轮毂电机转向节轻量化设计
2019-01-07 22:18:13·
本文为技术邻Altair优化设计大赛投稿作品,作者为技术邻用户:煮雨煮粥摘要本报告使用Altair公司提供的HyperMesh软件以及OptiStruct的结构优化功能,对轮毂电机转向节进行优化设计。本文重点介绍了在汽车极限左转向工况下转向节的约束载
本文为技术邻·Altair优化设计大赛投稿作品,作者为技术邻用户:煮雨煮粥
摘要 本报告使用Altair公司提供的HyperMesh软件以及OptiStruct的结构优化功能,对轮毂电机转向节进行优化设计。本文重点介绍了在汽车极限左转向工况下转向节的约束载荷,以及结合制造工艺中最小成员尺寸约束进行拓扑优化,使其达到轻量化,且对于转向节的优化设计具有一定的参考价值。
关键词:轮毂电机转向节 拓扑优化 轻量化 变密度法
1汽车轻量化设计背景介绍
在当今汽车工业中,减轻设计重量和缩短设计周期是两个突出的问题。汽车轻量化设计开始占据了汽车发展的主要地位,但是简单的汽车轻量化设计却是一把双刃剑,它在减轻汽车重量的同时,也牺牲了车辆的强度和刚度。在此情况下,Altair公司的有限元分析技术以及优化技术在汽车行业获得了非常成功的应用。特别是对于一些结构复杂的汽车零件,HyperWorks的有限元分析技术、拓扑优化技术使得很多材料的潜能及铸造的优势得到了充分的发挥。
转向节是汽车的重要安全零部件。该零件在原始设计中,由于整个机构的复杂性,只能作定性分析和类比估算。在确定实际结构时,往往选择的安全系数过大,致使设计出来的产品结构过于笨重、粗大。另外,由于对实际的受力点未能完全把握,导致结构材料分布不够均匀,铸造工艺性较差。
2有限元模型建立及分析
转向节与转向系统其它零部件相连的同时,通过法兰盘的制动器安装孔进行定位。由于整车全工况有限元模型的计算量太庞大,导致计算时间过长,因此仅选取在极限左转向工况下,转向节模型与转向系统零部件和轮毂电机相连接的六个节点作为输入载荷点,单独对转向节模型进行优化。
2.1 CAD建模
通过CAD软件进行转向节的设计与建模,模型如图2.1所示:
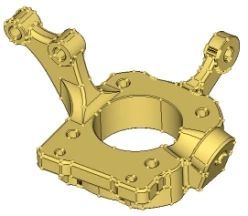
Figure2.1 转向节CAD模型
2.2 CAE建模
通过Altair公司hyperMesh软件对CAD模型进行有限元分析。此处采用Tetramesh进行四面体网格划分,其中与法兰盘的制动器安装的四个孔进行全自由度约束,其它孔径作为载荷输入点,所有孔壁均用RBE2进行刚性连接,有限元模型如图2.2所示:
