自动化技术在冲压生产线建设中的应用
2018-06-06 09:43:37· 来源:文/孙逸仙 锻造与冲压
冲压自动化生产线是汽车覆盖件冲压生产的重要组成部分,在新建冲压生产线的前期规划中,要结合汽车覆盖件的生产特点,合理规划生产线的功能与主要设备。自动化生产线的优势主要体现在生产节拍的提升、冲压件成本的降低以及冲压件品质的提
冲压自动化生产线是汽车覆盖件冲压生产的重要组成部分,在新建冲压生产线的前期规划中,要结合汽车覆盖件的生产特点,合理规划生产线的功能与主要设备。自动化生产线的优势主要体现在生产节拍的提升、冲压件成本的降低以及冲压件品质的提高等。本文结合我厂冲压生产线的建设,阐述了自动化技术的应用对于效率提升、质量提升以及成本降低方面的贡献,供工艺设计人员参考。
生产线规划和设备选型
自动化生产线规划的背景
为适应产品设计大型化、集成化特点,满足高标准产品质量、制造成本降低、安全环保及职业健康等多方面要求,工厂原有手工生产线无法应对,需新建大型自动化冲压生产线来适应公司的发展需求。为此,规划建设了一条应对大型零件生产的冲压自动化生产线。
自动化生产线设备选型
冲压车间的生产工艺主要有冲压毛坯的生产和冲压覆盖件的生产,其他还有试模、模具维修、冲压件返修、废料输送等辅助工作。
压机设备的参数根据各车型零件的生产工艺确定,零件均在4序内完成冲压,A、B、C各车型最大零件的冲压力如表1所示。
根据上表冲裁力需求,为保障压力机设备能力持有约10%的成形余裕度,首台压力机选型2400t,后续三台压力机选型1000t。考虑车型零件品种数量较多,为了适应多规格品种零件的生产,增加生产线柔性,生产线搬运设备选用机器人,线首拆跺、上料及线尾下料采用6轴机器人,线间传输采用直线7轴机器人。全自动冲压生产线如图1所示。
表1 零件冲压成形/冲裁力需求分析表
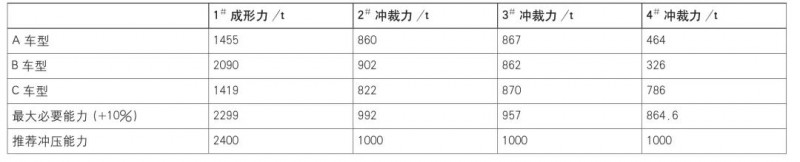
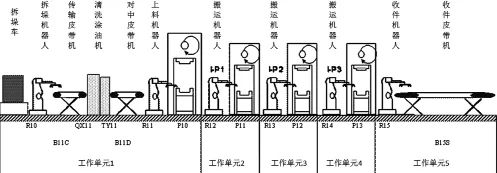
图1 1×2400t+3×1000t全自动冲压生产线
生产线自动化技术应用亮点
伺服液压拉深技术应用
传统生产方式采取气动拉深垫进行拉延平衡,无法实现灵活的设定和压力的精确稳定,无法保证大型、深拉延件的稳定生产,经常会发生零件质量波动,开裂等现象,需要大量涂抹拉延油以维持生产,带来了环境污染、涂装后处理困难、零件起皱等一系列问题,部分零件只能通过氮气缸弹簧压料、双动结构等模具设计来应对,但效果仍难以保证。
为满足我厂A、B、C等车型超大型深拉延件稳定生产,根据工厂多年技术经验的积累,尤其从A项目至C项目的工艺分析工作、同步工程工作形成的经验积累,对深拉延件的成形过程,条件需求形成了一定的规范,最终经过技术研讨,确定采用伺服液压拉深技术配置新建设的冲压自动化生产线。
首台2400t多连杆机械压力机,配置伺服液压拉深垫;后序3台为偏心式机械压力机,具备全线自动换模功能,伺服液压垫结构示意图如图2所示。
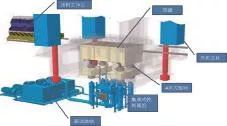
图2 伺服液压垫结构示意图
.jpg)
图3 前围挡板拉延模拟成形图
⑴驱动结构。驱动结构由四个活塞缸驱动布置在拉深垫顶罐的四角,通过独立PLC编程控制各点的压力值。从图3车型前围挡板CAE模拟结果可见,在零件基本对称设计的情况下,4点式压力输出已可以满足产品生产需要,不需中间输出点,这一原则基本可满足商用车大型覆盖件生产。
