汽车辊压门槛较冲压门槛性能更优
2018-08-08 14:23:13· 来源:锻压世界
轻量化是汽车技术发展的重要方向,大量采用辊压技术提高车身高强钢应用范围是重要方法。对某款车型辊压门槛与冲压门槛在质量、成本、性能这3个方面进行了分析。通过对比分析发现辊压门槛相比冲压门槛质量轻、价格便宜,整车碰撞性能更优。
轻量化是汽车技术发展的重要方向,大量采用辊压技术提高车身高强钢应用范围是重要方法。对某款车型辊压门槛与冲压门槛在质量、成本、性能这3个方面进行了分析。通过对比分析发现辊压门槛相比冲压门槛质量轻、价格便宜,整车碰撞性能更优。
在国外主流汽车厂商所开发的新车型中, 辊压型钢零部件已占到60%,而在我国轿车新车型中的用量仅为6%,因此有非常大的产业拓展空间。早期辊压型钢零部件主要应用在前防撞梁、车门上段等零件。但随着技术的不断成熟,应用范围不断扩展,辊压门槛的应用也越来越广泛。辊压门槛的长度基本不受限制,可实现不同车型同一零件的模块化设计,降低制造成本。如某品牌两款不同车型车门槛板(见图1、图 2)设计为同一截 面,材料牌号为HC50/980DP,抗拉强度为980MPa,两款车型共用同一生产线,实现了生产线共用。
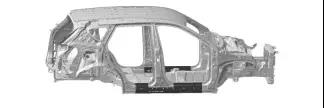
图1 车型1
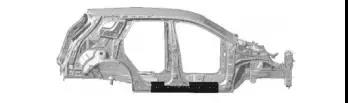
图2 车型2
同时辊压门槛生产效率高,适合于大批量生产,与冲压工艺相比,效率提高10倍以上,制造成本大幅降低。辊压门槛能解决冲压门槛产品回弹、褶皱以及壁翘曲难以控制、模具调试时间长等问题。
辊压门槛行业应用现状
辊压门槛在国外主流汽车厂商和合资品牌厂商应用较为广泛,比如上海通用、长安福特、上海大众等。
近年来,随着碰撞安全、车身轻量化要求的提升以及辊压工艺的发展成熟,自主品牌车型也在借鉴采用,特别的在长安汽车、奇瑞汽车等品牌厂商,都已经在新开发的车型上了采用了辊压门槛。表1为辊压门槛的应用实例。由表1可以看出,辊压门槛在门槛内板和门槛外板上都有所应用,但零件的牌号和料厚选择不尽相同。
表1 辊压门槛的应用实例
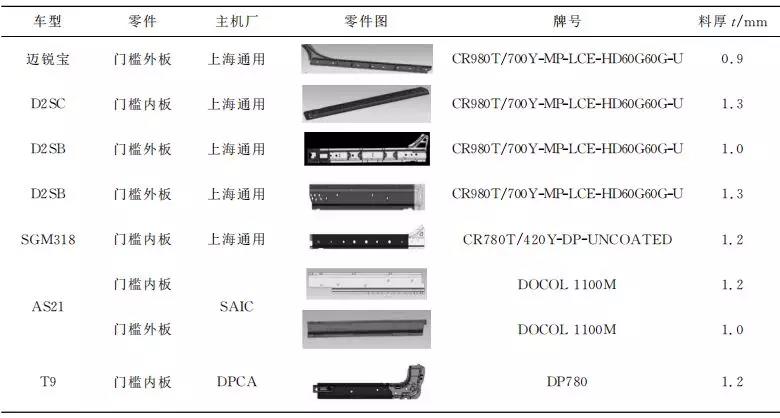
辊压门槛与传统冲压门槛对比分析
质量分析
