铝板冲压件ID mark工艺排布的创新及应用
2019-03-01 14:00:34· 来源:锻造与冲压 作者:何磊
汽车工业在蓬勃发展的同时,由于环保和节能的需要,汽车轻量化已成为世界汽车发展的潮流,汽车轻量化技术的研究已经成为未来汽车发展的必然趋势。铝合金材料具有一系列优良特性,如比重小,比强度高,良好的成形性能、力学性能、物理性能
汽车工业在蓬勃发展的同时,由于环保和节能的需要,汽车轻量化已成为世界汽车发展的潮流,汽车轻量化技术的研究已经成为未来汽车发展的必然趋势。铝合金材料具有一系列优良特性,如比重小,比强度高,良好的成形性能、力学性能、物理性能以及工艺性能。但由于铝板材料较软,在实际生产中相较于钢板更容易被硌伤。
ID mark即生产标识,是由一连串字母和数字组成,包含了零件号、班次号、变更级别号、年份、批次号等信息,是零件的身份证。当生产中出现质量问题,生产标识是质量排查追踪的重要信息,在生产中必不可少。
创新背景及意义
在生产中,X156机盖外板外观面上经常会出现硌伤,每批次都要多次停机擦模,严重影响了正常生产,造成了巨大浪费,也增加了工人的劳动强度,每批次返修率也非常高,约为16%,产生了大量返修件,影响了SPH、EE、FTC等考核指标。在跟踪调查中发现,制件ID mark附近产生的硌伤尤其多,约占所有硌伤区域的60%,图1为制件硌伤实物图。
