简单分析深孔加工切削液温度在线监测及控制
2018-01-31 16:30:17· 来源:工具技术 作者:刘英魁
本文基于PLC设计的深孔钻头降温装置,设有手动和自动两种工作模式,能够根据切削液的温度信号自动控制切削液流量,实现了深孔钻系统切削液温度在线监测的智能化控制,并且软件操作方便且容易实现,硬件也容易连接,同时对工作环境要求较低,工作稳定可靠,占地面积小,适用于车间现场使用。
深孔通常是指长径比大于5的孔。因为在深孔加工过程中切削区处于半封闭环境下,切削区会产生大量切削热且很难散失,但是操作人员不能准确、及时的获知深孔加工过程的实时状态,所以深孔加工的在线监控研究将具有重要意义。如果不能将切削热及时排出,深孔加工切削区域的温度将会极速上升。随着温度升高,钻头和工件会发生热变形,导致刀具走偏;钻头的性能下降,切削能力也随之急剧降低,钻头使用寿命大幅降低。在深孔加工过程中,通常采用切削液将切削热带出的方法。在深孔加工中,切削液担任着润滑、冷却和排屑等重要功能,深孔加工过程是否正常很大程度受切削液状态的影响。工程实践中,不同的工件和孔径采用的切削速度会有所差异。本文在尽量不改变转速和钻头进给量,不损失加工效率的基础上,采用控制切削液流量的方法达到控制切削区域温度的效果。本文设计了一套自动降低钻头温度的装置,运用PT100温度模块实现数据的实时采集,并依据温度信号的大小,经过PLC自动调整控制切削液流量,完成深孔钻削系统的温度自动控制,实现了手动和自动模式的切换。此装置具备操作简单、稳定性高和适用范围广等特点。
1 深孔加工系统监测方案
深孔钻削系统的在线监测方案建立在不同工况信号基础上,主要有:钻杆扭矩信号、钻杆振动信号、切削液油温信号等。深孔加工过程中如果出现状况,则与之对应的信号特征参数就会发生变化。本文主要以切削液温度为监测信号,最终达到控制切削液流量的目标。
在钻头、工件和切屑中聚集的大量热能,是在深孔加工切削过程中产生的。切削必将导致温度的急剧升高进而加剧刀具的损坏并影响钻头的切削性能,这样会使被加工工件表面粗糙度升高,质量大幅降低,同时也将大大降低刀具的使用寿命,造成经济损失,对生产产生严重影响。因为深孔加工有别于普通的机械加工,前者处于半封闭状态下,因此切削产生的热量更容易集聚,难以散发,必须由切削液将大量的切削热带出以降低切削区的温度。若在切削过程中钻头出现较严重的损毁或则磨损,则刀具、工件和切屑之间的摩擦将会大大增大,切削区温度急剧上升,切削液的温度也将随之升高。
