三厢车后盖总成质量控制与设计优化
2018-03-28 16:54:03· 来源:《金属加工(热加工)》 作者:黄平华
以三厢车后盖总成为研究对象,针对后盖总成常见的角部尺寸塌陷和激光焊接质量两个问题,从零件设计方面着手,结合实际生产工艺来分析不同的零件设计对总成质量的影响,提出了一些简单的零件设计方案来解决这些问题,避免了大量的单件模具与总装夹具工装优化调试工作,对今后类似的零件结构设计有较好的借鉴意义。
以三厢车后盖总成为研究对象,针对后盖总成常见的角部尺寸塌陷和激光焊接质量两个问题,从零件设计方面着手,结合实际生产工艺来分析不同的零件设计对总成质量的影响,提出了一些简单的零件设计方案来解决这些问题,避免了大量的单件模具与总装夹具工装优化调试工作,对今后类似的零件结构设计有较好的借鉴意义。
在项目开发前期,可制造性分析对于零件的设计非常重要,直接关系到单件及总成装车的质量。针对三厢后盖总成常见的角部尺寸塌陷和激光焊质量两个问题进行了深入分析讨论,同时结合实际生产现场经验,获得了一些可以明显改善单件和总成质量的设计理念:①在满足冲压模具零件生产以及折边模内外板合拢的情况下,后盖内板角部与外板圆角根部的距离越小越好。②后盖内板尖角和加强筋的距离需小于30mm。③后盖外板上部激光焊接面区域的法兰边缘需要有加强筋,同时开工艺缺口。
后盖总成在整车装配中是属于比较重要的零件,在后围匹配中处于核心位置,和两侧侧框及后保险杠、玻璃等都存在匹配关系。在车型开发过程中,后盖总成作为一个独立个体,不可避免地会有一些匹配问题会被重点抱怨。按照一般逻辑,后盖总成的尺寸问题不外乎有两个原因造成:第一是单件尺寸超差,第二是生产过程中带来的尺寸偏差。从而解决问题的方式也就是优化单件尺寸或优化总成的工装及生产过程。然而优化已经客观存在的缺陷会造成大量的单件模具调试工作,以及工装夹具的调试优化工作,在增加项目成本的同时优化效率也不高。
针对某在产车型后盖总成存在的角部尺寸塌陷和激光焊区域尺寸偏差问题,创造性地从零件结构设计角度出发,讨论哪种结构的设计可以避免或改善上述的一些尺寸问题,从而在今后的新产品设计开发阶段就可以把这些有利的信息应用进去,提高产品设计的成熟度。
角部塌陷问题分析及优化方案
三厢后盖在折边时经常会遇到一个问题,就是后盖后部的两个尖角在折边后出现角部塌陷,影响尺寸匹配的同时也会出现表面缺陷,如图1所示。
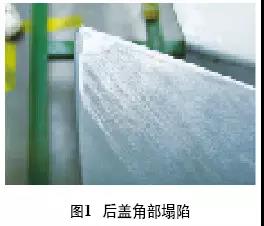
在检查折边工艺和折边设备后,发现后盖后部尖角的设计状态就是不折边,仅仅是通过角推把后盖外板的翻边角度向内推,如图2所示。
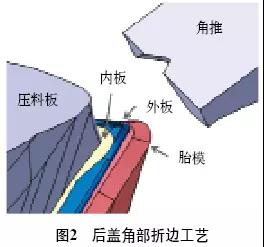
在试验过程中发现,由于后盖外板零件在角部位置成形硬化,刚度特别大,需要较大的角推力才能把翻边面推到理想位置。而后盖内板距离角部太远,有约7mm距离,导致在角推过程中外板零件的尖角部位处于自由状态,缺少内板零件的支撑和压料板的压合作用,如图3所示,从而出现角部塌陷。