受到各工序工作内容、冲压方向、模具结构等约束,机盖外板的ID mark被安排在OP20压出,压生产标识时会挤压出铝屑,这些铝屑会留在本序或带到后工序,从而导致制件硌伤。为了控制返修率,有效提高FTC,减少擦模停机,提高经济效益,改善和解决ID mark产生的铝屑非常必要。
ID mark工艺排布创新及方案设计
X156机盖内外板工艺方案
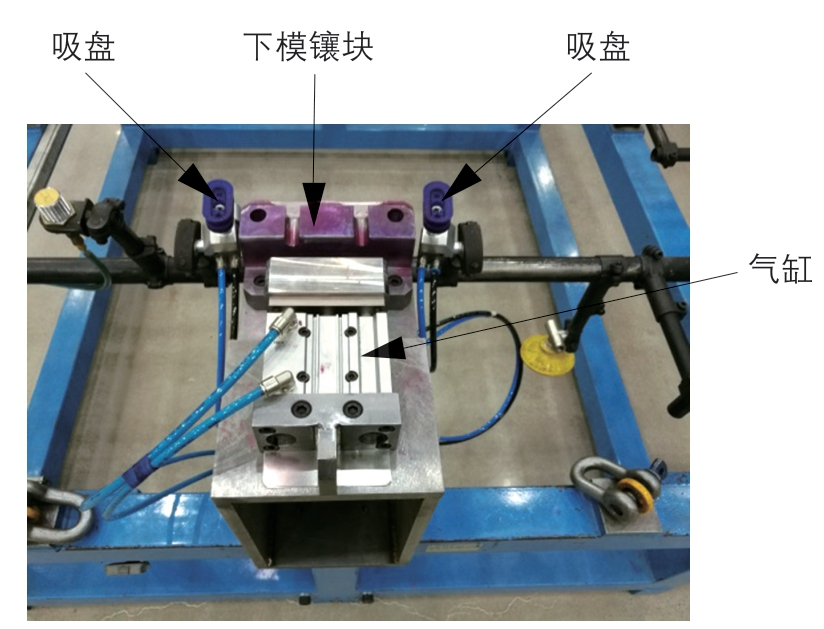
图1 制件硌伤
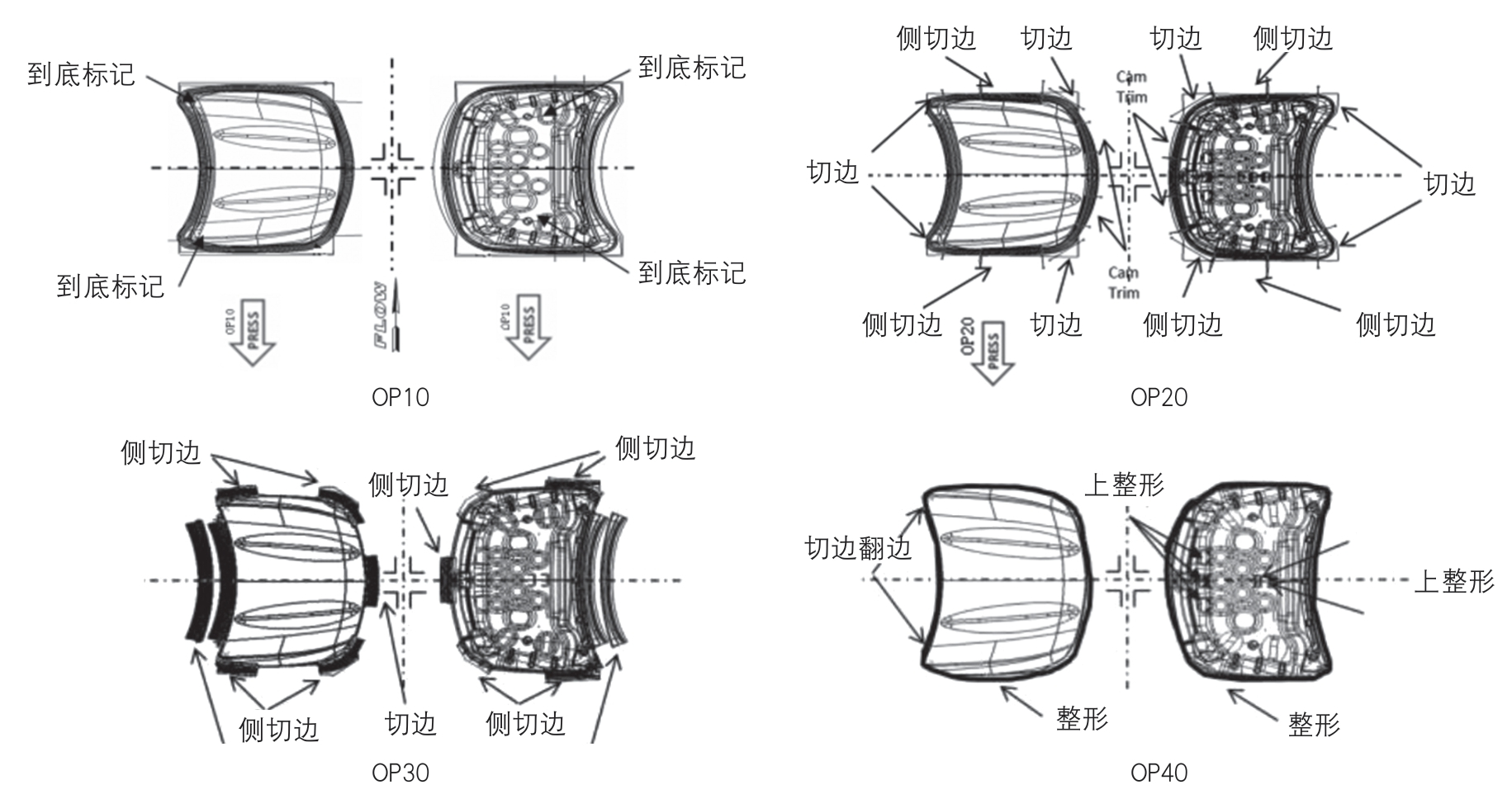
图2 各工序工艺内容
X156机盖内外板工艺方案共分为4序:OP10拉延,OP20修边、侧修边、冲孔、侧冲孔,OP30修边、侧修边、冲孔、二次切断,OP40整形、翻边、切边,如图2所示。由于自动化冲压线有5台压力机,所以第5台压力机不需要工作,设计为专门的空工位,空工位只是在自动化生产中起到传递制件的作用,不参与冲压件成形的工作。
ID mark工艺排布创新
经过分析研究,考虑到各工序工作内容,同时考虑到此零件生产时间紧张,每周2批次生产,且空工位为专用的,结合生产实际需要,创新性提出将生产标识由OP20移到空工位,此方案的优点如下:
⑴风险可控,即使方案调试不成功,仍可在OP20冲制生产标识,调试过程中可正常生产,对生产无影响。
⑵在空工位冲制生产标识,结构简单。
⑶易于调整,在调试过程中,遇到问题调整起来非常方便。
⑷可持续改进优化,在正式生产后,仍可不断地进行优化,如增加减重孔、改善生产稳定性等。
⑸成本低,整个方案费用为4000多元,包含了所有部件的加工和采购费用。
方案设计
⑴整体方案介绍。
在OP50空工位上增加一个气动装置,该装置通过螺钉紧固到空工位上,通过气缸打出生产标识,整体方案结构如图3所示,方案设计的生产标识位置和要求位置一致,如图4所示的红框区域。
气动装置的主体结构包含下模镶块(材质为Q235)、防侧块、生产标识安装块、气缸安装块、气缸、钢板焊接组件等,如图5所示。
⑵难点分析及对策。
在空工位上冲制生产标识,存在以下难点:
1)制件是由图6中所示的黄色托盘托起的,托盘下方无稳定支撑,无法精确定位。
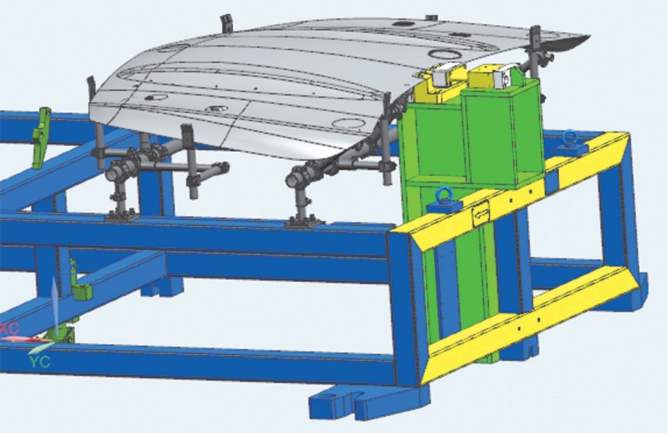
图3 方案设计图
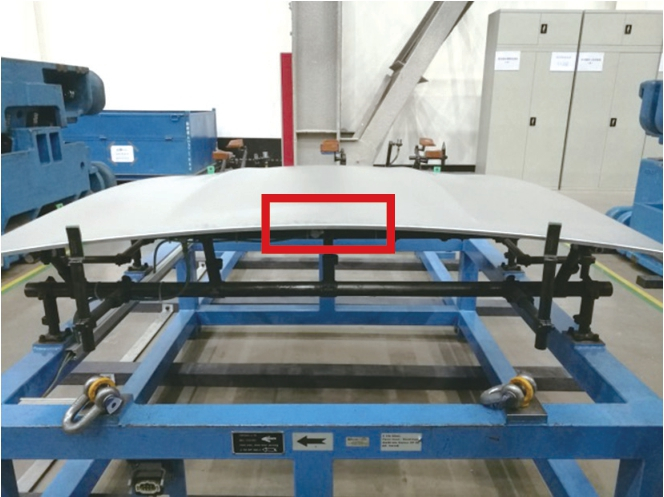
图4 生产标识位置
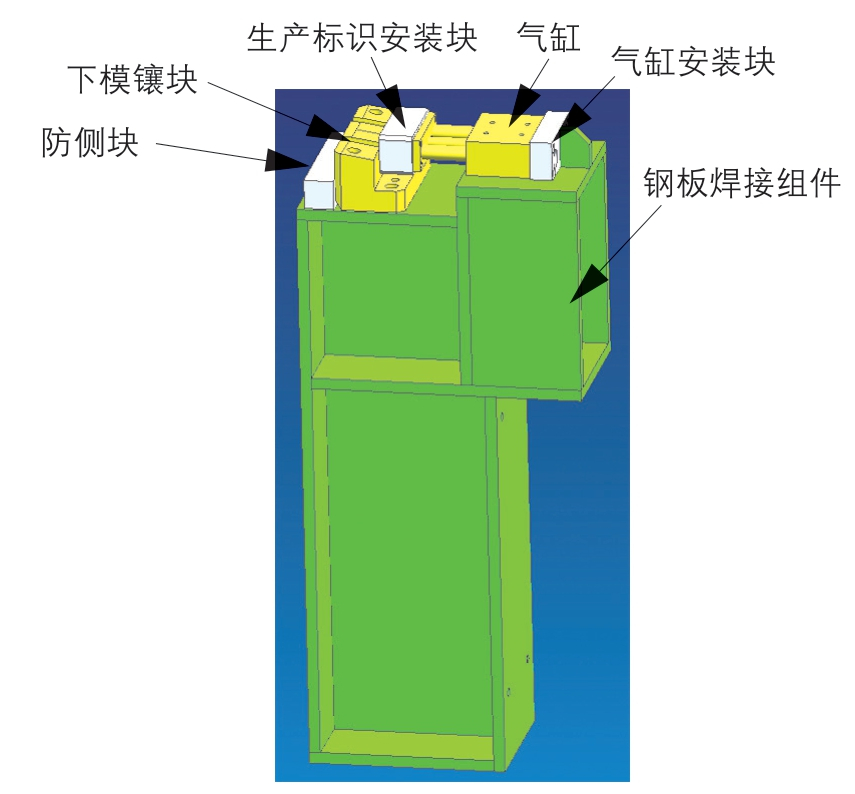