因此我们会发现,被加工工件的质量、刀具磨损以及深孔切削效率都与切削液温度之间有着不可分割的重要联系。所以,对切削液温度的实时在线监控研究将有助于操作人员准确的了解深孔钻削环境并及时做出调整。进而加速深孔加工自动化技术的全方面发展。
2 刀具温度的自动检测与控制方案
(1)深孔钻的加工原理
图1为BTA深孔钻在普通车床上的工作情形。包括主轴箱、中心架、授油器、钻杆、进给箱、过滤装置、液压泵、油箱等。首先由车床上的中心架夹紧被加工工件,钻孔加工时,工件由主轴的夹头夹紧并在主轴带动下旋转,钻杆则由进给箱带动作进给运动。机床工作台上安装了授油器,并通过O型密封圈与工件左端面密封连接。加压过的切削液经液压泵由油箱输送到授油器,然后从钻杆外径与孔壁间的缝隙流入切削区,对切削区进行润滑、冷却,同时将带有切屑的切削液反向推入钻杆内腔并排出到过滤装置,过滤后的切削液流回油箱,如此不断循环。切削液采用的乳化液浓度为5%;切削用量可选用转速n=500-800r/min、进给量f =0.04-0.08mm/r。机床导轨上安装的活动中心支承可以支承钻杆的任意位置,这样可以尽量减轻因钻杆过长而导致的钻杆变形,从而提高钻杆的稳定性。
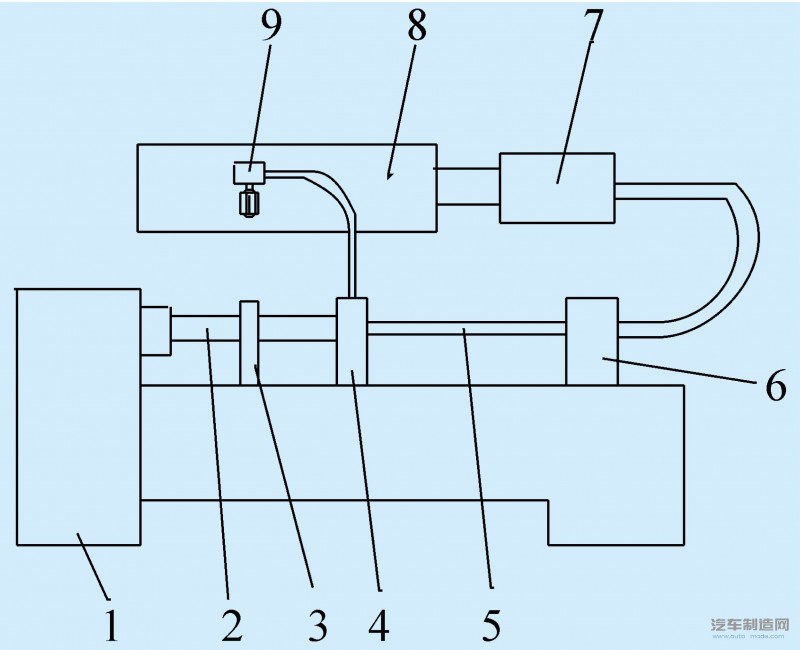
1.主轴箱 2.工件 3.中心架 4.授油器 5.钻杆 6.进给箱7.过滤器 8.油箱 9.液压泵
图1 BTA深孔加工原理
(2)温度传感器的测量位置
深孔钻床切削液温度变化范围不大。PT100温度传感器的温度采集范围可以在-200~+200℃。本文采用PT100采集切削液温度。根据试验将PT100放置于钻杆的排屑口处,接触到钻屑和切削液,温度的采集效果准确度高,但是考虑到此处切削液内携带大量的切屑,对PT100容易造成损坏。因此,本文将PT100放置在过滤装置的出口处,即图1中过滤器和油箱之间。在此处采集温度可能会有部分误差,但影响不大。
(3)控制系统
如图2所示,控制系统采用PLC控制,整个控制系统包括:PT100温度传感器、PLC、操作面板、变频器。开始工作时,切削液流经切削区域进行冷却,并携带切屑排出,经过滤装置后,由PT100温度传感器测得切削液温度。PT100温度传感器将测得数据传到PLC的热电阻模块。PLC比较分析后用过变频器控制液压泵转速,从而控制切削液的流量,达到智能冷却的目的。同时,PLC将数据发送到操作面板,实时显示控制系统的工作状态。
