聚焦汽车轻量化技术全方位解析
2018-06-11 11:14:49· 来源:中汽创新创业中心
随着新能源汽车发展,动力电池技术不断飞跃,电动汽车续航持续提升,电池能量密度不断攀升,同时,补贴下降又对动力电池成本要求更加严格。随着后补贴时代能耗考核的不断加严,新能源车行业不应仅把眼光放在电池密度上,更该结合车身轻量化,将更多注意力放在减轻能耗方面,我们相信能耗将成为后补贴时代政策导向和整车企业最重视的关键指标。
随着新能源汽车发展,动力电池技术不断飞跃,电动汽车续航持续提升,电池能量密度不断攀升,同时,补贴下降又对动力电池成本要求更加严格。随着后补贴时代能耗考核的不断加严,新能源车行业不应仅把眼光放在电池密度上,更该结合车身轻量化,将更多注意力放在减轻能耗方面,我们相信能耗将成为后补贴时代政策导向和整车企业最重视的关键指标。本文将对汽车轻量化技术做个统揽:
汽车的轻量化的定义
就是在保证汽车的强度和安全性能的前提下,尽可能地降低汽车的整备质量。汽车轻量化有以下优点:
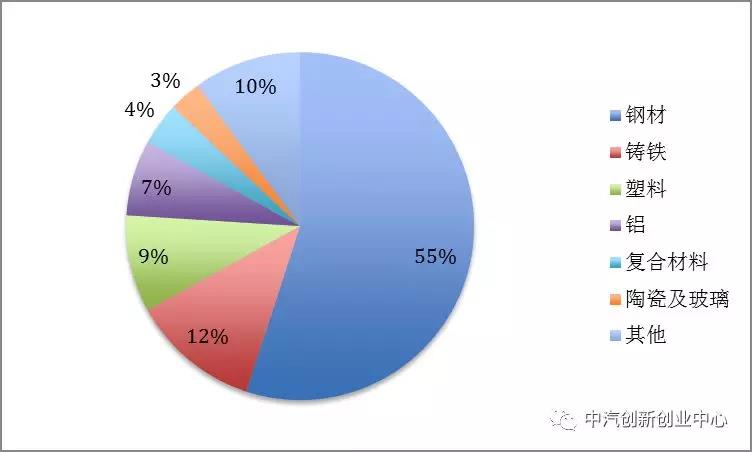
图:汽车材料使用占比
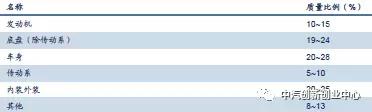
图:汽车各部件重量占比
汽车轻量化作为一个系统化的工程,并不是简单地针对某个零件的单独减重,局部重量的变化在很大程度上会影响汽车的其他部位,因此汽车轻量化是指在汽车制造过程中集设计、制造、材料技术等一起的系统性工程。在对汽车进行轻量化设计时,主要有以下三个途径:

一、材料轻量化
材料轻量化即通过使用轻量化材料来达到减轻新能源汽车质量的目的。目前,应用于新能源汽车的轻量化材料主要是有高强度钢、铝合金、镁合金、碳纤维等。例如,奇瑞新能源公司推出的新一代纯电动微型车小蚂蚁(代号eQ1)采用了“全铝空间结构+全复合材料外覆盖件”的组合形式,车身采用高强度镁铝合金应用比高达93%以上,全铝车身较传统汽车减重40%的同时车身刚性提高了60%以上;大众宝来通过更改材料减轻重量104.2kg,占总减重的41%。零件小型化后减轻重量144.1kg,占总减重的57%;
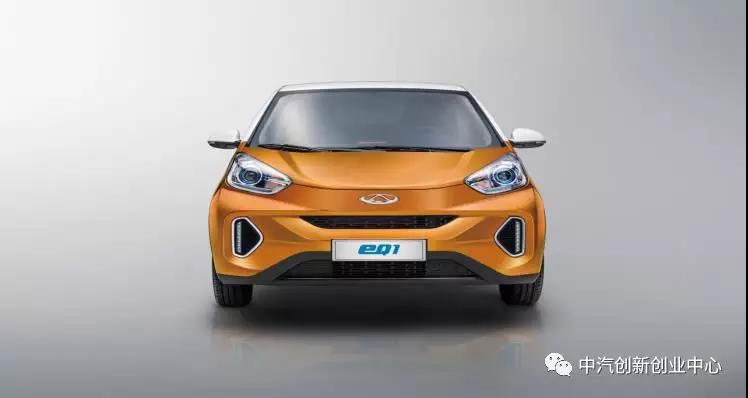
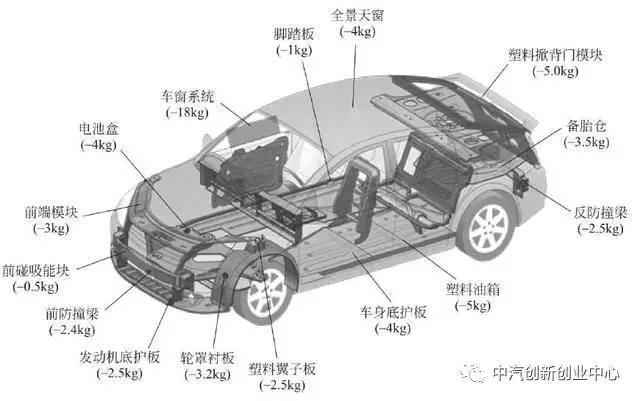
图:汽车外饰件采用轻量化材料减重途径

图:宝来汽车减重途径
二、结构轻量化
轻量化的另一手段就是在汽车零部件概念设计、初始结构设计、产品工程设计及样车制造过程中做相关结构的分析和优化,或去除零部件的冗余部分、或减少搭接(如花边形设计)、或改变结构,在不影响车身强度和安全性能的基础下尽量减少对零件的使用,有用则保留,无用则放弃,使车内布局达到最佳的效果,以实现对汽车零部件的精简化、整体化和轻质化。
结构轻量化包括车身结构优化设计和汽车实体结构布局设计这两种方式,主要运用ANSYS、UG、CAD、CATIA等软件,手段有形貌优化、尺寸优化、拓扑优化(包括多种轻量化材料的匹配、零部件的优化分块)、有限元分析和模块化集成设计等。
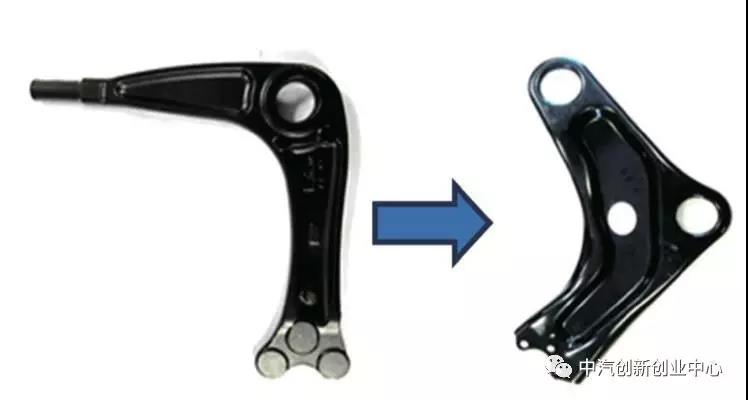
图:三角臂结构变更
例如神龙汽车公司将三角臂结构变更之后(三角臂是在汽车行驶于不平路面时起平衡支撑作用的结构件),质量减轻近50%,制造能耗降低65%。
三、制造工艺轻量化
为进一步达到减重降本的目的,除了开发应用轻量化材料外,一系列适应这些新材料的先进工艺,如热成型、激光焊接、液压成型、差厚轧制、径向锻造、半固态成型等应运而生。
例如,热成型技术是基于高强钢冷冲压成型中普遍存在塑性范围窄、易开裂、回弹大等问题而发展起来的板材成形新技术,通常在900~950°C的奥氏体状态下冲压,并在模具内淬火冷却,汽车上应用热成型技术的典型钢种是22MnB5,抗拉强度可达1500MPa。
激光拼焊是指将几个小零件通过激光焊接集成到一个大的毛坯,进而冲压成形成所需整体部件。使用激光拼焊板可使模具的数量和后续生产工序减少,从而降低了生产成本,并提高了零部件的质量、优化了零件结构,充分发挥了不同强度、不同厚度板材的特性,成为汽车轻化降低零件数量、保证汽车安全、优化设计和改进制造技术的重要手段。
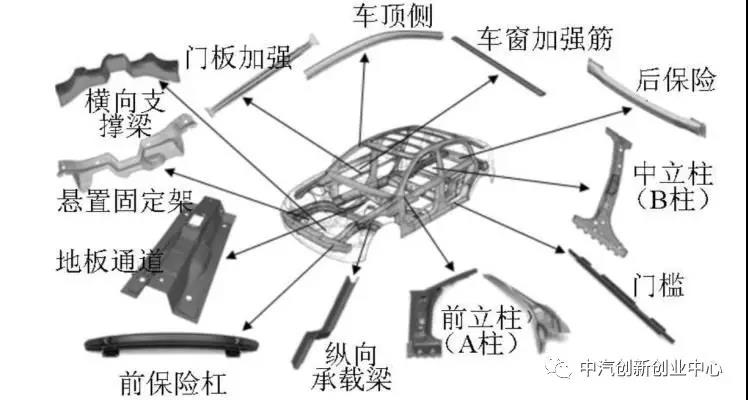
图:热成型在汽车零件上的典型应用
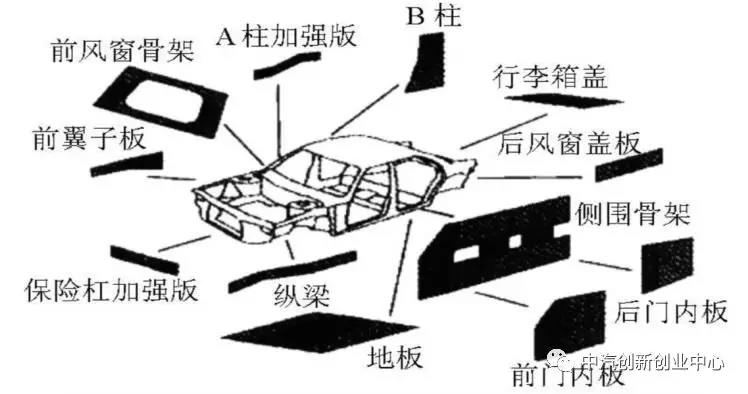
图:激光拼焊应用的典型零件
根据2017年新能源汽车目录列表中的汽车续航里程情况计算,乘用车平均续航里程为192km,新能源客车平均续航里程为238km,专用车为219km。考虑到测试数据一般要优于实际数据,所以我们认为新能源乘用车的平均续航能力要小于192km,与中央希望达到的250km以上的续航能力相差很远(根据补贴新政,中央将扶持250km以上乘用车,其中300km以上的将大力扶持)。对于那些续航能力在200km左右的车型来说,他们将寄希望于未来能够短时间内提升续航里程。那对于那些续航里程在200km左右的车型来说,用汽车轻量化的方法来达标是否可行呢?
答案是可行的。根据《论汽车轻量化》杂志报道,奇瑞汽车实车测试数据显示,电动汽车减重10%,平均续航能力增加5%-8%。对于那些续航能力在200km的汽车来说,在不改变汽车设计以及电池性能的条件下,将车体重量减少20%左右就可以达标。
综上所述,提升锂电池性能目前处于一个瓶颈期,锂电池性能在短时间内突破瓶颈可能性不大;增加锂电池数量也将增加汽车的重量以及成本,对于续航里程没有明显的提升;所以,最可行的、而且是最快速的方法就是汽车轻量化。
汽车轻量化材料市场前景广阔
本报告主要关注新能源汽车补贴新政落地后,对轻量化材料市场的影响。在接下来的篇幅中将重点讨论新材料在汽车轻量化的地位以及发展情况。
一、汽车轻量化材料之碳纤维
概述
碳纤维起源可以追溯到1860年,首先由英国人发明。由于其抗高温能力不如钨丝,所以无法成为电灯泡的发光材料,随后碳纤维的研究进入低谷。直到20世纪50年代,碳纤维的研究被美国人在导弹研究领域再一次推上舞台。碳纤维研究的里程碑发生在1959年,日本人近藤昭男发明了聚丙烯晴(PAN)基碳纤维。PAN碳纤维具有工艺成熟,性能良好和低成本等优势,在目前统计情况来看,PAN碳纤维占全部产量的90%以上。在今天的材料领域,如果不特指的话,碳纤维一般都是指PAN碳纤维。
碳纤维是有机纤维经过碳化和石墨化处理得到的微晶石墨材料,其微观结构类似人造石墨,是乱层石墨结构。其含碳量高于90%,如果含碳量高于99%则称为石墨纤维。碳纤维轴向强度和模量高,耐疲劳性好,比热和导电性质介于金属和非金属之间,热膨胀系数小,耐腐蚀,密度低。但是由于碳纤维耐冲击性较弱,容易发生氧化,所以一般需要进行表面处理。
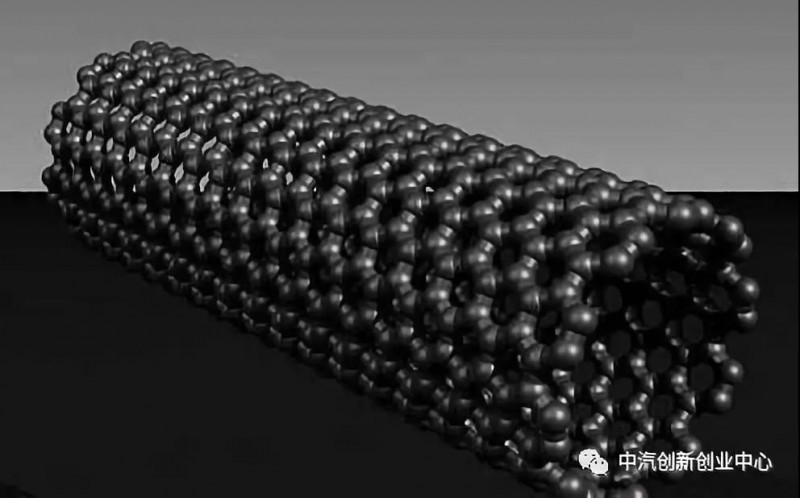
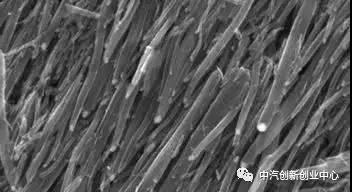
碳纤维的生产通常使用一些含碳的有机纤维(尼龙、腈纶、人造丝等)做原料,将有机纤维跟塑料树脂结合一起,在惰性气体环境中高压高热碳化而成。碳纤维可以通过高分子有机纤维碳化或者低分子烃类气相热解来制备。目前世界上生产销售的碳纤维大部分是用PAN纤维固相碳化而来。
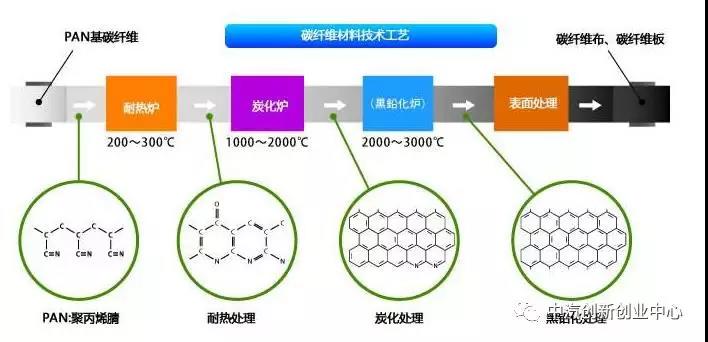
图:碳纤维生产方式
目前,碳纤维的主要生产国家有美国、日本等。日本是世界上碳纤维产能最大的国家,并且控制了高端碳纤维的生产。日本东丽公里在PAN碳纤维研制生产中充当急先锋,美国的Hexcel公司紧随其后。在小丝束碳纤维生产层面,除了东丽和Hexcel以外,日本东邦人造丝,日本三菱人造丝和美国Cytec公司都是在碳纤维生产制造上有一席之地,但是技术上还是与日本东丽有一定差距。在大丝束碳纤维生产层面,美国的Zoltek,Aldila,德国的SGLcarbon也有一定的话语权。总的来说,美国在大丝束碳纤维上有一定优势,日本则在小丝束上领先。
优缺点及应用
碳纤维具有多种优异的性质,具有密度小、强度高、热膨胀系数小、导热性好、耐腐蚀性好、耐磨性好等特性,使用碳纤维复合材料代替传统的汽车材料,有以下几个优点:
第一,碳纤维应用于汽车后,有利于实现汽车轻量化,提升汽车的节能、加速、制动性能。
第二,车身轻量化可以使整车的重心下移,提升了汽车操纵稳定性,车辆的运行将更加安全、稳定。碳纤维复合材料具有极佳的能量吸收率,碰撞吸能能力是钢的六到七倍、铝的三到四倍,碰撞时产生的碎片较少,进一步保证了汽车的安全性。
第三,碳纤维复合材料具有更高的震动阻尼,轻合金需要9秒才能停止震动,碳纤维复合材料2秒就能停止,故碳纤维应用在汽车上,对于整车NVH(噪声、振动与声振粗糙度)的提升贡献同样很大,会大幅增强汽车行驶的舒适性。
第四,碳纤维复合材料具有更高的疲劳强度,钢和铝的疲劳强度是抗拉强度的30-50%,而碳纤维复合材料可达70-80%,因此汽车上应用碳纤维复合材料对于材料疲劳可靠性有较大提升。

