简单分析镗刀在汽车领域的应用
2017-12-04 17:47:11· 来源:工具技术
Bosch Rexroth公司在液压、电气传动和控制、变速箱技术以及线性与安装等技术方面可以提供非常广泛的产品与服务。为了其市场主导地位,Bosch Rexroth公司一直把其产品、工艺和生产辅助设备放到检验台上进行详细检验。
针对铸件加工的高效镗刀
Bosch Rexroth公司在液压、电气传动和控制、变速箱技术以及线性与安装等技术方面可以提供非常广泛的产品与服务。为了其市场主导地位,Bosch Rexroth公司一直把其产品、工艺和生产辅助设备放到检验台上进行详细检验。在Homburg工厂所使用的特殊的硬质合金刀具方面,亦是如此。这些特殊刀具必须与各种生产条件作最佳匹配,并实现最好的经济性。刀具的加工路径、加工时间和预处理及后处理等步骤均与刀具成本呈比例关系。
在加工阀套贯穿孔时,需要对材料进行处理。迄今为止所采用的GG30 铸铁明显存在性能缺陷,也不具经济性。为此,Bosch Rexroth公司开始为此类钻孔寻找一种新的技术方案,并与多家特种刀具供应厂商联系。
其中一家位于Sien地区的Müller公司,它已经开始与Bosch Rexroth公司在其他生产步骤上进行合作。Müller公司是一家针对镗孔、锪孔、铰孔和铣削作业的VHM精密刀具的供应商。这家专业化的特种刀具制造商在其产品和服务上,首先是面向机床设备制造业、加工行业、汽车零部件配套业、汽车制造业和其他金属加工企业。在所选的技术工艺框架内,所有供应厂商都必须先提供一份包含建议、供货、对客户特殊需求的匹配和易损刀具的配备等方面内容的整体方案。
图1 Müller公司精密刀具生产现场
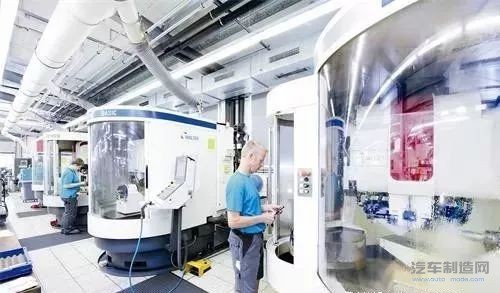
“Müller公司的技术方案瞬间就让我们折服。此外,该企业也具备精密刀具制造和精磨所需的ISO9001.2008相关的认证资质。”Bosch Rexroth公司刀具设计师Michael Koch表示。因此,Bosch Rexroth公司委托Müller公司为铸铁加工场合制造和提供特种刀具。
每件材质为GG30的Bosch Rexroth铸铁阀套上需要镗出三个高精密的孔,孔径为8.4 mm。在进行贯穿镗孔时,务必需要注意避免在孔的背面有毛刺生成,以免对孔进行费时费力的去毛刺和换装等繁琐步骤。此外,Müller公司还需证明,它所重磨和二次涂层的刀具可以达到与新制刀具完全相同的高质量。唯有如此,Bosch Rexroth公司方可确保所需的生产质量、作业安全性和经济性。
刀具可结合各种不同的分级外形设计
Müller公司为Bosch Rexroth公司专门研发符合其实际需求的高效镗刀。所设计的“Max-Feed-Plus”镗刀是一种可以与各种不同的阶梯外形相结合的特种刀具。双方对边角倒角作业有着特别的约定,这也决定了刀具的特定切削形状并可延长主刀片的使用寿命。这两种结果都可对作业稳定性和切屑排放产生积极影响。由于镗孔过程非常柔和,因此在贯穿孔时可以避免毛刺的产生。Max-Feed-Plus刀具的另外一个积极影响便是它可以达到非常高的定位精度。
针对铸件加工的高效镗刀
图2 所设计的Max-Feed-Plus特种刀具可以与各种不同的分级外形相结合
