数字化制造支持领先汽车零部件供应商的主要业务举措
2018-08-28 15:45:44· 来源:西门子plm
Behr价值流程图和物料流仿真提高了制造的灵活性。
业务挑战
-提高生产效率
-建立更灵活的制造工艺
-转变生产战略,支持多种产品制造
-实现工艺标准化
-修改流程以优化和降低成本
-彰显卓越,提高质量
成功关键
-借助价值流程图找出弱点
-借助 Tecnomatix® Plant Simulation 确定最佳制造方案
-核查和验证物料流规划
结果
-生产效率最高可提高 35%
-生产周期最高可缩短 66%
-成功地将制造过程从被动转变为主动
-减少了工作量,平均每天可节省数千欧元的开销
-缩短了交付时间
-缩短了对客户要求的响应时间
行业
汽车及交通运输
客户主要业务
Behr 是汽车空调和发动机冷却系统制造商。
解决方案/服务
-Tecnomatix
-Tecnomatix Plant Simulation
客户位置
斯图加特
德国
"最终结果证明了部署该软件的正确性。投入的成本很快就收回来了。"
Markus Schmidt
工艺设计人员
Behr
"该试点项目获得了极大成功。有 Siemens PLM Software 的大力支持,我相信此试点项目仅仅是个开始,未来会出现更多工艺优化项目。"
Juergen Wolf
油冷却器工艺设计和优化业务部门负责人
Behr
生产成本优化的促进因素
Behr Group 是一个为国际汽车产业服务的系统合作伙伴。Behr 总部设在德国斯图加特,在全球总共约有 17,000 名员工,分布在 17 个开发中心、28 个生产基地和 12 家合资企业。Behr 是汽车空调和发动机冷却系统的专业厂商,是全球领先的客车和商用车领域原始设备制造商和供应商之一。
Behr 的发动机冷却业务部负责设计并制造复杂的系统,同时确保每个品牌和类型对客户而言都是颇具成本效益的解决方案。此外,由于 Behr 是汽车行业主要的供应商,该公司面临着越来越大的成本压力,并且一直在寻找用于优化其生产成本的好方法。
制造工艺的灵活性是推动 Behr 优化生产过程的关键因素。在当今的经济形式下,Behr 需要增加所提供的产品变型数量。产品复杂性在不断提高,而发动机部件的生产周期却在不断缩短(虽然目前已经很短了,仅有 12 至 24 个月),这主要因为要满足新制定或修订的符合性法规要求,例如欧洲排放标准。
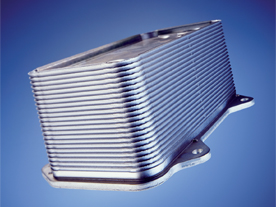
数字化制造之路
在 2008 年,Behr 启动了一个试点项目,专门优化其 Muehlacker 生产基地的栈板油冷却器的制造工艺。传统上,此生产基地主要制造结构严格定义的单一产品。为了提高竞争力,该公司将其单一产品制造系统更换为更加灵活的制造系统,以便能够生产多种产品和具有多种变型与选择的产品。
“我们并没有多少数字化制造经验,”Behr 的栈板油冷却器工艺设计人员 Markus Schmidt 解释说。他和 12 名同事放弃使用 ERP 和 CAD 数据,一直在使用表格式计算表单和演示程序制定制造计划。他们专门设立了一个试点项目,以通过在 Siemens PLM Software 的 Tecnomatix Plant Design and Optimization 解决方案中使用 Tecnomatix® Plant Simulation 应用程序来促进多种产品制造工艺优化。借助 Plant Simulation,企业能够在正式实施和启动实际的生产系统之前检验和精确验证物料流方案。
在该项目开始时,首先使用价值流程图评估 Behr 的现有制造情况。利用此分析技术,项目团队确定该生产基地的主要弱点是被动控制战略,建议 Behr 转为采用主动战略。若要提高生产效率,需要缩短生产周期,减少工作量,消除制造设备之前不必要的物料缓冲区。
