碳纤维复合材料车门多位一体研发技术
2019-02-14 17:16:44· 来源:Fiberbook波客复材产品正向研发
摘要:当前,新能源技术、轻量化技术和智能网联技术是引领汽车行业发展和技术革新的三大方向,碳纤维复合材料以其质轻高强的性能成为汽车轻量化技术领域的翘楚。由于碳纤维复合材料的特殊性和复杂性,本文从材料选择,结构设计与优化,铺
摘要:当前,新能源技术、轻量化技术和智能网联技术是引领汽车行业发展和技术革新的三大方向,碳纤维复合材料以其质轻高强的性能成为汽车轻量化技术领域的翘楚。由于碳纤维复合材料的特殊性和复杂性,本文从材料选择,结构设计与优化,铺层设计与优化,装配连接设计,仿真分析,工艺成型等多方位、全流程地探索碳纤维复合材料车门的研发技术,以实现车门结构的轻量化、集成化和模块化。
1 引言
轻量化技术作为新能源汽车的核心技术之一,是实现节能减排、绿色发展,以及促进汽车行业共赢的必经之路,目前已经成为世界汽车发展的潮流和趋势。实现汽车轻量化最直接、最有效的方式是使用轻量化材料。碳纤维复合材料(CFRP)具有高强度、高刚度、高断裂韧性、耐腐蚀、高阻尼等特点,可大幅减轻整车重量,减重比达50%-60%,同时大幅提高汽车服役寿命、燃油效率和安全舒适性,已被公认为汽车工业领域最理想的轻量化材料。
本文基于等刚度原则,以原金属钢制车门的性能指标为参考,通过对车门的多方位、全流程解析,提出了碳纤维复合材料车门设计的几种新思路和方法,充分发挥了复合材料的可设计性和多功能性,结合公司多个项目的设计经验,实现了碳纤维复合材料车门从理论到实践的演化,为汽车轻量化的发展提供参考方向。
2 材料选择与测试
根据零件的使用性能、安全耐久和受载情况等因素需要选择合适的材料来成型制造汽车复材制品。针对汽车行业碳纤维的性能要求,按碳纤维强度级别分常用的有T300、T700级;按中间材料形式有预浸料、织物、单向带、多轴向编织布等;按丝束大小有3K,6K,12K,18k,24K,48K等;按典型树脂类型有环氧树脂、聚氨酯、双马树脂、酚醛树脂、聚酰亚胺树脂等;以上材料成分和材料形式的选择都需要综合考虑外观,使用环境,性能,成本,工艺等诸多因素。
本文研究的车门选择T300级别,丝束3K的双轴向碳纤维织物增强环氧树脂基预浸料。
3 结构设计与优化
3.1模型简化设计
由于复合材料的成型是多层预浸料铺叠加压固化而成,因此在复合材料结构设计时必须考虑到纤维铺覆的工艺性,即尽可能使转角过渡平滑,减少加强筋、加强槽等特征。因此,在获得车门金属数据模型和设计硬点信息后,首先需要对模型进行简化处理,去除或减少用于增加刚度的加强槽和加强筋,处理转折区及圆角处的过渡。
车门内板的金属模型和简化处理后的复材模型结构如图3.1所示。
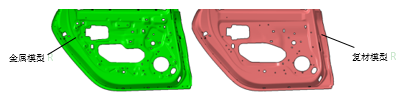
图3.1车门内板金属模型和复材模型
层压结构的圆角半径与所选用材料的柔性、模具、层压件厚度等有关。最小圆角半径需与制造部门确定,圆角半径过小,会在拐角区域发生纤维拉断、架桥和树脂堆积等制造缺陷,因此,设计复合材料层压结构时,在拐角处应尽可能的给较大的半径,尽量避免形成尖锐的棱角。
车门内板圆角过渡处金属模型和处理后的复材模型如图3.2所示。

图3.2 车门内板圆角过渡处金属模型和复材模型
3.2集成化设计
传统金属车门结构一般包括外板、内板、窗框加强板、上下铰链加强板、锁加强板、限位器加强板、腰线加强板和防撞横梁等结构组件,一般钢制金属车门模型爆炸图如图3.3所示。
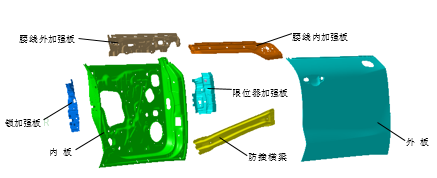