目前,碳纤维目前已经在高端车、超跑、赛车、改装车以及少量的电动车上开始大量。在汽车零部件中的应用,碳纤维主要分布在汽车车身、内外饰、底盘系统、动力系统等。

碳纤维在汽车车身、汽车轮毂、汽车刹车、传动系统以及汽车内饰、门窗等多个汽车组件上都有应用。
如宝马在多个系列的车型中使用了碳纤维,例如,在全新宝马7系的车体框架中,碳纤维被用于加固车顶横梁结构、B柱、C柱、底部侧围、中央通道和后部支撑,这些部件以往只能用高强度钢材打造,换成钢和碳纤维混合结构后重量直接减轻50%以上,而且强度是钢的5倍以上,最终7系比上一代减轻了130kg重量;宝马i3/i8Life模块由全碳纤维材质打造,该结构免去了中央通道对内部空间的占用,让乘客拥有更多空间,同时也抵消了高压蓄电池给车身带来的重量,还降低了汽车的重心;保时捷911Turbo采用碳纤维轮毂,比铝合金减重20%,强度提高了20%,且减轻簧下重量,让悬挂反应灵敏度增加、减少转动惯性以及缩短刹车距离。
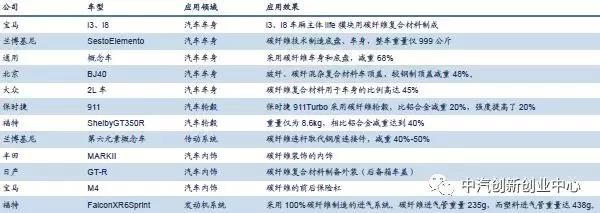
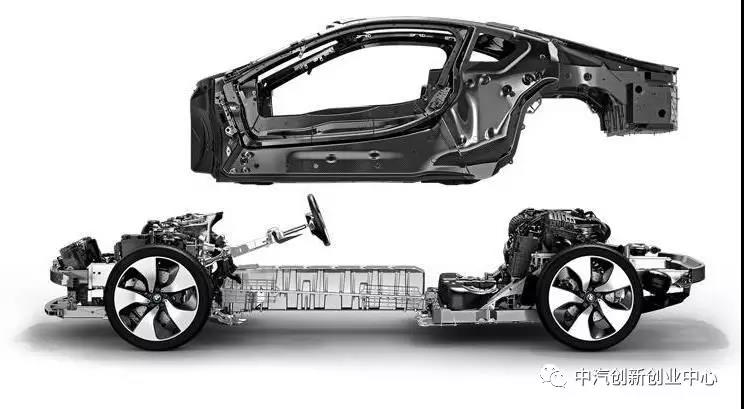
图:宝马i8碳纤维车身
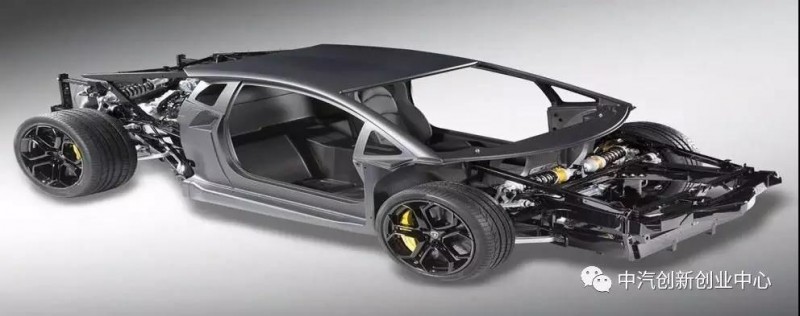
图:兰博基尼Aventador碳纤维车身
目前,碳纤维在民用领域的应用依然不多,主要集中应用在一些赛车和小批量高档轿车上,制约我国碳纤维及其复合材料业发展的问题在于碳纤维原丝质量差、价格高、应用基础研究薄弱等。
碳纤维是脆性材料,它的高强度只限于轴向,径向强度较低。如果受力过大,碳纤维会直接断裂。目前对于碳纤维材料在碰撞下的性能仍然了解不充分,损坏零部件的检测与维修技术还不成熟,因此损坏后基本无法修复。国产原丝不仅强度低,而且CV(强度离散系数)值大,很难生产出质量稳定的优质碳纤维。
另外,高昂的成本,使得碳纤维目前只能局限在部分超豪华车型上,难以普及。
例如,采用T300碳丝+环氧树脂代替SMC+ABS制造的某车型车身顶盖,质量由9.7kg减到5kg,但单件产品成本从三百多元翻了近五番;宝马i3电动车销量不佳部分原因是过度使用了碳纤维使得车辆太贵,一辆宝马i3价格大致为5.5万欧元;雷克萨斯推出的全碳纤维车身和底盘的LFA,售价高达30万-40万英镑。
因此,要促进碳纤维复合材料在汽车上的广泛应用,必须解决以下问题:
第一,降低碳纤维成本。每千克碳纤维耗费大概20美元,普通钢只1美元左右。随着生产工艺技术的重大突破,每千克碳纤维预计可以降到10美元左右,这将为碳纤维增强复合材料在汽车上的应用开辟广阔前景,碳纤维复合材料将大规模取代现用的工程材料。
第二,加强碳纤维及其复合材料的应用技术研究。主要包括碳纤维及其复合材料结构设计技术的研究、碳纤维及其复合材料成型工艺、性能表征和质量控制与保证、碳纤维及其复合材料相应标准的建立与完善、碳纤维复合材料的修补技术等。
二、汽车轻量化材料之玻璃纤维
概况
玻璃纤维(GFRP)是纤维状的玻璃,化学组成主要是二氧化硅(SiO2)、三氧化二硼(B2O3)、氧化钙(CaO)、三氧化二铝(Al2O3)等。玻璃纤维作为一种性能优异的无机非金属材料,是复合材料中使用量最大的一种增强材料,有着机械强度高、吸收冲击能亮大、耐热性强等优点,能提高基体材料机械强度、弹性模量等力学性能。
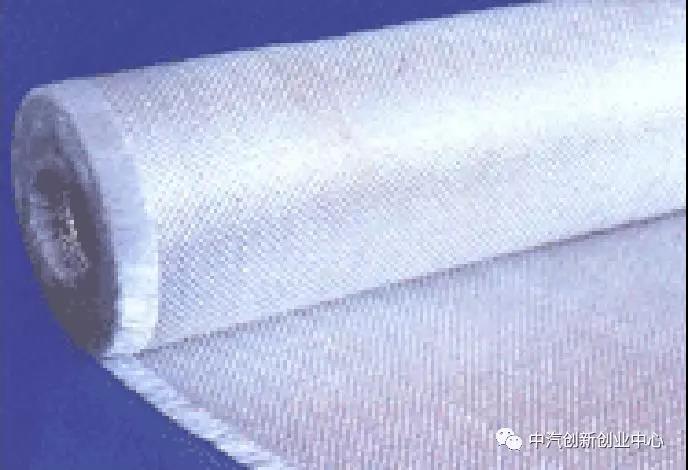
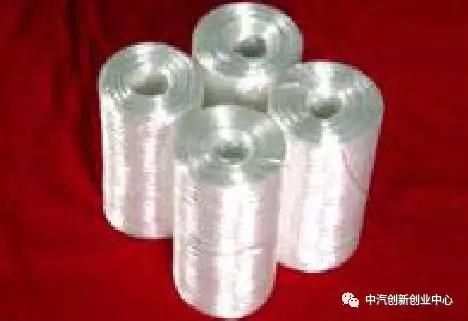
玻璃纤维分类方法很多,一般可以从成分,直径,纤维外观和纤维特性等方面分类。

玻璃纤维具有足够的刚性,耐冲击性能良好,能满足车身安全的基本要求;且具有足够的硬度及韧性,使得车身受到轻微碰撞时,能卸除部分冲击力,或产生回弹,对比铁质来说其安全系数更高;其抗刮能力强,耐腐蚀,抗老化能力表现也非常优秀。另外,玻璃纤维可塑性强,易成型;可后期拼接,也可与其他材质的部件拼接。
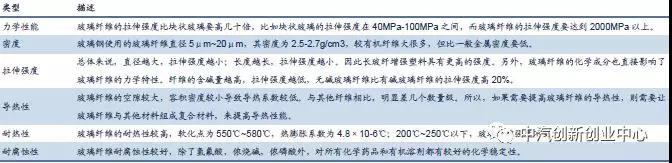
我国是一个玻璃纤维产业大国,2016年全球玻纤产量达到约625万吨,我国玻纤产量约为363万吨,占全球玻纤产量的58%,产量位居全球第一。但在生产技术、产品附加值、行业标准等方面,国内玻纤产业与国外存在较明显差距,尚未达到玻璃纤维强国的水平。