引入全自动化零件制造的需要还给工艺设计人员带来了更多挑战。以前,Behr 会购买栈板核心部件,并将这些部件通过去油设备进行处理。在手动制造过程中,工作人员组装冷却器、填充和控制真空炉,并对完成的冷却器进行裂隙测试。为了便于完全实现零件制造自动化,需要结合使用这两个不同系统,并且必须正确校准工艺控制。“栈板油冷却器是转变多种产品制造战略的理想测试目标,”Schmidt 说。“使用的热交换板数量决定了冷却器的性能。因此,我们能够生产可为各种发动机提供足够冷却效果的各种设备。从理论上讲,能够以相同方式实现多种产品变型。”
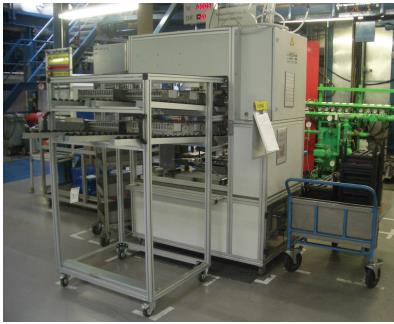
利用仿真推进最佳实践工艺
利用价值流程图和工艺团队在设备利用和制造方面的专业技术知识,该公司的工艺设计人员能够开发出一个具备多种不同方案的目标模型。工艺团队利用 Plant Simulation 评估这些方案的生产效率和生产周期。仿真结果显示该公司需要建立缓冲区以协调两种不同工艺因素。Behr 决定使用 FiFo(先进先出)缓冲区来应付这项任务,协助生产基地优化真空炉,这一直是制造工艺中的关键瓶颈。
对仿真模型的进一步调整着重于自动和手动制造工艺之间的结合点。虽然缓冲区设计成每个类型最多容纳 320 个零件,但仿真结果表明,缓冲区中的零件数量最好不要超过 200 个。 在将仿真结果与 Behr 传统规划方法进行比较后,Plant Simulation 的价值就会变得十分明显。实际上,如果不使用仿真,缓冲区的大小可能会达到必要大小的两倍。
最终,该公司的工艺设计人员能够通过仿真技术减少工作量。在过去采用的被动制造方法中,工艺链中所用的每类零件达到了 2,000 个。Behr 成功转为采用主动制造战略后,现在每类零件只有 700 个。
真空炉的利用率提高之后,消除了所有空闲时间(需要冷却和加热的阶段除外)。已经成功消除了所有不必要的缓冲区。该公司建立了理想的订单管理流程后,生产周期显著缩短了。Plant Simulation 发挥了关键作用,帮助公司工艺设计人员在可能实现节约和改进的方面作出正确的选择。现在,通过仿真可以详细规划和精确验证整个物料流。此外,已经彻底消除了费时费钱的发布更正。
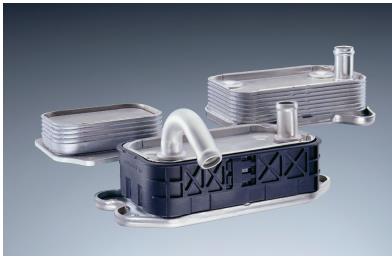
显著的日常收益
Behr 在栈板油冷却器的制造工艺中实施了最大部分的所需变更。最重要的是,借助经过优化的新工艺,该公司能够持续提高生产效率和实现财务收益。“最终结果证明了部署该软件的正确性;投入的成本很快就收回来了。”Schmidt 说。
所有仿真结果都在实践中得到了确认。工作量的减少每天可节约数千欧元的固定资金,一年下来就是好几百万欧元。从被动制造战略向主动制造战略的转换以及将生产控制转变为优化的 FiFo 缓冲区,改进了工艺同步并将生产周期缩短了高达 66%。交付时间显著缩短。Behr 现在能够更灵活、更快速地响应客户要求。该公司新的多种产品灵活制造系统能够在更短时间内生产出具有更多变型的产品。借助新方法,Behr 还使生产效率提高高达 35%。
“通过实施灵活的制造系统,我们能够以更加轻松的方式满足更多变型要求,更快地适应新形势,”Behr 油冷却器工艺设计和优化业务部门负责人 Juergen Wolf 解释说。“Plant Simulation 带来的好处大大提高了整个公司对数字化制造的关注。我相信此试点项目仅仅是个开始,未来会出现更多工艺优化项目。”
-提高生产效率
-建立更灵活的制造工艺
-转变生产战略,支持多种产品制造
-实现工艺标准化
-修改流程以优化和降低成本
