简单分析高速重载列车车轮加工刀具材料的研发过程
2018-03-08 09:38:59· 来源:工具技术 作者:朱国丽
目前降低碳含量并结合微合金化是国内高速车轮用钢发展的主要趋势。在数控机床中,列车车轮需要在高切速、大用量和干式(或湿式)切削的苛刻条件下进行粗、精切削加工,这对加工刀具提出了更为严格的要求。刀具必须是具有高强度、高耐磨性、高红硬性、高寿命的涂层硬质合金刀具。
车轮作为影响列车运行安全性、稳定性的关键部件之一,随着列车运行速度和载重的不断提升,在行驶时有可能会出现各种影响安全性的问题。客运高速列车车轮在高速运动条件下受到速度效应和制动方式的制约,其受力状态发生了很大变化,从而对强韧性、耐磨性、抗热裂性、抗疲劳性、抗剥离性提出了更高的要求;货运重载列车由于轮轨接触应力的增加,车轮制动热负荷上升,引起车轮剥离失效,在运用中最突出的问题是车轮踏面剥离严重。因此,对车轮材料来说,既要求高强度、高硬度和耐磨性能,又要求高的韧性和耐热性等多种性能的组合。
目前降低碳含量并结合微合金化是国内高速车轮用钢发展的主要趋势。在数控机床中,列车车轮需要在高切速、大用量和干式(或湿式)切削的苛刻条件下进行粗、精切削加工,这对加工刀具提出了更为严格的要求。刀具必须是具有高强度、高耐磨性、高红硬性、高寿命的涂层硬质合金刀具。
本文以加工高速、重载列车车轮用刀具为载体,结合进口先进轮毂刀的分析结果,从刀具材质及制备工艺、刀具涂层及工艺等技术入手,通过进一步技术创新,开发出适合于高速切削、重力切削条件下的高速、重载列车车轮加工刀具,以实现国产化,替代同类进口刀具产品。
1 试验过程
①试样制备
如表1所示,对进口轮毂刀片的基体、涂层和结构进行分析研究。根据进口刀片的分析结果,研发出相应的基体和涂层牌号。按照表2中的成分将原料进行混合,在45kN的压力下压制1组试样。采用低压烧结,在350℃下脱蜡1h,然后加热到1425℃,真空烧结0.5h,再快速充入3MPa氩气,加压烧结0.5h,最后冷却至常温,制得试样Z263。
②检测方法
