专家解读江淮汽车涂装生产线
2018-08-10 10:04:00· 来源:AI汽车制造业
江淮汽车在涂装工艺方面一直紧跟时代发展的步伐,围绕“绿色环保、节能低碳”的精益制造理念开展工作。今天,小编带大家真正了解一下江淮汽车的涂装生产线,更有江淮汽车技术中心工艺研究院涂装工艺部技术总监邢汶平女士的详尽分享。
江淮汽车在涂装工艺方面一直紧跟时代发展的步伐,围绕“绿色环保、节能低碳”的精益制造理念开展工作。今天,小编带大家真正了解一下江淮汽车的涂装生产线,更有江淮汽车技术中心工艺研究院涂装工艺部技术总监邢汶平女士的详尽分享。
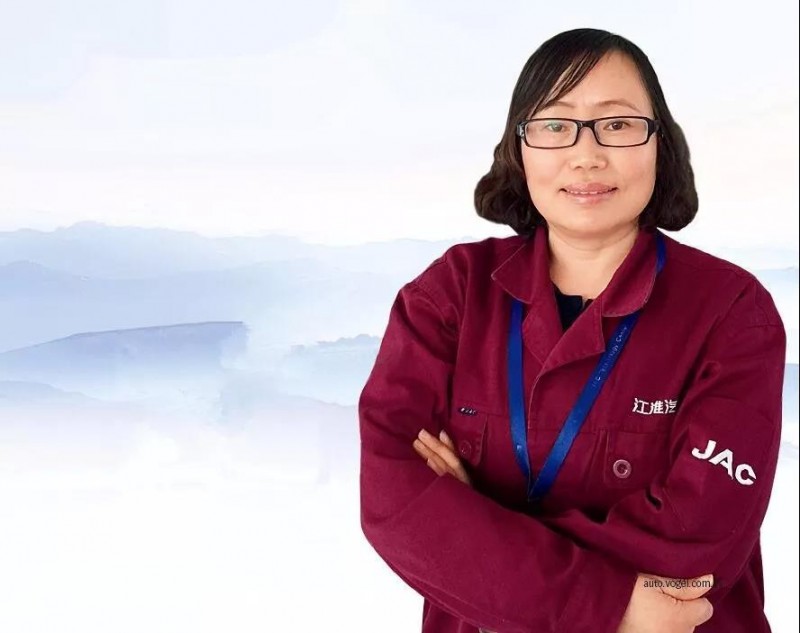
——江淮汽车技术中心工艺研究院涂装工艺部技术总监邢汶平女士
邢汶平女士担任安徽江淮汽车集团股份有限公司技术中心工艺研究院涂装工艺部技术总监一职,主要负责江淮汽车涂装生产线新建和改造项目的规划设计、建设和工艺调试工作及新产品的涂装工艺SE分析、生产线适应性改造、工艺调试和量产拉动等工作。
新技术、新设备
邢汶平女士:江淮汽车在涂装工艺方面按照安进董事长提出的“六化”要求,围绕技术领先化、制造精益化的理念,通过采用新工艺、新技术和新设备,打造“绿色环保、节能低碳”的世界先进涂装生产线。
在新工艺应用方面,江淮汽车具有敢为天下先的勇气,近几年不断引入新工艺、新技术。2012年,其率先在乘用车上采用当时国际先进的水性免中涂涂装工艺,在保证产品质量的同时,实现了能源消耗、VOC排放及生产成本的大幅下降,成为我国首条应用该技术的典范。2014年,江淮汽车采用的粉末涂料具有品质更加优良、废水/废气/废渣等零排放、涂料回收利用率高达95%以及生产成本更低等明显优势,被成功应用于商用车车厢涂装线,这也是国内首条车厢粉末生产线。
2015年,江淮汽车从欧洲引进了先进的水性单涂层工艺技术(工艺更加紧凑、VOC排放更低),用于江淮汽车遂宁工厂的素色漆生产,为国内商用车涂装线水性化改造建立了一个新的样板工厂。通过采用水性免中涂工艺取代原有3C2B溶剂型,采用水性单涂层工艺以及粉末涂料取代溶剂型单涂层技术等举措,江淮汽车实现了涂装技术在品质、绿色、精益等方面的不断升级。
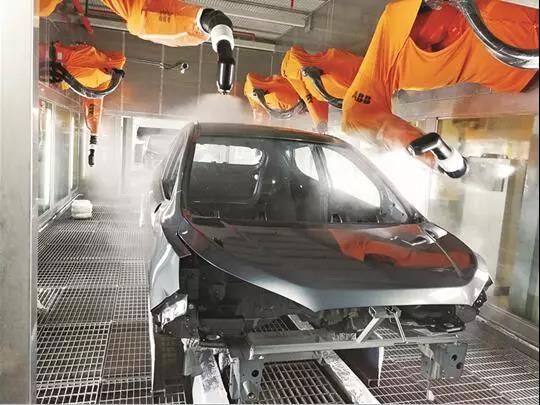