-彰显卓越,提高质量
成功关键
-借助价值流程图找出弱点
-借助 Tecnomatix® Plant Simulation 确定最佳制造方案
-核查和验证物料流规划
结果
-生产效率最高可提高 35%
-生产周期最高可缩短 66%
-成功地将制造过程从被动转变为主动
-减少了工作量,平均每天可节省数千欧元的开销
-缩短了交付时间
-缩短了对客户要求的响应时间
行业
汽车及交通运输
客户主要业务
Behr 是汽车空调和发动机冷却系统制造商。
解决方案/服务
-Tecnomatix
-Tecnomatix Plant Simulation
客户位置
斯图加特
德国
"最终结果证明了部署该软件的正确性。投入的成本很快就收回来了。"
Markus Schmidt
工艺设计人员
Behr
"该试点项目获得了极大成功。有 Siemens PLM Software 的大力支持,我相信此试点项目仅仅是个开始,未来会出现更多工艺优化项目。"
Juergen Wolf
油冷却器工艺设计和优化业务部门负责人
Behr
生产成本优化的促进因素
Behr Group 是一个为国际汽车产业服务的系统合作伙伴。Behr 总部设在德国斯图加特,在全球总共约有 17,000 名员工,分布在 17 个开发中心、28 个生产基地和 12 家合资企业。Behr 是汽车空调和发动机冷却系统的专业厂商,是全球领先的客车和商用车领域原始设备制造商和供应商之一。
Behr 的发动机冷却业务部负责设计并制造复杂的系统,同时确保每个品牌和类型对客户而言都是颇具成本效益的解决方案。此外,由于 Behr 是汽车行业主要的供应商,该公司面临着越来越大的成本压力,并且一直在寻找用于优化其生产成本的好方法。
制造工艺的灵活性是推动 Behr 优化生产过程的关键因素。在当今的经济形式下,Behr 需要增加所提供的产品变型数量。产品复杂性在不断提高,而发动机部件的生产周期却在不断缩短(虽然目前已经很短了,仅有 12 至 24 个月),这主要因为要满足新制定或修订的符合性法规要求,例如欧洲排放标准。
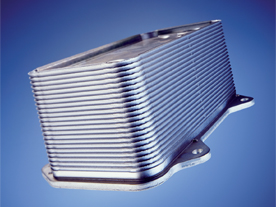
数字化制造之路
在 2008 年,Behr 启动了一个试点项目,专门优化其 Muehlacker 生产基地的栈板油冷却器的制造工艺。传统上,此生产基地主要制造结构严格定义的单一产品。为了提高竞争力,该公司将其单一产品制造系统更换为更加灵活的制造系统,以便能够生产多种产品和具有多种变型与选择的产品。
“我们并没有多少数字化制造经验,”Behr 的栈板油冷却器工艺设计人员 Markus Schmidt 解释说。他和 12 名同事放弃使用 ERP 和 CAD 数据,一直在使用表格式计算表单和演示程序制定制造计划。他们专门设立了一个试点项目,以通过在 Siemens PLM Software 的 Tecnomatix Plant Design and Optimization 解决方案中使用 Tecnomatix® Plant Simulation 应用程序来促进多种产品制造工艺优化。借助 Plant Simulation,企业能够在正式实施和启动实际的生产系统之前检验和精确验证物料流方案。
在该项目开始时,首先使用价值流程图评估 Behr 的现有制造情况。利用此分析技术,项目团队确定该生产基地的主要弱点是被动控制战略,建议 Behr 转为采用主动战略。若要提高生产效率,需要缩短生产周期,减少工作量,消除制造设备之前不必要的物料缓冲区。
