整体成形多向压力机
2018-08-22 10:22:49· 来源:锻造与冲压
想要具有几何形状分支的锻件以整体成形的方式制造,这个过程无法通过传统单轴锻造的方式实现,但是可以通过使用多向压力机来实现。在很多应用领域,使用多向压力机的目的就是通过无飞边锻造来减少材料的消耗。多向压力机具有高度柔性,可以专门使用配备6根压力机轴的液压驱动器。
想要具有几何形状分支的锻件以整体成形的方式制造,这个过程无法通过传统单轴锻造的方式实现,但是可以通过使用多向压力机来实现。在很多应用领域,使用多向压力机的目的就是通过无飞边锻造来减少材料的消耗。多向压力机具有高度柔性,可以专门使用配备6根压力机轴的液压驱动器。
下文介绍的是横向挤压和模锻领域的多向液压机。涡轮机叶片预成形件的锻造,可以通过卧式液压锻造机HWS和灵活的液压预成形设备“FlexiMat”来实现。
单动压力机大多配备一个垂直压力机轴,该装置能够同时闭合模具并开启实际成形过程。另外,双动压力机配备一个附加压力机轴,通常是拉深垫。多轴压力机配备有2至6个压力机轴,因此,闭模动作可以与实际成形过程分离,这是无飞边锻造的基础。
多轴压力机的优先驱动器是液压驱动器,因为没有具体下死点的液压机的行程可以灵活修改,而且速度也是可调的。此外,最大压力可能会出现在行程中的任意一点。特别是在配备了压力轴的大型锻造中心,只有液压传动装置可以与单个轴进行灵活组合。当使用多轴压力机锻造时,需要区分两个应用范围:横向挤压过程和专用模锻过程。
目前,图1展示的配件通常用单动压力机制造,这就意味着会产生毛边。这会造成过高的材料消耗、大量的无用功以及竞争劣势,尤其对于大批量生产的配件。通过无飞边锻造的方式在闭模中生产这种配件,至少需要一个附加压力机轴或者一个带有附加功能的专用工具。图1展示的锻件,在节约材料和减少毛边的模锻压力机中生产。长度从3米到15米的大型曲轴在单次行程的操作中锻造,该尺寸的曲轴多为船用柴油机、大型泵和压力机的偏心轴。