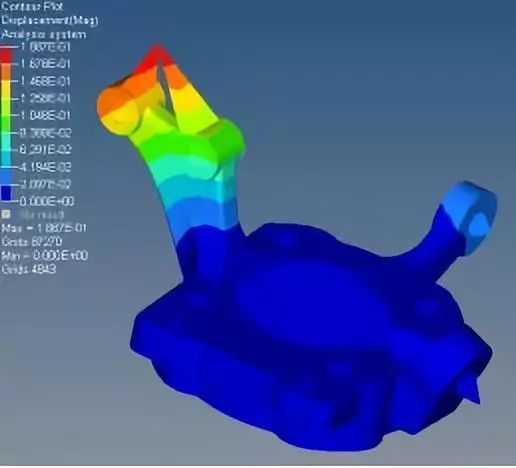
Figure2.2 转向节有限元模型
Table2.1 转向节有限元参数
零件
节点数
单元数
转向节
14305
407631
2.3材料属性
计算中使用的材料参数如表2.2所示:
Table2.2 转向节材料参数
材料
杨氏模量E(GPa)
泊松比
屈服强度
(MPa)
合金钢
210000
0.3
285
2.4边界载荷条件
转向节通过法兰盘的制动器安装的四个孔进行全自由度约束(图中4个蓝色约束),其它孔径为输入点(图中黄色箭头为力和力矩的输入)。通过Altair公司提供的MotionView软件进行整车动力学仿真,可获得在左转向工况下转向节响应的输入载荷,载荷和约束施加如图2.3所示:
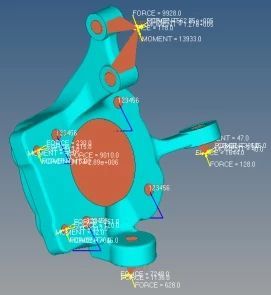
Figure2.3 转向节边界载荷
图2.3中,输入载荷力与力矩以及作用点的具体参数如下表所示:
Table2.3 转向节边界载荷参数
Load position
FX(N)
FY(N)
FZ(N)
TX(Nmm)
TY(Nmm)
TZ(Nmm)
轮心
-192
9010
8648
2885000
-3678
67987
控制臂外点
1136
-2248
628
0
0
0
转向横拉杆外点
-386
-1062
128
-186
40
-47
滑柱下点
-40
-732
-1182
327008
-7673
-29904
轮毂电机支撑上点
-230
215
116
48
-213
52
轮毂电机支撑下点
-251
120
70
32
-317
66
2.5转向节结果分析
转向节在上述工况下的分析结果如表2.4所示:
Table2.4 转向节分析结果
零件
最大位移(mm)
最大应力(MPa)
质量(Kg)
转向节
0.19
114.5
7.2
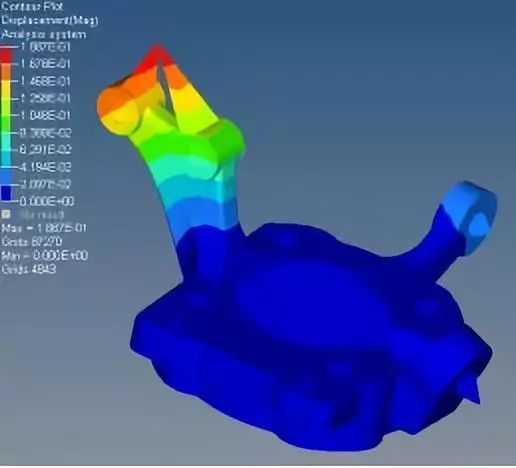
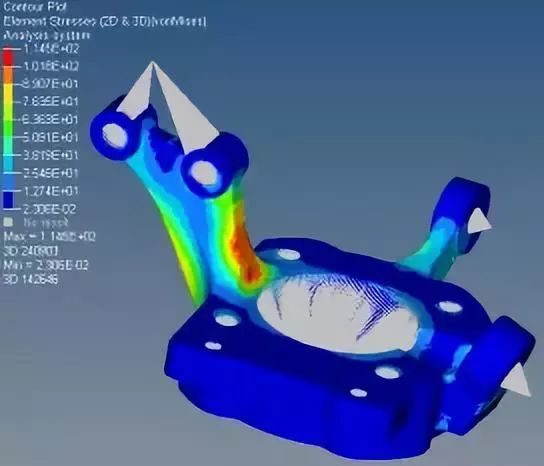
Figure2.5 转向节应力云图
3优化分析
OptiStruct结构优化主要分为拓扑优化、形貌优化和尺寸优化等。由于转向节采用实体单元建模,其优化目的是在给定的设计空间找到最优的材料分布,所以对其进行优化时将采用拓扑优化方法。
3.1确定优化流程设计
