揭秘上汽MG智能化程度最高的工厂
2018-08-09 17:14:49· 来源:Robotinside
制造名爵ZS的工厂位于郑州经开,该工厂2017年3月开工建设,9月一期工程竣工并投产。因此创下了中国汽车史上“当年签约、当年投产”跨地区合作最快速度的记录。6个月前二期30万辆产能项目启动,上汽规划该基地将成为继南京浦口和上海临港之后上汽乘用车国内最大的生产基地。
制造名爵ZS的工厂位于郑州经开,该工厂2017年3月开工建设,9月一期工程竣工并投产。因此创下了中国汽车史上“当年签约、当年投产”跨地区合作最快速度的记录。6个月前二期30万辆产能项目启动,上汽规划该基地将成为继南京浦口和上海临港之后上汽乘用车国内最大的生产基地。
本次参观的工厂主要生产MG名爵车型,上汽称其为“MG名爵全球样板工厂”,该工厂生产的车型不仅供应国内市场,同时也出口到英国、澳大利亚、智利、以色列等海外市场。基地内建有冲压、焊装、涂装、总装四大工艺车间,按照上汽全球质量标准建设和管理,该工厂运用了大量的自动化技术,其中焊装的生产自动化率达到了99.84%,几乎全程无需人工参与。以下将带你详细了解这家工厂。
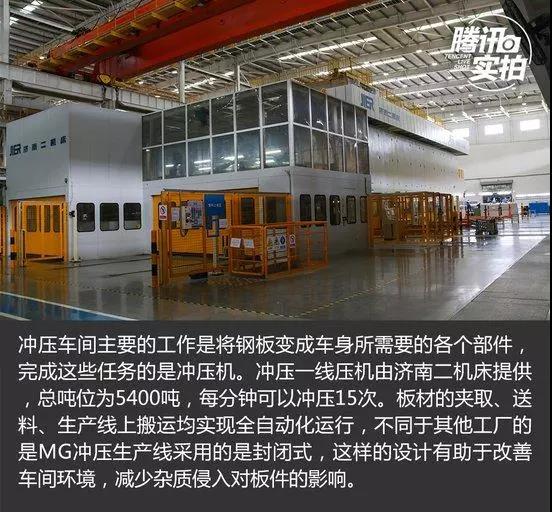
首先来到是冲压车间,该车间主要的工作是将钢板变成车身所需要的各个部件,完成这些任务的是冲压机。冲压一线压机由济南二机床提供,总吨位为5400吨,每分钟可以冲压15次。板材的夹取、送料、生产线上搬运均实现全自动化运行,不同于其他工厂的是MG冲压生产线采用的是封闭式,这样的设计有助于改善车间环境,减少杂质侵入对板件的影响。
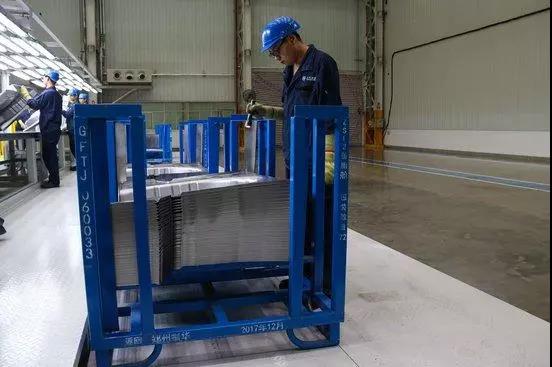
目前机器正在进行冲压的是后门板,一个车门需要冲压4次。工人正在检查冲压质量,可以看到每一块冲压件至少会经过3个人的检查,前排两人检查完毕后在后方还有一个人进行检查,另外每200件会进行一个详细的抽查。
