碳纤维复合材料汽车前地板的研制
2018-05-28 13:45:29· 来源:CST汽车轻量化
阐述了通过对碳纤维复合材料汽车前地板的研制,以金属白车身为设计依据确定了碳纤维复合材料前地板的结构。分析确定了材料及成型工艺,研究了预成型体制作,设计出了多点注射快速RTM模具,并成功制备了碳纤维增强热固性环氧复合材料前地板。产品经过刚度及模态测试,其结果满足汽车整车厂提出的技术要求,而且减重效果明显,说明碳纤维复合材料作为主受力结构件在汽车上的应用是可行的。
摘要:阐述了通过对碳纤维复合材料汽车前地板的研制,以金属白车身为设计依据确定了碳纤维复合材料前地板的结构。分析确定了材料及成型工艺,研究了预成型体制作,设计出了多点注射快速RTM模具,并成功制备了碳纤维增强热固性环氧复合材料前地板。产品经过刚度及模态测试,其结果满足汽车整车厂提出的技术要求,而且减重效果明显,说明碳纤维复合材料作为主受力结构件在汽车上的应用是可行的。
关键词:复合材料;汽车前地板;RTM成型
1概 述
随着汽车轻量化不断发展,节能、环保、安全、舒适已成为当今材料界和汽车界的研究热点。研究显示,车重每减少100kg,每百公里油耗可降低0.3~0.5L,二氧化碳的排放可以减少12g左右。车重减轻,可以提高车辆的加速度和制动效果。传统汽车钢铁材料约占车体总重的3/4,用碳纤维增强复合材料(CFRP)制造的车身和底盘在等刚度、等强度下可以减重40%~60%,相当于钢结构的1/3~1/6。因此,CFRP正日益成为汽车轻量化的首选材料,逐渐得到汽车行业越来越广泛的认可和应用。
2015年国内碳纤维需求总量为1.3万吨左右,如果保持平稳增长态势,预计2020年将达到2.5万吨。目前,我国复合材料在汽车工业中年用量比例还很小,因此,开发碳纤维复合材料在汽车上的应用研究具有很大的发展空间和应用前景。本文以碳纤维复合材料汽车前地板的研制为例,对其结构方案设计、纤维预成型体制作、成型工艺及性能测试进行了研究。
2结构设计方案
2. 1 结构设计依据
目标产品以金属白车身为设计依据,原金属汽车前地板横截面呈“几”字形,外形尺寸为1.7m×1.3m,重量为27.7kg,金属板厚为0.8mm左右,由21个板金冲压件组装焊接而成,如图1所示。
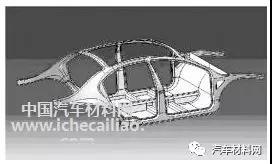
图 1 汽车白车身
2. 2 性能要求
减重:与金属钢制地板相比,减重不低于40%;
弯曲刚度:在1kN载荷下,中心点垂直挠度应小于2mm;
扭转刚度:≥104N·m2/rad;
一阶模态:≥20Hz。
2. 3 碳纤维复合材料地板设计过程
由于原金属汽车前地板零部件比较多,在复合材料成型中采用一体成型比较困难,为了充分发挥碳纤维复合材料性能及适应复合材料成型工艺特点,需要将原钢制地板结构进行局部的设计修改,修改内容主要有如下几个方面:
(1)取消加强筋板及多余的复杂筋条:充分发挥碳纤维复合材料的比强度、比模量高和可设计性强等的优点,根据等刚度设计原则,在前地板不同受力部位设计不同厚度CFRP,尽量取消加强筋板及多余的复杂筋条;
(2)取消工艺漏液孔:碳纤维复合材料前地板不同于钢制地板,产品焊接组装完成后无需在涂装车间进行电泳工序,所以可以取消各工艺漏液孔;
(3)在碳纤维零部件设计时,对于影响铺设成型的小圆角要尽量避免,原则上内角R≥3mm,以利于在模具上铺设成型,个别特殊部位可以将内角设计成R≥2mm,但会降低量产效率,应尽量避免;
(4)在碳纤维零部件壁厚不同的部位,应逐渐过渡,以免在成型固化过程中,因固化收缩不同而产生较大变形。
根据以上设计原则,重新修改设计后的前地板数模如图2所示。根据预先的有限元模拟,为了能够达到与原金属汽车前地板相同的刚度值,复合材料汽车前地板主板厚度为2.5mm,中央通道部分厚度为3.0mm。