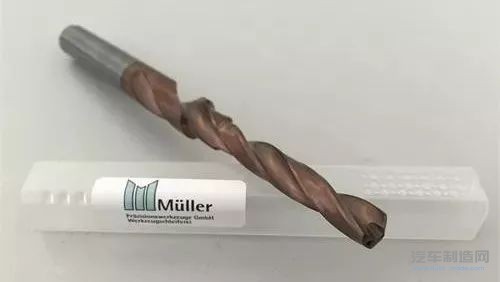
此外,Müller公司不仅仅制造和供应刀具。它同时也以大约400 000批次的年重磨量而跻身于镗刀、铣刀、锯刀和铰刀重磨业的主导专业厂家之列。经过重磨之后的刀具可以通过一种特殊的高效涂层工艺而获得与新刀产品非常相近的性能。Bosch Rexroth公司也因此可以节省费用,并从中受益。其特殊刀具的使用寿命可以比以往延长五倍。
Bosch Rexroth公司在批量生产过程中对Max-Feed-Plus型刀具进行了高强度的测试、评价和优化。所采用的是直径等级在8.4~9.4 mm之间的Max-Feed-Plus型分级镗刀。在对Bosch Rexroth阀套进行贯穿镗孔时,Max-Feed-Plus型分级镗刀可以达到Vc=100 m/min的切削速度和1300 mm/min的进给效率,实现了f=0.34 mm/U的双倍进给量的目标。
通过于所提高的进给量,高效镗刀的行程也可以加大一倍,而同时每个孔的循环加工时间却可以缩短一半。此外,可对边角曲率半径范围内的自由角度进行调整,使切削压力减小到最低的水平。综合起来看,与以往所采用的镗刀几何外形相比,改进型技术方案可以大幅降低所需的进给力。其结果是进给量翻了一倍,加工行程延长了一倍,同时每个孔的加工时间显著缩短。
针对铸件加工的高效镗刀
图3 Bosch Rexroth公司刀具设计人员Michael Koch与Müller公司技术咨询及销售人员Steffen Gospodarek在一起(从左至右)
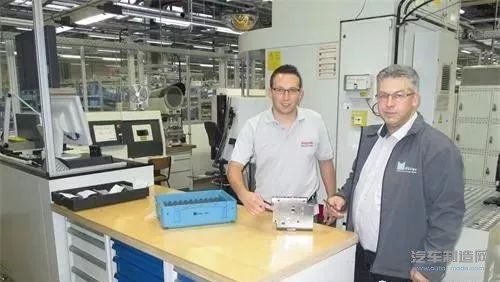
对特殊刀具继续进行测试
自两年以来,Müller公司的高效镗刀被投入使用。“刀具应该以不引起人们过多关注而见长。”Michael Koch强调到。“Müller公司的刀具不仅仅可以满足很高的质量要求,而且也以其极好的性能价格比而令人折服。尤其在与我们特殊要求的匹配和对接方面,Müller公司向我们提供了详尽的咨询服务和各种成熟的特殊技术方案。”这家传动与控制技术专业厂商对Müller公司的技术咨询、服务和效率以及作业安全性等方面的表现非常满意。因此,Bosch Rexroth公司计划就后续的生产步骤,继续对Müller公司的特种刀具进行测试。
采用内冷刀具提高切削速度
毫无疑问,在对钛、镍合金和高强度钢以及碳素纤维材料(CFK)进行高效切削时,传统的溢流冷却润滑剂往往会遇到其物理极限。带有内冷却功能、可以把冷却润滑剂定向地引向加工部位的刀具对此可以提供帮助。“采用带有现代冷却润滑技术的刀具,可以极大降低生产成本,提高刀具的使用寿命,改善切屑状况并加强切削作业的安全性。”Iscar公司镗削产品经理Herbert Volk认为,带有内冷却的镗刀的加工能力更强,“基本上带有内冷却的镗刀会更受欢迎。”他指出,对于镗孔深度超过大约2×D的情况来说,如果采用外部冷却剂导入的话,就无法保证整个加工过程达到足够的冷却效果。在无内冷却镗削作业中,刀具的使用寿命和加工品质都会明显变差。