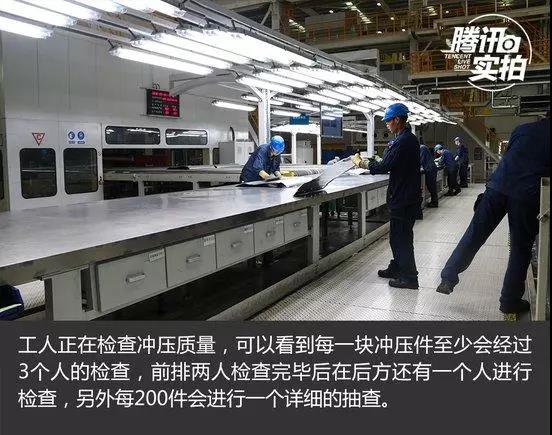
冲压模具来自上汽产业链内的赛科利以及亿森和和润,生产线的换模工作同样是自动化进行,首先机器将旧模弹出,然后图中橙色的部件将新模送入机器内组装,整个换模时间约为4分钟。
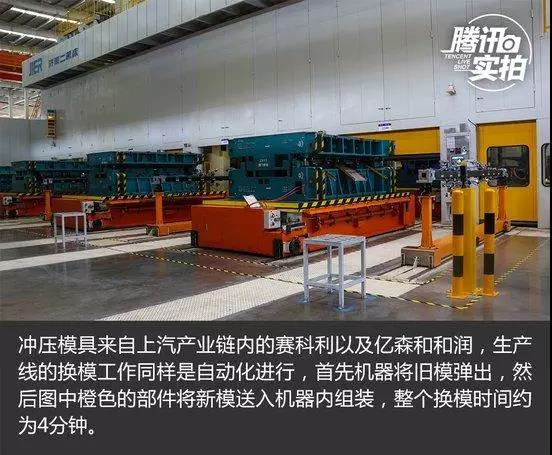
冲压二线处于调试阶段,包含5台压机,总吨位为6400吨,这条线的冲压制造精度更高,可以生产更复杂的冲压件,带来的好处就是可以让MG车身更加锐利和精致。
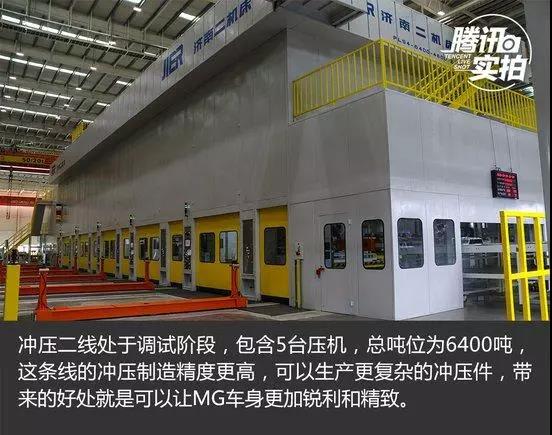
焊装车间的工作可以理解为搭积木,就是将各个部件拼合成一个完整的车身。车间分为5个步骤,分别是底板、侧围、门盖、总拼、表调,完成这些工作的大部分都是机器人。
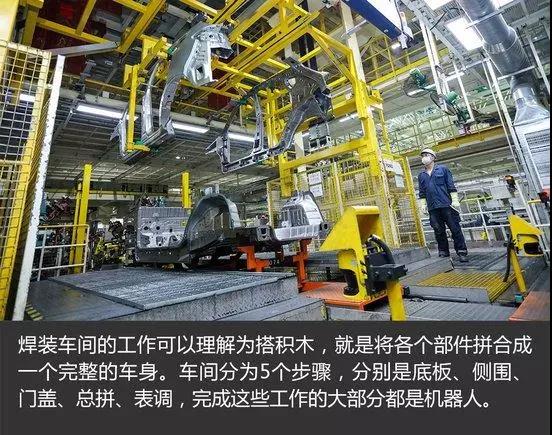
焊装车间总共有548台机器人,它们由FANUC提供。一台名爵ZS车身焊点达到2511个,其中机器人焊点2507个,人工焊点4个,人工焊点分别是油箱口下方和尾门LOGO部位,负责人介绍不采用机器人焊主要基于成本考虑。
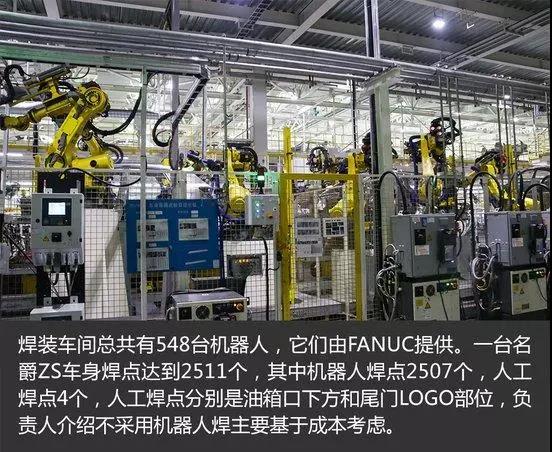
机器人可以实现包括电阻焊、激光钎焊、CMT冷却焊、混合气体保护焊、螺柱焊等多种焊接方式,焊接部位的不同,采用的焊接技术也会有区别,比如车身顶部采用激光钎焊就可以获得更美观的焊缝,并且强度更高、受力均匀。
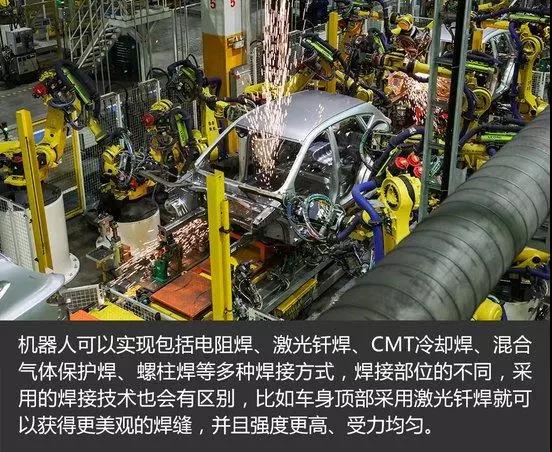