在涂装设备选型方面,江淮汽车以智能、低碳为原则,选用最先进、最节能且最环保的工艺装备。以江淮汽车新港生产基地为例,该项目车身内外表面均采用机器人喷涂,机器人数量达48台,实现了喷涂区域无人化,在保证产品一致性的同时,有效减少了人工并提高了涂料利用率。喷漆室采用最新的“空调循环风+热泵机组”节能技术,实现了单台涂装能耗下降15%。烘干系统采用TAR集中供热系统,在满足烘干加热需求的同时,实现了烘干废气焚烧达标,同时为最大程度地降低烘干能耗,设置了烟气余热回收装置,可实现年回收热量折合天然气26.2万立方米,减少碳年排放1 458.03 t。下地板涂胶采用“机器人+3D胶枪涂胶系统”,实现了地板涂胶和PVC全自动喷涂,确保地板优良防护性能,该项目建成后将是国内最先进的商用车生产线。
在环保措施方面,江淮汽车涂装线在全面采用水性涂料的同时,对于溶剂型清漆喷漆废气采用沸石转轮+RTO焚烧技术,将VOC排放量降至最低水平,可控制在 15 g/m2以下,满足国内最严格的排放限制要求,实现了真正意义上的绿色环保。
精益生产与技术先进性之间的平衡
邢汶平女士:精益生产体现在采用最合理的工艺方法和选用最适合的制造设备,而不一定是最先进的设备或技术。这需要通过对各类设备的技术特点及相关配套资源进行详细调研,在设备的投入费用、日常运行费用、废弃物处置费用以及设备维护保养费用等整个生命周期内进行系统分析,才能做出最佳选择。
我来举一个例子说明我们公司在这方面所做的工作。
设备方面,以喷漆室采用空调循环风技术为例,近几年国内外大多数汽车企业开始采用“干式喷漆室+循环风”技术实现喷涂系统的节能降耗,经过分析,我们发现该技术比较先进,也很节能,但设备投入及维护较高,且废漆渣处置费用也相对较高。
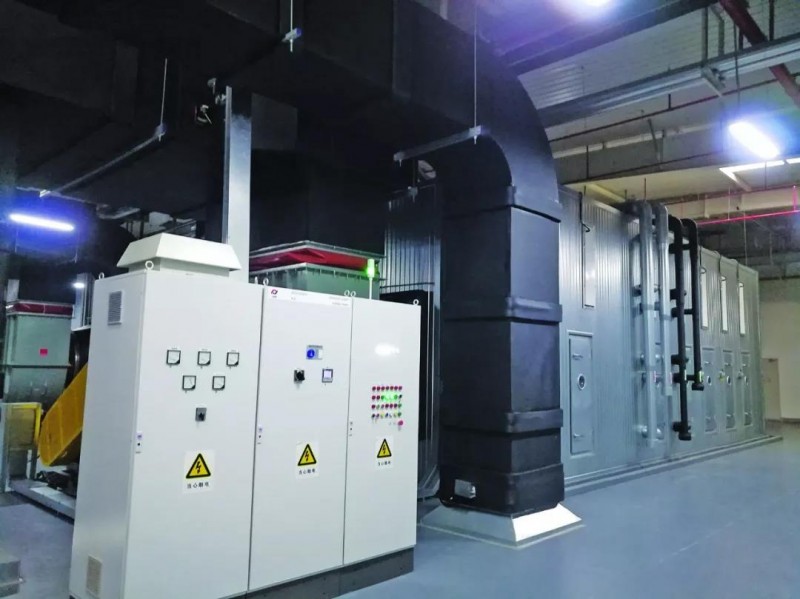
经过详细分析后,我们认为喷涂系统实现节能的根本在于采用了循环风技术,而不是取决于是否为干式喷漆室,同时文丘里形式的湿式喷漆室对喷漆漆雾的捕捉能力可以达到99%,优于目前使用的干式喷漆室,可以减轻循环风空调进口处过滤系统的压力。在漆渣处理方面,湿式喷漆室主要通过添加微量的漆雾凝聚剂进行漆渣处理,同时打捞出的漆渣经沥水干燥后,重量不会增加。
另外,湿式喷漆室技术比较成熟,已经应用了20年以上,设备已经完全国产化,同时设备运行较为稳定,基本没有设备维修费用。因此,我们最终选用了“湿式喷漆室+循环风空调+热泵”的组合方式,在同样实现节能降耗的同时,有效降低了前期的设备投入和后期的设备维护费用,经对半年的实际运行数据统计分析,可实现喷漆室区域能耗下降50%以上,整车能耗下降15%以上,这个例子仅供大家参考,适合的才是最好的。
