简单分析曲轴法兰端中心孔加工刀具优化
2018-01-03 13:46:15· 来源:工具技术 作者:刘将先
曲轴中心孔是工艺设计的工艺基准,也是后序加工、检测曲轴的定位基准,中心孔的好坏直接影响曲轴的产品质量,所以对中心孔的精度要求较高。EB2DT(S)曲轴是1.2T涡轮增压发动机内的主要零件之一,曲轴材料为38MnSiV5,硬度255-302HB,曲轴法兰端中心孔振纹问题严重影响生产效率。
1 曲轴中心孔的工艺要求及问题
曲轴中心孔是工艺设计的工艺基准,也是后序加工、检测曲轴的定位基准,中心孔的好坏直接影响曲轴的产品质量,所以对中心孔的精度要求较高。EB2DT(S)曲轴是1.2T涡轮增压发动机内的主要零件之一,曲轴材料为38MnSiV5,硬度255-302HB,曲轴法兰端中心孔振纹问题严重影响生产效率。
原加工工艺为麻花钻与锥铰刀组合加工,简单来说,就是先用麻花钻钻Φ15.4mm直孔,再用锥铰刀加工60°与120°锥孔,中心孔60°锥是后序加工基准与定位基准、检测基准。加工设备是德国申克加工中心,加工时曲轴不转,刀具旋转。通过这种方式加工出来的曲轴,中心孔出现振纹(见图1),不能满足0.02mm的圆度要求。
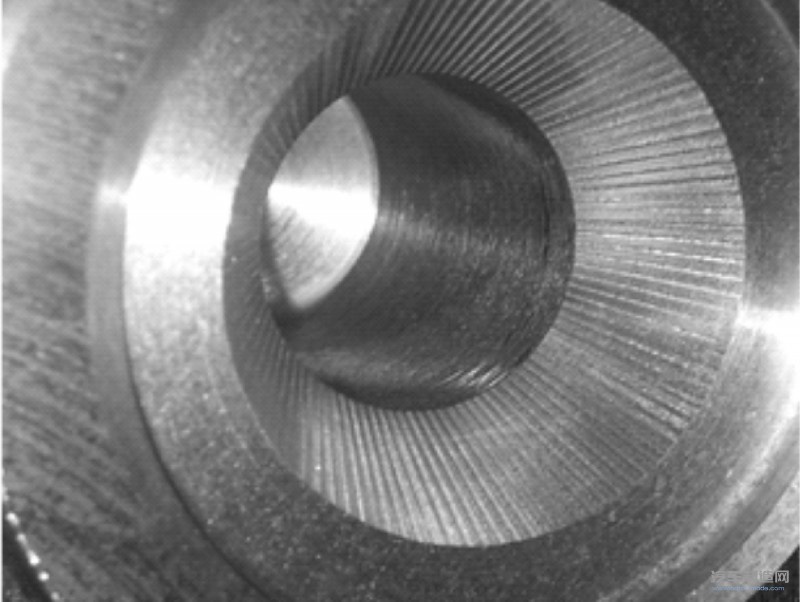
图1 中心孔振纹
2 工艺优化