质量检测同样交给机器人,图中的就是检测位,为什么要有红色幕布盖住呢?因为采用的是激光检测设备,为了避免光线产生影响。检测机器人会对所有产品的棱边、孔等位置实行100%检测,另外还会对重要的受力部位采用超声波探伤,以保证焊装品质。
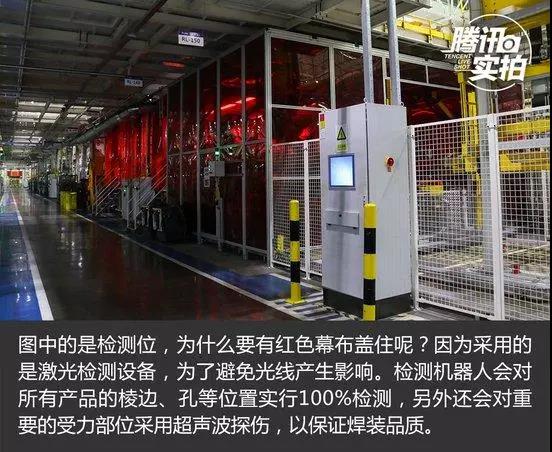
正在进行的是焊装车间的最后一个步骤,表调。工人正在安装车门,熟悉流程的人可能会觉得奇怪,车门不是应该在总装阶段安装的吗?其实此时安装是为了减小部件出现的误差,避免总装阶段部件安装出现问题。
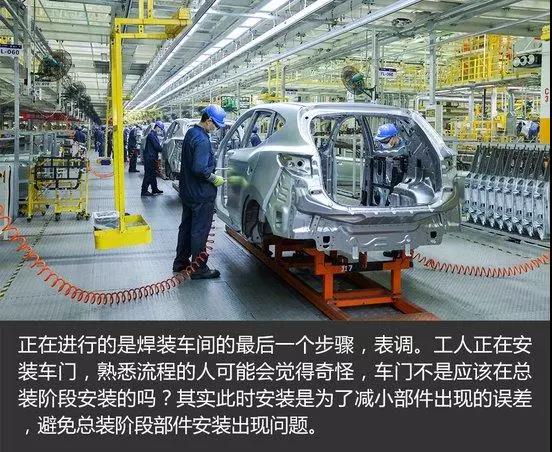
此时钢板已经变成了一个完整的白车身,但是还需要给它“穿”一套保护膜,这套工序就是涂装。
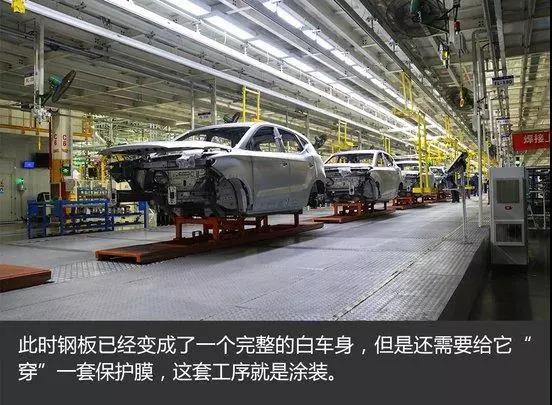
汽车车漆不仅是渲染车身颜色,还具有保护金属的功能。MG采用的是免中涂喷漆工艺,首先车身需要先浸泡吸附一层底漆,然后在涂上色漆和清漆,中途还需要经过烘烤。这些工作全部由44台机器人完成。
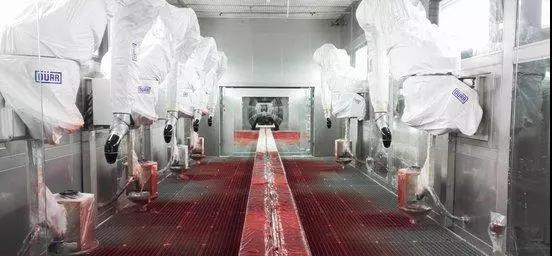
懂行的人会知道涂装车间是产生污染最严重的区域,值得一提的是MG涂装车间针对环保进行了特殊设计。采用硅烷工艺无锌、镍等重金属排放,无BOD和COD排放,固体废物排放减少90%,废水减少50%,涂装车间墙体采用隔热材料,喷漆工艺采用湿式循环风技术,整体运行能耗降低了20%。总结就是,废物排放少,能源消耗少。
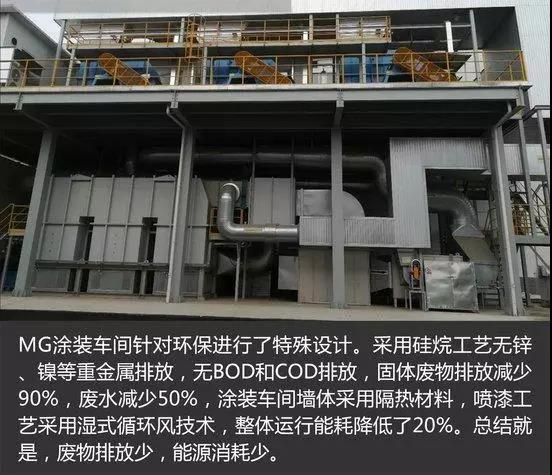
最后一步是给车身安装上动力总成以及配套设备。这时候就来到了总装车间,相比前几个车间的无人化生产,这里应该是人气最高的地方了。
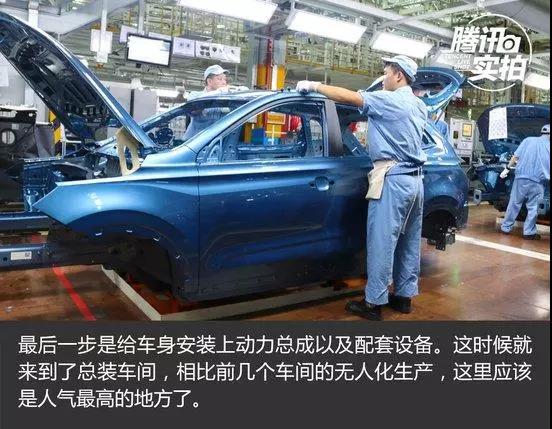
