混合动力变速箱下壳体加工辅助工艺定位的设计及改进
2018-04-26 17:02:36· 来源:机工机床世界
图1为混合动力变速箱壳体示意图,产品毛坯为压铸成型,每个面的加工余量在0.3~0.5mm,孔的加工余量单边0.3mm,产品外轮廓尺寸326mm×289mm×110mm,A、B、C、D、E、F面及面上的孔都需机加工,5个面上的孔都对基准A、B、C有φ0.15mm的位置度要求。
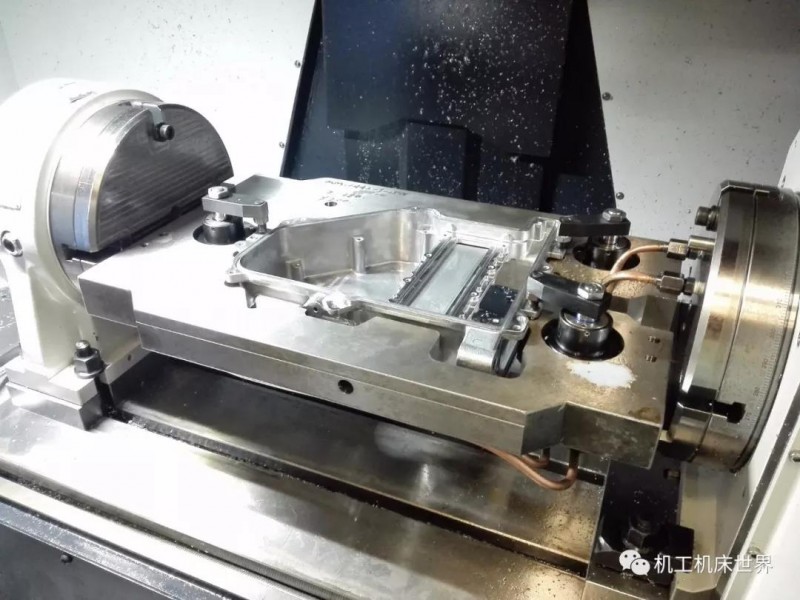
一、工艺分析
图1为混合动力变速箱壳体示意图,产品毛坯为压铸成型,每个面的加工余量在0.3~0.5mm,孔的加工余量单边0.3mm,产品外轮廓尺寸326mm×289mm×110mm,A、B、C、D、E、F面及面上的孔都需机加工,5个面上的孔都对基准A、B、C有φ0.15mm的位置度要求。
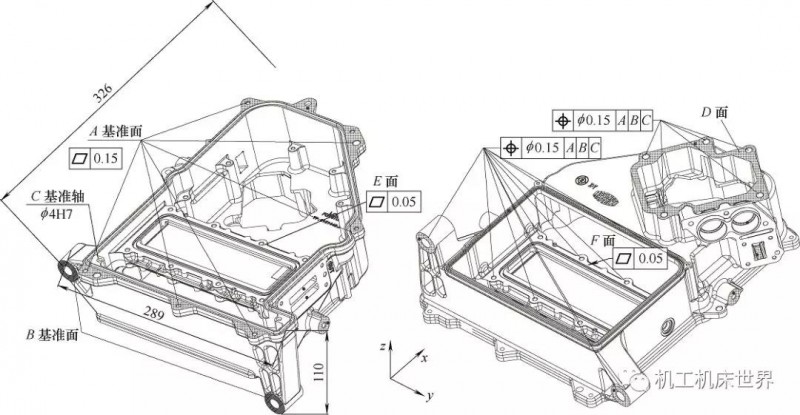
1、如果使用3轴立式加工中心,机床便宜,编程、加工操作简单,但5个面需要5次定位装夹,位置度难以保证。因此使用3轴立式加工中心、逐个面加工的方法不可行。
2、使用4轴立式加工中心,按照工序集中原则,在机加工第一序中,通过一次定位装夹,可以加工A、B、C、D、E、F面及A、C、D、E、F面上的孔,保证各面之间的相对位置及孔对A、B、C基准面的位置度,是较可行的方法。但从图1中找不到合适的定位及压紧位置,需要另想办法。