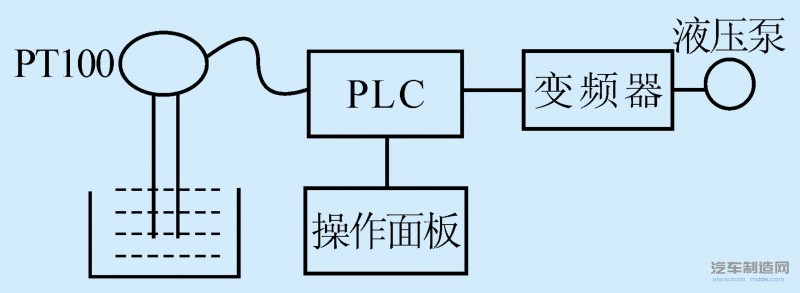
图2 温度测量与控制示意图
控制程序设置为手动控制和自动控制。当手动控制时,在操作面板上设置为“手动”,在此之前应先开启系统,检查各项指标是否正常。并输入要求的温度值,PLC比较该温度值与此时采集到的切削液温度,调节液压泵转速,直到采集到的温度达到该数值。一般直接钻削浅孔时可用手动模式,同样深孔钻床在检修或变频器失灵时也可直接使用手动模式。手动启动时由对应的启动按钮完成并点亮指示灯,停止时由对应的停止按钮完成并熄灭指示灯。
当自动控制时,在操作面板上设置为“自动”,此时,系统在PLC的控制下自动工作。系统将根据事先设置好的“温度—转速”曲线自动调节液压泵转速。保护钻头不会温度过热而损坏,工件发生热变形而工件失效。“温度—转速”曲线可以在操作面板上进行设置。
3 试验分析
深孔加工过程中,其切削区的温度不断升高,随着温度升高,钻头发生热变形,钻头耐磨性能急速下降,切削能力严重减弱。图3通过高倍显微镜对深孔加工过的切削刃进行观察,可见,中间齿切削刃中部明显发黑,说明此处磨损较严重,所以试验以切削刃的磨损程度为参考,以此来验证温度控制装置是否有效。
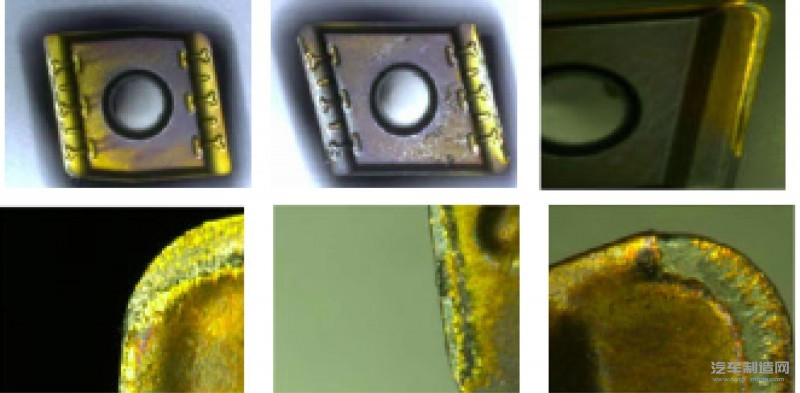
图3 显微系统下外齿、中间齿、中心齿的磨损情况
进行两次有无温度控制装置的深孔加工对比试验,检验两种情况下刀片磨损程度。试验刀片材料为YG8,加工材料分别为45钢和钛合金(TC4),切削用量:转速n=600r/min、进给量f =0.05mm/r。试验数据见表1。
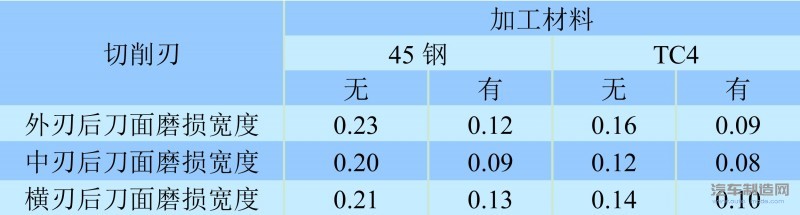
表1 刀具磨损值(mm)
图4和图5分别为使用和未使用温度控制系统加工45钢的刀具磨损情况。从表1、图4和图5可以得出:钻削45钢及钛合金时,没有使用温度控制装置的刀具磨损较大,尤其是加工45钢时的刀具磨损较为严重,而在加工钛合金时两种情况下磨损差别不是特别大,这主要是因为钛合金的主要切削力小于45钢等因素造成。通过试验可以看出,使用本文设计的温度控制装置能够有效降低切削区的温度,进而减轻刀具的磨损程度。
(a)外刃后刀面磨损(b)中刃后刀面磨损(c)横刃后刀面磨损
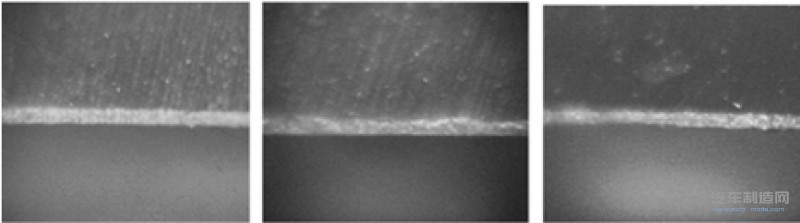
图4 使用温度控制系统加工45钢的刀具磨损情况