图5 主体结构三维图
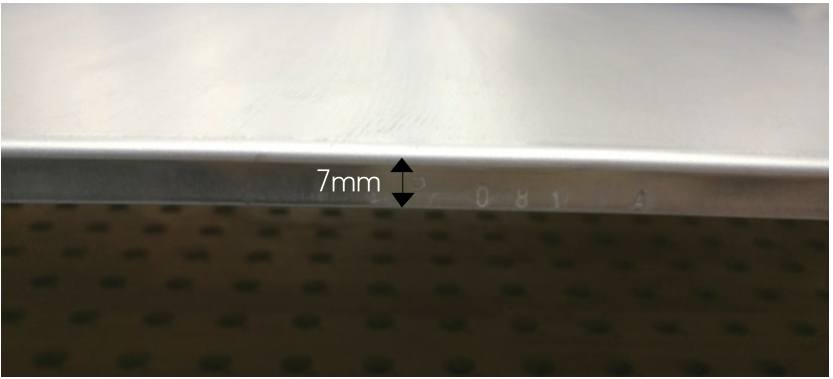
图6 空工位图
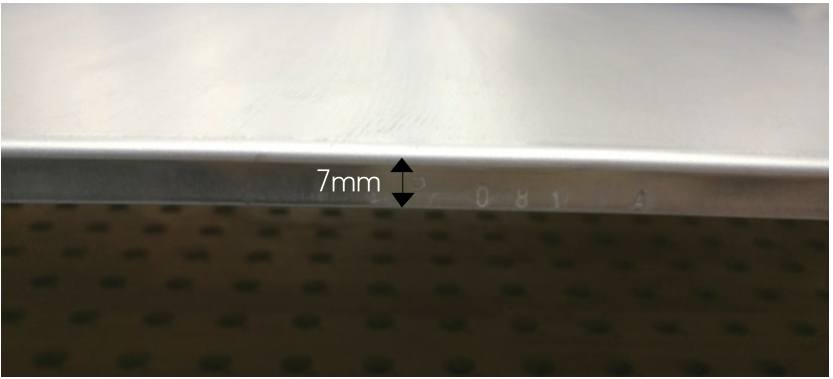
图7 制件合边面高度
2)制件合边面高度只有7mm(图7),在如此窄的区域冲制生产标识,必须保证冲制的精度和稳定性。
3)无压料装置,冲制生产标识时,制件此区域外观面容易变形,出现凹坑缺陷。
针对以上问题,经过分析研究,制定了专门的对策:
1)专门设计下模镶块用于下模符形支撑,同时选用自带导向的气缸MGPM32-50,可保证冲制生产标识的精度。
2)下模镶块附近增加两处吸盘,如图8所示,保证制件到位稳定,防止在冲压生产标识过程中,制件抖动。
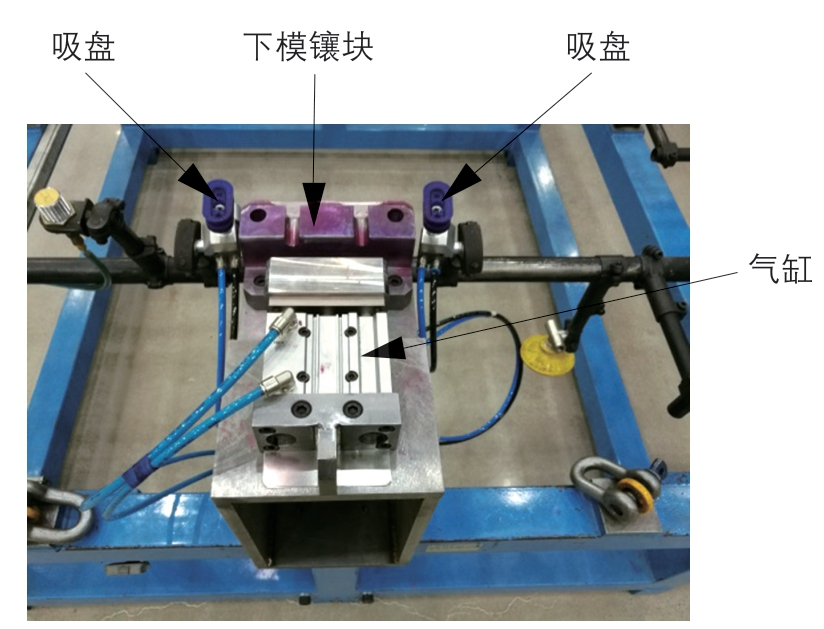
图8 气动装置实图
3)安装调速阀,控制气缸力,气缸力的大小要合适,气缸力过大,制件外观面会出现凹坑,气缸力过小,生产标识不清晰。
组装调试流程和注意事项
零部件加工和组装
将加工好的零部件进行组装,并安装到空工位上,同时安装吸盘、气管、调速阀等气路装置,重点关注以下两点:
⑴安装时要保证各个部件相对位置,要保证和设计的一致性。
⑵安装时保证下模镶块和其余托盘高低一致,要同时托起制件。