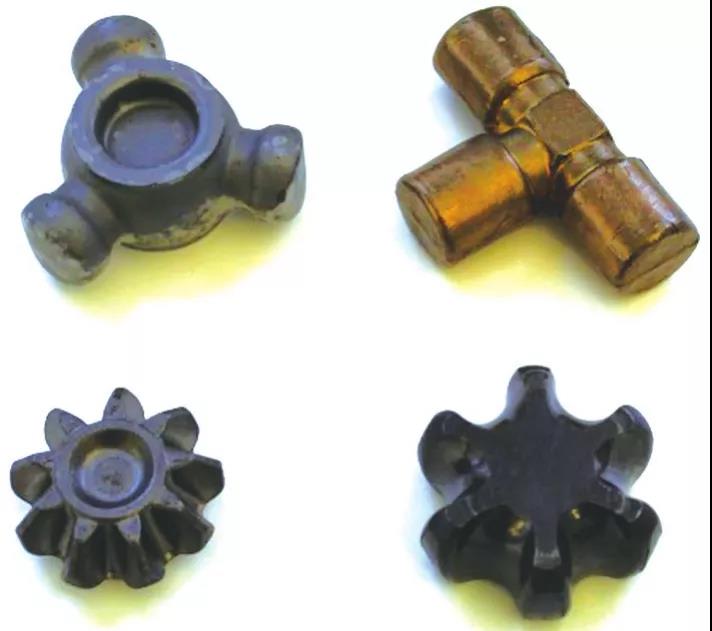
图1 使用多轴液压机的例子
横向挤压力机
需要使用4根可移动的轴,通过横向挤压的方式制造一个锻件。从图2可以看出,首先将坯料定位,然后两个平分模具闭合,最后横向冲头开始横向挤压。多轴压力机或专用闭合装置对横向挤压来说十分必要,因为在这个过程中,轴可以通过液压的方式组合,也可以通过气压弹簧的方式组合。
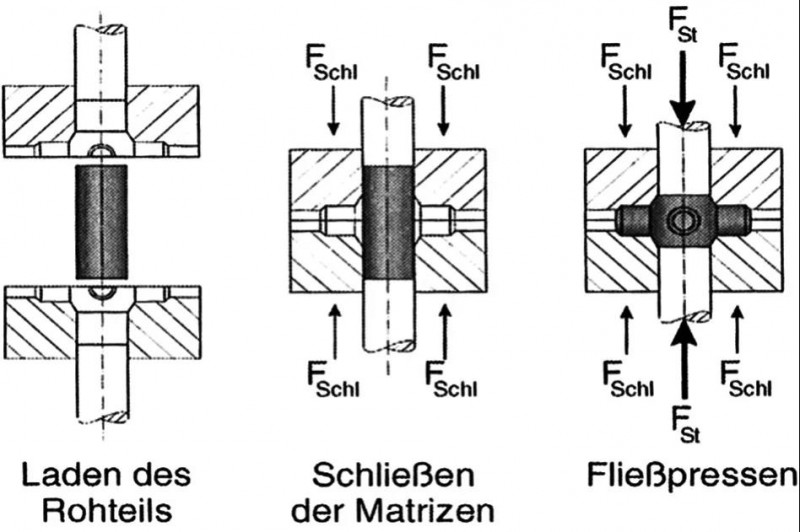
图2 横向挤压的加工过程
模锻操作
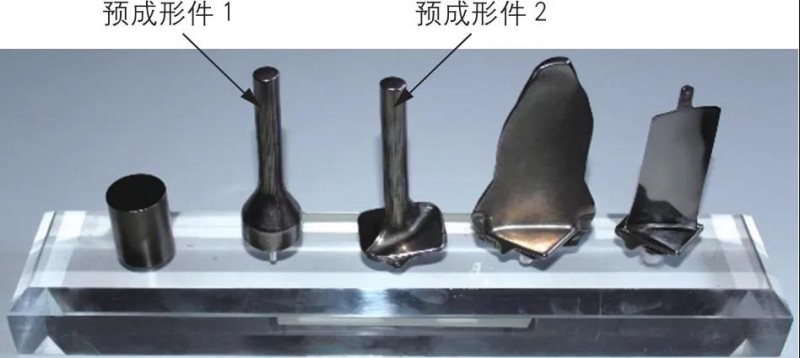
图3 涡轮机叶片的工序
涡轮机叶片是安全零件。因此,需要特别关注无瑕疵的预成形。预成形件通过两个步骤制造,几乎没有毛边(图3)。在分隔开的闭模中,首先通过镦锻来增加材料头部的体积,然后再制成涡轮机叶片。通常使用螺旋压力机,在没有加工改造预成形件的情况下进行终锻。涡轮机叶片的预成形件经过一两次打击后锻造,随后在螺旋压力机上加工成涡轮机叶片。
卧式液压锻造机HWS
即使到今天,上述操作都是通过机械传动的卧式锻造机实现的。图4为机械镦锻机的功能原理。卧式镦锻压头作为偏心驱动器,由主传动装置驱动。夹持驱动器用来关闭两部分组成的模具。它是垂直设置的,由一个带有主传动装置的坚硬机械轴节驱动。
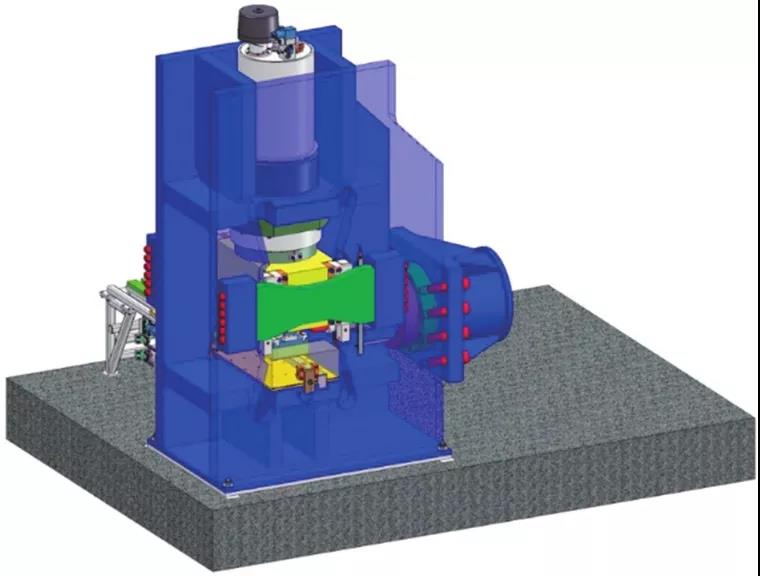
图4 机械镦锻机的功能原理
这些机器最大的问题就是两个紧密结合的驱动器之间的永久相互作用。此外,它们是不可弯曲的,模具尺寸和闭合高度都是无法改变的。