节能环保方面的努力
邢汶平女士:我们围绕涂装生产如何实现节能降耗和绿色环保,采用具体项目具体分析的方法,根据我们的产品目标和生产线定位,设计和开发最为适合的生产工艺和涂装设备。
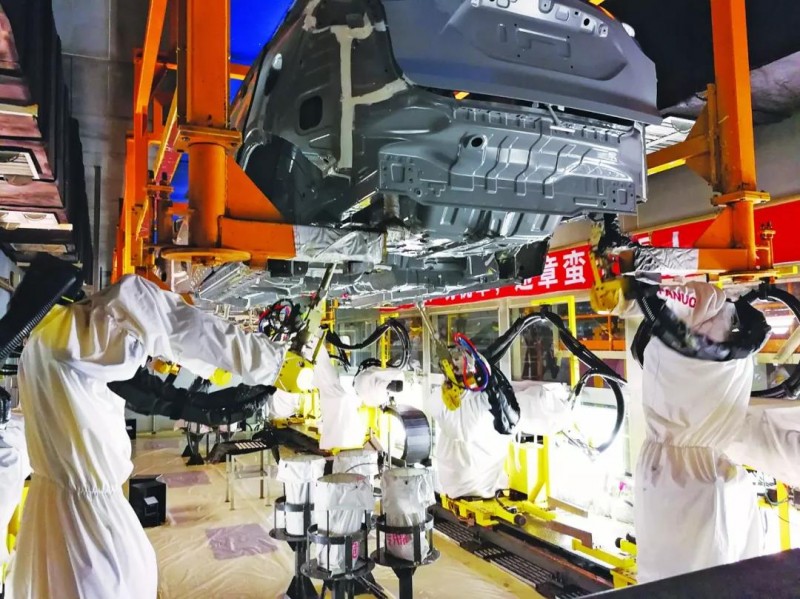
这里有一个典型例子可以说明,在我们公司大车厢涂装生产线设计过程中,经过对车厢产品特点和各类涂装工艺的优缺点进行详细分析,车厢产品需与车身的颜色相匹配,因此其颜色主要有白色、蓝色(素色漆)和蓝色、红色等金属漆为主,其中白色占比为50%以上。而粉末涂料素色漆喷涂可采用2C1B工艺,涂料利用率达到95%以上,生产成本更低,且可实现“三废”零排放,环保性能优良。
但粉末涂料的金属漆需要2C2B工艺,即金属面漆喷涂后需要在高温下固化方可进行罩光清漆的喷涂,罩光清漆喷涂后仍需要再次高温烘干,能耗更高,液体金属漆喷涂工艺则可以实现2C1B工艺,能耗相对较低。因此为满足车厢生产多颜色的需求,我们设计了液体涂料和粉末涂料共线生产工艺,充分利用这两种工艺的优点,采用粉末涂料生产素色漆车厢,采用液体涂料生产金属漆车厢,从而最大限度地实现节能降耗和绿色环保。
“自主创新”的生产实践
邢汶平女士:我们的自主创新主要分为原始创新、消化吸收创新和集成创新三类,而自主创新课题的来源分为两种,一种是满足现有生产线在实现新产品上线及省人省力自动化方面的需求而做的技术创新工作;另一种是围绕新工艺、新技术和新材料等应用方面所做的技术创新工作,如为满足水性免中涂新工艺的应用,需要根据该工艺特有的技术特点开发配套的工艺装备及方法,如我们开发的水性免中涂预烘干系统等。
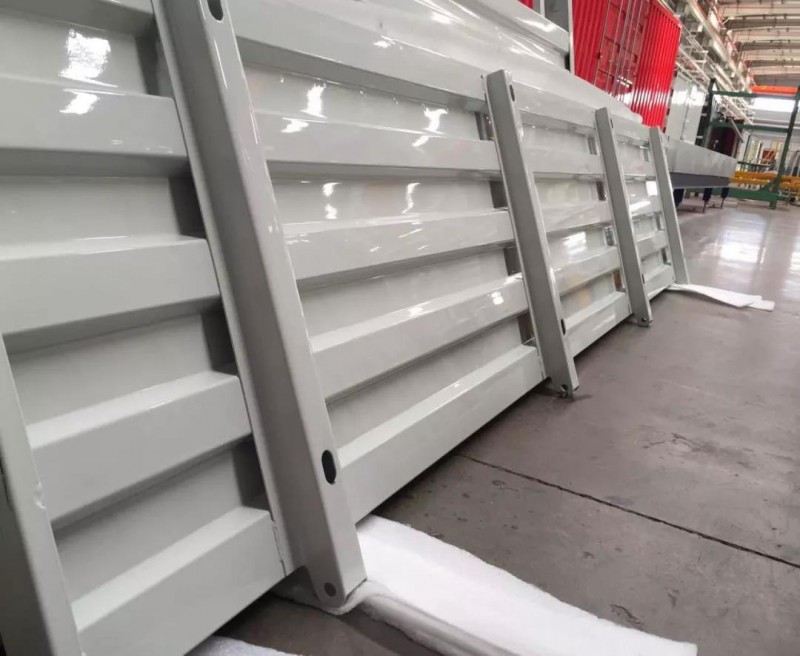
截至2017年,我们部门已获得20多项发明专利证书和100多项实用新型专利证书,上面提到的液体涂料与粉末涂料共线生产工艺就是工艺上实现集成创新的典型例子,另外,我部门还为M6新车型开发了一种裙边胶自动喷涂系统,该系统可实现车身自动识别、自动喷涂和自动完成遮蔽,同时还可实现残胶的回收利用,系统投资仅40万元,还有许许多多的专利覆盖涂装新工艺、新设备和新方法等各个方面的改进和创新,主要是围绕产品质量提升、减少人工、精益生产和投资等方面的优化和改进。
智能制造取得哪些成绩
邢汶平女士:智能制造方面,我们主要从生产线仿真分析、自动化(即用自动设备或机器人等取代人工)、柔性化、数字化和网络化方面开展工作。