每一个车身都有一个TPS码,这就像车辆的身份证,工人通过读取TPS码可以了解该车的配置信息,还能够通过后台实现对任意车辆的调度管理。
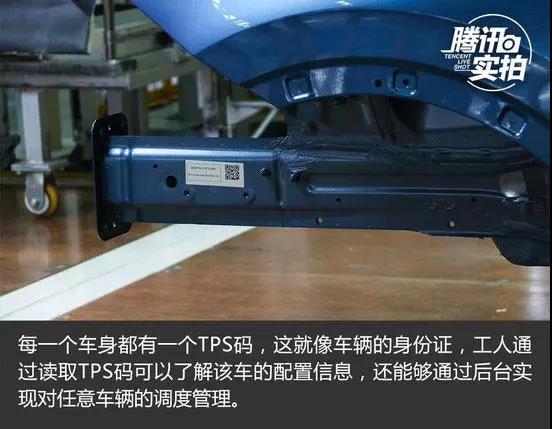
厂区随处可见忙碌的AGV智能小车,它通过磁线导引自动配送物料,整个厂区的零件配送工作都由这些小家伙来完成。
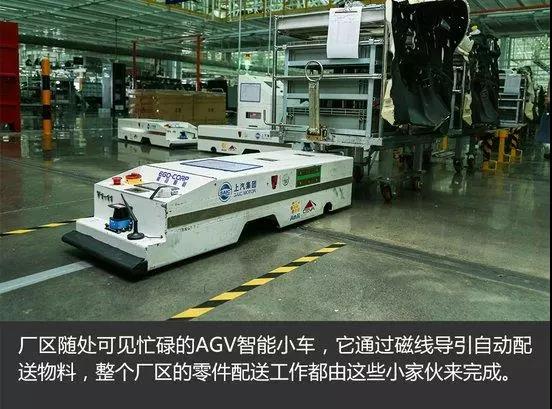
名爵ZS的采用的是底盘与车身整体合装的工艺,底盘总成会先放在台架上组装好然后与配置好的车身进行合装,这样可以提升装配效率与装配品质。
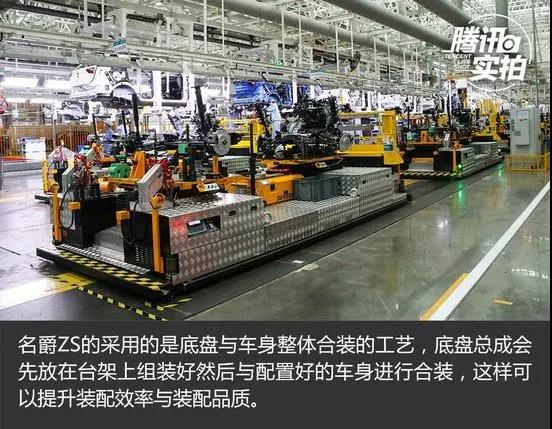
工人正在用辅助助力设备安装门板,据介绍车间内大于10KG以上的部件装配均有设备辅助完成,可以有效降低劳动强度,减少事故率与错误率。
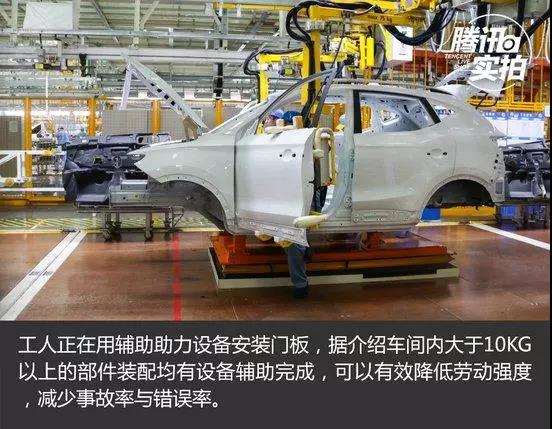
QCQS系统对涉及安全的280颗关键螺栓进行精确的扭矩控制与记录,实时监控防止错装与漏装。
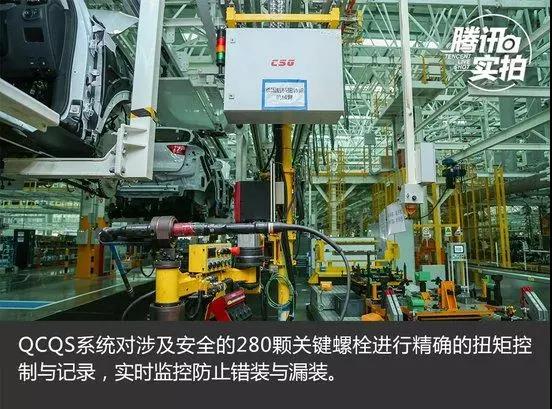
ECOS设备将ECU、TCU、斑马智行系统进行写入,并检查整车线路状态。
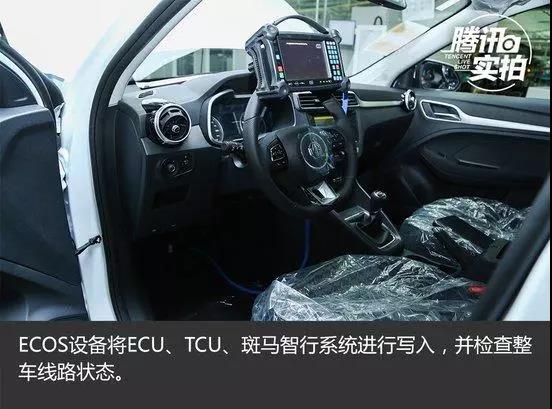
组装完成后的车还需要经过一系列的检查才可下线,包括外观检测、性能测试、雨淋测试之后还要进行一段简短的路试,全部通过后就可以入库了。
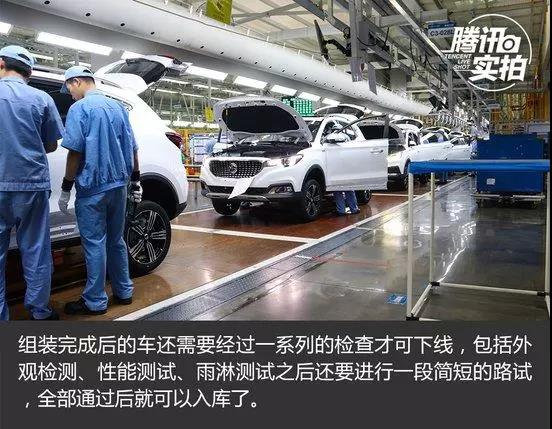
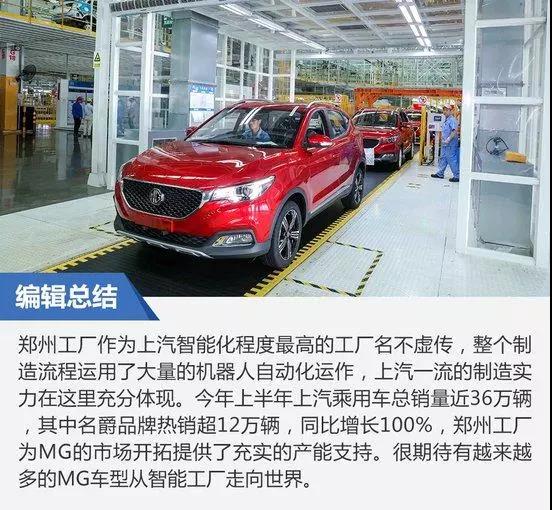
总结:郑州工厂作为上汽智能化程度最高的工厂名不虚传,整个制造流程运用了大量的机器人自动化运作,上汽一流的制造实力在这里充分体现。今年上半年上汽乘用车总销量近36万辆,其中名爵品牌热销超12万辆,同比增长100%,郑州工厂为MG的市场开拓提供了充实的产能支持。很期待有越来越多的MG车型从智能工厂走向世界。
