镗杆的加工工艺过程
2017-12-19 16:06:03· 来源:《金属加工(冷加工)》杂志
镗杆是机床中的主要核心部件之一,依靠两个导向键导向,作前后轴向移动, 实现轴向进给,同时由空心主轴通过对键传动转矩作回转运动,实现周向旋转。镗杆是机床主运动的核心,它的制造质量对机床工作性能的好坏有极其重要的影响。因此,分析研究镗杆的加工工艺过程,对机床发挥其加工的可靠性、稳定性和优质性有极其重要的意义。
镗杆是机床中的主要核心部件之一,依靠两个导向键导向,作前后轴向移动, 实现轴向进给,同时由空心主轴通过对键传动转矩作回转运动,实现周向旋转。镗杆是机床主运动的核心,它的制造质量对机床工作性能的好坏有极其重要的影响。因此,分析研究镗杆的加工工艺过程,对机床发挥其加工的可靠性、稳定性和优质性有极其重要的意义。
镗杆材料的选用
镗杆是主传动的主要部件,需要具有很高的抗弯性、耐磨性及抗冲击韧性等机械性能,这就要求镗杆在心部具有足够韧性的同时,表面还要有足够的硬度。38CrMoAlA这种优质合金结构钢的含碳量使钢材具有足够的强度,而Cr、Mo、Al等合金元素能与碳形成复杂的弥散相,均匀地分布在基体中,当受到外应力作用时,起到机械阻碍作用而强化。其中,Cr的加入可显著提高氮化层的硬度,提高钢的淬透性及心部强度;Al的加入可显著提高氮化层的硬度和细化晶粒;Mo主要消除钢材的回火脆性。经过多年的试验及探究,38CrMoAlA能够满足镗杆的主要性能要求,也是目前镗杆材料的首选。
镗杆热处理安排及作用
热处理安排: 正火+调质+氮化。镗杆氮化是热处理工艺中最后一道工序,为使镗杆心部具有必要的机械性能, 消除加工应力, 减少氮化过程的变形, 以及为获得最好的氮化层作组织准备,故镗杆在氮化前需要进行适当的预先热处理,即正火和调质。
(1)正火。正火处理是将钢件加热到临界温度以上,保温一段时间,然后用空气冷却,冷却速度比较快,经正火后,正火组织为块状“铁素体+珠光体”,零件组织得到细化,增加强度与韧性,较少内应力,改善切削性能。正火前不需要冷加工,但正火处理所产生的氧化脱碳层将导致氮化后脆性增加及硬度不足等弊病,故正火工序应留有足够的加工余量。
(2)调质。正火后加工量很大,切削后将产生很大的机械加工应力,为了消除粗加工后的机械加工应力,减少氮化过程中的变形,粗加工后增加一次调质处理是很有必要的。调质是淬火后高温回火,获得的组织是细密的索氏体。经调质后的零件具有足够的韧性和强度,很多重要的零件都需要经过调质处理。
(3)正火基体组织与“正火+调质”基体组织的区别。正火后的基体组织是块状的铁素体和珠光体(见图1),而“正火+调质”后的基体组织是细密的索氏体组织(见图2)。
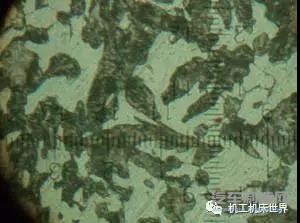
图1 正火基体组织
.jpg)