早在1955年,欧洲就开始在汽车上使用GFRP,曾在STM-Ⅲ型车上试用GFRP板。1970年,日本就用GFRP制造汽车车轮装饰罩。1971年日本铃木公司用GFRP制造发动机罩、翼子板、保险杠等。1974年英国厄夫公司试制成功了GFRP驾驶室。1979年美国克莱斯勒公司用GFRP制造轿车车身尾部零件。1980年美国通用公司用GFRP制造客货两用车车门,该公司用GFRP制造的驾驶室于1983年正式用于“将军”型载货车上。
此外,GFRP在国内的汽车企业中也得到了广泛的应用。北京251厂的BJ121GFRP驾驶室的成功研制,为GFRP在国内汽车应用上奠定了坚实基础,随后第一汽车制造厂成功研制GFRP发动机罩及平头可翻式驾驶室。受国产汽车工业的影响,较多应用在国内汽车工业是在80年代后期。1986年山东武城旅行车厂成功研制了BWC-6440全GFRP车身旅行车,该厂研制的BWC6470、BWC6480全GFRP车身旅行车1992年通过了3万公里可靠性定型试验和碰撞试验。2013年广东省中山大学研究院与东莞雅日玻璃钢有限公司成功研制了全GFRP车身电动巴士。
长玻纤增强材料
按照塑料粒子的长度和玻璃纤维的长度,有短玻纤增强塑料与长玻纤增强塑料之分。长玻纤一般指长度超过10mm的玻纤,与短玻纤相比,长玻纤纤维长度较长,力学性能更佳,且刚度和比强度高,抗冲击性能好,耐疲劳性能优良,特别适合汽车部件的应用;另外,长玻纤耐蠕变性能提高,尺寸稳定性好,部件成型精度高,成型过程中纤维可以在成型模具中相对移动,纤维损伤小。目前,LFT已在汽车防撞梁、前端模块、仪表盘骨架、车门中间承载板、电瓶箱、座椅骨架板、备胎仓以及车底部护板等结构件和半结构件中得到广泛应用。
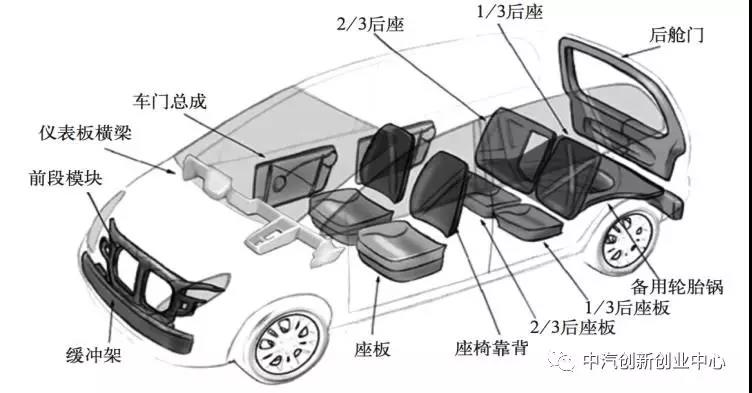
图:长玻纤增强材料在汽车零部件中的应用
玻璃纤维毡增强热塑性复合材料
玻璃纤维毡增强热塑性复合材料简称GMT,是目前国际上极为活跃的复合材料开发品种。这是一种以热塑性树脂为基体,以玻璃纤维毡为增强骨架的新颖、节能、轻质的复合材料,一般可以生产出片材半成品,然后直接加工成所需形状的产品,纤维可以是短切玻璃纤维或连续的玻璃纤维毡,热塑性树脂可以是通用塑料,工程塑料或高性能塑料。GMT产品具有很多优异的性能,如耐化学性好,强度/重量比大,在高、低温环境中的抗冲击性能优良。GMT工艺生产的轻质高强度的GMT片材,通过结构优化设计,可取代部分金属材料,获得显著的减重效果,而且节省模具费用,并有利于多种零件组合,形成模块化生产方式。用GMT片材可较原金属件减重30~80%,能耗仅为钢制品的60~80%,铝制品的35~50%。
GMT片材在汽车工业中的应用,已达40多种,主要有座椅骨架、保险杠、仪表板、发动机罩、电池托架、脚踏板、前端、地板、护板、后牵门、车顶棚、行李托架、遮阳板、备用轮胎架等部件。国内已经投产的AuidA6以及A4车已采用GMT材料,但尚未实现国产化。
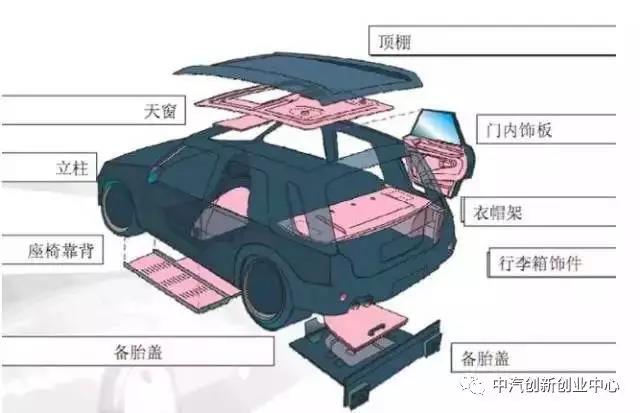
图:GMT片材在在汽车零部件中的应用
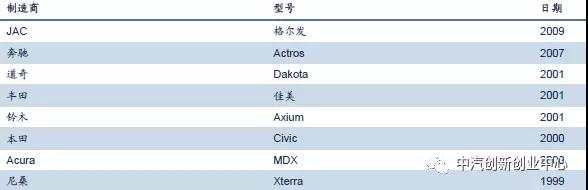
图:GMT片材内饰顶的应用举例
玻璃纤维增强复合材料具有优异的综合性能,是当今塑料复合材料最重要的发展趋势之一,在汽车上的应用前景很可观。玻璃纤维已开始在欧洲和美国的汽车制造业中广泛使用,但在国产汽车上还未得到广泛的应用。
未来,车用玻纤材料需要着力从以下几个方面进行改进:
第一,降低成本,扩大应用领域。价格是制约汽车车身新材料应用的重要因素,只有大幅度降低新材料的制造出成本,才可能使诸多新材料更容易被主机厂接受并加入批量生产。
第二,玻璃纤维具有很好的可设计性,但其与金属制件的连接在国内仍是制约其发展的瓶颈,未来需要着力提高玻纤与其他的材料的结合性。
第三,加快玻纤材料的开发和成型技术的研究,包括扩大增强纤维和基体的种类,开发先进的高效节能的成型技术和相应的回收技术,扩大器在汽车轻量化中的应用,推动中国汽车轻量化的进展。
三、汽车轻量化材料之镁合金
优缺点
镁合金是以镁为原料的高性能轻型结构材料,比重与塑料相近,刚度、强度不亚于铝,具有较强的抗震、防电磁、导热、导电等优异性能,并且可以全回收无污染。具体来说,镁合金在汽车生产中有以下几个优点:
第一,镁合金密度小但强度高、刚性好。在现有工程用金属中,镁的密度最小,是钢的1/5,锌的1/4,铝的2/3。普通铸造镁合金和铸造铝合金的刚度相同,因而其比强度明显高于铝合金。镁合金的刚度随厚度的增加而成立方比增加,故而镁合金制造刚性好的性能对整体构件的设计十分有利。
第二,镁合金的韧性好、减震性强。镁合金在受外力作用时,易产生较大的变形。但当受冲击载荷时,吸收的能量是铝的1.5倍,因此,很适合应于受冲击的零件—车轮;镁合金有很高的阻尼容量,是避免由于振动、噪音而引起工人疲劳等场合的理想材料。
第三,镁合金的热容量低、凝固速度快、压铸性能好。镁合金是良好的压铸材料,它具有很好的流动性和快速凝固率,能生产表面精细、棱角清晰的零件,并能防止过量收缩以保证尺寸公差。由于镁合金热容量低,与生产同样的铝合金铸件相比,其生产效率高40%~50%,且铸件尺寸稳定,精度高,表面光洁度好。
第四,镁合金具有优良的切削加工性。镁合金是所有常用金属中较容易加工的材料。加工时可采用较高的切削速度和廉价的切削刀具,工具消耗低。而且不需要磨削和抛光,用切削液就可以得到十分光洁的表面。
第五,镁合金的储量丰富,占地球地壳2.7%,开采寿命分别为铁和铝的20和4倍,我们国家占有世界70%的储量。另外我国白云石储备超过70亿吨,而白云石是制造镁合金的基础原材料。
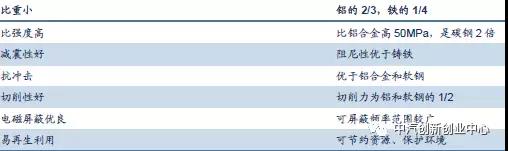
易燃烧和耐腐蚀性差是镁合金普及的“拦路虎”。
镁元素与氧元素具有极大的亲和力,其在高温下甚至还处于固态的情况下,就很容易与空气中的氧气发生反应,放出大量热,且生成的氧化镁导热性能不好,热量不能及时发散,继而促进了氧化反应的进一步进行,形成了恶性循环,而且氧化镁疏松多孔,不能有效阻隔空气中氧的侵入。镁合金加工过程中,容易发生燃烧和爆炸,存在安全生产问题,生产现场需要严格的管理来保证安全生产。
镁合金高温抗蠕变性和耐腐蚀性差等缺点也限制了其在汽车中的应用。大部分镁合金都是只有4个独立滑移系的六方结构,塑性变形能力差。镁合金的蠕变方式主要是位错滑移和晶界滑移,AZ91系镁合金高温蠕变能力弱是由于晶界处β相(Mg17Al12)的熔点很低,容易高温变形,无法稳定晶界,晶界滑动进而引起蠕变的产生。镁是活泼的化学元素,与其他金属接触时易发生电偶腐蚀现象,并充当阳极。室温下的镁在空气中形成致密系数仅为0.79的氧化镁薄膜,体积缩小,导致耐蚀性很差。
应用
国外镁合金在汽车上的应用十分广泛。在美国、西欧、日本等汽车工业发达国家,轻质镁合金已经广泛应用于汽车及零部件领域。在2007年,美国轿车95%的发动机缸盖和50%缸体已经采用铝铸件;欧洲的每车铝铸件,1990年已经为55kg/辆,2006年为98kg/辆。而密度比铝合金轻三分之一的镁合金铸件在轿车上的应用更呈现大幅上升的趋势。
美国通用汽车公司每车已经采用45个镁合金铸件,每车已达100kg以上;美国福特公司每车已经采用30个镁合金铸件,每车达到100kg;美国克莱斯勒每车已经采用20个镁合金铸件,每车已达40kg。“通用”计划镁合金用量最高每辆达到150kg/辆;“福特”最高每车118kg/辆;“大众”计划10年内每车最大达到178kg/辆。镁合金推广正向大型集成目标发展,美国三大汽车公司计划开发超大型镁合金集成件。近几年,丰田、菲亚特等也已经进入全力推广阶段。
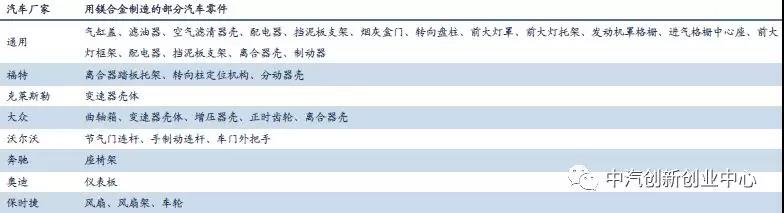
目前,我国镁合金的应用与国外有一定差距。20世纪末,随着轿车工业的兴起,汽车镁合金件才起步。2004年全年510万辆汽车使用镁合金1.8万t,2010年全国汽车达到1806万辆时,镁合金实用6.13万t。目前,我国单车镁合金用量仅在2-4kg左右,低于全球汽车平均每辆用镁合金4~5kg,更低于日本为9.3kg/辆的镁合金用量。国内为汽车行业提供镁合金件的供应商大约60家,生产概况如下表:
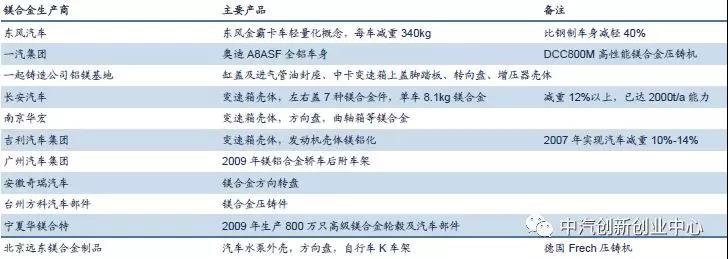
轿车上采用镁合金的部件有座椅上一些部件、膝垫、转向柱部件、转向盘、制动与离合器踏板托架、安全气囊限制装臵、踏板托架、轿车音响小的散热器框架、镜托架以及可开式车顶的一些部件;轿车发动机中的发动机机体、气缸盖、进气管、油泵壳体、辅助装臵的支架以及电器接线装臵;还有变速箱、离合器壳体、转向盘、柱、阀盖、阀板、车窗、马达壳体、油滤接头、进气歧管、镜罩、大灯保持架、制动防抱死系统的托架、车轮、油箱门。未来的发展中,在一些大型压铸件上,也将拓展它的应用,如车顶、发动机盖、后舱盖、内门板框架、仪表板等。其它的如需要安全及高断裂韧性的零部件,也将是镁合金拓展应用的领域,如座椅框架、转向柱、车身保护板、发动机前的散热器格栅加强板及一些车身结构支撑件。
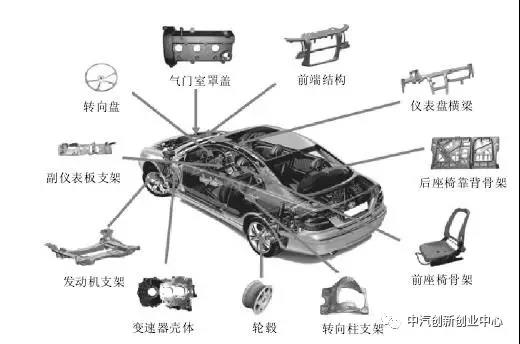
加速“镁代铝” 一直以来,高强度钢、铝合金等轻量化材料广泛应用于汽车及汽车零部件制造的各个方面,而镁合金鉴于种种原因没有得到大力推广和使用。