卧式液压锻造机HWS是在传统卧式机械锻造机上进一步开发的产品,目前该产品仍在世界范围内使用。HWS的独立液压轴改善了不利条件。夹持力最多可以设置为最大顶锻力的150%,且能够安全地关闭机具,并独立进行镦锻操作。并且,可以保留正在使用的机具。在控制工程方面,配备了具有自动机械和传输系统的自动装置。
拉斯科公司首台HWS(图5)的顶锻力达到3150kN,该产品将于2018年秋天交付给涡轮机叶片制造商。该客户拥有数台传统卧式锻造机,希望通过此设备大幅度提高叶片预成形件的精度。
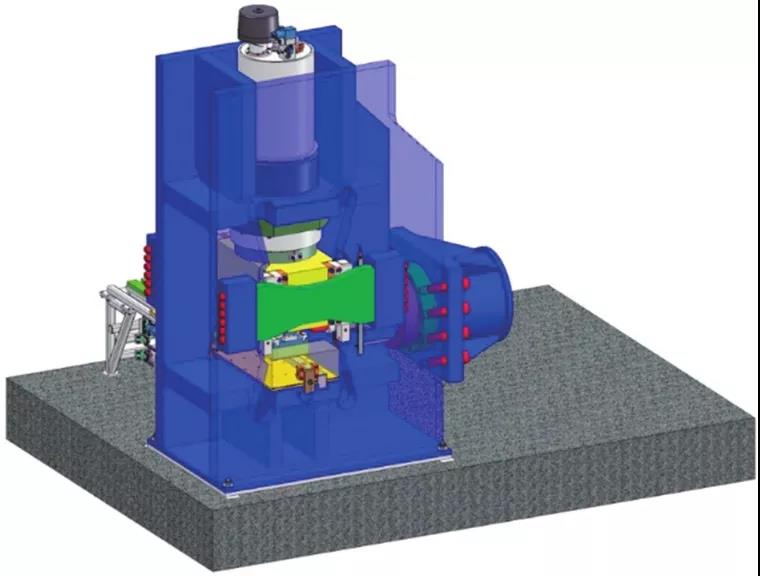
图5 卧式液压锻造机HWS
液压预成形机器——FlexiMat
FlexiMat的开发源于德国联邦教育与研究部资助的一个项目(资金编号:17PNT023),并在固态成形行业的LFM Iserlohn公司和拉斯科公司的指导下进行。两个公司共同设计了预成形机,开发了机器的基本功能,评估了机器效率。
FlexiMat的特点是拥有两个垂直的闭合和成形轴以及两个独立的卧式镦锻轴的模块化设计(图6)。因此,可以生产七个基础形状——在组合物中,可以通过多个(多达三种)成形方法制作更多几何形状复杂的零件,可以进行单独和多重操作的传输系统用来运输零件。
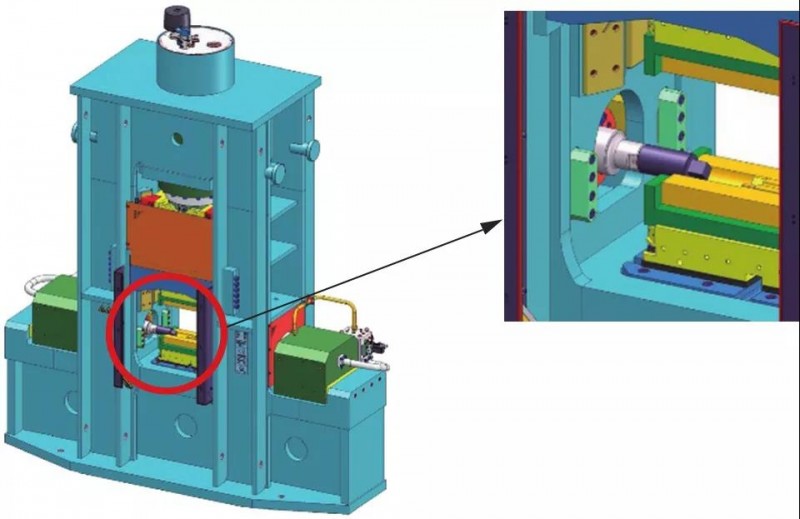
图6 FlexiMat的功能原理
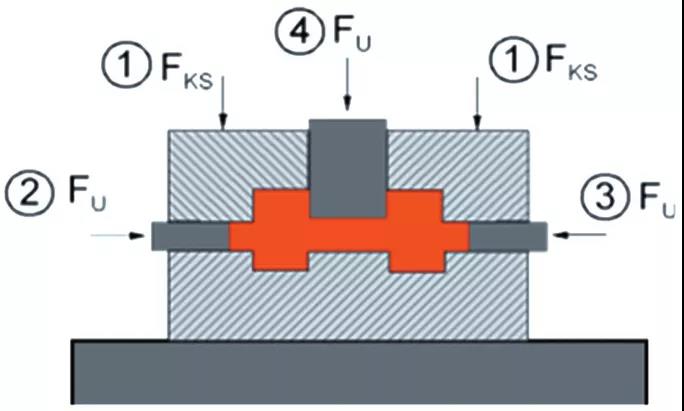
图7 FlexiMat 40/60
同时,拉斯科公司已经可以批量生产FlexiMat。该型号首台压力机FlexiMat 40/60(图7)拥有4000kN的卧式顶锻力,6000kN的闭合力。我们的客户Leistritz Turbinentechnik已经预定了该机器。该机器将被交付给位于泰国的工厂,与其同时引进的拉斯科螺旋压力机SPR 1600的预成形设备配套使用。
