碳纤维材料助力电动车轻量化
2019-03-11 21:54:46· 来源:Astroys
为电动车减负。还记得之前在有关Rivian的一些介绍信息中提到过,Rivian的电池包是用碳纤维材料封装的(可能是考虑到越野属性,需要确保足够的强度)。最近威廉姆斯先进工程公司(Williams Advanced Engineering,威廉姆斯旗下的技术服务
“ 为电动车减负。”
还记得之前在有关Rivian的一些介绍信息中提到过,Rivian的电池包是用碳纤维材料封装的(可能是考虑到越野属性,需要确保足够的强度)。
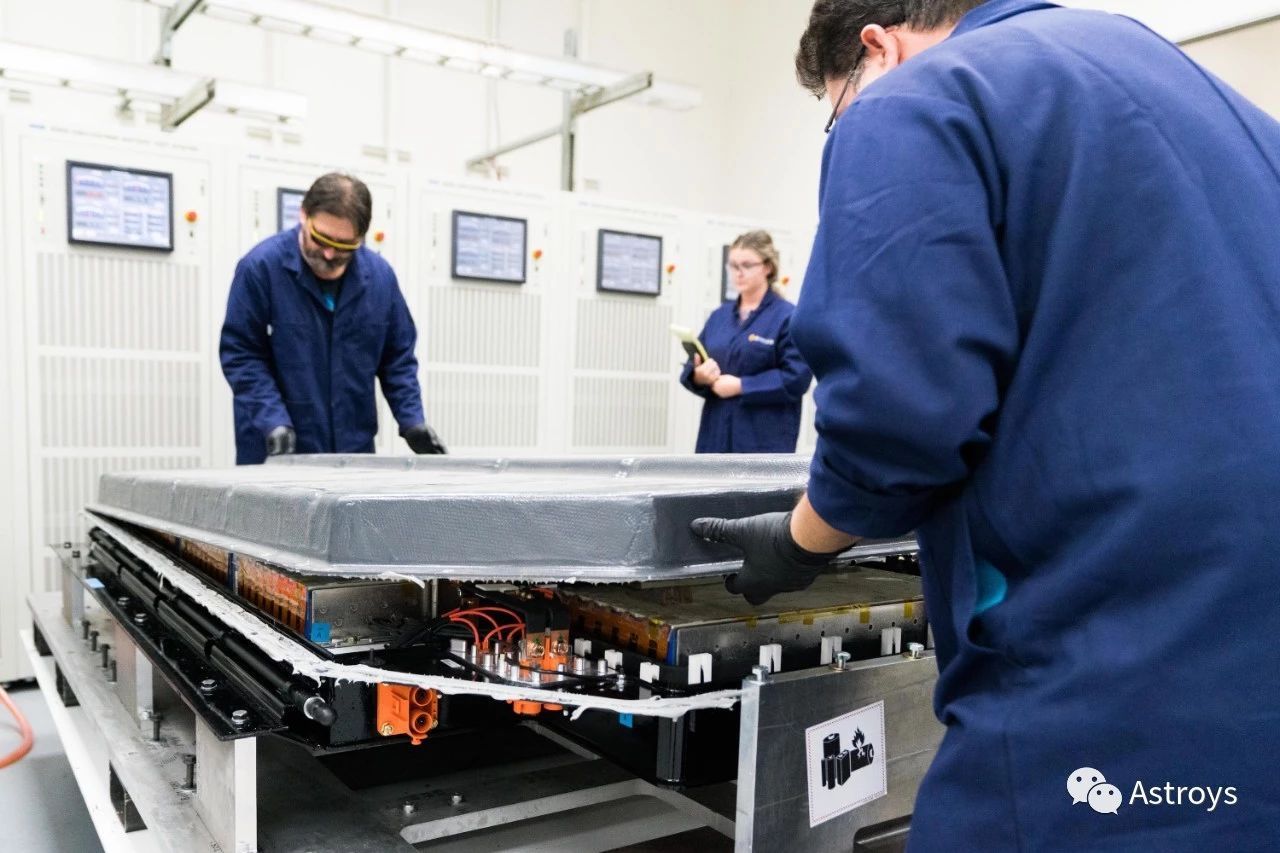
最近威廉姆斯先进工程公司(Williams Advanced Engineering,威廉姆斯旗下的技术服务公司)开发了一组碳纤维相关的技术,可大幅降低碳纤维材料在汽车行业领域使用的成本,他们还特别提到电动车领域的应用。巧合的是Rivian也恰好在英国有一支技术团队,是原来迈凯伦的工程团队。不知道这些从迈凯伦出来的团队和这项技术有没有关系。
CFRP材料
威廉姆斯的这组技术被称为“223”和“Racetrak”(名字听起来咋赶脚就是出自赛车技术呢?),可实现与现有复合材料解决方案相当的性能,却在成本方面能够达到主流应用的接受范围。
这些不仅仅是制造方面的创新,也是端到端的全生命周期的解决方案,可以解决碳纤维增强聚合物(Carbon Fiber Reinforced Polymer,以下简称CFRP)的制造、使用和再循环的各个方面,以及为车辆设计和制造提供一种新的方法。
CFRP是一种具有巨大潜力的材料。它有着很高的强度重量比,出色的刚度、抗疲劳性和耐环境性使其成为各行业和应用中非常重视的技术。特别是在汽车行业中,轻量化被视为满足日益严苛的燃油经济性和排放目标所需的主要途径之一,对于电动车轻量化来讲更是有意义(除此之外,还有望拓展到铁路车厢、风力涡轮机等应用领域)。
