反T形类型材零件的拉弯成形工艺研究
2019-03-04 16:12:09· 来源:钣金与制作 作者:马永明
型材拉弯成形工艺在航空、航天以及汽车、高铁上的型材弯曲件的制造中得到了非常广泛的应用。在民用(航空、高铁等)领域,很多骨架零件都采用了型材框。因此,拉弯技术的研究对提高拉弯件的质量和加速拉弯件的国产化进程有着十分重要的意义
型材拉弯成形工艺在航空、航天以及汽车、高铁上的型材弯曲件的制造中得到了非常广泛的应用。在民用(航空、高铁等)领域,很多骨架零件都采用了型材框。因此,拉弯技术的研究对提高拉弯件的质量和加速拉弯件的国产化进程有着十分重要的意义。
采用拉弯工艺可以使零件获得合理的校形余量,提高零件的制造精度,降低零件的制造成本。拉弯是指型材在弯矩和纵向拉力的联合作用下压入模具型槽内的成形过程。拉弯在工业生产中是一种重要的成形工艺,用于制造尺寸大、外形准确度要求较高、相对弯曲半径大的变曲率挤压和板弯型材弯曲件。
型材拉弯具有如下工艺特点:
⑴能成形空间结构复杂的型材零件;⑵能成形屈强比大的型材弯曲零件;⑶具有不同工艺方法相结合的综合成形特点;⑷弯曲精度高,回弹小;⑸具有柔性制造的特点。
拉弯零件的最后形状与加载参数、拉弯模具和型材形状参数、型材材料参数、摩擦系数等众多因素有关,而且非常复杂。
需要研究的零件基本信息
零件材料为7A09M;型材标准为DQ5417/GJB 2507A-2015;零件外形为半圆,外半径为:R1673mm;零件图如图1所示。
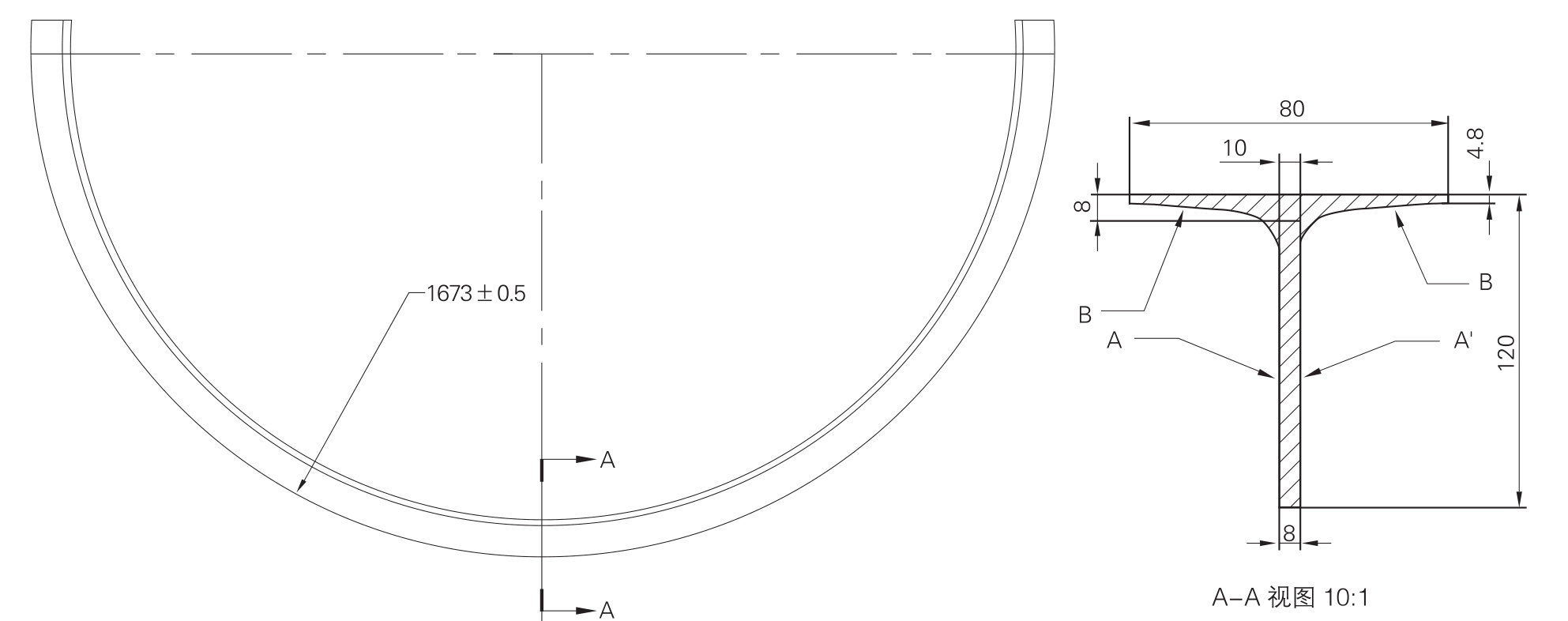
图1 零件图
工艺流程设计
工艺流程图
主要的工艺流程如图2所示。

图2 工艺流程图
主要加工流程的介绍
⑴来料检查。按要求检查型材截面尺寸,型材平直度,毛坯长度,表面质量,特别注意是否有表面缺陷。
⑵铣切加工。对于反T形框,型材截面在拉弯前需要铣切,为了确保拉弯后的尺寸符合要求,我们在龙门铣机床上进行铣切加工,加工尺寸到名义值+2mm。
