浅谈桥形件的成形工艺
2019-06-04 23:37:15· 来源:锻造与冲压 作者:王红伟
桥形零件由于其形状像跨越在河流上方的拱桥,中间窄长面为人行通道,两侧似护栏而得名,在冲压行业内属于常见的内板件,一般为加强件。比如汽车的中央通道加强板、拖拉机的机罩盖板加强梁等。该类零件形状起伏较大,成形性较差。目前主要
桥形零件由于其形状像跨越在河流上方的拱桥,中间窄长面为人行通道,两侧似护栏而得名,在冲压行业内属于常见的内板件,一般为加强件。比如汽车的中央通道加强板、拖拉机的机罩盖板加强梁等。
该类零件形状起伏较大,成形性较差。目前主要有两种成形方法:拉延成形和翻边成形,且行业内常用拉延工艺。拉延工艺的优点为零件成形充分,修边后零件回弹较小;缺点为材料利用率较低,前期的拉延面等工艺设计复杂,且模具结构较复杂、成本较高。相对而言,翻边成形工艺的优点为材料利用率较高,工艺设计及模具结构较简单,制造及后期维护成本较低;缺点为零件部分区域成形不充分,可能造成后序修边后零件回弹。在实际应用中需要针对不同零件, 选出最优的成形方案。
中央通道前加强板
零件如图1所示,尺寸为290mm×123mm×174 mm,上下落差达174mm,材质为B280VK,料厚为1mm。
从零件的结构上分析,如果采用成形工艺,以中间长条形状为压料面,采用翻边成形。由于零件端头为斜面,所以压料困难。且两侧支腿斜面夹角为37°,成形时会在顶面形成大量余料,从而形成起皱缺陷。显然采用成形工艺不合适。
而采用拉延工艺,虽然零件的起伏较大,但是由于零件的局部翻边高度都不超过 30mm,所以该零件的拉延性良好。添加工艺补充面后的拉延工艺如图2 所示。经 CAE 分析,压边力设置为 25t,结果如图 3 所示。从图中可以看出端头根部起皱现象已基本消除,仅顶面位置还有起皱趋势。但是,材料厚度中等,在实际生产中抗起皱能力较好。
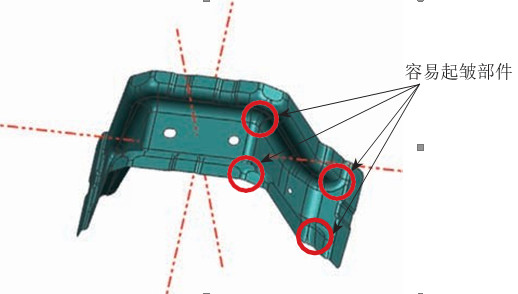
图 1 中央通道前加强板制件图
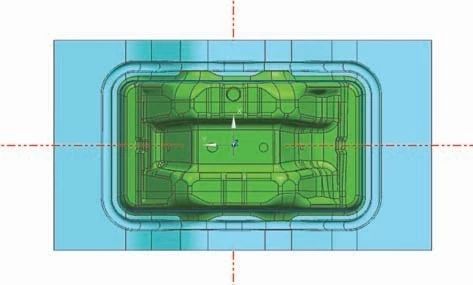
图 2 拉延工艺补充后
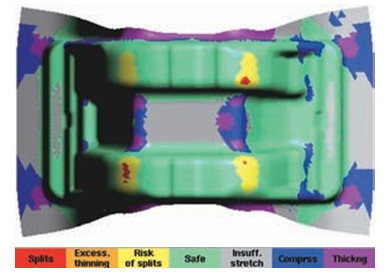
图 3 CAE 成形性能分析结果
实际生产出来的零件如图4 所示,零件状态较好无明显起皱与回弹现象,与分析结果基本一致, 证明采用该拉延成形方式是合适的,材料利用率为47.01%。零件在检具上检测合格率为 98%。
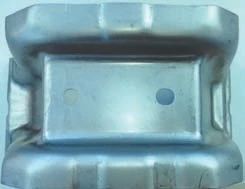
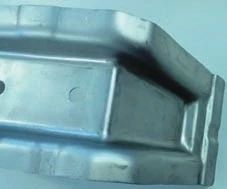
图 4 成品件(左顶面,右侧面)
支架
零件如图5所示,外形尺寸为240mm×114mm×81mm,材质为B410LA,料厚为1.4mm。该零件与中央通道前加强板的零件结构相似,不同的是,该零件顶面比较平缓,两端头较陡,夹角为27°,所以在两端头位置容易聚料起皱。
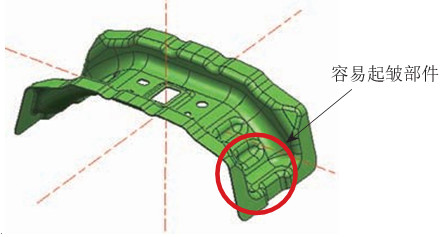
图 5 支架制件图
采用翻边成形工艺进行成形时,只能以零件底面为压料面,整个一圈侧壁向上翻边,在端头四个端点处材料聚在一起无法流动,导致严重起皱,且无法在后续成形中去除该缺陷。所以,采用翻边成形无法实现。
如图6 所示,以蓝色面为压料面,绿色面为拉延面,采用拉延工艺。制件全部在拉延凸模型面中, 充分延展,材料利用率为 48.3%。进行 CAE 分析, 结果如图 7 所示,起皱趋势与预想一致,主要集中在两端头。实际生产中,由于材料较厚,拉延后如图8 所示,四个端头起皱现象不太明显。后续整形之后,已有起皱基本消除。零件在检具上检测合格率为 99%(图 9)。
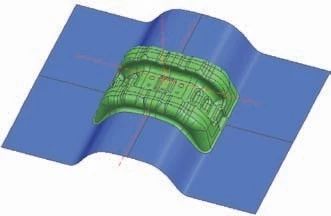
图 6 拉延工艺