液压伺服直接驱动器
如上所述,液压驱动器是一个独特的驱动器,可以灵活地将多个压力机轴彼此联接起来。过去几年,拉斯科公司一直关注最新开发的液压伺服直接驱动器。该驱动技术以启动液压泵的伺服电动机而著名。与伺服电动机出色的可控性原理相反,传统的压力机驱动器通常受到恒速运转的异步电动机的影响。伺服电动机可以精确地控制速度、扭矩和泵转子的位置。因此,可以通过伺服电动机单独控制速度、压力、甚至是液压缸的活塞位置。控制阀和调节阀的使用并不是必需的。图8显示了传统液压驱动器和现代化液压伺服直接驱动器的对比。
通常情况下,液压伺服泵在活塞上面运行驱动,另一个泵或者泵组在活塞下面运行驱动。驱动原理还允许进行能量恢复,这指的是压制操作之后,油缸中的压缩油通过泵反转来启动伺服电动机。除了出色的可控性,伺服直接驱动器在节能方面拥有明显优势,因为当压力机油缸没有移动的时候,所有的电机都是停止的,而且无需能量。
表1 驱动系统能耗的对比
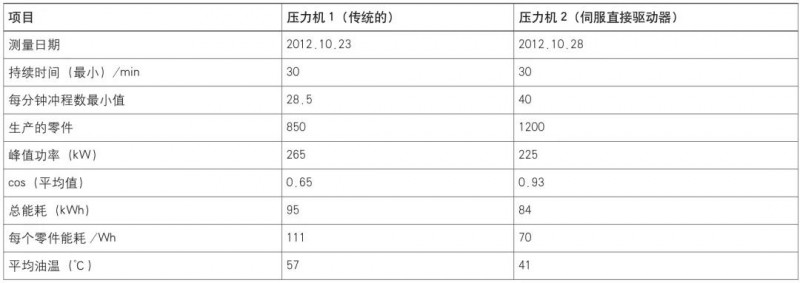
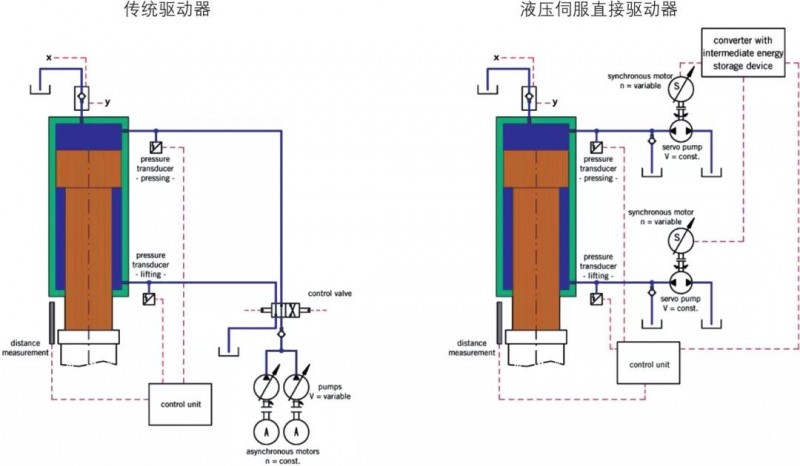
图8 传统驱动器和伺服直接驱动器的对比
拉斯科公司可以测量客户的能耗,该客户同时操作一台800吨的传统液压金属板压力机和一台配备有液压伺服直接驱动器的现代化拉斯科压力机。测量能耗时需将相同的机具在30分钟内交替安装在两个压力机中。表1显示了测量结果。液压伺服直接驱动器的单个零件的能量消耗是36.9%,小于传统液压机的能量消耗。
结束语
液压设备是多轴压力机的优先驱动系统。最新开发的液压伺服直接驱动器可以明显提高机器的灵活性和能效。涡轮机叶片生产的例子展示了两个最新开发的用于模锻操作的多轴压力机。