⑵伺服液压拉深技术的功能。
1)拉深压力灵活设定。液压拉深垫四点压力单独设定,数据可以存入压力机控制系统的模具参数数据库,在自动换模过程中与其他模具参数一起调出。
2)带预加速的拉深。伺服液压垫配置有预加速功能,在启动预加速功能时,拉深垫在滑块下降时不停留在上限位置,而是先于滑块向下移动。在运行30mm后,滑块赶上了拉深垫,继续运行,形成反力,拉深过程开始。拉深垫的返回运动与滑块同步或延迟回程,避免零件碰撞,方便取料,也可实现滑块下死点保压。液压拉深垫在不使用预加速功能的情况下,部分区域板料变形率不足如图4所示。在拉深过程中增加预加速功能后,板料变形变得相对均匀如图5所示。
预加速功能目前无法使用CAE方式进行模拟,我们通过参数置换等方式粗略模拟这种情况,该功能会提高生产的稳定性,拉延变形效果更均匀,最终根据压力机参数曲线完成预加速参数设计。
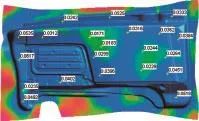
图4 未使用预加速功能的零件成形情况
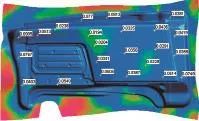
图5 使用预加速功能的零件成形情况
3)生产参数数字化控制。液压驱动系统状态与压力机PLC连接,可实现设定、状态监控、故障报警、数据实时反馈以及设定的生产参数调用等。采用伺服液压拉深技术可提高拉延件稳定性,返修率降低10%,废品率降低2%。对C车型部分零件而言,采用单动拉延设计、取消氮气弹簧,可节约模具投入约100万元。
自动化生产中板料上料对中系统
整线自动化包含线首、线间、线尾三个部分。线首通过采用视觉加机械对中系统,可有效提升可靠性和生产线柔性。线间配置的直线七轴机器人可大幅提升生产线节拍。线尾配置六轴机器人下料,在满足下料需求的前提下,可降低投资成本。
⑴柔性化对中系统组成。
1)一套独立安装的拍摄和照明系统(图6)。灯架安装在防护罩上与压力机等运动机构软连接,落地支撑在车间地坪上,避免振动。灯具选用LED节能灯,拍摄区域照度800Lux以上,广角高清摄像头拍摄范围2.5m×3m。
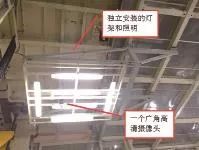
图6 照明系统示意图

图7 对中平台示意图
2)多条同步带组合限位检测的对中平台。图7所示对中皮带采用10条圆形同步带,单条独立变频驱动电机驱动,确保同步及到位准确,皮带间隔300mm,间隔区域内安装2组检测开关,控制皮带缓冲速度、停止。最前端设置翻转挡块,料宽大于300mm时,可防止板料送进过程意外飞出,主要用于调试阶段工人的安全保护。底色采用黑色整块2.5m×3m底板,与材料颜色形成对比,利于成像。
3)过渡工位。图8所示过渡工位布置在前段清洗涂油机和对中工位中间,用于承接前段板料处理,此时运行速度与清洗机速度匹配,同时用于给对中工位及时送料,此时速度与对中工位匹配,确保及时送料和控制板料初速度,速度指令有整线PLC根据送料逻辑发送,一次示教后自动调用。
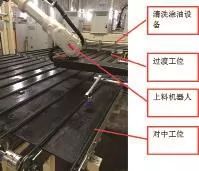
图8 过渡工位示意图
⑵柔性化对中系统优势。