试样烧结后,试样条(10根)经金刚石砂轮磨削至30mm×5mm×5mm。采用三点弯曲法在RGM100液压式万能试验机上测量抗弯强度,跨距20mm,各测定10个试样,去掉最高值及最低值后取算术平均值;在THR-150DXC型数字洛氏硬度计上测量洛氏硬度,一个试样测5点,取算术平均值;用OLYMPUS DP71光学显微镜评价烧结体的孔隙度和显微组织;用VEGA3 SEM扫描电镜观察合金基体显微组织和涂层形貌;直接用分析天平测量并计算合金密度;用钴磁检测仪、矫顽磁力检测仪分别测量合金的磁饱和值和矫顽磁力。
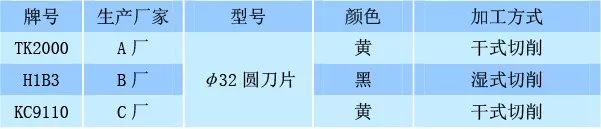
表1 进口刀片信息

表2 原料粉末的化学成分(wt%)
2 试验结果与分析
(1)进口轮毂刀片牌号的分析结果
表3为进口刀片基体的主要性能参数。由表中的分析结果可知,三种进口刀片合金的Co含量都低于6%,属于低钴合金,硬度HRA均大于91.5,从平均晶粒度可以推断,三种合金基体均属于细晶硬质合金。
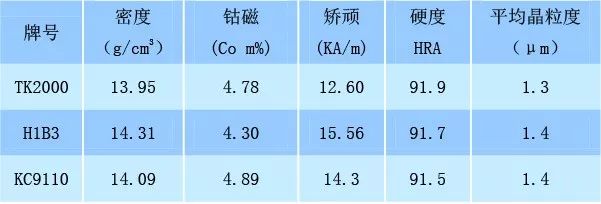
表3 进口刀片基体的主要性能参数
表4列出了三种进口刀片基体的EDS分析结果(因EDS不能测试碳含量,所以该数据是经过换算的金属碳化物成分)。从表中可以看出,在三种进口刀片基体中除硬质相WC和粘接相Co外,还有不同含量的TiC、TaC和NbC,其中KC9110中含有少量的Cr。在合金中,TaC或NbC的主要作用是提高合金的高温硬度与强度,同时还可以提高合金的常温硬度、抗氧化能力、抗月牙洼磨损和抗后刀面磨损能力。此外,TaC还可提高WC-TiC-Co类合金的抗弯强度与冲击韧性,增加刀刃强度,提高刀刃抗碎裂和抗破损能力。这样的基体成分是为了适应列车车轮加工时高切速、大用量和干式(或湿式)切削的苛刻条件。
图1为三种进口刀片的基体断口SEM照片。由图可知,三种进口刀片基体都是由三相组成:α相(WC)、Co相和γ相(固溶体)。其中,α相为多角形黑灰色组织;Co相是围绕在WC晶粒周围的白色组织;γ相是近似圆形的晶粒。三相分布均匀、组织致密。
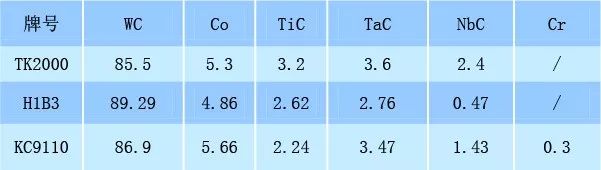
表4 进口刀片基体的成分(wt%)
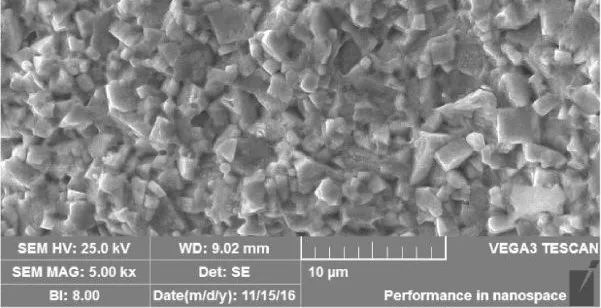
(a)TK2000
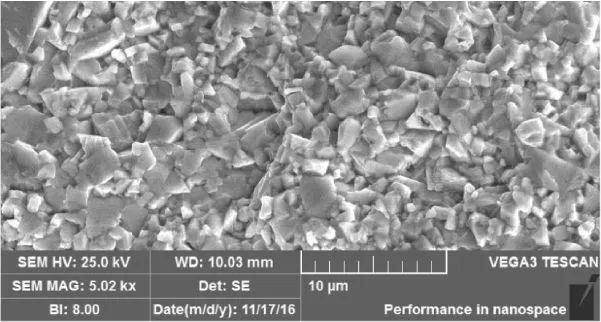
(b)H1B2