下文介绍的是横向挤压和模锻领域的多向液压机。涡轮机叶片预成形件的锻造,可以通过卧式液压锻造机HWS和灵活的液压预成形设备“FlexiMat”来实现。
单动压力机大多配备一个垂直压力机轴,该装置能够同时闭合模具并开启实际成形过程。另外,双动压力机配备一个附加压力机轴,通常是拉深垫。多轴压力机配备有2至6个压力机轴,因此,闭模动作可以与实际成形过程分离,这是无飞边锻造的基础。
多轴压力机的优先驱动器是液压驱动器,因为没有具体下死点的液压机的行程可以灵活修改,而且速度也是可调的。此外,最大压力可能会出现在行程中的任意一点。特别是在配备了压力轴的大型锻造中心,只有液压传动装置可以与单个轴进行灵活组合。当使用多轴压力机锻造时,需要区分两个应用范围:横向挤压过程和专用模锻过程。
目前,图1展示的配件通常用单动压力机制造,这就意味着会产生毛边。这会造成过高的材料消耗、大量的无用功以及竞争劣势,尤其对于大批量生产的配件。通过无飞边锻造的方式在闭模中生产这种配件,至少需要一个附加压力机轴或者一个带有附加功能的专用工具。图1展示的锻件,在节约材料和减少毛边的模锻压力机中生产。长度从3米到15米的大型曲轴在单次行程的操作中锻造,该尺寸的曲轴多为船用柴油机、大型泵和压力机的偏心轴。
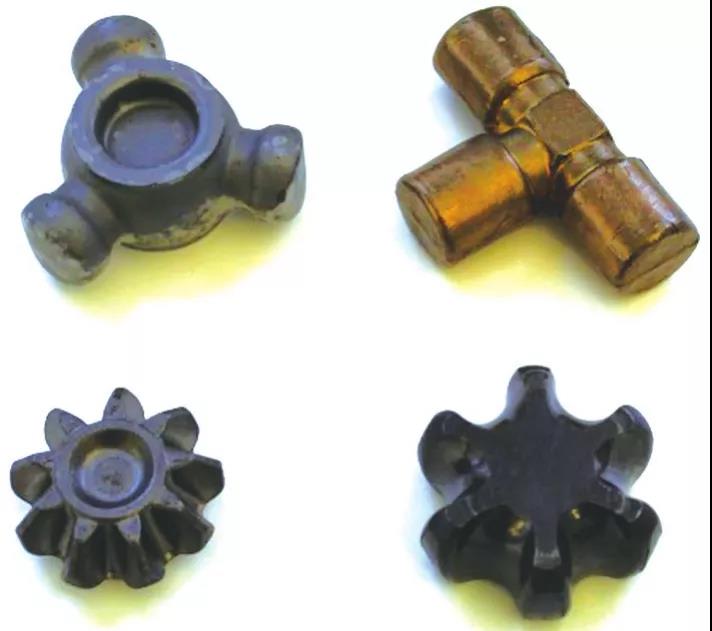
图1 使用多轴液压机的例子
横向挤压力机
需要使用4根可移动的轴,通过横向挤压的方式制造一个锻件。从图2可以看出,首先将坯料定位,然后两个平分模具闭合,最后横向冲头开始横向挤压。多轴压力机或专用闭合装置对横向挤压来说十分必要,因为在这个过程中,轴可以通过液压的方式组合,也可以通过气压弹簧的方式组合。