镁合金是最轻的金属结构材料,镁的密度只有1.74g/cm3,是铝的2/3,钢的1/5。采用镁合金能减轻整车重量,在车身、动力总成、底盘和内饰等4个部分进行材料替换,被镁和镁合金替代后的汽车部件减重比例达到20%~70%。
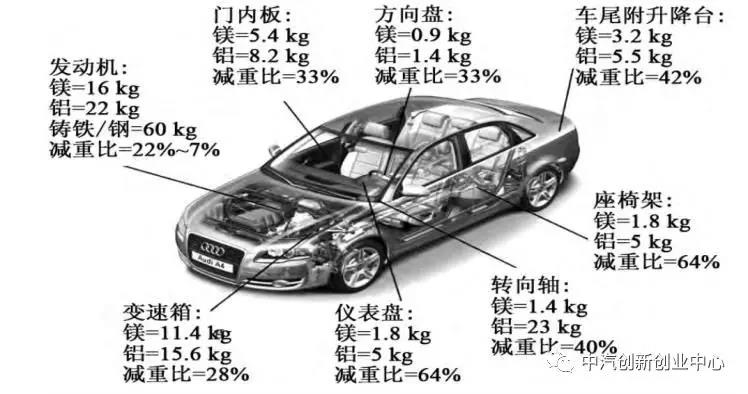
图:采用镁材料替换铝和钢后的汽车减重情况
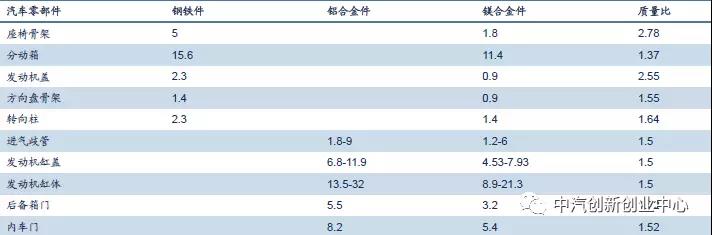
图:不同金属材料的汽车零部件质量对比
相较于铝合金,在成熟产品上镁合金将具备更高的性价比:2018年3月26日,根据长江有色市场平均价,镁的价格为16150元/吨,铝的价格为13670元/吨,虽然镁的价格比铝要高大约18%,但是考虑到镁合金比重较小(镁比重约为1.7kg/m3,铝比重约为2.7kg/m3),相同体积的镁合金成本较铝合金低约34%。
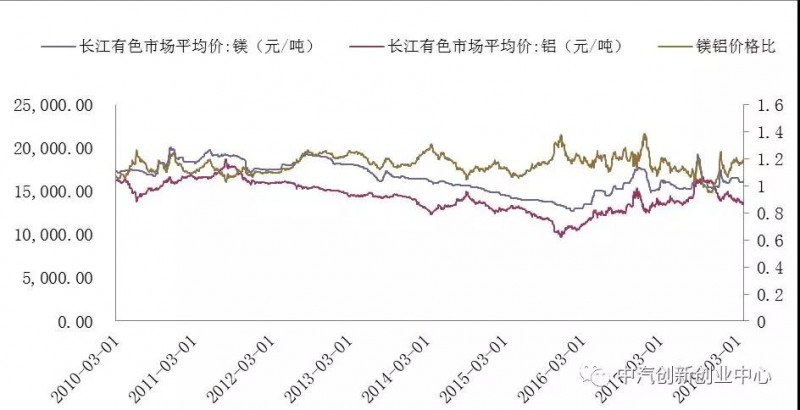
图:镁合金、铝合金价格对比
汽车用镁合金的技术不断突破,应用范围已经逐渐能够与铝合金相媲美,一方面随着充氧压铸、真空铸造和半固态压铸等工艺不断发展,高性能镁合金挤压加工技术、镁合金高效短流程成形技术等技术能有效提高镁合金耐腐蚀性,提高镁合金产品的性能及生产效率,降低生产成本;另一方面现有镁合金压铸件应用范围与铝合金的重合度日渐扩大,随着镁合金的压铸工艺进一步提升,镁合金替代铝合金产品将成为未来汽车轻量化的主要趋势。
四、汽车轻量化材料之树脂
优缺点
树脂基复合材料又称纤维增强塑料(FRO),是以合成树脂为基体,以纤维为增强材料的一种新型复合材料。树脂基体包括热固性树脂和热塑性树脂;增强纤维材料常用的有玻璃纤维、碳纤维、芳纶纤维、高密度聚乙烯纤维等。树脂基复合材料具有以下优点:
第一,质量轻,比强度高。树脂基复合材料的相对密度较小,一般介于1.5-2.0g/cm3之间,只有普通碳钢的1/4-1/5,但是比强度大,承载能力高。
第二,材料性能具有可设计性。树脂基复合材料的物理性能、化学性能、力学性能都可以通过合理选择原材料的种类、配比、加工方法、纤维含量和铺层方式进行设计,由于树脂基体材料的种类很多,故其选材设计的自由度很大。
第三,具有优良的耐腐蚀性。树脂具有优良的耐腐蚀性,有针对性的选择树脂来生产复合材料,可以使树脂基复合材料具有不同的耐腐蚀性能。
第四,减震性好。由于树脂基复合材料震动衰减系数大,受冲击时能够吸收大量的冲击能,当汽车发生碰撞时,可以避免或减少对乘客的伤害,有利于提高行车的安全性。
第五,工艺成型简单。树脂基复合材料可以用磨具一次成型制造各种构件,从而减少了零部件的数量及接头等紧固件,节省原材料和工时,有效降低了生产成本。在中等批量生产的车型中,用树脂基复合材料代替铝材可以降低成本40%左右。此外,树脂基复合材料对缺口、应力集中敏感性小,而且纤维和集体洁面能够阻止和改变裂纹扩展方向,因此具有较高的疲劳极限。

按树脂基体分类,可以将树脂基复合材料分为热固性树脂和热塑性树脂两种。热固性树脂初加热时软化,可塑造成型,但固化后再加热时将不再软化,也不溶于溶剂。常用的热固性树脂有酚醛树脂、环氧树脂、不饱和聚醋树脂和有机硅树脂等。热塑性树脂加热时会软化和熔融,可塑造成型,冷却后即成型并保持即得形状,这一过程具有重复性。应用较多的热塑性树脂是:尼龙、聚烯烃类、聚苯乙烯类、热塑性聚醋和聚碳酸醋等。
车用复合材料的树脂基体,目前仍以热固性树脂为主,但热固性复合材料的缺点是废弃物回收再利用困难。随着国际社会对环境保护的要求越来越高,热塑性树脂基复合材料越来越受到人们的关注。与热固性树脂基复合材料相比,热塑性树脂基复合材料有许多优点。例如断裂韧性高、成型过程中无化学反应,因此成型速度快,成型周期短;预浸料可以无限期存放,且对存放无特殊要求,易于回收再利用,不环境污染;能够实现快速、无污染、自动化生产。所以近年来汽车用热塑性复合材料的增长速度高于热固性复合材料。
应用
树脂基复合材料在汽车上用途广泛,可用于制造汽车外板、汽车结构件、发动机及发动机周边部件等。应用范围由内饰件、覆盖件向外装件、结构件和功能件发展。发动机及发动机周边部件以往通常使用金属材料制造,从1990年开始树脂基复合材料被大量应用于汽车发动机部件。美国通用汽车公司首先将它应用于3.3/3.SLV6轿车发动机气门罩壳上,用它代替金属罩壳。
传统的车身材料通常采用高强度薄钢板,为了减轻汽车自重,采用树脂基复合材料代替钢材,已成为车身结构发展的必然趋势。通用公司早在1953年就推出克尔维特(Corvette)牌全塑车身的轿车,除翼子板用尼龙注射成型外,所有壳体都是用玻璃纤维增强塑料(FRP)压铸模塑成型的。到1980年已有65%的美国轿车采用玻璃钢片状模塑料作前脸和散热器护栅板。目前树脂基复合材料已被广泛应用于车身结构件(如骨架、梁、柱等)、覆盖件(如前脸面罩、前翼子板、发动机罩、顶盖、车门、行李箱盖、后侧板等)以及保险杠、油箱等。
与钢铁材料、铝合金等传统材料相比,树脂基复合材料具有重量轻、比强度高、耐腐蚀、减振性能好、可设计性强、易于加工等优点。尽管树脂基复合材料的许多优点使其很好地适应了汽车工业的发展要求,但其存在的一些缺点也是现代汽车工业所不能容忍的,如:原材料成本较高、弹性模量较低、材料特性分散性大、生产周期较长、可回收性差等。目前,树脂基复合材料的加工方法仍不成熟,难以进行大规模商业化生产。作为汽车上重要的轻量化材料,树脂基复合材料越来越多地取代了传统的金属材料,其应用范围由汽车内装饰件、覆盖件向外装件、结构件方向发展,随着生产工艺的进步,树脂基复合材料在汽车工业中应用前景十分广阔。
市场容量测算
我们希望更加量化地测算出汽车轻量化的市场规模。由于汽车轻量化是一个系统性、复杂性的工程,所以我们只能推算出某种材料最大理论市场规模。具体方法如下:
1) 对比目前国内外车重的差距,计算出替代材料单个车辆的需求。
2) 从单车需求推导出整体需求。
3) 根据材料价格推算出市场规模。
国内外汽车轻量化的差距
汽车轻量化在发达国家已经推广了十几年了,目前全球最大的轻量化市场在北美,欧洲为第二大市场。中国在汽车轻量化方面才刚刚起步,但是发展势头比较迅猛。
由于目前国内政策并没有把汽车轻量化的减重目标做量化规定,所以我们把最发达的美国减重目标作为对标标的。美国轻量化的汽车的发展目标:2020年要在13年的基础上降重20%,2025年要降重30%。由此,我们假设未来中国汽车轻量化目标也在减重20%左右。
目前汽车车身主要材料还是以钢为原材料,车身重量大约在1100kg左右。在下文中我们将对碳纤维、玻纤、镁合金、树脂等材料做定量分析,来计算出理论市场规模。
各种材料市场规模测算
钢铁的密度是7.8;碳纤维密度是1.8;玻纤密度是2.6;镁合金密度是1.8;树脂密度是1.4-2.2左右(为了保守预计,我们取2.2为树脂密度)。
工信部苗圩部长接受采访时提出,2020年中国新能源车药占比达到10%。目前中国汽车产量在每年2600万辆左右,预计到2020年这个数字将达到3000万辆。保守起见,我们预计2020年新能源汽车生产数量为150万辆。
由于轻量化目标是减重20%,所以1100kg的车身减重的重量理论上为220kg。从中我们可以计算出替代物的替代规模,推导出理论市场规模。计算结果见下表。