该系统采用组合式的对中平台设计,确保板料到位精度,并适应任何形状的板料。双工位的对中设计,能有效确保整线上料节拍要求。圆形条式对中皮带组合机械式检测及可调式限位设计可准确保障板料的对中效果。
该系统与传统机械式对中系统相比,减少了20组可调式限位机构,节约投资成本约20万元。由于该系统的柔性化程度较高,可有效避免后期产品拓展时的设备改造和报废。
零件柔性搬运系统
零件在压力机之间的搬运采用直线7轴机器人,其技术优点总结如下:
⑴工件在生产过程中始终保持平行移动,无须旋转。这有益于提高工件在上下工序压力机之间的传递速度,进而提高生产线的效率,尤其是在生产“整体顶盖”等大型覆盖件时,优势更明显。
⑵工件在上下工序压力机之间传递时保持平行移动方式,可以使大型工件在较小的空间内传递,减小压力机之间的间距,也就减少整条冲压线在厂房内的占地面积,从而降低厂房的建设成本。
⑶采用直线七轴技术的机器人搬运系统适应性强,柔性化高。在该冲压自动线上,小至“侧围内板”,大至“整体顶盖”等冲压件均可以全自动化高效生产。
⑷配合大型机器人,直线七轴装置的有效负载能力强。在该冲压自动线上,配置直线七轴技术的机器人选用的是ABB IRB7600 325/3.1型机器人,直线七轴装置端部的负载能力可以达到90kg。减去端拾器和刚朵拉的重量,可以提供60kg的负载能力给冲压件,这已经足够满足商用车覆盖件的重量。
结束语
自动化技术在冲压生产线中的应用已非常成熟广泛,选择适应公司产品规划要求的工艺设备是首要考量的关注点,在选择生产线设备及功能配置时,如何运用自动化技术减少投资费用、降低后期设备维护费用、降低产品废品率,从而达到降低制造成本提升产品竞争力的目的,是我们应该重点考虑的问题。
——节选自《锻造与冲压》2018年第6期
生产线规划和设备选型
自动化生产线规划的背景
为适应产品设计大型化、集成化特点,满足高标准产品质量、制造成本降低、安全环保及职业健康等多方面要求,工厂原有手工生产线无法应对,需新建大型自动化冲压生产线来适应公司的发展需求。为此,规划建设了一条应对大型零件生产的冲压自动化生产线。
自动化生产线设备选型
冲压车间的生产工艺主要有冲压毛坯的生产和冲压覆盖件的生产,其他还有试模、模具维修、冲压件返修、废料输送等辅助工作。
压机设备的参数根据各车型零件的生产工艺确定,零件均在4序内完成冲压,A、B、C各车型最大零件的冲压力如表1所示。
根据上表冲裁力需求,为保障压力机设备能力持有约10%的成形余裕度,首台压力机选型2400t,后续三台压力机选型1000t。考虑车型零件品种数量较多,为了适应多规格品种零件的生产,增加生产线柔性,生产线搬运设备选用机器人,线首拆跺、上料及线尾下料采用6轴机器人,线间传输采用直线7轴机器人。全自动冲压生产线如图1所示。
表1 零件冲压成形/冲裁力需求分析表
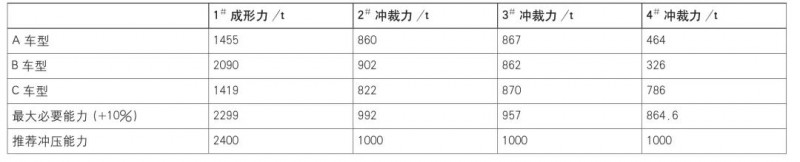
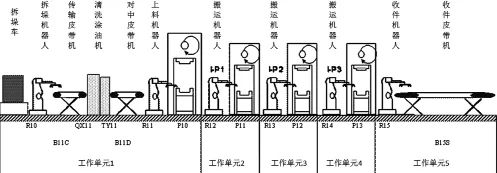
图1 1×2400t+3×1000t全自动冲压生产线
生产线自动化技术应用亮点
伺服液压拉深技术应用
传统生产方式采取气动拉深垫进行拉延平衡,无法实现灵活的设定和压力的精确稳定,无法保证大型、深拉延件的稳定生产,经常会发生零件质量波动,开裂等现象,需要大量涂抹拉延油以维持生产,带来了环境污染、涂装后处理困难、零件起皱等一系列问题,部分零件只能通过氮气缸弹簧压料、双动结构等模具设计来应对,但效果仍难以保证。
