同轴式电驱桥的轻量化设计
2019-05-12 18:19:20· 来源:EDC电驱未来
现在新能源汽车的电驱动桥基本都是在燃油车车桥的基础上额外增置驱动电机。由于电机偏置会导致驱动桥钢板座承受额外的倾覆力矩,进而引起车身振动,降低驾驶舒适性。针对电驱动桥电机偏置问题,有人提出了双转子电动机电驱动桥设计,在保
现在新能源汽车的电驱动桥基本都是在燃油车车桥的基础上额外增置驱动电机。由于电机偏置会导致驱动桥钢板座承受额外的倾覆力矩,进而引起车身振动,降低驾驶舒适性。针对电驱动桥电机偏置问题,有人提出了双转子电动机电驱动桥设计,在保证汽车动力性的前提下有效避免了非同轴布置产生的问题,但是双转子电动机电驱动桥造价昂贵、控制复杂且非同轴。因此,新能源汽车电驱动桥的同轴设计非常重要。同时,如何在满足汽车使用性能的要求下,实现电驱动桥的轻量化设计,降低簧下质量提高乘坐舒适性,是亟需解决的另一难题。
针对电驱动桥非同轴问题、为减少环境污染,笔者提出一种纯电动汽车同轴一体化电驱动桥结构,建立其有限元模型进行强度、刚度以及性能分析;根据仿真分析结果,实现了电驱动桥的轻量化设计。
1 电驱动桥结构设计及其有限元模型
1.1纯电动汽车电驱动桥结构设计
为了克服电机悬挂所产生倾覆力矩的影响,提出一种同轴一体化电驱动桥结构,其结构原理图如图 1所示。
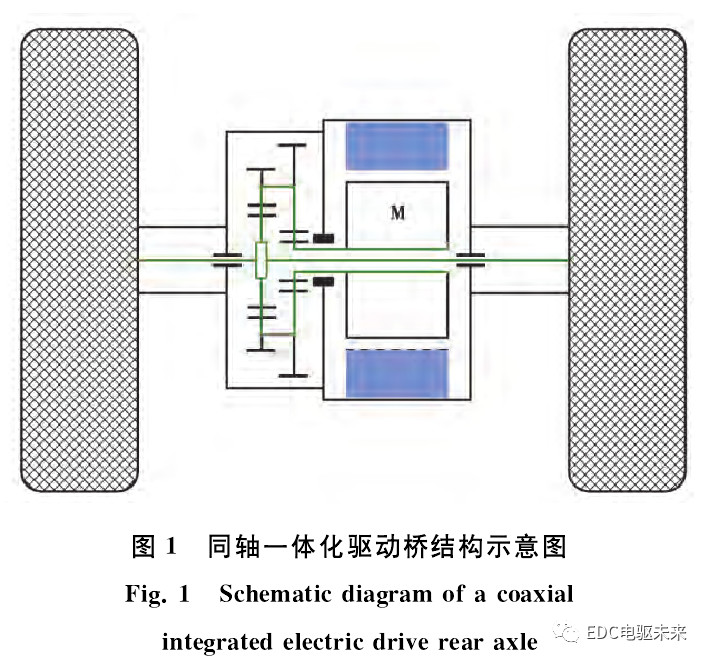