“切屑形成区域上的直接冷却,切屑排放的进一步优化和冷却,冲洗能耗的进一步降低,这些都是刀具研发工作的目标所在。”在位于杜塞多夫的Sandvik Tooling Deutschland公司负责圆形刀具与卡盘的产品经理Markus Groppe博士强调说。与无内冷却功能的镗刀相比,带有内冷却功能镗刀的加工能力取决于很多因素。“很多特定的应用场合只能采取内冷却方式。”Groppe表示,“而且刀具的使用寿命往往可以提高300%。当然,这种提高并非零成本。与无内冷却功能的镗刀相比,带有内冷却功能的镗刀价格最多要高出40%。”
内冷刀具的正面功效
“刀具的内冷却基本上可以把冷却润滑剂尽可能近地引到刀具加工区。”Kennametal Shared Services公司镗孔和端面铣削产品负责人Tilo Krieg博士表示。他列举出一些正面的影响:“另外,从接触区域把热量排放出来,这有利于延长刀具使用寿命、优化切屑排放、改善表面质量并减少对工件表面的影响。”后续研发工作的目标便是要把这些效果应用到其他等级的刀具上。
当然,在这方面仍然存在着一些传统的局限性,例如多刃刀具、带有很长圆周刀刃的刀具、复杂的成型刀具和其他一些在直径和结构上使得冷却通路受限的刀具。“在这些方面,我们正在下大力气进行研发。”Krieg补充说,“当然,可制造性也是我们所关注的一个方面。”
“总的来说,内冷却硬质合金刀具可以达到较高的切削数据。当镗孔深度超过4×D时,这种刀具也有助于切屑的排放并实现较长的使用寿命。”Walter公司的高级产品经理Helmut Gschrey表示。
“内冷却刀具的后续研发主要涉及最优化问题。”Komet公司负责硬金属与研磨刀具研发的经理Reinhard Durst博士解释说,“我们致力于寻找能够达到冷却剂最大传送量的冷却孔径与刀具具备足够的强度之间的最佳匹配。此外,我们还对冷却孔出口的位置(特别是当采用特殊刀具时)和微量润滑刀具的冷却孔截面及出口进行优化。”对于在何种场合使用何种内冷却刀具的问题,Durst表示,“在金属批量加工场合,几乎只使用内冷却刀具,这是因为唯有通过把冷却剂定向输送到加工位置上并且加强对切屑的排放,才能确保实现较高的切削效率。”在采取微量润滑策略时,则尤为如此。
“对于深镗孔开槽刀具(例如单刃镗刀)来说,内冷却方式是至关重要的,这是因为切屑只有通过冷却剂从镗孔中带出。”TBT公司镗孔刀具业务部经理 Jürgen Bek介绍道。在孔深为250×D以下时,内冷却刀具的工作状态是安全的,“TBT借助于有限元法来对冷却孔的大小和形状进行优化。”对此,切屑通道在开口角度和形状方面的优化不容忽视。
“实际工作表明,内冷却刀具一方面能够为用户带来经济效益,另一方面也可以极大改善加工作业的安全性。”Hartmetall-Werkzeugfabrik Paul Horn公司研发部经理Matthias Luik博士指出,“在切槽口时,采用传统冷却方式的冷却剂往往无法到达刀刃的位置,而采用内冷却方式则可达到最佳效果,并使刀刃的寿命提高6倍。在深部镂空和外冷却剂无法达到的场合,内冷却铣刀则可以充分发挥出其优势,这是因为铣刀往往受到工件的遮挡。由于这种情况在模具制造中经常出现,因此此类场合均采用内冷却铣刀作为技术标配。”
Jakob Lach公司与Audi公司的合作研发工作推进了铝材切削技术能力:一种带有切屑引导功能的内冷却整体PKD铣刀。“把通过PKD切削面所引导的冷却液流与切屑排放功能集合在一个刀具上的技术方案,对于加工作业来说是最理想的。”总经理Horst Lach说,尤其在HSC铝材切割加工上,可以实现用户希望达到的极高的切削速度和进给量,“不仅如此,冷却剂导入整体铣刀可以携带多套PKD刀片,因为在切削作业中所产生的切屑可从加工区域里被即刻排走。”总之,通过在汽车制造业上(例如针对发动机和减速箱外壳的加工)采用新开发的PKD整体铣刀,加工循环时间已经下降50%以上。