为满足我厂A、B、C等车型超大型深拉延件稳定生产,根据工厂多年技术经验的积累,尤其从A项目至C项目的工艺分析工作、同步工程工作形成的经验积累,对深拉延件的成形过程,条件需求形成了一定的规范,最终经过技术研讨,确定采用伺服液压拉深技术配置新建设的冲压自动化生产线。
首台2400t多连杆机械压力机,配置伺服液压拉深垫;后序3台为偏心式机械压力机,具备全线自动换模功能,伺服液压垫结构示意图如图2所示。
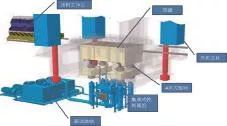
图2 伺服液压垫结构示意图
.jpg)
图3 前围挡板拉延模拟成形图
⑴驱动结构。驱动结构由四个活塞缸驱动布置在拉深垫顶罐的四角,通过独立PLC编程控制各点的压力值。从图3车型前围挡板CAE模拟结果可见,在零件基本对称设计的情况下,4点式压力输出已可以满足产品生产需要,不需中间输出点,这一原则基本可满足商用车大型覆盖件生产。
⑵伺服液压拉深技术的功能。
1)拉深压力灵活设定。液压拉深垫四点压力单独设定,数据可以存入压力机控制系统的模具参数数据库,在自动换模过程中与其他模具参数一起调出。
2)带预加速的拉深。伺服液压垫配置有预加速功能,在启动预加速功能时,拉深垫在滑块下降时不停留在上限位置,而是先于滑块向下移动。在运行30mm后,滑块赶上了拉深垫,继续运行,形成反力,拉深过程开始。拉深垫的返回运动与滑块同步或延迟回程,避免零件碰撞,方便取料,也可实现滑块下死点保压。液压拉深垫在不使用预加速功能的情况下,部分区域板料变形率不足如图4所示。在拉深过程中增加预加速功能后,板料变形变得相对均匀如图5所示。
预加速功能目前无法使用CAE方式进行模拟,我们通过参数置换等方式粗略模拟这种情况,该功能会提高生产的稳定性,拉延变形效果更均匀,最终根据压力机参数曲线完成预加速参数设计。
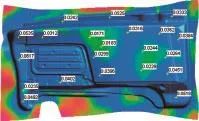
图4 未使用预加速功能的零件成形情况
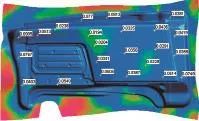
图5 使用预加速功能的零件成形情况
3)生产参数数字化控制。液压驱动系统状态与压力机PLC连接,可实现设定、状态监控、故障报警、数据实时反馈以及设定的生产参数调用等。采用伺服液压拉深技术可提高拉延件稳定性,返修率降低10%,废品率降低2%。对C车型部分零件而言,采用单动拉延设计、取消氮气弹簧,可节约模具投入约100万元。
自动化生产中板料上料对中系统
整线自动化包含线首、线间、线尾三个部分。线首通过采用视觉加机械对中系统,可有效提升可靠性和生产线柔性。线间配置的直线七轴机器人可大幅提升生产线节拍。线尾配置六轴机器人下料,在满足下料需求的前提下,可降低投资成本。
⑴柔性化对中系统组成。
1)一套独立安装的拍摄和照明系统(图6)。灯架安装在防护罩上与压力机等运动机构软连接,落地支撑在车间地坪上,避免振动。灯具选用LED节能灯,拍摄区域照度800Lux以上,广角高清摄像头拍摄范围2.5m×3m。
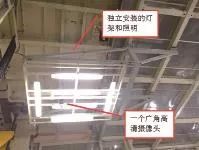
图6 照明系统示意图

图7 对中平台示意图