基于这种状态,我们可以考虑在冲压车间修边条件允许的情况下,把内板零件角部的圆角缩小到R3mm,此时内板角部与外板圆角根部的距离就缩小到3.2mm,如图4所示。
根据建议优化冲压模具得到新的内板零件后,把角推工位压料板通过焊接获得更多的压料面积,同时把压料板和零件进行研配,最终获得折边后的后盖总成情况如图5所示,可以看到角部塌陷改善了很多。
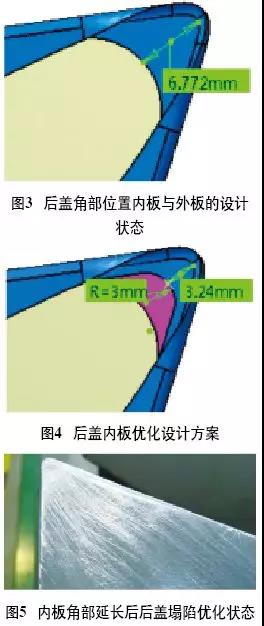
需要注意的是,把内板圆角延长后可能会产生新的问题,内板角部钣金偏软,如某车型后盖内板在生产过程中发现了如图6所示的零件变形,经过过程跟踪发现是在冲压机械手把零件放置在输送带上时造成的变形。
检查该车型后盖内板零件,发现在角部的咬边法兰面比较宽,尖角距离内板造型加强筋较远从而导致尖角偏软(见图7)。
对比以往车型后盖内板造型及实际生产状况,得出经验数据:为保证后盖内板尖角的刚性和稳定性,尖角和内板造型加强筋距离需小于30mm。
综上所述,为保证后盖总成在后盖尖角处的尺寸质量以及稳定性,对于后盖内板尖角处的零件设计需要同时满足两个条件:①在满足冲压模具零件生产以及折边模内外板合拢的情况下,后盖内板角部与外板圆角根部的距离越小越好。②后盖内板尖角和加强筋的距离需小于30mm。因此,对于后盖内板角部的设计可采用图8所示造型。
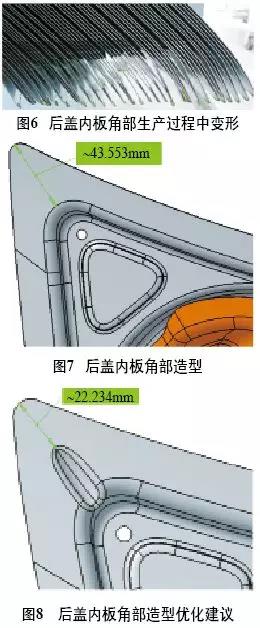
激光焊接面质量问题分析及优化方案
目前,上汽大众三厢车后盖的设计方案基本上都是上下板通过激光焊接,然后再和后盖内板进行咬边。激光焊接面的质量好坏会直接影响后盖总成在Z向和X向的功能尺寸,反映到装车就有可能会影响到后盖总成下部与后保险杠之间的缝隙匹配及后盖两侧与后保险杠之间平整度匹配。当然,这两个匹配问题由很多因素造成,如后盖下部本身的尺寸超差,后盖内板在X向的尺寸回弹及折边损耗的控制等。在此仅针对后盖外板上部激光焊接面质量控制方面进行相对深入分析。
一般后盖外板上板激光焊接面的结构如图9所示,法兰边缘除了有两个缺口,是平坦的。
为保证激光焊接面的平整度质量,冲压模具在设计斜楔翻边模时会采用增加下托料的翻边方式来控制翻边法兰起皱和保证尺寸的稳定性,但这种设计同时会造成法兰面向外翻转,如图10所示黑色虚线的实际零件和紫色理论零件位置的偏差。
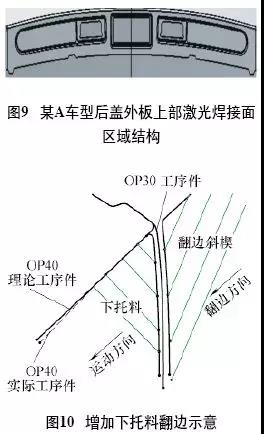
同时在翻边完毕后由于法兰边缘存在应力释放会导致激光焊接面的尺寸波动很大,如图11所示,某A车型后盖外板单件的测量报告显示,激光焊接面左右尺寸落差达8mm。这种尺寸落差在激光焊接的时候尽管可以通过总成夹具进行强制压合然后完成激光焊接,对激光焊接的质量影响不是很大,出现焊接中断、脱焊的概率不是很高。但后盖外板上下部焊接完成后,不可避免会存在一些应力。而这种残余应力在涂装车间进行电泳及烘干工序时会得到释放从而导致后盖变形。这种不可控的影响对后盖装车影响比较恶劣,我们还是要从根本上想办法去解决。