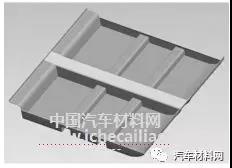
图 2 碳纤维复合材料前地板数模
3成型工艺及试制
3. 1 原材料
对于汽车前地板这种主受力结构件,一般需要首选快速成型的碳纤维复合材料。本项目设计选用性能较好的日本东丽碳纤维T700CS-12K织物,面密度分别为480g/m2和200g/m2;单轴向布为200g/m2。树脂体系选用快速固化的环氧树脂体系EpoTech167A/167B(广州博汇)。
3. 2 成型工艺
复合材料成本已成为制约复合材料规模化应用的瓶颈,以快速RTM成型技术为代表的低成本复合材料技术已成为目前复合材料领域的研究热点之一。RTM工艺具有一系列的优点,可以一次性快速成型大型、复杂(包括带夹芯或插件)的构件;无需胶衣涂层即可为构件提供光滑表面,后处理工作量小;预成型体尺寸易控,可设计性强;生产周期适中,可实现半自动或自动化生产,效率高;纤维含量较高;能够应用计算机辅助设计进行模具和产品设计,可实现充模过程的模拟;无需二次粘接。鉴于以上技术优点,本项目选用了快速RTM成型工艺试制地板。
3. 3 纤维预成型体制作
纤维预成型技术是RTM工艺的一个重要环节。对质量要求高、性能稳定、结构复杂、自动化程度要求高的制品来说,这项技术显得尤为重要。其原理是采用增粘剂/定型剂或编织/缝纫等技术将增强材料固结成与制品相同形状的半成品。纤维预成型技术在保证产品质量、生产工艺快速及自动化方面具有重要意义,是实施RTM低成本化的重要途径及手段。
根据汽车前地板结构特点,将其设计为由5个单独的预成型件缝合组装成一个整体。该预成型件采用了美国Airtech公司研制生产的Airtac 2增粘剂,通过研究确定最佳工艺参数为:增粘剂喷涂量为3%~5%、定型加热温度为90~100℃、定型时间为20~25min。
3. 4 基于多点注射的快速RTM模具设计技术
根据碳纤维复合材料前地板的结构特征以及RTM模具与合模液压机配合使用考虑,模具的结构类型可以采用多点浇口的三板式注射模具。对于该汽车前地板制件而言,产品需要装车验证,尺寸精度要求较;因产品结构复杂、尺寸大,所以注胶过程中的压力也较高;生产效率较高,要求快速成型,所以材料的导热性能要好。另外,该模具需采用现有的100t合模液压机作为启模、闭模的机构,模具重量不易过大。经初步设计分析,如果采用钢模,模具重量达12t左右,而采用铝模,其重量仅5t左右。综合以上考虑,该汽车地板RTM模具采用了高强度铝合金材料。
考虑到铝合金比钢材的硬度小,在设计铝合金模具时还应在一些细节上进行如下考虑:①如果在铝合金模具上加工螺纹孔,为了防止螺牙被螺栓磨损,需要安装钢丝螺套;②模具上设置的顶出点需要安装钢垫块;③导柱采用轴承套导柱,减少导柱的摩擦力。图3为该模具总体设计结构。
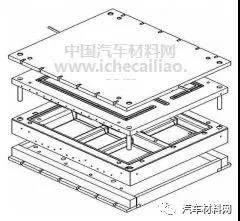
图3总体结构爆炸图
3. 5 碳纤维增强热固性环氧树脂复合材料前地板试制
主要工艺参数: 胶液温度为50℃,模具温度为55℃,注胶流量为10~20mL/s,固化温度为90℃,保温时间为20min,为了预防在注胶过程中发生爆模,注胶压力不得超过1MPa。产品从注胶到脱模,成型周期在30min以下,基本达到了RTM快速成型的要求。
4试验结果
4. 1 重 量
产品重量为16.0kg,与钢制地板相比减重42%,满足设计指标要求。
4. 2 静态弯曲刚度测试
将样件安装及固定在弯曲刚度测试台上,调平。样件的固定位置如图4所示。
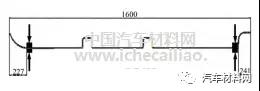
图4 样件弯曲刚度测试夹持位置图
在样件中心位置分别按照50.10kg、(50.10kg+30.45kg)、(50.10kg+30.45kg+20.30kg)三个加载块顺序加载,并记录各测点的变形量。弯曲刚度测试数据见表1。