在设备上需要满足的条件
在设备方面必须满足的若干前提条件:内冷却至少必须具备15 bar(最佳为50 bar,1 bar=105 Pa)的压力,以输送冷却润滑乳化液、油、MMS、空气或冷却剂等介质,15 000~30 000 r/min之间的高转速和20 000~40 000 mm/min的进给量。
高效切割的目标当然尚未达到。采用CO2或N2等冷却剂来取代常规的冷却润滑剂,可以继续提高单位时间切割量并降低刀具的磨损程度。针对镗削作业的内冷却,例如Chemnitz TU大学机床和生产工艺学院(IWP)目前就在研究如何采用CO2来实现高效冷却的策略问题,正如切削技术教学和研究系主任Martin Dix博士所强调的那样:“在采取这种冷却策略时,针对难切削的金属材料,尤其重要的一点便是要把冷却定位在刀具上并进行优化,以便对刀具重要区域进行冷却。”
低温冷却可以实现无润滑剂的高效镗削作业和较长的刀具使用寿命。为了提高加工效益,需要采取有效的保温措施并对冷却剂液流进行匹配。在刀具上的热量分布方面,冷却通道及其出口的位置非常关键。“这是因为首先工件会得到冷却。”Dix博士表示,“因此工件的硬度会上升,由此在大多数应用场合中刀具的切削力和磨损程度都会随之增加。”唯有在加工塑料材料时,同时冷却工件的做法才有意义,这是因为这种做法可以有效提高材料的可切削性。
Bosch Rexroth公司在液压、电气传动和控制、变速箱技术以及线性与安装等技术方面可以提供非常广泛的产品与服务。为了其市场主导地位,Bosch Rexroth公司一直把其产品、工艺和生产辅助设备放到检验台上进行详细检验。在Homburg工厂所使用的特殊的硬质合金刀具方面,亦是如此。这些特殊刀具必须与各种生产条件作最佳匹配,并实现最好的经济性。刀具的加工路径、加工时间和预处理及后处理等步骤均与刀具成本呈比例关系。
在加工阀套贯穿孔时,需要对材料进行处理。迄今为止所采用的GG30 铸铁明显存在性能缺陷,也不具经济性。为此,Bosch Rexroth公司开始为此类钻孔寻找一种新的技术方案,并与多家特种刀具供应厂商联系。
其中一家位于Sien地区的Müller公司,它已经开始与Bosch Rexroth公司在其他生产步骤上进行合作。Müller公司是一家针对镗孔、锪孔、铰孔和铣削作业的VHM精密刀具的供应商。这家专业化的特种刀具制造商在其产品和服务上,首先是面向机床设备制造业、加工行业、汽车零部件配套业、汽车制造业和其他金属加工企业。在所选的技术工艺框架内,所有供应厂商都必须先提供一份包含建议、供货、对客户特殊需求的匹配和易损刀具的配备等方面内容的整体方案。
图1 Müller公司精密刀具生产现场
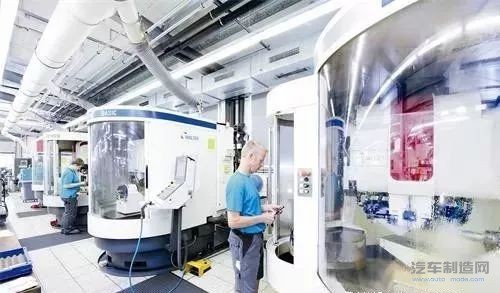
“Müller公司的技术方案瞬间就让我们折服。此外,该企业也具备精密刀具制造和精磨所需的ISO9001.2008相关的认证资质。”Bosch Rexroth公司刀具设计师Michael Koch表示。因此,Bosch Rexroth公司委托Müller公司为铸铁加工场合制造和提供特种刀具。