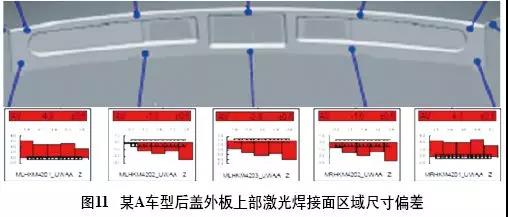
既然是由于斜楔翻边后的残余应力释放导致的焊接面尺寸偏差,那我们可以从残余应力的方面着手来加以控制。因此,在某个新车型B的开发过程中,就在该激光焊接区域的造型设计方面提出新的方案:在法兰边缘部位增加一条加强筋,如图12所示。
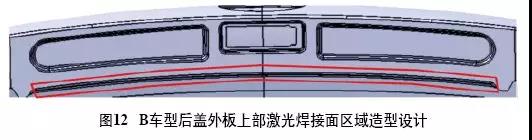
这条加强筋的成形是在完成整个激光焊接面的翻边后完成的,和翻边面上的其他特征一起成形。在造型方面就可以很好地控制翻边后产生的应力释放,同时让冲压模具有一个整形工序,可以来调整该法兰边缘部位的尺寸。如图13所示,B车型后盖外板上部的测量报告中显示,这种增加加强筋的后盖外板激光焊接面左右的尺寸落差仅有2mm,且左右基本上对称。
B车型后盖外板造型设计获得了一定成绩,比起A车型尺寸落差8mm有了很大改善。根据自身的经验积累和判断,如果在激光焊接面区域除了增加加强筋,再增加一两个工艺缺口,应该可以使得该区域在翻边过程中应力释放更加彻底,激光焊接面的相关尺寸得到更好的控制,如图14所示。这类的后盖外板设计已经应用在新的项目中,然而目前零件还没有量产,具体的对于零件优化的效果还有待进一步验证。
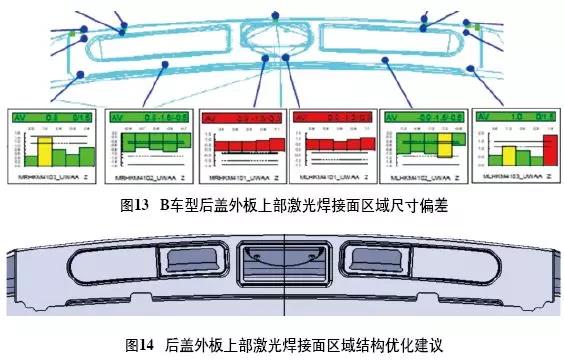
在项目开发前期,可制造性分析对于零件的设计非常重要,直接关系到单件及总成装车的质量。针对三厢后盖总成常见的角部尺寸塌陷和激光焊质量两个问题进行了深入分析讨论,同时结合实际生产现场经验,获得了一些可以明显改善单件和总成质量的设计理念:①在满足冲压模具零件生产以及折边模内外板合拢的情况下,后盖内板角部与外板圆角根部的距离越小越好。②后盖内板尖角和加强筋的距离需小于30mm。③后盖外板上部激光焊接面区域的法兰边缘需要有加强筋,同时开工艺缺口。
后盖总成在整车装配中是属于比较重要的零件,在后围匹配中处于核心位置,和两侧侧框及后保险杠、玻璃等都存在匹配关系。在车型开发过程中,后盖总成作为一个独立个体,不可避免地会有一些匹配问题会被重点抱怨。按照一般逻辑,后盖总成的尺寸问题不外乎有两个原因造成:第一是单件尺寸超差,第二是生产过程中带来的尺寸偏差。从而解决问题的方式也就是优化单件尺寸或优化总成的工装及生产过程。然而优化已经客观存在的缺陷会造成大量的单件模具调试工作,以及工装夹具的调试优化工作,在增加项目成本的同时优化效率也不高。
针对某在产车型后盖总成存在的角部尺寸塌陷和激光焊区域尺寸偏差问题,创造性地从零件结构设计角度出发,讨论哪种结构的设计可以避免或改善上述的一些尺寸问题,从而在今后的新产品设计开发阶段就可以把这些有利的信息应用进去,提高产品设计的成熟度。