表1弯曲刚度测试数据表
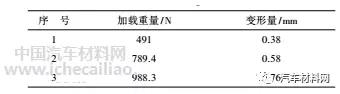
注:加载点和测量点均在样件中心位置。
根据图5所示地板弯曲刚度加载-变形图可知:碳纤维复合材料地板中心在1kN载荷下,中心点垂直挠度为0.76mm,满足设计指标小于2mm的要求。
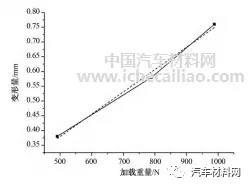
图5地板弯曲刚度加载-变形图
4. 3 扭转刚度测试
将样件安装固定在扭转刚度测试台上,调平。在样件扭转夹持杆上对应安装布置千分表,并测量记录各对应点千分表距中心轴的距离。扭转加载按表2加载重量依次加载测试。
表2扭转刚度测试数据表
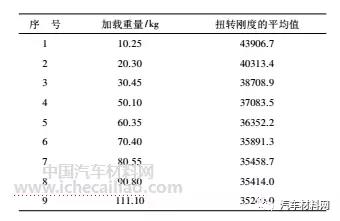
由图6所示地板加载-扭转刚度图可知:碳纤维复合材料地板扭转刚度大于3.5×104Nm2/rad,满足设计指标大于104Nm2/rad的要求。
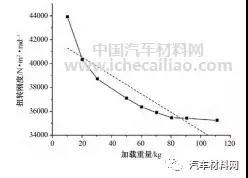
图6地板加载-扭转刚度图
4. 4 模态测试
将产品安装在振动试验台上,测试设备型号为V8-440(英国LDS)。设定振动加速度为0.3g(1g=9.8m/s2);扫频范围为10~500Hz;扫频速度为10ct/min。振动扫频测试结果见表3。
表3地板振动扫频测试结果
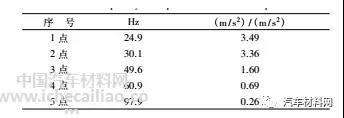
由表3可知,该碳纤维复合材料地板的阶模态频率均大于24.9Hz,满足设计指标大于20Hz的要求。
5结 语
通过对白车身汽车地板的结构设计确定碳纤维复合材料作为汽车前地板材料,选择RTM为成型工艺,采用多点注射的快速RTM模具,成功制备了碳纤维增强热固性环氧树脂复合材料前地板。通过静态弯曲刚度、扭转刚度及模态试验测试,结果满足汽车整车厂提出的技术要求,在保证与金属前地板互换性的基础上,重量减轻效果明显,证明复合材料在汽车领域使用的可行性,为未来汽车轻减化技术提供了一条可行的途径。
文章来源:期刊——玻璃钢/复合材料
作者:陈 刚,涂丽艳,陈明达,刘东
关键词:复合材料;汽车前地板;RTM成型
1概 述
随着汽车轻量化不断发展,节能、环保、安全、舒适已成为当今材料界和汽车界的研究热点。研究显示,车重每减少100kg,每百公里油耗可降低0.3~0.5L,二氧化碳的排放可以减少12g左右。车重减轻,可以提高车辆的加速度和制动效果。传统汽车钢铁材料约占车体总重的3/4,用碳纤维增强复合材料(CFRP)制造的车身和底盘在等刚度、等强度下可以减重40%~60%,相当于钢结构的1/3~1/6。因此,CFRP正日益成为汽车轻量化的首选材料,逐渐得到汽车行业越来越广泛的认可和应用。
2015年国内碳纤维需求总量为1.3万吨左右,如果保持平稳增长态势,预计2020年将达到2.5万吨。目前,我国复合材料在汽车工业中年用量比例还很小,因此,开发碳纤维复合材料在汽车上的应用研究具有很大的发展空间和应用前景。本文以碳纤维复合材料汽车前地板的研制为例,对其结构方案设计、纤维预成型体制作、成型工艺及性能测试进行了研究。
2结构设计方案
2. 1 结构设计依据
目标产品以金属白车身为设计依据,原金属汽车前地板横截面呈“几”字形,外形尺寸为1.7m×1.3m,重量为27.7kg,金属板厚为0.8mm左右,由21个板金冲压件组装焊接而成,如图1所示。
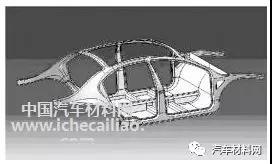
图 1 汽车白车身
2. 2 性能要求
减重:与金属钢制地板相比,减重不低于40%;
弯曲刚度:在1kN载荷下,中心点垂直挠度应小于2mm;
扭转刚度:≥104N·m2/rad;
一阶模态:≥20Hz。
2. 3 碳纤维复合材料地板设计过程