图2 “正火+调质”基体组织
(4)氮化。氮化是使零件表层有高的硬度和耐磨性,而心部保持原有的强度和韧性的热处理方法, 含有铬、钼或铝的钢采用氮化处理后会获得比较理想的效果。工件氮化后质量:① 工件表面呈银灰色无光泽。②工件表面硬度≥1 000HV,磨削后表面硬度≥900HV。③氮化层深度≥0.56mm,磨削后深度>0.5mm。④氮化变形要求振摆≤0.08mm。⑤脆性1~2级为合格,现实生产中都能达到,经研磨后更好。
(5)“正火+氮化”与“正火+调质+氮化”的组织区别。从图3~图6可见,“正火+调质+氮化”的氮化效果明显优于“正火+氮化”的氮化效果。“正火+氮化”的氮化组织中,有明显的块状、粗针状脆性氮化物存在,这一点也可以作为分析镗杆有时出现氮化层脱落现象的参考(见图7)。
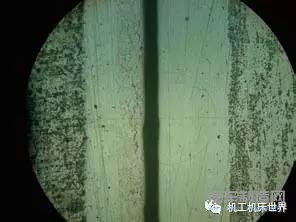
图3 “正火+氮化”层深0.60mm,并可见脉状脆性氮化物(左)“正火+调质+氮化”层深0.68mm(右)
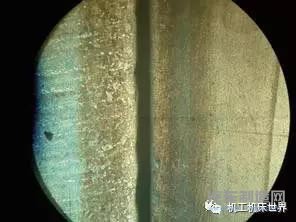
图4 “正火+氮化”氮化组织中有快状、针状脆性氮化物(左)“正火+调质+氮化”组织细密,无明显脆性氮化物(右)
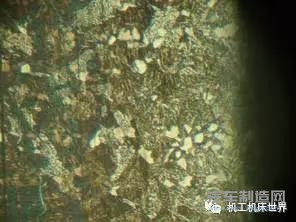
图5 “正火+氮化”显微镜下(500×)金相组织块状、针状脆性氮化物
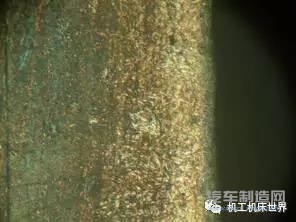
图6 “正火+调质+氮化”显微镜下(500×)金相组织,无明显脆性氮化物
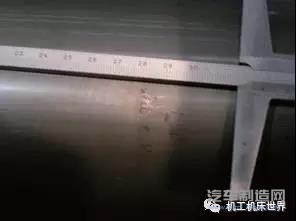
图7 镗杆氮化层脱落照片镗杆的精加工
(1)以镗杆Z104339为例,镗杆的精度要求如图8所示。

图 8
(2)工艺过程:下料→正火→钻粗车用中心孔→粗车→调质→半精车→粗磨外圆→粗磨锥孔→划→铣各槽→探伤→粗磨对键槽(留精磨量)→半精磨外圆→半精磨里孔→氮化→半精磨锥孔(留精磨量)→半精磨外圆(留精磨量)→磨对键槽→精磨外圆→精磨锥孔→研磨外圆→抛光→钳。
( 3 ) 镗杆精加工工艺过程。由于镗杆需要经过氮化处理,故特意安排两次半精磨外圆工序。第一次半精磨安排在氮化前,目的为氮化处理打好基础。主要是控制镗杆磨前余量和几何精度,以保证氮化后氮化层硬度在900HV以上。氮化时虽然弯曲变形较小,但绝不能校正氮化前的变形,否则只能比原来变形更大。我厂工艺确定,第一次半精磨时外圆留量为0.07~0.1mm,第二次半精磨外圆工序安排在精磨锥孔后进行。该工序在锥孔内装上磨芯,两端顶好,一端顶镗杆小头端面中心孔,一端顶磨芯中心孔,再用形式中心架架好磨外圆,不卸磨芯,转花键磨床磨对键槽。第二次半精磨外圆就是为了使后来精磨外圆时产生的内应力首先反映出来,这样精磨对键槽的精度会提高, 也比较稳定,又因有半精磨外圆的基础,精磨外圆时对键槽的影响就很小了。