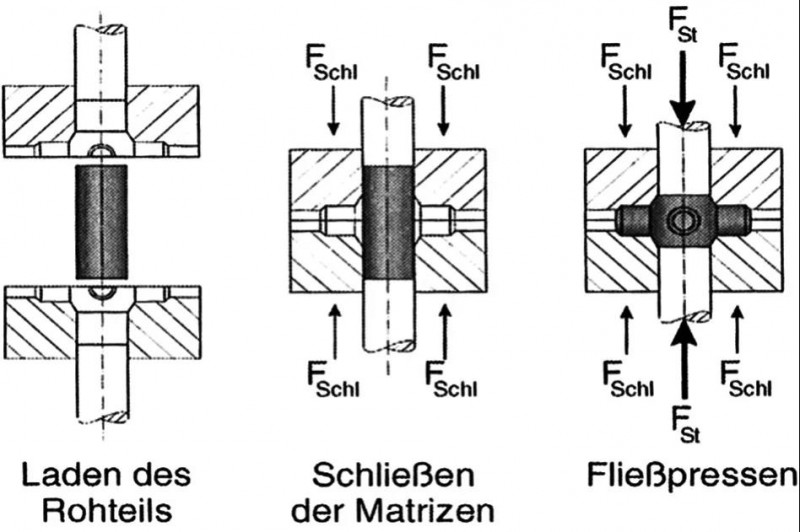
图2 横向挤压的加工过程
模锻操作
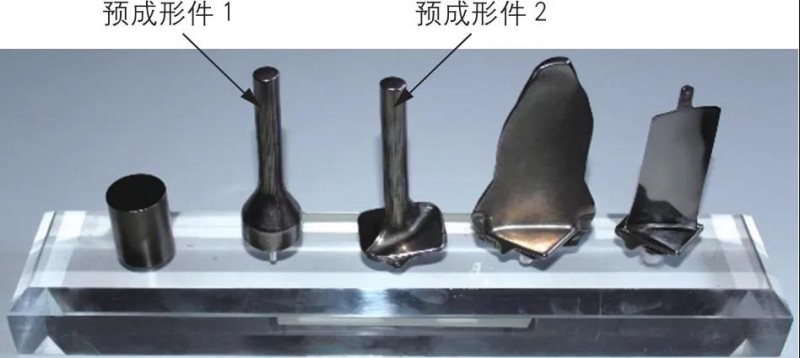
图3 涡轮机叶片的工序
涡轮机叶片是安全零件。因此,需要特别关注无瑕疵的预成形。预成形件通过两个步骤制造,几乎没有毛边(图3)。在分隔开的闭模中,首先通过镦锻来增加材料头部的体积,然后再制成涡轮机叶片。通常使用螺旋压力机,在没有加工改造预成形件的情况下进行终锻。涡轮机叶片的预成形件经过一两次打击后锻造,随后在螺旋压力机上加工成涡轮机叶片。
卧式液压锻造机HWS
即使到今天,上述操作都是通过机械传动的卧式锻造机实现的。图4为机械镦锻机的功能原理。卧式镦锻压头作为偏心驱动器,由主传动装置驱动。夹持驱动器用来关闭两部分组成的模具。它是垂直设置的,由一个带有主传动装置的坚硬机械轴节驱动。
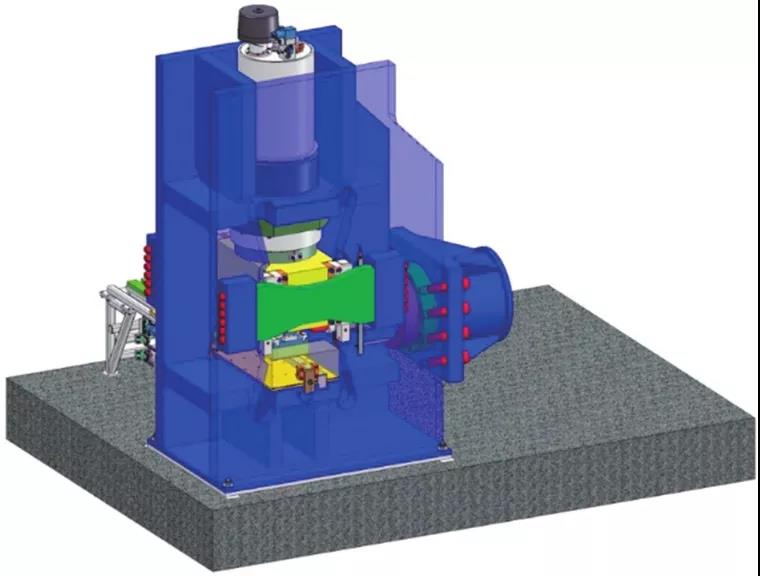
图4 机械镦锻机的功能原理
这些机器最大的问题就是两个紧密结合的驱动器之间的永久相互作用。此外,它们是不可弯曲的,模具尺寸和闭合高度都是无法改变的。
卧式液压锻造机HWS是在传统卧式机械锻造机上进一步开发的产品,目前该产品仍在世界范围内使用。HWS的独立液压轴改善了不利条件。夹持力最多可以设置为最大顶锻力的150%,且能够安全地关闭机具,并独立进行镦锻操作。并且,可以保留正在使用的机具。在控制工程方面,配备了具有自动机械和传输系统的自动装置。
拉斯科公司首台HWS(图5)的顶锻力达到3150kN,该产品将于2018年秋天交付给涡轮机叶片制造商。该客户拥有数台传统卧式锻造机,希望通过此设备大幅度提高叶片预成形件的精度。
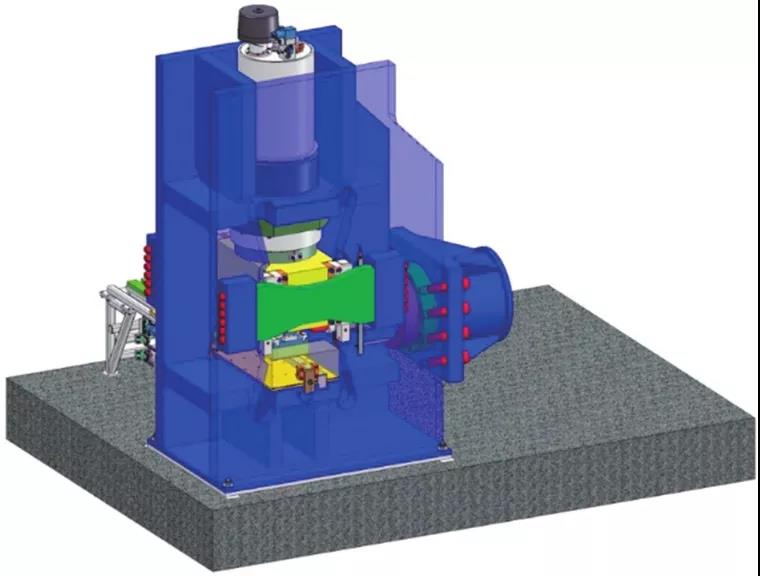