线下调试
为了减少线上调试时间,需对组装完成的结构进行线下调试优化,主要工作为以下两点:
⑴对下模镶块进行符形研合,保证下模镶块着色均匀,否则容易出现外观缺陷。
⑵通过调整调速阀来控制气缸冲制生产标识的力量,找到一个平衡点,力量太大制件外观容易出现缺陷,力量太小生产标识不清晰,达不到生产要求。
线上生产调试验证
线下调试合格后,需要进行线上调试验证,主要调试气源控制角度,调节好机械手放件、取件以及气缸和吸盘之间的相对运动关系,要保证图9所示的先后运动关系。
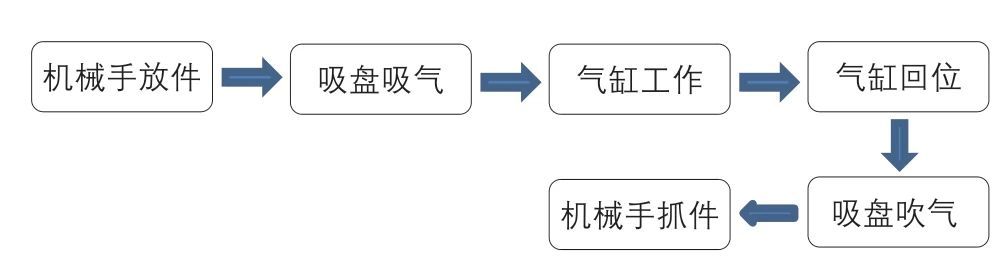
图9 运动关系
生产验证和经济效益
生产稳定,制件外观无缺陷
经过多批次生产验证,生产标识清晰,满足生产要求,同时生产标识附近区域,制件外观状态较好,未出现外观缺陷,产品质量可以得到有效保证。图10为机盖外板空工位生产实图。
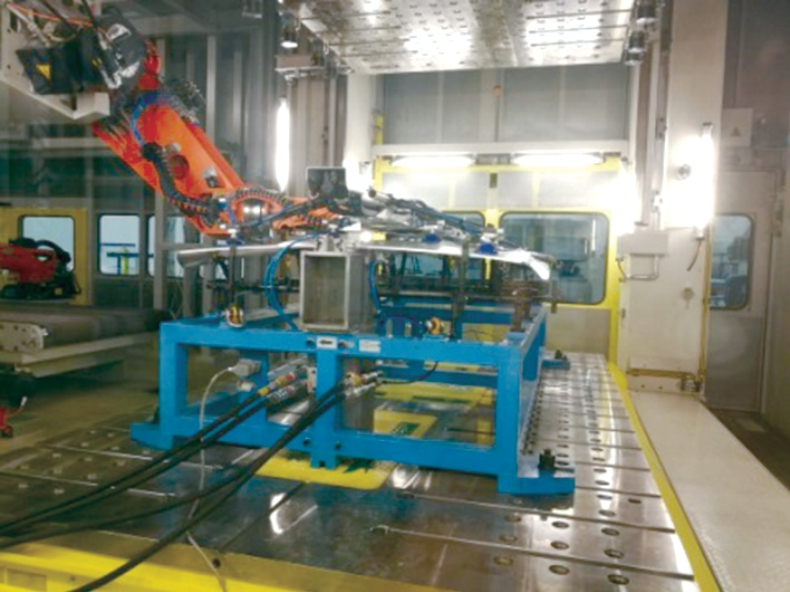
图10 机盖外板空工位生产实图
返修率降低明显
该优化方案正式实施后,X156机盖外板在线返修率大幅降低,图11为方案实施前后每月在线返修率情况。方案实施后在线返修率由16%降低到6%,降低60%左右。
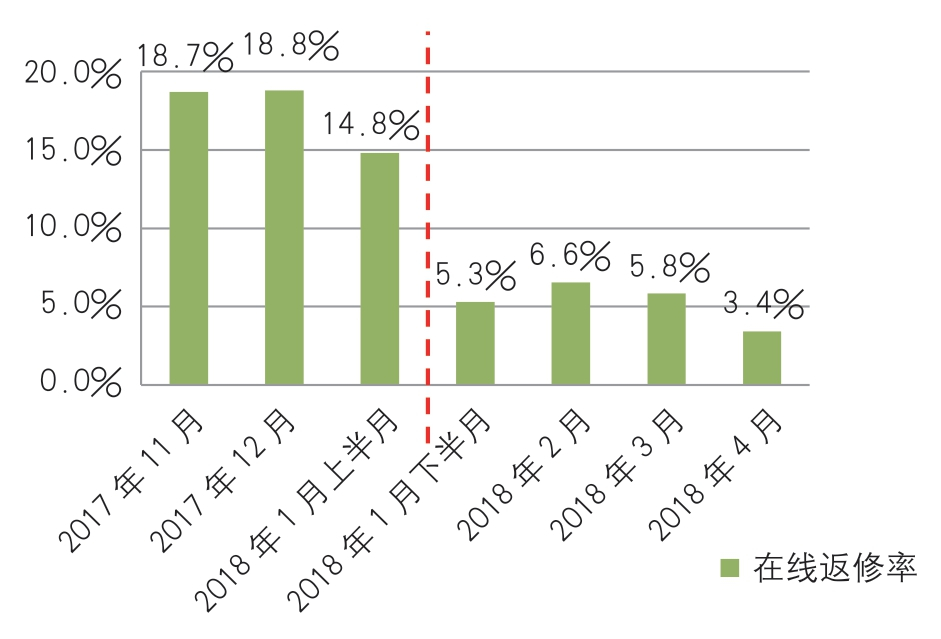