我厂精磨对键槽使用的是花键磨床,一端顶镗杆小头端面中心孔,一端顶磨芯中心孔。这样磨削时键槽向上,外圆的弯曲变形及机床导轨的直线度只影响槽底,对槽两侧面影响不大。如果使用导轨磨床加工,则由于机床导轨直线度及镗杆自重,引起的变形会影响键槽直线度,一般情况下,使用花键磨床容易达到对键槽的直线度、平行度等各项要求,如图9所示。
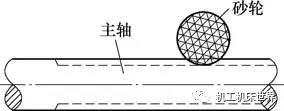
图9 花键磨床磨对键槽
镗杆外圆精磨是在万能磨上进行,采用方法是纵向走刀中心磨削法。
锥孔的跳动是镗床的一项主要成品精度。锥孔加工最终要求:①锥孔对外径跳动应保证在主轴端部0.005mm,在距离端部300mm处为0.01mm。②锥孔的接触面积为70%。③锥孔表面粗糙度值Ra=0.4μm。锥孔精加工方法:一是留余量,然后由装配自磨而使锥孔的接触达到最后成品精度;二是加工过程中直接达到技术要求。我厂现采用第二种方法,其做法是用卡帽卡镗杆后端M76X2—5g,前端用中心架架外圆φ 110h8MF,用千分表按外圆φ 80js6找正,磨锥孔。
研磨抛光是镗杆最后光整加工。研磨可以获得很高的尺寸精度和很低的表面粗糙度。一般来说,研磨工具的材料比工件材料要软,且组织均匀。最常用的是铸铁研具(见图10),适用于加工各种工件材料和精研加工,能保证较好的研磨质量和较高的生产率, 并且研具制造容易,成本也较低。在研磨过程中,研磨液不仅起调和磨料及润滑冷却作用,而且还起着化学作用,加速研磨过程。它会附着在工件表面,使工件表面很快产生一层氧化膜, 并起到磨平工件表面凸峰,保护工件表面凹谷作用。镗杆研磨时所使用的研磨剂成份为白色氧化铝的白刚玉粉和煤油的混合剂。
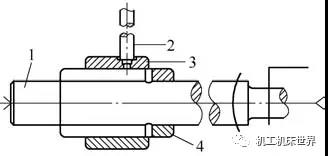
图 10
镗杆经研磨后尽管取得较好的尺寸精度及较低的表面粗糙度,但其表面出现嵌砂,并呈乌黑色,镗杆与空心主轴装配后,有黑水流出现象。为消除镗杆表面的研磨嵌砂,我厂采用自制的抛光具,对镗杆表面涂绿色的氧化铬进行抛光加工,实际效果非常好,镗杆表面光亮美观且防腐蚀。
镗杆的检测
(1)检测直线度。在0级平台上放置一对等高的V形铁。将镗杆放在V形铁上,V形铁所占的位置在φ 110h8MF的2/9L处(见图11)。镗杆全长直线度允差为0.01mm。
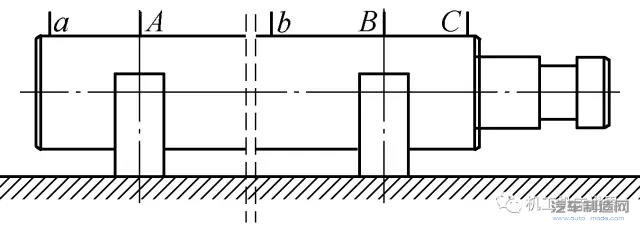
图11 检测镗杆直线度
首先用千分表检测2/9L两点A、B处的等高性,A、B两点的读表数值为0。然后,镗杆不动,测中间和两端点a、b、c三点高度,记上数值(见表1);保持镗杆轴向不动,用手使镗杆转动90°,用千分表测出a、b、c三点的高度,记上数值;再使镗杆转动90°,测a、b、c三点高度,记上数值,所有数值如表1所示。如果检测的数值没有一点超出0.01mm,则表示合格,反之亦然。