⑶预拉弯。在拉弯机上,利用拉弯模及拉弯夹头,通过控制拉弯参数(拉弯力、拉弯包角等)对毛坯进行预拉弯以达到预成形的要求。
⑷修整。检查两个面的平面度、角度,确保这些值符合要求,对于R值,可以利用三辊滚弯机辅助修整,修整到我们预定的外形即可。
⑸预拉弯后的检验。检验两个面的平面度、角度、截面的宽度等符合要求,对于R1000mm值达到我们预定的外形。
⑹淬火后的运输保存。为了保证铝合金材料的新淬火状态,淬火后成形前,需要把零件放入低于-10℃的温度中保存,在热处理出来以后,先放入冷库保存,运输时,用冷藏车运输,冷藏车的温度要低于-10℃。
⑺补拉弯。在拉弯机上,利用拉弯模及拉弯夹头,通过控制拉弯参数(拉弯力、拉弯包角等)对半成品进行再拉弯以达到最终要求;在补拉弯时,会根据不同零件的具体情况,选择性的进行边拉边修整以达到理想的外形和尺寸。
⑻修整。在校正平台上,用榔头等辅助工具进行修整,必要时,用校正检验模上进行敲修。
⑼检验。用检验模配合卡尺,塞尺进行检验,确保符合客户技术要求及图纸要求。
⑽钳工。用百洁布等打磨工具对表面进行修饰清理,零件及试片打标,确保可追溯性。
工艺技术难点分析
成形后零件底面平面度、弧度及立边角度要求均较小,拉弯直径的圆度为1mm,反T形类型材的面与面之间间隙≯1.5mm。在拉弯过程中,回弹是零件成形精度最主要的影响因素,因立边较高、底面较宽,而且厚度都是变截面,因此零件的平面度和角度也很难控制,很难手工修整。
主要技术难点
⑴拉弯成形模的设计。
1)拉弯模理论外形的确定;2)材料流动不顺畅;3)零件产生扭曲变形;4)零件和模具的润滑;5)反T形类型材在成形时,120mm高度的这个面很容易产生失稳现象,这严重影响产品的质量和生产效率(其他截面零件该现象比较轻微,对产品影响不明显)。
⑵工艺参数的确定。1)预拉和补拉后的外形无法满足要求;2)材料被拉断。
⑶人工校形。由于型材截面比较大,圆弧直径也很大,对于手工成形的难度非常大。
主要技术难点的解决方案
⑴拉弯成形模的设计。
