汽车轻量化材料及连接技术现状分析
2019-03-27 22:47:16· 来源:汽车实用技术杂志社 作者:孙建亮 王立新
前言 近年来,随着汽车保有量和产销量的不断增加,汽车工业与能源、环境之间的矛盾愈演愈烈,同时国家对节能减排的需求越来越迫切,国家环保政策也逐渐加严,因此,汽车行业的节能减排也是迫在眉睫的事情。降低汽车燃油消耗、减少尾气排
前言
近年来,随着汽车保有量和产销量的不断增加,汽车工业与能源、环境之间的矛盾愈演愈烈,同时国家对节能减排的需求越来越迫切,国家环保政策也逐渐加严,因此,汽车行业的节能减排也是迫在眉睫的事情。降低汽车燃油消耗、减少尾气排放最直接的途径就是轻量化,是指在保证零部件使用性能和行驶安全性的前提下,实现整车减重。实验证明,汽车减重 10%,油耗将减少 6-8%,排放减少 6%,制动距离减少 5%,加速时间减少 8%,转向力减少 6%,轮胎寿命提 高 7%,材料疲劳寿命提高 10%。因此,轻量化已经成为世 界各国汽车制造商提高自身竞争力的重要手段。汽车轻量化技术是结构设计、材料、工艺的集成应用,主要途径有:(1)新材料的应用,主要是采用轻质高强材料及其成型技术,以达到减轻零部件重量的目的。(2)结构优化设计,使零部件薄壁化、中空化、小型化、复合化以及对车身零部件进行结构和工艺的改进等。其中轻量化材料及其连接技术是关键问题,本文针对目前轻量化材料及连接技术做简单分析,供汽车轻量化技术工作者参考。
1 轻量化材料
目前,汽车车身轻量化材料主要有高强度钢、铝合金、碳纤维复合材料等轻质高强材料,其中,高强度钢是性价比最好、最具吸引力的材质。
1.1 高强度高
高强度钢分为普通高强度钢(高强度 IF 钢(HSIF)、烘烤硬化钢(BH)、冷轧各向同性钢(IS)、冷轧高强度含 P 钢和高强度低合金钢(HSLA))和先进高强度钢(复相钢(CP)、双相钢(DP)、相变诱发塑性钢(TRIP)和孪生诱发塑性钢(TWIP))。车身设计师可根据板制零件受力情况和形状复杂程度来选择钢板品种。采用高强度钢板可以增加车身强度,减轻车身重量。高强度钢板主要用于车身上受力较大的结构和与安全相关的结构中,如车身前后碰撞横梁、A 柱、B 柱、车门防撞横梁、发动机舱边梁和一些车身连接板、安装板和加强件等。由于高强度钢板材料比较贵,且对模具的使用寿命有影响,所以经济型车采用高强度钢板比较少,豪华轿车采用的比较多。高强度钢具有高强度、成本低、制造技术成熟、环境友好等优点,在减重、节能、提高安全性、降低排放发面应用前景良好。但存在冷冲压时存在回弹大、成形性较差、焊接件的氢脆敏感性的缺点。
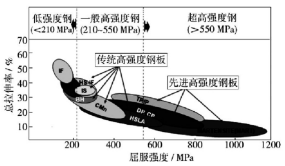
图 1 高强度钢分类示意图
2018 欧洲车身会议参展车型包含了卡车、皮卡、越野车等非常规车型,在材料应用方面,大多数车型车身采用钢材,斯堪尼亚的 NTG 卡车、铃木雨燕为全钢车身,通用 GMC 的皮卡、吉普牧马人为钢铝混合车身(四门两盖为铝),捷豹为全铝车身。
表 1 2018 欧洲车身会议参展车型的用钢量
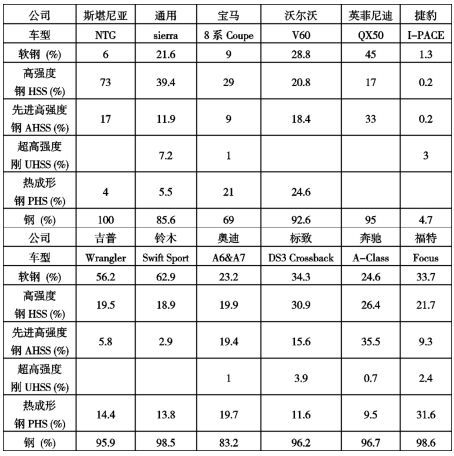
1.2 铝合金
铝合金已成为仅次于钢材的汽车用金属材料,能够为汽车提供各种铝合金铸件、冲压结构件和挤压的铝型材。铝合金主要用于制造发动机缸体、活塞、进气支管、气缸盖、变速器壳体、轿车的骨架、车身、座椅支架、车轮等部件。与汽车钢板相比,铝合金具有密度小(2.7g/cm3)、比强度高、耐锈蚀、热稳定性好、易成形、可回收再生、技术成熟等优点,但也存在延伸率低、成型难度大、制备工艺复杂、焊接性能差、成本相对较高等缺点。目前,较多使用铝合金的车 型往往是中高档的汽车。