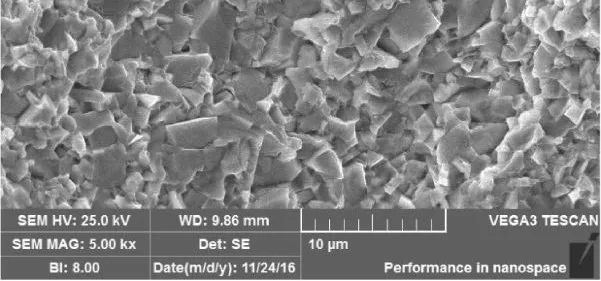
(c)KC9110
图1 三种进口刀片的基体断口SEM照片
图2为三种进口刀片的涂层断口SEM照片。由图可知,三种进口刀片涂层均为多层复合涂层。TK2000涂层分为3层,涂层总厚度约为13μm,主要结构是基体-TiCN-Al2O3-TiN,其中7μm厚的TiCN是细密的柱状晶形,具有很好的耐磨性能,而Al2O3层厚度约5μm,具有很好的抗高温性能,保障高速干切削时刀片基体抗塑性变形能力。
由图2a的金相结构可以看出,TK2000基体表面形成缺立方相碳化物和碳氮化物的韧性区域,即表面为富钴的WC+Co薄层,厚度约25μm。这样的结构一方面可以阻止表面裂纹的扩展;另一方面能满足基体抗变形性能的要求,有效地提高了刀具材料的使用寿命。
由图2b可知,H1B2涂层为2层,涂层总厚度约9μm,主要结构是基体-TiCN-Al2O3,其中TiCN约4μm,Al2O3约5μm。从金相图可以看出,H1B2基体表面也有韧性区域,厚度约15μm。
由图2c可知,KC9110涂层为4层,涂层总厚度约25μm,主要结构是基体-TiCN-TiN-Al2O3-TiN,其中TiCN约14μm,Al2O3约10μm。从金相图可以看出,KC9110基体表面也有韧性区域,厚度约20μm。
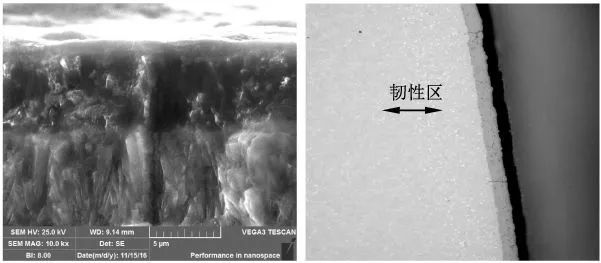
(a)TK2000

(b)H1B2
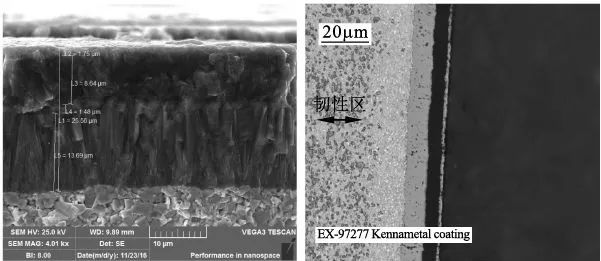
(c)KC9110
图2 三种进口刀片的涂层断口SEM和金相照片(1500×)
(2)基体牌号和涂层的研发
根据表3中进口轮毂刀牌号基体性能的分析结果,以低钴、细晶为研究方向,自主研发了硬质合金牌号Z263,其性能如表5所示,其中钴磁为6.35,硬度91.5HRA,平均晶粒度1.3μm。

表5 Z263的主要性能参数
图3是自主研发的基体牌号Z263的断口SEM照片。由图可知,其晶粒较细,三相组织均匀,没有异常长大的晶粒和缺陷。
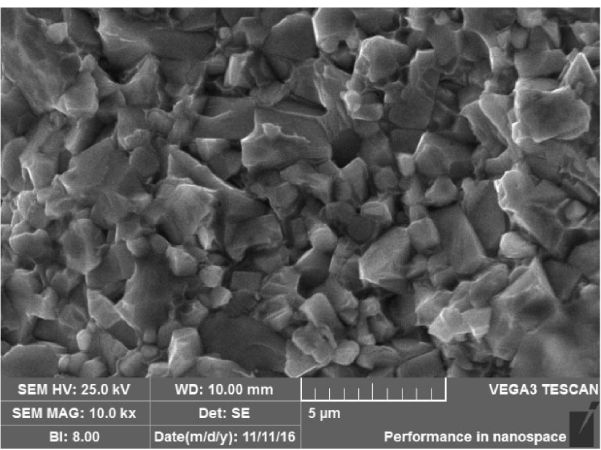
图3 Z263基体断口SEM照片
