智能化装配技术在高节拍汽车总装中的应用分析
汽车总装车间的装配过程中,需要投入大量的人员进行手工作业,随着当前社会发展和人力成本逐年增加,少人化和自动化成为总装车间规划的目标和突破点。目前各大主机厂总装车间普遍应用的自动化智能装配有全景天幕自动化装配、风窗自动化装配、轮胎自动化装配,部分主机厂高节拍总装车间已尝试投入仪表自动化装配站、无框车门自动调整站、塑料尾门自动装配站、底盘自动合装以及动力电池自动合装等。
总装自动化智能装配方案介绍
主机厂总装车间常规节拍有10JPH、20JPH、30JPH、40JPH,高节拍有60JPH、75JPH,以下自动化智能装配方案以某主机厂60JPH总装产线为例进行介绍。
1. 全景天幕自动化智能装配站
全景天幕自动化智能装配站布置在总装车间前装线。前装线采用电动升降滑板线,智能装配站包含天幕自动上料、自动底涂、自动涂胶和自动装配等作业内容,为减少线体线边占用面积,智能装配站采用“U”形布局,天幕自动涂胶后通过举升机提升至空中并转接到跨线移栽机,输送至线边机器人进行抓取装配。
工艺流程如下:
1)自动上料移栽机从料框中取出天幕并放入上料工位,传动带输送机将天幕输送到机器人清洁底涂工位。
2)顶升对中台对中天幕,机器人对天幕清洗底涂,并在线测量底涂质量。底涂视觉测量合格后经过备用人工清洁底涂工位继续向烘干工位输送,如果视觉测量不合格,人工在备用工位清洁底涂。
3)天幕经过烘干工位到机器人涂胶工位,机器人涂胶并在线测涂胶质量。
4)天幕输送到转接及备用人工涂胶工位,如果涂胶质量合格,经举升机提升至空中并转接到跨线移栽机,再输送至天幕翻转机工位;如果涂胶质量不合格,则在该工位人工涂胶,并经移栽机输送至天幕翻转机工位。
5)翻转机将天幕翻转到对中台并对中,机器人抓走天幕。机器人经视觉系统测量天幕安装位置并安装天幕。
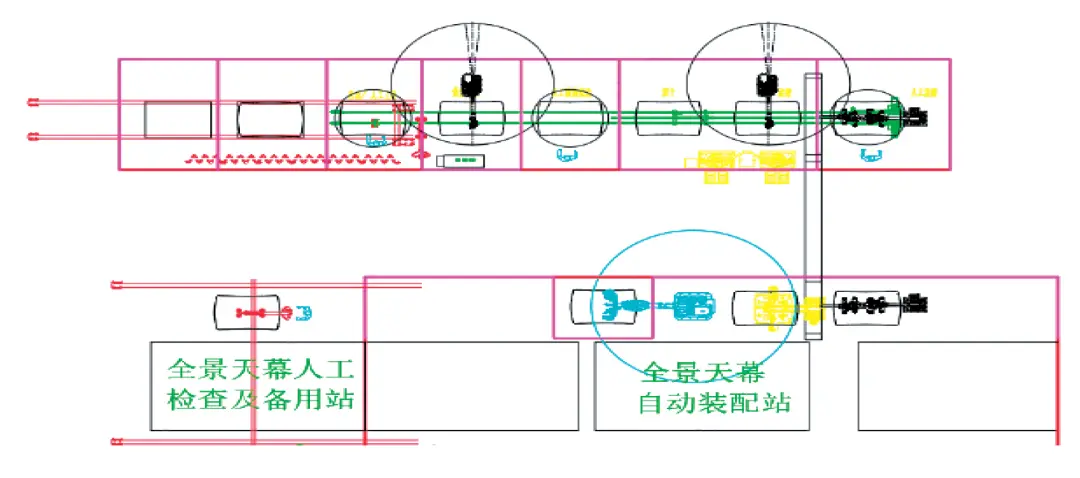
2. 风窗自动化智能装配站
风窗自动化智能装配站布置在总装车间前装线,前装线采用电动升降滑板线,智能装配站包含风窗自动上料、自动底涂、自动涂胶及自动装配等作业内容。
工艺流程如下:
1)取料机器人根据上位信息从料框中取出玻璃并放入底涂输送线。
2)底涂输送线将玻璃输送至对中台,对中台对中风窗玻璃。
