冷冲压汽车高强度纵梁开发实例
2018-08-23 16:31:37·
基于某MPV车型纵梁前段冲压件模具设计制造实例, 利用计算机辅助有限元分析、冲压件结构与模面设计、基准与公差设计等手段, 优化纵梁工艺设计。将实物与理论分析相结合, 通过模具加工工艺的优化、表面处理技术应用及调试影响参数控制, 得到符合整车要求的纵梁前段。结果表明:型面回弹补偿量为1.251.5倍的回弹值时可得到相对优化的模面, 拉延中底面扭曲及侧壁内凹的控制可采用顶部压料机构及拉延槛;纵梁前段侧壁设计特殊公差01.0 mm有利于装配;采用淬火后精加工工艺及表面处理提前实施可减少模具反复的调试;原材料性能
摘要
基于某MPV车型纵梁前段冲压件模具设计制造实例, 利用计算机辅助有限元分析、冲压件结构与模面设计、基准与公差设计等手段, 优化纵梁工艺设计。将实物与理论分析相结合, 通过模具加工工艺的优化、表面处理技术应用及调试影响参数控制, 得到符合整车要求的纵梁前段。结果表明:型面回弹补偿量为1.251.5倍的回弹值时可得到相对优化的模面, 拉延中底面扭曲及侧壁内凹的控制可采用顶部压料机构及拉延槛;纵梁前段侧壁设计特殊公差01.0 mm有利于装配;采用淬火后精加工工艺及表面处理提前实施可减少模具反复的调试;原材料性能的波动直接影响冲压件稳定性。
一、产品特征
该纵梁为MPV车型纵梁前段, 为左右件对称设计, 设计材质为宝钢B410LA, 屈服强度为410~560 MPa, 抗拉强度为590 MPa, 料厚为1.6 mm, 产品尺寸为2157 mm×250 mm×198 mm。
纵梁前段冲压件造型如图1所示, 该冲压件主要特征是:在车身坐标Y向呈S型, 同时在车身坐标Z向有台阶, 侧壁为纵梁加强板及车架横梁焊接面, 法兰面为前地板焊接面, 冲压件底部和侧面孔为安装过孔。
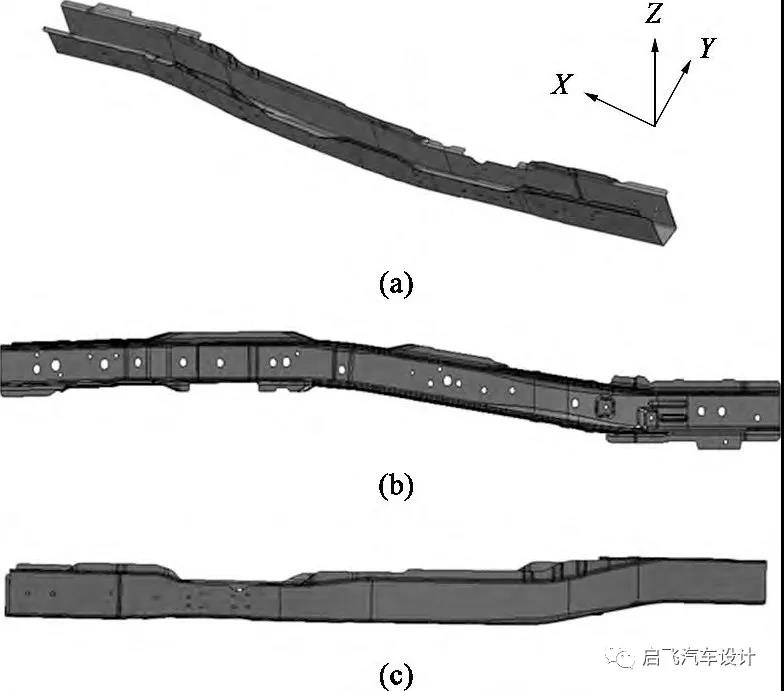
图1 纵梁前段(a) 示意图 (b) 俯视图 (c) 正视图
二、工艺设计
1.拉延模面设计
模面设计整体采用开口拉延, 压料面沿法兰面展开, 竖直翻边部分采用修边后再翻边工艺, 同时采用拉延槛工艺, 以控制拉延时板料流动。对于造型剧烈变化区域使用上模局部压料, 如图2所示。