图11 X156机盖外板在线返修率
目前机盖外板每月产量约为6000件,方案实施后每月可减少返修600件。机盖外板返修通常需要两名工人协同工作,每个件返修时间约10min,这样每个月可节约200工时,全年可节约2400工时,每年可节省人工成本约13万元。
减少后工序擦模停机,提高设备使用效率
对此方案实施前后的停机情况进行统计后发现,本方案实施后,擦模停机时间降低44%,共减少98min,如图12所示。
从以上统计可以得出,一年共可减少停机392min,约合6.53h,每年大约可节省30万元停机费用。
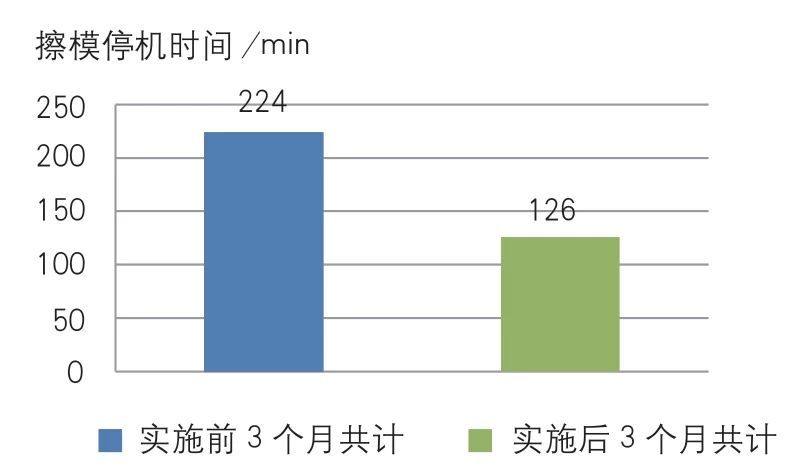
图12 擦模停机时间
生产标识批次号更换更方便,时间更短
X156机盖外板生产标识在OP20冲制时,因生产标识在模具里面,更换生产标识中的批次号比较麻烦,需要使用天车将模具从模具存放区运送到模具维修区,并将模具上下模分开,占用模具维修场地,同时需要3个钳工进行协作,约用时25min,将生产标识移到空工位后,只需1个钳工在空工位存放区进行更换,不占用天车和维修场地,同时仅需5min。机盖外板每月生产7批次,每月可节约8.2工时,全年可节约98工时。
结束语