1)拉弯模修回弹(零件要求是等曲率的圆弧,我们把拉弯模外形近似修正为椭圆,长轴为原零件外形半径,短轴在半径的基础上缩0.2%~0.3%);
2)调整模具表面粗糙度到0.8μm;
3)调整合理的模具间隙到0.2~0.3mm;
4)提高拉弯夹头的对称性;
5)零件和模具的润滑。在零件表面均匀涂机油,在模具表面均匀涂黄油的方法,我公司采用两种润滑方式进行试验。①在零件和模具表面均匀涂机油润滑。该润滑方式适用于一般零件成形,但是在此零件的加工过程中,因与模具接触的面积也大,摩擦系数也大,不能起到很好的润滑效果。在试验中发现,由于润滑效果不好,型材与模具之间摩擦力大,拉力不易传递到中间截面,这导致钳口处材料所受的拉力与中间截面不一致,钳口处的材料截面变形严重,不符合制造要求。②在零件表面均匀涂机油,在模具表面均匀涂黄油。该润滑方式有利于力的传递,零件成形后的截面均匀性较好,回弹量有所减小。在难加工复杂零件的成形过程中一般采用这种方法进行润滑;
6)为了确保反T形框产品能符合要求,我们在拉弯模上配置了聚氨酯垫块,垫块宽度在50~100mm之间,用钢丝连起来并确保和工件一起运动,垫块示意图如图3所示。
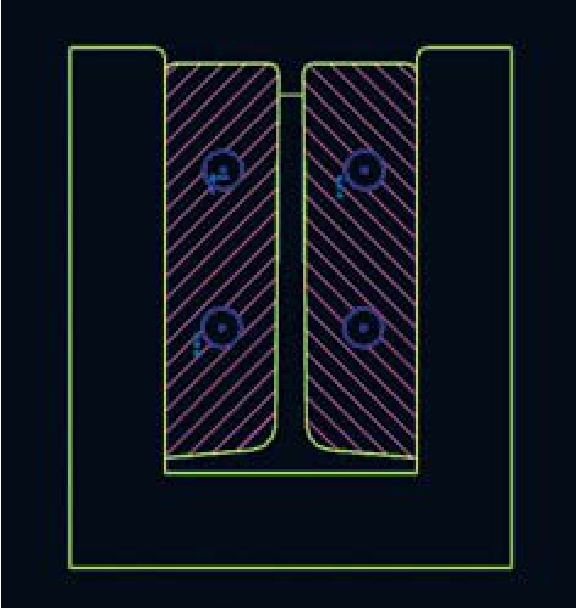
图3 聚氨酯垫块示意图
⑵工艺参数。
1)预拉时参数的确定(预拉力、预拉包角和预拉量);2)补拉时的参数的确定(补拉力、补拉包角和补拉量);3)通过理论计算和实践相结合的方法,总结出各框的参数值。
⑶人工修形。1)淬火后,再拉弯前需要增加人工修形,确保零件能顺利进入拉弯模;2)淬火后,为了确保材料的塑性,便于成形,要在2小时内成形;3)招聘有经验的钣金师傅指导并培训工人。
工艺装备
成形工装
拉弯成形设备采用双臂式型材拉弯机,如图4所示。拉弯机主要参数如下:双臂式,拉力为130t,双臂最大长度9000mm,最小长度3500mm;该设备可以用于冷拉成形铝合金、碳钢、低合金钢等型材,在拉力作用下,将直条状工件通过组合拉伸动作,使其在长度方向上发生弯曲,并贴合模具以达到所需形状。可以实现型材的力控制或者位移控制以实现拉弯成形。本批试验件我们采用力控+位移控制模式成形零件,在预拉及补拉包角时采用力控模式,在补拉时采用位移控制模式。