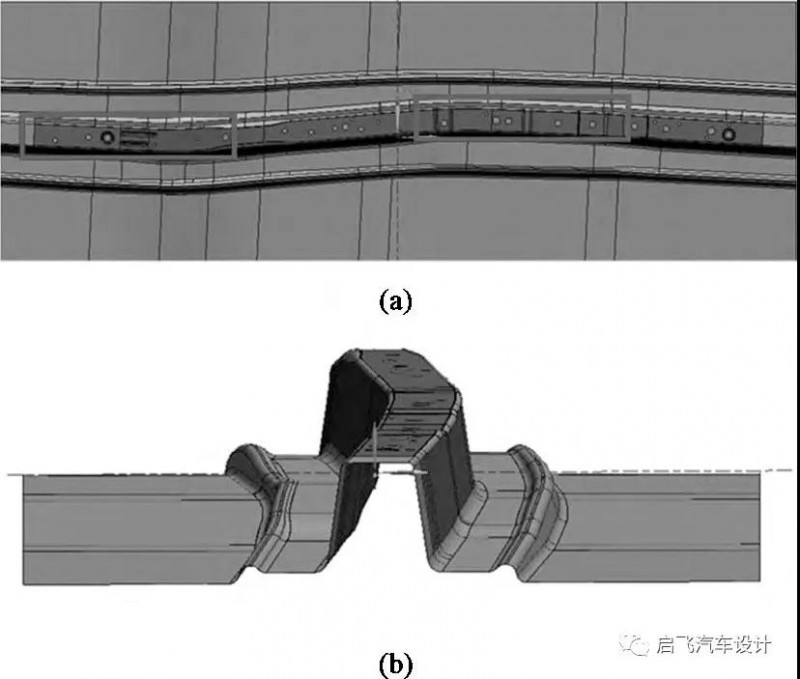
图2 拉延模面(a) 俯视图 (b) 侧视图
补充完整的模面需要借助有限元软件CAE分析其成形性, 对分析产生的开裂和起皱问题 (图3) 首先通过模面优化解决, 提出产品设计变更为备用方案, 产品的变更不能影响相关专业如焊装、涂装质量。
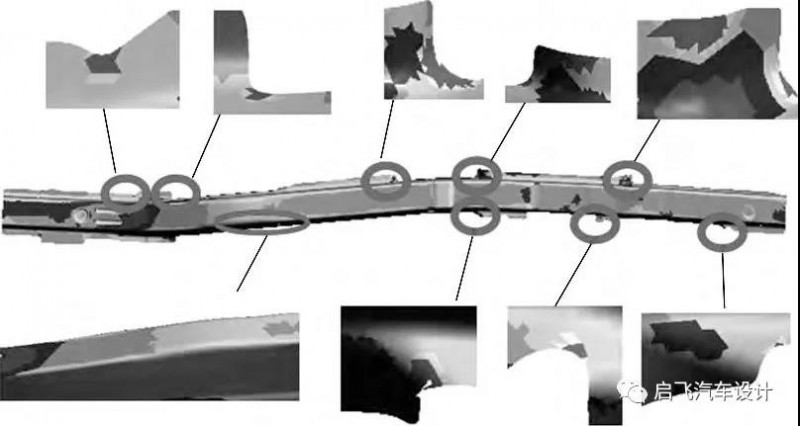
图3 CAE模拟的模面缺陷
使用有限元软件分析时, 回弹补偿非常关键。模面的型面补偿采用手动补偿, 即借助UG或CATIA软件修改模面, 以解决自动补偿带来的负角及塑性回弹补偿缺失等缺陷。型面进行回弹后进行10次以上的“反算”, 通过软件分析与现场经验 (1.25~1.5 mm补偿量) 相结合, 得到相对最优的模面。
工艺内容为OP10:拉延;OP20:修边冲孔;OP30:翻边整形;OP40:侧整形;OP50:冲孔侧冲孔。
1.基准与公差设计
保证模具、夹具、检具采用统一的定位基准, 尽可能与车身定位系统中的定位点保持一致。纵梁定位采用传统3-2-1定位原则即两孔+面的形式。根据工艺内容, 在纵梁前段定位, 第1基准 (面) 比第2、第3基准 (孔) 对其定位稳定性影响更大, 优选考虑质量容易保证的纵梁底面而非法兰面作为第1基准。纵梁底面为拉延1次成形到位, 一致性容易保证, 且除底面外, 单件检具其他区域不设夹持点, 如图4所示, 目的在于减少检测时附加变形。

图4 检具定位基准
纵梁的搭接关系属于典型的杯型件搭接, 如图5所示。纵梁前段侧壁设计正公差为0~1.0 mm, 其内搭接件设计负公差为-1.0~0 mm;特殊公差从底部R角处开始, 涉及有搭接关系的整个侧壁;特殊公差的补偿值直接体现在模具的加工数据中, 最终加工的模面是基于回弹补偿、特殊公差补偿以及理论分析与实物差异补偿合成的型面。
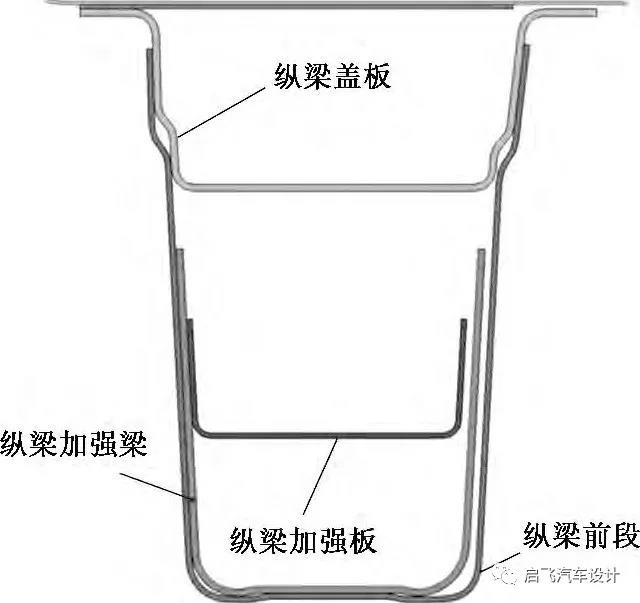
图5 纵梁焊接面
三、模具加工与调试