对于门槛加强板,采 用冲压方案:料 厚为1.4mm,质量约8.90kg;采用辊压方案:料厚为1.2mm,质量约7.63kg。因此,门槛加强板采用辊压方案可以减重约1.27kg(见表2)。
表2 奇瑞某款车型辊压门槛与冲压门槛对比
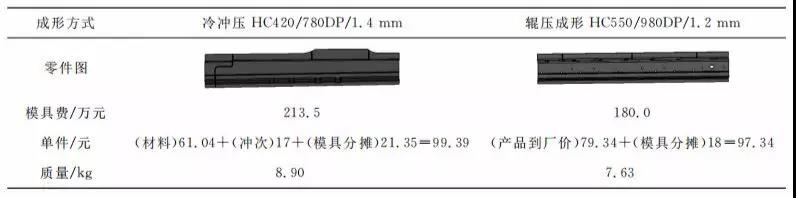
成本分析
辊压方案(包含材料、辊压线、检具)与冷冲压方案(含材料、模具、检具、冲次费)成本对比见表2。因此,门槛加强板采用辊压方案可以减少成本2.05单件/元。辊压门槛成本核算分析如表3所示。
表3 辊压门槛成本核算分析
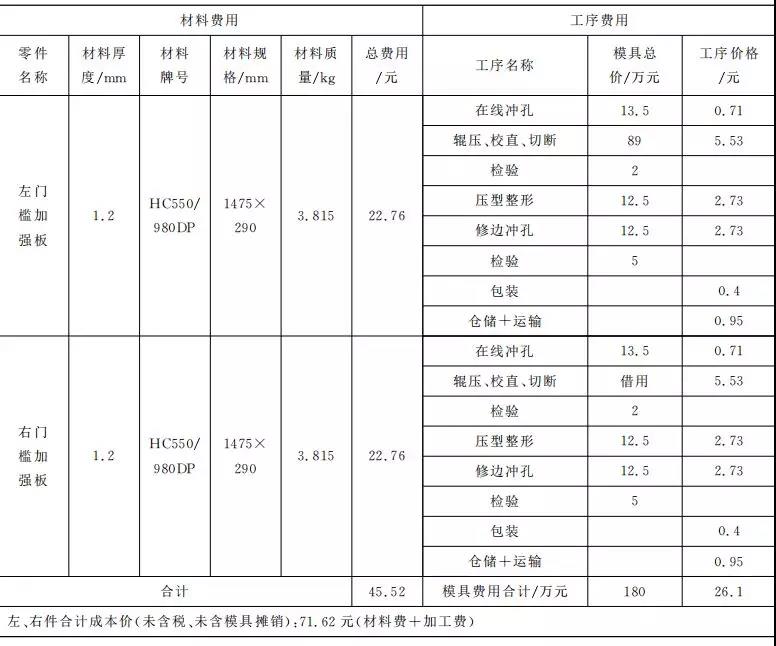
性能分析
辊压方案:门槛材料采用高强钢板 HC550/980DP,料厚为1.2mm,屈服强度为550~730MPa。
冲 压 方 案:门 槛 材 料 采 用 高 强 钢 板 HC420/780DP,料 厚为1.4mm,屈 服强度为420~550MPa。采用高强度辊压形式门槛有利于减轻车身质量,同时提高碰撞安全性能,且成本低于冲压形式。碰撞 CAE分析结果如图3所示。侧碰B柱CAE 分析考查位置如图4所示。从表4 CAE分析对比结果可以看出,B柱和前门侵入量辊压方案相对冲压方案侵入量减小,采用 HC550/980DP 辊压方案优势显著。
表4 辊压方案和冲压方案碰撞安全性能对比分析
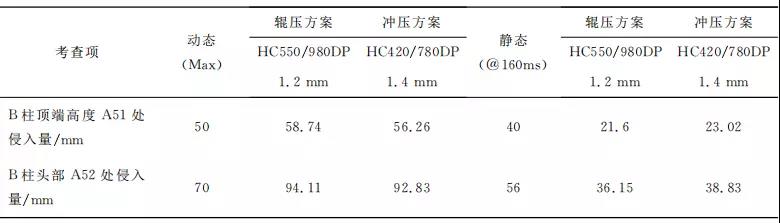
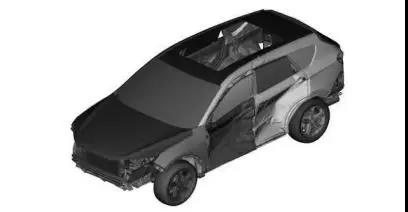
图3 碰撞CAE析结果
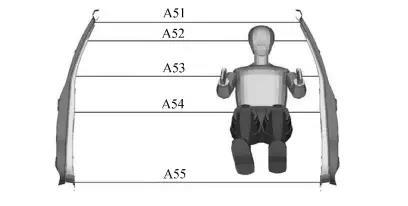
图4 侧碰B柱CAE分析考查位
通用化分析
辊压件截面、模具通用,有利于后续车型以及平台沿用,降低成本,减少固定投资,提高生产效率。
结论
门槛加强板采用冷冲压工艺,材料抗拉强度为78MPa,模具费昂贵;采用辊压工艺,材料抗拉强度为1000~1200MPa,并且料厚降低,满足车身轻量化,且横梁断面通用性更容易使同一种辊压断面可以适用于不同的车型,降低开发费用。在发生撞击时,尤其侧面撞击时, 可有效减少驾驶舱、乘员舱变形,保护驾乘人员的安全。辊压生产效率高,适合大批量生产,加工产品的长度基本不受限制,产品的精度高、一致性好,材料利用率高,设备投入低。