图:2020年轻量化材料理论市场规模
根据中国产业信息网信息,目前碳纤维的价格在200元/kg;玻纤6元/kg;镁合金30元/kg;树脂10元/kg。如果在2020年新能源汽车规模能够达到150万辆,普通车规模能够达到3000万辆,则上述各材料对应市场规模如下:碳纤维:200亿/4000亿;玻纤:10亿/ 200亿;镁合金:30亿/约600亿;树脂:13亿/约260亿。目前我国在这些产业的产能和市场规模分别是:碳纤维:约5000吨/约10亿;玻纤:约400万吨/约240亿;镁合金:约50万吨/约150亿;树脂:约500万吨/约500亿。
从潜在市场规模对比现有市场规模来看,影响力从大到小排序分别为:碳纤维、镁合金、树脂、玻纤。
汽车的轻量化的定义
就是在保证汽车的强度和安全性能的前提下,尽可能地降低汽车的整备质量。汽车轻量化有以下优点:
- 轻量化可以通过减轻车辆的质量来减少新能源汽车的惯性,使汽车的运动状态更容易改变,进而提升汽车的加速性能、制动性能和操控性能,有利于应对危急情况。
- 根据轻量化技术领域的相关研究,重量的减轻可以增加续航里程。如纯电动汽车整车重量若降低10kg,续驶里程可增加2.5km。
- 在装备等条件一致的情况下,只改变质量,新能源汽车的能耗会随着质量的减轻而减少,可以在一定程度上达到节省电力、燃料等的结果。
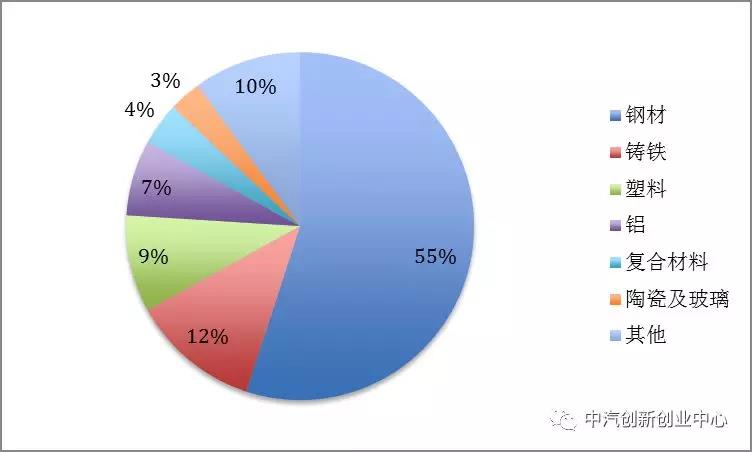
图:汽车材料使用占比
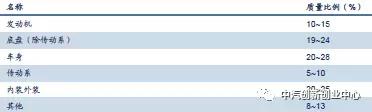
图:汽车各部件重量占比
汽车轻量化作为一个系统化的工程,并不是简单地针对某个零件的单独减重,局部重量的变化在很大程度上会影响汽车的其他部位,因此汽车轻量化是指在汽车制造过程中集设计、制造、材料技术等一起的系统性工程。在对汽车进行轻量化设计时,主要有以下三个途径:

一、材料轻量化
材料轻量化即通过使用轻量化材料来达到减轻新能源汽车质量的目的。目前,应用于新能源汽车的轻量化材料主要是有高强度钢、铝合金、镁合金、碳纤维等。例如,奇瑞新能源公司推出的新一代纯电动微型车小蚂蚁(代号eQ1)采用了“全铝空间结构+全复合材料外覆盖件”的组合形式,车身采用高强度镁铝合金应用比高达93%以上,全铝车身较传统汽车减重40%的同时车身刚性提高了60%以上;大众宝来通过更改材料减轻重量104.2kg,占总减重的41%。零件小型化后减轻重量144.1kg,占总减重的57%;
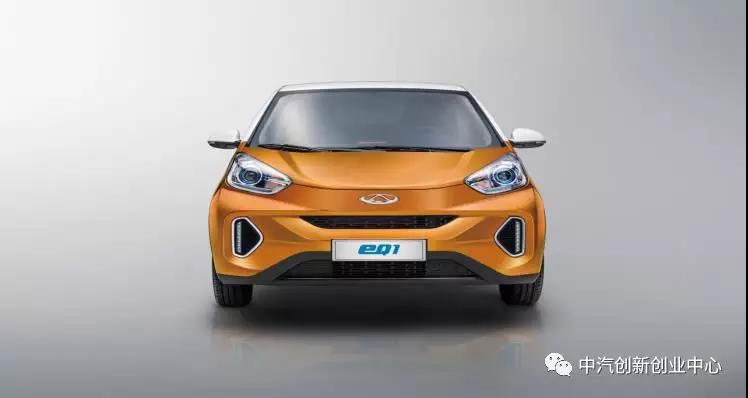
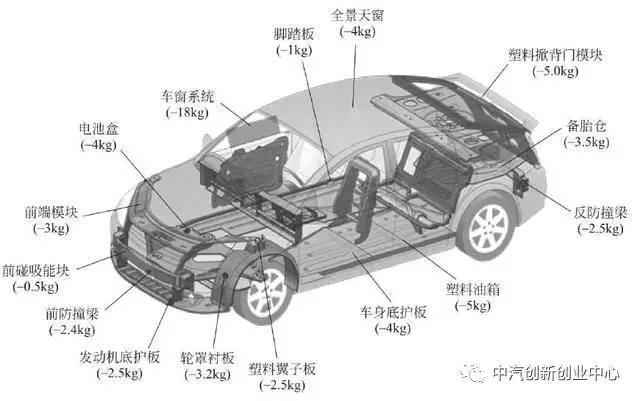
图:汽车外饰件采用轻量化材料减重途径

图:宝来汽车减重途径
二、结构轻量化
轻量化的另一手段就是在汽车零部件概念设计、初始结构设计、产品工程设计及样车制造过程中做相关结构的分析和优化,或去除零部件的冗余部分、或减少搭接(如花边形设计)、或改变结构,在不影响车身强度和安全性能的基础下尽量减少对零件的使用,有用则保留,无用则放弃,使车内布局达到最佳的效果,以实现对汽车零部件的精简化、整体化和轻质化。
结构轻量化包括车身结构优化设计和汽车实体结构布局设计这两种方式,主要运用ANSYS、UG、CAD、CATIA等软件,手段有形貌优化、尺寸优化、拓扑优化(包括多种轻量化材料的匹配、零部件的优化分块)、有限元分析和模块化集成设计等。
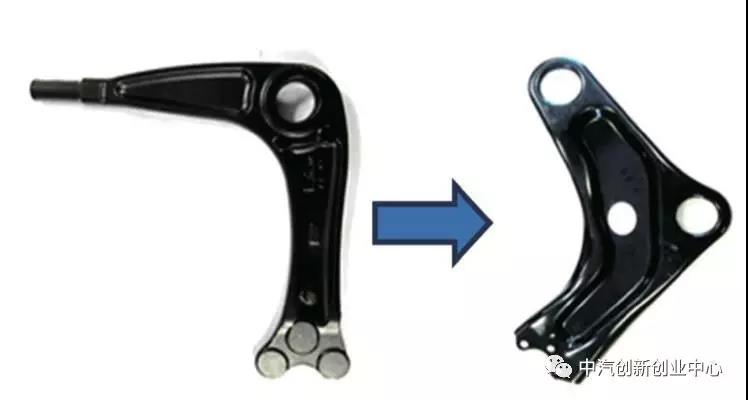
图:三角臂结构变更
例如神龙汽车公司将三角臂结构变更之后(三角臂是在汽车行驶于不平路面时起平衡支撑作用的结构件),质量减轻近50%,制造能耗降低65%。
三、制造工艺轻量化
为进一步达到减重降本的目的,除了开发应用轻量化材料外,一系列适应这些新材料的先进工艺,如热成型、激光焊接、液压成型、差厚轧制、径向锻造、半固态成型等应运而生。
例如,热成型技术是基于高强钢冷冲压成型中普遍存在塑性范围窄、易开裂、回弹大等问题而发展起来的板材成形新技术,通常在900~950°C的奥氏体状态下冲压,并在模具内淬火冷却,汽车上应用热成型技术的典型钢种是22MnB5,抗拉强度可达1500MPa。
激光拼焊是指将几个小零件通过激光焊接集成到一个大的毛坯,进而冲压成形成所需整体部件。使用激光拼焊板可使模具的数量和后续生产工序减少,从而降低了生产成本,并提高了零部件的质量、优化了零件结构,充分发挥了不同强度、不同厚度板材的特性,成为汽车轻化降低零件数量、保证汽车安全、优化设计和改进制造技术的重要手段。
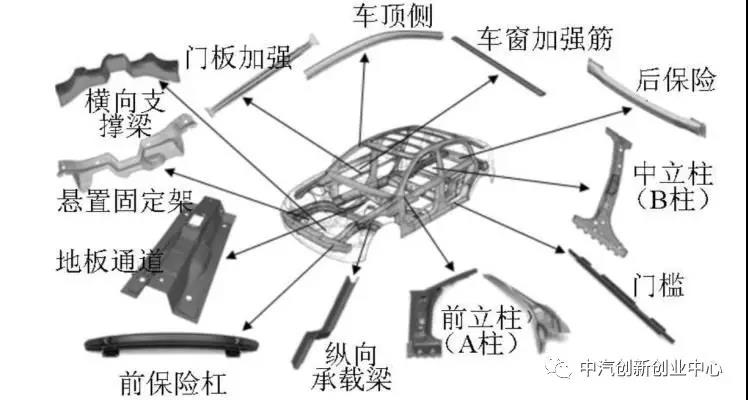
图:热成型在汽车零件上的典型应用
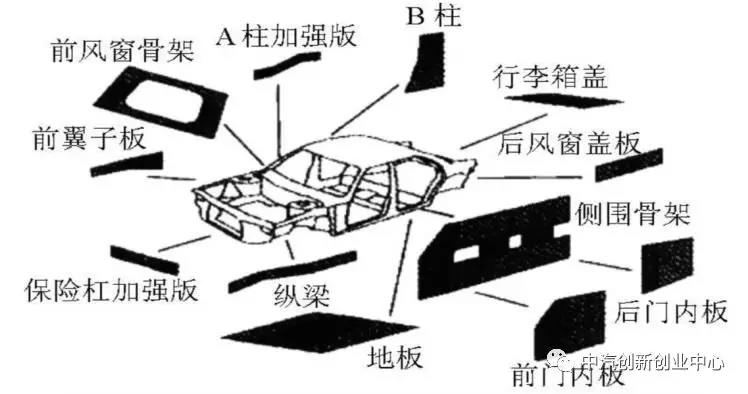
图:激光拼焊应用的典型零件
根据2017年新能源汽车目录列表中的汽车续航里程情况计算,乘用车平均续航里程为192km,新能源客车平均续航里程为238km,专用车为219km。考虑到测试数据一般要优于实际数据,所以我们认为新能源乘用车的平均续航能力要小于192km,与中央希望达到的250km以上的续航能力相差很远(根据补贴新政,中央将扶持250km以上乘用车,其中300km以上的将大力扶持)。对于那些续航能力在200km左右的车型来说,他们将寄希望于未来能够短时间内提升续航里程。那对于那些续航里程在200km左右的车型来说,用汽车轻量化的方法来达标是否可行呢?
答案是可行的。根据《论汽车轻量化》杂志报道,奇瑞汽车实车测试数据显示,电动汽车减重10%,平均续航能力增加5%-8%。对于那些续航能力在200km的汽车来说,在不改变汽车设计以及电池性能的条件下,将车体重量减少20%左右就可以达标。
综上所述,提升锂电池性能目前处于一个瓶颈期,锂电池性能在短时间内突破瓶颈可能性不大;增加锂电池数量也将增加汽车的重量以及成本,对于续航里程没有明显的提升;所以,最可行的、而且是最快速的方法就是汽车轻量化。
汽车轻量化材料市场前景广阔
本报告主要关注新能源汽车补贴新政落地后,对轻量化材料市场的影响。在接下来的篇幅中将重点讨论新材料在汽车轻量化的地位以及发展情况。
一、汽车轻量化材料之碳纤维
概述
碳纤维起源可以追溯到1860年,首先由英国人发明。由于其抗高温能力不如钨丝,所以无法成为电灯泡的发光材料,随后碳纤维的研究进入低谷。直到20世纪50年代,碳纤维的研究被美国人在导弹研究领域再一次推上舞台。碳纤维研究的里程碑发生在1959年,日本人近藤昭男发明了聚丙烯晴(PAN)基碳纤维。PAN碳纤维具有工艺成熟,性能良好和低成本等优势,在目前统计情况来看,PAN碳纤维占全部产量的90%以上。在今天的材料领域,如果不特指的话,碳纤维一般都是指PAN碳纤维。
碳纤维是有机纤维经过碳化和石墨化处理得到的微晶石墨材料,其微观结构类似人造石墨,是乱层石墨结构。其含碳量高于90%,如果含碳量高于99%则称为石墨纤维。碳纤维轴向强度和模量高,耐疲劳性好,比热和导电性质介于金属和非金属之间,热膨胀系数小,耐腐蚀,密度低。但是由于碳纤维耐冲击性较弱,容易发生氧化,所以一般需要进行表面处理。
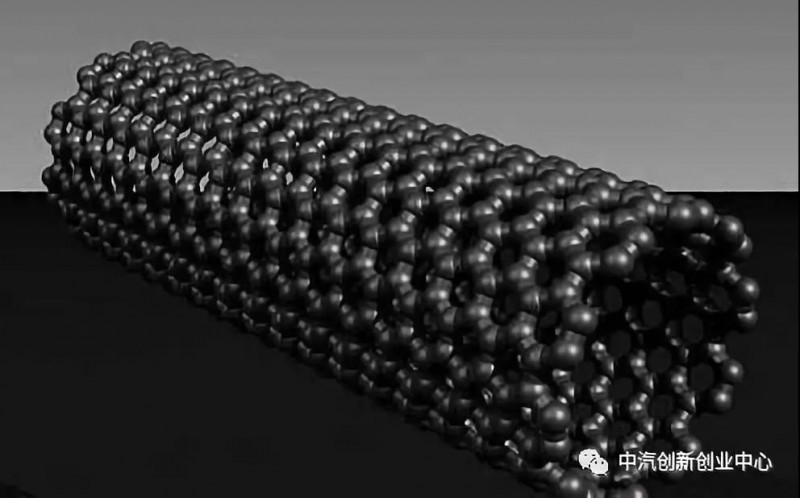
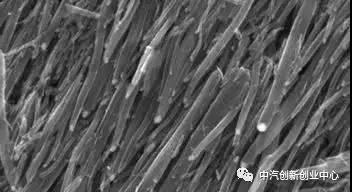
碳纤维的生产通常使用一些含碳的有机纤维(尼龙、腈纶、人造丝等)做原料,将有机纤维跟塑料树脂结合一起,在惰性气体环境中高压高热碳化而成。碳纤维可以通过高分子有机纤维碳化或者低分子烃类气相热解来制备。目前世界上生产销售的碳纤维大部分是用PAN纤维固相碳化而来。
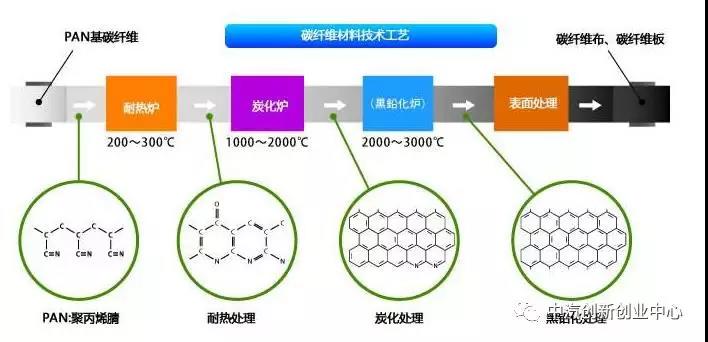
图:碳纤维生产方式
目前,碳纤维的主要生产国家有美国、日本等。日本是世界上碳纤维产能最大的国家,并且控制了高端碳纤维的生产。日本东丽公里在PAN碳纤维研制生产中充当急先锋,美国的Hexcel公司紧随其后。在小丝束碳纤维生产层面,除了东丽和Hexcel以外,日本东邦人造丝,日本三菱人造丝和美国Cytec公司都是在碳纤维生产制造上有一席之地,但是技术上还是与日本东丽有一定差距。在大丝束碳纤维生产层面,美国的Zoltek,Aldila,德国的SGLcarbon也有一定的话语权。总的来说,美国在大丝束碳纤维上有一定优势,日本则在小丝束上领先。
优缺点及应用
碳纤维具有多种优异的性质,具有密度小、强度高、热膨胀系数小、导热性好、耐腐蚀性好、耐磨性好等特性,使用碳纤维复合材料代替传统的汽车材料,有以下几个优点:
第一,碳纤维应用于汽车后,有利于实现汽车轻量化,提升汽车的节能、加速、制动性能。
第二,车身轻量化可以使整车的重心下移,提升了汽车操纵稳定性,车辆的运行将更加安全、稳定。碳纤维复合材料具有极佳的能量吸收率,碰撞吸能能力是钢的六到七倍、铝的三到四倍,碰撞时产生的碎片较少,进一步保证了汽车的安全性。
第三,碳纤维复合材料具有更高的震动阻尼,轻合金需要9秒才能停止震动,碳纤维复合材料2秒就能停止,故碳纤维应用在汽车上,对于整车NVH(噪声、振动与声振粗糙度)的提升贡献同样很大,会大幅增强汽车行驶的舒适性。
第四,碳纤维复合材料具有更高的疲劳强度,钢和铝的疲劳强度是抗拉强度的30-50%,而碳纤维复合材料可达70-80%,因此汽车上应用碳纤维复合材料对于材料疲劳可靠性有较大提升。

