铝合金汽车顶盖拉延成形优化及回弹控制
2018-04-25 09:38:44· 来源:锻造与冲压
构成汽车车身的零件一般分为三类:外覆盖件、内覆盖件和骨架件,前两者统称为覆盖件。汽车顶盖作为一种典型的外覆盖件,在质量要求上被划分为A类件,是消费者最直观接触到的零件之一,这就要求汽车顶盖在其表面上有着相对苛刻的要求。对于本文所述无天窗类顶盖,其拉深程度小,表面圆弧大,没有复杂的特征形状,因此总体来说其成形相对简单,但是仍不可避免存在圆角凹陷和破裂、法兰部位起皱等缺陷,其中最难以解决的问题是拉延后大面积回弹。
产品介绍及分析
构成汽车车身的零件一般分为三类:外覆盖件、内覆盖件和骨架件,前两者统称为覆盖件。汽车顶盖作为一种典型的外覆盖件,在质量要求上被划分为A类件,是消费者最直观接触到的零件之一,这就要求汽车顶盖在其表面上有着相对苛刻的要求。对于本文所述无天窗类顶盖,其拉深程度小,表面圆弧大,没有复杂的特征形状,因此总体来说其成形相对简单,但是仍不可避免存在圆角凹陷和破裂、法兰部位起皱等缺陷,其中最难以解决的问题是拉延后大面积回弹。
在汽车轻量化的要求下,顶盖常用5系及6系铝合金进行冷冲成形,且厚度较薄,一般在1mm左右。本文所述为江淮某型号汽车顶盖,其材料指定为6016铝合金,厚度为1mm。该材料强度较高,综合性能较好,但是延伸率较低,屈强比大,在常温下成形性能并不是很好,而且成形后回弹严重,因此需要设计更为有效的柔性成形工艺来提高表面质量和制件精度。充液拉深工艺作为一种典型的柔性成形工艺,被广泛应用于汽车制造和航空航天领域。该工艺在成形阶段通入高压液体代替凹模或者凸模,降低模具成本以及后期的修模时间,并能在模具之间形成良好的润滑作用,减小摩擦力。现针对该零件已经设计完成一套完整的拉延模具,但在后续参数调整中发现仍然存在一定的问题,主要是法兰起皱和回弹量过大,本文在现有模具基础上,基于大型商用有限元模拟软件Dynaform对模具进行调整和工艺改进,提高成形质量并减小回弹。
初始模具成形效果