节选于《模具技术》
作者简介: 奇瑞商用车(安徽)有限公司 黄伟男,向志凌,吕进
在国外主流汽车厂商所开发的新车型中, 辊压型钢零部件已占到60%,而在我国轿车新车型中的用量仅为6%,因此有非常大的产业拓展空间。早期辊压型钢零部件主要应用在前防撞梁、车门上段等零件。但随着技术的不断成熟,应用范围不断扩展,辊压门槛的应用也越来越广泛。辊压门槛的长度基本不受限制,可实现不同车型同一零件的模块化设计,降低制造成本。如某品牌两款不同车型车门槛板(见图1、图 2)设计为同一截 面,材料牌号为HC50/980DP,抗拉强度为980MPa,两款车型共用同一生产线,实现了生产线共用。
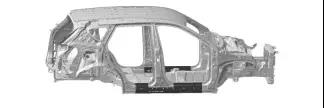
图1 车型1
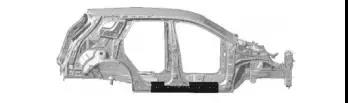
图2 车型2
同时辊压门槛生产效率高,适合于大批量生产,与冲压工艺相比,效率提高10倍以上,制造成本大幅降低。辊压门槛能解决冲压门槛产品回弹、褶皱以及壁翘曲难以控制、模具调试时间长等问题。
辊压门槛行业应用现状
辊压门槛在国外主流汽车厂商和合资品牌厂商应用较为广泛,比如上海通用、长安福特、上海大众等。
近年来,随着碰撞安全、车身轻量化要求的提升以及辊压工艺的发展成熟,自主品牌车型也在借鉴采用,特别的在长安汽车、奇瑞汽车等品牌厂商,都已经在新开发的车型上了采用了辊压门槛。表1为辊压门槛的应用实例。由表1可以看出,辊压门槛在门槛内板和门槛外板上都有所应用,但零件的牌号和料厚选择不尽相同。
表1 辊压门槛的应用实例
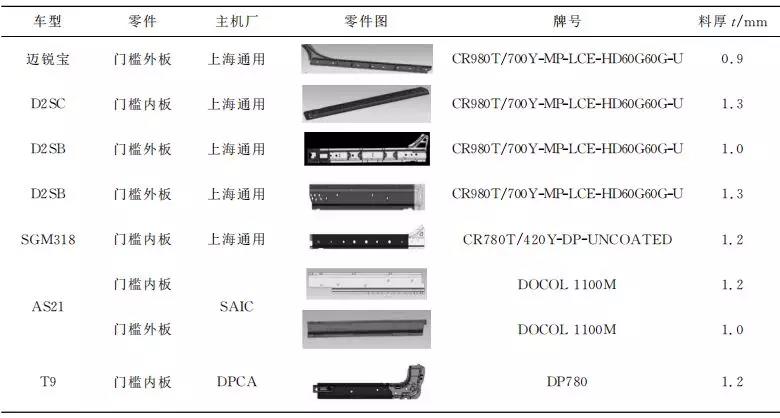
辊压门槛与传统冲压门槛对比分析
质量分析
对于门槛加强板,采 用冲压方案:料 厚为1.4mm,质量约8.90kg;采用辊压方案:料厚为1.2mm,质量约7.63kg。因此,门槛加强板采用辊压方案可以减重约1.27kg(见表2)。
表2 奇瑞某款车型辊压门槛与冲压门槛对比
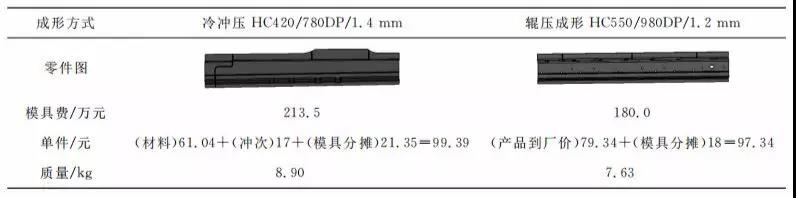
成本分析
辊压方案(包含材料、辊压线、检具)与冷冲压方案(含材料、模具、检具、冲次费)成本对比见表2。因此,门槛加强板采用辊压方案可以减少成本2.05单件/元。辊压门槛成本核算分析如表3所示。
