大型一体化压铸技术正成为汽车压铸件的关键技术方向
1、汽车压铸铝合金零部件行业发展概况
汽车铝合金零部件可以大致分为变形铝合金零部件、铸造铝合金两类,其中变形铝合金包括发动机罩、翼子板、顶盖和后备箱盖等汽车用铝部件,集中在车轮、发动机缸体缸盖;铸造铝合金则主要包括新能源汽车电机壳体、控制器壳体、减速箱壳体、发动机、轮毂和变速器等。铸造铝合金在汽车用铝合金中占据主导地位,占汽车用铝量的80%左右。据研究表明,目前汽车用铝合金材料中55.1%的使用高压压铸生产,25.7%的为普通铸造,8.9%的为轧制,8.6%为挤压,1.7%为锻造。
在包括汽车、建筑、机械设备等在内的诸多压铸产业下游应用领域之中,汽车用铝铸件的占比是最高的,占比超过70%。根据中国铸造协会发布的数据,受新能源汽车高速增长、汽车轻量化发展的驱动,近年来我国铝合金压铸行业产量整体呈现波动上升趋势。
2019-2023年我国铝合金铸件产量
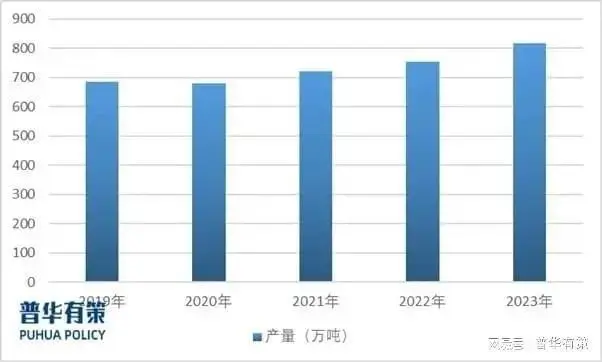
据预测,我国汽车用铝合金仍存在进一步增长的巨大空间,2016年我国乘用车的平均单车用铝量为110.36kg,预计到2030年我国乘用车平均单车用铝量将达到242.22kg,较2016年翻一番。
2、汽车压铸铝合金零部件行业发展趋势
当前,我国汽车行业是推动新一轮科技革命和产业变革的重要力量,新一代信息通信、新能源、新材料等技术与汽车产业加速融合,汽车产业进入关键的转型升级期,无论是整车厂商还是上游汽车零部件产业都面临着竞争格局的全面重塑。在此背景下,汽车压铸铝合金零部件行业面临着以下发展趋势:
(1)汽车电动化趋势延续,新能源汽车渗透率持续提升,但市场竞争将逐步加剧
2018年以来,我国汽车市场在经历了持续高速增长后,已经进入降速调整、转型升级阶段,未来汽车销量增速降低将成为常态,汽车市场结构将逐步由增量发展向存量竞争转变,新能源汽车与主流传统燃油汽车市场逐步展开市场竞争。2023年,国内新能源汽车市场渗透率达到31.60%,较2022年增加约6个百分点,未来一段时间内新能源汽车销量预计将持续保持高速增长,预计在2030年前达成国内市场超过50%的目标。
但随着汽车行业整体增速放缓,未来一段时间里竞争将在全方位展开,预计我国汽车企业数量将有所减少,产业集中度进一步提升。2022年以来,恒大、威马等造车新势力企业陆续经历经营困难、停工停产等风险,新能源汽车市场淘汰节奏加快。2023年以来,在新能源补贴退坡背景下,在头部企业特斯拉、比亚迪等的带动下,大量车企宣布降价并且降价潮蔓延至传统燃油车企,下游竞争策略和竞争更趋于激烈化、复杂化,未来随着下游车企进入深层次竞争洗牌阶段,势必也将影响上游汽车零部件供应链。下游市场竞争加剧也将倒逼车企对上游供应链提出更高的零部件价格年降要求,这就要求零部件生产企业进一步加强工艺开发和降本能力,配合下游车企提升产品竞争力。
(2)汽车零部件采购全球化,我国零部件产业对外扩张步伐加快
随着汽车市场竞争的日益激烈,以及各类汽车零部件厂商的日益成熟,世界各大汽车公司开始专注于自身的核心业务即汽车的设计与组装。全球汽车工业已经确立了明确的国际分工合作体系,大型头部整车企业除了在消费市场建立自己的整车工厂之外,还广泛采取全球化的零部件采购战略,整体行业高度专业化分工、生产精益化趋势明显。
