底盘紧固件开发的流程和关键技术
底盘是指汽车上由传动系、行驶系、转向系和制动系四部分组成的组合。底盘的作用是支承、安装汽车发动机及其各部件、总成,形成汽车的整体造型,接受发动机的动力,使汽车产生运动,保证正常行驶。
一个好的底盘,可以保证驾驶者的生命安全。底盘的四大组成部件和发动机都是使用高强度螺纹紧固件连接在一起的, 这些紧固件的连接质量直接关系到汽车的行驶安全。
01 底盘紧固件开发流程
底盘紧固件在整车正向开发过程中的作用相当关键,涉及环节多,需要每个环节都制定完备的流程来优化设计和预防失效发生。下面的流程图是主流汽车厂底盘紧固件开发的主要节点。
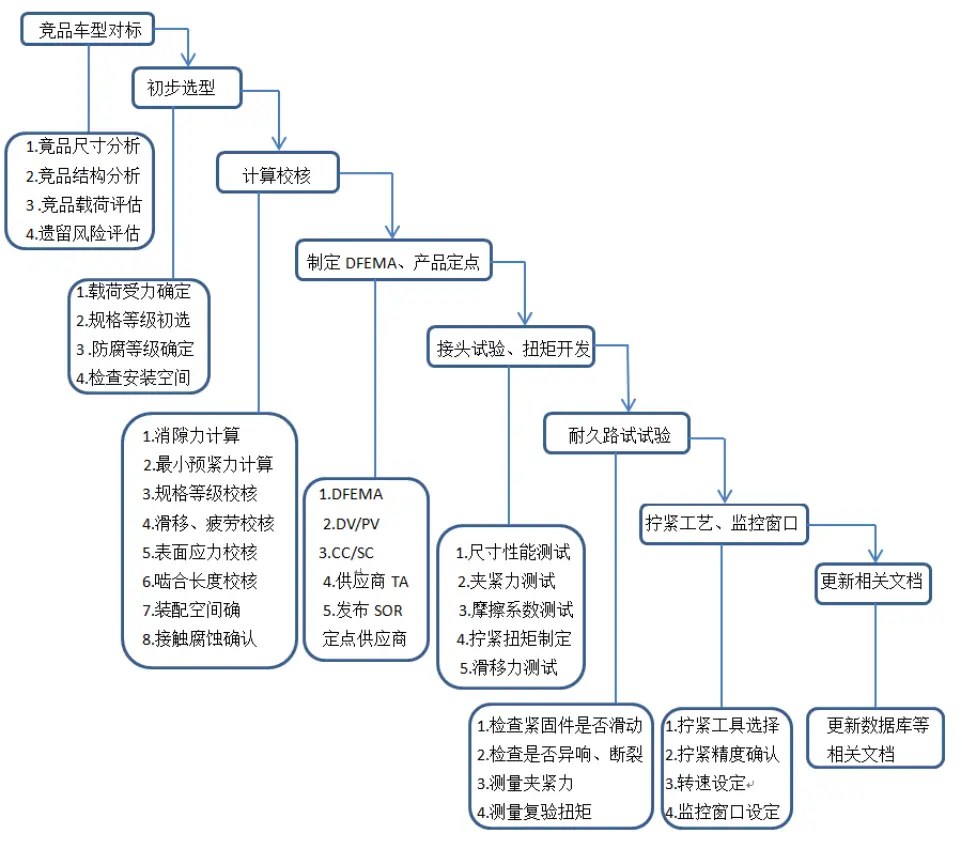
02 底盘用紧固件防松处理
由于底盘受力复杂,造成紧固件扭矩衰减的因素较多,所以通常在连接副设计中采取防松措施,如螺纹预涂胶、全金属自锁螺母、带自锁功能的螺纹结构、具有防松功能的专利螺纹牙,或者是连接副设计自锁功能。底盘中使用最多的是螺纹预涂胶和全金属自锁螺母。如下图,螺纹预涂胶可参考DIN267、锁紧螺母可参考Q330。
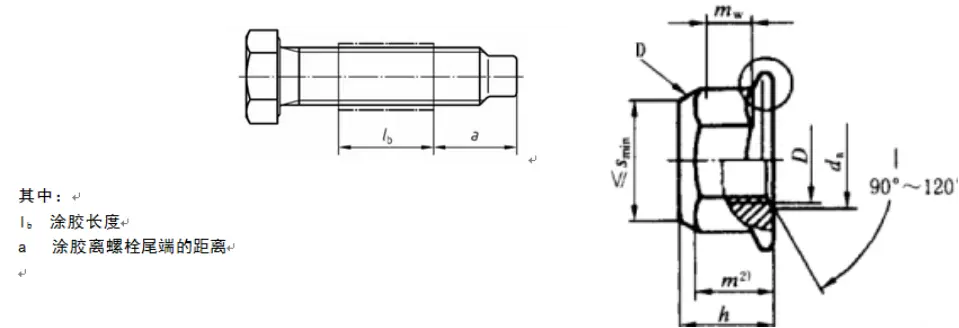
03 底盘用紧固件常用材料
底盘连接副一般多采用扭矩-转角法,还有一些连接点采用屈服点拧紧法安装。这对螺栓的性能指标提出很高的要求,并要求处理好摩擦系数、硬度、伸长量、屈服强度之间的关系。下表是主机厂底盘紧固件常用的材料。
04 底盘用紧固件螺纹精度等级
螺纹的配合是间隙配合,精度不高的配合会引起连接副扭矩衰减,造成连接失效。为了保证在电泳或涂覆之后螺纹精度合格,一般采取减小外螺纹中径,加大内螺纹中径的方式。螺纹精度等级按GB/T 196,和GB/T 197标准执行。在不同的表面处理工艺下,对精度要求不同。