每件材质为GG30的Bosch Rexroth铸铁阀套上需要镗出三个高精密的孔,孔径为8.4 mm。在进行贯穿镗孔时,务必需要注意避免在孔的背面有毛刺生成,以免对孔进行费时费力的去毛刺和换装等繁琐步骤。此外,Müller公司还需证明,它所重磨和二次涂层的刀具可以达到与新制刀具完全相同的高质量。唯有如此,Bosch Rexroth公司方可确保所需的生产质量、作业安全性和经济性。
刀具可结合各种不同的分级外形设计
Müller公司为Bosch Rexroth公司专门研发符合其实际需求的高效镗刀。所设计的“Max-Feed-Plus”镗刀是一种可以与各种不同的阶梯外形相结合的特种刀具。双方对边角倒角作业有着特别的约定,这也决定了刀具的特定切削形状并可延长主刀片的使用寿命。这两种结果都可对作业稳定性和切屑排放产生积极影响。由于镗孔过程非常柔和,因此在贯穿孔时可以避免毛刺的产生。Max-Feed-Plus刀具的另外一个积极影响便是它可以达到非常高的定位精度。
针对铸件加工的高效镗刀
图2 所设计的Max-Feed-Plus特种刀具可以与各种不同的分级外形相结合
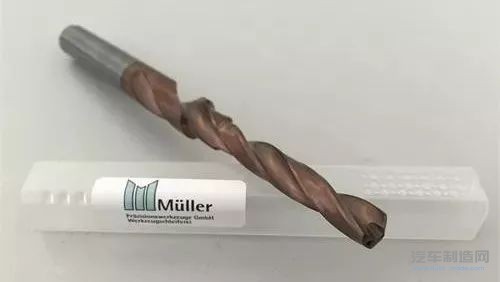
此外,Müller公司不仅仅制造和供应刀具。它同时也以大约400 000批次的年重磨量而跻身于镗刀、铣刀、锯刀和铰刀重磨业的主导专业厂家之列。经过重磨之后的刀具可以通过一种特殊的高效涂层工艺而获得与新刀产品非常相近的性能。Bosch Rexroth公司也因此可以节省费用,并从中受益。其特殊刀具的使用寿命可以比以往延长五倍。
Bosch Rexroth公司在批量生产过程中对Max-Feed-Plus型刀具进行了高强度的测试、评价和优化。所采用的是直径等级在8.4~9.4 mm之间的Max-Feed-Plus型分级镗刀。在对Bosch Rexroth阀套进行贯穿镗孔时,Max-Feed-Plus型分级镗刀可以达到Vc=100 m/min的切削速度和1300 mm/min的进给效率,实现了f=0.34 mm/U的双倍进给量的目标。
通过于所提高的进给量,高效镗刀的行程也可以加大一倍,而同时每个孔的循环加工时间却可以缩短一半。此外,可对边角曲率半径范围内的自由角度进行调整,使切削压力减小到最低的水平。综合起来看,与以往所采用的镗刀几何外形相比,改进型技术方案可以大幅降低所需的进给力。其结果是进给量翻了一倍,加工行程延长了一倍,同时每个孔的加工时间显著缩短。
针对铸件加工的高效镗刀
图3 Bosch Rexroth公司刀具设计人员Michael Koch与Müller公司技术咨询及销售人员Steffen Gospodarek在一起(从左至右)
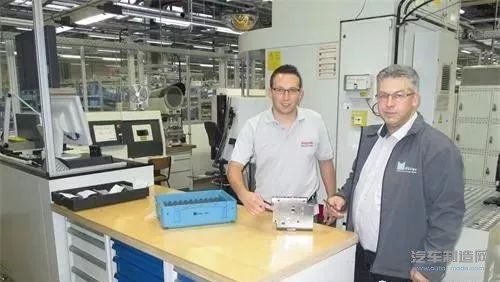
对特殊刀具继续进行测试
自两年以来,Müller公司的高效镗刀被投入使用。“刀具应该以不引起人们过多关注而见长。”Michael Koch强调到。“Müller公司的刀具不仅仅可以满足很高的质量要求,而且也以其极好的性能价格比而令人折服。尤其在与我们特殊要求的匹配和对接方面,Müller公司向我们提供了详尽的咨询服务和各种成熟的特殊技术方案。”这家传动与控制技术专业厂商对Müller公司的技术咨询、服务和效率以及作业安全性等方面的表现非常满意。因此,Bosch Rexroth公司计划就后续的生产步骤,继续对Müller公司的特种刀具进行测试。