借助对加工工艺的分析,发现工艺及刀具选型不合理:①加工底孔采用麻花钻不当,给后序铰孔带来较大余量,尤其是60°锥面余量太大;②铰中心孔时,切削余量大,定心不好,导致切削时振动而产生振纹;③铰60°锥面切削参数:转速950t/min,每转进给0.4mm/t;④铰120°锥面切削参数:转速320t/min,每转进给0.3mm/t。
对刀具及工艺进行优化改进:①把加工底孔的Φ15.4mm的麻花钻改为Φ15.4mm阶梯钻,刀柄从Φ16mm改为Φ25mm,在加工底孔时,增加了刚性,同时把60°锥面加工到只有0.5mm的余量。②将铰中心孔的锥铰刀换成具有自定心作用的中心孔铰刀,一方面因锥面铰削余量少,另一方面因在铰削锥面时前面在铰削直孔,可以起到有效防振的作用,直孔从Φ15.4mm铰至Φ15.7mm,为该孔后序加工到Φ16mm减少了加工余量。③在优化刀具的同时,对加工中心孔的工艺进行优化(见图2)。
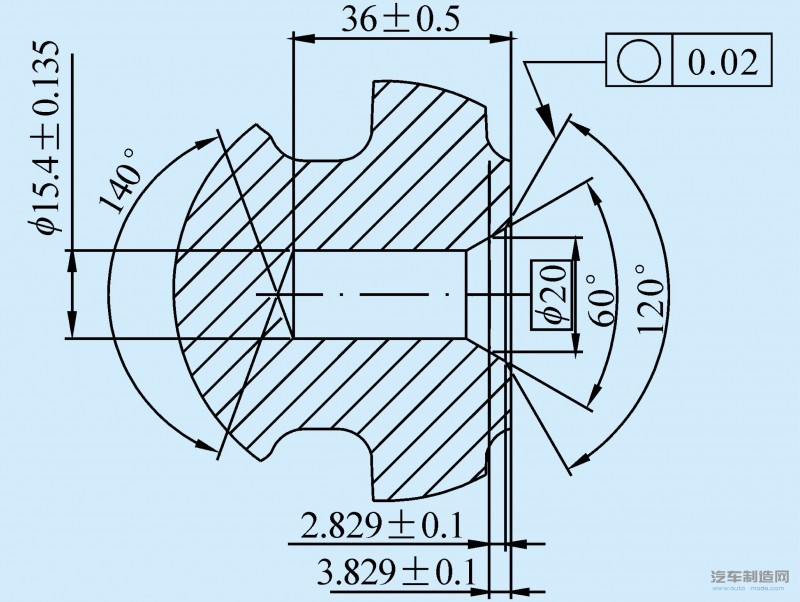
(a)优化前
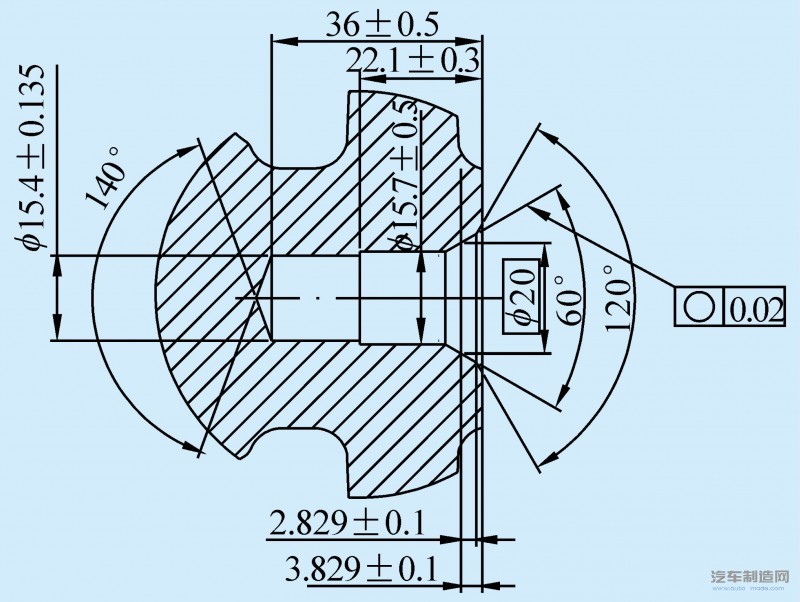
(b)优化后
图2 优化前后中心孔加工示意图
3 效果验证
因此,通过上述工艺改进,消除了振纹,中心孔圆度合格,均在0.02mm以内,解决了曲轴的质量问题。在刀具优化过程中,改变了刀具结构,麻花钻变粗了。同时,通过刀具的国产化,降低了刀具价格,提高了刀具寿命,降低了产品成本。
