汽车后视镜镜壳注塑模设计
2018-04-09 08:25:51· 来源:CAE技术资讯 作者:邓成林
汽车后视镜是汽车外饰件的重要组成部分,位于汽车的两侧,是汽车最重要的外饰件之一。汽车后视镜是用来让驾驶人员在驾驶过程中观测路面状况的一个装置,可以说是驾驶员的眼睛。汽车后视镜一般由镜圈,基座,镜壳,支架,旋转轴等零件组成。
1 前言
汽车后视镜是汽车外饰件的重要组成部分,位于汽车的两侧,是汽车最重要的外饰件之一。汽车后视镜是用来让驾驶人员在驾驶过程中观测路面状况的一个装置,可以说是驾驶员的眼睛。汽车后视镜一般由镜圈,基座,镜壳,支架,旋转轴等零件组成。
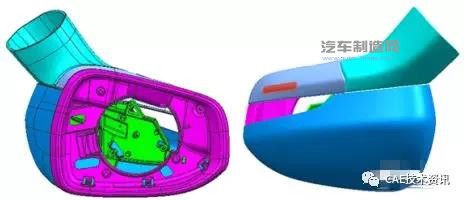
图1 汽车后视镜构造图
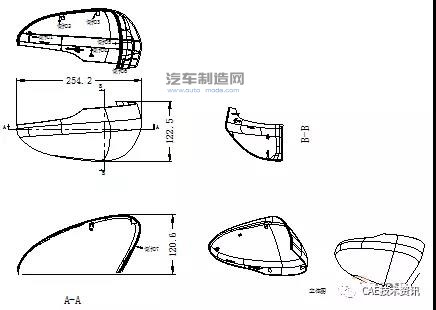
图2 汽车后视镜镜壳零件图
图1所示零件为品牌汽车福特蒙迪欧的后视镜,本文以汽车后视镜镜壳为例,分析介绍汽车后视镜零件模具的设计要点与经验。汽车后视镜镜壳零件图如图2所示。
2 塑件外观要求与结构分析
图2所示为福特蒙迪欧汽车后视镜镜壳零件图,材料为ABS,收缩率一般取1.005,塑件为左右镜像件,模具型腔数为1+1。塑件为外观件,是汽车最重要的外饰件之一。塑件尺寸为:254.2*122.5*120.6mm。塑件特点如下:(1)塑件外观面不允许有斑点,浇口痕迹,更不允许有收缩凹陷.熔接痕.飞边等缺陷。(2)塑件为外饰件,塑件外观高配为细纹件,低配为喷漆件,外观要求极高。(3)塑件外形复杂,外观夹线要求极高,塑件外侧面有1个大面积倒扣,内侧面有6个倒扣,倒扣多且面积大,是汽车后视镜模具的典型结构。
3 模具结构分析
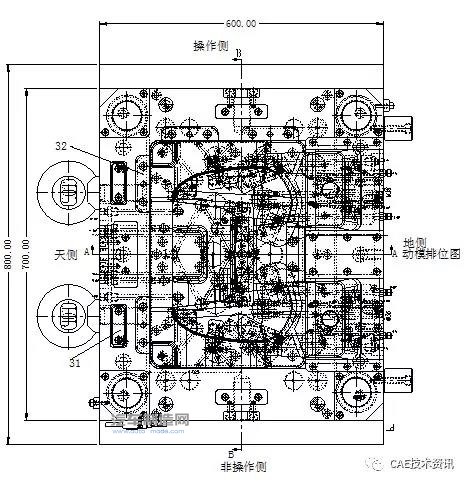
图3 汽车后视镜镜壳注塑模具结构图1
根据镜壳塑件的结构特点,模具优先采用热流道注塑模结构,采用1点开放式+冷流道+香蕉式浇口(俗称牛角)。图2所示塑件内外侧面有7个倒扣,本模具部分倒扣面积大且倒扣多。本模具内侧面4个倒扣均采用斜推块抽芯的结构,倒扣5,倒扣6由于倒扣面积大,故采用斜推块+直推块组合的结构,对于此类镜壳模具,塑件顶出脱模后只能采用手工取件的方式,前提是取件时一定要有手工取件掰的空间。塑件外侧面由于出模方向是倾斜的,故均采用斜滑块抽芯结构。本模具外形尺寸为:800*600*647(mm),总重量约0.9吨,属于中型注塑模具。详细结构见图3-图5。
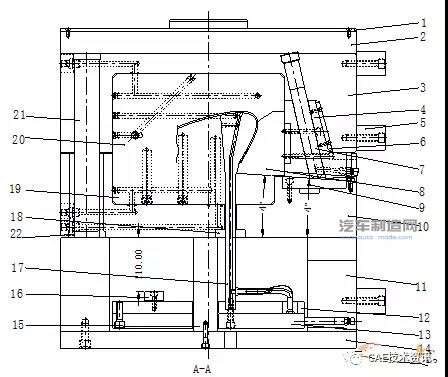
图4 汽车后视镜镜壳注塑模具结构图2
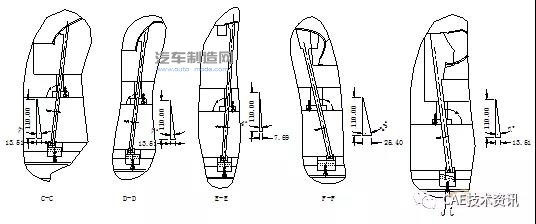