图3.3 金属车门总成模型爆炸图
复合材料的优势是可以将若干个零部件组合为整体成型,以大幅减少零件和紧固件数量,简化连接和装配,降低复合材料的制造成本,实现材料、功能、结构的一体化。
使用复合材料集成化设计可以将车门限位器加强板、锁加强板和铰链加强板集成到内板,在保证各项法规要求和性能指标的前提下,解决限位器的安装问题和运动校核,在限位器和铰链安装区域局部加厚,提高局部强度和刚度;还可以将防撞梁集成到车门外板,采用夹心结构的设计方式不但提高了外板的整体刚度,还减少了零件数量和装配成本。
防撞横梁集成到外板的碳纤维复合材料泡沫夹芯结构如图3.4所示。
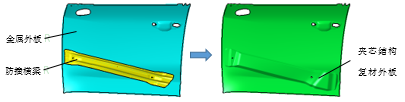
图3.4 金属车门方案与复材车门方案
4 铺层设计与优化
铺层设计是复合材料结构设计的关键,铺层设计的核心技术是如何将单层结构的优异性能传递到复合材料结构部件上,使铺层结构起到承上启下的作用。因此,复合材料铺层设计既要考虑到复合材料部件的受载情况和传力路径,还要注意复合材料成型的工艺难易程度。碳纤维复合材料结构设计的基本原则为:
a) 主应力原则:纤维取向应尽量与构件的主应力方向一致,充分发挥纤维的承载性能。
b) 对称均衡原则:对称均衡层合板可以避免各种耦合作用引起固化后的翘曲变形。
c) 铺层定向原则:一般多采用0°、90°和±45°等铺层方向,尽量减少铺层方向以简化设计和施工量,且任一铺层的最小比例≥10%。
d) 铺设顺序原则:同一铺层角的铺层尽量均匀分布,一般不超过4层,以防分层、开裂破坏。
在虚拟工艺铺覆过程中,需要对铺覆结果进行评估,铺覆性不好的地方应采取合理分块、更改铺层起始点,剪口,补片等设计手段对分块或者铺层原点进行优化,直至铺覆性分析完全通过。
本文中的碳纤维复合材料外板结构简单,外形流畅光顺,在所选预浸料布幅足够的情况下直接整体铺覆;内板结构较为复杂,为了满足预浸料铺覆的工艺性,需要分块铺覆。
基于西门子Fibersim复合材料设计软件,对外板和内板的各铺层方向织物的铺覆性进行了分析和优化,内板和外板工艺铺覆性良好,能够满足制造需要。车门外板铺覆性效果如图4.1所示,车门内板铺覆性效果如图4.2所示。
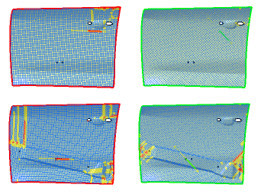
图4.1 车门外板铺覆性效果
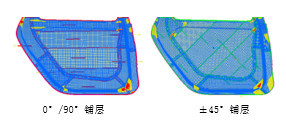
图4.2 车门内板铺覆性效果
铺层展开图用于复合材料车门的制造,导出数据可以直接作为自动裁布机可识别的信息。碳纤维复合材料车门内板0/90°方向铺层展开图如图4.3所示。
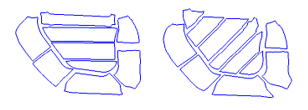
图4.3 车门内板铺层展开图
5 连接设计与装配
在复合材料连接设计技术中,一般需要考虑到结构件传递载荷的大小、连接部位的重要程度、被连接件的材料特性等因素,除此之外还要从环境状况、可检测性、可拆卸性及可修理性以及工艺性和制造成本等方面进行考虑。复合材料连接一般分为机械连接、胶接及混合连接。
5.1机械连接
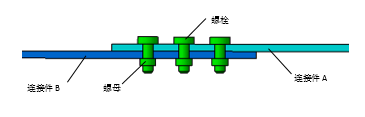
图5.1 机械连接示意图
5.2胶接连接
复合材料的胶接是指借助胶粘剂将零件连接成不可拆卸的整体,是一种较实用、有效的连接工艺技术,在复合材料结构连接中应用较普遍。胶粘连接接头的结构设计形式也是多种多样的,根据被粘物形状可分为平面搭接、角形搭接、T形粘接和管、棒形粘接等形式;根据材料的粘接方式又可分为对接、搭接、插接、阶梯搭接等等。胶接连接示意图如图5.2所示。