采用内冷刀具提高切削速度
毫无疑问,在对钛、镍合金和高强度钢以及碳素纤维材料(CFK)进行高效切削时,传统的溢流冷却润滑剂往往会遇到其物理极限。带有内冷却功能、可以把冷却润滑剂定向地引向加工部位的刀具对此可以提供帮助。“采用带有现代冷却润滑技术的刀具,可以极大降低生产成本,提高刀具的使用寿命,改善切屑状况并加强切削作业的安全性。”Iscar公司镗削产品经理Herbert Volk认为,带有内冷却的镗刀的加工能力更强,“基本上带有内冷却的镗刀会更受欢迎。”他指出,对于镗孔深度超过大约2×D的情况来说,如果采用外部冷却剂导入的话,就无法保证整个加工过程达到足够的冷却效果。在无内冷却镗削作业中,刀具的使用寿命和加工品质都会明显变差。
“切屑形成区域上的直接冷却,切屑排放的进一步优化和冷却,冲洗能耗的进一步降低,这些都是刀具研发工作的目标所在。”在位于杜塞多夫的Sandvik Tooling Deutschland公司负责圆形刀具与卡盘的产品经理Markus Groppe博士强调说。与无内冷却功能的镗刀相比,带有内冷却功能镗刀的加工能力取决于很多因素。“很多特定的应用场合只能采取内冷却方式。”Groppe表示,“而且刀具的使用寿命往往可以提高300%。当然,这种提高并非零成本。与无内冷却功能的镗刀相比,带有内冷却功能的镗刀价格最多要高出40%。”
内冷刀具的正面功效
“刀具的内冷却基本上可以把冷却润滑剂尽可能近地引到刀具加工区。”Kennametal Shared Services公司镗孔和端面铣削产品负责人Tilo Krieg博士表示。他列举出一些正面的影响:“另外,从接触区域把热量排放出来,这有利于延长刀具使用寿命、优化切屑排放、改善表面质量并减少对工件表面的影响。”后续研发工作的目标便是要把这些效果应用到其他等级的刀具上。
当然,在这方面仍然存在着一些传统的局限性,例如多刃刀具、带有很长圆周刀刃的刀具、复杂的成型刀具和其他一些在直径和结构上使得冷却通路受限的刀具。“在这些方面,我们正在下大力气进行研发。”Krieg补充说,“当然,可制造性也是我们所关注的一个方面。”
“总的来说,内冷却硬质合金刀具可以达到较高的切削数据。当镗孔深度超过4×D时,这种刀具也有助于切屑的排放并实现较长的使用寿命。”Walter公司的高级产品经理Helmut Gschrey表示。
“内冷却刀具的后续研发主要涉及最优化问题。”Komet公司负责硬金属与研磨刀具研发的经理Reinhard Durst博士解释说,“我们致力于寻找能够达到冷却剂最大传送量的冷却孔径与刀具具备足够的强度之间的最佳匹配。此外,我们还对冷却孔出口的位置(特别是当采用特殊刀具时)和微量润滑刀具的冷却孔截面及出口进行优化。”对于在何种场合使用何种内冷却刀具的问题,Durst表示,“在金属批量加工场合,几乎只使用内冷却刀具,这是因为唯有通过把冷却剂定向输送到加工位置上并且加强对切屑的排放,才能确保实现较高的切削效率。”在采取微量润滑策略时,则尤为如此。