由于原金属汽车前地板零部件比较多,在复合材料成型中采用一体成型比较困难,为了充分发挥碳纤维复合材料性能及适应复合材料成型工艺特点,需要将原钢制地板结构进行局部的设计修改,修改内容主要有如下几个方面:
(1)取消加强筋板及多余的复杂筋条:充分发挥碳纤维复合材料的比强度、比模量高和可设计性强等的优点,根据等刚度设计原则,在前地板不同受力部位设计不同厚度CFRP,尽量取消加强筋板及多余的复杂筋条;
(2)取消工艺漏液孔:碳纤维复合材料前地板不同于钢制地板,产品焊接组装完成后无需在涂装车间进行电泳工序,所以可以取消各工艺漏液孔;
(3)在碳纤维零部件设计时,对于影响铺设成型的小圆角要尽量避免,原则上内角R≥3mm,以利于在模具上铺设成型,个别特殊部位可以将内角设计成R≥2mm,但会降低量产效率,应尽量避免;
(4)在碳纤维零部件壁厚不同的部位,应逐渐过渡,以免在成型固化过程中,因固化收缩不同而产生较大变形。
根据以上设计原则,重新修改设计后的前地板数模如图2所示。根据预先的有限元模拟,为了能够达到与原金属汽车前地板相同的刚度值,复合材料汽车前地板主板厚度为2.5mm,中央通道部分厚度为3.0mm。
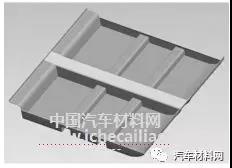
图 2 碳纤维复合材料前地板数模
3成型工艺及试制
3. 1 原材料
对于汽车前地板这种主受力结构件,一般需要首选快速成型的碳纤维复合材料。本项目设计选用性能较好的日本东丽碳纤维T700CS-12K织物,面密度分别为480g/m2和200g/m2;单轴向布为200g/m2。树脂体系选用快速固化的环氧树脂体系EpoTech167A/167B(广州博汇)。
3. 2 成型工艺
复合材料成本已成为制约复合材料规模化应用的瓶颈,以快速RTM成型技术为代表的低成本复合材料技术已成为目前复合材料领域的研究热点之一。RTM工艺具有一系列的优点,可以一次性快速成型大型、复杂(包括带夹芯或插件)的构件;无需胶衣涂层即可为构件提供光滑表面,后处理工作量小;预成型体尺寸易控,可设计性强;生产周期适中,可实现半自动或自动化生产,效率高;纤维含量较高;能够应用计算机辅助设计进行模具和产品设计,可实现充模过程的模拟;无需二次粘接。鉴于以上技术优点,本项目选用了快速RTM成型工艺试制地板。
3. 3 纤维预成型体制作
纤维预成型技术是RTM工艺的一个重要环节。对质量要求高、性能稳定、结构复杂、自动化程度要求高的制品来说,这项技术显得尤为重要。其原理是采用增粘剂/定型剂或编织/缝纫等技术将增强材料固结成与制品相同形状的半成品。纤维预成型技术在保证产品质量、生产工艺快速及自动化方面具有重要意义,是实施RTM低成本化的重要途径及手段。
根据汽车前地板结构特点,将其设计为由5个单独的预成型件缝合组装成一个整体。该预成型件采用了美国Airtech公司研制生产的Airtac 2增粘剂,通过研究确定最佳工艺参数为:增粘剂喷涂量为3%~5%、定型加热温度为90~100℃、定型时间为20~25min。
3. 4 基于多点注射的快速RTM模具设计技术
根据碳纤维复合材料前地板的结构特征以及RTM模具与合模液压机配合使用考虑,模具的结构类型可以采用多点浇口的三板式注射模具。对于该汽车前地板制件而言,产品需要装车验证,尺寸精度要求较;因产品结构复杂、尺寸大,所以注胶过程中的压力也较高;生产效率较高,要求快速成型,所以材料的导热性能要好。另外,该模具需采用现有的100t合模液压机作为启模、闭模的机构,模具重量不易过大。经初步设计分析,如果采用钢模,模具重量达12t左右,而采用铝模,其重量仅5t左右。综合以上考虑,该汽车地板RTM模具采用了高强度铝合金材料。
考虑到铝合金比钢材的硬度小,在设计铝合金模具时还应在一些细节上进行如下考虑:①如果在铝合金模具上加工螺纹孔,为了防止螺牙被螺栓磨损,需要安装钢丝螺套;②模具上设置的顶出点需要安装钢垫块;③导柱采用轴承套导柱,减少导柱的摩擦力。图3为该模具总体设计结构。