二、第一次辅助工艺定位、压紧点的设计
由于机加工第一序中,产品上没有合适的定位、压紧点,需要使用辅助工艺台,并在后续工序中去除。通过与客户协商,在不影响产品装配和外观的情况下,允许增加辅助工艺台,因此在压铸毛坯上做出辅助工艺台。如图2所示,设计4个辅助定位、压紧工艺台,保证产品加工中受力均匀、刚性足够。
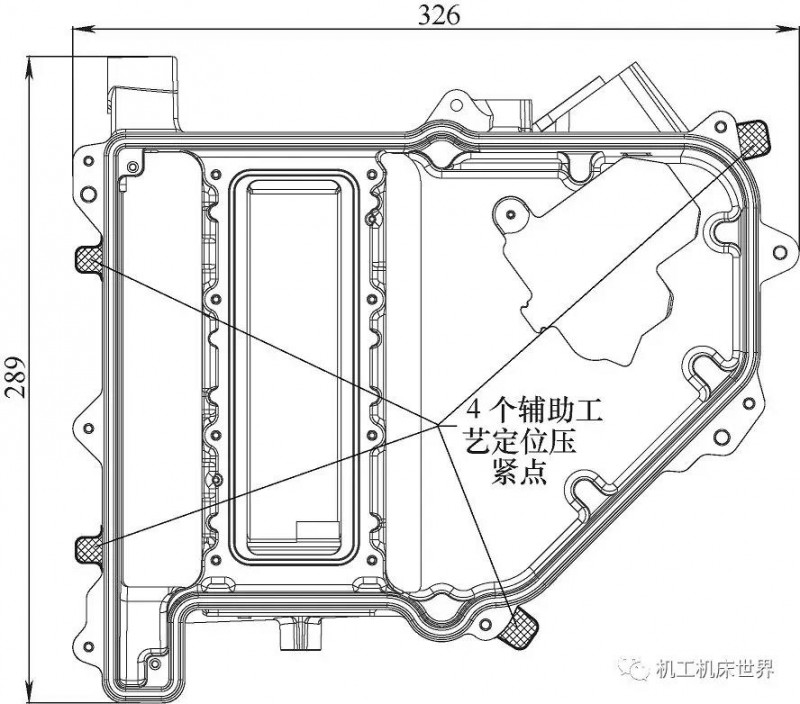
夹具设计以产品毛坯外轮廓限制X、Y的自由度,同时限制Z轴旋转自由度,Z向移动自由度用4个工艺台的底面限制,液压夹具设计如图3所示。定位点以φ5mm平头支承产品,压紧也是以φ5mm平头压在产品上,压紧点轴线尽量与支承点轴线对齐,防止压紧变形。
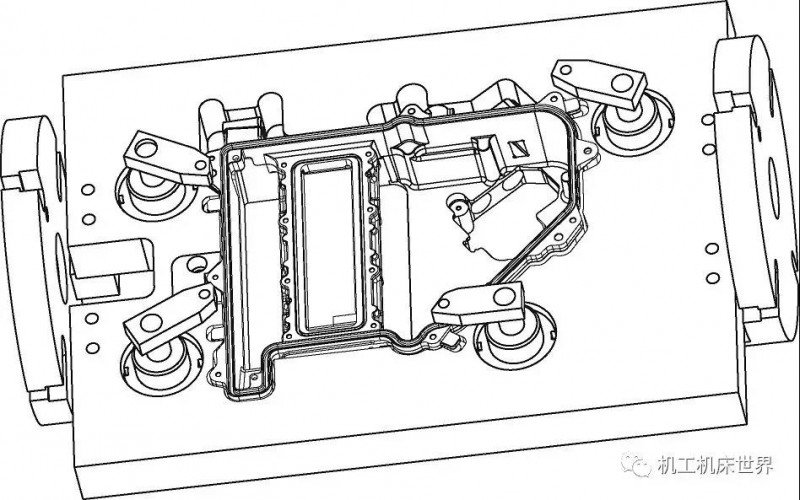
结果验证:试制初期,加工了100件产品,通过三坐标全检,尺寸及位置度都合格,PPK达到了要求,初步评审工艺方案及夹具设计是合理的,可以用于批量生产。但在量产时,进行CPK分析,发现有位置度不合格现象,通过观察分析,加工后,Z向由4个定位压紧点在机加工后有弹性变形,同时由于是采用外轮廓定X、Y方向移动自由度,缺少防呆措施,在切削力作用下,也会产生位置漂移现象,需要改进。
三、定位、夹紧点的改进
如图4所示,为了防止定位压紧造成产品变形,影响加工后产品精度,采用Z向3点形成一面的定位方式,避免了压紧变形对加工精度的影响,同时X、Y方向的移动及Z轴旋转,采用1个圆孔和一个腰形孔定位,符合一面两销定位要求,腰形孔与圆柱销定位,具有棱形销相同功能,定位准确,也可防止加工过程中因切削力变化产生的位置漂移,工艺台及定位孔由压铸毛坯时成型。
