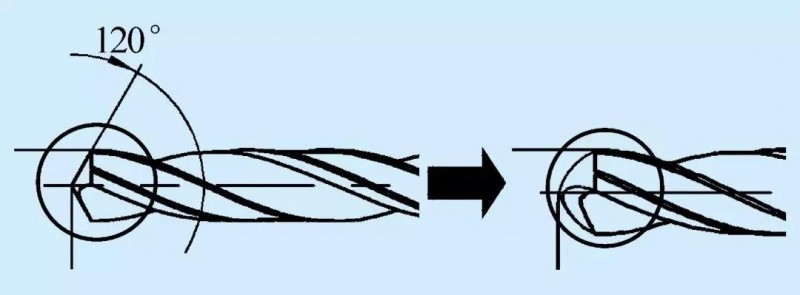
(a) 改造前钻尖形式 (b) 改造后钻尖形式
图6改造前后钻头钻尖结构对比
小结
通过理论分析和模拟仿真明确了工艺优化改进方向,以刀具失效形式为切入点,实现了在不改变机床夹具和工件结构的情况下有效降低刀具崩刃问题的发生,减少工件报废。该工艺优化方案在柳州某汽车发动机生产现场实施后,运行状况良好,取得了可观的经济效益。
- 下一篇:汽车涂装的节能减排技术
- 上一篇:2018捷克国际机械工业博览会新闻发布会在京举行
举报 0
收藏 0
分享 90
-
涡轮增压器螺杆孔加工
2018-05-26 涡轮增压器螺杆孔加工 -
简单分析深孔加工切削液温度在线监测及控制
2018-01-31 孔加工 -
简单分析曲轴法兰端中心孔加工刀具优化
-
孔加工解决方案 销量明星DRA家族再添新成员
编辑推荐
最新资讯
-
辐射亚太,链接全球——采埃孚再制造
2025-07-30 11:46
-
思看科技发布子品牌SCANOLOGY,全球
2025-07-30 11:06
-
风雨不动安如山——比亚迪叉车构筑“
2025-07-30 08:48
-
NEAS CHINA 新能源汽车技术与生态链
2025-07-29 09:52
-
三维扫描革新碾磨机辊套检测,效率与
2025-07-25 10:46