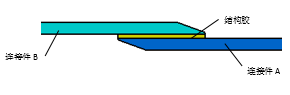
图5.2 胶接连接示意图
5.3混合连接
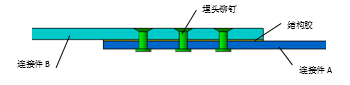
图5.3 混合连接示意图
6 工艺成型及加工处理
6.1工艺成型
先进树脂基复合材料的成型与制造技术基本上可分为两大类,即湿法成型和干法成型。
湿法成型常用的成型方法有树脂传递模塑成型(RTM)、真空辅助成型(VARI)等。
干法成型常用的成型方法有热压罐成型、模压成型等。对于大尺寸形状复杂、整体化程度高的制件,要用热压罐成型。而对于尺寸较小的高精度制件,通常用模压成型。
碳纤维复合材料成型工艺的选择是与原材料的选择同时进行的。本文研究的车门外板和内板均选用了预浸料,其成行方式随之也就确定为干法成型,考虑到其尺寸较大、安装面和安装孔精度要求较高,尤其是车门外板的表面质量要达到A级,内板结构复杂且为变厚度层压结构,因此,内板和外板均采用预浸料双面刚性模具模压成型。
6.2加工处理
复合材料固化成型之后还需要对其机加工处理,一般都需要钻孔,切边,打磨等,尤其是对于类似车门内外板这种结构复杂的复材制品,制孔数量多、难度大、精度高,加工耗时多,成本高。
碳纤维复合材料制品的机械加工通常分为传统加工和先进加工两类方法,传统机械加工方法基本上沿用了金属加工工艺和设备,先进复合材料加工方法大大提升了制品的加工质量和性能。传统加工方式不能满足加工质量要求,还可能对复材制品造成损伤,甚至破坏,先进加工方法设备昂贵,加工成本太高。
先进加工技术包括激光加工、高压水射流加工、超声波加工等技术。
7 结论
以上提到的碳纤维复合材料车门结构设计流程和技术已获得多个项目的实际验证,但是难免有不足之处,比如经济性、维修性和制造能力等因素成为汽车企业向碳纤维市场转移的障碍。随着碳纤维行业的不断发展和汽车轻量化技术的日益成熟,碳纤维复合材料在汽车行业的应用会更加广泛。
波客公司通过大量相关产品研发项目实践经验,总结出了碳纤维复合材料结构设计在汽车行业应用的基本流程,探索出了汽车轻量化设计的新思路、新技术,尤其是汽车覆盖件的复材化设计技术已经相当成熟,相对钢制金属覆盖件减重比超过50%,为多家国内汽车主机厂或研发中心提供技术咨询和服务。
参考文献
[1] 何天白,陈友汜,祝颖丹,唐涛, 《碳纤维复合材料轻量化技术》
[2] 常仕军,肖红,侯兆珂,董楹, 《飞机复合材料结构装配连接技术》
[3] 沈真,章怡宁,黎观生,李野, 《复合材料结构设计手册》
[4] 刘雄亚,晏石林, 《复合材料制品设计及应用》
举报 0
收藏 0
分享 132
-
高温季行车安全需重视:TRW SPS 制动盘让你的刹
2025-07-19 -
跨越速运凭什么“圈粉”万千客户?“中国零担30
2025-07-01 -
驭动未来,智启新程-采埃孚油护新出行
2025-06-25 -
旭化成荣获2025年度发明表彰,助力离子交换膜法
2025-06-11
编辑推荐
最新资讯
-
创新功率器件构建可持续未来 ——三
2025-09-04 15:57
-
旭化成为芬兰氢能项目提供集装箱式碱
2025-09-02 17:45
-
旭化成旗下宾霸品牌重磅亮相2025上海
2025-09-01 16:52
-
中国车企服务出海先行者:新央企新长
2025-08-29 16:13
-
携手共赴“智”造未来!埃马克推动大
2025-08-27 18:12