该电驱动桥采取同轴式结构,主要由电机、二级减速器、差速器和半轴组成,电机输出轴通过花键带动减速器的输入轴旋转,经两级齿轮减速后将动力传递给差速器,而半轴穿过空心电机轴插入差速器,最后动力经半轴输出到车轮。
1.2 电驱桥有限元模型
建立电驱动桥桥壳有限元模型,如图2所示。
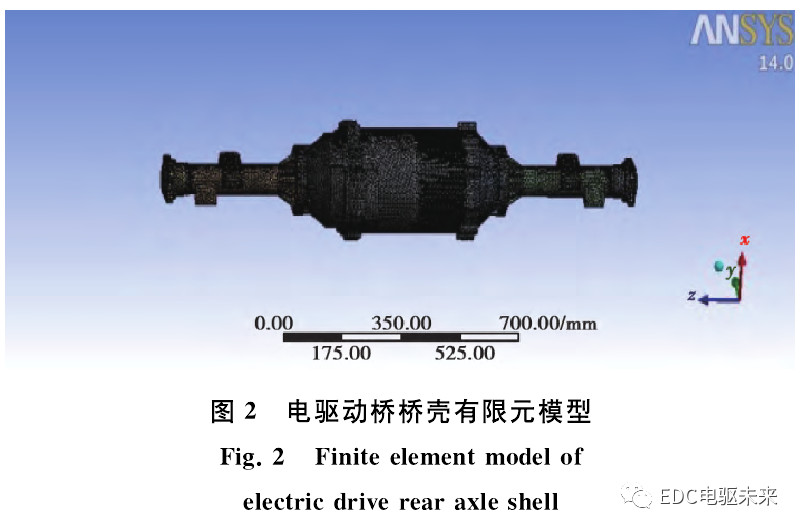
电动汽车一体化电动桥壳的主要参数为满轴载荷1.9t,轮距1490mm,板簧距1016mm。材料设定为40Cr,将桥壳进行调质处理,处理后的40Cr参数如表1所示。
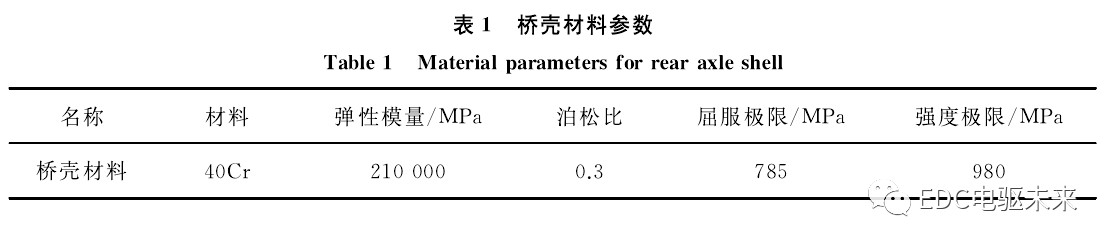
某电动商用车基本参数及驱动系统参数如表2所示。
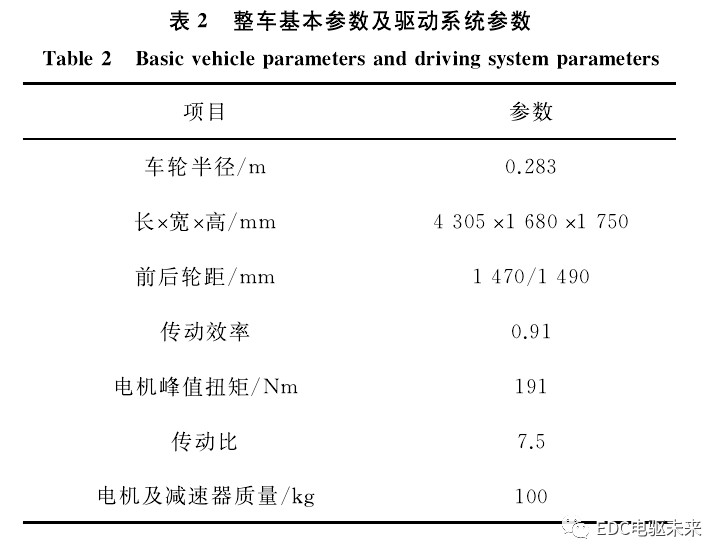
2 同轴一体化电驱桥极限工况分析
汽车实际受力情况较为复杂,按最大冲击工况、最大驱动力工况、紧急制动工况以及最大侧向力工况进行分析。如电动汽车在上述4种极限工况下驱动后桥桥壳达到强度刚度使用条件,则可以确定驱动桥满足电动汽车实际使用要求。
2.1 最大冲击工况下的桥壳强度刚度分析
当汽车满载行驶在不平路面受冲击载荷的极限工况下时,桥壳除承受汽车自身的满载重力G、驱动电机和减速器重力G1作用外,还需承受冲击载荷的作用。
弹簧钢板座处受垂直力为:
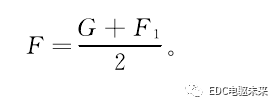