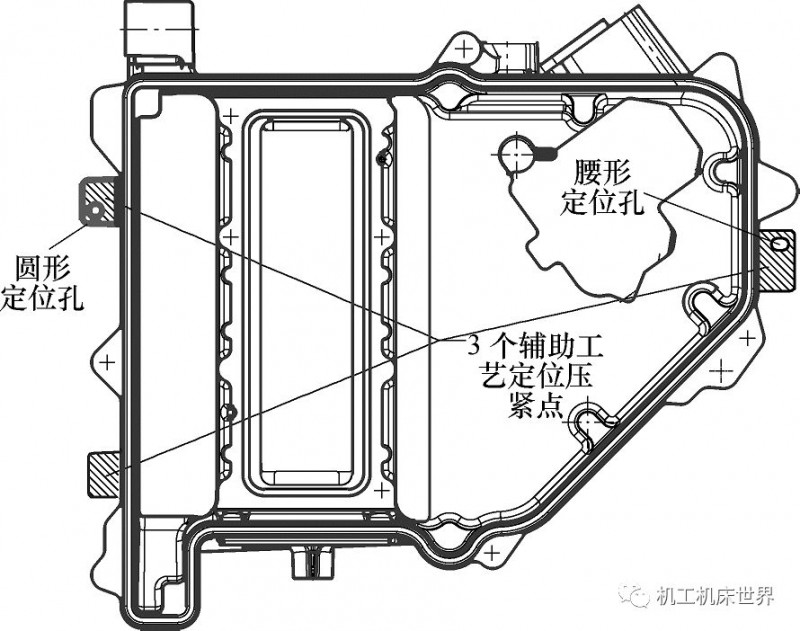
夹具设计如图5所示。夹具的支承柱定位点设计为钢球万向的,避免形成过定位而引起产品变形。同时,夹具定位支承柱和压板着力点轴线尽量保持同轴,防止产品因压紧产生弹性变形。
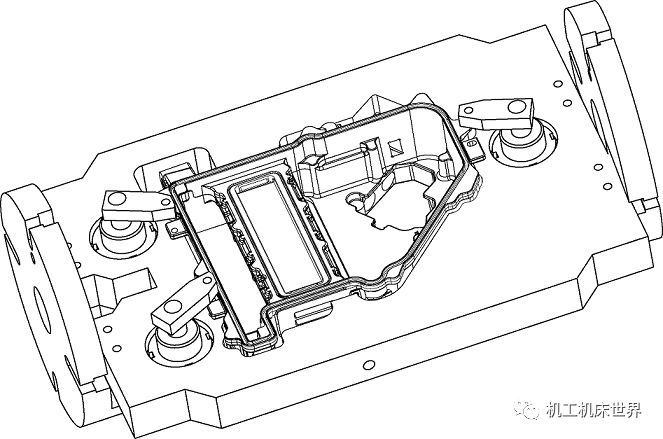
免责声明:本文系网络转载,版权归原作者所有。但因转载众多,无法确认真正原始作者,故仅标明转载来源。本文所用视频、图片、文字如涉及作品版权问题,请第一时间告知,我们将根据您提供的证明材料确认版权并按国家标准支付稿酬或立即删除内容!本文内容为原作者观点,并不代表本公众号赞同其观点和对其真实性负责。
- 下一篇:刚性专机变速箱壳体生产线柔性改造
- 上一篇:探究汽车变速器壳体加工新工艺
编辑推荐
最新资讯
-
辐射亚太,链接全球——采埃孚再制造
2025-07-30 11:46
-
思看科技发布子品牌SCANOLOGY,全球
2025-07-30 11:06
-
风雨不动安如山——比亚迪叉车构筑“
2025-07-30 08:48
-
NEAS CHINA 新能源汽车技术与生态链
2025-07-29 09:52
-
三维扫描革新碾磨机辊套检测,效率与
2025-07-25 10:46