本次参观的工厂主要生产MG名爵车型,上汽称其为“MG名爵全球样板工厂”,该工厂生产的车型不仅供应国内市场,同时也出口到英国、澳大利亚、智利、以色列等海外市场。基地内建有冲压、焊装、涂装、总装四大工艺车间,按照上汽全球质量标准建设和管理,该工厂运用了大量的自动化技术,其中焊装的生产自动化率达到了99.84%,几乎全程无需人工参与。以下将带你详细了解这家工厂。
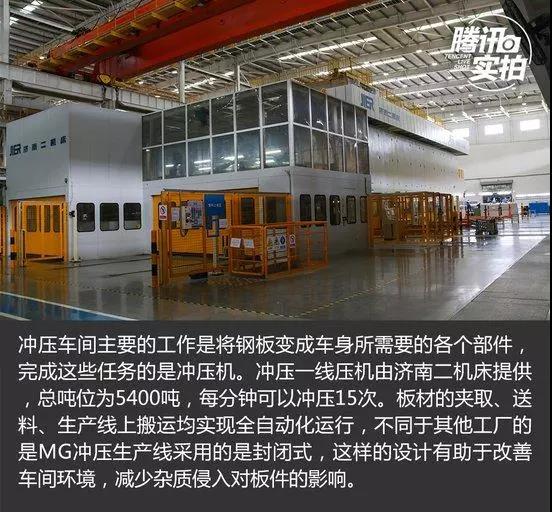
首先来到是冲压车间,该车间主要的工作是将钢板变成车身所需要的各个部件,完成这些任务的是冲压机。冲压一线压机由济南二机床提供,总吨位为5400吨,每分钟可以冲压15次。板材的夹取、送料、生产线上搬运均实现全自动化运行,不同于其他工厂的是MG冲压生产线采用的是封闭式,这样的设计有助于改善车间环境,减少杂质侵入对板件的影响。
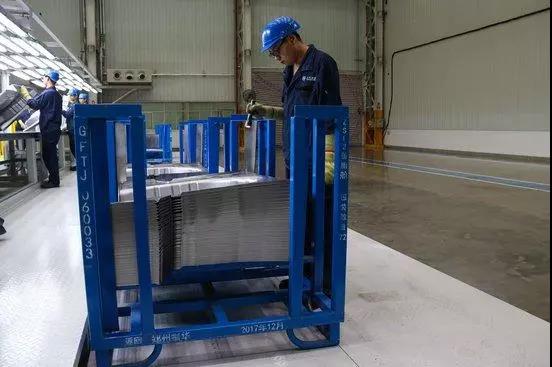
目前机器正在进行冲压的是后门板,一个车门需要冲压4次。工人正在检查冲压质量,可以看到每一块冲压件至少会经过3个人的检查,前排两人检查完毕后在后方还有一个人进行检查,另外每200件会进行一个详细的抽查。
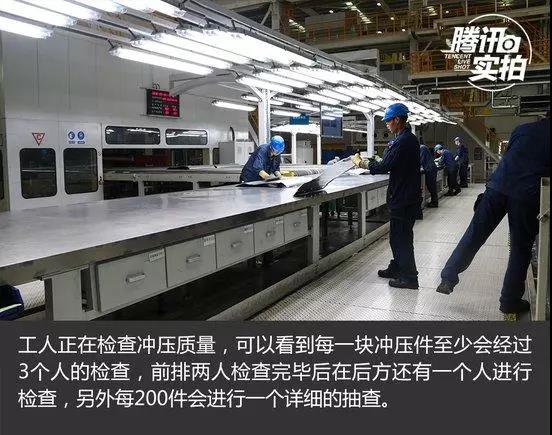
冲压模具来自上汽产业链内的赛科利以及亿森和和润,生产线的换模工作同样是自动化进行,首先机器将旧模弹出,然后图中橙色的部件将新模送入机器内组装,整个换模时间约为4分钟。
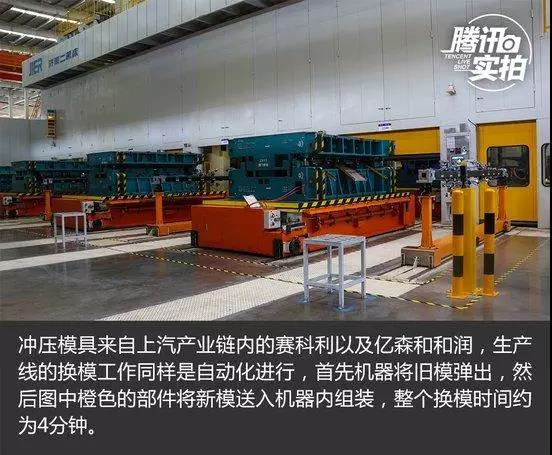
冲压二线处于调试阶段,包含5台压机,总吨位为6400吨,这条线的冲压制造精度更高,可以生产更复杂的冲压件,带来的好处就是可以让MG车身更加锐利和精致。