其中弹簧钢板座处的冲击载荷为:
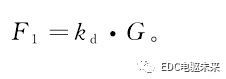
电机与减速器在冲击作用下的总载荷为:
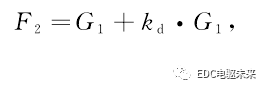
式中kd为动载荷系数。
桥壳不平路面冲击载荷约束如图3所示。加载载荷:在弹簧座处施加3.213kN垂直力;在电机及减速器重心位置施加2.45kN力。约束条件:约束一体化桥壳一端x、y、z 方向的移动及x、y 方向的转动,另一端约束x、y 方向的移动及x、y 方向的转动。
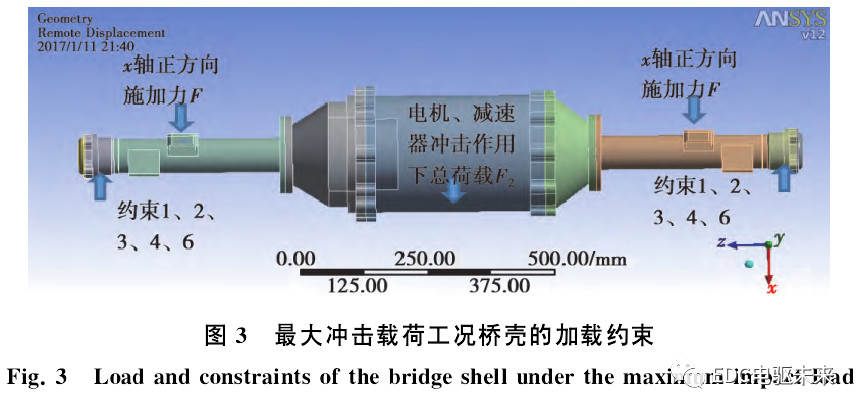
将不平路面冲击下的边界仿真载荷施加在图2所示的有限元模型上,得到的等效应力云图如图4所示,
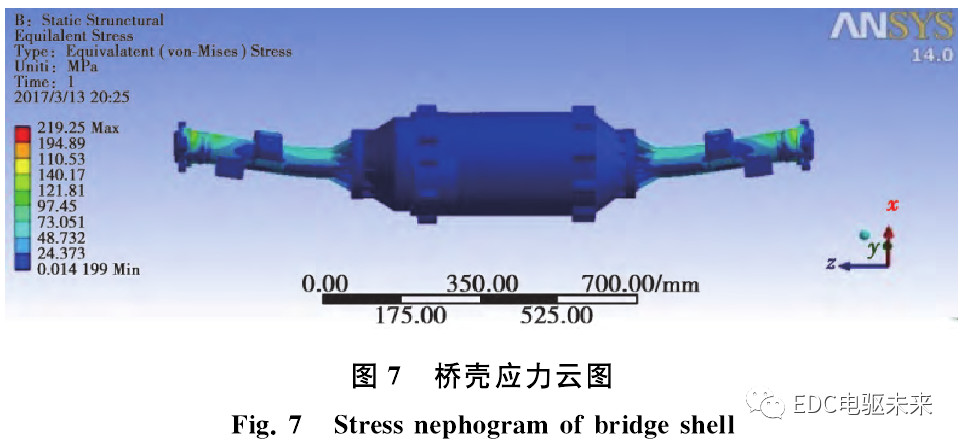
等效位移云图如图5所示。
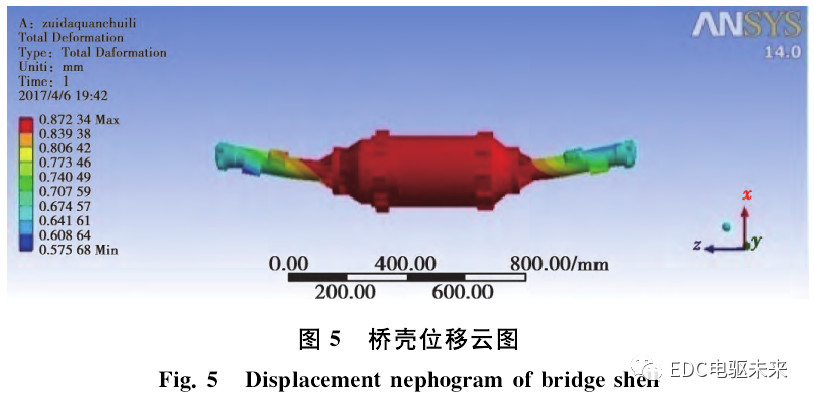
由图4可知,驱动桥桥壳最大应力位于半轴套管约束处,最大应力234.22MPa,小于40Cr的屈服强度785MPa。因此,驱动桥满足强度要求。
由图5可知,驱 动 桥 桥 壳 的 位 移 较 大 区 域 位 于 两 板 簧 座 之 间 区 域 的 电 机 和 减 速 部 分。最 大 变 形 量0.872mm,位于中间电 机 和 减速 器 连 接 的 区 域。每 米 轮 距 变 形 量 0.585mm/m,小 于 国 家 标 准 规 定 值1.5mm/m。因此,该驱动桥满足刚度要求。