图1为根据现有模具提取的有限元模拟当中使用的模型示意图。该零件成形过程中,其成形质量主要受到压边力、拉延筋形状和分布、以及液压加载方式的影响。现有模具中拉延筋的形状和位置已经固定,从俯视图来看主要为四周直边,圆角处无拉延筋,前阶段模拟中主要调整压边力以及液压加载曲线。通过模拟得到的最优的压边力为40kN,液压力在调整过程中主要采用如图2所示的三种加载方式,得到的最优路径为c,该路径可以保证成形过程中板料充分变形,减少起皱和拉裂缺陷。模拟得到的最佳结果如图3(a)所示。
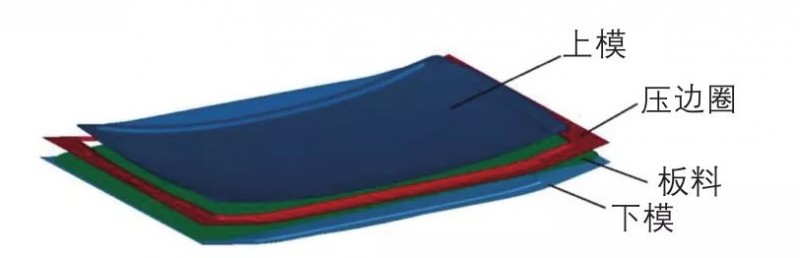
图1 原始模面充液拉深有限元模型
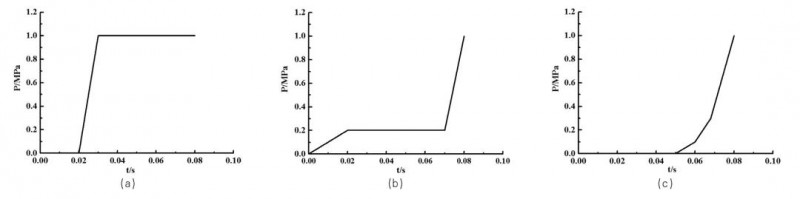
图2 不同液压加载路径
由图3(a)可以发现经过优化后四个圆角处仍然存在较为严重的起皱现象,这与现场实物出现的问题一致,如图3(b)所示。可以判断,现有模具仍存在待改进之处,因此设计两种改进方案如下文所述。

图3 模拟结果与实物对照示意图
改进方案一(压边圈填补法)
进一步分析起皱的原因可以发现,凹模口4个交角区域在上模下行的过程中没有模具限制,成形后出现严重的起皱缺陷,如图4所示。因此对原模面进行优化设计,如图5所示,将上模4个交角区域(图5(a)标注区域)添加到压边圈上。通过补充压边圈内圆角处,增大压边圈在下压过程中对坯料的作用效果,减小坯料圆角成形过程中的失稳现象,从而消除起皱。优化后的模面得到图6所示的结果,可以发现起皱现象得到明显改善,减薄率为13.9%,符合制件减薄率<15%的要求。
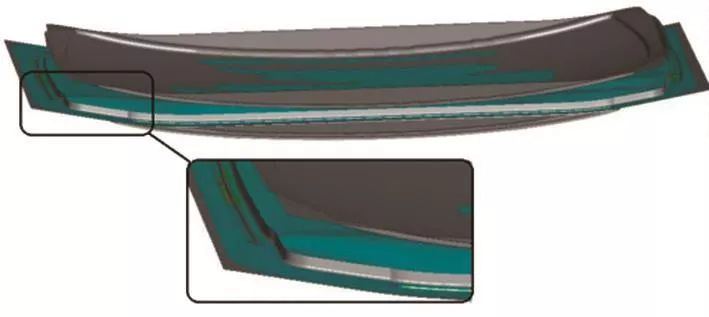
图4 起皱原因示意图
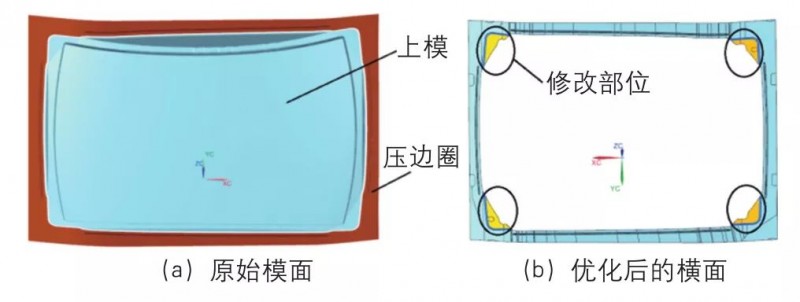
图5 模具优化示意图
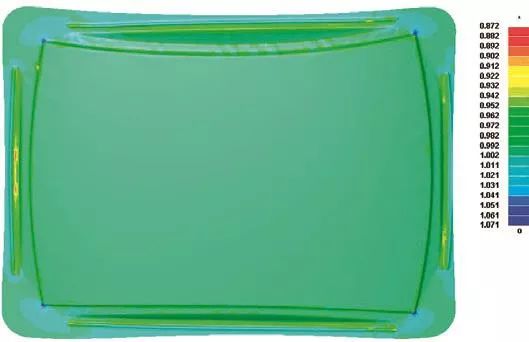
图6 方案一优化结果示意图
分析上述结果可以判断该修模方案可以很好的满足对顶盖成形质量的要求,但是仍然存在一些问题。如果按照上述方案进行优化,需要对压边圈及凸模进行较大程度修改,这是一个相对来讲很复杂的工作,会花费大量的人力物力,这就要求找到更为简单的方法。