1.模具加工
理论分析与实物差异的补偿直接影响模具数控加工模型。为了减小理论与实际的差异造成的加工偏差, 采用非量产模具钢 (45钢) 加工出件, 根据出件状态, 使用三坐标测量回弹值, 而进行实物的反向补偿。基于实物的反向补偿一般需要至少3轮以上验证, 在出件状态与理论分析基本吻合时, 才对量产的模具材料 (SKD11等) 进行加工。
将传统加工工艺“粗加工精加工淬火”更改为“半精加工淬火精加工”, 目的是解决淬火后镶块变形造成型面偏差, 尽量减少回弹调整的反复。在拉延精加工之后, 不轻易调整拉延模型面, 以更好地控制底面扭曲。
2.表面处理
模具生产中, 板料流动与模具凸模和压料面摩擦, 在生产约200件时模具表面温度升高明显, 导致冲压件表面产生拉毛缺陷。如不及时处理拉毛问题, 导致碎屑粘连在模具表面, 继续生产会导致冲压件开裂。
在模具批量生产前, 需要对模具表面进行硬化处理, 如图6所示, 常采用熔盐渗金属、渗钒等, 也称TD覆层技术。通过热扩散作用于工件表面形成一层数微米级的碳化钒覆层, 增加模具表面耐磨、抗拉伤性能。
虽然表面处理形成的覆层是微米级别, 但表面处理前后的模具生产的冲压件状态也存在差异。表面处理工作安排在模具出厂前完成, 在模具进入生产场地后的机床匹配性调试内容主要是坯料尺寸、机床压力和凸凹模及压边圈间隙的调整。表面处理后的模具表面不允许补焊。因此, 模具进场后的调试主要通过侧整形序模具调整, 目的在于减少拉延模具调试的反复, 减少调试工作量。
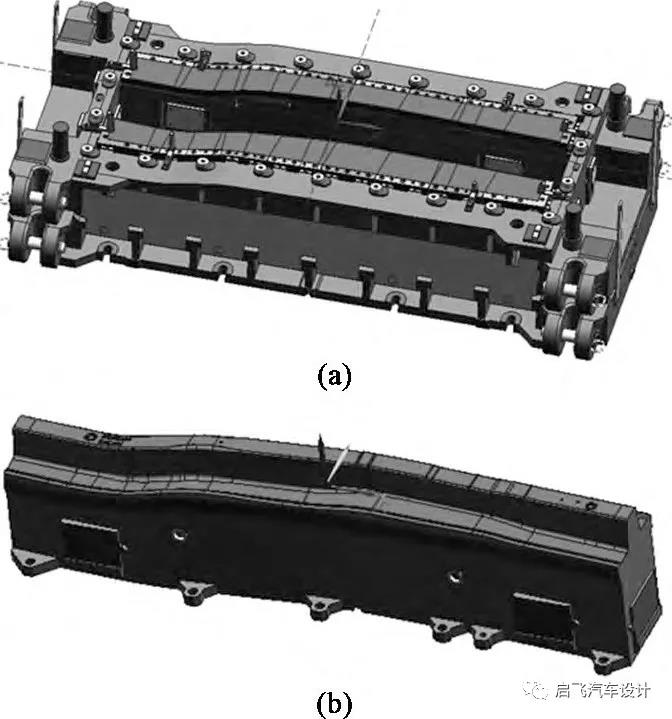
图6 模具表面处理区域(a) 压边圈 (b) 凸模
3.模具调试
(1)机床参数。模具进厂前的调试参数确定, 模具首次上机床的机床参数根据CAE分析值设定。同时考虑坯料厚度偏差、原材料拉延过程减薄以及机床参数误差等因素, 根据首件状态对应调整参数。通过机床参数调整无法提升冲压件质量时, 对模具进行整改。
模具进厂后调试主要是机床匹配性验证, 参数一般按照进厂前固化的数值设定。参数的调整是基于机床的差异性, 因此应避免改变模具状态。生产场地模具调试机床应为量产时的生产机床, 一般情况下不允许变更。