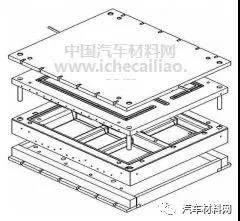
图3总体结构爆炸图
3. 5 碳纤维增强热固性环氧树脂复合材料前地板试制
主要工艺参数: 胶液温度为50℃,模具温度为55℃,注胶流量为10~20mL/s,固化温度为90℃,保温时间为20min,为了预防在注胶过程中发生爆模,注胶压力不得超过1MPa。产品从注胶到脱模,成型周期在30min以下,基本达到了RTM快速成型的要求。
4试验结果
4. 1 重 量
产品重量为16.0kg,与钢制地板相比减重42%,满足设计指标要求。
4. 2 静态弯曲刚度测试
将样件安装及固定在弯曲刚度测试台上,调平。样件的固定位置如图4所示。
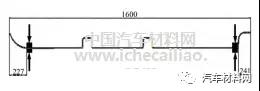
图4 样件弯曲刚度测试夹持位置图
在样件中心位置分别按照50.10kg、(50.10kg+30.45kg)、(50.10kg+30.45kg+20.30kg)三个加载块顺序加载,并记录各测点的变形量。弯曲刚度测试数据见表1。
表1弯曲刚度测试数据表
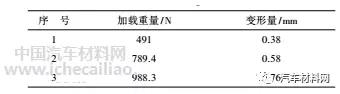
注:加载点和测量点均在样件中心位置。
根据图5所示地板弯曲刚度加载-变形图可知:碳纤维复合材料地板中心在1kN载荷下,中心点垂直挠度为0.76mm,满足设计指标小于2mm的要求。
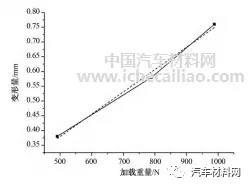
图5地板弯曲刚度加载-变形图
4. 3 扭转刚度测试
将样件安装固定在扭转刚度测试台上,调平。在样件扭转夹持杆上对应安装布置千分表,并测量记录各对应点千分表距中心轴的距离。扭转加载按表2加载重量依次加载测试。
表2扭转刚度测试数据表
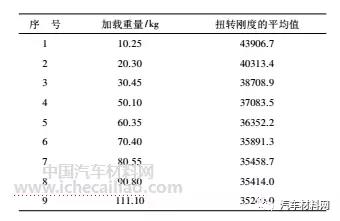
由图6所示地板加载-扭转刚度图可知:碳纤维复合材料地板扭转刚度大于3.5×104Nm2/rad,满足设计指标大于104Nm2/rad的要求。
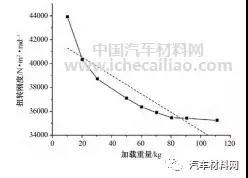
图6地板加载-扭转刚度图
4. 4 模态测试
将产品安装在振动试验台上,测试设备型号为V8-440(英国LDS)。设定振动加速度为0.3g(1g=9.8m/s2);扫频范围为10~500Hz;扫频速度为10ct/min。振动扫频测试结果见表3。
表3地板振动扫频测试结果
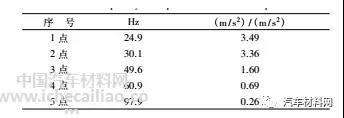
由表3可知,该碳纤维复合材料地板的阶模态频率均大于24.9Hz,满足设计指标大于20Hz的要求。
5结 语
通过对白车身汽车地板的结构设计确定碳纤维复合材料作为汽车前地板材料,选择RTM为成型工艺,采用多点注射的快速RTM模具,成功制备了碳纤维增强热固性环氧树脂复合材料前地板。通过静态弯曲刚度、扭转刚度及模态试验测试,结果满足汽车整车厂提出的技术要求,在保证与金属前地板互换性的基础上,重量减轻效果明显,证明复合材料在汽车领域使用的可行性,为未来汽车轻减化技术提供了一条可行的途径。
文章来源:期刊——玻璃钢/复合材料
作者:陈 刚,涂丽艳,陈明达,刘东
- 下一篇:解密冲压工艺中工业机器人应用技术
- 上一篇:大众化电动汽车之设计趋势
编辑推荐
最新资讯
-
辐射亚太,链接全球——采埃孚再制造
2025-07-30 11:46
-
思看科技发布子品牌SCANOLOGY,全球
2025-07-30 11:06
-
风雨不动安如山——比亚迪叉车构筑“
2025-07-30 08:48
-
NEAS CHINA 新能源汽车技术与生态链
2025-07-29 09:52
-
三维扫描革新碾磨机辊套检测,效率与
2025-07-25 10:46