但仍有许多因素阻碍了CFRP的大规模应用。其中最主要的是成本,传统复合材料的生产方法涉及昂贵的材料和漫长的加工时间,且废品率还相对较高(通常约30%),以及用传统工艺很难在产品生命周期结束时找到回收价值。
正因为这些问题使CRFP的应用主要局限于小众应用。例如,在汽车领域,采用传统复合技术生产的白车身通常比钢结构轻约60%,但成本却是20倍。所以我们也只能偶尔在一些高端小众的车型上看到该技术的采用(比如早期宝马i3,后来宝马也烧不起了)。
威廉姆斯的创新技术就旨在解决这些挑战,释放CFRP的优势。
223工艺
先说说223,它的核心是将机织干纤维增强片与单独制备的树脂基质整合在一起的完全不同工艺(目前还比较保密)。
223工艺被认为是从二维创建三维复合结构的经济有效的手段。它适用于盒状几何形状,例如用于电动车的电池外壳,或甚至可能是用于车身外板。
223非常适合当前由许多单独组件组装的结构。一个很好的例子是汽车白车身,它通常由大约300个冲压件组成(同时需要600种不同的工具);一般来说大件(例如前/后备箱盖、顶盖或侧围这类大件的外板)一般需要四道冲压工序。如果使用223,就可以减少冲压的工序,可在一台压机上完成。这会大大降低成本,要知道在四大工艺中冲压的模具和压机是最昂贵的。
这与等效的铝合金材料相比,可以减重25-30%。而与传统的复合材料解决方案相比,可以以更低的成本实现更大批量的生产。
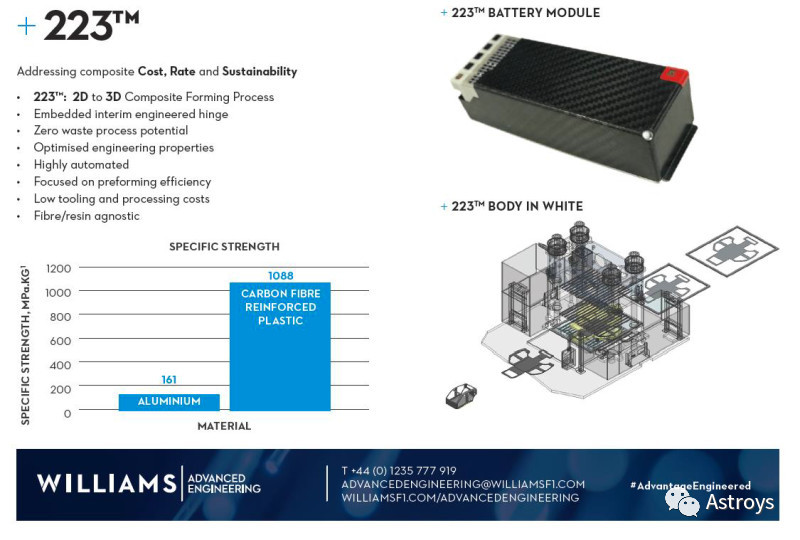
Racetrak
Racetrak是用于创建连接两个或多点的高强度的结构件(这个在冲压件上不属于大件,很多主机厂车型一多会把部分外包出去)。该技术可以让例如像碳纤维这种单向材料的连续循环提供极高的环向强度。当与高水平的自动化相结合时,可以实现比传统复合材料替代品轻得多的经济实惠的组件。