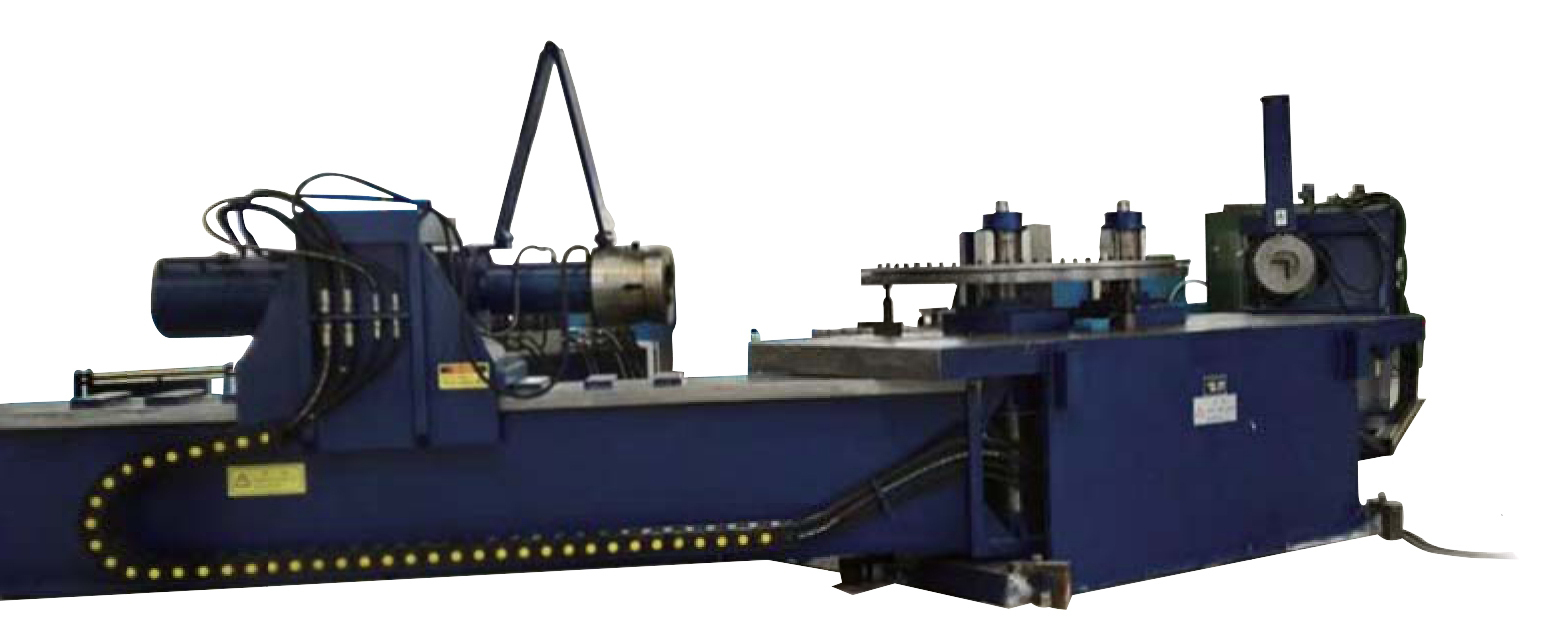
图4 典型双臂式型材拉弯机
具体拉弯操作过程如下:
拉弯模放在拉弯机的平台上,平台上有两个约200mm的柱子,拉弯模中对应加工出两个相对应的孔,利用柱子定位拉弯模,张臂式拉弯机有两个夹头,用来夹持需要拉弯的工件或者毛坯,拉弯时,先夹持毛坯两头,再慢慢绕着拉弯模具开始拉弯动作,直到毛坯包住拉弯模到我们期望的外形为止,在拉弯时,要确保型材能顺利进入拉弯模。
针对每一类型材,我们分别根据图纸要求单独设计和制造拉弯模,拉弯模具示意图如图5所示。

图5 拉弯模具示意图
检验工装
针对此类零件,我们采用检验工装和样板配合常规检验仪器来执行检验工作,常规仪器为千分尺、卡尺、塞尺、等高块等。
检验模主要用于检验下列关键尺寸:⑴面与面,以及面与模胎的贴合间隙;⑵两个贴合零件之间的贴合面间隙;⑶自由状态下Ф3346mm的圆度;⑷竖直边垂直度。
工艺技术参数
理论计算得到的拉力和补拉量只能作为参考,实际拉力与计算值有较大出入,需在试拉过程中加以调整。⑴在零件表面均匀涂机油、在模具表面均匀涂黄油的方法较好,该方法有利于力的传递,零件成形后的均匀性较好。⑵预拉力在一定的范围内增大能较好地控制零件的回弹,提高成形精度。增大预拉力,回弹量减小,但减小幅度随着预拉伸力的增加而变小。⑶补拉量对零件的回弹及平面度有影响,补拉量在一定范围内的增大,使零件贴胎效果好,且平面度较好。同样,补拉量大,需要较大的拉力,也会造成零件截面畸变,影响后续加工。
综上,拉弯参数(拉弯速率,变形量等)分别如下:
预拉力设定为430kN,预拉包角为26°;补拉力为510kN,补拉包角为-5°,补拉量为45mm的工艺参数;同时,拉弯时原材料毛坯不能小于5900mm,力学试片尺寸150mm ,分别在每一个零件直线段取制。
鉴定试验过程和验证结果