全球汽车整车厂商亦在逐渐降低零部件自制比率,全球化采购趋势进一步加强,为我国具备先进制造能力的本土汽车零部件供应商提供了良好的发展机遇。依靠国内汽车市场规模以及成本优势,我国部分优质自主零部件厂商凭借自身技术积累以及技术引进,企业规模不断壮大,行业地位持续提升,部分领先的汽车零部件及上游企业正在通过出口、海外建厂、并购等方式实现对外扩张。
(3)汽车零部件开发逐步迈向平台化开发模式
为了加快产品开发速度、减少开发成本,汽车工业已经平台化开发战略,将汽车开发从单车型的开发转向系统化、共享化的开发,提高基础零部件的通用性,尽最大限度实现零部件共享。通过实施平台化开发战略,整车企业可以发挥规模效应,降低开发和生产成本;同时又能在竞争日剧激烈的消费市场以多样化、个性化的车型吸引潜在消费者,扩大市场份额。例如大众汽车开发四大模块化平台(MQB、MLB、MHB和中置发动机平台)、吉利汽车面向下一代排放、油耗标准打造的蓝鲸NE动力平台等。
在平台开发模式下的开发体系分为平台开发、车型开发、零部件总成/模块/系统开发三个层次,会对原有的零部件采购模式产生重大影响。由于平台架构适用于整车企业的系列产品群而非单个产品,开发的难度和要求更高,需要零部件企业有零部件通用化设计开发能力;同时平台化开发模式下,通用零部件的产品生命周期更长、订单规模更高,需要零部件厂商在平台开发阶段就能有足够的技术预研和质量策划能力,一旦适用于整个平台架构级别的零部件发生质量召回事件,将为零部件生产企业带来巨大的经营风险。
(4)汽车轻量化仍是下游行业发展的重要方向,推动铝合金零部件使用量上升
汽车轻量化是指在满足汽车使用要求、安全性和成本控制的条件下,将结构轻量化设计技术与多种轻量化材料、轻量化制造技术集成应用,从而实现产品减重。作为节能汽车、新能源汽车和智能网联汽车的共性基础技术之一,汽车轻量化是目前实现汽车节能减排的重要途径之一。
对传统燃油车而言,汽车平均油耗与整车质量正相关,因此汽车轻量化对降低传统燃油车油耗具有积极作用。2020年10月,中国汽车工程学会牵头组织编制的《节能与新能源汽车技术路线图2.0》发布,对各类汽车每百公里油耗提出了要求,目标是在2035年我国新能源汽车占到总销量50%,乘用车每百公里油耗降低至3.2L,该文件还列出了节能汽车降低油耗的时间表。研究表明,若燃油车减重10%,油耗将降低5%-10%;汽车自重每减少100kg,百公里油耗可以降低0.3-0.6升。要达成2035年油耗降低目标,汽车轻量化技术仍是未来一段时间传统燃油车企技术升级的重要方向。
对新能源汽车而言,汽车轻量化的重要性更加不言而喻。虽然在政策扶持、市场发育的双重作用下,新能源汽车的渗透率持续提升,已经进入增长快车道。但对部分消费者而言,“里程焦虑”仍是限制购买意愿的重要因素。在解决续航里程问题上,由于电池能量密度的提升有赖于电池技术的突破和充分商业化,所以铝合金材料替代汽车钢材零部件的轻量化技术是当前新能源汽车延长续航里程的最直接、有效的手段。若新能源车减重100kg,续航里程将提升10-11%,同时降低20%的电池成本和日常损耗成本。因此,对于传统燃油车和新能源汽车而言,轻量化技术能够提升动力系统工作效率,从而减少能量消耗、提升整车续航,逐渐成为各大整车及零部件企业的重要技术方向。而汽车轻量化可以从材料替代、工艺改进和结构优化等方面入手,其中,以铝合金替代钢材是最常见的轻量化实现方式。
根据《节能与新能源汽车技术路线图2.0》的规划,未来10年国内汽车轻量化发展趋势不变,单车用铝量将在2025年超过250kg,2030年超过350kg,在此背景下汽车用铝合金精密零部件具有巨大的增长空间。