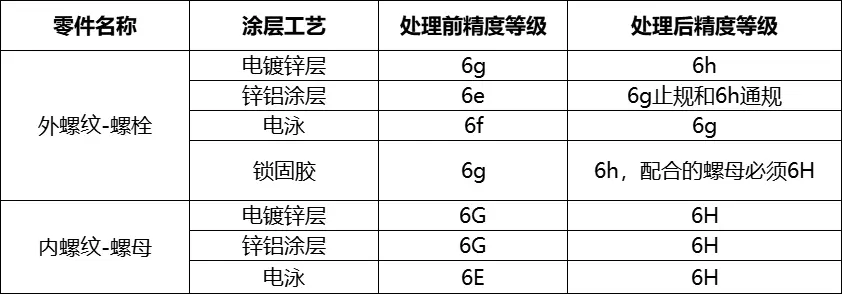
05 底盘用紧固件装配方式的选择
1、扭矩法装配
目前主机厂总装线上最常用的是扭矩法装配。扭矩法是利用在弹性区域内扭矩值与预紧力的线性关系,只对紧固扭矩进行控制,操作简便。
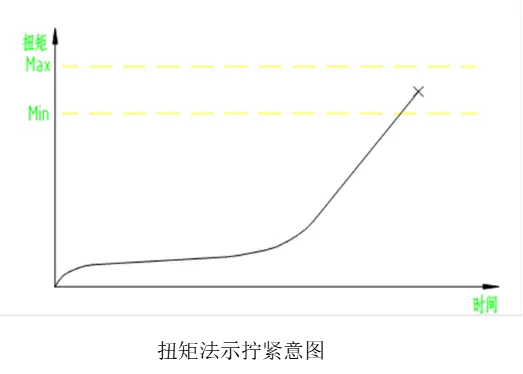
扭矩法的优缺点:
a 直接控制加载扭矩,操作简单,易实现,拧紧设备便宜;
b 用于螺栓弹性区域;
c 预紧力有较大散差,通常可达到±30%;
d 受摩擦系数影响大;
e 紧固件材料利用率低;
f 90%的加载扭矩用于克服摩擦力。
2、扭矩-转角法
最近几年,越来越多的扭矩-转角法被使用。扭矩-转角法是拧紧至规定的起始扭矩后,再转过一定的转角达到螺栓的塑性变形区或弹性变形区。设计扭矩-转角法的关键在于起始扭矩和转角的定义,这个要结合试验室曲线取值。
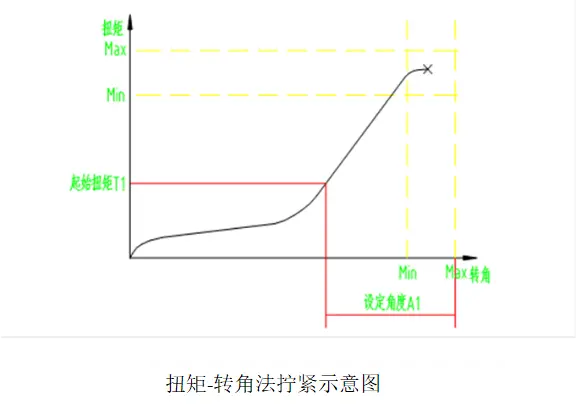
相对扭矩法,扭矩-转角法因通过转角直接控制螺栓伸长量,拧紧后能获得较小的预紧力散差,通常在±15%左右。但拧紧设备贵,使用成本高。
扭矩-转角法的使用要求条件:
a 足够的螺纹夹持长度(至少6颗牙,并且为螺栓直径1倍以上);
b 足够的内螺纹强度,使螺栓拧紧失效的形式为断裂而不是滑牙;
c 连接副摩擦系数的稳定性较好;
d 被连接件的过孔公差以及刚度一致性较好;
e 拧紧设备的控制精度较好;
f 连接副过屈服后至断裂需要较长的转角;
g 拧紧过程中不宜出现粘滑现象。
06 底盘常用紧固件类型和技术要点
套管连接类
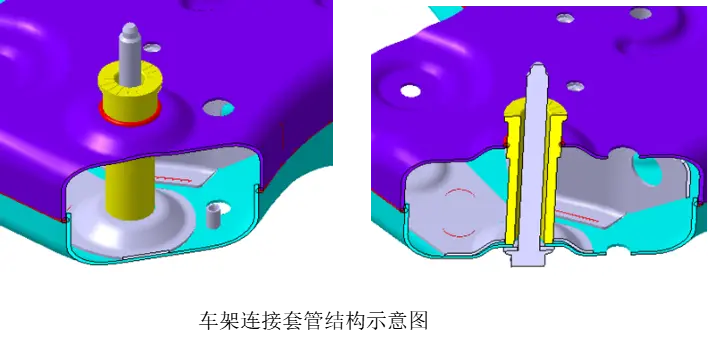
冲压板材副车架与车身紧固时,由于副车架上下板材间距较大,一般在副车架两层板材之间增加一个套管支撑。
设计时需要注意:
a)焊接套管需要注意焊缝的清理,不能有影响贴合的多余焊渣存在;