在用于汽车领域的情况下,会比铝板轻40%左右、比钢板轻60%,而且还相比铝板更具有成本竞争力,此工艺可实现每年50万套。
老实说,这部分更详细的技术解释,我没肯动,需要进一步学习下。

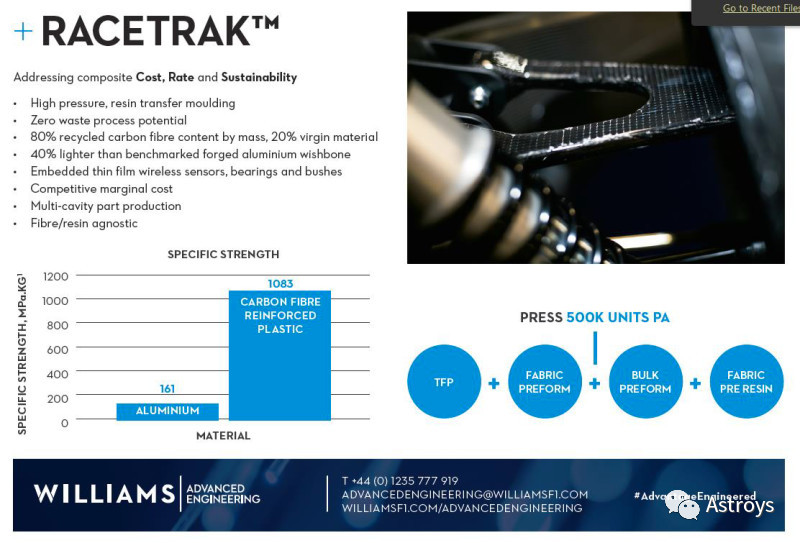
之前Munro说到model 3的fit&finish的问题时就聊到过一些铝制车身和碳纤维车身的问题。说到目前铝制车身的sweet point在7万台/年(稍微明白一点冲压的就知道,铝板粘性高,冲出来毛刺会比较多。而且也由于粘性高,冲压速度上要比钢板低很多,良品率较低),而碳纤维的话也就是5万台/年。一旦超出这个量最好还是用回钢板。不知道这套技术是否会为电动车的轻量化带来一定的飞跃。
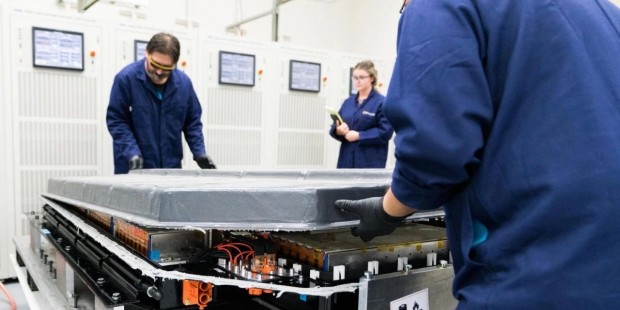
上图是威廉姆斯公开的采用了223与Racetrak工艺的电动车平台概念。
- 下一篇:机器人滚边质量缺陷的仿真分析与改善措施
- 上一篇:舍弗勒集团完成2018年预期目标
举报 0
收藏 0
分享 141
-
高温季行车安全需重视:TRW SPS 制动盘让你的刹
2025-07-19 -
跨越速运凭什么“圈粉”万千客户?“中国零担30
2025-07-01 -
驭动未来,智启新程-采埃孚油护新出行
2025-06-25 -
旭化成荣获2025年度发明表彰,助力离子交换膜法
2025-06-11
编辑推荐
最新资讯
-
辐射亚太,链接全球——采埃孚再制造
2025-07-30 11:46
-
思看科技发布子品牌SCANOLOGY,全球
2025-07-30 11:06
-
风雨不动安如山——比亚迪叉车构筑“
2025-07-30 08:48
-
NEAS CHINA 新能源汽车技术与生态链
2025-07-29 09:52
-
三维扫描革新碾磨机辊套检测,效率与
2025-07-25 10:46