图4为19H涂层断口SEM图,为多层复合加厚CVD涂层,共5层涂层,由内往外分别是TiN-TiCN-TiN-Al2O3-TiN,总厚度20μm,其中Al2O3约8μm。
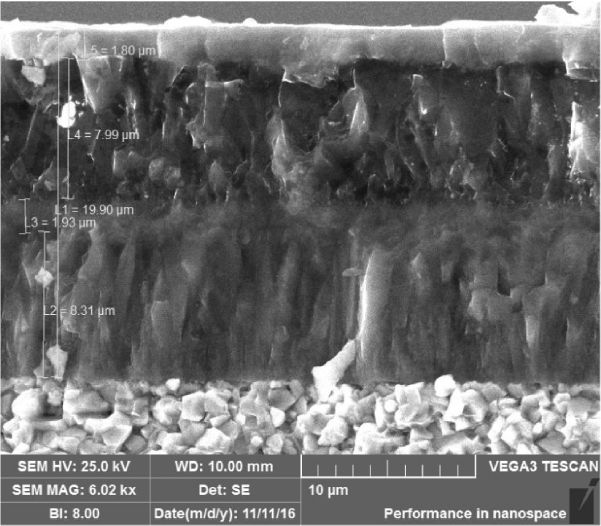
(a)
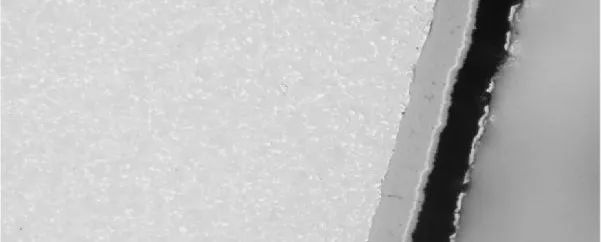
(b)
图4 19H涂层断口SEM和金相照片(1500×)
(3)现场使用结果
采用自主研发的轮毂刀专用基体Z263制备出型号为RCMX320900的轮毂刀片,并在车轮厂进行现场试用,干式切削加工材质为CL60的高速车轮内、外辐板。
加工参数:切削速度v=100m/min,进给量f=1-1.5mm,切削深度ap=5-8mm。搭配高性能超厚CVD涂层19,加工寿命为41件,现场用国外进口涂层刀片的寿命为30件,可见Z263+19涂层的RCMX320900轮毂刀的寿命达到国外进口刀片水平。
总结
三种国外进口轮毂刀的基体TK2000、H1B3和KC9110属于低钴合金,硬度HRA大于91.5,基体中都含有Ta和Nb,同时基体都是表面富钴的梯度合金,涂层为CVD多层复合涂层。
自主研发的低钴细晶合金Z263,组织均匀,性能优良;19H涂层为加厚CVD多层复合涂层,总厚度达到20μm,其中Al2O3约为8μm。Z263搭配19H涂层生产的Φ32轮毂刀,现场试用寿命达到国外进口刀片的水平。
目前降低碳含量并结合微合金化是国内高速车轮用钢发展的主要趋势。在数控机床中,列车车轮需要在高切速、大用量和干式(或湿式)切削的苛刻条件下进行粗、精切削加工,这对加工刀具提出了更为严格的要求。刀具必须是具有高强度、高耐磨性、高红硬性、高寿命的涂层硬质合金刀具。
本文以加工高速、重载列车车轮用刀具为载体,结合进口先进轮毂刀的分析结果,从刀具材质及制备工艺、刀具涂层及工艺等技术入手,通过进一步技术创新,开发出适合于高速切削、重力切削条件下的高速、重载列车车轮加工刀具,以实现国产化,替代同类进口刀具产品。
1 试验过程
①试样制备
如表1所示,对进口轮毂刀片的基体、涂层和结构进行分析研究。根据进口刀片的分析结果,研发出相应的基体和涂层牌号。按照表2中的成分将原料进行混合,在45kN的压力下压制1组试样。采用低压烧结,在350℃下脱蜡1h,然后加热到1425℃,真空烧结0.5h,再快速充入3MPa氩气,加压烧结0.5h,最后冷却至常温,制得试样Z263。