3)清洗&底涂机器人从对中台中抓取玻璃并清洗、底涂,底涂后将玻璃放入涂胶输送线。
4)涂胶输送线将玻璃输送至人工备用底涂工位、底涂烘干工位、涂胶对中台。
5)涂胶对中台对中风窗玻璃,涂胶安装机器人抓取玻璃并涂胶。
6)胶型在线检测合格后涂胶安装机器人根据安装引导机器人提供的位置信息安装风窗玻璃。
7)若胶型在线检测不合格,涂胶安装机器人将玻璃放入NG台下线后人工处理。
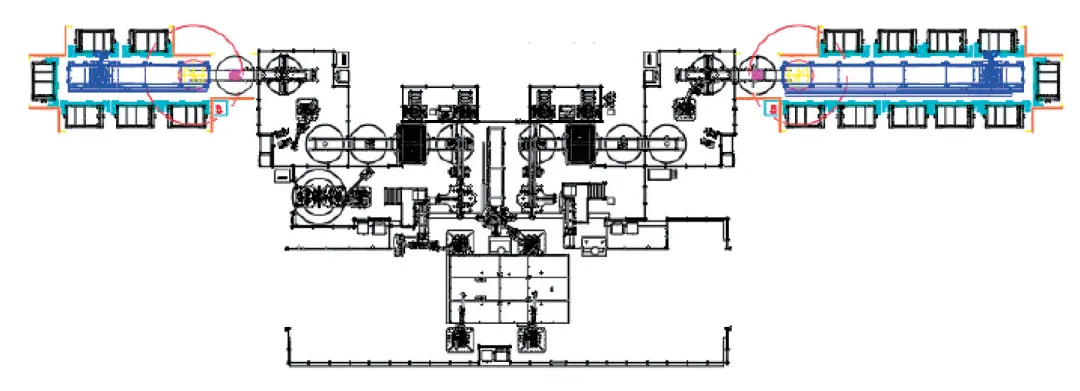
3. 轮胎自动化智能装配站
轮胎自动化智能装配站布置(图3)在总装车间后装线,后装线采用电动升降滑板线,智能装配站包含轮胎自动识别、自动抓取、自动装配、自动送钉及自动拧紧等作业内容。
工艺流程如下:
1)轮胎输送线将轮胎输送至对中台,对中台举升并对中轮胎。
2)高位相机检测轮胎轮毂形状并核对轮毂信息。
3)底位相机检测轮胎安装孔角度信息并传给轮胎安装机器人。
4)轮胎安装机器人从螺栓分度盘取螺栓,并在螺栓检测台检测螺栓是否抓取到位。
5)轮胎安装机器人从轮胎对中台抓取轮胎。
6)轮胎安装机器人到轮胎安装位视觉检测制动盘角度并安装拧紧轮胎。
7)安装完成后滑板放行。
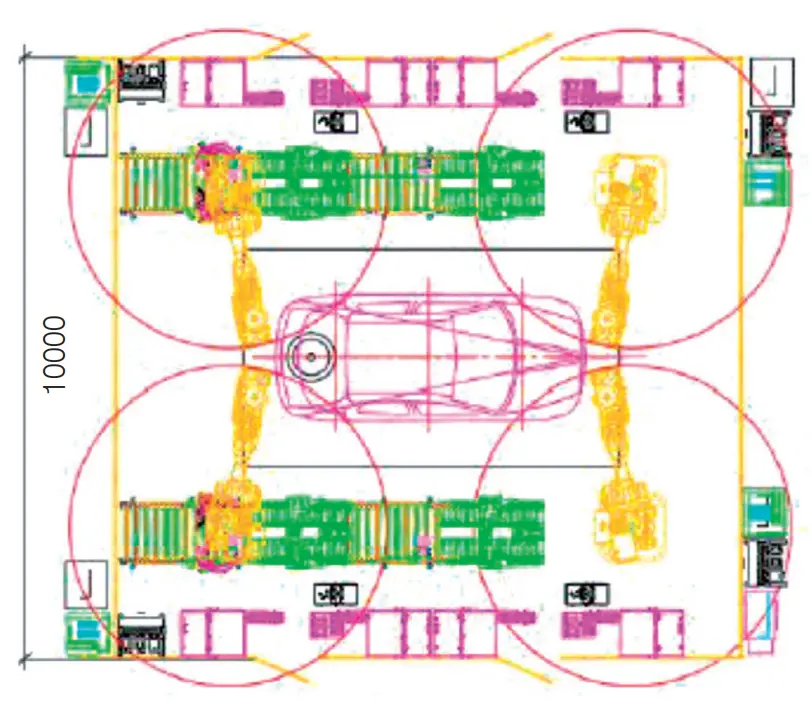
4. 无框车门自动调整装配站
无框车门自动调整装配站布置在总装车间车门分装线,车门分装线采用FDS(摩擦线)形式,装配站包含车门自动识别、自动定位、玻璃自动调整及自动拧紧等作业内容。
工艺流程如下:
1)门吊具带车门进入智能调整工位并停止,自动扫码及解析系统对门吊具上的指示票进行扫描,并与从门线获取的队列信息进行比对,识别到需要调整的车型后,系统启动,不需要调整的直接放行。
2)门吊具及车门定位机构对门吊具及车门进行有效夹紧及定位。
3)拍照及拧紧机器人对车门钣金定位点及门玻璃切边定位点进行拍照,计算玻璃相对车门的调整量并反馈给门玻璃调整机器人。
4)门玻璃调整机器人夹紧及吸附玻璃,并将玻璃调整到正确的空间位置。
5)拍照及拧紧机器人对门玻璃升降器螺纹孔拍照定位后,对螺钉进行拧紧。
6)各机器人回原位,门吊具及车门定位机构松开,门吊具快出离开工位。
7)如果某个车门因故未进行自动调整,由安装在人工调整工位的显示屏上提醒工人(包括车型及哪个门),工人从备用调整工装放置台上拿取备用调整工装进行手动调整。