引入全自动化零件制造的需要还给工艺设计人员带来了更多挑战。以前,Behr 会购买栈板核心部件,并将这些部件通过去油设备进行处理。在手动制造过程中,工作人员组装冷却器、填充和控制真空炉,并对完成的冷却器进行裂隙测试。为了便于完全实现零件制造自动化,需要结合使用这两个不同系统,并且必须正确校准工艺控制。“栈板油冷却器是转变多种产品制造战略的理想测试目标,”Schmidt 说。“使用的热交换板数量决定了冷却器的性能。因此,我们能够生产可为各种发动机提供足够冷却效果的各种设备。从理论上讲,能够以相同方式实现多种产品变型。”
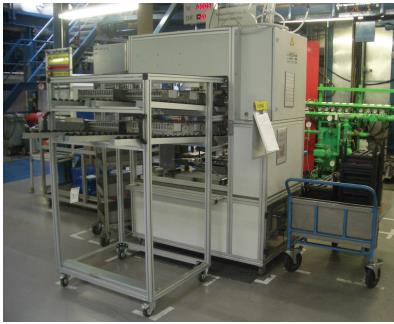
利用仿真推进最佳实践工艺
利用价值流程图和工艺团队在设备利用和制造方面的专业技术知识,该公司的工艺设计人员能够开发出一个具备多种不同方案的目标模型。工艺团队利用 Plant Simulation 评估这些方案的生产效率和生产周期。仿真结果显示该公司需要建立缓冲区以协调两种不同工艺因素。Behr 决定使用 FiFo(先进先出)缓冲区来应付这项任务,协助生产基地优化真空炉,这一直是制造工艺中的关键瓶颈。
对仿真模型的进一步调整着重于自动和手动制造工艺之间的结合点。虽然缓冲区设计成每个类型最多容纳 320 个零件,但仿真结果表明,缓冲区中的零件数量最好不要超过 200 个。 在将仿真结果与 Behr 传统规划方法进行比较后,Plant Simulation 的价值就会变得十分明显。实际上,如果不使用仿真,缓冲区的大小可能会达到必要大小的两倍。
最终,该公司的工艺设计人员能够通过仿真技术减少工作量。在过去采用的被动制造方法中,工艺链中所用的每类零件达到了 2,000 个。Behr 成功转为采用主动制造战略后,现在每类零件只有 700 个。
真空炉的利用率提高之后,消除了所有空闲时间(需要冷却和加热的阶段除外)。已经成功消除了所有不必要的缓冲区。该公司建立了理想的订单管理流程后,生产周期显著缩短了。Plant Simulation 发挥了关键作用,帮助公司工艺设计人员在可能实现节约和改进的方面作出正确的选择。现在,通过仿真可以详细规划和精确验证整个物料流。此外,已经彻底消除了费时费钱的发布更正。
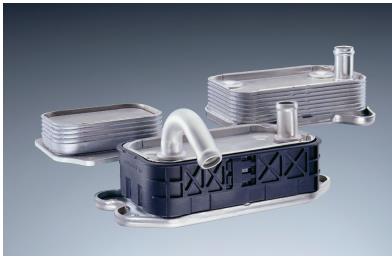
显著的日常收益
Behr 在栈板油冷却器的制造工艺中实施了最大部分的所需变更。最重要的是,借助经过优化的新工艺,该公司能够持续提高生产效率和实现财务收益。“最终结果证明了部署该软件的正确性;投入的成本很快就收回来了。”Schmidt 说。
所有仿真结果都在实践中得到了确认。工作量的减少每天可节约数千欧元的固定资金,一年下来就是好几百万欧元。从被动制造战略向主动制造战略的转换以及将生产控制转变为优化的 FiFo 缓冲区,改进了工艺同步并将生产周期缩短了高达 66%。交付时间显著缩短。Behr 现在能够更灵活、更快速地响应客户要求。该公司新的多种产品灵活制造系统能够在更短时间内生产出具有更多变型的产品。借助新方法,Behr 还使生产效率提高高达 35%。
“通过实施灵活的制造系统,我们能够以更加轻松的方式满足更多变型要求,更快地适应新形势,”Behr 油冷却器工艺设计和优化业务部门负责人 Juergen Wolf 解释说。“Plant Simulation 带来的好处大大提高了整个公司对数字化制造的关注。我相信此试点项目仅仅是个开始,未来会出现更多工艺优化项目。”
编辑推荐
最新资讯
-
辐射亚太,链接全球——采埃孚再制造
2025-07-30 11:46
-
思看科技发布子品牌SCANOLOGY,全球
2025-07-30 11:06
-
风雨不动安如山——比亚迪叉车构筑“
2025-07-30 08:48
-
NEAS CHINA 新能源汽车技术与生态链
2025-07-29 09:52
-
三维扫描革新碾磨机辊套检测,效率与
2025-07-25 10:46