角部塌陷问题分析及优化方案
三厢后盖在折边时经常会遇到一个问题,就是后盖后部的两个尖角在折边后出现角部塌陷,影响尺寸匹配的同时也会出现表面缺陷,如图1所示。
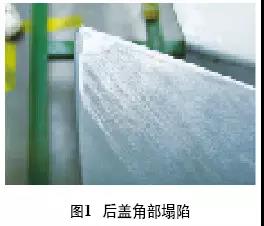
在检查折边工艺和折边设备后,发现后盖后部尖角的设计状态就是不折边,仅仅是通过角推把后盖外板的翻边角度向内推,如图2所示。
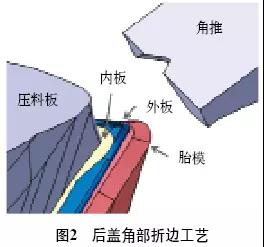
在试验过程中发现,由于后盖外板零件在角部位置成形硬化,刚度特别大,需要较大的角推力才能把翻边面推到理想位置。而后盖内板距离角部太远,有约7mm距离,导致在角推过程中外板零件的尖角部位处于自由状态,缺少内板零件的支撑和压料板的压合作用,如图3所示,从而出现角部塌陷。
基于这种状态,我们可以考虑在冲压车间修边条件允许的情况下,把内板零件角部的圆角缩小到R3mm,此时内板角部与外板圆角根部的距离就缩小到3.2mm,如图4所示。
根据建议优化冲压模具得到新的内板零件后,把角推工位压料板通过焊接获得更多的压料面积,同时把压料板和零件进行研配,最终获得折边后的后盖总成情况如图5所示,可以看到角部塌陷改善了很多。
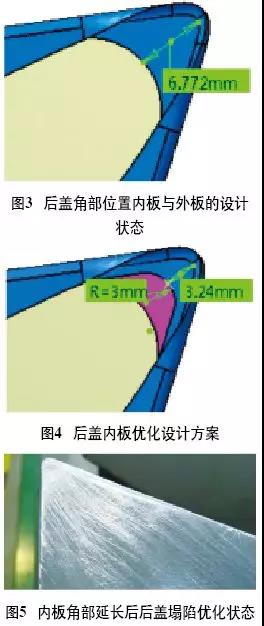
需要注意的是,把内板圆角延长后可能会产生新的问题,内板角部钣金偏软,如某车型后盖内板在生产过程中发现了如图6所示的零件变形,经过过程跟踪发现是在冲压机械手把零件放置在输送带上时造成的变形。
检查该车型后盖内板零件,发现在角部的咬边法兰面比较宽,尖角距离内板造型加强筋较远从而导致尖角偏软(见图7)。
对比以往车型后盖内板造型及实际生产状况,得出经验数据:为保证后盖内板尖角的刚性和稳定性,尖角和内板造型加强筋距离需小于30mm。
综上所述,为保证后盖总成在后盖尖角处的尺寸质量以及稳定性,对于后盖内板尖角处的零件设计需要同时满足两个条件:①在满足冲压模具零件生产以及折边模内外板合拢的情况下,后盖内板角部与外板圆角根部的距离越小越好。②后盖内板尖角和加强筋的距离需小于30mm。因此,对于后盖内板角部的设计可采用图8所示造型。
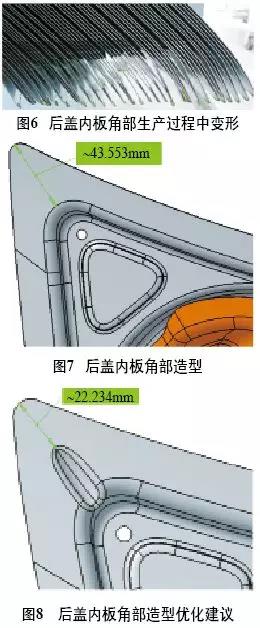
激光焊接面质量问题分析及优化方案
目前,上汽大众三厢车后盖的设计方案基本上都是上下板通过激光焊接,然后再和后盖内板进行咬边。激光焊接面的质量好坏会直接影响后盖总成在Z向和X向的功能尺寸,反映到装车就有可能会影响到后盖总成下部与后保险杠之间的缝隙匹配及后盖两侧与后保险杠之间平整度匹配。当然,这两个匹配问题由很多因素造成,如后盖下部本身的尺寸超差,后盖内板在X向的尺寸回弹及折边损耗的控制等。在此仅针对后盖外板上部激光焊接面质量控制方面进行相对深入分析。