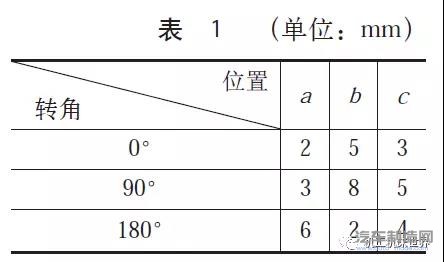
(2)检测尺寸、圆度和圆柱度。镗杆外圆尺寸用外径千分尺检测。将镗杆φ 110h8MF抛光面全长尺寸分为17等份,用外径千分尺按径向a、b、c、d的顺序位置分别测出直径方向上的尺寸(见图12),将测得的数据列入镗杆检验记录表(见表2)。
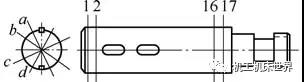
图 12
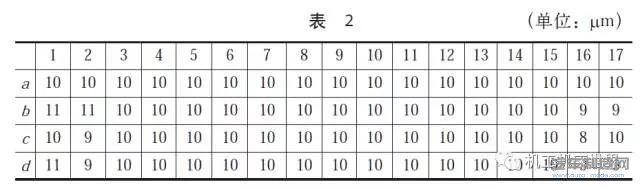
圆柱度误差是指其一方向上的直径之差,按表中横向数值计算,a向圆柱度误差为0,b向误差为2μm,c向误差为2μm,d向误差为2μm,将a、b、c、d四个方向综合来看,其中最大值和最小值之差,方是真正的圆柱度误差2μm。
圆度误差按表内竖行各数值分别对比,取各数值之差最大值,如表中第二列b向与c向的差值为2μm,则此镗杆的圆度误差为2μm。如果镗杆检验不合格或其中一项超差,则需继续研磨抛光直至合格为止。
另外,检测时应注意室温和人体温度(手握千分尺)对测量结果的影响,并注意剔除过失误差,减小测量误差的影响,尽可能使测量数值准确。
结语
随着产品的不断更新,工艺方法也应不断地进行改进,研究新工艺、探讨新方法是我们从事技术工艺工作的追求目标,只要不断努力,不能加工和难加工零件都将被突破。
镗杆材料的选用
镗杆是主传动的主要部件,需要具有很高的抗弯性、耐磨性及抗冲击韧性等机械性能,这就要求镗杆在心部具有足够韧性的同时,表面还要有足够的硬度。38CrMoAlA这种优质合金结构钢的含碳量使钢材具有足够的强度,而Cr、Mo、Al等合金元素能与碳形成复杂的弥散相,均匀地分布在基体中,当受到外应力作用时,起到机械阻碍作用而强化。其中,Cr的加入可显著提高氮化层的硬度,提高钢的淬透性及心部强度;Al的加入可显著提高氮化层的硬度和细化晶粒;Mo主要消除钢材的回火脆性。经过多年的试验及探究,38CrMoAlA能够满足镗杆的主要性能要求,也是目前镗杆材料的首选。
镗杆热处理安排及作用
热处理安排: 正火+调质+氮化。镗杆氮化是热处理工艺中最后一道工序,为使镗杆心部具有必要的机械性能, 消除加工应力, 减少氮化过程的变形, 以及为获得最好的氮化层作组织准备,故镗杆在氮化前需要进行适当的预先热处理,即正火和调质。
(1)正火。正火处理是将钢件加热到临界温度以上,保温一段时间,然后用空气冷却,冷却速度比较快,经正火后,正火组织为块状“铁素体+珠光体”,零件组织得到细化,增加强度与韧性,较少内应力,改善切削性能。正火前不需要冷加工,但正火处理所产生的氧化脱碳层将导致氮化后脆性增加及硬度不足等弊病,故正火工序应留有足够的加工余量。