2)多条同步带组合限位检测的对中平台。图7所示对中皮带采用10条圆形同步带,单条独立变频驱动电机驱动,确保同步及到位准确,皮带间隔300mm,间隔区域内安装2组检测开关,控制皮带缓冲速度、停止。最前端设置翻转挡块,料宽大于300mm时,可防止板料送进过程意外飞出,主要用于调试阶段工人的安全保护。底色采用黑色整块2.5m×3m底板,与材料颜色形成对比,利于成像。
3)过渡工位。图8所示过渡工位布置在前段清洗涂油机和对中工位中间,用于承接前段板料处理,此时运行速度与清洗机速度匹配,同时用于给对中工位及时送料,此时速度与对中工位匹配,确保及时送料和控制板料初速度,速度指令有整线PLC根据送料逻辑发送,一次示教后自动调用。
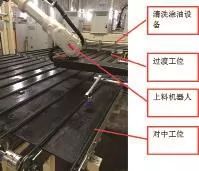
图8 过渡工位示意图
⑵柔性化对中系统优势。
该系统采用组合式的对中平台设计,确保板料到位精度,并适应任何形状的板料。双工位的对中设计,能有效确保整线上料节拍要求。圆形条式对中皮带组合机械式检测及可调式限位设计可准确保障板料的对中效果。
该系统与传统机械式对中系统相比,减少了20组可调式限位机构,节约投资成本约20万元。由于该系统的柔性化程度较高,可有效避免后期产品拓展时的设备改造和报废。
零件柔性搬运系统
零件在压力机之间的搬运采用直线7轴机器人,其技术优点总结如下:
⑴工件在生产过程中始终保持平行移动,无须旋转。这有益于提高工件在上下工序压力机之间的传递速度,进而提高生产线的效率,尤其是在生产“整体顶盖”等大型覆盖件时,优势更明显。
⑵工件在上下工序压力机之间传递时保持平行移动方式,可以使大型工件在较小的空间内传递,减小压力机之间的间距,也就减少整条冲压线在厂房内的占地面积,从而降低厂房的建设成本。
⑶采用直线七轴技术的机器人搬运系统适应性强,柔性化高。在该冲压自动线上,小至“侧围内板”,大至“整体顶盖”等冲压件均可以全自动化高效生产。
⑷配合大型机器人,直线七轴装置的有效负载能力强。在该冲压自动线上,配置直线七轴技术的机器人选用的是ABB IRB7600 325/3.1型机器人,直线七轴装置端部的负载能力可以达到90kg。减去端拾器和刚朵拉的重量,可以提供60kg的负载能力给冲压件,这已经足够满足商用车覆盖件的重量。
结束语
自动化技术在冲压生产线中的应用已非常成熟广泛,选择适应公司产品规划要求的工艺设备是首要考量的关注点,在选择生产线设备及功能配置时,如何运用自动化技术减少投资费用、降低后期设备维护费用、降低产品废品率,从而达到降低制造成本提升产品竞争力的目的,是我们应该重点考虑的问题。
——节选自《锻造与冲压》2018年第6期
举报 0
收藏 0
分享 129
-
乘用车金属冲压
2025-05-29 -
冲压技术在电机叠片制造的应用
2024-09-06 -
车身零部件包边质量控制要点
2024-09-05 -
轻量化技术——热汽胀形工艺技术解析
2024-09-04
最新资讯
-
辐射亚太,链接全球——采埃孚再制造
2025-07-30 11:46
-
思看科技发布子品牌SCANOLOGY,全球
2025-07-30 11:06
-
风雨不动安如山——比亚迪叉车构筑“
2025-07-30 08:48
-
NEAS CHINA 新能源汽车技术与生态链
2025-07-29 09:52
-
三维扫描革新碾磨机辊套检测,效率与
2025-07-25 10:46