“对于深镗孔开槽刀具(例如单刃镗刀)来说,内冷却方式是至关重要的,这是因为切屑只有通过冷却剂从镗孔中带出。”TBT公司镗孔刀具业务部经理 Jürgen Bek介绍道。在孔深为250×D以下时,内冷却刀具的工作状态是安全的,“TBT借助于有限元法来对冷却孔的大小和形状进行优化。”对此,切屑通道在开口角度和形状方面的优化不容忽视。
“实际工作表明,内冷却刀具一方面能够为用户带来经济效益,另一方面也可以极大改善加工作业的安全性。”Hartmetall-Werkzeugfabrik Paul Horn公司研发部经理Matthias Luik博士指出,“在切槽口时,采用传统冷却方式的冷却剂往往无法到达刀刃的位置,而采用内冷却方式则可达到最佳效果,并使刀刃的寿命提高6倍。在深部镂空和外冷却剂无法达到的场合,内冷却铣刀则可以充分发挥出其优势,这是因为铣刀往往受到工件的遮挡。由于这种情况在模具制造中经常出现,因此此类场合均采用内冷却铣刀作为技术标配。”
Jakob Lach公司与Audi公司的合作研发工作推进了铝材切削技术能力:一种带有切屑引导功能的内冷却整体PKD铣刀。“把通过PKD切削面所引导的冷却液流与切屑排放功能集合在一个刀具上的技术方案,对于加工作业来说是最理想的。”总经理Horst Lach说,尤其在HSC铝材切割加工上,可以实现用户希望达到的极高的切削速度和进给量,“不仅如此,冷却剂导入整体铣刀可以携带多套PKD刀片,因为在切削作业中所产生的切屑可从加工区域里被即刻排走。”总之,通过在汽车制造业上(例如针对发动机和减速箱外壳的加工)采用新开发的PKD整体铣刀,加工循环时间已经下降50%以上。
在设备上需要满足的条件
在设备方面必须满足的若干前提条件:内冷却至少必须具备15 bar(最佳为50 bar,1 bar=105 Pa)的压力,以输送冷却润滑乳化液、油、MMS、空气或冷却剂等介质,15 000~30 000 r/min之间的高转速和20 000~40 000 mm/min的进给量。
高效切割的目标当然尚未达到。采用CO2或N2等冷却剂来取代常规的冷却润滑剂,可以继续提高单位时间切割量并降低刀具的磨损程度。针对镗削作业的内冷却,例如Chemnitz TU大学机床和生产工艺学院(IWP)目前就在研究如何采用CO2来实现高效冷却的策略问题,正如切削技术教学和研究系主任Martin Dix博士所强调的那样:“在采取这种冷却策略时,针对难切削的金属材料,尤其重要的一点便是要把冷却定位在刀具上并进行优化,以便对刀具重要区域进行冷却。”
低温冷却可以实现无润滑剂的高效镗削作业和较长的刀具使用寿命。为了提高加工效益,需要采取有效的保温措施并对冷却剂液流进行匹配。在刀具上的热量分布方面,冷却通道及其出口的位置非常关键。“这是因为首先工件会得到冷却。”Dix博士表示,“因此工件的硬度会上升,由此在大多数应用场合中刀具的切削力和磨损程度都会随之增加。”唯有在加工塑料材料时,同时冷却工件的做法才有意义,这是因为这种做法可以有效提高材料的可切削性。
编辑推荐
最新资讯
-
跨越速运凭什么“圈粉”万千客户?“
2025-07-01 14:42
-
数智破局启新篇・生态共生再启程 —
2025-06-27 20:13
-
助力汽车零部件产线智能化升级,西门
2025-06-27 13:59
-
BBA集体转向!放弃全面电动化
2025-06-26 17:32
-
比换柜省钱,比自研省心,西门子Xcel
2025-06-25 15:07