优化分析模型一般由目标函数、约束条件、优化设计变量三个方面组成,借助HyperWorks里的OptiStruct模块可以很方便的实现对转向节的优化设计,施加载荷点在上述工况下的最大合位移作为约束条件,体积最小化作为目标函数,这样利用拓扑优化可以获得一个最佳的材料布局,即最佳的材料分布。然后在这个最优结构布局的基础上按照实际需求形成一个新的设计方案,并借助CAD软件,形成新的CAD模型,并按照上述同样的工况条件对新设计方案进行有限元分析验证。
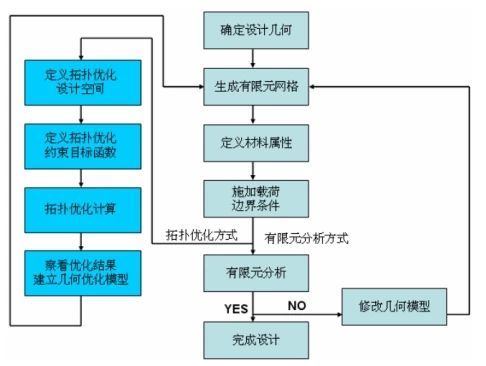
Figure3.1 优化设计流程图
3.2 拓扑优化分析
首先对转向节非干涉和非装配部位进行必要的材料填充,然后将有限元网络划分为设计区域(蓝色)和非设计区域(红色),如图3.2所示
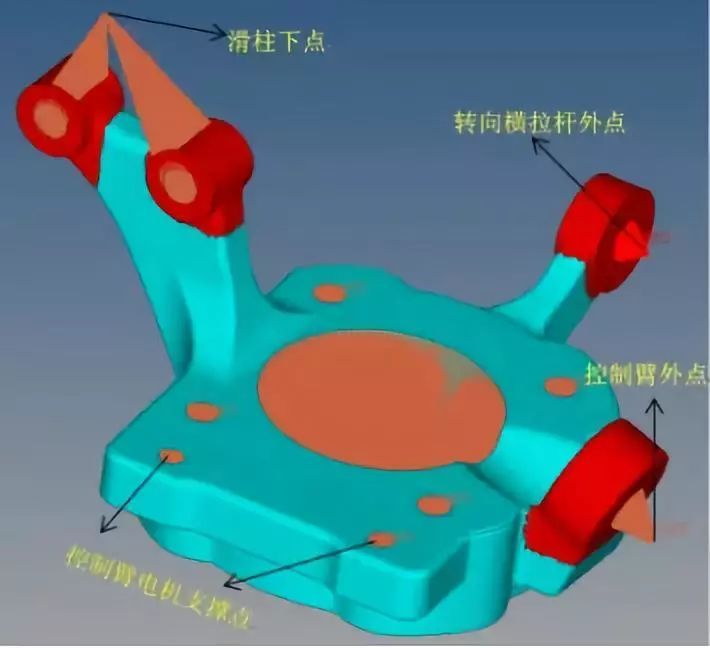
Figure3.2 设计区域和非设计区域有限元模型
通过MotionView对整车模型不同工况进行仿真,模拟仿真出转向节的各个孔径可接受的最大合位移,如表3.1所示:
Table3.1 约束条件最大合位移
节点号
滑柱下点
转向横拉杆外点
控制臂外点
位移(mm)
0.320
0.202
0.238
选取单元密度作为设计变量,增加最小成员尺寸约束,施加载荷点在工况下的最大合位移作为约束条件,体积最小化作为目标函数进行拓扑优化分析,如表3.2所示。并将拓扑优化中整个模型的最大应力控制在260MPa以下。
Table3.2 优化设计
设计变量
单元密度
约束条件
体积最小化
优化目标
最大合位移
基于变密度法对汽车转向节进行拓扑优化,单元密度结果如图3.3所示:
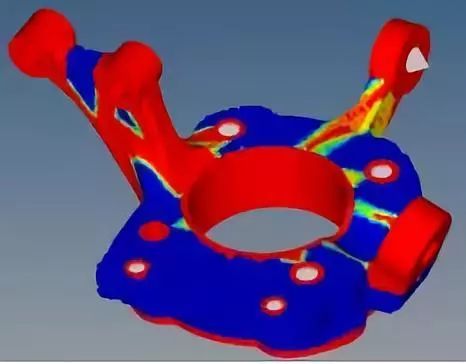
Figure3.3 拓扑优化单元密度
根据拓扑优化的单元密度等值面图指定的精度值,在该工况下可优化出新的设计方案,舍去图3.3中蓝色部分,可减轻50%以上质量,但是由于其相应拓扑关系,与其他零件的装配关系以及生产工艺难易程度等综合考虑,给予此工况下可进行的优化,如图3.3所示,其中黑色区域为在不干涉其装配且方便加工条件下的优化区域:
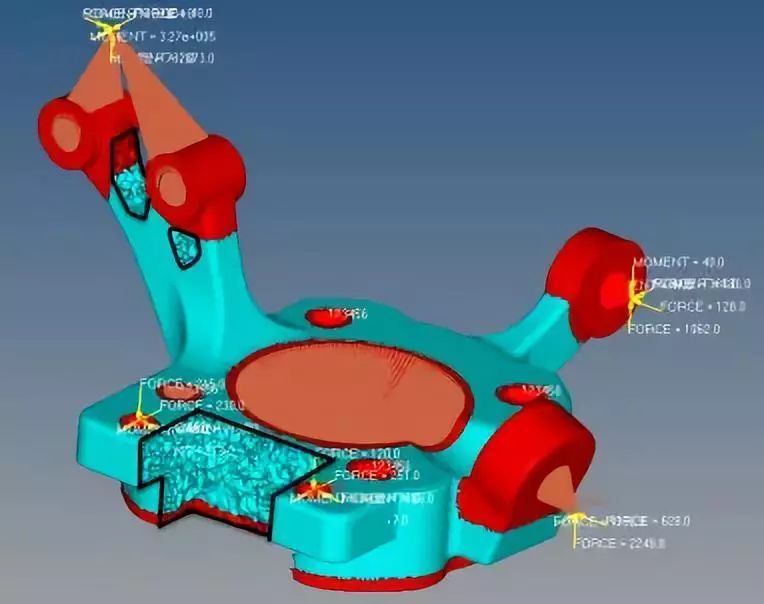
Figure3.4 拓扑优化
按照原始结构的工况条件对拓扑优化设计方案进行有限元分析验证,其计算结果如表3.3以及图3.5和图3.6所示:
Table3.3优化前后对比
转向节
质量
最大应力
最大位移
原方案
7.2
114.5
0.19
拓扑优化方案
6.3
151.1
0.20
优化率
轻量化12.5%