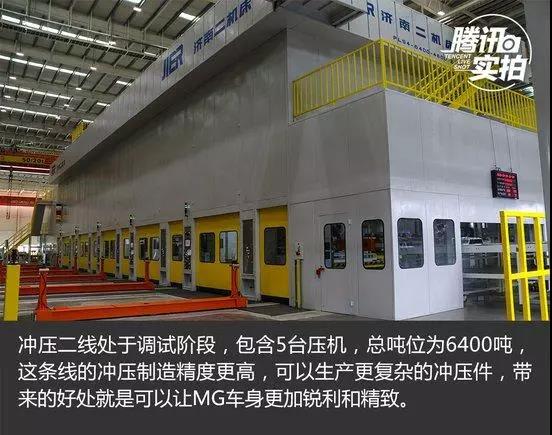
焊装车间的工作可以理解为搭积木,就是将各个部件拼合成一个完整的车身。车间分为5个步骤,分别是底板、侧围、门盖、总拼、表调,完成这些工作的大部分都是机器人。
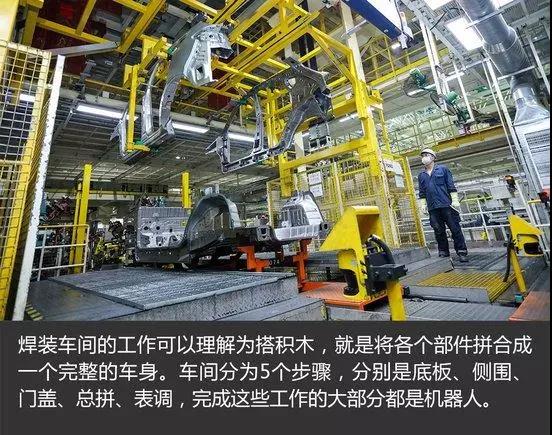
焊装车间总共有548台机器人,它们由FANUC提供。一台名爵ZS车身焊点达到2511个,其中机器人焊点2507个,人工焊点4个,人工焊点分别是油箱口下方和尾门LOGO部位,负责人介绍不采用机器人焊主要基于成本考虑。
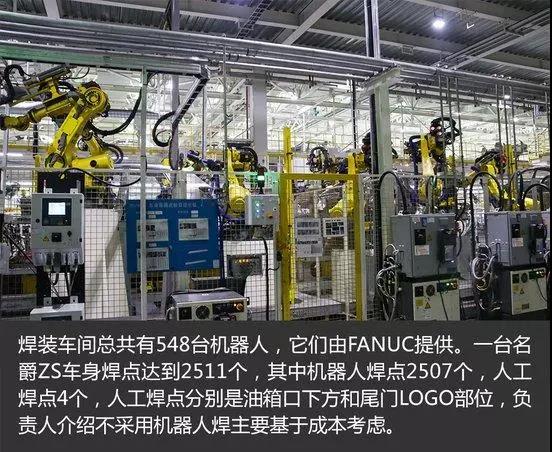
机器人可以实现包括电阻焊、激光钎焊、CMT冷却焊、混合气体保护焊、螺柱焊等多种焊接方式,焊接部位的不同,采用的焊接技术也会有区别,比如车身顶部采用激光钎焊就可以获得更美观的焊缝,并且强度更高、受力均匀。
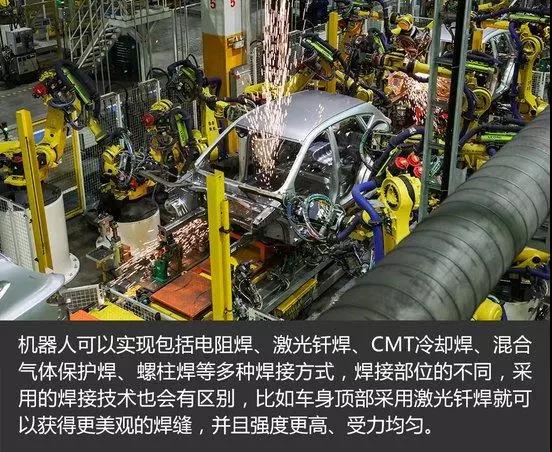
质量检测同样交给机器人,图中的就是检测位,为什么要有红色幕布盖住呢?因为采用的是激光检测设备,为了避免光线产生影响。检测机器人会对所有产品的棱边、孔等位置实行100%检测,另外还会对重要的受力部位采用超声波探伤,以保证焊装品质。
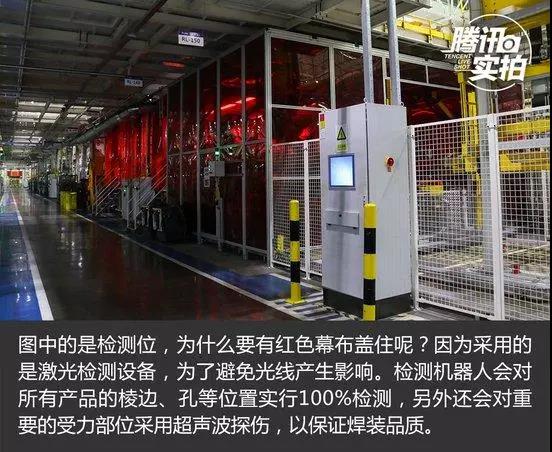
正在进行的是焊装车间的最后一个步骤,表调。工人正在安装车门,熟悉流程的人可能会觉得奇怪,车门不是应该在总装阶段安装的吗?其实此时安装是为了减小部件出现的误差,避免总装阶段部件安装出现问题。
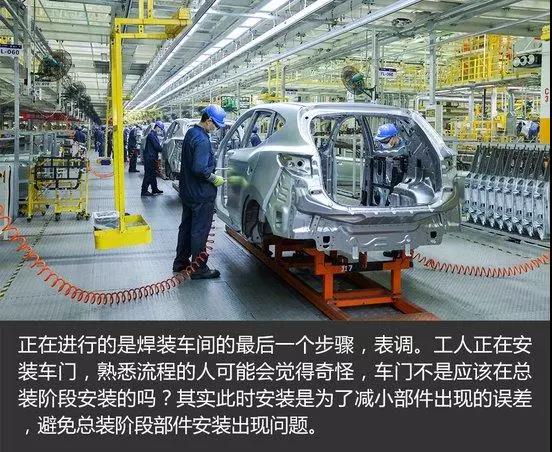
