福特开发碳纤维后悬架转向节
2018-09-24 11:57:25· 来源:复材网
福特汽车公司与WMG,华威大学,Gestamp和GRM咨询公司合作,为Innovate UK开发了一款用于C级车辆的轻质复合材料后悬架转向节。结合独特的碳纤维部署,优化技术和定制的制造工艺,与目前制造的钢部件相比,可以减轻50%的重量。通过将先进
福特汽车公司与WMG,华威大学,Gestamp和GRM咨询公司合作,为Innovate UK开发了一款用于C级车辆的轻质复合材料后悬架转向节。
结合独特的碳纤维部署,优化技术和定制的制造工艺,与目前制造的钢部件相比,可以减轻50%的重量。
通过将先进的加工技术与GRM的模拟技术相结合,该团队开发出了同类产品中的第一个。该部件的设计是完整的,该部件的制造试验目前正在进行,以开发全面的批量生产过程。
介绍
全球汽车行业正在推动更严格的质量目标,以满足不断增加和严格的排放法规以及客户对扩展范围的电动汽车的需求。福特选择通过选择系列钢悬架部件并将设计重新设计为可生产的复合轻质部件来开始开发周期。所选择的部件呈现出相互矛盾的结构要求,具有最小和最大刚度,屈曲和强度目标。这种特殊的非弹簧部件的重量减轻增加了弹簧和减震器的相对效率,从而提高了乘客的舒适度和驾驶员操控性。这种新开发的复合材料部件证明适用于高性能C级车辆。在材料和工艺选择之间获得的精细和完美的平衡导致总循环时间低至5分钟。这个短周期时间是可比的,或者在大多数情况下,超过了旧制造技术的处理时间。
合作至关重要
这一成功案例是由Innovate UK部分资助的两年项目的结果,该项目由福特汽车公司,Gestamp,WMG,华威大学和GRM咨询等一系列组织执行。该项目名为“复合轻型汽车悬架系统”(CLASS)。复合材料技术不得不从学术界和航空航天工业发展到主流汽车工程实践,以抵消电动和自动车辆固有的重量增加。复合材料行为的复杂性仍然是整个主流汽车行业需要克服的挑战。虽然大量的研究致力于理解工业和学术界的复合材料,复合材料行为的预测艺术仍处于起步阶段。GRM咨询公司在开发赛车运动中的碳纤维结构预测工具方面拥有数十年的经验,通过规避传统方法以及减少所需的物理测试量,为该项目做出了重大贡献。使用VR&D Genesis作为FEA和设计优化软件,GRM采用了基于优化的方法来降低成本和工程时间,而不会影响性能。这需要理解在强度,刚度和屈曲载荷情况下无限多种纤维取向组合的机制的失效点。
设计方法:
在项目的两年开发期间,复合材料部件的设计从单一材料部件演变为多材料设计,挑战制造和优化团队。基于各种文章的初步调查表明,复合轻质关节的想法可以通过单一材料片状模塑料(SMC)实现。然而,漫长的工程时间表最终导致设计工程团队走向多材料系统; 其中预浸料层具有所需的平面机械性能,并且SMC的包覆成型允许复杂的几何细节和面外硬化。将单轴和双轴预浸料与SMC结合的方法表明,复合材料部件可以实现机械强度,刚度和屈曲目标。其他设计挑战意味着必须引入进一步的创新,同时保持设计简介而不影响制造。该设计仅在完成大量模拟和实验工作后才最终确定。这已经优化和改进了设计,以满足OEM耐用性和NVH目标。
该项目实现的最终重量减少至少30%,可能具有50%的优异功能,具有相同的功能。
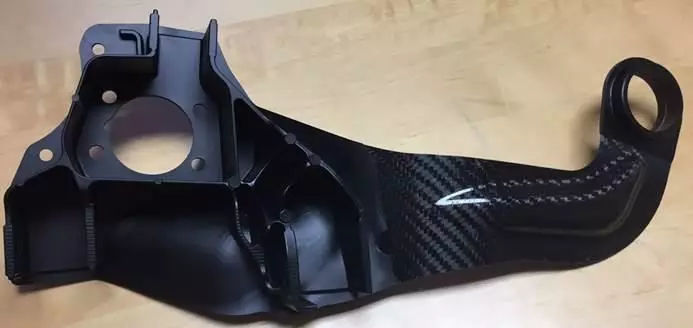
图1:钢制转向节叶片
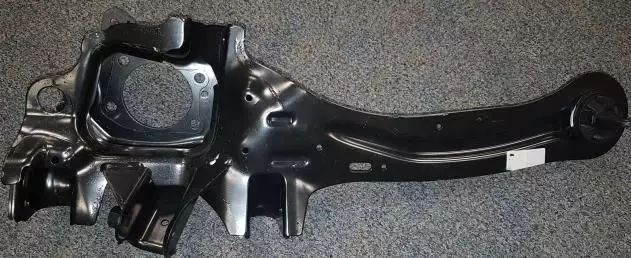
图2:原型复合转向节 - 系叶片
创新的制造技术:
已经开发出一种压缩成型制造工艺,能够大规模制造这种高强度和复杂形状的悬架转向节。2017年第二季度将展示制造和物理测试的示范部分。
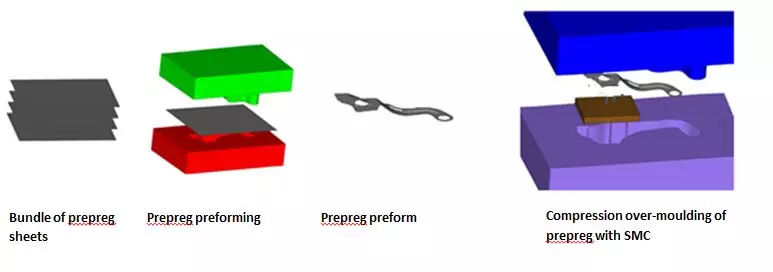
图3:复合材料部件的制造步骤
使用由Mitsubishi Rayon Corporation提供的材料,基本工具的图示如图3所示。在开始制造复合转向节连接刀片之前,CLASS候选碳纤维材料在迪尔伯恩的福特研究与创新中心成型。美国。这种经验有助于项目优化工艺参数,从而获得最大的机械性能和几何精度。
经验教训
通过GRM Consulting和相关公司的共同努力,该项目的结构和减重目标得以实现,而项目期间获得的经验帮助工程师了解如何在多材料设计中实现最佳平衡。随着它的发展,VR&D Genesis中的优化方法得到了改进,材料选择方法得到了修改,以支持设计和制造工程师满足严格的要求。
福特向项目团队提出挑战,要求他们提供一个高度复杂且负载很重的部件,这表明如果可以提供,那么许多其他车辆部件将相对简单。有迹象表明,这是通过减轻重量来实现的,从而为整个车辆提供了巨大的机会。
举报 0
收藏 0
分享 89
-
高温季行车安全需重视:TRW SPS 制动盘让你的刹
2025-07-19 -
跨越速运凭什么“圈粉”万千客户?“中国零担30
2025-07-01 -
驭动未来,智启新程-采埃孚油护新出行
2025-06-25 -
旭化成荣获2025年度发明表彰,助力离子交换膜法
2025-06-11
编辑推荐
最新资讯
-
辐射亚太,链接全球——采埃孚再制造
2025-07-30 11:46
-
思看科技发布子品牌SCANOLOGY,全球
2025-07-30 11:06
-
风雨不动安如山——比亚迪叉车构筑“
2025-07-30 08:48
-
NEAS CHINA 新能源汽车技术与生态链
2025-07-29 09:52
-
三维扫描革新碾磨机辊套检测,效率与
2025-07-25 10:46