总装自动化智能装配的优势
自动化智能装配站相对于传统的装配方案(人工装配),其优势在于智能装配站可与总装车间AVI系统网联,车辆及零部件信息自动校验,同时可通过视觉系统进行自动定位、自动胶型检测、自动拧紧,解决生产线作业人员劳动强度大、作业环境差、装配质量一致性差的痛点问题,同时可实现零部件自动防错。
总装自动化智能装配的投资回收周期
全景天幕自动化智能装配站投资费用约485万元,双班节省人力10人,人工费用10万元/(年・人),投资回收周期4.85年。风窗自动化智能装配站投资费用约950万元,双班节省人力20人,投资回收周期4.75年。轮胎自动化智能装配站投资费用约530万元,双班节省人力12人,投资回收周期4.42年。无框车门自动调整装配站投资费用约760万元,双班节省人力8人,投资回收周期9.5年。以上自动化智能装配站除了无框车门自动调整投资周期皆在5年以内,考虑人工成本逐年上升因素,投资回收周期会有所下降,综合质量、效率提升等因素,自动化智能装配投资收益可观。无框车门自动调整装配站由于最近几年刚刚应用,设备投资较大,以后随着应用的普遍性和技术成熟度增加,投资费用会减少。
结语
综上所述,高节拍的总装自动化智能装配可以满足生产线生产需求,对于总装车间而言不仅仅是减少人力降低工艺HPV,同时可提升装配质量,保证装配一致性。随着装备技术的日益发展,后续总装车间的自动化会有更多的应用,总装车间的自动化率会显著提高。
-
推动汽车行业转型的引领者——面向未来的总装NE
2024-12-03 -
总装工艺成本优化实践案例
2024-08-05 -
如何提高螺栓连接的强度?
2024-07-30 -
案例分析:螺栓“跑丢了”!
2024-07-29
编辑推荐
最新资讯
-
辐射亚太,链接全球——采埃孚再制造
2025-07-30 11:46
-
思看科技发布子品牌SCANOLOGY,全球
2025-07-30 11:06
-
风雨不动安如山——比亚迪叉车构筑“
2025-07-30 08:48
-
NEAS CHINA 新能源汽车技术与生态链
2025-07-29 09:52
-
三维扫描革新碾磨机辊套检测,效率与
2025-07-25 10:46