(2)调质。正火后加工量很大,切削后将产生很大的机械加工应力,为了消除粗加工后的机械加工应力,减少氮化过程中的变形,粗加工后增加一次调质处理是很有必要的。调质是淬火后高温回火,获得的组织是细密的索氏体。经调质后的零件具有足够的韧性和强度,很多重要的零件都需要经过调质处理。
(3)正火基体组织与“正火+调质”基体组织的区别。正火后的基体组织是块状的铁素体和珠光体(见图1),而“正火+调质”后的基体组织是细密的索氏体组织(见图2)。
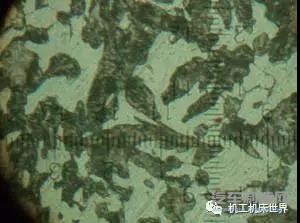
图1 正火基体组织
.jpg)
图2 “正火+调质”基体组织
(4)氮化。氮化是使零件表层有高的硬度和耐磨性,而心部保持原有的强度和韧性的热处理方法, 含有铬、钼或铝的钢采用氮化处理后会获得比较理想的效果。工件氮化后质量:① 工件表面呈银灰色无光泽。②工件表面硬度≥1 000HV,磨削后表面硬度≥900HV。③氮化层深度≥0.56mm,磨削后深度>0.5mm。④氮化变形要求振摆≤0.08mm。⑤脆性1~2级为合格,现实生产中都能达到,经研磨后更好。
(5)“正火+氮化”与“正火+调质+氮化”的组织区别。从图3~图6可见,“正火+调质+氮化”的氮化效果明显优于“正火+氮化”的氮化效果。“正火+氮化”的氮化组织中,有明显的块状、粗针状脆性氮化物存在,这一点也可以作为分析镗杆有时出现氮化层脱落现象的参考(见图7)。
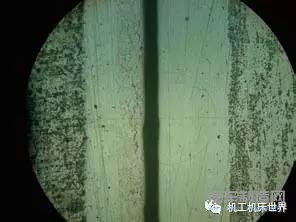
图3 “正火+氮化”层深0.60mm,并可见脉状脆性氮化物(左)“正火+调质+氮化”层深0.68mm(右)
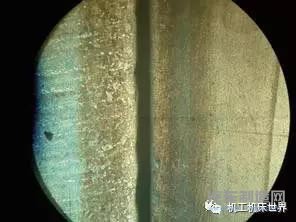
图4 “正火+氮化”氮化组织中有快状、针状脆性氮化物(左)“正火+调质+氮化”组织细密,无明显脆性氮化物(右)
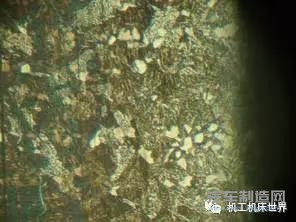
图5 “正火+氮化”显微镜下(500×)金相组织块状、针状脆性氮化物
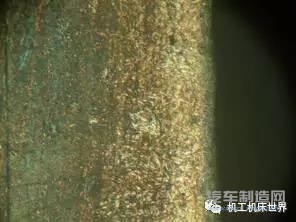
图6 “正火+调质+氮化”显微镜下(500×)金相组织,无明显脆性氮化物
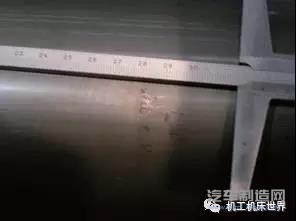
图7 镗杆氮化层脱落照片镗杆的精加工
(1)以镗杆Z104339为例,镗杆的精度要求如图8所示。

图 8
(2)工艺过程:下料→正火→钻粗车用中心孔→粗车→调质→半精车→粗磨外圆→粗磨锥孔→划→铣各槽→探伤→粗磨对键槽(留精磨量)→半精磨外圆→半精磨里孔→氮化→半精磨锥孔(留精磨量)→半精磨外圆(留精磨量)→磨对键槽→精磨外圆→精磨锥孔→研磨外圆→抛光→钳。