图5 汽车后视镜镜壳注塑模具结构图3
3.1 成型零件设计
本模具定动模采用镶拼式,常用材料为:2344。定动模为同一种材料,在材料订购时,要注明动模硬度比定模小2度左右,避免硬度一样,因为定动模硬度一致会使模具容易磨损与插烧。成型零件设计的原则是在保证模具强度和寿命的前提下尺寸做到最小,以降低模具的制造成本和生产成本。本车型后视镜模具使用寿命为30万次,因而材料采用2344。
3.2 浇注系统设计
本模具浇注系统采用热流道进胶,采用1点开放式热流道+冷流道+香蕉式浇口的进胶方式,塑件材料为ABS。
由于塑件为ABS料,材料流动性较好,在设计流道时流道设计范围广些,但热嘴至塑件边缘的流道长度尽量设计在60mm以内,如果实在不行也尽量控制在100mm以内,避免冷流道过长与避免压力损失大。汽车后视镜镜壳注塑模热流道浇口位置见图6所示 。
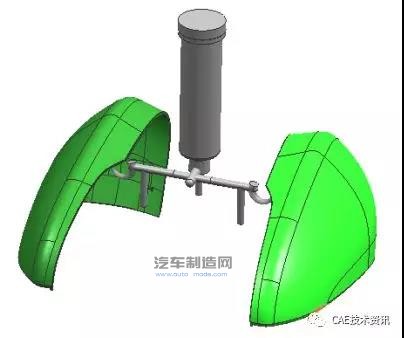
图6 1点开放式热流道控制系统
3.3 侧向抽芯机构设计
侧向抽芯机构是本模具最重要的结构之一。针对塑件外侧的倒扣7,模具采用了斜滑块的抽芯机构,抽芯方向见图2.图3。本模具优先将斜滑块设计在地侧,斜滑块由于自身的重量,斜导柱抽芯时滑块会往地侧下掉,因而不需要设计弹簧。塑件内侧面倒扣1-倒扣4均采用斜推块抽芯的结构,倒扣5,倒扣6由于倒扣面积大,故采用斜推块+直推块组合的结构,对于此类镜壳模具,塑件顶出脱模后只能采用手工取件的方式,前提是取件时一定要有手工取件掰的空间。
3.4 温度控制系统设计
汽车后视镜镜壳为外饰件,外观要求极高,因此温度控制系统设计的好坏对模具的成型周期与塑件成型质量影响很大。冷却水道设计原则之一是距离型腔面要大致相等,以达到模具型腔各处温度大致均衡。本模具的温度控制系统采用了“直通式水管+倾斜式水路+水井”的组合形式(见图7和图8)。这种组合形式是优先采用直通式水管,其次是采用倾斜式水路,最后采用水井。其优点是塑件冷却均匀,成型周期短,成型质量高,适用于高要求与外观性能要求高的模具。
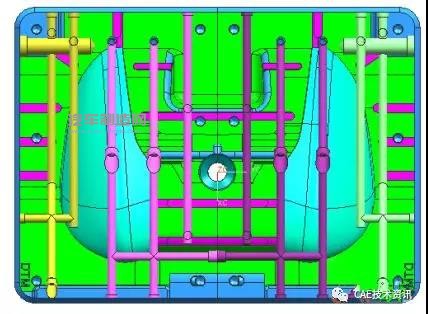
图7 (a)定模冷却系统
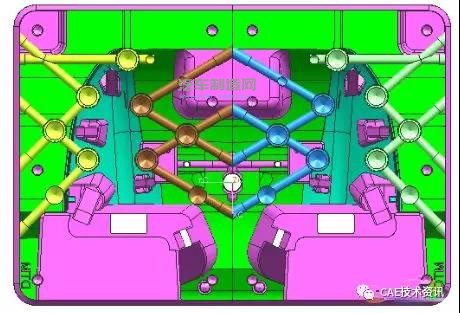
图8 (b)动模冷却系统