此时钢板已经变成了一个完整的白车身,但是还需要给它“穿”一套保护膜,这套工序就是涂装。
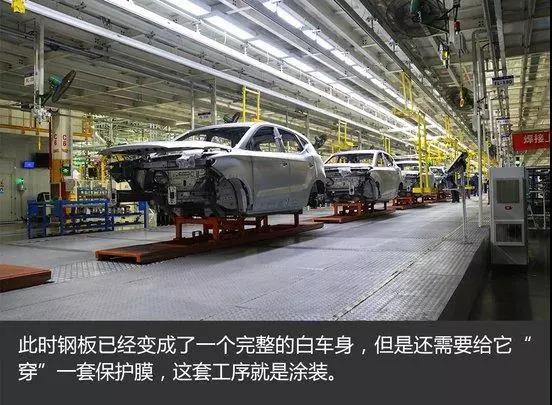
汽车车漆不仅是渲染车身颜色,还具有保护金属的功能。MG采用的是免中涂喷漆工艺,首先车身需要先浸泡吸附一层底漆,然后在涂上色漆和清漆,中途还需要经过烘烤。这些工作全部由44台机器人完成。
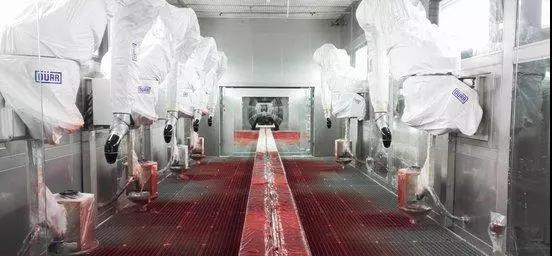
懂行的人会知道涂装车间是产生污染最严重的区域,值得一提的是MG涂装车间针对环保进行了特殊设计。采用硅烷工艺无锌、镍等重金属排放,无BOD和COD排放,固体废物排放减少90%,废水减少50%,涂装车间墙体采用隔热材料,喷漆工艺采用湿式循环风技术,整体运行能耗降低了20%。总结就是,废物排放少,能源消耗少。
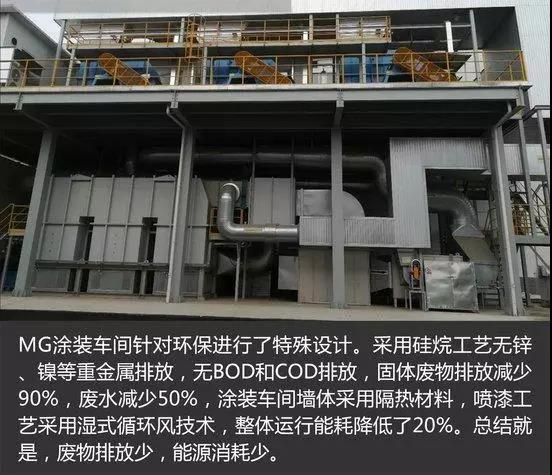
最后一步是给车身安装上动力总成以及配套设备。这时候就来到了总装车间,相比前几个车间的无人化生产,这里应该是人气最高的地方了。
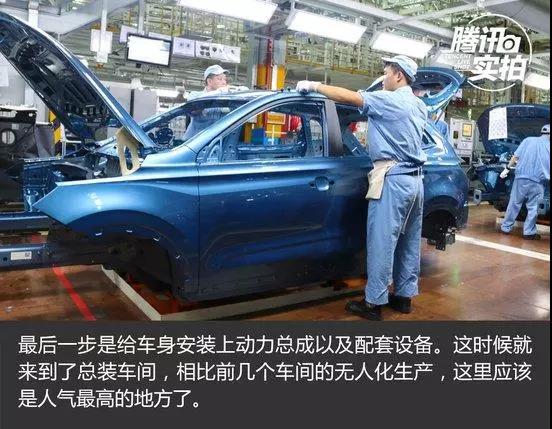
每一个车身都有一个TPS码,这就像车辆的身份证,工人通过读取TPS码可以了解该车的配置信息,还能够通过后台实现对任意车辆的调度管理。
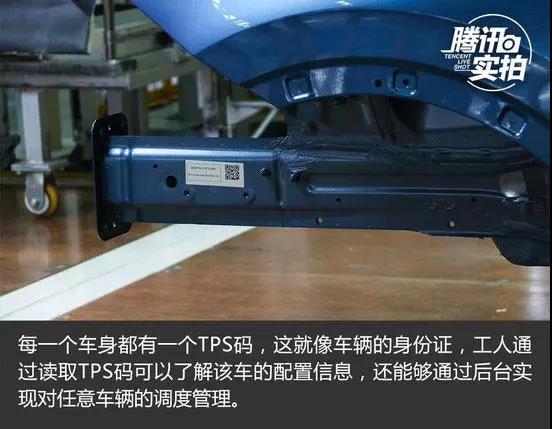
厂区随处可见忙碌的AGV智能小车,它通过磁线导引自动配送物料,整个厂区的零件配送工作都由这些小家伙来完成。
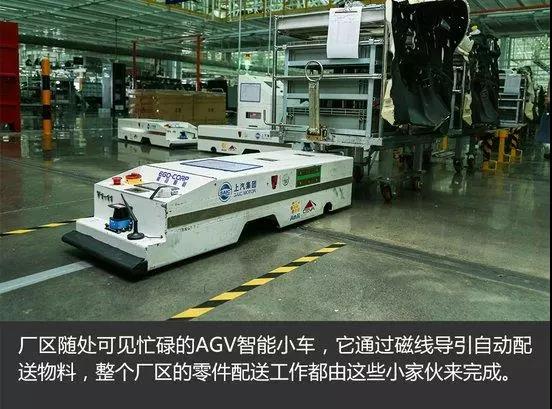
名爵ZS的采用的是底盘与车身整体合装的工艺,底盘总成会先放在台架上组装好然后与配置好的车身进行合装,这样可以提升装配效率与装配品质。
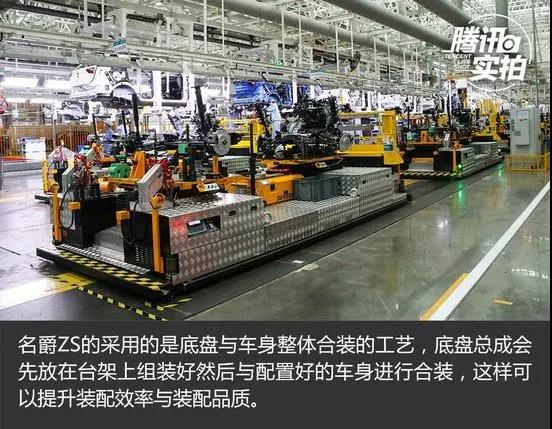