b)副车架与套管的连接点需要足够大的支承面,保证紧固件完全贴合到副车架上;
c)套管应有足够的强度和刚度。
U型连接类
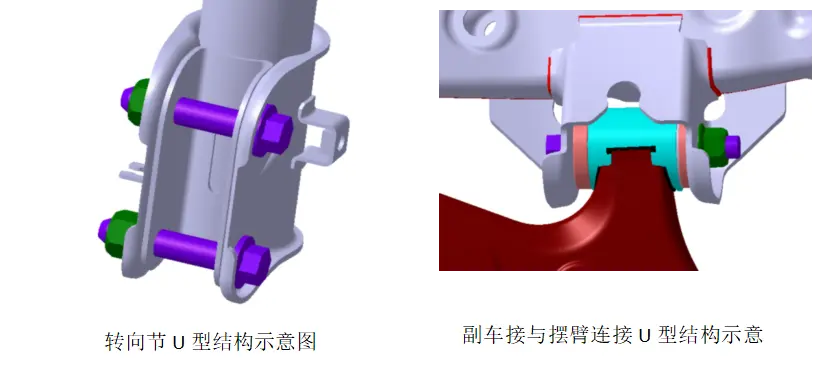
典型的U型连接包括减振器与转向节连接点、铸造型副车架与摆臂连接点。这类连接由于受到冲压后整形的影响,很容易导致U型开口的尺寸不一致,需要消除的间隙较大。
设计时需要注意:
a)保证U型开口尺寸的一致性;
b) 设计紧固件时最好考虑到采用扭矩-转角法,以消除间隙的影响;
c)注意电泳层对摩擦系数的影响,并注意是否存在粘滑现象;
d)设定安装扭矩时注意拧紧过程动态曲线是否存在屈服现象;
f)在安装动态曲线图上注意连接间隙是否消除。
板材连接类
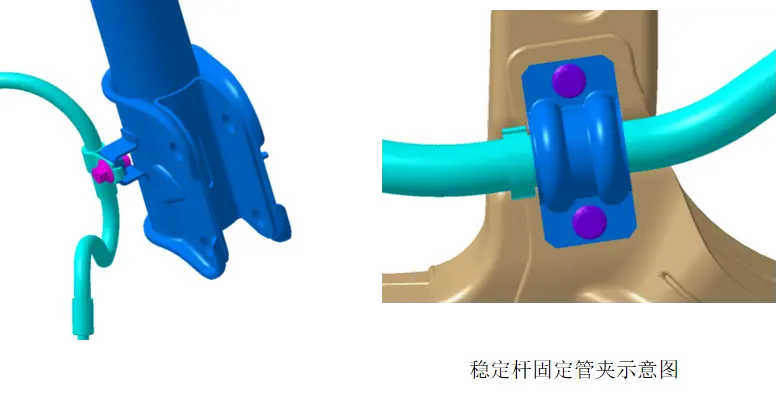
底盘上的板材连接类型较少,但要注意以下设计要点:
a) 对板材厚度 t 和螺栓的肩距 a 的配合尺寸要满足夹紧厚度的要求;
b) 需要足够的支承面,保证紧固件与被连接件完全接触。
-
京东工业发布汽车等九大行业场景采购解决方案手
2025-08-26 -
京东集团与东风汽车达成战略合作 打造汽车行业
2025-08-15 -
助力汽车零部件产线智能化升级,西门子Xcelerat
2025-06-27 -
BBA集体转向!放弃全面电动化
2025-06-26
编辑推荐
最新资讯
-
京东工业发布汽车等九大行业场景采购
2025-08-26 18:11
-
制造现场推动节能革新,电装稳步迈向
2025-08-25 14:04
-
携手共赴“智”造未来!埃马克推动大
2025-08-22 19:41
-
伦福德机脚-汽车平稳行驶的守护者
2025-08-19 16:38
-
比亚迪叉车:新能源时代的绿色智能引
2025-08-19 14:37