(2)板材性能。高强度钢板的屈服强度为一个范围, 如B410l A屈服强度为410~560 MPa, 因此, 不同采购批次的板料性能可能存在很大差异, 导致冲压件质量波动非常大。保证供货源的稳定性才能相对保证冲压件质量。
(3)模具整改。模具进厂后的型面修改是不可避免的, 应尽量通过调试整形模来实现调试目的, 拉延模型面的改动对纵梁调试工作是颠覆性的。拉延模的调试主要是验证拉延件的一致性, 因拉延件属于过程件, 其不能使用检具检测, 而采用游标卡尺测量开口尺寸来判断是否合格。
模具调试时, 工序件存储最好使用专用工位器具, 工序件之前不能有堆积, 如图7所示, 目的是避免工序件堆积导致张口外张引起的测量数据失真, 而影响模具整改量的计算。
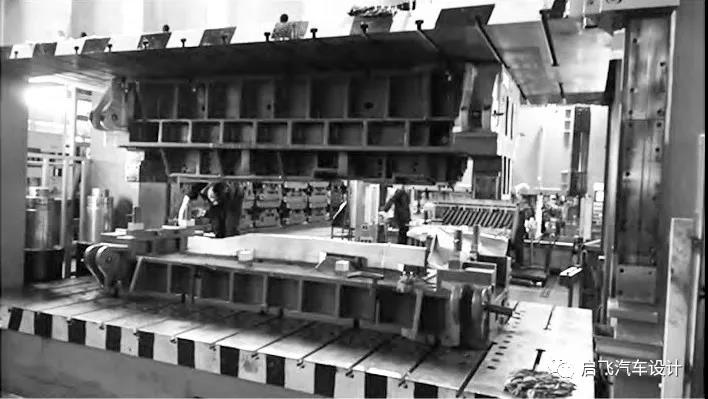
图7 模具调试
冲压件符合检具后, 在焊装白车身零件时仍会出现搭接间隙过大或搭接干涉等问题, 这是由公差累积、定位误差导致的。因此, 在制件整改时还需重点关注法兰面的相对偏差及搭接面的开口宽度。因当前工艺水平限制而难以解决的问题, 应综合考虑工艺水平、开发周期、调试成本及对工装的寿命等因素的影响, 必要时整改纵梁匹配件, 以保证白车身质量为最终目的。
四、结论
(1)CAE分析的起皱、开裂等缺陷首选通过模面优化解决, 提出产品设计变更为备用方案, 产品的变更不能影响相关专业质量。
(2)模面的型面补偿采用手动补偿, 通过软件分析与现场经验相结合, 可以得到相对最优的模面。
(3)定位系统设计由各专业协同完成, 特殊公差的设计采用传统经验设计, 可进一步探索3D公差分析软件的应用, 使公差设计更合理。
(4)拉延模调试稳定后再进行后序侧整形调整, 拉延模的表面处理在进厂前完成, 模具进厂后的调试主要通过侧整形序模具调整。
(5)使用量产时的生产机床进行模具调试、保证板料货源稳定及使用工位器具可有效保障模具调试工作的进行。
作者:楚伟峰 崔礼春 赵烈伟 孙连福 来源:锻压技术