用于汽车车身的铝合金板材有:Al-Mg(5000 系)和 AlMg-Si(6000 系)。5000 系合金中 Mg 是主要的合金元素,固溶于铝基体中,形成固溶强化效应,是一种热处理不可强化的铝合金,5000 系的铝合金成形性更好,可用于一些复杂形状的冲压件。6000 系合金中主要的合金元素是 Mg 和 Si,并形成 Mg2Si 相,属于热处理可强化铝合金。Al2Mg2Si 合金具有较高的强度、较好的塑性和优良的耐腐蚀性。6000 系的铝合金综合性能良好,可用于冲压发动机罩盖,具有烘烤硬化效应。
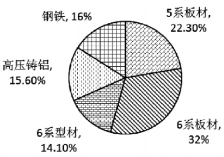
图 2 捷豹路虎车身用材及比例
1.3 玻纤/碳纤增强复合材料
树脂基复合材料不仅可使零部件降低多达 40%的质量,而且还可以使生产成本降低 40%左右。目前,玻璃纤维增强树脂复合材料和碳纤维增强树脂复合材料在汽车上已经获得成功的应用,已大量应用于汽车内饰件和外饰件。玻璃纤维增强树脂复合材料(GFRP)耐腐蚀、绝缘性好,特别是有良好的可塑性,对模具要求较低,对制造车身大型覆盖件的模具加工工艺较简易,生产周期短,成本较低。在轿车和客车上,采用玻璃纤维增强树脂复合材料制造的轿车车身覆盖件、客车前后围覆盖件和货车驾驶室等零部件。碳纤维增强树脂基复合材料(CFRP)具有轻质高强、高断裂韧性、耐腐蚀、可设计性强、易成型、减振阻尼性能好等一系列优点,既能够满足部件刚强度、轻量化的设计要求,在车辆安全性上也具有明显优势,因而是很有前途的汽车用轻量化材料,不过,目前存在成本高、成型周期长等缺点。
2 连接技术
目前汽车连接方式有焊接、铆接、螺接和胶接等,由于铝合金、高强钢、复合材料等轻量化材料的使用,传统的焊接不再适用,需要新的连接方式。异种材料的连接主要面临三个问题:界面硬脆相、电化学腐蚀、变形和应力。针对异质材料连接所面临的上述挑战,汽车科技人员开发了不同的连接工艺,如表 2 所示。
表 2 不同材料之间的连接方式

从表 2 可见,钢和钢之间的连接可用传统的电阻电焊、激光电焊等,使用无铆钉铆接(Clinching)、锁铆(SPR)和热熔钻(FDS)技术可实现钢铝的连接,搅拌摩擦焊是铝材之间较好连接方式。
2.1 无铆钉铆接和锁铆
无铆钉铆接(Clinching)和锁铆(Self-piercing riveting,SPR)是目前汽车车身制造中应用最为广泛的两种机械连接工艺。
无铆钉连接工艺的原理:即通过使用专门的连接模具,在一个冲压过程中,利用材料自身的可塑性,在挤压处形成一个相互镶嵌的圆点或者矩形点,由此将两层或多层板件连接起来。无铆钉铆接接头的强度主要通过板材间的嵌入量及上层板在接头颈部的厚度共同决定,而这些几何特征又与冲头和下模的几何形貌有关。无铆钉铆接工艺因其工艺过程简单且成本低,在汽车车身中得到广泛应用。但因其静态强度和疲劳强度都较低,通常只应用于行李箱盖、发动机罩、后轮罩等非承载部位。
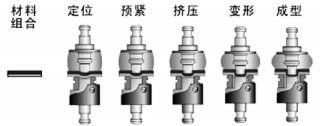
图 3 无铆钉铆接过程