(a)外刃后刀面磨损 (b)中刃后刀面磨损 (c)横刃后刀面磨损
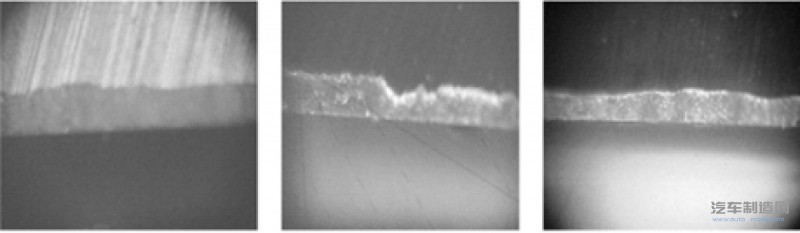
图5 未使用温度控制系统加工45钢的刀具磨损情况
总结:
本文基于PLC设计的深孔钻头降温装置,设有手动和自动两种工作模式,能够根据切削液的温度信号自动控制切削液流量,实现了深孔钻系统切削液温度在线监测的智能化控制,并且软件操作方便且容易实现,硬件也容易连接,同时对工作环境要求较低,工作稳定可靠,占地面积小,适用于车间现场使用。
1 深孔加工系统监测方案
深孔钻削系统的在线监测方案建立在不同工况信号基础上,主要有:钻杆扭矩信号、钻杆振动信号、切削液油温信号等。深孔加工过程中如果出现状况,则与之对应的信号特征参数就会发生变化。本文主要以切削液温度为监测信号,最终达到控制切削液流量的目标。
在钻头、工件和切屑中聚集的大量热能,是在深孔加工切削过程中产生的。切削必将导致温度的急剧升高进而加剧刀具的损坏并影响钻头的切削性能,这样会使被加工工件表面粗糙度升高,质量大幅降低,同时也将大大降低刀具的使用寿命,造成经济损失,对生产产生严重影响。因为深孔加工有别于普通的机械加工,前者处于半封闭状态下,因此切削产生的热量更容易集聚,难以散发,必须由切削液将大量的切削热带出以降低切削区的温度。若在切削过程中钻头出现较严重的损毁或则磨损,则刀具、工件和切屑之间的摩擦将会大大增大,切削区温度急剧上升,切削液的温度也将随之升高。
因此我们会发现,被加工工件的质量、刀具磨损以及深孔切削效率都与切削液温度之间有着不可分割的重要联系。所以,对切削液温度的实时在线监控研究将有助于操作人员准确的了解深孔钻削环境并及时做出调整。进而加速深孔加工自动化技术的全方面发展。
2 刀具温度的自动检测与控制方案
(1)深孔钻的加工原理
图1为BTA深孔钻在普通车床上的工作情形。包括主轴箱、中心架、授油器、钻杆、进给箱、过滤装置、液压泵、油箱等。首先由车床上的中心架夹紧被加工工件,钻孔加工时,工件由主轴的夹头夹紧并在主轴带动下旋转,钻杆则由进给箱带动作进给运动。机床工作台上安装了授油器,并通过O型密封圈与工件左端面密封连接。加压过的切削液经液压泵由油箱输送到授油器,然后从钻杆外径与孔壁间的缝隙流入切削区,对切削区进行润滑、冷却,同时将带有切屑的切削液反向推入钻杆内腔并排出到过滤装置,过滤后的切削液流回油箱,如此不断循环。切削液采用的乳化液浓度为5%;切削用量可选用转速n=500-800r/min、进给量f =0.04-0.08mm/r。机床导轨上安装的活动中心支承可以支承钻杆的任意位置,这样可以尽量减轻因钻杆过长而导致的钻杆变形,从而提高钻杆的稳定性。