基于某MPV车型纵梁前段冲压件模具设计制造实例, 利用计算机辅助有限元分析、冲压件结构与模面设计、基准与公差设计等手段, 优化纵梁工艺设计。将实物与理论分析相结合, 通过模具加工工艺的优化、表面处理技术应用及调试影响参数控制, 得到符合整车要求的纵梁前段。结果表明:型面回弹补偿量为1.251.5倍的回弹值时可得到相对优化的模面, 拉延中底面扭曲及侧壁内凹的控制可采用顶部压料机构及拉延槛;纵梁前段侧壁设计特殊公差01.0 mm有利于装配;采用淬火后精加工工艺及表面处理提前实施可减少模具反复的调试;原材料性能的波动直接影响冲压件稳定性。
一、产品特征
该纵梁为MPV车型纵梁前段, 为左右件对称设计, 设计材质为宝钢B410LA, 屈服强度为410~560 MPa, 抗拉强度为590 MPa, 料厚为1.6 mm, 产品尺寸为2157 mm×250 mm×198 mm。
纵梁前段冲压件造型如图1所示, 该冲压件主要特征是:在车身坐标Y向呈S型, 同时在车身坐标Z向有台阶, 侧壁为纵梁加强板及车架横梁焊接面, 法兰面为前地板焊接面, 冲压件底部和侧面孔为安装过孔。
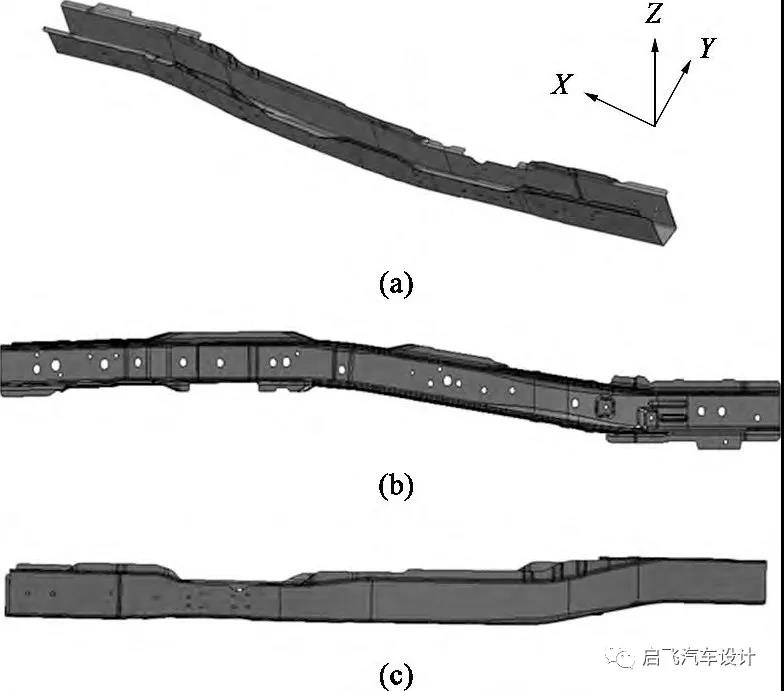
图1 纵梁前段(a) 示意图 (b) 俯视图 (c) 正视图
二、工艺设计
1.拉延模面设计
模面设计整体采用开口拉延, 压料面沿法兰面展开, 竖直翻边部分采用修边后再翻边工艺, 同时采用拉延槛工艺, 以控制拉延时板料流动。对于造型剧烈变化区域使用上模局部压料, 如图2所示。
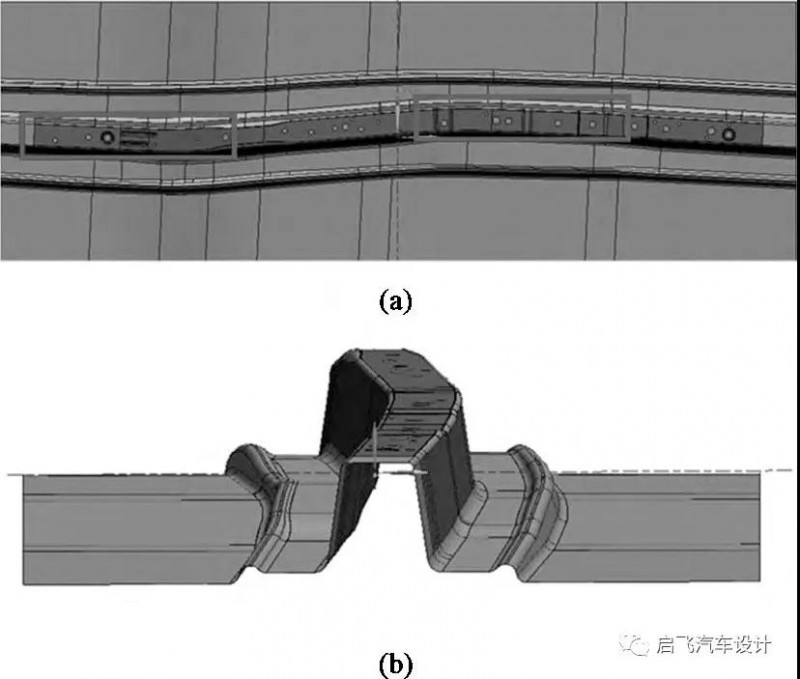
图2 拉延模面(a) 俯视图 (b) 侧视图
补充完整的模面需要借助有限元软件CAE分析其成形性, 对分析产生的开裂和起皱问题 (图3) 首先通过模面优化解决, 提出产品设计变更为备用方案, 产品的变更不能影响相关专业如焊装、涂装质量。
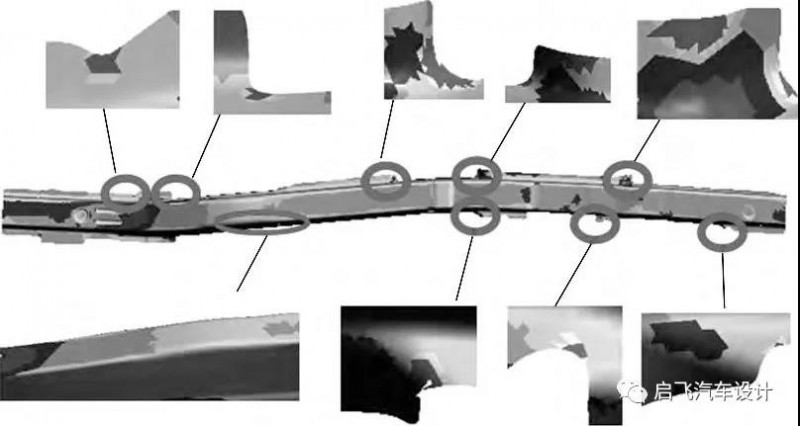
图3 CAE模拟的模面缺陷