图5 卧式液压锻造机HWS
液压预成形机器——FlexiMat
FlexiMat的开发源于德国联邦教育与研究部资助的一个项目(资金编号:17PNT023),并在固态成形行业的LFM Iserlohn公司和拉斯科公司的指导下进行。两个公司共同设计了预成形机,开发了机器的基本功能,评估了机器效率。
FlexiMat的特点是拥有两个垂直的闭合和成形轴以及两个独立的卧式镦锻轴的模块化设计(图6)。因此,可以生产七个基础形状——在组合物中,可以通过多个(多达三种)成形方法制作更多几何形状复杂的零件,可以进行单独和多重操作的传输系统用来运输零件。
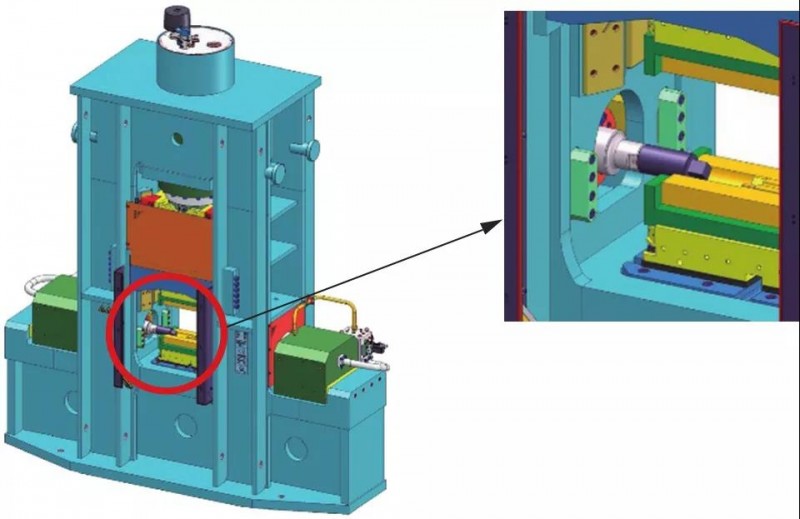
图6 FlexiMat的功能原理
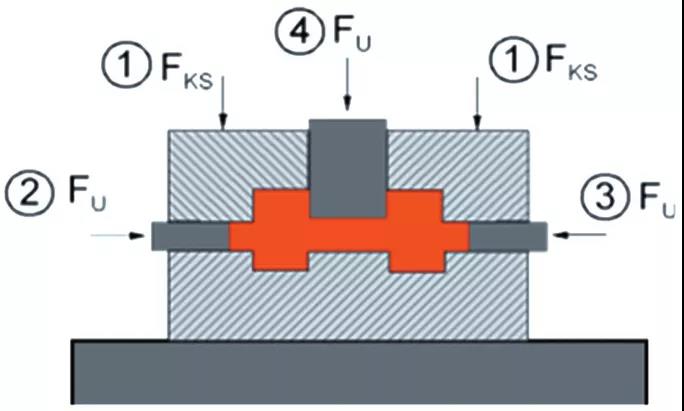
图7 FlexiMat 40/60
同时,拉斯科公司已经可以批量生产FlexiMat。该型号首台压力机FlexiMat 40/60(图7)拥有4000kN的卧式顶锻力,6000kN的闭合力。我们的客户Leistritz Turbinentechnik已经预定了该机器。该机器将被交付给位于泰国的工厂,与其同时引进的拉斯科螺旋压力机SPR 1600的预成形设备配套使用。
液压伺服直接驱动器
如上所述,液压驱动器是一个独特的驱动器,可以灵活地将多个压力机轴彼此联接起来。过去几年,拉斯科公司一直关注最新开发的液压伺服直接驱动器。该驱动技术以启动液压泵的伺服电动机而著名。与伺服电动机出色的可控性原理相反,传统的压力机驱动器通常受到恒速运转的异步电动机的影响。伺服电动机可以精确地控制速度、扭矩和泵转子的位置。因此,可以通过伺服电动机单独控制速度、压力、甚至是液压缸的活塞位置。控制阀和调节阀的使用并不是必需的。图8显示了传统液压驱动器和现代化液压伺服直接驱动器的对比。