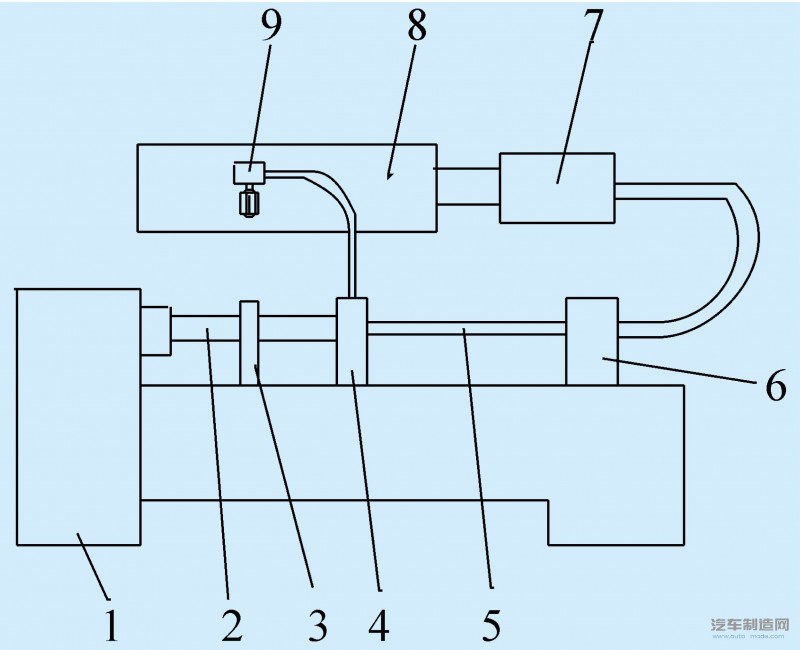
1.主轴箱 2.工件 3.中心架 4.授油器 5.钻杆 6.进给箱7.过滤器 8.油箱 9.液压泵
图1 BTA深孔加工原理
(2)温度传感器的测量位置
深孔钻床切削液温度变化范围不大。PT100温度传感器的温度采集范围可以在-200~+200℃。本文采用PT100采集切削液温度。根据试验将PT100放置于钻杆的排屑口处,接触到钻屑和切削液,温度的采集效果准确度高,但是考虑到此处切削液内携带大量的切屑,对PT100容易造成损坏。因此,本文将PT100放置在过滤装置的出口处,即图1中过滤器和油箱之间。在此处采集温度可能会有部分误差,但影响不大。
(3)控制系统
如图2所示,控制系统采用PLC控制,整个控制系统包括:PT100温度传感器、PLC、操作面板、变频器。开始工作时,切削液流经切削区域进行冷却,并携带切屑排出,经过滤装置后,由PT100温度传感器测得切削液温度。PT100温度传感器将测得数据传到PLC的热电阻模块。PLC比较分析后用过变频器控制液压泵转速,从而控制切削液的流量,达到智能冷却的目的。同时,PLC将数据发送到操作面板,实时显示控制系统的工作状态。
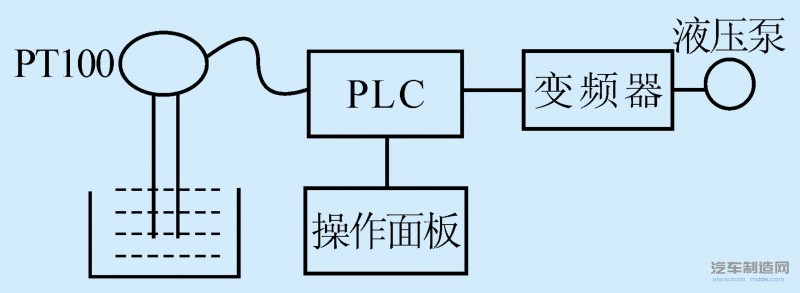
图2 温度测量与控制示意图
控制程序设置为手动控制和自动控制。当手动控制时,在操作面板上设置为“手动”,在此之前应先开启系统,检查各项指标是否正常。并输入要求的温度值,PLC比较该温度值与此时采集到的切削液温度,调节液压泵转速,直到采集到的温度达到该数值。一般直接钻削浅孔时可用手动模式,同样深孔钻床在检修或变频器失灵时也可直接使用手动模式。手动启动时由对应的启动按钮完成并点亮指示灯,停止时由对应的停止按钮完成并熄灭指示灯。
当自动控制时,在操作面板上设置为“自动”,此时,系统在PLC的控制下自动工作。系统将根据事先设置好的“温度—转速”曲线自动调节液压泵转速。保护钻头不会温度过热而损坏,工件发生热变形而工件失效。“温度—转速”曲线可以在操作面板上进行设置。
3 试验分析