使用有限元软件分析时, 回弹补偿非常关键。模面的型面补偿采用手动补偿, 即借助UG或CATIA软件修改模面, 以解决自动补偿带来的负角及塑性回弹补偿缺失等缺陷。型面进行回弹后进行10次以上的“反算”, 通过软件分析与现场经验 (1.25~1.5 mm补偿量) 相结合, 得到相对最优的模面。
工艺内容为OP10:拉延;OP20:修边冲孔;OP30:翻边整形;OP40:侧整形;OP50:冲孔侧冲孔。
1.基准与公差设计
保证模具、夹具、检具采用统一的定位基准, 尽可能与车身定位系统中的定位点保持一致。纵梁定位采用传统3-2-1定位原则即两孔+面的形式。根据工艺内容, 在纵梁前段定位, 第1基准 (面) 比第2、第3基准 (孔) 对其定位稳定性影响更大, 优选考虑质量容易保证的纵梁底面而非法兰面作为第1基准。纵梁底面为拉延1次成形到位, 一致性容易保证, 且除底面外, 单件检具其他区域不设夹持点, 如图4所示, 目的在于减少检测时附加变形。

图4 检具定位基准
纵梁的搭接关系属于典型的杯型件搭接, 如图5所示。纵梁前段侧壁设计正公差为0~1.0 mm, 其内搭接件设计负公差为-1.0~0 mm;特殊公差从底部R角处开始, 涉及有搭接关系的整个侧壁;特殊公差的补偿值直接体现在模具的加工数据中, 最终加工的模面是基于回弹补偿、特殊公差补偿以及理论分析与实物差异补偿合成的型面。
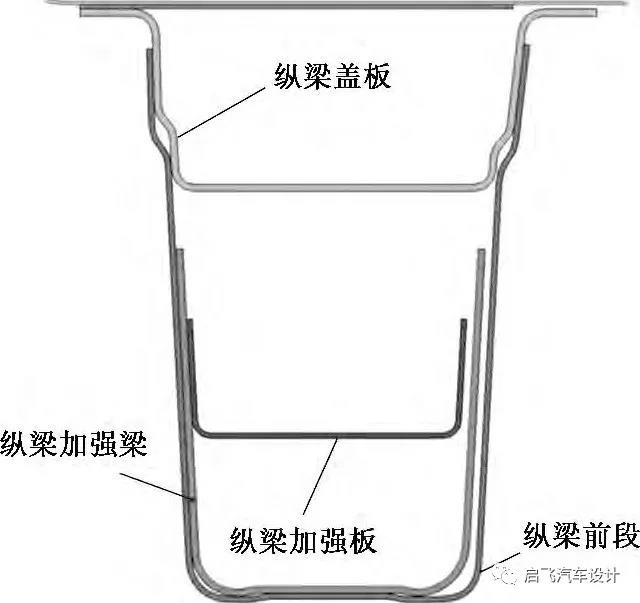
图5 纵梁焊接面
三、模具加工与调试
1.模具加工
理论分析与实物差异的补偿直接影响模具数控加工模型。为了减小理论与实际的差异造成的加工偏差, 采用非量产模具钢 (45钢) 加工出件, 根据出件状态, 使用三坐标测量回弹值, 而进行实物的反向补偿。基于实物的反向补偿一般需要至少3轮以上验证, 在出件状态与理论分析基本吻合时, 才对量产的模具材料 (SKD11等) 进行加工。
将传统加工工艺“粗加工精加工淬火”更改为“半精加工淬火精加工”, 目的是解决淬火后镶块变形造成型面偏差, 尽量减少回弹调整的反复。在拉延精加工之后, 不轻易调整拉延模型面, 以更好地控制底面扭曲。
2.表面处理
模具生产中, 板料流动与模具凸模和压料面摩擦, 在生产约200件时模具表面温度升高明显, 导致冲压件表面产生拉毛缺陷。如不及时处理拉毛问题, 导致碎屑粘连在模具表面, 继续生产会导致冲压件开裂。