模拟过程中可以发现成形主要的影响参数为拉延筋形状和位置、压边力以及液压曲线,这几个参数反复协调以后发现角部仍存在起皱以及拉裂情况,因此在较优参数下又进行了坯料形状和大小的优化,目的是应用最小阻力原则改善金属在角部的流动情况。在设计的几种板料形状中选择主要的三种如图7所示,其图7(a)方形板料尺寸为1700×1300mm2,图7(b)和图7(c)所示板料是在图7(a)所示板料基础上分别进行了倒圆角和倒斜角处理,从模拟结果可知图7(c)所示板料形状为最优,如图8(b)所示,无拉裂和起皱情况,减薄率符合要求。
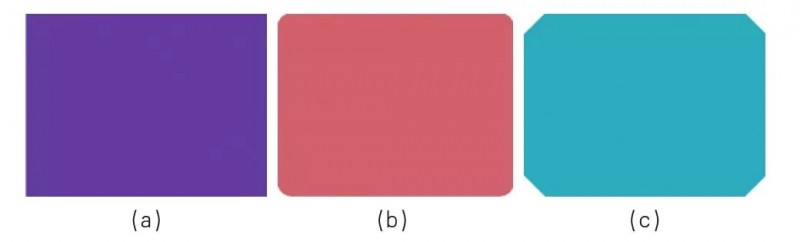
图7 坯料形状优化示意图
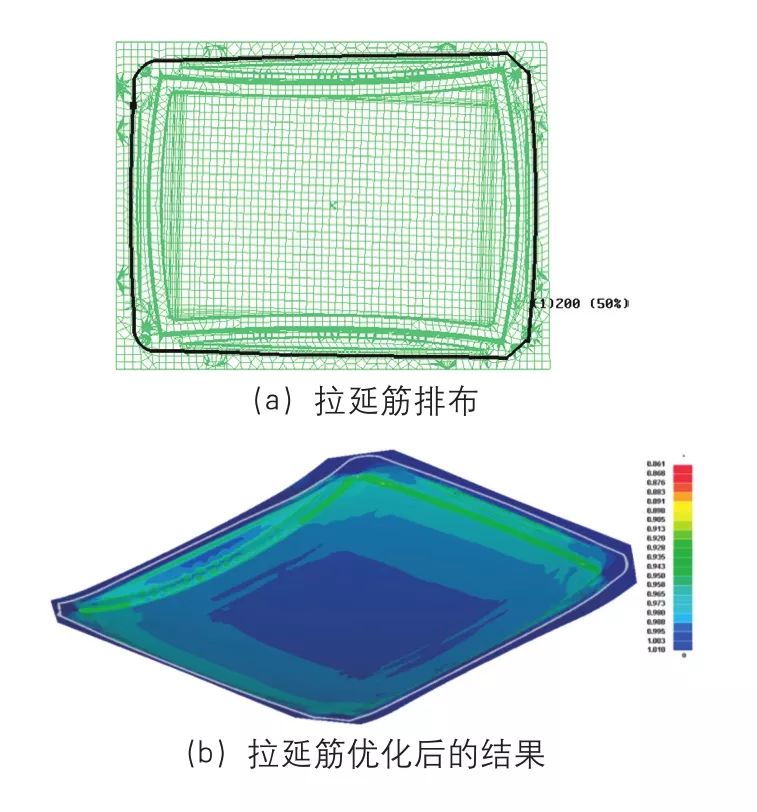
图8 拉延筋优化示意图
回弹预测
通过前期对模面的修改工作,已经可以很好的达到成形要求,但是仍需要对拉延结束后的回弹进行预测和分析。图9(a)为公司按照原有工艺生产的零件在拉延之后实际测得的回弹量,图9(b)为基于Dynaform软件的回弹模块得到的回弹云图,两者整体趋势基本相同,模拟的数值略大于实测值。由图中可以看到,回弹最严重的的部位发生在两侧的工艺补充面上,一般认为,只要实际的零件覆盖范围内回弹值满足要求即可,在此基础上尽量控制补充面上的回弹,避免在修边工序后应力释放导致回弹加剧。
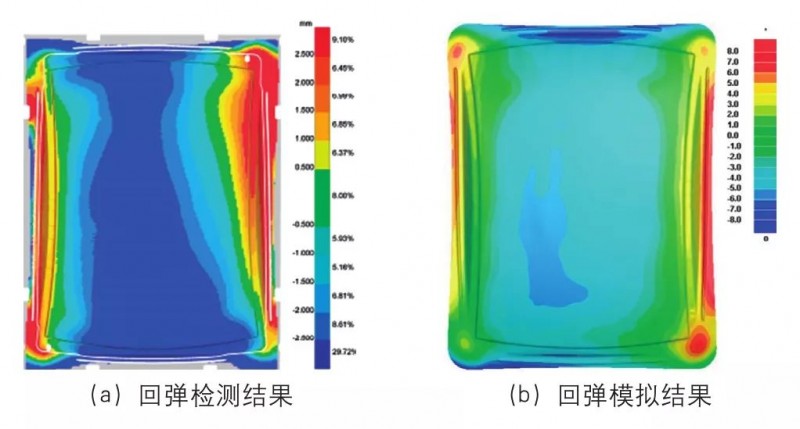
图9 回弹检测报告及模拟结果
在现有结果基础上根据最终制定的拉延筋排布方式以及坯料的形状,进行拉延筋参数、压边力、模具间隙和液压力这几个影响回弹的主要参数进行协调和优化,得到的回弹优化结果如图10所示。从图中可以知道,零件覆盖的范围内回弹基本小于0.5mm,满足生产要求,即使修边之后应力释放使回弹增大,生产中可以通过后续整形工步实现回弹控制。
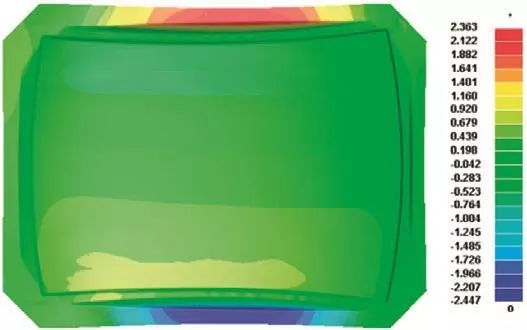
图10 回弹优化后回弹模拟结果
结论
最新资讯
-
辐射亚太,链接全球——采埃孚再制造
2025-07-30 11:46
-
思看科技发布子品牌SCANOLOGY,全球
2025-07-30 11:06
-
风雨不动安如山——比亚迪叉车构筑“
2025-07-30 08:48
-
NEAS CHINA 新能源汽车技术与生态链
2025-07-29 09:52
-
三维扫描革新碾磨机辊套检测,效率与
2025-07-25 10:46