试制过程中常出现的问题及解决措施,见表1。
表1 试制中出现的问题及解决措施

尺寸精度检测方法:我们是用外形样板配合塞尺来检测R1673的弧度;对于面与面以及面与模胎的贴合间隙我们是用等高块配合塞尺来进行测量,如图6所示。
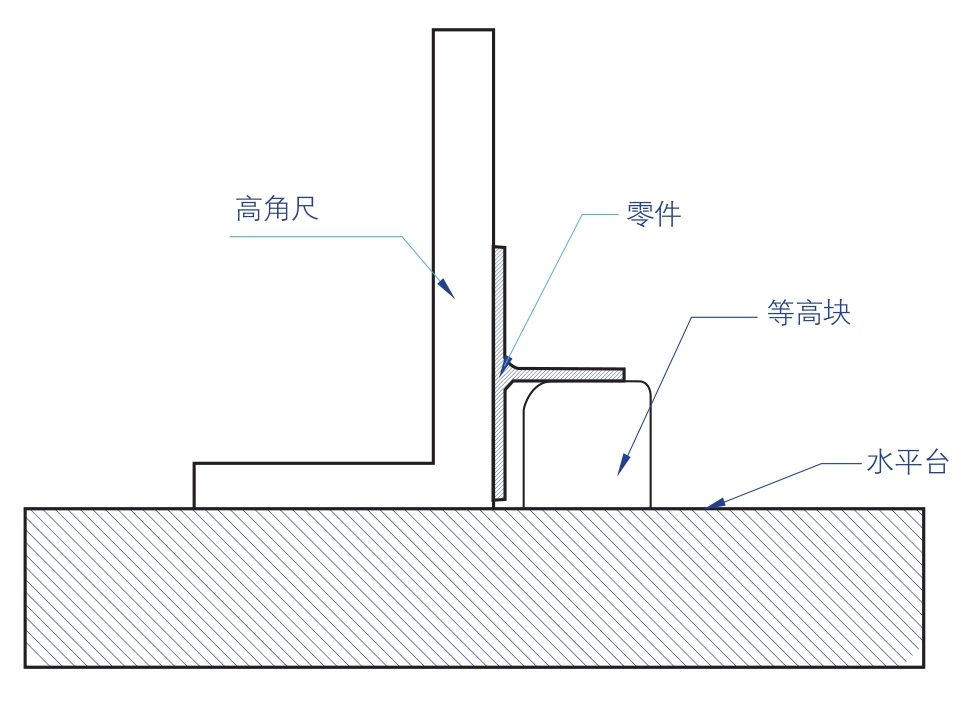
图6 等高块工作原理示意图
尺寸精度对比:与国内某大型航空制造公司的产品进行比对,结果如表2所示。
从表2可以看出,以上四种框环平面度、垂直度尺寸、R间隙,我们均优于大型航空制造型企业;尽管有部分尺寸超差,但是经最终客户确认,可以满足装配要求。
表2 尺寸精度对比表(单位:mm)

结束语
我公司经过工艺试制分别得出了工艺方法,工艺参数等,形成了一套完整的工艺文件,工艺方法,制定了检验方法以及设计并制造了工装和检验样块/板,产品性能指标,尺寸数据基本满足设计要求,同时也得出了各型材框的拉弯参数和回弹等工艺参数;截止到2018年年底,我们已经生产出合格零件86件,而且试制时超差的部分尺寸经过后面的改善,也全部合格。
由此可以证明,我们的研究成果是可以指导生产的,而且对同类反向拉弯件有很大的借鉴意义,此套工艺方案具有推广运用的价值。
——节选自《钣金与制作》2019年第2期
举报 0
收藏 0
分享 123
-
乘用车金属冲压
2025-05-29 -
冲压技术在电机叠片制造的应用
2024-09-06 -
车身零部件包边质量控制要点
2024-09-05 -
轻量化技术——热汽胀形工艺技术解析
2024-09-04
最新资讯
-
辐射亚太,链接全球——采埃孚再制造
2025-07-30 11:46
-
思看科技发布子品牌SCANOLOGY,全球
2025-07-30 11:06
-
风雨不动安如山——比亚迪叉车构筑“
2025-07-30 08:48
-
NEAS CHINA 新能源汽车技术与生态链
2025-07-29 09:52
-
三维扫描革新碾磨机辊套检测,效率与
2025-07-25 10:46