在仿真分析方面,我们面向产品开发和工程开发两个方面开展工作。围绕产品开发,我们通过引入VPS电泳仿真分析软件,在产品处于数模阶段就完成了涂装质量方面的分析工作,确保产品涂装质量达标;围绕工程开发,我们通过三维设计软件实现生产线的三维设计,并开展产品3D模拟通过性分析及与厂房、公用管线的干涉检查。在自动化方面,如我们最新的新港基地涂装线,除必须由人工操作的工位(如打磨、目视检查、精修和车身内表面涂胶等工位),其他工位已全部实现自动化。
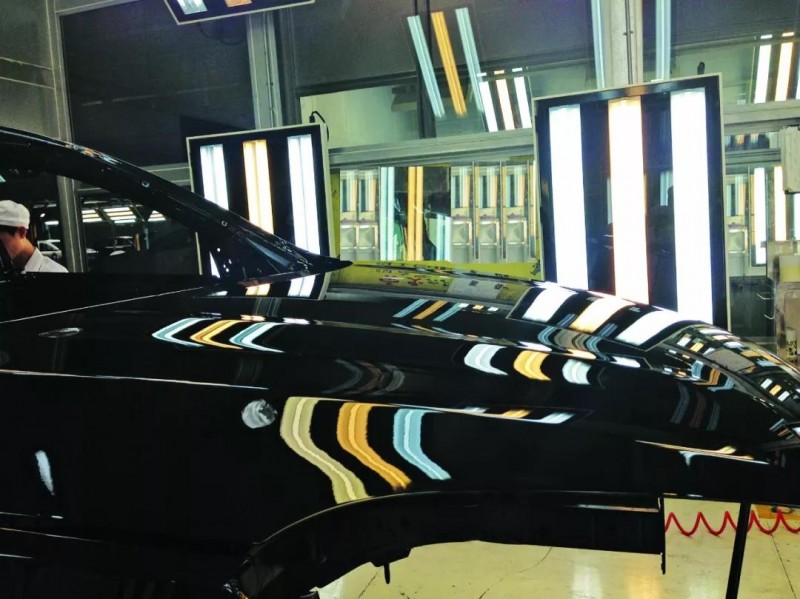
在柔性化方面,我们已实现了17种车型的混线生产,通过自动识别车型实现自动切换车型对应的橇体、调用对应的工艺参数及自动分流等功能,同时设置AVI系统实现车身的实时位置跟踪。
在数字化方面,生产线已基本实现设备运行数据、工艺参数数据、外观质量数据、能耗数据等采集、分析及报警。在网络化方面,我们也实施了全生产环节的FAS系统,即通过网络实现全生产环节的信息化和生产指令下发等,但尚不能实现订单化生产。
邢汶平眼中的工业4.0时代的汽车涂装车间?
工业4.0时代的汽车涂装车间
邢汶平
邢汶平女士:工业4.0时代的汽车涂装车间应该是涂装生产能耗更低,大气VOC、CO2和污水等排放量更小,智能化程度更高,同时在配有大量传感器和大数据基础上实现各类设备运行数据、工艺参数及质量数据的自动分析、自动纠偏的数字化,和可实现订单式生产、设备远程监控、远程诊断的网络化方面更加深入,最终实现客户个性化定制的柔性化生产。
最后,借用涂装界泰斗王锡春先生的一句话作为补充:“‘互联网+绿色涂装’是将汽车涂装行业做大做强的必经之路。它需从第三次工业革命的软件嵌入模式发展到以网络化、智能化为动力,是工业化和信息化的深度融合。”
未来发展计划和目标
在未来几年,邢汶平女士将带领涂装工艺部技术团队重点开展如下工作:
1)根据国家政策和公司规划,新能源汽车都将是后期发展的重心,而新能源汽车车身将会采用铝合金、塑料件及碳纤维等新型材料。涂装工艺部将紧跟这一趋势,围绕这些新材料的涂装技术开展研究。
2)涂装工艺作为汽车制造领域中的污染和能耗大户,涂装工艺部仍将会在满足和提升产品质量的情况下,对可以实现节能降耗、更加绿色环保的涂装新工艺、新材料、新技术和新设备等开展技术研究工作。
3)为实现“中国制造2025”的落地,涂装工艺部将会继续深化在智能化、数字化及网络化方面的研究,以一条生产线为试点,通过生产运行收集大量的数据形成大数据库,探索数字化工厂的建设。