曲轴中心孔是工艺设计的工艺基准,也是后序加工、检测曲轴的定位基准,中心孔的好坏直接影响曲轴的产品质量,所以对中心孔的精度要求较高。EB2DT(S)曲轴是1.2T涡轮增压发动机内的主要零件之一,曲轴材料为38MnSiV5,硬度255-302HB,曲轴法兰端中心孔振纹问题严重影响生产效率。
原加工工艺为麻花钻与锥铰刀组合加工,简单来说,就是先用麻花钻钻Φ15.4mm直孔,再用锥铰刀加工60°与120°锥孔,中心孔60°锥是后序加工基准与定位基准、检测基准。加工设备是德国申克加工中心,加工时曲轴不转,刀具旋转。通过这种方式加工出来的曲轴,中心孔出现振纹(见图1),不能满足0.02mm的圆度要求。
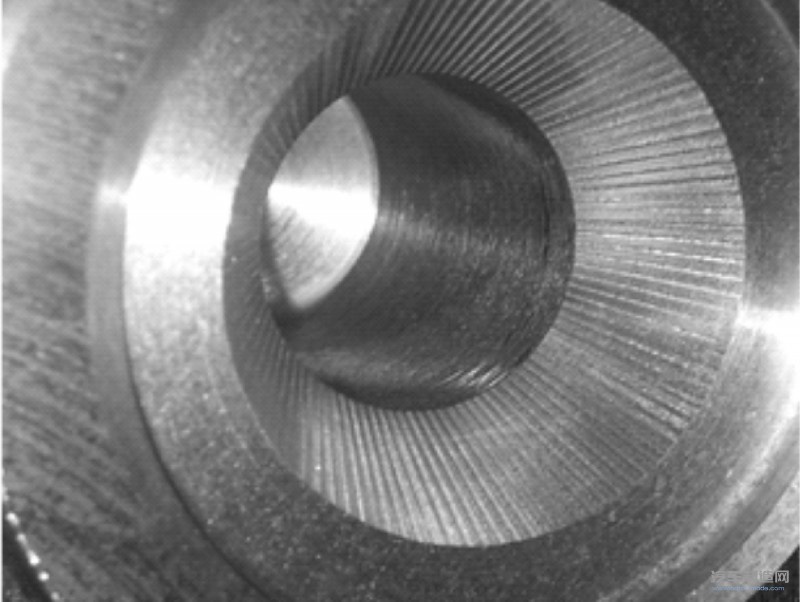
图1 中心孔振纹
2 工艺优化
借助对加工工艺的分析,发现工艺及刀具选型不合理:①加工底孔采用麻花钻不当,给后序铰孔带来较大余量,尤其是60°锥面余量太大;②铰中心孔时,切削余量大,定心不好,导致切削时振动而产生振纹;③铰60°锥面切削参数:转速950t/min,每转进给0.4mm/t;④铰120°锥面切削参数:转速320t/min,每转进给0.3mm/t。