一般后盖外板上板激光焊接面的结构如图9所示,法兰边缘除了有两个缺口,是平坦的。
为保证激光焊接面的平整度质量,冲压模具在设计斜楔翻边模时会采用增加下托料的翻边方式来控制翻边法兰起皱和保证尺寸的稳定性,但这种设计同时会造成法兰面向外翻转,如图10所示黑色虚线的实际零件和紫色理论零件位置的偏差。
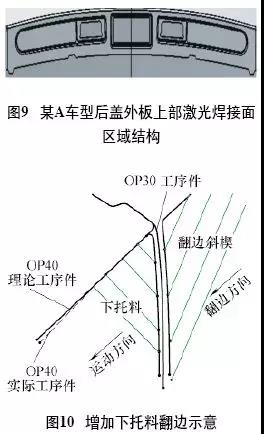
同时在翻边完毕后由于法兰边缘存在应力释放会导致激光焊接面的尺寸波动很大,如图11所示,某A车型后盖外板单件的测量报告显示,激光焊接面左右尺寸落差达8mm。这种尺寸落差在激光焊接的时候尽管可以通过总成夹具进行强制压合然后完成激光焊接,对激光焊接的质量影响不是很大,出现焊接中断、脱焊的概率不是很高。但后盖外板上下部焊接完成后,不可避免会存在一些应力。而这种残余应力在涂装车间进行电泳及烘干工序时会得到释放从而导致后盖变形。这种不可控的影响对后盖装车影响比较恶劣,我们还是要从根本上想办法去解决。
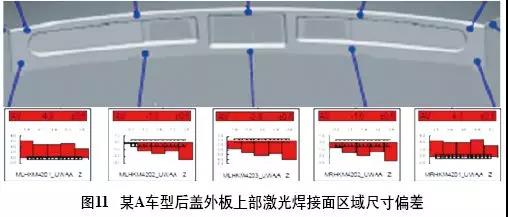
既然是由于斜楔翻边后的残余应力释放导致的焊接面尺寸偏差,那我们可以从残余应力的方面着手来加以控制。因此,在某个新车型B的开发过程中,就在该激光焊接区域的造型设计方面提出新的方案:在法兰边缘部位增加一条加强筋,如图12所示。
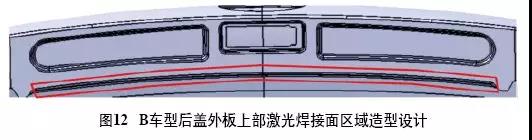
这条加强筋的成形是在完成整个激光焊接面的翻边后完成的,和翻边面上的其他特征一起成形。在造型方面就可以很好地控制翻边后产生的应力释放,同时让冲压模具有一个整形工序,可以来调整该法兰边缘部位的尺寸。如图13所示,B车型后盖外板上部的测量报告中显示,这种增加加强筋的后盖外板激光焊接面左右的尺寸落差仅有2mm,且左右基本上对称。
B车型后盖外板造型设计获得了一定成绩,比起A车型尺寸落差8mm有了很大改善。根据自身的经验积累和判断,如果在激光焊接面区域除了增加加强筋,再增加一两个工艺缺口,应该可以使得该区域在翻边过程中应力释放更加彻底,激光焊接面的相关尺寸得到更好的控制,如图14所示。这类的后盖外板设计已经应用在新的项目中,然而目前零件还没有量产,具体的对于零件优化的效果还有待进一步验证。
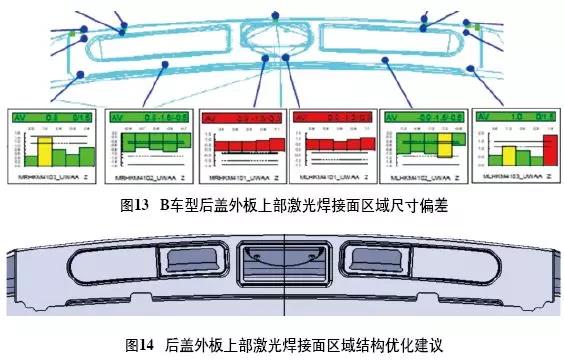
最新资讯
-
辐射亚太,链接全球——采埃孚再制造
2025-07-30 11:46
-
思看科技发布子品牌SCANOLOGY,全球
2025-07-30 11:06
-
风雨不动安如山——比亚迪叉车构筑“
2025-07-30 08:48
-
NEAS CHINA 新能源汽车技术与生态链
2025-07-29 09:52
-
三维扫描革新碾磨机辊套检测,效率与
2025-07-25 10:46