2.2 最大驱动力工况下的桥壳强度刚度分析
当汽车满载以最大驱动力行驶时,桥壳除承受汽车自身的满载重力 G、驱动电机和减速器重力 G1作用外,还要承受电机驱动力对桥壳的反扭矩作用。
弹簧钢板座处受垂直力为:
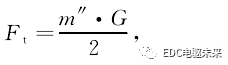
式中 m″为车桥载荷转移系数。
单侧所受旋转反扭矩为:
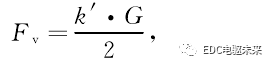
式中:Tmax为驱动电机最大输出扭矩;i为驱动后桥减速器传动比;ηT为后桥传动系统效率。桥壳最大驱动力工况下的载荷约束如图6所示,
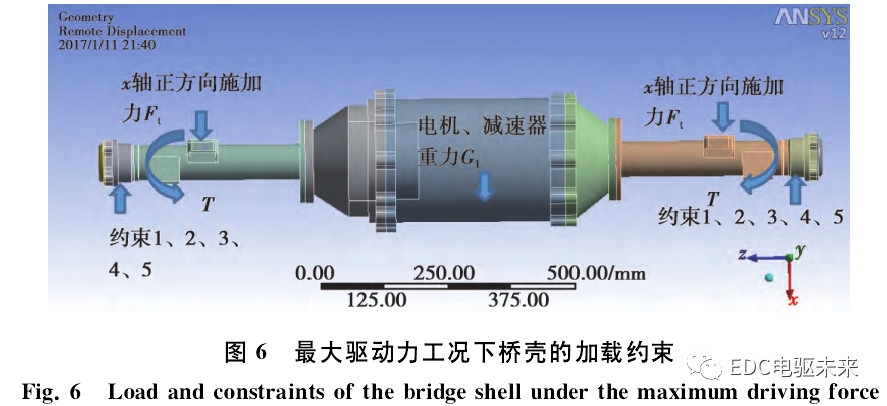
加载载荷:在弹簧座处施加22.285kN 垂直力;在电机和减速器重心位置施加0.98kN 力;在弹簧座处施加807.225Nm 扭矩。约束条件:约束桥壳两端x、y、z 方向的移动及y、z 方向转动。
等效应力云图如图7所示,等效位移云图如图8所示。
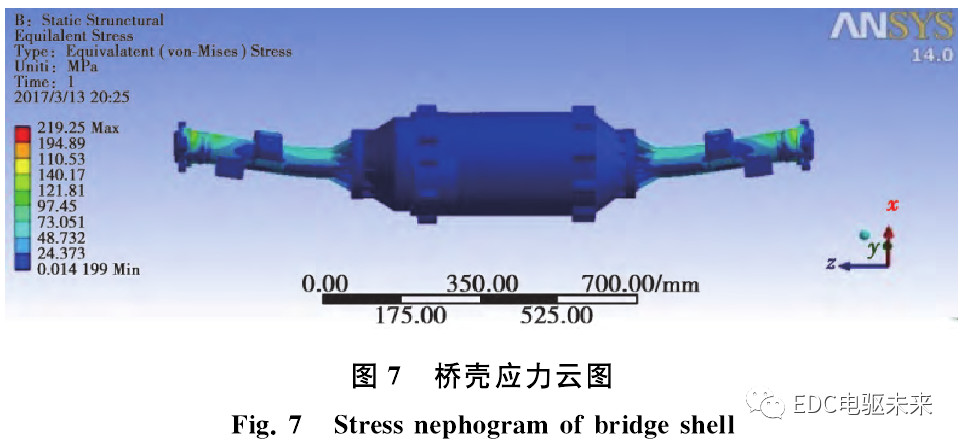
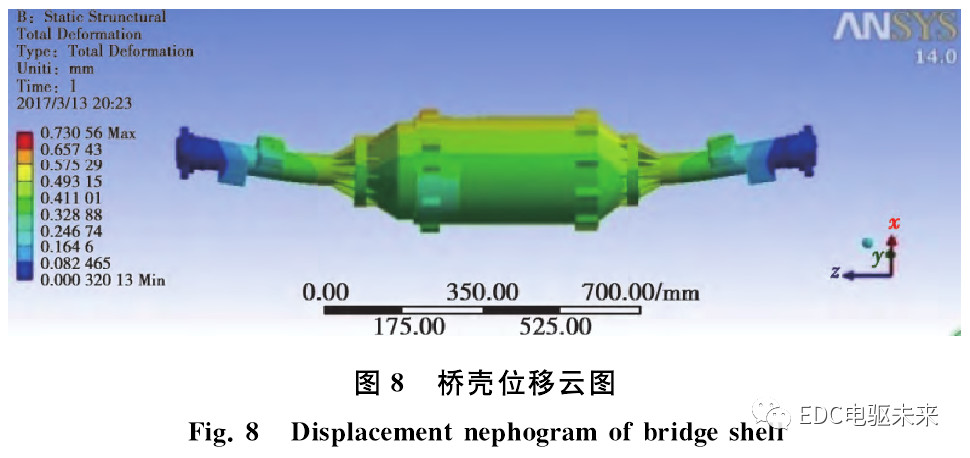