汽车模具冷却水道排布按以下规律设计:1.冷却水方向要与料流方向一致。2.定.动模冷却水道优先设计成十字网格形式,冷却回路形成互相交叉形成水路交织网,均匀冷却塑件。3.在不能设计成十字交叉式水路时,定.动模水路在互相有缝隙处交互布置。4.每一组冷却水尽量只设计四条循环水路,避免水路距离长影响塑件冷却效果。5.冷却水路要设计成可与另一组水路进行外部接水管连接的方式,方便后续塑件因变形.收缩等现象的调整。通过水路调整塑件缺陷,在汽车内外饰塑件模具上应用广泛。6.各冷却水道间隔距离控制在水道的3.5-5倍直径(一般50-60mm左右),塑件胶位面距离运水的距离一般在15-25mm之间,具体根据模具大小决定。7.冷却水道与推杆.斜推杆.镶件之间的距离要保证在8-10mm以上,因为模具大且水道长,容易钻偏。8.在汽车模具设计中,热嘴尽量要单独设计一组水路,不能与其它水路串联,以利于热嘴区域的热量散失。
本模具定动模温度控制系统为:定动模都设计了4组水路,每个模腔各设计2组水路,定动模都是4进4出,模具冷却水路设计做到了与料流方向一致,采用:“直通式水管+倾斜式水路+水井”的设计形式,进出水距离做到了大致相等,因而使塑件得到了良好的冷却效果与外观质量。本模具斜滑块,以及倒扣5处侧向抽芯投影面积大,热量集中,因而斜滑块与直推块上设计了冷却水,对斜滑块,直推块处胶位进行了重点冷却。
3.5 脱模系统设计
本模具为“推杆+推块+斜推块”结构,模具在定.动模开模后,依靠推件推出塑件与流道,推件固定板由注塑机通过油缸推动和在4支复位杆的作用下复位。在设计脱模系统时要注意以下几点:1.大型模具(长宽方向超过1400mmX700mm)需设计6支复位杆与6支推杆板导柱,所有汽车模具复位杆上要设计一比复位杆大一级的回复块,回复块一般选45#(S50C)氮化处理。推杆板导柱要布置在推出力大的推出元件附近(如油缸.复位杆等)。2.所有汽车模具需要设计限位柱,限位柱要优先布置在KO孔上方或附近。推杆要排布在靠近R处的受力位置,布置在包紧力大的位置,推杆设计要大,推杆布置要多些,设计推杆尽量设计成同一规格,不要设计很多种规格,这样可以避免频繁更换钻嘴,节省加工时间与加工成本。
4 模具工作过程
熔体通过注塑机喷嘴,经热嘴23进入模具型腔,熔体充满型腔后,经保压、冷却和固化,至足够刚性后,注塑机拉动模具的动模固定板14,模具从分型面PLⅠ处开模。开模300mm后,注塑机油缸推动推件固定板12,推件固定板推动推杆30,接着油缸继续作用,继续推出60mm,推动所有推件将成型塑件推离动模。塑件取出后,注塑机油缸拉动推件及其固定板复位,接着注塑机推动动模合模,模具开始下一次注射成型。
5 结果与讨论
本模具采用推杆+推块+斜推块推出的脱模机构,这是汽车后视镜镜壳模具的典型结构,设计本类模具要注意,这种结构必须是手工取件,手工取件需要取件时手工掰出塑件,对于这类塑件,塑件必须要有摆动的空间。这种依靠手工掰出的塑件,在汽车模具设计中也不少,如汽车转向柱,油门盖等。