目前将ID mark移到空工位上的方案,经过长时间、多批次、大产量的验证,该方案稳定可靠,改善效果明显,经济效益突出,完全达到了设计预期。在可查阅到的资料及信息中,未曾有将生产标识安装到空工位上,且实现序列化生产的先例,本方案是在结合生产实际的情况下,首次创造性的将ID mark移到空工位上,以X156机盖外板为例,给生产中类似问题提供了很好的解决思路和方法。
—— 来源:《锻造与冲压》 2019年第2期
- 下一篇:德纳完成对欧瑞康集团传动系统事业部的收购
- 上一篇:牧野a51nx自动化线案例分享
举报 0
收藏 0
分享 107
-
乘用车金属冲压
2025-05-29 -
冲压技术在电机叠片制造的应用
2024-09-06 -
车身零部件包边质量控制要点
2024-09-05 -
轻量化技术——热汽胀形工艺技术解析
2024-09-04
最新资讯
-
辐射亚太,链接全球——采埃孚再制造
2025-07-30 11:46
-
思看科技发布子品牌SCANOLOGY,全球
2025-07-30 11:06
-
风雨不动安如山——比亚迪叉车构筑“
2025-07-30 08:48
-
NEAS CHINA 新能源汽车技术与生态链
2025-07-29 09:52
-
三维扫描革新碾磨机辊套检测,效率与
2025-07-25 10:46