由图7可知,驱动桥桥壳最大应力位于半轴套管约束处,最大应力219.25MPa,满足强度要求。
由图8可知,桥壳最大变形量0.739mm,位于左板簧座和凸包之间的区域;每米轮距变形量0.496mm/m,满足刚度要求。
2.3 紧急制动工况下的桥壳强度刚度分析
当汽车满载处于紧急制动极限工况时,桥壳除承受汽车自身的满载重力 G、驱动电机和减速器重力 G1作用外,还要承受地面对车轮的制动力矩。
弹簧钢板座处受垂直力为:
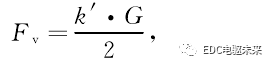
式中k′ 为汽车制动时的质量转移系数。
制动力矩为:

式中:φ为车轮与地面间的附着系数,r 为驱动车轮的滚动半径。 桥壳紧急制动载荷约束如图9所示。加载载荷:在弹簧座处施加6.964kN 垂直力;在电机及减速器重心位置施加0.98kN 力;在弹簧座处施加1970.8Nm 制动力矩。约束条件:约束桥壳两端x、y、z 方向移动及y、z 方向的转动。
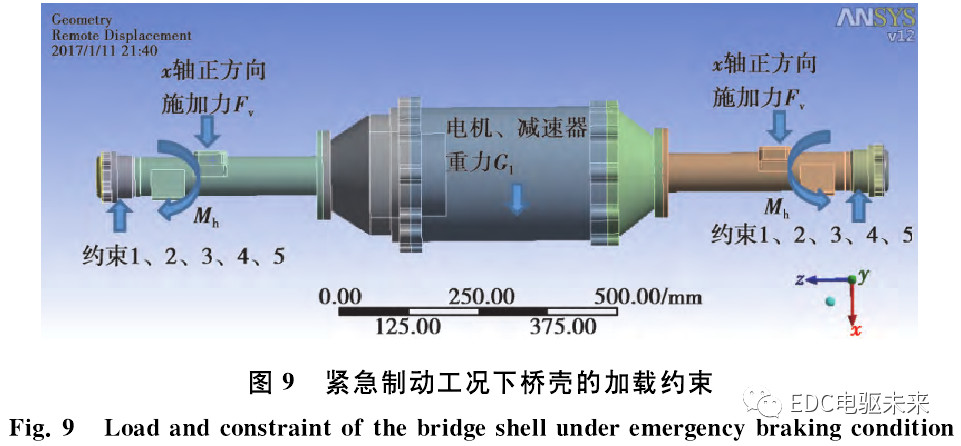
对应得到的等效应力云图如图10所示,等效位移云图如图11所示。
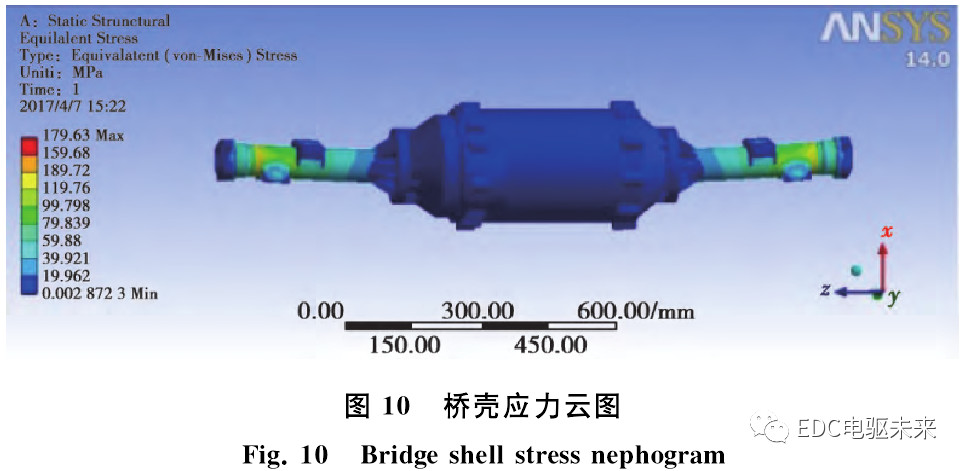
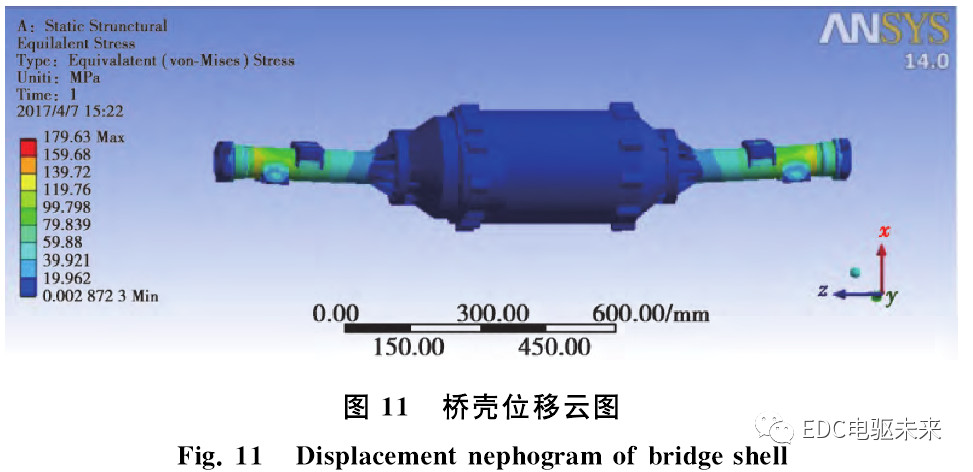
由图10可知,驱动桥桥壳最大应力位于半轴套管约束处,最大应力179.4MPa,满足强度要求。