对刀具及工艺进行优化改进:①把加工底孔的Φ15.4mm的麻花钻改为Φ15.4mm阶梯钻,刀柄从Φ16mm改为Φ25mm,在加工底孔时,增加了刚性,同时把60°锥面加工到只有0.5mm的余量。②将铰中心孔的锥铰刀换成具有自定心作用的中心孔铰刀,一方面因锥面铰削余量少,另一方面因在铰削锥面时前面在铰削直孔,可以起到有效防振的作用,直孔从Φ15.4mm铰至Φ15.7mm,为该孔后序加工到Φ16mm减少了加工余量。③在优化刀具的同时,对加工中心孔的工艺进行优化(见图2)。
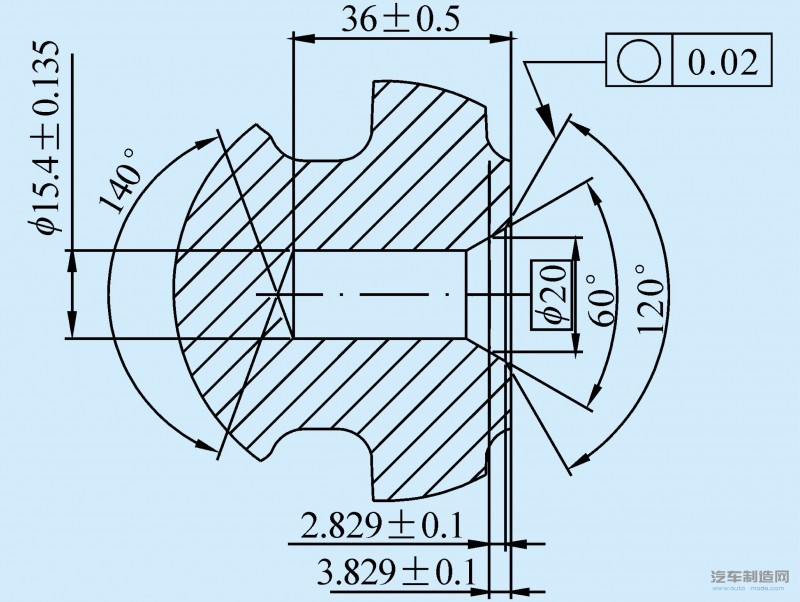
(a)优化前
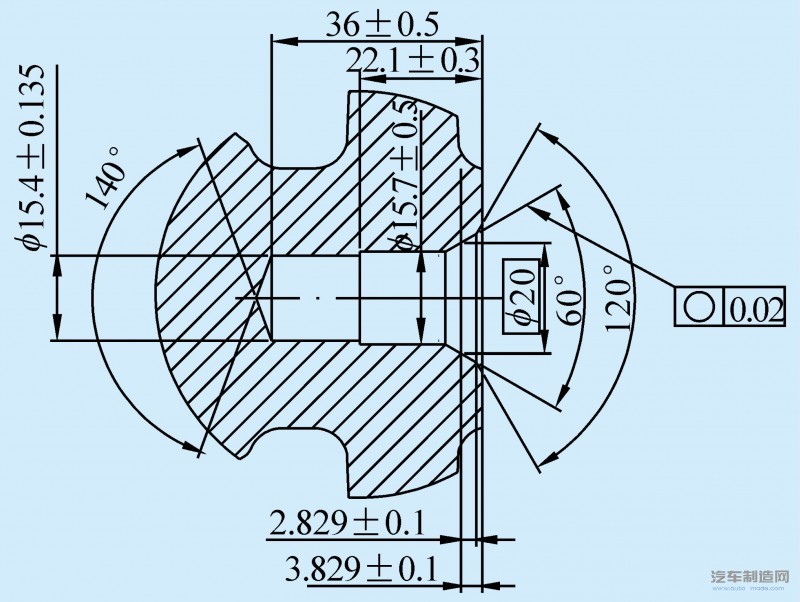
(b)优化后
图2 优化前后中心孔加工示意图
3 效果验证
因此,通过上述工艺改进,消除了振纹,中心孔圆度合格,均在0.02mm以内,解决了曲轴的质量问题。在刀具优化过程中,改变了刀具结构,麻花钻变粗了。同时,通过刀具的国产化,降低了刀具价格,提高了刀具寿命,降低了产品成本。
编辑推荐
最新资讯
-
比亚迪叉车:用科技创新驱动绿色物流
2025-07-10 10:40
-
全球首个!比亚迪率先实现媲美L4级智
2025-07-10 09:31
-
精度±微米,节拍7秒——埃马克VST 5
2025-07-09 18:17
-
跨越速运凭什么“圈粉”万千客户?“
2025-07-01 14:42
-
数智破局启新篇・生态共生再启程 —
2025-06-27 20:13