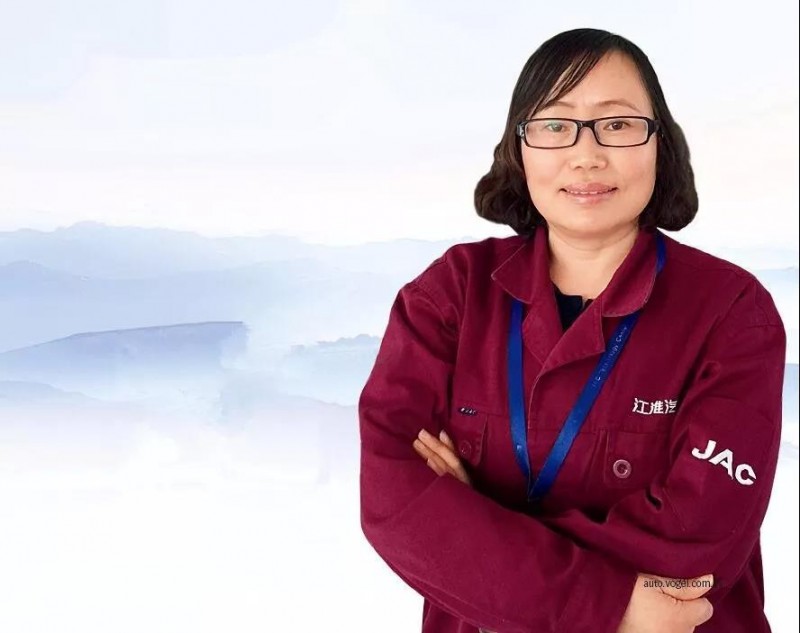
——江淮汽车技术中心工艺研究院涂装工艺部技术总监邢汶平女士
邢汶平女士担任安徽江淮汽车集团股份有限公司技术中心工艺研究院涂装工艺部技术总监一职,主要负责江淮汽车涂装生产线新建和改造项目的规划设计、建设和工艺调试工作及新产品的涂装工艺SE分析、生产线适应性改造、工艺调试和量产拉动等工作。
新技术、新设备
邢汶平女士:江淮汽车在涂装工艺方面按照安进董事长提出的“六化”要求,围绕技术领先化、制造精益化的理念,通过采用新工艺、新技术和新设备,打造“绿色环保、节能低碳”的世界先进涂装生产线。
在新工艺应用方面,江淮汽车具有敢为天下先的勇气,近几年不断引入新工艺、新技术。2012年,其率先在乘用车上采用当时国际先进的水性免中涂涂装工艺,在保证产品质量的同时,实现了能源消耗、VOC排放及生产成本的大幅下降,成为我国首条应用该技术的典范。2014年,江淮汽车采用的粉末涂料具有品质更加优良、废水/废气/废渣等零排放、涂料回收利用率高达95%以及生产成本更低等明显优势,被成功应用于商用车车厢涂装线,这也是国内首条车厢粉末生产线。
2015年,江淮汽车从欧洲引进了先进的水性单涂层工艺技术(工艺更加紧凑、VOC排放更低),用于江淮汽车遂宁工厂的素色漆生产,为国内商用车涂装线水性化改造建立了一个新的样板工厂。通过采用水性免中涂工艺取代原有3C2B溶剂型,采用水性单涂层工艺以及粉末涂料取代溶剂型单涂层技术等举措,江淮汽车实现了涂装技术在品质、绿色、精益等方面的不断升级。
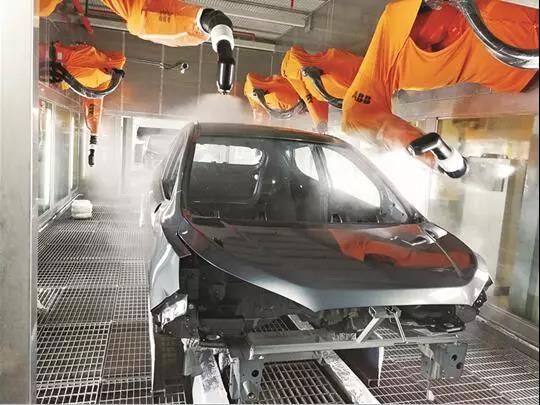
在涂装设备选型方面,江淮汽车以智能、低碳为原则,选用最先进、最节能且最环保的工艺装备。以江淮汽车新港生产基地为例,该项目车身内外表面均采用机器人喷涂,机器人数量达48台,实现了喷涂区域无人化,在保证产品一致性的同时,有效减少了人工并提高了涂料利用率。喷漆室采用最新的“空调循环风+热泵机组”节能技术,实现了单台涂装能耗下降15%。烘干系统采用TAR集中供热系统,在满足烘干加热需求的同时,实现了烘干废气焚烧达标,同时为最大程度地降低烘干能耗,设置了烟气余热回收装置,可实现年回收热量折合天然气26.2万立方米,减少碳年排放1 458.03 t。下地板涂胶采用“机器人+3D胶枪涂胶系统”,实现了地板涂胶和PVC全自动喷涂,确保地板优良防护性能,该项目建成后将是国内最先进的商用车生产线。