目前,碳纤维目前已经在高端车、超跑、赛车、改装车以及少量的电动车上开始大量。在汽车零部件中的应用,碳纤维主要分布在汽车车身、内外饰、底盘系统、动力系统等。

碳纤维在汽车车身、汽车轮毂、汽车刹车、传动系统以及汽车内饰、门窗等多个汽车组件上都有应用。
如宝马在多个系列的车型中使用了碳纤维,例如,在全新宝马7系的车体框架中,碳纤维被用于加固车顶横梁结构、B柱、C柱、底部侧围、中央通道和后部支撑,这些部件以往只能用高强度钢材打造,换成钢和碳纤维混合结构后重量直接减轻50%以上,而且强度是钢的5倍以上,最终7系比上一代减轻了130kg重量;宝马i3/i8Life模块由全碳纤维材质打造,该结构免去了中央通道对内部空间的占用,让乘客拥有更多空间,同时也抵消了高压蓄电池给车身带来的重量,还降低了汽车的重心;保时捷911Turbo采用碳纤维轮毂,比铝合金减重20%,强度提高了20%,且减轻簧下重量,让悬挂反应灵敏度增加、减少转动惯性以及缩短刹车距离。
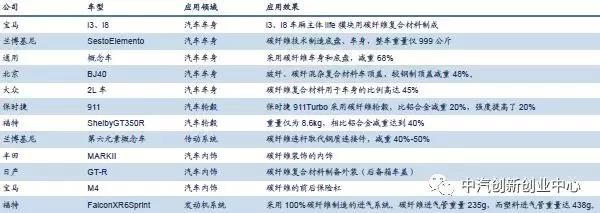
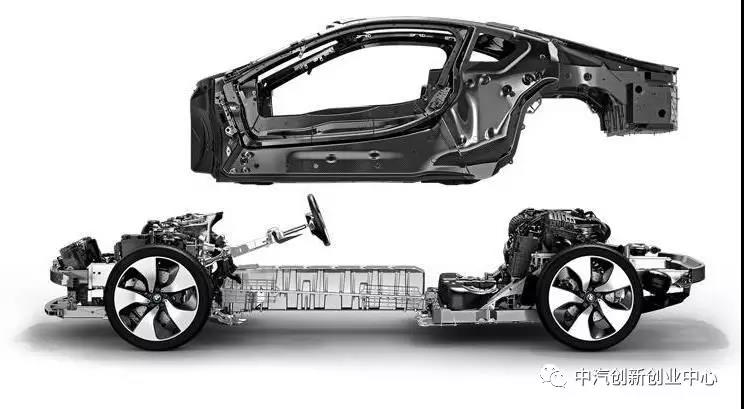
图:宝马i8碳纤维车身
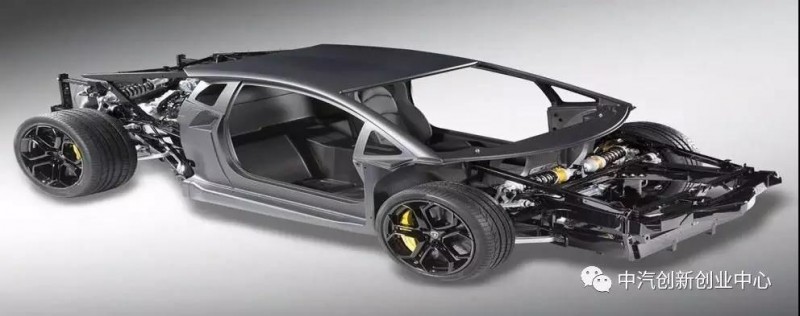
图:兰博基尼Aventador碳纤维车身
目前,碳纤维在民用领域的应用依然不多,主要集中应用在一些赛车和小批量高档轿车上,制约我国碳纤维及其复合材料业发展的问题在于碳纤维原丝质量差、价格高、应用基础研究薄弱等。
碳纤维是脆性材料,它的高强度只限于轴向,径向强度较低。如果受力过大,碳纤维会直接断裂。目前对于碳纤维材料在碰撞下的性能仍然了解不充分,损坏零部件的检测与维修技术还不成熟,因此损坏后基本无法修复。国产原丝不仅强度低,而且CV(强度离散系数)值大,很难生产出质量稳定的优质碳纤维。
另外,高昂的成本,使得碳纤维目前只能局限在部分超豪华车型上,难以普及。
例如,采用T300碳丝+环氧树脂代替SMC+ABS制造的某车型车身顶盖,质量由9.7kg减到5kg,但单件产品成本从三百多元翻了近五番;宝马i3电动车销量不佳部分原因是过度使用了碳纤维使得车辆太贵,一辆宝马i3价格大致为5.5万欧元;雷克萨斯推出的全碳纤维车身和底盘的LFA,售价高达30万-40万英镑。
因此,要促进碳纤维复合材料在汽车上的广泛应用,必须解决以下问题:
第一,降低碳纤维成本。每千克碳纤维耗费大概20美元,普通钢只1美元左右。随着生产工艺技术的重大突破,每千克碳纤维预计可以降到10美元左右,这将为碳纤维增强复合材料在汽车上的应用开辟广阔前景,碳纤维复合材料将大规模取代现用的工程材料。
第二,加强碳纤维及其复合材料的应用技术研究。主要包括碳纤维及其复合材料结构设计技术的研究、碳纤维及其复合材料成型工艺、性能表征和质量控制与保证、碳纤维及其复合材料相应标准的建立与完善、碳纤维复合材料的修补技术等。
二、汽车轻量化材料之玻璃纤维
概况
玻璃纤维(GFRP)是纤维状的玻璃,化学组成主要是二氧化硅(SiO2)、三氧化二硼(B2O3)、氧化钙(CaO)、三氧化二铝(Al2O3)等。玻璃纤维作为一种性能优异的无机非金属材料,是复合材料中使用量最大的一种增强材料,有着机械强度高、吸收冲击能亮大、耐热性强等优点,能提高基体材料机械强度、弹性模量等力学性能。
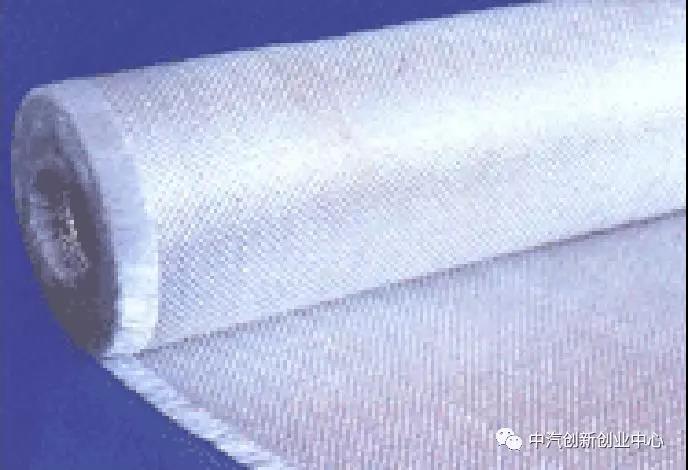
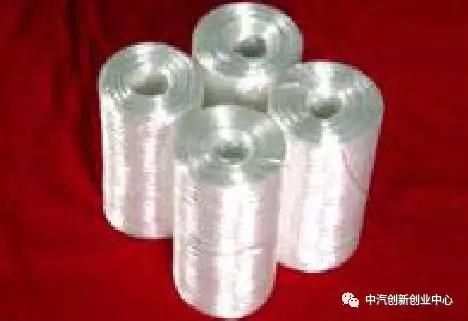
玻璃纤维分类方法很多,一般可以从成分,直径,纤维外观和纤维特性等方面分类。

玻璃纤维具有足够的刚性,耐冲击性能良好,能满足车身安全的基本要求;且具有足够的硬度及韧性,使得车身受到轻微碰撞时,能卸除部分冲击力,或产生回弹,对比铁质来说其安全系数更高;其抗刮能力强,耐腐蚀,抗老化能力表现也非常优秀。另外,玻璃纤维可塑性强,易成型;可后期拼接,也可与其他材质的部件拼接。
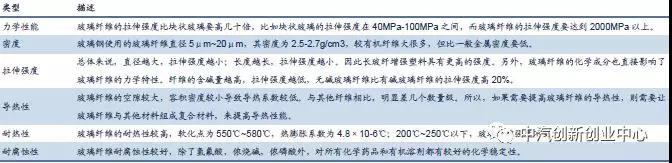
我国是一个玻璃纤维产业大国,2016年全球玻纤产量达到约625万吨,我国玻纤产量约为363万吨,占全球玻纤产量的58%,产量位居全球第一。但在生产技术、产品附加值、行业标准等方面,国内玻纤产业与国外存在较明显差距,尚未达到玻璃纤维强国的水平。