表3 辊压门槛成本核算分析
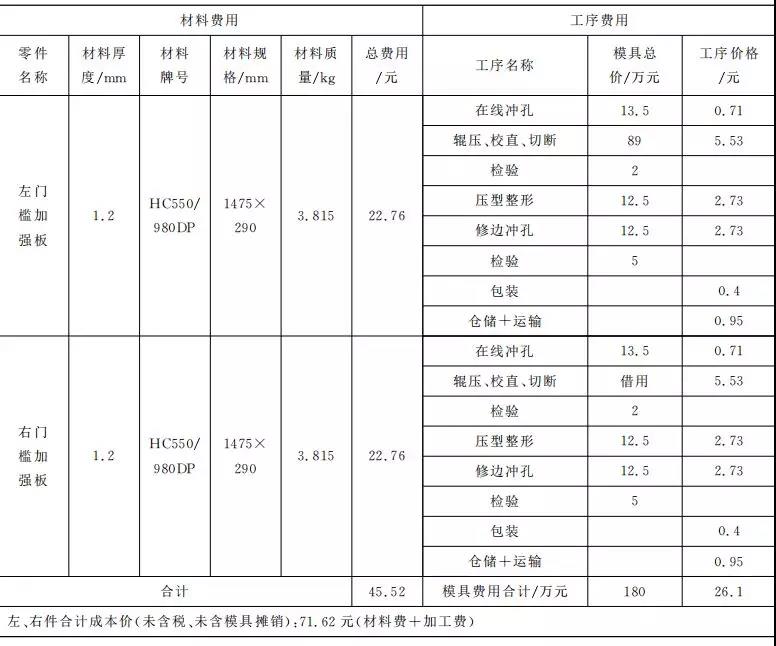
性能分析
辊压方案:门槛材料采用高强钢板 HC550/980DP,料厚为1.2mm,屈服强度为550~730MPa。
冲 压 方 案:门 槛 材 料 采 用 高 强 钢 板 HC420/780DP,料 厚为1.4mm,屈 服强度为420~550MPa。采用高强度辊压形式门槛有利于减轻车身质量,同时提高碰撞安全性能,且成本低于冲压形式。碰撞 CAE分析结果如图3所示。侧碰B柱CAE 分析考查位置如图4所示。从表4 CAE分析对比结果可以看出,B柱和前门侵入量辊压方案相对冲压方案侵入量减小,采用 HC550/980DP 辊压方案优势显著。
表4 辊压方案和冲压方案碰撞安全性能对比分析
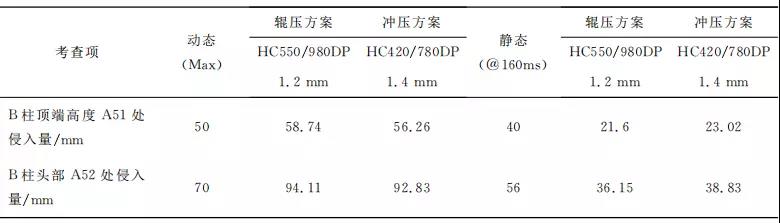
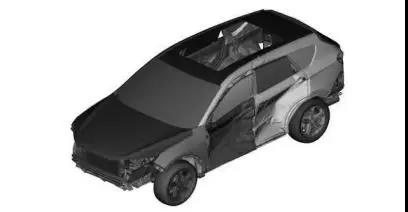
图3 碰撞CAE析结果
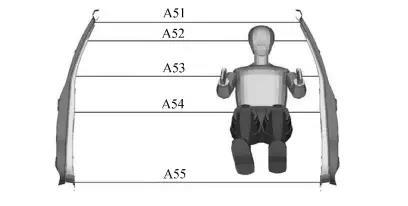
图4 侧碰B柱CAE分析考查位
通用化分析
辊压件截面、模具通用,有利于后续车型以及平台沿用,降低成本,减少固定投资,提高生产效率。
结论
门槛加强板采用冷冲压工艺,材料抗拉强度为78MPa,模具费昂贵;采用辊压工艺,材料抗拉强度为1000~1200MPa,并且料厚降低,满足车身轻量化,且横梁断面通用性更容易使同一种辊压断面可以适用于不同的车型,降低开发费用。在发生撞击时,尤其侧面撞击时, 可有效减少驾驶舱、乘员舱变形,保护驾乘人员的安全。辊压生产效率高,适合大批量生产,加工产品的长度基本不受限制,产品的精度高、一致性好,材料利用率高,设备投入低。
节选于《模具技术》
作者简介: 奇瑞商用车(安徽)有限公司 黄伟男,向志凌,吕进
最新资讯
-
中国车企服务出海先行者:新央企新长
2025-08-29 16:13
-
携手共赴“智”造未来!埃马克推动大
2025-08-27 18:12
-
京东工业发布汽车等九大行业场景采购
2025-08-26 18:11
-
制造现场推动节能革新,电装稳步迈向
2025-08-25 14:04
-
携手共赴“智”造未来!埃马克推动大
2025-08-22 19:41