锁铆连接是锁铆铆钉在外力的作用下,通过穿透第一层材料和中间层材料,并在底层材料中进行流动和延展,形成一个相互镶嵌的塑性变形的铆钉连接过程。与无钉铆接相比,锁铆接头具有良好的静态力学性能和较高的疲劳寿命,已经被通用、奥迪、宝马、捷豹、奔驰和大众等公司广泛应用于铝/钢等异质材料以及多层板的连接。
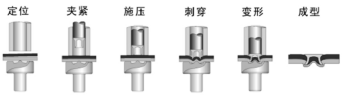
图 4 锁铆铆接过程
2.2 流动钻铆
FDS 技术通常称为流钻螺钉或热融自攻钉技术,该连接技术是将带有螺纹的螺钉高速旋转刺穿板材,并通过形成螺纹联接实现板材连接的一种技术,适应于板材与型材等管状封闭结构的连接。目前,凯迪拉克 CT6、捷豹路虎、宝马、奔驰、奥迪等车型采用了大量 FDS 技术。未来,随着铸铝件在白车身上的比重提高,FDS 技术在国内汽车行业会得到更大的发展。
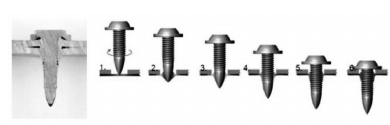
图 5 FDS 工艺过程示意图
2.3 搅拌摩擦焊
搅拌摩擦焊(Friction stir welding)是一种新型固相焊技术,是由英国焊接研究所(TWI)在 1991 年发明的一项最具革命性的新型材料连接方式[6],其焊接原理是:开始焊接时,搅拌针高速旋转着插入到被焊工件内部,直到轴肩下压到被焊工件内,焊接过程中,通过高速旋转的搅拌头和工件摩擦产生热量作为热源,使母材处于热塑性状态(未熔化),并被挤压在一起,随着热量的降低形成新的连接。搅拌摩擦焊焊接温度低,变形小,没有电弧,无辐射,是一种绿色环保的焊接技术。可用于汽车铝合金轮毂、底盘、门板、动力电池托盘、电池箱体、电机壳等部件。
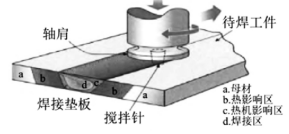
图 6 搅拌摩擦焊原理图
2.4 CMT焊接(冷金属过渡焊接)
冷金属过度焊接技术(Cold metal Transfer,CMT)是一种全新的 MIG/MAG 焊接工艺[11],将焊丝的运动与焊接过程结合起来,严格控制熔滴过渡中的输入电流,大幅度降低了焊接热输入,可以应用于钢和铝之间的连接。
3 结论
保护环境、节约能源、减少有害物排放是全世界的共同目标。汽车工业是能源消耗、资源消耗及尾气排放的大户,汽车轻量化技术作为节能、降耗、减排的重要手段,是未来的发展趋势。汽车轻量化材料有多种,每种材料都有长处和不足,只有多种材料混合使用,做到适量、合适的材料用在合适的地方,才能达到最终的轻量化目标。多材料混用在提升汽车轻量化水平的同时,也为材料或者零部件之间的连接提出更高的要求,随着新材料不断地应用,新型高效连接技术也将相 伴产生。
- 下一篇:延锋多家公司荣获吉利汽车客户嘉奖
- 上一篇:瓦尔特公司:创新与现代化生产
举报 0
收藏 0
分享 129
-
高温季行车安全需重视:TRW SPS 制动盘让你的刹
2025-07-19 -
跨越速运凭什么“圈粉”万千客户?“中国零担30
2025-07-01 -
驭动未来,智启新程-采埃孚油护新出行
2025-06-25 -
旭化成荣获2025年度发明表彰,助力离子交换膜法
2025-06-11
编辑推荐
最新资讯
-
辐射亚太,链接全球——采埃孚再制造
2025-07-30 11:46
-
思看科技发布子品牌SCANOLOGY,全球
2025-07-30 11:06
-
风雨不动安如山——比亚迪叉车构筑“
2025-07-30 08:48
-
NEAS CHINA 新能源汽车技术与生态链
2025-07-29 09:52
-
三维扫描革新碾磨机辊套检测,效率与
2025-07-25 10:46