早在1955年,欧洲就开始在汽车上使用GFRP,曾在STM-Ⅲ型车上试用GFRP板。1970年,日本就用GFRP制造汽车车轮装饰罩。1971年日本铃木公司用GFRP制造发动机罩、翼子板、保险杠等。1974年英国厄夫公司试制成功了GFRP驾驶室。1979年美国克莱斯勒公司用GFRP制造轿车车身尾部零件。1980年美国通用公司用GFRP制造客货两用车车门,该公司用GFRP制造的驾驶室于1983年正式用于“将军”型载货车上。
此外,GFRP在国内的汽车企业中也得到了广泛的应用。北京251厂的BJ121GFRP驾驶室的成功研制,为GFRP在国内汽车应用上奠定了坚实基础,随后第一汽车制造厂成功研制GFRP发动机罩及平头可翻式驾驶室。受国产汽车工业的影响,较多应用在国内汽车工业是在80年代后期。1986年山东武城旅行车厂成功研制了BWC-6440全GFRP车身旅行车,该厂研制的BWC6470、BWC6480全GFRP车身旅行车1992年通过了3万公里可靠性定型试验和碰撞试验。2013年广东省中山大学研究院与东莞雅日玻璃钢有限公司成功研制了全GFRP车身电动巴士。
长玻纤增强材料
按照塑料粒子的长度和玻璃纤维的长度,有短玻纤增强塑料与长玻纤增强塑料之分。长玻纤一般指长度超过10mm的玻纤,与短玻纤相比,长玻纤纤维长度较长,力学性能更佳,且刚度和比强度高,抗冲击性能好,耐疲劳性能优良,特别适合汽车部件的应用;另外,长玻纤耐蠕变性能提高,尺寸稳定性好,部件成型精度高,成型过程中纤维可以在成型模具中相对移动,纤维损伤小。目前,LFT已在汽车防撞梁、前端模块、仪表盘骨架、车门中间承载板、电瓶箱、座椅骨架板、备胎仓以及车底部护板等结构件和半结构件中得到广泛应用。
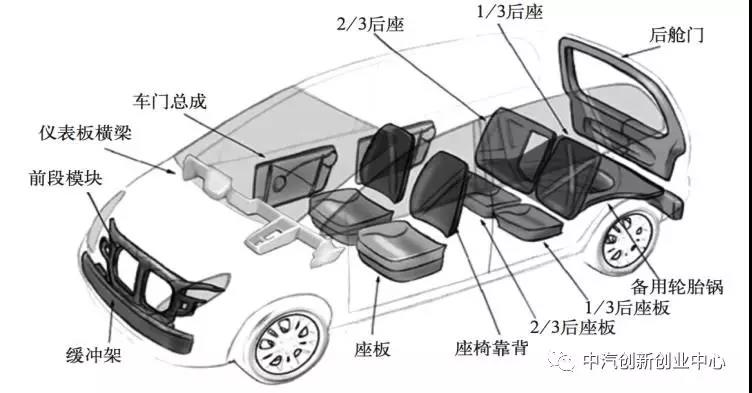
图:长玻纤增强材料在汽车零部件中的应用
玻璃纤维毡增强热塑性复合材料
玻璃纤维毡增强热塑性复合材料简称GMT,是目前国际上极为活跃的复合材料开发品种。这是一种以热塑性树脂为基体,以玻璃纤维毡为增强骨架的新颖、节能、轻质的复合材料,一般可以生产出片材半成品,然后直接加工成所需形状的产品,纤维可以是短切玻璃纤维或连续的玻璃纤维毡,热塑性树脂可以是通用塑料,工程塑料或高性能塑料。GMT产品具有很多优异的性能,如耐化学性好,强度/重量比大,在高、低温环境中的抗冲击性能优良。GMT工艺生产的轻质高强度的GMT片材,通过结构优化设计,可取代部分金属材料,获得显著的减重效果,而且节省模具费用,并有利于多种零件组合,形成模块化生产方式。用GMT片材可较原金属件减重30~80%,能耗仅为钢制品的60~80%,铝制品的35~50%。
GMT片材在汽车工业中的应用,已达40多种,主要有座椅骨架、保险杠、仪表板、发动机罩、电池托架、脚踏板、前端、地板、护板、后牵门、车顶棚、行李托架、遮阳板、备用轮胎架等部件。国内已经投产的AuidA6以及A4车已采用GMT材料,但尚未实现国产化。
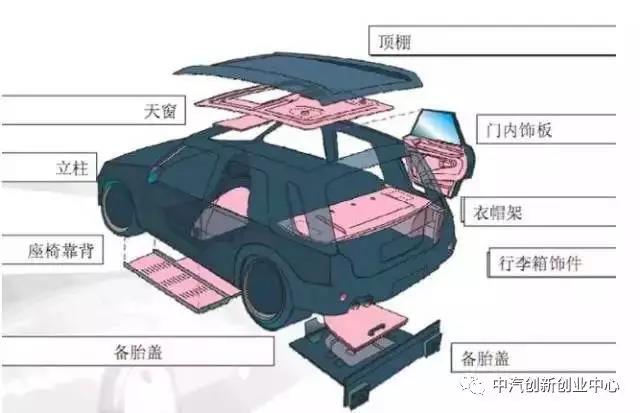
图:GMT片材在在汽车零部件中的应用
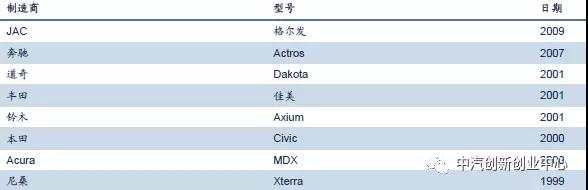
图:GMT片材内饰顶的应用举例
玻璃纤维增强复合材料具有优异的综合性能,是当今塑料复合材料最重要的发展趋势之一,在汽车上的应用前景很可观。玻璃纤维已开始在欧洲和美国的汽车制造业中广泛使用,但在国产汽车上还未得到广泛的应用。
未来,车用玻纤材料需要着力从以下几个方面进行改进:
第一,降低成本,扩大应用领域。价格是制约汽车车身新材料应用的重要因素,只有大幅度降低新材料的制造出成本,才可能使诸多新材料更容易被主机厂接受并加入批量生产。
第二,玻璃纤维具有很好的可设计性,但其与金属制件的连接在国内仍是制约其发展的瓶颈,未来需要着力提高玻纤与其他的材料的结合性。
第三,加快玻纤材料的开发和成型技术的研究,包括扩大增强纤维和基体的种类,开发先进的高效节能的成型技术和相应的回收技术,扩大器在汽车轻量化中的应用,推动中国汽车轻量化的进展。
三、汽车轻量化材料之镁合金
优缺点
镁合金是以镁为原料的高性能轻型结构材料,比重与塑料相近,刚度、强度不亚于铝,具有较强的抗震、防电磁、导热、导电等优异性能,并且可以全回收无污染。具体来说,镁合金在汽车生产中有以下几个优点:
第一,镁合金密度小但强度高、刚性好。在现有工程用金属中,镁的密度最小,是钢的1/5,锌的1/4,铝的2/3。普通铸造镁合金和铸造铝合金的刚度相同,因而其比强度明显高于铝合金。镁合金的刚度随厚度的增加而成立方比增加,故而镁合金制造刚性好的性能对整体构件的设计十分有利。
第二,镁合金的韧性好、减震性强。镁合金在受外力作用时,易产生较大的变形。但当受冲击载荷时,吸收的能量是铝的1.5倍,因此,很适合应于受冲击的零件—车轮;镁合金有很高的阻尼容量,是避免由于振动、噪音而引起工人疲劳等场合的理想材料。
第三,镁合金的热容量低、凝固速度快、压铸性能好。镁合金是良好的压铸材料,它具有很好的流动性和快速凝固率,能生产表面精细、棱角清晰的零件,并能防止过量收缩以保证尺寸公差。由于镁合金热容量低,与生产同样的铝合金铸件相比,其生产效率高40%~50%,且铸件尺寸稳定,精度高,表面光洁度好。
第四,镁合金具有优良的切削加工性。镁合金是所有常用金属中较容易加工的材料。加工时可采用较高的切削速度和廉价的切削刀具,工具消耗低。而且不需要磨削和抛光,用切削液就可以得到十分光洁的表面。
第五,镁合金的储量丰富,占地球地壳2.7%,开采寿命分别为铁和铝的20和4倍,我们国家占有世界70%的储量。另外我国白云石储备超过70亿吨,而白云石是制造镁合金的基础原材料。
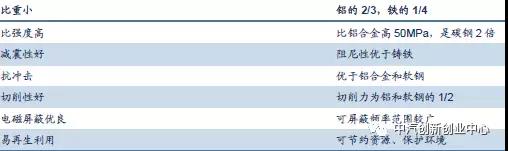
易燃烧和耐腐蚀性差是镁合金普及的“拦路虎”。
镁元素与氧元素具有极大的亲和力,其在高温下甚至还处于固态的情况下,就很容易与空气中的氧气发生反应,放出大量热,且生成的氧化镁导热性能不好,热量不能及时发散,继而促进了氧化反应的进一步进行,形成了恶性循环,而且氧化镁疏松多孔,不能有效阻隔空气中氧的侵入。镁合金加工过程中,容易发生燃烧和爆炸,存在安全生产问题,生产现场需要严格的管理来保证安全生产。
镁合金高温抗蠕变性和耐腐蚀性差等缺点也限制了其在汽车中的应用。大部分镁合金都是只有4个独立滑移系的六方结构,塑性变形能力差。镁合金的蠕变方式主要是位错滑移和晶界滑移,AZ91系镁合金高温蠕变能力弱是由于晶界处β相(Mg17Al12)的熔点很低,容易高温变形,无法稳定晶界,晶界滑动进而引起蠕变的产生。镁是活泼的化学元素,与其他金属接触时易发生电偶腐蚀现象,并充当阳极。室温下的镁在空气中形成致密系数仅为0.79的氧化镁薄膜,体积缩小,导致耐蚀性很差。
应用
国外镁合金在汽车上的应用十分广泛。在美国、西欧、日本等汽车工业发达国家,轻质镁合金已经广泛应用于汽车及零部件领域。在2007年,美国轿车95%的发动机缸盖和50%缸体已经采用铝铸件;欧洲的每车铝铸件,1990年已经为55kg/辆,2006年为98kg/辆。而密度比铝合金轻三分之一的镁合金铸件在轿车上的应用更呈现大幅上升的趋势。
美国通用汽车公司每车已经采用45个镁合金铸件,每车已达100kg以上;美国福特公司每车已经采用30个镁合金铸件,每车达到100kg;美国克莱斯勒每车已经采用20个镁合金铸件,每车已达40kg。“通用”计划镁合金用量最高每辆达到150kg/辆;“福特”最高每车118kg/辆;“大众”计划10年内每车最大达到178kg/辆。镁合金推广正向大型集成目标发展,美国三大汽车公司计划开发超大型镁合金集成件。近几年,丰田、菲亚特等也已经进入全力推广阶段。
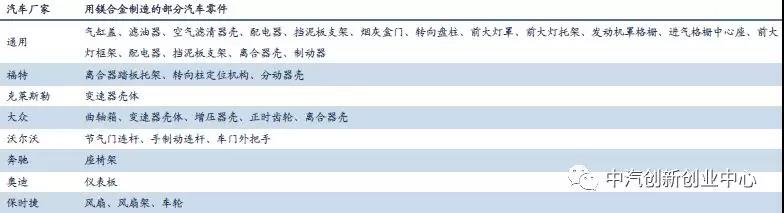
目前,我国镁合金的应用与国外有一定差距。20世纪末,随着轿车工业的兴起,汽车镁合金件才起步。2004年全年510万辆汽车使用镁合金1.8万t,2010年全国汽车达到1806万辆时,镁合金实用6.13万t。目前,我国单车镁合金用量仅在2-4kg左右,低于全球汽车平均每辆用镁合金4~5kg,更低于日本为9.3kg/辆的镁合金用量。国内为汽车行业提供镁合金件的供应商大约60家,生产概况如下表:
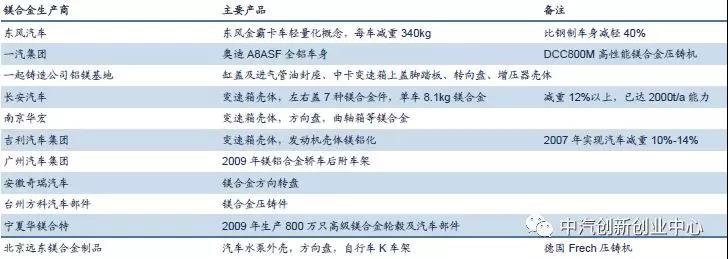
轿车上采用镁合金的部件有座椅上一些部件、膝垫、转向柱部件、转向盘、制动与离合器踏板托架、安全气囊限制装臵、踏板托架、轿车音响小的散热器框架、镜托架以及可开式车顶的一些部件;轿车发动机中的发动机机体、气缸盖、进气管、油泵壳体、辅助装臵的支架以及电器接线装臵;还有变速箱、离合器壳体、转向盘、柱、阀盖、阀板、车窗、马达壳体、油滤接头、进气歧管、镜罩、大灯保持架、制动防抱死系统的托架、车轮、油箱门。未来的发展中,在一些大型压铸件上,也将拓展它的应用,如车顶、发动机盖、后舱盖、内门板框架、仪表板等。其它的如需要安全及高断裂韧性的零部件,也将是镁合金拓展应用的领域,如座椅框架、转向柱、车身保护板、发动机前的散热器格栅加强板及一些车身结构支撑件。
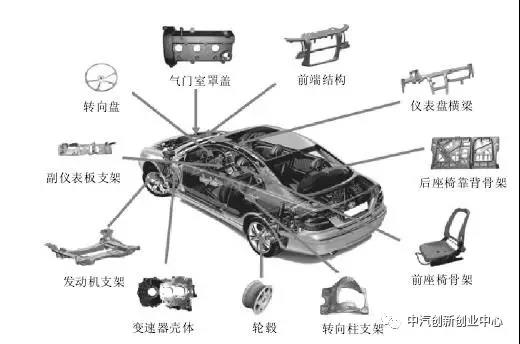
加速“镁代铝” 一直以来,高强度钢、铝合金等轻量化材料广泛应用于汽车及汽车零部件制造的各个方面,而镁合金鉴于种种原因没有得到大力推广和使用。