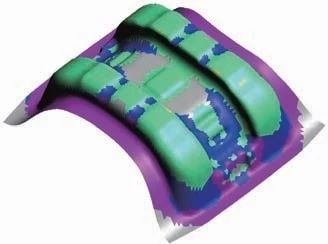
图 7 CAE 成形性能分析结果
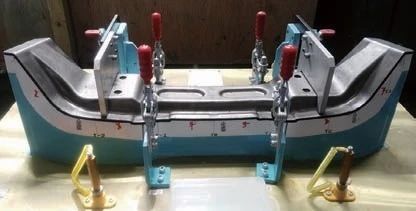
图 8 拉延后半工序件
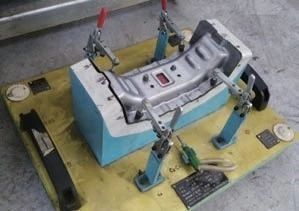
图 9 零件检具检测
机罩盖板后加强梁
该零件如图10所示,外形尺寸为676mm×159mm×133mm,材料厚度为1.5mm。形状左右对称,两端两个搭接面,要求面差为 ±0.5mm。与前两个零件相比,该零件尺寸较大、顶面及两端头都较平缓。

图 10 机罩盖板后加强梁制件图
采用拉延成形,拉延工艺与前面支架零件相似, 零件全部包在拉延面中,需要大量的工艺补充面。使用翻边成形(图 11)时,以两条分模线中间形状为压料面翻边成形。容易在四个端头造成起皱缺陷。为了消除该缺陷,在两端头各增加一条压料槛,使成形时延缓料向端头处积聚,从而减轻起皱。

图 11 翻边成形工艺
两种工艺对比,拉延工艺可以使零件塑性变形更充分,所以在修边、冲孔之后,制件回弹较小。但是,拉延工艺比较复杂需要做大量的工艺补充面,势必降低材料利用率,使冲压成本增加。而翻边成形工艺中塑性变形较拉延工艺差,在后续修边、冲孔之后,容易出现回弹现象。但是,相对于拉延成形可节省材料、降低成本。
使用CAE 软件进行分析发现,使用压料槛(图12)后,两端头的起皱现象明显消除(图 13)。实际生产出来的零件如图 14 所示,材料利用率达到了68%。成品件如图 15 所示,在检具上检测合格。
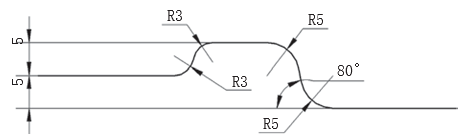
图 12 压料槛结构示意图
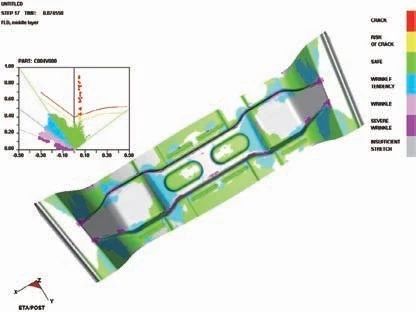
图 13CAE 分析结果
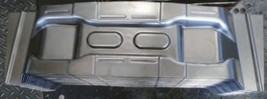
图 14 成形后状态图
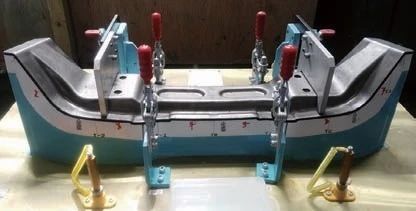
图 15 零件检具检测
虽然翻边成形工艺中零件塑性变形比拉延工艺少,但是零件上的小筋成形充分,有效防止成形后零件的回弹现象。另外压料槛的应用消除了端头的起皱缺陷。最终,使其达到了合格状态。
结论
桥形件作为常见的冲压加强件,采用翻边成形工艺还是拉延工艺,需要根据零件的具体结构进行分析。本文通过对三个典型的桥形件工艺分析对比,总结出该类零件的成形工艺特点,希望对其他类似零件进行工艺策划时有所启发。该类零件从工艺上分析,采用拉延成形工艺,可以使其产生最大区域的塑性变形,防止后续修边后零件回弹。但是,拉延工艺使零件的材料利用率降低到50%以下,对零件的成本控制影响较大。采用翻边成形工艺,材料利用率可以达到约70%,较拉延工艺提高了近 20%。
采用翻边成形工艺可以有效提高材料利用率,但是零件结构应该满足:⑴零件两端头为开放式的,可以增加工艺补充(加压料槛)防止零件起皱。⑵零件的两个支腿角度应尽量平缓,防止中间位置聚料起皱。因为如果支腿较陡,成形时在凹模与顶出器作用下,毛坯料会在中间顶端位置聚集大量材料,从而形成起皱缺陷。
举报 0
收藏 0
分享 134
-
乘用车金属冲压
2025-05-29 -
冲压技术在电机叠片制造的应用
2024-09-06 -
车身零部件包边质量控制要点
2024-09-05 -
轻量化技术——热汽胀形工艺技术解析
2024-09-04
最新资讯
-
辐射亚太,链接全球——采埃孚再制造
2025-07-30 11:46
-
思看科技发布子品牌SCANOLOGY,全球
2025-07-30 11:06
-
风雨不动安如山——比亚迪叉车构筑“
2025-07-30 08:48
-
NEAS CHINA 新能源汽车技术与生态链
2025-07-29 09:52
-
三维扫描革新碾磨机辊套检测,效率与
2025-07-25 10:46