②检测方法
试样烧结后,试样条(10根)经金刚石砂轮磨削至30mm×5mm×5mm。采用三点弯曲法在RGM100液压式万能试验机上测量抗弯强度,跨距20mm,各测定10个试样,去掉最高值及最低值后取算术平均值;在THR-150DXC型数字洛氏硬度计上测量洛氏硬度,一个试样测5点,取算术平均值;用OLYMPUS DP71光学显微镜评价烧结体的孔隙度和显微组织;用VEGA3 SEM扫描电镜观察合金基体显微组织和涂层形貌;直接用分析天平测量并计算合金密度;用钴磁检测仪、矫顽磁力检测仪分别测量合金的磁饱和值和矫顽磁力。
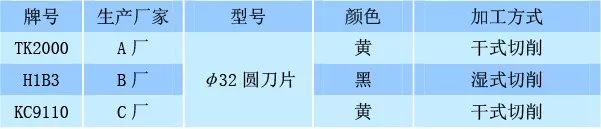
表1 进口刀片信息

表2 原料粉末的化学成分(wt%)
2 试验结果与分析
(1)进口轮毂刀片牌号的分析结果
表3为进口刀片基体的主要性能参数。由表中的分析结果可知,三种进口刀片合金的Co含量都低于6%,属于低钴合金,硬度HRA均大于91.5,从平均晶粒度可以推断,三种合金基体均属于细晶硬质合金。
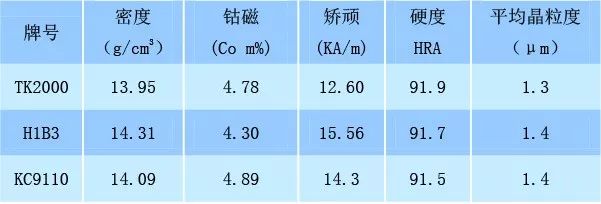
表3 进口刀片基体的主要性能参数
表4列出了三种进口刀片基体的EDS分析结果(因EDS不能测试碳含量,所以该数据是经过换算的金属碳化物成分)。从表中可以看出,在三种进口刀片基体中除硬质相WC和粘接相Co外,还有不同含量的TiC、TaC和NbC,其中KC9110中含有少量的Cr。在合金中,TaC或NbC的主要作用是提高合金的高温硬度与强度,同时还可以提高合金的常温硬度、抗氧化能力、抗月牙洼磨损和抗后刀面磨损能力。此外,TaC还可提高WC-TiC-Co类合金的抗弯强度与冲击韧性,增加刀刃强度,提高刀刃抗碎裂和抗破损能力。这样的基体成分是为了适应列车车轮加工时高切速、大用量和干式(或湿式)切削的苛刻条件。
图1为三种进口刀片的基体断口SEM照片。由图可知,三种进口刀片基体都是由三相组成:α相(WC)、Co相和γ相(固溶体)。其中,α相为多角形黑灰色组织;Co相是围绕在WC晶粒周围的白色组织;γ相是近似圆形的晶粒。三相分布均匀、组织致密。