在环保措施方面,江淮汽车涂装线在全面采用水性涂料的同时,对于溶剂型清漆喷漆废气采用沸石转轮+RTO焚烧技术,将VOC排放量降至最低水平,可控制在 15 g/m2以下,满足国内最严格的排放限制要求,实现了真正意义上的绿色环保。
精益生产与技术先进性之间的平衡
邢汶平女士:精益生产体现在采用最合理的工艺方法和选用最适合的制造设备,而不一定是最先进的设备或技术。这需要通过对各类设备的技术特点及相关配套资源进行详细调研,在设备的投入费用、日常运行费用、废弃物处置费用以及设备维护保养费用等整个生命周期内进行系统分析,才能做出最佳选择。
我来举一个例子说明我们公司在这方面所做的工作。
设备方面,以喷漆室采用空调循环风技术为例,近几年国内外大多数汽车企业开始采用“干式喷漆室+循环风”技术实现喷涂系统的节能降耗,经过分析,我们发现该技术比较先进,也很节能,但设备投入及维护较高,且废漆渣处置费用也相对较高。
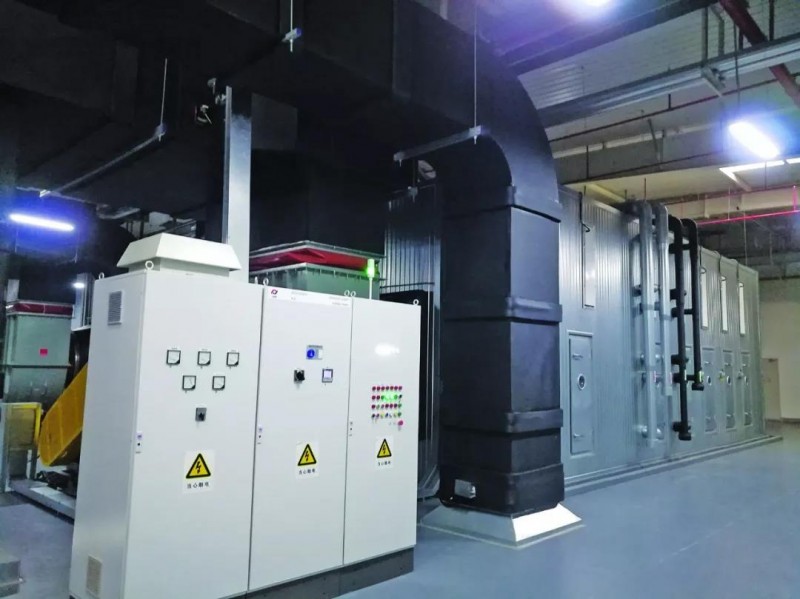
经过详细分析后,我们认为喷涂系统实现节能的根本在于采用了循环风技术,而不是取决于是否为干式喷漆室,同时文丘里形式的湿式喷漆室对喷漆漆雾的捕捉能力可以达到99%,优于目前使用的干式喷漆室,可以减轻循环风空调进口处过滤系统的压力。在漆渣处理方面,湿式喷漆室主要通过添加微量的漆雾凝聚剂进行漆渣处理,同时打捞出的漆渣经沥水干燥后,重量不会增加。
另外,湿式喷漆室技术比较成熟,已经应用了20年以上,设备已经完全国产化,同时设备运行较为稳定,基本没有设备维修费用。因此,我们最终选用了“湿式喷漆室+循环风空调+热泵”的组合方式,在同样实现节能降耗的同时,有效降低了前期的设备投入和后期的设备维护费用,经对半年的实际运行数据统计分析,可实现喷漆室区域能耗下降50%以上,整车能耗下降15%以上,这个例子仅供大家参考,适合的才是最好的。
节能环保方面的努力
邢汶平女士:我们围绕涂装生产如何实现节能降耗和绿色环保,采用具体项目具体分析的方法,根据我们的产品目标和生产线定位,设计和开发最为适合的生产工艺和涂装设备。
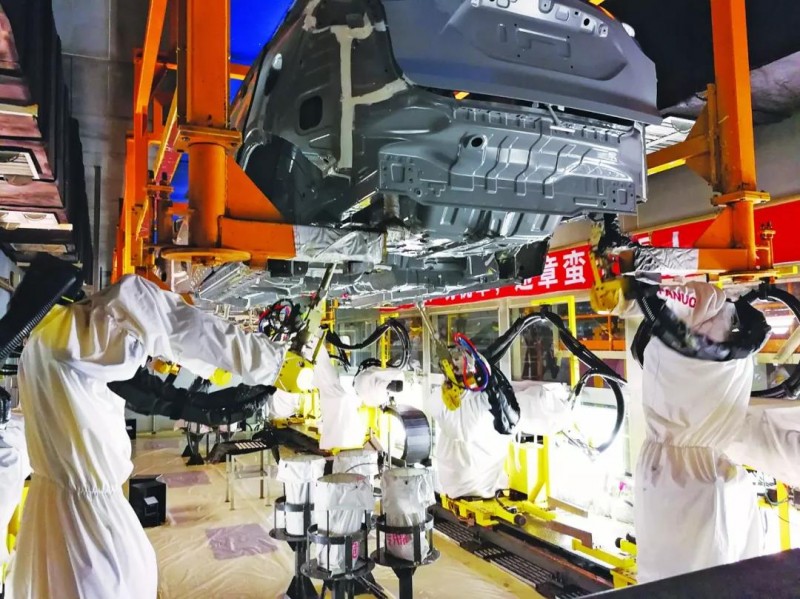
这里有一个典型例子可以说明,在我们公司大车厢涂装生产线设计过程中,经过对车厢产品特点和各类涂装工艺的优缺点进行详细分析,车厢产品需与车身的颜色相匹配,因此其颜色主要有白色、蓝色(素色漆)和蓝色、红色等金属漆为主,其中白色占比为50%以上。而粉末涂料素色漆喷涂可采用2C1B工艺,涂料利用率达到95%以上,生产成本更低,且可实现“三废”零排放,环保性能优良。