( 3 ) 镗杆精加工工艺过程。由于镗杆需要经过氮化处理,故特意安排两次半精磨外圆工序。第一次半精磨安排在氮化前,目的为氮化处理打好基础。主要是控制镗杆磨前余量和几何精度,以保证氮化后氮化层硬度在900HV以上。氮化时虽然弯曲变形较小,但绝不能校正氮化前的变形,否则只能比原来变形更大。我厂工艺确定,第一次半精磨时外圆留量为0.07~0.1mm,第二次半精磨外圆工序安排在精磨锥孔后进行。该工序在锥孔内装上磨芯,两端顶好,一端顶镗杆小头端面中心孔,一端顶磨芯中心孔,再用形式中心架架好磨外圆,不卸磨芯,转花键磨床磨对键槽。第二次半精磨外圆就是为了使后来精磨外圆时产生的内应力首先反映出来,这样精磨对键槽的精度会提高, 也比较稳定,又因有半精磨外圆的基础,精磨外圆时对键槽的影响就很小了。
我厂精磨对键槽使用的是花键磨床,一端顶镗杆小头端面中心孔,一端顶磨芯中心孔。这样磨削时键槽向上,外圆的弯曲变形及机床导轨的直线度只影响槽底,对槽两侧面影响不大。如果使用导轨磨床加工,则由于机床导轨直线度及镗杆自重,引起的变形会影响键槽直线度,一般情况下,使用花键磨床容易达到对键槽的直线度、平行度等各项要求,如图9所示。
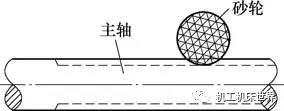
图9 花键磨床磨对键槽
镗杆外圆精磨是在万能磨上进行,采用方法是纵向走刀中心磨削法。
锥孔的跳动是镗床的一项主要成品精度。锥孔加工最终要求:①锥孔对外径跳动应保证在主轴端部0.005mm,在距离端部300mm处为0.01mm。②锥孔的接触面积为70%。③锥孔表面粗糙度值Ra=0.4μm。锥孔精加工方法:一是留余量,然后由装配自磨而使锥孔的接触达到最后成品精度;二是加工过程中直接达到技术要求。我厂现采用第二种方法,其做法是用卡帽卡镗杆后端M76X2—5g,前端用中心架架外圆φ 110h8MF,用千分表按外圆φ 80js6找正,磨锥孔。
研磨抛光是镗杆最后光整加工。研磨可以获得很高的尺寸精度和很低的表面粗糙度。一般来说,研磨工具的材料比工件材料要软,且组织均匀。最常用的是铸铁研具(见图10),适用于加工各种工件材料和精研加工,能保证较好的研磨质量和较高的生产率, 并且研具制造容易,成本也较低。在研磨过程中,研磨液不仅起调和磨料及润滑冷却作用,而且还起着化学作用,加速研磨过程。它会附着在工件表面,使工件表面很快产生一层氧化膜, 并起到磨平工件表面凸峰,保护工件表面凹谷作用。镗杆研磨时所使用的研磨剂成份为白色氧化铝的白刚玉粉和煤油的混合剂。
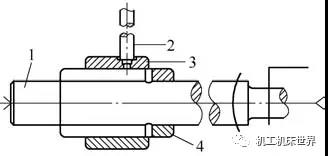
图 10