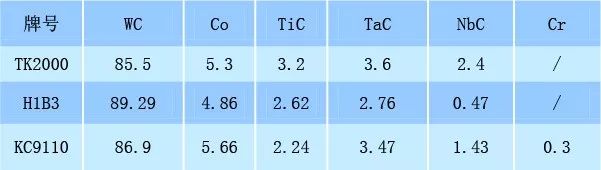
表4 进口刀片基体的成分(wt%)
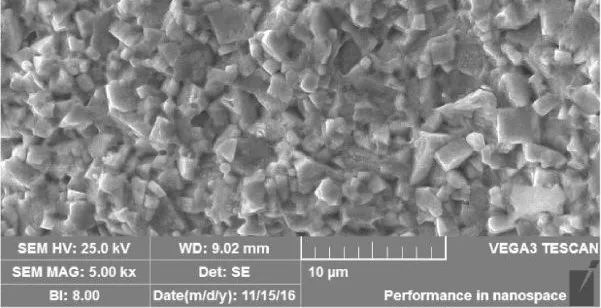
(a)TK2000
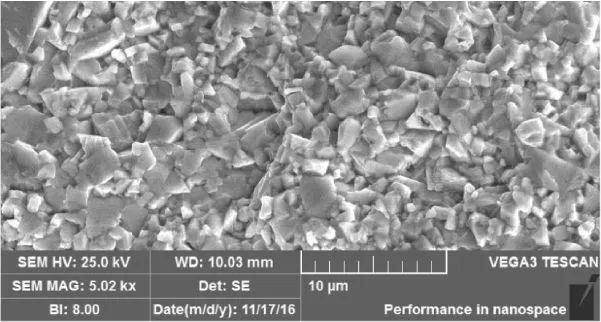
(b)H1B2
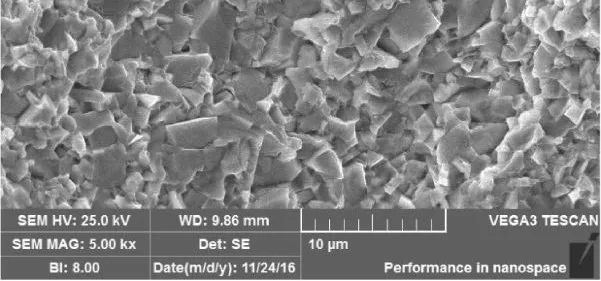
(c)KC9110
图1 三种进口刀片的基体断口SEM照片
图2为三种进口刀片的涂层断口SEM照片。由图可知,三种进口刀片涂层均为多层复合涂层。TK2000涂层分为3层,涂层总厚度约为13μm,主要结构是基体-TiCN-Al2O3-TiN,其中7μm厚的TiCN是细密的柱状晶形,具有很好的耐磨性能,而Al2O3层厚度约5μm,具有很好的抗高温性能,保障高速干切削时刀片基体抗塑性变形能力。
由图2a的金相结构可以看出,TK2000基体表面形成缺立方相碳化物和碳氮化物的韧性区域,即表面为富钴的WC+Co薄层,厚度约25μm。这样的结构一方面可以阻止表面裂纹的扩展;另一方面能满足基体抗变形性能的要求,有效地提高了刀具材料的使用寿命。
由图2b可知,H1B2涂层为2层,涂层总厚度约9μm,主要结构是基体-TiCN-Al2O3,其中TiCN约4μm,Al2O3约5μm。从金相图可以看出,H1B2基体表面也有韧性区域,厚度约15μm。
由图2c可知,KC9110涂层为4层,涂层总厚度约25μm,主要结构是基体-TiCN-TiN-Al2O3-TiN,其中TiCN约14μm,Al2O3约10μm。从金相图可以看出,KC9110基体表面也有韧性区域,厚度约20μm。
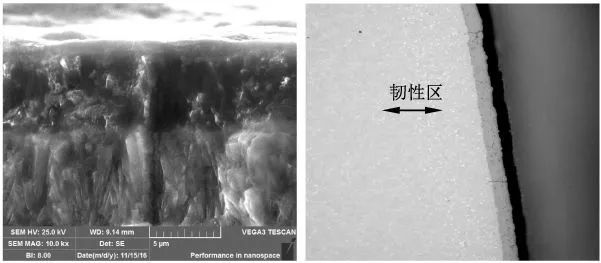
(a)TK2000

(b)H1B2
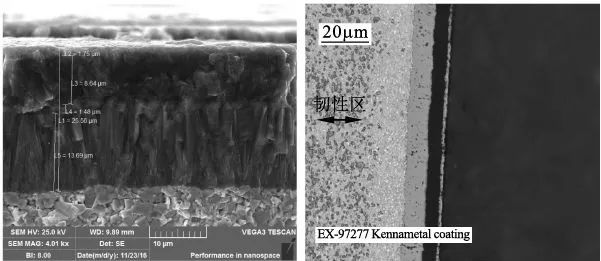
(c)KC9110
图2 三种进口刀片的涂层断口SEM和金相照片(1500×)
(2)基体牌号和涂层的研发
根据表3中进口轮毂刀牌号基体性能的分析结果,以低钴、细晶为研究方向,自主研发了硬质合金牌号Z263,其性能如表5所示,其中钴磁为6.35,硬度91.5HRA,平均晶粒度1.3μm。