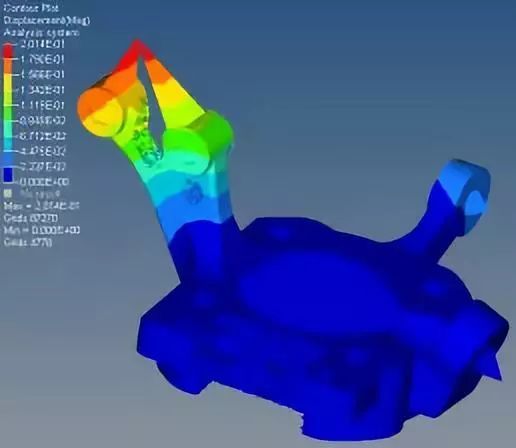
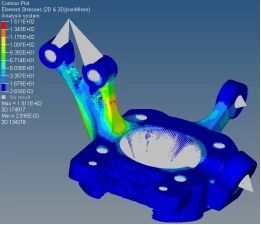
Figure3.6拓扑优化设计方案应力云图
4 分析与结论
经过拓扑优化,最终得到了较为理想的设计方案,将对原始方案与优化设计方案相比较,可以清楚地看到优化方案重量较以前减轻了12.5%,虽然同种工况下原始方案的最大应力为114.1MPa,优化后的最大应力增大为151.1Mpa,位移由0.18mm增大到0.20mm,但是均远低于设计要求的最大值。此次分析只是针对汽车在左转向极限静力工况下对转向节进行的优化设计,在实际工程运用中,还需要综合考虑其它载荷工况进行更全面的验证和优化,这也是优化设计的关键点,此外在优化参数的设置上还应考虑拔模约束等工艺的约束条件,使得最终的优化设计方案更加具有可制造加工性。通过该分析实例,也说明拓扑优化设计具有实际的工程运用意义,当然这还需要后续试验的验证。
参考文献
1 余志生. 汽车理论[M].机械工业出版社,2007
2 张胜兰等. 基于HyperWorks的结构优化设计技术[M].机械工业出版社,2007
3 王钰栋等. HyperMesh&HyperView应用技巧与高级实例[M].机械工业出版社,2012
4 洪清泉等. OptiStruct&HyperMesh理论基础与工程应用[M].机械工业出版社,2013
5 李颖琎等. HyperMesh在汽车转向节优化设计中的应用[J].HyperWorks技术大会,2008
来源:技术邻CAE学院
- 下一篇:九种最重要的汽车轻量化先进工艺技术
- 上一篇:森萨塔科技,从此安全“驰”久
举报 0
收藏 0
分享 130
-
高温季行车安全需重视:TRW SPS 制动盘让你的刹
2025-07-19 -
跨越速运凭什么“圈粉”万千客户?“中国零担30
2025-07-01 -
驭动未来,智启新程-采埃孚油护新出行
2025-06-25 -
旭化成荣获2025年度发明表彰,助力离子交换膜法
2025-06-11
编辑推荐
最新资讯
-
旭化成旗下宾霸品牌重磅亮相2025上海
2025-09-01 16:52
-
中国车企服务出海先行者:新央企新长
2025-08-29 16:13
-
携手共赴“智”造未来!埃马克推动大
2025-08-27 18:12
-
京东工业发布汽车等九大行业场景采购
2025-08-26 18:11
-
制造现场推动节能革新,电装稳步迈向
2025-08-25 14:04