深孔加工过程中,其切削区的温度不断升高,随着温度升高,钻头发生热变形,钻头耐磨性能急速下降,切削能力严重减弱。图3通过高倍显微镜对深孔加工过的切削刃进行观察,可见,中间齿切削刃中部明显发黑,说明此处磨损较严重,所以试验以切削刃的磨损程度为参考,以此来验证温度控制装置是否有效。
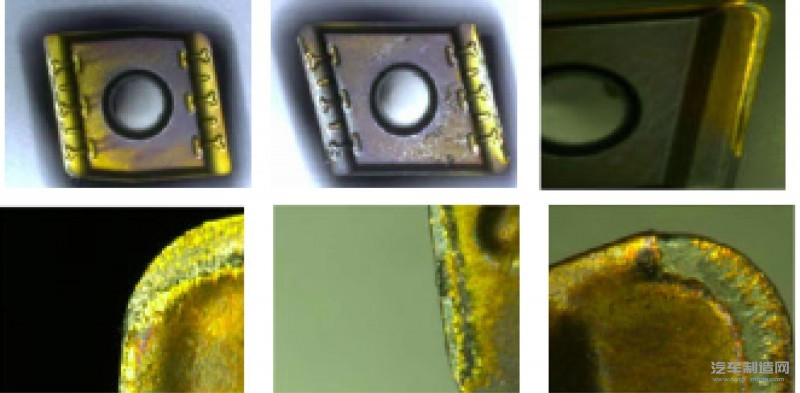
图3 显微系统下外齿、中间齿、中心齿的磨损情况
进行两次有无温度控制装置的深孔加工对比试验,检验两种情况下刀片磨损程度。试验刀片材料为YG8,加工材料分别为45钢和钛合金(TC4),切削用量:转速n=600r/min、进给量f =0.05mm/r。试验数据见表1。
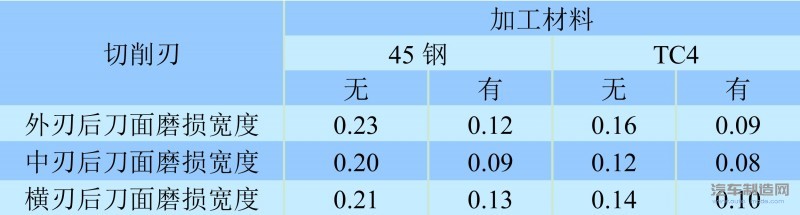
表1 刀具磨损值(mm)
图4和图5分别为使用和未使用温度控制系统加工45钢的刀具磨损情况。从表1、图4和图5可以得出:钻削45钢及钛合金时,没有使用温度控制装置的刀具磨损较大,尤其是加工45钢时的刀具磨损较为严重,而在加工钛合金时两种情况下磨损差别不是特别大,这主要是因为钛合金的主要切削力小于45钢等因素造成。通过试验可以看出,使用本文设计的温度控制装置能够有效降低切削区的温度,进而减轻刀具的磨损程度。
(a)外刃后刀面磨损(b)中刃后刀面磨损(c)横刃后刀面磨损
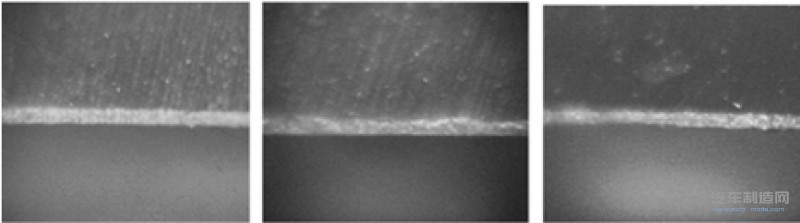
图4 使用温度控制系统加工45钢的刀具磨损情况
(a)外刃后刀面磨损 (b)中刃后刀面磨损 (c)横刃后刀面磨损
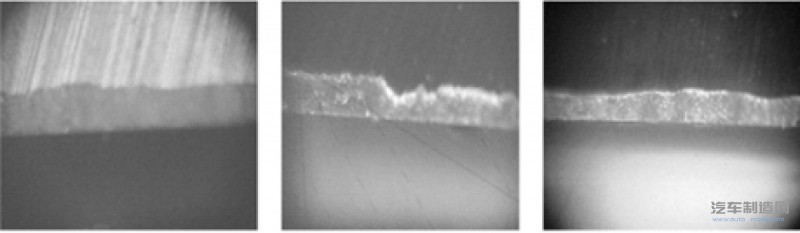
图5 未使用温度控制系统加工45钢的刀具磨损情况
总结:
本文基于PLC设计的深孔钻头降温装置,设有手动和自动两种工作模式,能够根据切削液的温度信号自动控制切削液流量,实现了深孔钻系统切削液温度在线监测的智能化控制,并且软件操作方便且容易实现,硬件也容易连接,同时对工作环境要求较低,工作稳定可靠,占地面积小,适用于车间现场使用。
编辑推荐
最新资讯
-
辐射亚太,链接全球——采埃孚再制造
2025-07-30 11:46
-
思看科技发布子品牌SCANOLOGY,全球
2025-07-30 11:06
-
风雨不动安如山——比亚迪叉车构筑“
2025-07-30 08:48
-
NEAS CHINA 新能源汽车技术与生态链
2025-07-29 09:52
-
三维扫描革新碾磨机辊套检测,效率与
2025-07-25 10:46