表5 Z263的主要性能参数
图3是自主研发的基体牌号Z263的断口SEM照片。由图可知,其晶粒较细,三相组织均匀,没有异常长大的晶粒和缺陷。
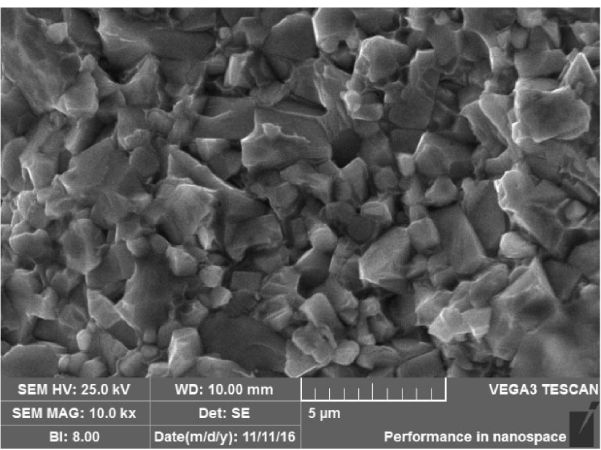
图3 Z263基体断口SEM照片
图4为19H涂层断口SEM图,为多层复合加厚CVD涂层,共5层涂层,由内往外分别是TiN-TiCN-TiN-Al2O3-TiN,总厚度20μm,其中Al2O3约8μm。
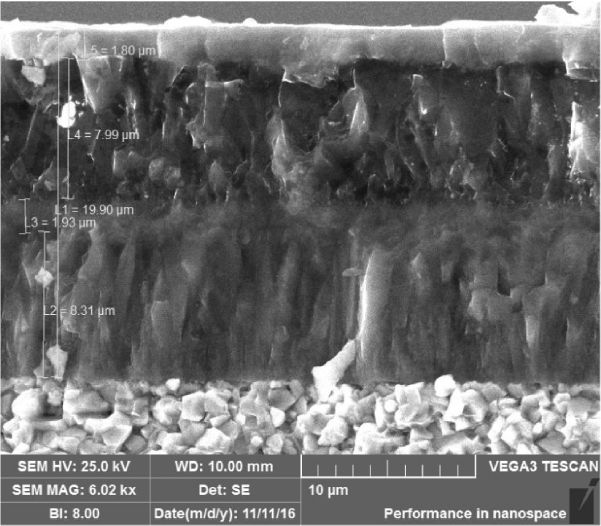
(a)
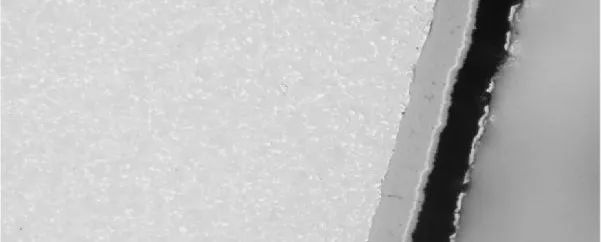
(b)
图4 19H涂层断口SEM和金相照片(1500×)
(3)现场使用结果
采用自主研发的轮毂刀专用基体Z263制备出型号为RCMX320900的轮毂刀片,并在车轮厂进行现场试用,干式切削加工材质为CL60的高速车轮内、外辐板。
加工参数:切削速度v=100m/min,进给量f=1-1.5mm,切削深度ap=5-8mm。搭配高性能超厚CVD涂层19,加工寿命为41件,现场用国外进口涂层刀片的寿命为30件,可见Z263+19涂层的RCMX320900轮毂刀的寿命达到国外进口刀片水平。
总结
三种国外进口轮毂刀的基体TK2000、H1B3和KC9110属于低钴合金,硬度HRA大于91.5,基体中都含有Ta和Nb,同时基体都是表面富钴的梯度合金,涂层为CVD多层复合涂层。
自主研发的低钴细晶合金Z263,组织均匀,性能优良;19H涂层为加厚CVD多层复合涂层,总厚度达到20μm,其中Al2O3约为8μm。Z263搭配19H涂层生产的Φ32轮毂刀,现场试用寿命达到国外进口刀片的水平。
编辑推荐
最新资讯
-
辐射亚太,链接全球——采埃孚再制造
2025-07-30 11:46
-
思看科技发布子品牌SCANOLOGY,全球
2025-07-30 11:06
-
风雨不动安如山——比亚迪叉车构筑“
2025-07-30 08:48
-
NEAS CHINA 新能源汽车技术与生态链
2025-07-29 09:52
-
三维扫描革新碾磨机辊套检测,效率与
2025-07-25 10:46