由图11 可 知,桥 壳 最 大 变 形 量 为0.901mm,位 于 在 左 板 簧 座 和 凸 包 之 间;每 米 轮 距 变 形 量 为0.605mm/m,满足刚度要求。
2.4 最大侧向力工况下的桥壳强度刚度分析
当汽车处于最大侧向力极限工况时,桥壳除承受汽车自身的满轴载荷 G、驱动电机和减速器重力 G1作用外,还要承受侧向力 P。
汽车驱动桥的侧滑条件为汽车承受的侧向力大于等于轮胎的侧向附着力,即:

式中:P 为汽车桥所受的侧向力,此时最大侧向力 P=G·φ;YL、YR分别为地面给左右驱动车轮的侧向反作用力。
假设汽车右侧滑移时,左、右驱动车轮的支撑反力分别为

式中:H 为汽车满轴载荷时的质心高度;B 为汽车驱动车轮轮距。

桥壳最大侧向力工况下的载荷约束如图12所示。加载载荷:在右侧弹簧座处施加18.571kN 垂直支撑反力;在电机及减速器重心位置施加0.98kN 力;在右侧弹簧座处施加18.571kN 右侧向力。约束条件:约束桥壳一端x、y、z 方向的平动及z 方向的转动,另一端约束x、y 方向的平动及z 方向的转动。
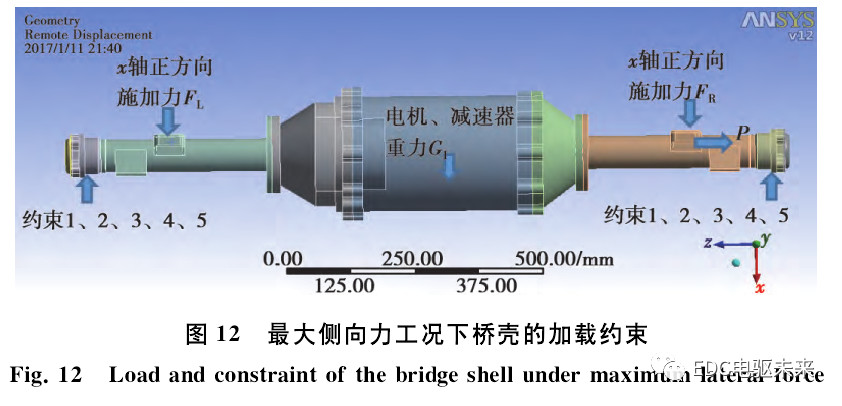
将最大侧向力工况下的载荷及约束边界条件施加到驱动桥桥壳上,获得等效应力云图如图13所示,等效位移云图如图14所示。
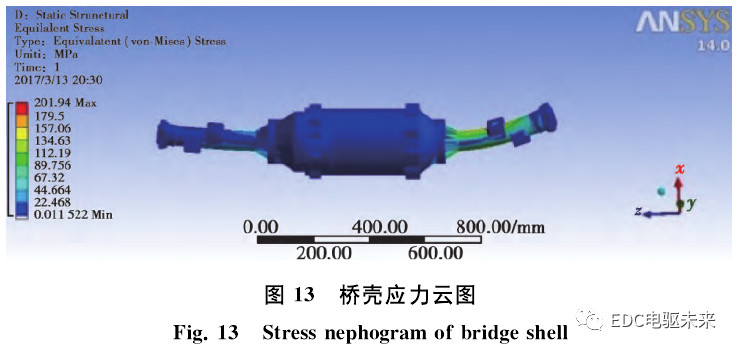