通常情况下,液压伺服泵在活塞上面运行驱动,另一个泵或者泵组在活塞下面运行驱动。驱动原理还允许进行能量恢复,这指的是压制操作之后,油缸中的压缩油通过泵反转来启动伺服电动机。除了出色的可控性,伺服直接驱动器在节能方面拥有明显优势,因为当压力机油缸没有移动的时候,所有的电机都是停止的,而且无需能量。
表1 驱动系统能耗的对比
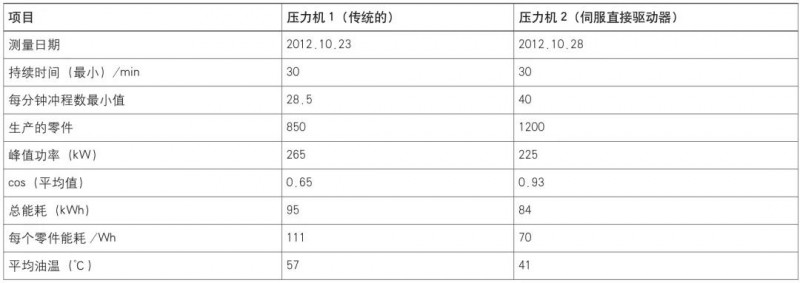
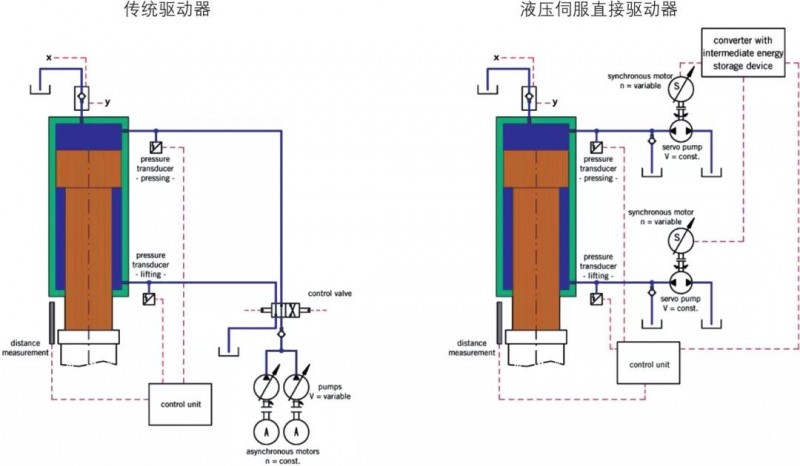
图8 传统驱动器和伺服直接驱动器的对比
拉斯科公司可以测量客户的能耗,该客户同时操作一台800吨的传统液压金属板压力机和一台配备有液压伺服直接驱动器的现代化拉斯科压力机。测量能耗时需将相同的机具在30分钟内交替安装在两个压力机中。表1显示了测量结果。液压伺服直接驱动器的单个零件的能量消耗是36.9%,小于传统液压机的能量消耗。
结束语
液压设备是多轴压力机的优先驱动系统。最新开发的液压伺服直接驱动器可以明显提高机器的灵活性和能效。涡轮机叶片生产的例子展示了两个最新开发的用于模锻操作的多轴压力机。
- 下一篇:安森美半导体谈汽车电子的新动向
- 上一篇:铝合金汽车覆盖件冲压成形的回弹模拟分析
最新资讯
-
辐射亚太,链接全球——采埃孚再制造
2025-07-30 11:46
-
思看科技发布子品牌SCANOLOGY,全球
2025-07-30 11:06
-
风雨不动安如山——比亚迪叉车构筑“
2025-07-30 08:48
-
NEAS CHINA 新能源汽车技术与生态链
2025-07-29 09:52
-
三维扫描革新碾磨机辊套检测,效率与
2025-07-25 10:46