工人正在用辅助助力设备安装门板,据介绍车间内大于10KG以上的部件装配均有设备辅助完成,可以有效降低劳动强度,减少事故率与错误率。
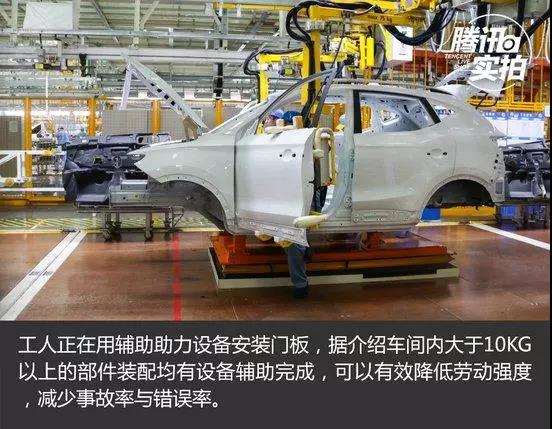
QCQS系统对涉及安全的280颗关键螺栓进行精确的扭矩控制与记录,实时监控防止错装与漏装。
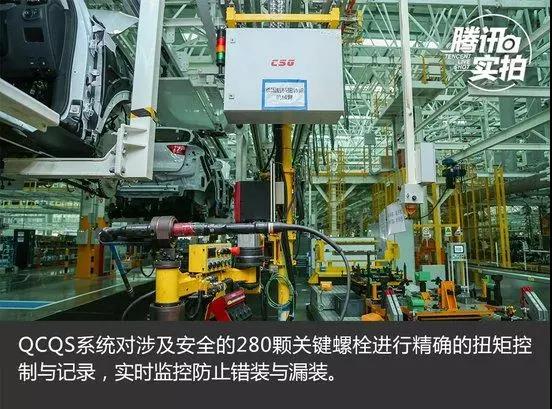
ECOS设备将ECU、TCU、斑马智行系统进行写入,并检查整车线路状态。
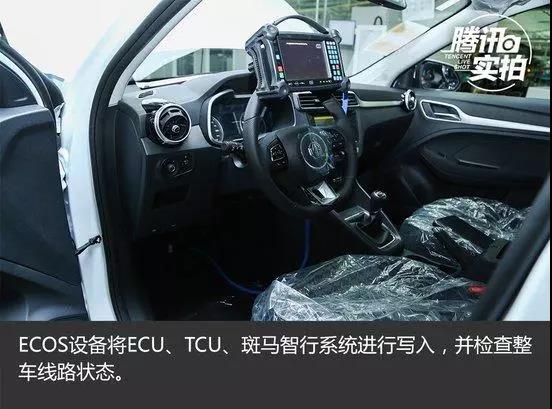
组装完成后的车还需要经过一系列的检查才可下线,包括外观检测、性能测试、雨淋测试之后还要进行一段简短的路试,全部通过后就可以入库了。
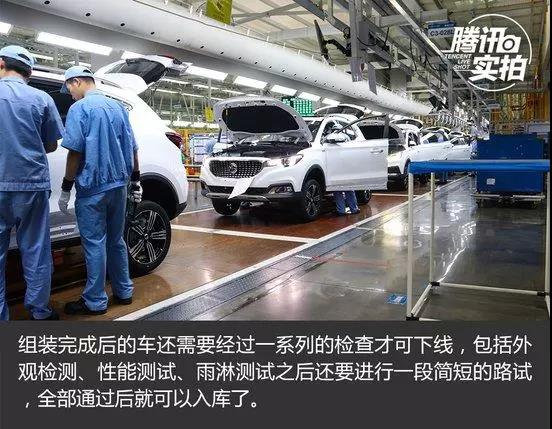
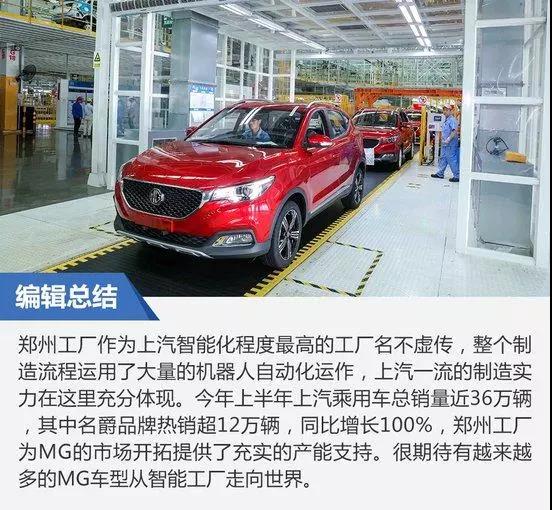
总结:郑州工厂作为上汽智能化程度最高的工厂名不虚传,整个制造流程运用了大量的机器人自动化运作,上汽一流的制造实力在这里充分体现。今年上半年上汽乘用车总销量近36万辆,其中名爵品牌热销超12万辆,同比增长100%,郑州工厂为MG的市场开拓提供了充实的产能支持。很期待有越来越多的MG车型从智能工厂走向世界。
编辑推荐
最新资讯
-
辐射亚太,链接全球——采埃孚再制造
2025-07-30 11:46
-
思看科技发布子品牌SCANOLOGY,全球
2025-07-30 11:06
-
风雨不动安如山——比亚迪叉车构筑“
2025-07-30 08:48
-
NEAS CHINA 新能源汽车技术与生态链
2025-07-29 09:52
-
三维扫描革新碾磨机辊套检测,效率与
2025-07-25 10:46