汽车后视镜是汽车外饰件的重要组成部分,位于汽车的两侧,是汽车最重要的外饰件之一。汽车后视镜是用来让驾驶人员在驾驶过程中观测路面状况的一个装置,可以说是驾驶员的眼睛。汽车后视镜一般由镜圈,基座,镜壳,支架,旋转轴等零件组成。
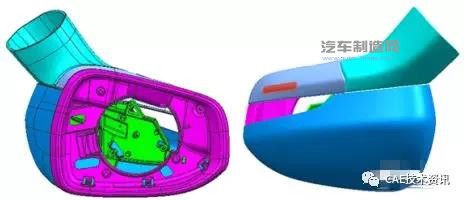
图1 汽车后视镜构造图
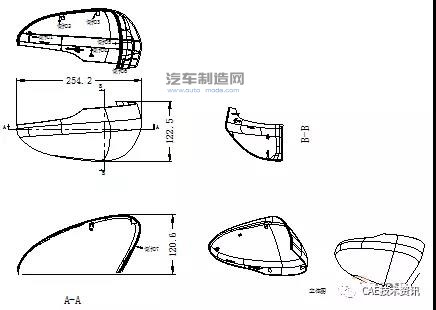
图2 汽车后视镜镜壳零件图
图1所示零件为品牌汽车福特蒙迪欧的后视镜,本文以汽车后视镜镜壳为例,分析介绍汽车后视镜零件模具的设计要点与经验。汽车后视镜镜壳零件图如图2所示。
2 塑件外观要求与结构分析
图2所示为福特蒙迪欧汽车后视镜镜壳零件图,材料为ABS,收缩率一般取1.005,塑件为左右镜像件,模具型腔数为1+1。塑件为外观件,是汽车最重要的外饰件之一。塑件尺寸为:254.2*122.5*120.6mm。塑件特点如下:(1)塑件外观面不允许有斑点,浇口痕迹,更不允许有收缩凹陷.熔接痕.飞边等缺陷。(2)塑件为外饰件,塑件外观高配为细纹件,低配为喷漆件,外观要求极高。(3)塑件外形复杂,外观夹线要求极高,塑件外侧面有1个大面积倒扣,内侧面有6个倒扣,倒扣多且面积大,是汽车后视镜模具的典型结构。
3 模具结构分析
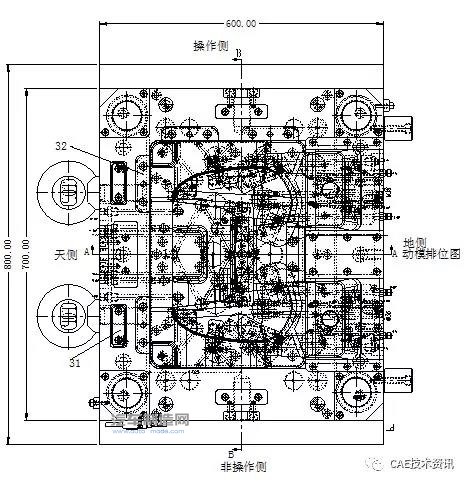
图3 汽车后视镜镜壳注塑模具结构图1
根据镜壳塑件的结构特点,模具优先采用热流道注塑模结构,采用1点开放式+冷流道+香蕉式浇口(俗称牛角)。图2所示塑件内外侧面有7个倒扣,本模具部分倒扣面积大且倒扣多。本模具内侧面4个倒扣均采用斜推块抽芯的结构,倒扣5,倒扣6由于倒扣面积大,故采用斜推块+直推块组合的结构,对于此类镜壳模具,塑件顶出脱模后只能采用手工取件的方式,前提是取件时一定要有手工取件掰的空间。塑件外侧面由于出模方向是倾斜的,故均采用斜滑块抽芯结构。本模具外形尺寸为:800*600*647(mm),总重量约0.9吨,属于中型注塑模具。详细结构见图3-图5。
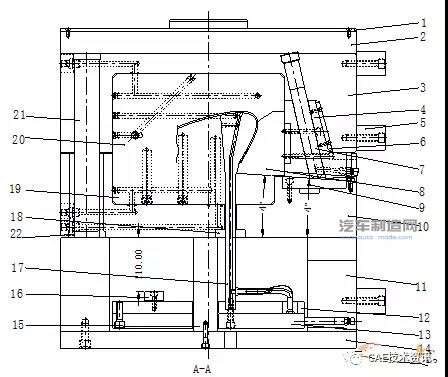
图4 汽车后视镜镜壳注塑模具结构图2
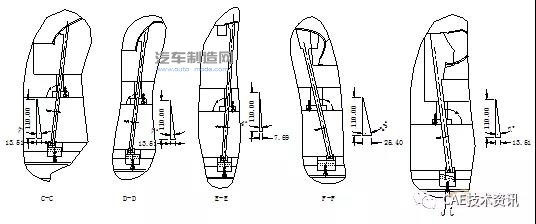
图5 汽车后视镜镜壳注塑模具结构图3
3.1 成型零件设计
本模具定动模采用镶拼式,常用材料为:2344。定动模为同一种材料,在材料订购时,要注明动模硬度比定模小2度左右,避免硬度一样,因为定动模硬度一致会使模具容易磨损与插烧。成型零件设计的原则是在保证模具强度和寿命的前提下尺寸做到最小,以降低模具的制造成本和生产成本。本车型后视镜模具使用寿命为30万次,因而材料采用2344。