(5)在汽车压铸件领域,大型一体化压铸技术正成为领军企业布局的关键技术方向
在减重、提效和降本的多重驱动力下,2019年特斯拉提出了车身一体成形铸造方法,通过采用一体成形压铸方式生产ModelY底板总成,将原先由多工序所需的70多个零件精简为一体化成型的一个压铸件,减少了组装焊接等程序,减重约30%,降低制造成本约40%。同时,零件一体化成型在应对碰撞时能更好地承受冲击力,提升车身的骨架安全性。
相比于传统的称身“冲压+焊接”工艺,一体化压铸具有轻量化、零件数量及焊接工序步骤减少、制造精度提升、人力和土地成本降低的优势,大幅降低了整车的制造成本。一体化压铸的上述优势已引起各个主机厂及配套的铝合金零部件厂商的高度关注,自特斯拉发布相关技术和产品应用以来,一体化压铸已经成为汽车铝合金压铸企业产能布局与技术开发的主要方向之一。目前,部分资金实力较为雄厚的同行业上市企业如晋拓股份、文灿股份等已陆续订购超大吨位(6000T以上)压铸机,提前布局超大型一体化压铸市场。随着一体化压铸技术的渗透率提升,2025年超大型一体化压铸件的市场空间有望达到389亿元,2021-2025年的复合增长率达到205%。
车身大型一体化压铸件重量可达60余公斤,浇铸重量达到100公斤以上,需要使用锁模力在6000T以上的超大型压铸机(特斯拉ModelY所使用的压铸机为6000-8000T),相关设备造价高昂,对中小压铸企业来说形成了较大的资金壁垒。此外,要进入大型一体化压铸件市场,除了购置设备之外,还需要解决大型压铸件所带来的压铸工艺难度大幅增加、大型压铸模具开发、免热处理合金材料开发、压铸周边设备升级等一系列技术问题。未来一段时间内,大型一体化压铸技术将是行业内领军企业布局的关键技术方向。
3、汽车压铸铝合金零部件行业竞争格局
整体来看,我国铸造行业的市场集中度较低,参与者众多,市场竞争较为激烈。我国目前尚有2万多家铸造企业,企业平均规模偏小,行业发展不平衡问题较为突出。
在汽车零部件压铸行业领域,主要的市场竞争者大体可以分为三类:外资或合资压铸企业、国内整车厂商的附属压铸企业和独立的内资压铸企业。
其中,第一类外资或合资压铸企业的数量少,单个企业规模大,专业化程度高,在大型、精密、复杂压铸件设计制造方面具有较强的竞争力,领先于国内大多数供应商,相关企业包括NEMAK(诺玛科)、RYOBI(利优比)、皮尔博格;第二类国内整车厂商附属压铸企业通常从属于下游整体集团,依附于整车厂为相关车企提供压铸产品配套,相关企业包括一汽铸造有限公司、东风(十堰)有色铸件有限公司、比亚迪旗下的弗迪精工有限公司;第三类独立的内资压铸企业则以其技术研发优势、产品质量优势、全方位服务优势等在汽车零部件细分领域形成一定的竞争优势,能对客户需求进行快速反应,已与国内外知名车企建立了长期稳定的合作关系,相关自主供应商包括广东鸿图、文灿股份、爱柯迪、旭升股份等。
4、汽车压铸铝合金零部件行业进入壁垒
(1)资金和规模壁垒
汽车零部件铸造行业属于资金密集型行业。汽车零部件厂商需要配置包括熔炼设备、压铸设备、机加工中心、精密检测设备等在内的一系列设备,设备数量众多、购置费用较高;下游国内外知名整车企业也往往要求其合格供应商具有一定规模的产能和交货能力,所需的固定资产投入较大,并且随着下游车企客户对轻量化和复杂精密结构件的要求不断提高,汽车零部件厂商还需要持续投入资金对生产线进行升级改造,因此本行业具有较高的资金进入门槛。