镁合金是最轻的金属结构材料,镁的密度只有1.74g/cm3,是铝的2/3,钢的1/5。采用镁合金能减轻整车重量,在车身、动力总成、底盘和内饰等4个部分进行材料替换,被镁和镁合金替代后的汽车部件减重比例达到20%~70%。
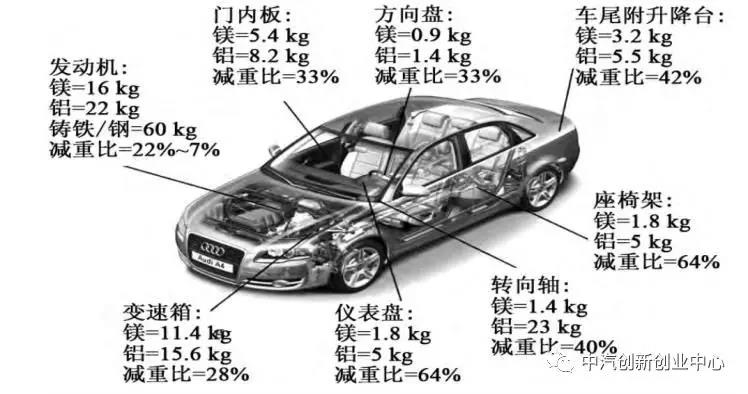
图:采用镁材料替换铝和钢后的汽车减重情况
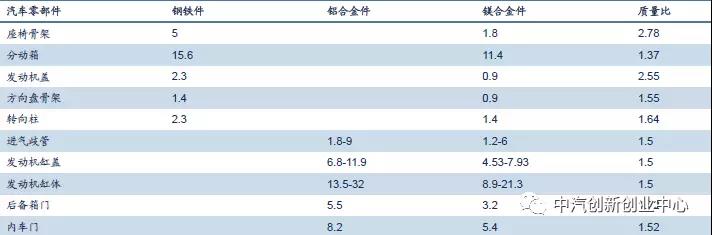
图:不同金属材料的汽车零部件质量对比
相较于铝合金,在成熟产品上镁合金将具备更高的性价比:2018年3月26日,根据长江有色市场平均价,镁的价格为16150元/吨,铝的价格为13670元/吨,虽然镁的价格比铝要高大约18%,但是考虑到镁合金比重较小(镁比重约为1.7kg/m3,铝比重约为2.7kg/m3),相同体积的镁合金成本较铝合金低约34%。
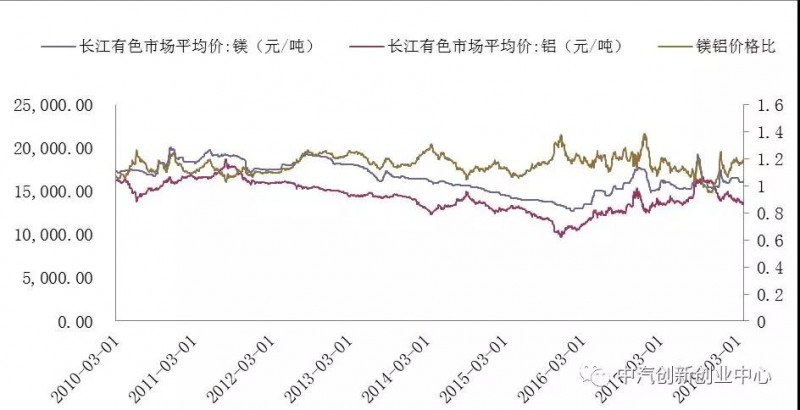
图:镁合金、铝合金价格对比
汽车用镁合金的技术不断突破,应用范围已经逐渐能够与铝合金相媲美,一方面随着充氧压铸、真空铸造和半固态压铸等工艺不断发展,高性能镁合金挤压加工技术、镁合金高效短流程成形技术等技术能有效提高镁合金耐腐蚀性,提高镁合金产品的性能及生产效率,降低生产成本;另一方面现有镁合金压铸件应用范围与铝合金的重合度日渐扩大,随着镁合金的压铸工艺进一步提升,镁合金替代铝合金产品将成为未来汽车轻量化的主要趋势。
四、汽车轻量化材料之树脂
优缺点
树脂基复合材料又称纤维增强塑料(FRO),是以合成树脂为基体,以纤维为增强材料的一种新型复合材料。树脂基体包括热固性树脂和热塑性树脂;增强纤维材料常用的有玻璃纤维、碳纤维、芳纶纤维、高密度聚乙烯纤维等。树脂基复合材料具有以下优点:
第一,质量轻,比强度高。树脂基复合材料的相对密度较小,一般介于1.5-2.0g/cm3之间,只有普通碳钢的1/4-1/5,但是比强度大,承载能力高。
第二,材料性能具有可设计性。树脂基复合材料的物理性能、化学性能、力学性能都可以通过合理选择原材料的种类、配比、加工方法、纤维含量和铺层方式进行设计,由于树脂基体材料的种类很多,故其选材设计的自由度很大。
第三,具有优良的耐腐蚀性。树脂具有优良的耐腐蚀性,有针对性的选择树脂来生产复合材料,可以使树脂基复合材料具有不同的耐腐蚀性能。
第四,减震性好。由于树脂基复合材料震动衰减系数大,受冲击时能够吸收大量的冲击能,当汽车发生碰撞时,可以避免或减少对乘客的伤害,有利于提高行车的安全性。
第五,工艺成型简单。树脂基复合材料可以用磨具一次成型制造各种构件,从而减少了零部件的数量及接头等紧固件,节省原材料和工时,有效降低了生产成本。在中等批量生产的车型中,用树脂基复合材料代替铝材可以降低成本40%左右。此外,树脂基复合材料对缺口、应力集中敏感性小,而且纤维和集体洁面能够阻止和改变裂纹扩展方向,因此具有较高的疲劳极限。

按树脂基体分类,可以将树脂基复合材料分为热固性树脂和热塑性树脂两种。热固性树脂初加热时软化,可塑造成型,但固化后再加热时将不再软化,也不溶于溶剂。常用的热固性树脂有酚醛树脂、环氧树脂、不饱和聚醋树脂和有机硅树脂等。热塑性树脂加热时会软化和熔融,可塑造成型,冷却后即成型并保持即得形状,这一过程具有重复性。应用较多的热塑性树脂是:尼龙、聚烯烃类、聚苯乙烯类、热塑性聚醋和聚碳酸醋等。
车用复合材料的树脂基体,目前仍以热固性树脂为主,但热固性复合材料的缺点是废弃物回收再利用困难。随着国际社会对环境保护的要求越来越高,热塑性树脂基复合材料越来越受到人们的关注。与热固性树脂基复合材料相比,热塑性树脂基复合材料有许多优点。例如断裂韧性高、成型过程中无化学反应,因此成型速度快,成型周期短;预浸料可以无限期存放,且对存放无特殊要求,易于回收再利用,不环境污染;能够实现快速、无污染、自动化生产。所以近年来汽车用热塑性复合材料的增长速度高于热固性复合材料。
应用
树脂基复合材料在汽车上用途广泛,可用于制造汽车外板、汽车结构件、发动机及发动机周边部件等。应用范围由内饰件、覆盖件向外装件、结构件和功能件发展。发动机及发动机周边部件以往通常使用金属材料制造,从1990年开始树脂基复合材料被大量应用于汽车发动机部件。美国通用汽车公司首先将它应用于3.3/3.SLV6轿车发动机气门罩壳上,用它代替金属罩壳。
传统的车身材料通常采用高强度薄钢板,为了减轻汽车自重,采用树脂基复合材料代替钢材,已成为车身结构发展的必然趋势。通用公司早在1953年就推出克尔维特(Corvette)牌全塑车身的轿车,除翼子板用尼龙注射成型外,所有壳体都是用玻璃纤维增强塑料(FRP)压铸模塑成型的。到1980年已有65%的美国轿车采用玻璃钢片状模塑料作前脸和散热器护栅板。目前树脂基复合材料已被广泛应用于车身结构件(如骨架、梁、柱等)、覆盖件(如前脸面罩、前翼子板、发动机罩、顶盖、车门、行李箱盖、后侧板等)以及保险杠、油箱等。
与钢铁材料、铝合金等传统材料相比,树脂基复合材料具有重量轻、比强度高、耐腐蚀、减振性能好、可设计性强、易于加工等优点。尽管树脂基复合材料的许多优点使其很好地适应了汽车工业的发展要求,但其存在的一些缺点也是现代汽车工业所不能容忍的,如:原材料成本较高、弹性模量较低、材料特性分散性大、生产周期较长、可回收性差等。目前,树脂基复合材料的加工方法仍不成熟,难以进行大规模商业化生产。作为汽车上重要的轻量化材料,树脂基复合材料越来越多地取代了传统的金属材料,其应用范围由汽车内装饰件、覆盖件向外装件、结构件方向发展,随着生产工艺的进步,树脂基复合材料在汽车工业中应用前景十分广阔。
市场容量测算
我们希望更加量化地测算出汽车轻量化的市场规模。由于汽车轻量化是一个系统性、复杂性的工程,所以我们只能推算出某种材料最大理论市场规模。具体方法如下:
1) 对比目前国内外车重的差距,计算出替代材料单个车辆的需求。
2) 从单车需求推导出整体需求。
3) 根据材料价格推算出市场规模。
国内外汽车轻量化的差距
汽车轻量化在发达国家已经推广了十几年了,目前全球最大的轻量化市场在北美,欧洲为第二大市场。中国在汽车轻量化方面才刚刚起步,但是发展势头比较迅猛。
由于目前国内政策并没有把汽车轻量化的减重目标做量化规定,所以我们把最发达的美国减重目标作为对标标的。美国轻量化的汽车的发展目标:2020年要在13年的基础上降重20%,2025年要降重30%。由此,我们假设未来中国汽车轻量化目标也在减重20%左右。
目前汽车车身主要材料还是以钢为原材料,车身重量大约在1100kg左右。在下文中我们将对碳纤维、玻纤、镁合金、树脂等材料做定量分析,来计算出理论市场规模。
各种材料市场规模测算
钢铁的密度是7.8;碳纤维密度是1.8;玻纤密度是2.6;镁合金密度是1.8;树脂密度是1.4-2.2左右(为了保守预计,我们取2.2为树脂密度)。
工信部苗圩部长接受采访时提出,2020年中国新能源车药占比达到10%。目前中国汽车产量在每年2600万辆左右,预计到2020年这个数字将达到3000万辆。保守起见,我们预计2020年新能源汽车生产数量为150万辆。
由于轻量化目标是减重20%,所以1100kg的车身减重的重量理论上为220kg。从中我们可以计算出替代物的替代规模,推导出理论市场规模。计算结果见下表。

图:2020年轻量化材料理论市场规模
根据中国产业信息网信息,目前碳纤维的价格在200元/kg;玻纤6元/kg;镁合金30元/kg;树脂10元/kg。如果在2020年新能源汽车规模能够达到150万辆,普通车规模能够达到3000万辆,则上述各材料对应市场规模如下:碳纤维:200亿/4000亿;玻纤:10亿/ 200亿;镁合金:30亿/约600亿;树脂:13亿/约260亿。目前我国在这些产业的产能和市场规模分别是:碳纤维:约5000吨/约10亿;玻纤:约400万吨/约240亿;镁合金:约50万吨/约150亿;树脂:约500万吨/约500亿。
从潜在市场规模对比现有市场规模来看,影响力从大到小排序分别为:碳纤维、镁合金、树脂、玻纤。
编辑推荐
最新资讯
-
辐射亚太,链接全球——采埃孚再制造
2025-07-30 11:46
-
思看科技发布子品牌SCANOLOGY,全球
2025-07-30 11:06
-
风雨不动安如山——比亚迪叉车构筑“
2025-07-30 08:48
-
NEAS CHINA 新能源汽车技术与生态链
2025-07-29 09:52
-
三维扫描革新碾磨机辊套检测,效率与
2025-07-25 10:46