3.2 浇注系统设计
本模具浇注系统采用热流道进胶,采用1点开放式热流道+冷流道+香蕉式浇口的进胶方式,塑件材料为ABS。
由于塑件为ABS料,材料流动性较好,在设计流道时流道设计范围广些,但热嘴至塑件边缘的流道长度尽量设计在60mm以内,如果实在不行也尽量控制在100mm以内,避免冷流道过长与避免压力损失大。汽车后视镜镜壳注塑模热流道浇口位置见图6所示 。
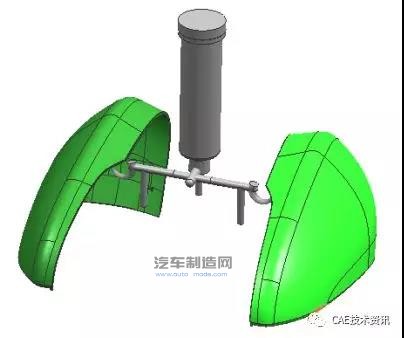
图6 1点开放式热流道控制系统
3.3 侧向抽芯机构设计
侧向抽芯机构是本模具最重要的结构之一。针对塑件外侧的倒扣7,模具采用了斜滑块的抽芯机构,抽芯方向见图2.图3。本模具优先将斜滑块设计在地侧,斜滑块由于自身的重量,斜导柱抽芯时滑块会往地侧下掉,因而不需要设计弹簧。塑件内侧面倒扣1-倒扣4均采用斜推块抽芯的结构,倒扣5,倒扣6由于倒扣面积大,故采用斜推块+直推块组合的结构,对于此类镜壳模具,塑件顶出脱模后只能采用手工取件的方式,前提是取件时一定要有手工取件掰的空间。
3.4 温度控制系统设计
汽车后视镜镜壳为外饰件,外观要求极高,因此温度控制系统设计的好坏对模具的成型周期与塑件成型质量影响很大。冷却水道设计原则之一是距离型腔面要大致相等,以达到模具型腔各处温度大致均衡。本模具的温度控制系统采用了“直通式水管+倾斜式水路+水井”的组合形式(见图7和图8)。这种组合形式是优先采用直通式水管,其次是采用倾斜式水路,最后采用水井。其优点是塑件冷却均匀,成型周期短,成型质量高,适用于高要求与外观性能要求高的模具。
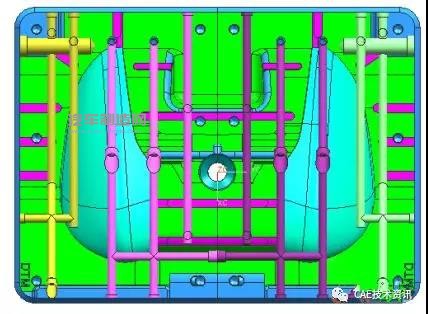
图7 (a)定模冷却系统
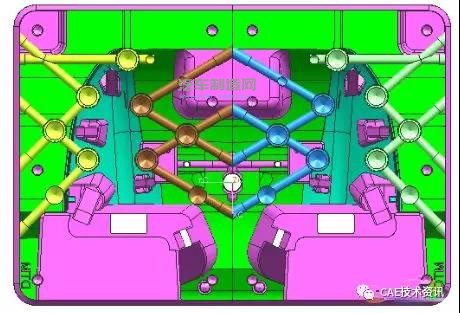
图8 (b)动模冷却系统
汽车模具冷却水道排布按以下规律设计:1.冷却水方向要与料流方向一致。2.定.动模冷却水道优先设计成十字网格形式,冷却回路形成互相交叉形成水路交织网,均匀冷却塑件。3.在不能设计成十字交叉式水路时,定.动模水路在互相有缝隙处交互布置。4.每一组冷却水尽量只设计四条循环水路,避免水路距离长影响塑件冷却效果。5.冷却水路要设计成可与另一组水路进行外部接水管连接的方式,方便后续塑件因变形.收缩等现象的调整。通过水路调整塑件缺陷,在汽车内外饰塑件模具上应用广泛。6.各冷却水道间隔距离控制在水道的3.5-5倍直径(一般50-60mm左右),塑件胶位面距离运水的距离一般在15-25mm之间,具体根据模具大小决定。7.冷却水道与推杆.斜推杆.镶件之间的距离要保证在8-10mm以上,因为模具大且水道长,容易钻偏。8.在汽车模具设计中,热嘴尽量要单独设计一组水路,不能与其它水路串联,以利于热嘴区域的热量散失。