与此同时,由于汽车零部件铸造行业具有一定的重资产特征,汽车零部件铸造企业所需要足够的生产规模才能充分发挥规模经济,降低边际成本,对新进入者而言在短时间内实现规模化生产的难度较大,前期可能面临盈利较差甚至亏损的局面。因此,资金和规模壁垒形成了新进入者进入本行业的主要障碍之一。
(2)客户和认证壁垒
汽车行业高度专业化、精细化,为满足汽车在安全性、舒适性以及成本效益等方面的严格要求,全球汽车整车厂商、一级汽车零部件厂商在选择上游供应商方面建立了一套严格的供应商认证标准,除了行业内通用的IATF16949质量体系认证审核之外,部分大型跨国车企还依据自身质量控制标准和采购流程建立了自身的质量体系认证标准,比如大众汽车的FormelQ基本准则、通用汽车的供应商制造体系BIQS、戴勒姆-奔驰的供应商现场审核OSA等。在进入下游车企或一级零部件厂商的合格供应商目录前,汽车零部件铸造企业往往需要经过长时间的全面考核,评审内容主要涵盖质量控制能力、生产组织能力、企业管理能力和市场应变能力等,对供应商的技术水平、生产流程、质量控制、设备状况等方面提出严格要求。经过多次审查、检验后,供应商与客户达成初步合作意向。在初步合作阶段,供应商根据客户个性化的产品需求进行产品研发以及小批量试制,待产品质量稳定并经客户验收合格后,供应商才进入其正式供应商名录,相关产品才可以进入量产阶段。这个客户认证过程往往长达1年以上。因此,一旦确立合作关系,整车厂商通常不会轻易更换供应商,形成较强的客户粘性。相比于行业新进入者,现有国内主要压铸企业与各下游整车厂商已经建立了长期稳定的合作关系,具有较明显的先发优势及客户资源优势。
(3)产品开发和技术壁垒
随着汽车工业的发展,整车企业对汽车零部件的性能、质量、轻量化、安全性等要求逐步提升,行业技术壁垒不断提高。具体到汽车精密零部件铸造行业,供应商在产品结构设计与工艺方案开发、工装模具设计开发、压铸工艺技术等多个环节都需要长期的技术积累,才能满足下游整车企业和一级零部件供应商对产品的质量要求。
另一方面,随着全球汽车产业链专业化分工日益明显,新能源汽车技术快速发展、产品迭代周期缩短,汽车零部件各级配套供应商协同研发已成为行业发展趋势,从而要求汽车零部件厂商具备更强的新产品开发能力和精细化的项目管理能力。上游汽车零部件供应商需要在下游客户提出产品需求的基础上,综合考量产品质量稳定性、生产效率、成本控制等因素进行产品研发,并根据客户反馈意见不断对产品设计进行调整。这种上下游同步研发模式对汽车零部件供应商的自主研发、持续创新及快速反应能力提出较高要求,由此,产品开发和技术壁垒也是行业新进入者面临的主要障碍之一。
-
乘用车金属冲压
2025-05-29 -
冲压技术在电机叠片制造的应用
2024-09-06 -
车身零部件包边质量控制要点
2024-09-05 -
轻量化技术——热汽胀形工艺技术解析
2024-09-04
最新资讯
-
创新功率器件构建可持续未来 ——三
2025-09-04 15:57
-
旭化成为芬兰氢能项目提供集装箱式碱
2025-09-02 17:45
-
旭化成旗下宾霸品牌重磅亮相2025上海
2025-09-01 16:52
-
中国车企服务出海先行者:新央企新长
2025-08-29 16:13
-
携手共赴“智”造未来!埃马克推动大
2025-08-27 18:12