在模具批量生产前, 需要对模具表面进行硬化处理, 如图6所示, 常采用熔盐渗金属、渗钒等, 也称TD覆层技术。通过热扩散作用于工件表面形成一层数微米级的碳化钒覆层, 增加模具表面耐磨、抗拉伤性能。
虽然表面处理形成的覆层是微米级别, 但表面处理前后的模具生产的冲压件状态也存在差异。表面处理工作安排在模具出厂前完成, 在模具进入生产场地后的机床匹配性调试内容主要是坯料尺寸、机床压力和凸凹模及压边圈间隙的调整。表面处理后的模具表面不允许补焊。因此, 模具进场后的调试主要通过侧整形序模具调整, 目的在于减少拉延模具调试的反复, 减少调试工作量。
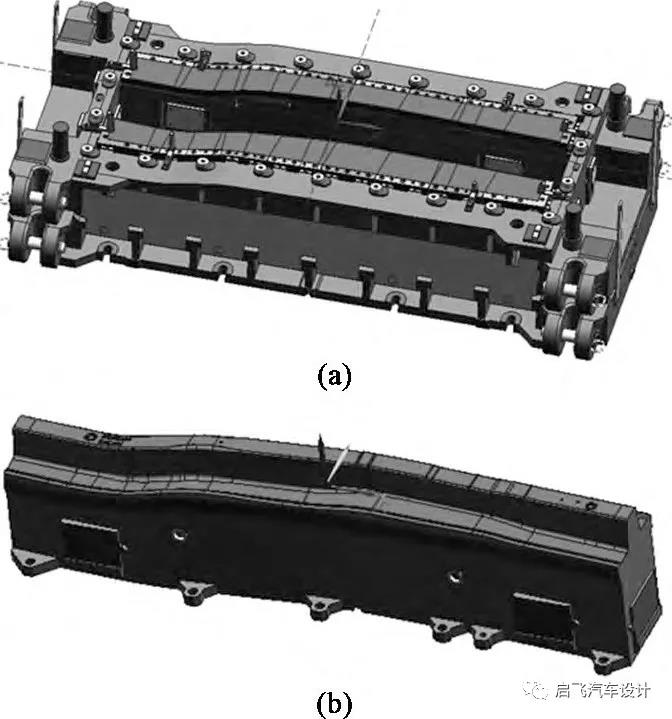
图6 模具表面处理区域(a) 压边圈 (b) 凸模
3.模具调试
(1)机床参数。模具进厂前的调试参数确定, 模具首次上机床的机床参数根据CAE分析值设定。同时考虑坯料厚度偏差、原材料拉延过程减薄以及机床参数误差等因素, 根据首件状态对应调整参数。通过机床参数调整无法提升冲压件质量时, 对模具进行整改。
模具进厂后调试主要是机床匹配性验证, 参数一般按照进厂前固化的数值设定。参数的调整是基于机床的差异性, 因此应避免改变模具状态。生产场地模具调试机床应为量产时的生产机床, 一般情况下不允许变更。
(2)板材性能。高强度钢板的屈服强度为一个范围, 如B410l A屈服强度为410~560 MPa, 因此, 不同采购批次的板料性能可能存在很大差异, 导致冲压件质量波动非常大。保证供货源的稳定性才能相对保证冲压件质量。
(3)模具整改。模具进厂后的型面修改是不可避免的, 应尽量通过调试整形模来实现调试目的, 拉延模型面的改动对纵梁调试工作是颠覆性的。拉延模的调试主要是验证拉延件的一致性, 因拉延件属于过程件, 其不能使用检具检测, 而采用游标卡尺测量开口尺寸来判断是否合格。
模具调试时, 工序件存储最好使用专用工位器具, 工序件之前不能有堆积, 如图7所示, 目的是避免工序件堆积导致张口外张引起的测量数据失真, 而影响模具整改量的计算。