本模具定动模温度控制系统为:定动模都设计了4组水路,每个模腔各设计2组水路,定动模都是4进4出,模具冷却水路设计做到了与料流方向一致,采用:“直通式水管+倾斜式水路+水井”的设计形式,进出水距离做到了大致相等,因而使塑件得到了良好的冷却效果与外观质量。本模具斜滑块,以及倒扣5处侧向抽芯投影面积大,热量集中,因而斜滑块与直推块上设计了冷却水,对斜滑块,直推块处胶位进行了重点冷却。
3.5 脱模系统设计
本模具为“推杆+推块+斜推块”结构,模具在定.动模开模后,依靠推件推出塑件与流道,推件固定板由注塑机通过油缸推动和在4支复位杆的作用下复位。在设计脱模系统时要注意以下几点:1.大型模具(长宽方向超过1400mmX700mm)需设计6支复位杆与6支推杆板导柱,所有汽车模具复位杆上要设计一比复位杆大一级的回复块,回复块一般选45#(S50C)氮化处理。推杆板导柱要布置在推出力大的推出元件附近(如油缸.复位杆等)。2.所有汽车模具需要设计限位柱,限位柱要优先布置在KO孔上方或附近。推杆要排布在靠近R处的受力位置,布置在包紧力大的位置,推杆设计要大,推杆布置要多些,设计推杆尽量设计成同一规格,不要设计很多种规格,这样可以避免频繁更换钻嘴,节省加工时间与加工成本。
4 模具工作过程
熔体通过注塑机喷嘴,经热嘴23进入模具型腔,熔体充满型腔后,经保压、冷却和固化,至足够刚性后,注塑机拉动模具的动模固定板14,模具从分型面PLⅠ处开模。开模300mm后,注塑机油缸推动推件固定板12,推件固定板推动推杆30,接着油缸继续作用,继续推出60mm,推动所有推件将成型塑件推离动模。塑件取出后,注塑机油缸拉动推件及其固定板复位,接着注塑机推动动模合模,模具开始下一次注射成型。
5 结果与讨论
本模具采用推杆+推块+斜推块推出的脱模机构,这是汽车后视镜镜壳模具的典型结构,设计本类模具要注意,这种结构必须是手工取件,手工取件需要取件时手工掰出塑件,对于这类塑件,塑件必须要有摆动的空间。这种依靠手工掰出的塑件,在汽车模具设计中也不少,如汽车转向柱,油门盖等。
编辑推荐
最新资讯
-
数智破局启新篇・生态共生再启程 —
2025-06-27 20:13
-
助力汽车零部件产线智能化升级,西门
2025-06-27 13:59
-
BBA集体转向!放弃全面电动化
2025-06-26 17:32
-
比换柜省钱,比自研省心,西门子Xcel
2025-06-25 15:07
-
采埃孚售后再制造中心乔迁临港 领航
2025-06-25 14:44