由图13可知,桥壳最大应力位于轴套管约束处,最大应力201.9MPa,满足强度要求。
由图14可知,驱动桥桥壳的最大变形量1.2469mm,位于左板簧座和凸包之间的区域。每米轮距变形量0.837mm/m,满足刚度要求。
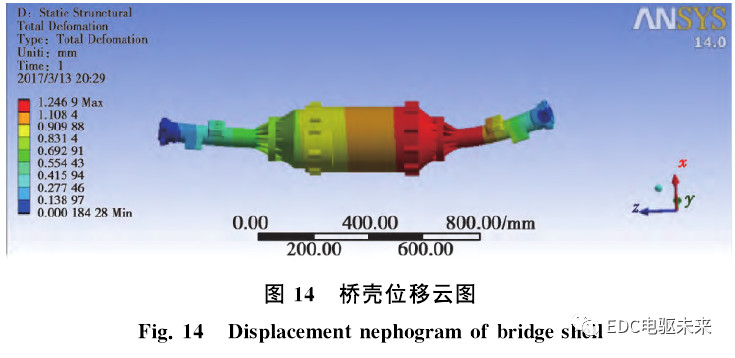
未完,待续
声明:本平台只提供分享和交流不作商业用途,如侵权请及时联系我们删除!
- 下一篇:延锋获北京奔驰优秀供应商特别大奖
- 上一篇:汽车前轴万吨自动化锻造生产线
举报 0
收藏 0
分享 147
-
高温季行车安全需重视:TRW SPS 制动盘让你的刹
2025-07-19 -
跨越速运凭什么“圈粉”万千客户?“中国零担30
2025-07-01 -
驭动未来,智启新程-采埃孚油护新出行
2025-06-25 -
旭化成荣获2025年度发明表彰,助力离子交换膜法
2025-06-11
编辑推荐
最新资讯
-
携手共赴“智”造未来!埃马克推动大
2025-08-27 18:12
-
京东工业发布汽车等九大行业场景采购
2025-08-26 18:11
-
制造现场推动节能革新,电装稳步迈向
2025-08-25 14:04
-
携手共赴“智”造未来!埃马克推动大
2025-08-22 19:41
-
伦福德机脚-汽车平稳行驶的守护者
2025-08-19 16:38