但粉末涂料的金属漆需要2C2B工艺,即金属面漆喷涂后需要在高温下固化方可进行罩光清漆的喷涂,罩光清漆喷涂后仍需要再次高温烘干,能耗更高,液体金属漆喷涂工艺则可以实现2C1B工艺,能耗相对较低。因此为满足车厢生产多颜色的需求,我们设计了液体涂料和粉末涂料共线生产工艺,充分利用这两种工艺的优点,采用粉末涂料生产素色漆车厢,采用液体涂料生产金属漆车厢,从而最大限度地实现节能降耗和绿色环保。
“自主创新”的生产实践
邢汶平女士:我们的自主创新主要分为原始创新、消化吸收创新和集成创新三类,而自主创新课题的来源分为两种,一种是满足现有生产线在实现新产品上线及省人省力自动化方面的需求而做的技术创新工作;另一种是围绕新工艺、新技术和新材料等应用方面所做的技术创新工作,如为满足水性免中涂新工艺的应用,需要根据该工艺特有的技术特点开发配套的工艺装备及方法,如我们开发的水性免中涂预烘干系统等。
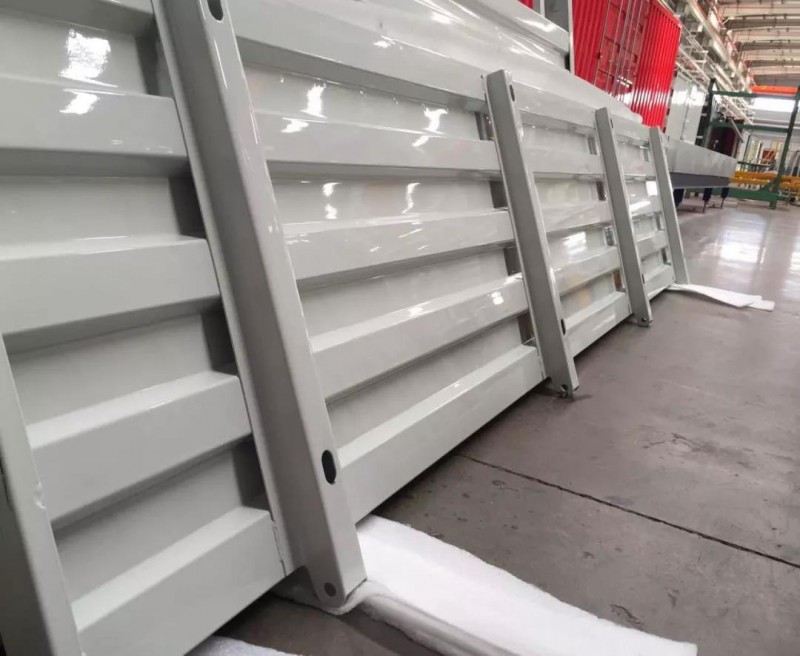
截至2017年,我们部门已获得20多项发明专利证书和100多项实用新型专利证书,上面提到的液体涂料与粉末涂料共线生产工艺就是工艺上实现集成创新的典型例子,另外,我部门还为M6新车型开发了一种裙边胶自动喷涂系统,该系统可实现车身自动识别、自动喷涂和自动完成遮蔽,同时还可实现残胶的回收利用,系统投资仅40万元,还有许许多多的专利覆盖涂装新工艺、新设备和新方法等各个方面的改进和创新,主要是围绕产品质量提升、减少人工、精益生产和投资等方面的优化和改进。
智能制造取得哪些成绩
邢汶平女士:智能制造方面,我们主要从生产线仿真分析、自动化(即用自动设备或机器人等取代人工)、柔性化、数字化和网络化方面开展工作。
在仿真分析方面,我们面向产品开发和工程开发两个方面开展工作。围绕产品开发,我们通过引入VPS电泳仿真分析软件,在产品处于数模阶段就完成了涂装质量方面的分析工作,确保产品涂装质量达标;围绕工程开发,我们通过三维设计软件实现生产线的三维设计,并开展产品3D模拟通过性分析及与厂房、公用管线的干涉检查。在自动化方面,如我们最新的新港基地涂装线,除必须由人工操作的工位(如打磨、目视检查、精修和车身内表面涂胶等工位),其他工位已全部实现自动化。
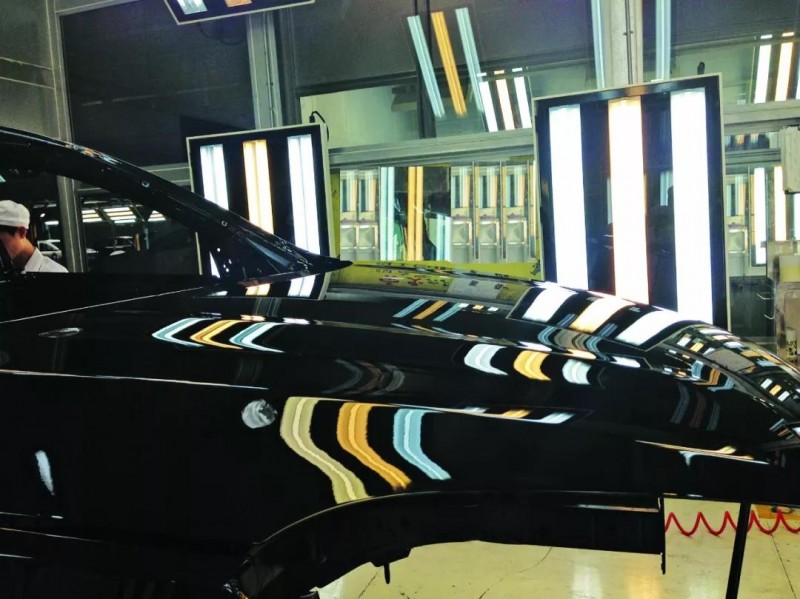