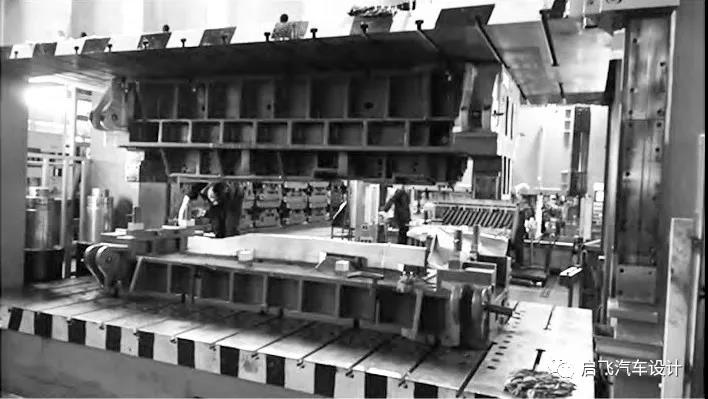
图7 模具调试
冲压件符合检具后, 在焊装白车身零件时仍会出现搭接间隙过大或搭接干涉等问题, 这是由公差累积、定位误差导致的。因此, 在制件整改时还需重点关注法兰面的相对偏差及搭接面的开口宽度。因当前工艺水平限制而难以解决的问题, 应综合考虑工艺水平、开发周期、调试成本及对工装的寿命等因素的影响, 必要时整改纵梁匹配件, 以保证白车身质量为最终目的。
四、结论
(1)CAE分析的起皱、开裂等缺陷首选通过模面优化解决, 提出产品设计变更为备用方案, 产品的变更不能影响相关专业质量。
(2)模面的型面补偿采用手动补偿, 通过软件分析与现场经验相结合, 可以得到相对最优的模面。
(3)定位系统设计由各专业协同完成, 特殊公差的设计采用传统经验设计, 可进一步探索3D公差分析软件的应用, 使公差设计更合理。
(4)拉延模调试稳定后再进行后序侧整形调整, 拉延模的表面处理在进厂前完成, 模具进厂后的调试主要通过侧整形序模具调整。
(5)使用量产时的生产机床进行模具调试、保证板料货源稳定及使用工位器具可有效保障模具调试工作的进行。
作者:楚伟峰 崔礼春 赵烈伟 孙连福 来源:锻压技术
举报 0
收藏 0
分享 136
-
助力汽车零部件产线智能化升级,西门子Xcelerat
2025-06-27 -
BBA集体转向!放弃全面电动化
2025-06-26 -
西门子SiePA斩获麒麟认证,服务能力再升级!
2025-06-24 -
Geega产品图谱 | Geega OS 工业操作系统
2025-06-23
编辑推荐
最新资讯
-
辐射亚太,链接全球——采埃孚再制造
2025-07-30 11:46
-
思看科技发布子品牌SCANOLOGY,全球
2025-07-30 11:06
-
风雨不动安如山——比亚迪叉车构筑“
2025-07-30 08:48
-
NEAS CHINA 新能源汽车技术与生态链
2025-07-29 09:52
-
三维扫描革新碾磨机辊套检测,效率与
2025-07-25 10:46