镗杆经研磨后尽管取得较好的尺寸精度及较低的表面粗糙度,但其表面出现嵌砂,并呈乌黑色,镗杆与空心主轴装配后,有黑水流出现象。为消除镗杆表面的研磨嵌砂,我厂采用自制的抛光具,对镗杆表面涂绿色的氧化铬进行抛光加工,实际效果非常好,镗杆表面光亮美观且防腐蚀。
镗杆的检测
(1)检测直线度。在0级平台上放置一对等高的V形铁。将镗杆放在V形铁上,V形铁所占的位置在φ 110h8MF的2/9L处(见图11)。镗杆全长直线度允差为0.01mm。
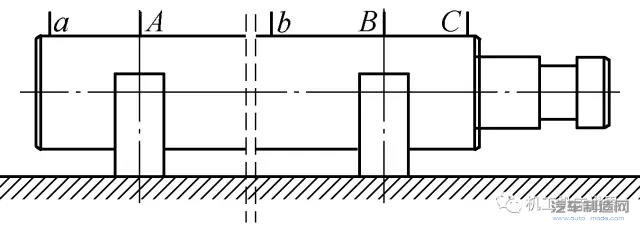
图11 检测镗杆直线度
首先用千分表检测2/9L两点A、B处的等高性,A、B两点的读表数值为0。然后,镗杆不动,测中间和两端点a、b、c三点高度,记上数值(见表1);保持镗杆轴向不动,用手使镗杆转动90°,用千分表测出a、b、c三点的高度,记上数值;再使镗杆转动90°,测a、b、c三点高度,记上数值,所有数值如表1所示。如果检测的数值没有一点超出0.01mm,则表示合格,反之亦然。
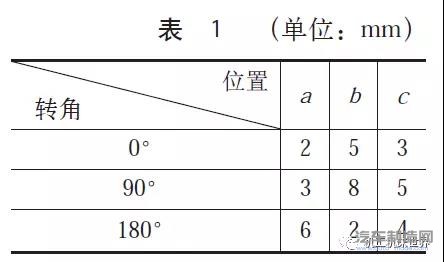
(2)检测尺寸、圆度和圆柱度。镗杆外圆尺寸用外径千分尺检测。将镗杆φ 110h8MF抛光面全长尺寸分为17等份,用外径千分尺按径向a、b、c、d的顺序位置分别测出直径方向上的尺寸(见图12),将测得的数据列入镗杆检验记录表(见表2)。
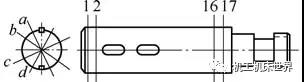
图 12
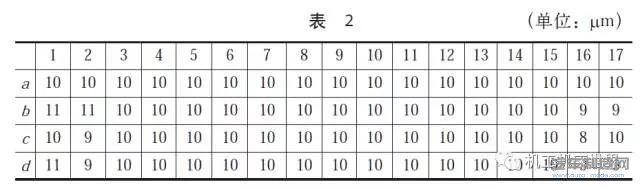
圆柱度误差是指其一方向上的直径之差,按表中横向数值计算,a向圆柱度误差为0,b向误差为2μm,c向误差为2μm,d向误差为2μm,将a、b、c、d四个方向综合来看,其中最大值和最小值之差,方是真正的圆柱度误差2μm。
圆度误差按表内竖行各数值分别对比,取各数值之差最大值,如表中第二列b向与c向的差值为2μm,则此镗杆的圆度误差为2μm。如果镗杆检验不合格或其中一项超差,则需继续研磨抛光直至合格为止。
另外,检测时应注意室温和人体温度(手握千分尺)对测量结果的影响,并注意剔除过失误差,减小测量误差的影响,尽可能使测量数值准确。
结语
随着产品的不断更新,工艺方法也应不断地进行改进,研究新工艺、探讨新方法是我们从事技术工艺工作的追求目标,只要不断努力,不能加工和难加工零件都将被突破。
编辑推荐
最新资讯
-
辐射亚太,链接全球——采埃孚再制造
2025-07-30 11:46
-
思看科技发布子品牌SCANOLOGY,全球
2025-07-30 11:06
-
风雨不动安如山——比亚迪叉车构筑“
2025-07-30 08:48
-
NEAS CHINA 新能源汽车技术与生态链
2025-07-29 09:52
-
三维扫描革新碾磨机辊套检测,效率与
2025-07-25 10:46