在柔性化方面,我们已实现了17种车型的混线生产,通过自动识别车型实现自动切换车型对应的橇体、调用对应的工艺参数及自动分流等功能,同时设置AVI系统实现车身的实时位置跟踪。
在数字化方面,生产线已基本实现设备运行数据、工艺参数数据、外观质量数据、能耗数据等采集、分析及报警。在网络化方面,我们也实施了全生产环节的FAS系统,即通过网络实现全生产环节的信息化和生产指令下发等,但尚不能实现订单化生产。
邢汶平眼中的工业4.0时代的汽车涂装车间?
工业4.0时代的汽车涂装车间
邢汶平
邢汶平女士:工业4.0时代的汽车涂装车间应该是涂装生产能耗更低,大气VOC、CO2和污水等排放量更小,智能化程度更高,同时在配有大量传感器和大数据基础上实现各类设备运行数据、工艺参数及质量数据的自动分析、自动纠偏的数字化,和可实现订单式生产、设备远程监控、远程诊断的网络化方面更加深入,最终实现客户个性化定制的柔性化生产。
最后,借用涂装界泰斗王锡春先生的一句话作为补充:“‘互联网+绿色涂装’是将汽车涂装行业做大做强的必经之路。它需从第三次工业革命的软件嵌入模式发展到以网络化、智能化为动力,是工业化和信息化的深度融合。”
未来发展计划和目标
在未来几年,邢汶平女士将带领涂装工艺部技术团队重点开展如下工作:
1)根据国家政策和公司规划,新能源汽车都将是后期发展的重心,而新能源汽车车身将会采用铝合金、塑料件及碳纤维等新型材料。涂装工艺部将紧跟这一趋势,围绕这些新材料的涂装技术开展研究。
2)涂装工艺作为汽车制造领域中的污染和能耗大户,涂装工艺部仍将会在满足和提升产品质量的情况下,对可以实现节能降耗、更加绿色环保的涂装新工艺、新材料、新技术和新设备等开展技术研究工作。
3)为实现“中国制造2025”的落地,涂装工艺部将会继续深化在智能化、数字化及网络化方面的研究,以一条生产线为试点,通过生产运行收集大量的数据形成大数据库,探索数字化工厂的建设。
- 下一篇:瓦尔特涡轮罩精密刀具
- 上一篇:工业的大门已为协作机器人敞开
编辑推荐
最新资讯
-
辐射亚太,链接全球——采埃孚再制造
2025-07-30 11:46
-
思看科技发布子品牌SCANOLOGY,全球
2025-07-30 11:06
-
风雨不动安如山——比亚迪叉车构筑“
2025-07-30 08:48
-
NEAS CHINA 新能源汽车技术与生态链
2025-07-29 09:52
-
三维扫描革新碾磨机辊套检测,效率与
2025-07-25 10:46